旋挖钻孔桩沉渣产生原因及二次清孔工艺优化选择
钻孔桩清孔工艺

桩基施工的二次清孔技术及工艺钻孔灌注桩施工,钻机一般采用冲击、冲抓、正反循环旋转钻、旋挖钻等。
使用泥浆护壁成孔工艺。
由于采用泥浆护壁,当钻孔至设计深度后,经检验符合设计要求,必须把钻孔底部的浓泥浆及钻碴沉积物全部清除干净,才能保证质量。
需进行清孔作业。
把泥浆各项指标、比重、粘度、含砂率等降至规范要求以内。
其目的在于使沉淀层尽可能减薄,提高孔底承载力。
1、换浆法清孔:正返循环旋转钻机钻孔终孔后,停止进尺,将钻头提离孔底10~20cm低速空转,泥浆循环正常,把调制好的符合要求的泥浆压入,把孔内比重大的泥浆换出,经沉淀池流回泥浆池,加入调制好的浆循环,使含砂率逐步减小,并小于4%,清孔换浆时间一般为4~10小时,合格后下钢筋笼、导管。
2、抽碴清孔法:返循环钻孔终孔后,采用钻杆清孔,把钻头提离孔底10cm,采用砂石泵把孔底的泥碴抽出,在护筒口注入符合指标的泥浆,计算泵流量,换除孔内全部泥浆,到泥浆合格为止,随后下笼、导管等。
3、捞碴换浆清孔法:适用于冲击、冲抓成孔的摩擦桩,终孔后,用捞碴筒清孔,捞到用手摸泥浆无2~3mm大的颗粒,再把钻头绑一根高压胶管放到孔底,泥浆泵循环泥浆,在沉淀池中沉淀沙土及渣子。
再加入符合要求的泥浆,直到把孔內全部泥浆各项指标清到符合要求为止。
捞渣筒:一般用8—10mm钢板卷制,直径为桩径的0.7—0.8倍,高1.5—2.0m 其上用圆钢作吊环,下装有活门。
由于钢筋笼、导管下到孔底,下钢筋笼时,笼子箍筋碰擦孔壁,把泥皮带到孔底,时间长,泥浆沉淀,形成上清下浊,上下比重不一致,经测量孔底高程,阻力很大,有沉淀,需进行二次清孔。
采用换浆射水清孔法:给导管安装一弯头,连接泥浆泵的高压胶管,钢导管放到距孔底10cm处,再压入调制好的泥浆。
用此方法清孔后,再灌注水下混凝土导管的两侧,各安装一根φ30mm的射水管,射水嘴伸到导管底下面约5cm,使用高压射水冲洗孔底2~5分钟之后,孔底沉淀物翻上,立即停止射水。
旋挖桩施工质量问题原因分析及防治措施

旋挖桩主要施工质量问题原因分析及防治措施一、概述旋挖桩施工具有高效、节能、低噪音、无污染、适应地层较广泛等优点,施工性化、经济性、工期短、功效高、技术先进的等优势已得到体现,但其施工工艺质量控制标准和施工工艺技术标准现还无国家工法标准,施工过程控制须加强施工组织、加快其它工序的衔接等。
控制不好时也会遇到问题。
旋挖钻孔灌注桩较常见的主要施工质量问题有:塌孔、卡钻、埋钻、孔斜、漏浆、掉钻头、掉钻头底板、不进尺、扩孔缩孔、孔底沉渣过多、堵管、断桩、钢筋笼上浮等。
(一)塌孔原因分析:泥浆选择不当,泥浆比重不稳定、相对密度不够;护筒直径偏小、长度不够;由于旋挖钻机的圆柱形钻头在提出泥浆液面时会使钻头下局部空间产生“真空”,同时由于钻头提升时泥浆对护筒下部与孔眼相交部位孔壁的冲刷作用,很容易造成护筒底孔壁坍塌;水头压力小或出现承压水;钻头钻速过快或空转时间太长都易引起钻孔下部坍塌;成孔后待灌时间和灌注时间过长,补浆不及时。
预防措施:根据土层不同选配与之相适应的泥浆,严格控制护筒加工材料、质量、尺寸等;要把护筒下牢与孔位同心,如地下水位变化大,采取升高护筒的办法,增大水头;松散地层钻进时,适当控制钻进速度,提钻速度要均匀;补浆要及时,要尽快灌注,灌注时间不超过3。
5h。
事故处理:应立即暂停钻进,查明塌孔原因及大概位置,当溻孔不严重时,可增大泥浆粘度、比重及孔内水头高度,同时慢转轻压试钻一段时间;如遇砂层可在泥浆中掺适量水泥改善泥浆性能;如果塌孔继续加重,应停钻用粘土回填,2~4周后再重新钻孔。
(二)掉钻头、钻头底板脱落原因及预防措施:引起埋钻的原因主要有以下几种原因:挖钻钻进时进尺太长或孔壁坍塌,造成钻头和钻杆埋入孔中;孔口塌陷或机械操作失误使孔口的钻头掉入;提钻时受阻或施工中钢丝绳拉断,造成钻头和钻杆埋入孔中;工作扭矩过大,造成钻杆断裂,连接销或提引器损坏造成的掉钻.预防措施:控制钻进进尺长度,钻进过程中根据地层情况调整泥浆特性,确保孔壁稳定;将钻头等杂物远离孔口放置,护筒顶口周边夯实,封闭地表水;提钻时加强监视卷扬压力表,钻进时确保垂直度,提钻时发现压力突变时,及时调整方向;经常检查钢丝绳状况,勤更换;班组施工过程中对连接销、钻杆和提引器等设备勤做检查保养。
泥浆护壁钻孔灌注桩为什么要进行二次清孔 什么时候进行二次清孔 沉渣厚度验收规范是如何规定的

内容介绍
刚开始清孔时泥浆比重大为1.25~1.45之间,地质不取大值,随着孔底成渣的减少泥比重逐渐 减少。 第二次清孔在安装导管后,利用导管输送循环泥浆。清孔后孔底泥浆的含砂率应≤8%,粘度 ≤28S,泥浆比重<1.25。灌注混凝土之前孔底沉渣厚度应符合下列规定:端承桩≤50㎜,摩擦 端承桩、端承摩擦桩≤100㎜,摩擦桩≤300㎜。控制在泥浆比重控制在1.15~1.25之间,孔底 沉渣厚度控制在≤50mm。
谢谢观看
泥浆护壁钻孔灌注桩为什么要进行二 次清孔?什么时候进行二次清孔?沉
渣厚度验收规范是如何规定的
பைடு நூலகம்
内容介绍
因为从清孔到砼开始浇筑中间过程太长,有部分沉淀,所以须二次清孔二次;清孔时间为导管下 完后,浇筑砼前;一般为30d或按设计要求。 灌注桩成桩后进行第一次清孔的目的主要是尽最大可能清理桩底的沉渣,但是它有个局限性,就 是第一次清孔后要保持孔内泥浆的比重,防止缩孔或者塌孔。 此时下钢筋笼、导管。然后进行彻底的二次清孔,这次对泥浆比重要求较高,一般为1.04~1.15, 尽量稀释泥浆,并彻底清理孔底的沉渣,沉渣厚度:端承桩小于等于5cm,摩擦桩小于等于10cm, 抗拔桩小于等于15cm。 为利用导管输送循环泥浆;作用为控制在泥浆比重。 清孔采用正循环换浆方法,分两次清孔。第一次清孔在钻进至设计深度后,使钻头慢速空转不进 尺,不断循环换浆。
浅谈旋挖钻孔灌注桩孔底沉渣的质量控制

浅谈旋挖钻孔灌注桩孔底沉渣的质量控制摘要:结合工程案例,介绍了在较厚砂层进行旋挖钻孔灌注桩施工技术,并提出了控制孔底沉渣厚度的有效措施及方法。
关键词:旋挖钻孔;灌注桩;孔底沉渣;质量控制1 旋挖钻孔灌注桩孔底沉渣产生的原因分析1.1 桩孔孔壁塌落(1)杂填土层较厚且不稳定造成孔口表土层塌落孔内;(2)淤泥层及砂层由于钻孔过程的提、放钻具在孔内产生正、负压差所引起的抽吸作用,造成孔壁塌落;(3)在提、放钻具及下放钢筋笼时刮蹭孔壁,造成孔壁砂土掉落孔内;(4)成孔后未及时浇筑混凝土,空置时间太长导致泥浆分层离析孔壁失去稳定;(5)孔口附近有较大的集中荷载作用压垮孔壁;(6)泥浆比重过小,使得泥浆侧向护壁能力不足造成孔壁塌落;(7)由于钻具转速过快、扰动过大引起砂层液化造成孔壁塌落。
1.2 泥浆沉淀(1)由于泥浆粘度过低,悬浮能力差,使得泥浆发生分层沉淀;(2)泥浆含砂率过高,造成孔底沉砂过多;(3)混凝土浇注前的等待时间过长,使得悬浮物下沉堆积孔底。
1.3 钻孔残留(1)因钻具磨损、变形过大造成渣土泄漏、残留而产生沉渣;(2)受钻具自身结构限制,因钻齿间隙所造成的渣土残留。
1.4 清孔工艺(1)清孔所用的水泵功率太大,其过强水流产生的冲刷作用引发孔壁剥落;(2)采用钻具清孔时,其清孔工艺及钻具选择不合理,孔底沉渣无法清除干净;(3)采用正、反循环清孔时,泥浆性能不达标造成沉渣无法携带出孔底。
1.5 施工人员量测误判(1)由于施工员经验不足,在进行孔底沉渣厚度量测时误判,错误将清孔不合格的桩孔判断为合格孔;(2)孔底沉渣厚度量测工具选择不当产生误判。
2 旋挖钻孔灌注桩孔底沉渣控制措施(1)根据孔口土层情况适当增加护筒埋设深度,使其穿过杂填土层并高出孔口30~40cm,始终保持孔内水位高于地下水位≮ 1.5m,同时护筒直径比钻具直径大 20cm 并防止碰撞及震动;(2)在钻进过程中慢提、慢放钻具,速度控制在70cm/s左右,在进入砂层时降低钻具转速,防止因扰动过大造成砂层液化;(3)在提、放钻具及下放钢筋笼时注意保持对中和垂直,钻进过程中每三钻复核一次钻杆垂直度,将垂直度控制在 1%以内,钢筋笼保护层垫块采用可转动的混凝土圆形垫块,减少刮蹭孔壁;(4)合理组织,紧凑工序,在进行第一次清孔时即开始安排混凝土罐车到场等待,为预防不测,商品混凝土的缓凝时间设定在 4h 以上;(5)在旋挖钻孔桩机及混凝土罐车停放面的近孔口一侧安放较大钢板,钻进过程中孔内取出的泥土及时清离孔口,以减少孔口的集中荷载;(6)在钻进过程中,根据地质情况适当加大泥浆比重至1.13~1.18,调整泥浆粘度至19~21Pa •s,增加泥浆的护壁及悬浮能力;(7)采用泥浆分离机分离出泥浆中的砂及其它大颗粒物,将泥浆中的含砂率控制在 4% 以内;(8)根据不同地层情况选用适当钻具,加强对钻底结构的检查、修补维护,减小转动底与固定底之间的间隙。
旋挖钻孔桩沉渣产生原因及清孔工艺优化选择
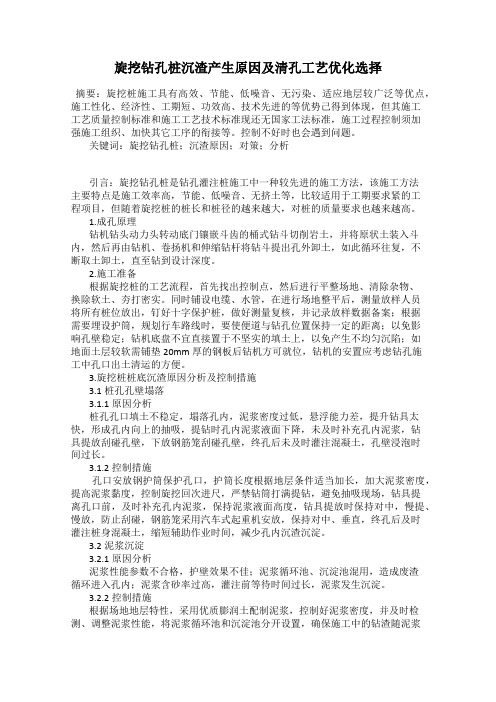
旋挖钻孔桩沉渣产生原因及清孔工艺优化选择摘要:旋挖桩施工具有高效、节能、低噪音、无污染、适应地层较广泛等优点,施工性化、经济性、工期短、功效高、技术先进的等优势己得到体现,但其施工工艺质量控制标准和施工工艺技术标准现还无国家工法标准,施工过程控制须加强施工组织、加快其它工序的衔接等。
控制不好时也会遇到问题。
关键词:旋挖钻孔桩;沉渣原因;对策;分析引言:旋挖钻孔桩是钻孔灌注桩施工中一种较先进的施工方法,该施工方法主要特点是施工效率高,节能、低噪音、无挤土等,比较适用于工期要求紧的工程项目,但随着旋挖桩的桩长和桩径的越来越大,对桩的质量要求也越来越高。
1.成孔原理钻机钻头动力头转动底门镶嵌斗齿的桶式钻斗切削岩土,并将原状土装入斗内,然后再由钻机、卷扬机和伸缩钻杆将钻斗提出孔外卸土,如此循环往复,不断取土卸土,直至钻到设计深度。
2.施工准备根据旋挖桩的工艺流程,首先找出控制点,然后进行平整场地、清除杂物、换除软土、夯打密实。
同时铺设电缆、水管,在进行场地整平后,测量放样人员将所有桩位放出,钉好十字保护桩,做好测量复核,并记录放样数据备案;根据需要埋设护筒,规划行车路线时,要使便道与钻孔位置保持一定的距离;以免影响孔壁稳定;钻机底盘不宜直接置于不坚实的填土上,以免产生不均匀沉陷;如地面土层较软需铺垫20mm厚的钢板后钻机方可就位,钻机的安置应考虑钻孔施工中孔口出土清运的方便。
3.旋挖桩桩底沉渣原因分析及控制措施3.1桩孔孔壁塌落3.1.1原因分析桩孔孔口填土不稳定,塌落孔内,泥浆密度过低,悬浮能力差,提升钻具太快,形成孔内向上的抽吸,提钻时孔内泥浆液面下降,未及时补充孔内泥浆,钻具提放刮碰孔壁,下放钢筋笼刮碰孔壁,终孔后未及时灌注混凝土,孔壁浸泡时间过长。
3.1.2控制措施孔口安放钢护筒保护孔口,护筒长度根据地层条件适当加长,加大泥浆密度,提高泥浆黏度,控制旋挖回次进尺,严禁钻筒打满提钻,避免抽吸现场,钻具提离孔口前,及时补充孔内泥浆,保持泥浆液面高度,钻具提放时保持对中,慢提、慢放,防止刮碰,钢筋笼采用汽车式起重机安放,保持对中、垂直,终孔后及时灌注桩身混凝土,缩短辅助作业时间,减少孔内沉渣沉淀。
浅谈旋挖成孔桩基沉渣处理
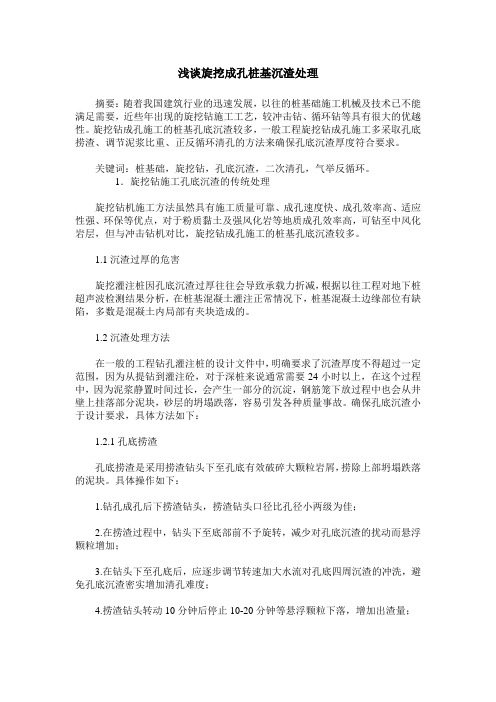
浅谈旋挖成孔桩基沉渣处理摘要:随着我国建筑行业的迅速发展,以往的桩基础施工机械及技术已不能满足需要,近些年出现的旋挖钻施工工艺,较冲击钻、循环钻等具有很大的优越性。
旋挖钻成孔施工的桩基孔底沉渣较多,一般工程旋挖钻成孔施工多采取孔底捞渣、调节泥浆比重、正反循环清孔的方法来确保孔底沉渣厚度符合要求。
关键词:桩基础,旋挖钻,孔底沉渣,二次清孔,气举反循环。
1.旋挖钻施工孔底沉渣的传统处理旋挖钻机施工方法虽然具有施工质量可靠、成孔速度快、成孔效率高、适应性强、环保等优点,对于粉质黏土及强风化岩等地质成孔效率高,可钻至中风化岩层,但与冲击钻机对比,旋挖钻成孔施工的桩基孔底沉渣较多。
1.1沉渣过厚的危害旋挖灌注桩因孔底沉渣过厚往往会导致承载力折减,根据以往工程对地下桩超声波检测结果分析,在桩基混凝土灌注正常情况下,桩基混凝土边缘部位有缺陷,多数是混凝土内局部有夹块造成的。
1.2沉渣处理方法在一般的工程钻孔灌注桩的设计文件中,明确要求了沉渣厚度不得超过一定范围,因为从提钻到灌注砼,对于深桩来说通常需要24小时以上,在这个过程中,因为泥浆静置时间过长,会产生一部分的沉淀,钢筋笼下放过程中也会从井壁上挂落部分泥块,砂层的坍塌跌落,容易引发各种质量事故。
确保孔底沉渣小于设计要求,具体方法如下:1.2.1孔底捞渣孔底捞渣是采用捞渣钻头下至孔底有效破碎大颗粒岩屑,捞除上部坍塌跌落的泥块。
具体操作如下:1.钻孔成孔后下捞渣钻头,捞渣钻头口径比孔径小两级为佳;2.在捞渣过程中,钻头下至底部前不予旋转,减少对孔底沉渣的扰动而悬浮颗粒增加;3.在钻头下至孔底后,应逐步调节转速加大水流对孔底四周沉渣的冲洗,避免孔底沉渣密实增加清孔难度;4.捞渣钻头转动10分钟后停止10-20分钟等悬浮颗粒下落,增加出渣量;5.捞渣4-5斗后停止捞渣1小时以上,待孔底沉渣相对稳定后继续捞渣。
1.2.2泥浆比重调节在施工过程中回填上部采用钢护筒护壁,下部采用泥浆护壁,这样能有效的减少塌孔,保证成孔质量,减少和杜绝孔底沉渣,保证混泥土的充盈系数。
钻孔灌注桩桩底沉渣过厚、桩身夹渣及断桩措施技术
一、钻孔灌注桩(包括旋挖桩,冲孔桩)桩底沉渣过厚1.分两次进行清孔,第一次清孔应在成孔完成后进行,第二次清孔应在安放钢筋笼和导管安装完毕后进行。
2.第一次清孔可采用正循环或反循环方式进行,在清孔过程中应不断置换泥浆,并保持孔内浆液面的稳定,置换后的泥浆指标(如比重、粘度、含砂量等)应符合有关规范的要求。
3.在吊放钢筋笼、浇注混凝土等作业时,应防止扰动孔口土和碰撞孔壁导致泥土坍塌落入柱底。
4.第二次清孔可采用正循环或气举反循环的方式进行,采用气举反循环清孔时要保证补浆充足和孔内泥浆液面稳定。
5.在灌注第一斗混凝土之前,孔底沉渣厚度必须满足设计和有关规范的要求,否则不得灌注混凝土。
二、钻孔灌注桩(包括旋挖桩,冲孔桩)桩身夹渣及断桩1.导管使用前应进行试拼装和压水试验,水压力应根据孔深通过计算确定。
2.在混凝灌注时,混凝土的期落度应控制在18-22cm要具有良好的和易性、流动性。
3.开始灌注混凝土时,导管底部至孔底距离控制在30cm-40cm,应有足够的混凝土储备量,使导管一次埋入混凝土内1m以上。
混凝土灌注过程中,导管埋入混凝土深度宜为2~5m,严禁将导管提出混凝土灌注面,并应控制提拔导管速度。
灌注过程中应不断测定混凝土面上升高度,并根据混凝土的供应情况来确定拆卸导管的时间及长度。
4.混凝土灌注必须连续施工,并严格控制每车混凝土的坍落度,每根桩的灌注时间应按混凝土的初凝时间控制,混凝土的初凝时间应控制在不小于正常运输和灌注时间之和的两倍。
5.在灌注混凝土的过程中应注意控制泥浆的比重等性能指标。
三、钻孔灌注桩(包括旋挖桩,冲孔桩)钢筋笼保护层不足或露筋1.钢筋笼箍筋或加强筋上应设置混凝土保护层垫块,宜采用预制混凝土滚轮式垫块。
2.钢筋笼宜分段孔口安装,长钢筋笼一次安装时,应采取措施避免钢筋笼变形.3.钢筋笼应对孔中心按放,并确保最小保护层厚度,安放完成后宜与钢护简焊接固定。
旋挖钻孔桩常见施工质量问题及防治措施
旋挖钻孔桩常见施工质量问题及防治措施一、旋挖钻孔前工作出现的质量问题及防治措施1、确保桩位无偏差,钻机跳好四步曲大家都知道,在钻机进行作业前一是将钻机就位到指定桩点;二是确定放点无误后进行十字放线;三是调校钻机后对点下钻;四是埋设好护筒等待测验。
我将其称为“钻机四步曲”。
2、常见的护筒冒水,护筒倾斜移位,造成钻孔偏斜,甚至无法施工。
造成原因:埋设护筒时围土没有夯实,或护筒内水位差过低,或钻头起落时破坏泥浆保护层。
防治措施:在埋筒时,孔四周应土分层夯实。
护筒内保持在护筒项部以下30公分处的水头高度。
钻头起落时,应防止碰撞护筒。
发现护筒冒水时,应立即停止钻孔,用粘土在四周填实加固,若护筒严重下沉或移位时,则应重新埋设护筒。
3、钻进过程中,如发现泥浆中不断出现气泡,泥浆突然漏失,则表示有孔壁坍陷迹象。
造成原因:孔壁坍陷的主要原因是土质松散和砂层地段,泥浆护壁不好,护筒周围未用粘土填封以及护筒内水位不高。
钻进速度过快、空钻时间过长、成孔后待灌时间过长和灌注时间过长也会引起孔壁坍陷。
防治措施:在松散易坍的土砂层中,适当埋深护筒,用粘土密实填封护筒四周,使用优质的泥浆,提高泥浆的比重和粘度,保持护筒内泥浆水位高度。
搬运和吊装钢筋笼时,应防止变形,笼子下放要对准孔位,避免碰撞孔壁,钢筋笼焊接长时间不要过长,尽量要加快焊接时间,尽可能缩短沉放时间。
成孔后,待灌时间一般不应大于3小时,并控制混凝土的灌注时间,在保证施工质量的情况下,尽量缩短灌注时间。
4、缩径即孔径小于设计孔径造成原因:塑性土膨胀。
防治措施:采用优质泥浆,降低失水量。
成孔时,应加大泵量,加快成孔速度,在成孔一段时间内,孔壁形成泥皮,则孔壁不会渗水,亦不会引起膨胀。
或在钻具上可焊接边片,在钻进或起钻时起到扫孔作用。
如出现缩径应采用上下反复扫孔的办法,以扩大孔径。
5、钻孔偏斜造成原因:钻机安装就位稳定性差,钻具下钻不对正,地面软弱或软硬不均匀;土层呈斜状分布或土层中夹有大的孤石或其它硬物等情形。
旋挖灌注桩桩底沉渣处理方案
旋挖灌注桩桩底沉渣处理方案旋挖灌注桩是一种常用的地基处理方法,其中桩底沉渣处理是该工程中重要的一个环节。
桩底沉渣是在灌注桩施工过程中产生的,主要包括土壤、砂石等杂质。
这些沉渣对于施工质量和环境保护都有一定的影响,所以需要采取合适的处理方案。
桩底沉渣处理方案应该从环保、经济和施工质量等多个角度综合考虑。
以下是一种可行的桩底沉渣处理方案:1.沉渣初步处理:在挖掘桩孔的过程中,将底部沉积的土壤、砂石等杂质先行清除。
可以使用挖掘机、抽泵等设备进行清理,将沉渣堆放在指定的区域。
2.沉渣中继处理:清理后的沉渣需要进行二次处理,以去除更细小的颗粒和有机物质。
可以采用筛分、洗涤等方法,将沉渣中的杂质进行进一步的分离和过滤。
这一步可以通过人工操作或机械设备来完成,以提高处理效率。
3.沉渣填充和利用:经过中继处理后的沉渣可以用于填充挖掘桩孔或作为建筑材料的一部分。
填充沉渣时需要注意均匀性和稳定性,以确保施工质量。
如果沉渣无法全部填充,则可以考虑利用作为道路基础填料或其他项目中的填料。
这种处理方法可以减少沉渣对环境造成的影响,同时也可以节约成本。
4.沉渣处置:如果沉渣无法进行填充或利用,需要进行专门的处置。
可以选择将沉渣运送至专门的垃圾处理中心进行处理,或者选择委托专业的处理公司进行处置。
这种处理方式需要注意环保要求,确保处理过程符合相关法规和标准。
在桩底沉渣处理过程中,需要注意以下几点:1.环保要求:处理过程必须严格按照相关的环保法规和标准进行。
在处理过程中,应采用环保设备和工艺,尽量减少对环境的影响。
2.施工质量:处理过程中需要保证施工质量,确保沉渣处理后的填充物或材料的稳定性和可靠性。
3.经济成本:处理方案应该兼顾经济成本,选择合适的处理方法,既能够满足环保要求,又能够控制成本。
4.安全性:处理过程中需要采取相应的安全措施,避免发生事故和环境污染。
总之,旋挖灌注桩桩底沉渣处理方案需要考虑环保、经济和施工质量等多个方面的因素。
浅谈旋挖成孔桩基沉渣处理
浅谈旋挖成孔桩基沉渣处理摘要:随着我国建筑行业的迅速发展,以往的桩基础施工机械及技术已不能满足需要,近些年出现的旋挖钻施工工艺,较冲击钻、循环钻等具有很大的优越性。
旋挖钻成孔施工的桩基孔底沉渣较多,一般工程旋挖钻成孔施工多采取孔底捞渣、调节泥浆比重、正反循环清孔的方法来确保孔底沉渣厚度符合要求。
关键词:桩基础,旋挖钻,孔底沉渣,二次清孔,气举反循环。
1.旋挖钻施工孔底沉渣的传统处理旋挖钻机施工方法虽然具有施工质量可靠、成孔速度快、成孔效率高、适应性强、环保等优点,对于粉质黏土及强风化岩等地质成孔效率高,可钻至中风化岩层,但与冲击钻机对比,旋挖钻成孔施工的桩基孔底沉渣较多。
1.1沉渣过厚的危害旋挖灌注桩因孔底沉渣过厚往往会导致承载力折减,根据以往工程对地下桩超声波检测结果分析,在桩基混凝土灌注正常情况下,桩基混凝土边缘部位有缺陷,多数是混凝土内局部有夹块造成的。
1.2沉渣处理方法在一般的工程钻孔灌注桩的设计文件中,明确要求了沉渣厚度不得超过一定范围,因为从提钻到灌注砼,对于深桩来说通常需要24小时以上,在这个过程中,因为泥浆静置时间过长,会产生一部分的沉淀,钢筋笼下放过程中也会从井壁上挂落部分泥块,砂层的坍塌跌落,容易引发各种质量事故。
确保孔底沉渣小于设计要求,具体方法如下:1.2.1孔底捞渣孔底捞渣是采用捞渣钻头下至孔底有效破碎大颗粒岩屑,捞除上部坍塌跌落的泥块。
具体操作如下:1.钻孔成孔后下捞渣钻头,捞渣钻头口径比孔径小两级为佳;2.在捞渣过程中,钻头下至底部前不予旋转,减少对孔底沉渣的扰动而悬浮颗粒增加;3.在钻头下至孔底后,应逐步调节转速加大水流对孔底四周沉渣的冲洗,避免孔底沉渣密实增加清孔难度;4.捞渣钻头转动10分钟后停止10-20分钟等悬浮颗粒下落,增加出渣量;5.捞渣4-5斗后停止捞渣1小时以上,待孔底沉渣相对稳定后继续捞渣。
1.2.2泥浆比重调节在施工过程中回填上部采用钢护筒护壁,下部采用泥浆护壁,这样能有效的减少塌孔,保证成孔质量,减少和杜绝孔底沉渣,保证混泥土的充盈系数。
- 1、下载文档前请自行甄别文档内容的完整性,平台不提供额外的编辑、内容补充、找答案等附加服务。
- 2、"仅部分预览"的文档,不可在线预览部分如存在完整性等问题,可反馈申请退款(可完整预览的文档不适用该条件!)。
- 3、如文档侵犯您的权益,请联系客服反馈,我们会尽快为您处理(人工客服工作时间:9:00-18:30)。
旋挖钻孔桩沉渣产生原因及清孔工艺优化选择雷斌叶坤李榛柴源(深圳市工勘岩土工程有限公司,广东深圳 518026)[摘要] 随着旋挖钻孔灌注桩的广泛应用,桩底沉渣过厚成为突出的质量通病。
本文结合作者从事旋挖钻孔灌注桩的施工实践,分析了桩底沉渣过厚产生的原因,介绍了六种泥浆正循环、反循环、无循环清孔工艺方法,并对比分析了各种清孔工艺的特点,提出了旋挖桩清孔工艺的优化选择方法。
[关键词] 旋挖钻孔桩;孔底沉渣;清孔工艺;优化选择The Causes of the Sediment at the Hole Bottom of Rotating Excavation Drilling Pile and the Optimal Selection of Hole Cleaning MethodBin Lei, Kun Ye, Zhen Li ,Yuan Cai(Shenzhen Gong Kan Geotechnical Engineering Co. Ltd, Shenzhen Guangdong 518026)Abstract: With the widely application of the rotating excavation drilling cast-in-place pile, the overweighting sediment at the hole bottom is becoming one of the most prominent quality problems. This article has analyzed the causes of the overweighting sediment at the hole bottom, which is based on the author's construction practice experience of working on rotating excavation drilling cast-in-place pile. In addition, it also introduces six hole cleaning methods including the slurry direct circulation, the slurry reverse circulation, the non-cycle, and so on. And by the comparison analysis of all the hole cleaning methods, author gives an optimal selection method of cleaning process in the rotating excavation drilling pile.Key words: rotating excavation drilling pile; sediment at the hole bottom; hole cleaning methods; optimal selection1 引言旋挖钻机具有机电一体化、钻孔速度快、入岩能力强、综合成本低、机动灵活、绿色环保等显著特点,随着旋挖钻机整体性能的提升,以及旋挖钻具的不断改进,旋挖钻孔桩已广泛应用于桩基础工程施工。
据不完全统计,目前在深圳及周边地区使用的旋挖钻机数量已超过上百台,完成的各类基桩数量已超过总量的40%,预计数年后其使用量还将大幅提高。
深圳桩基市场中旋挖钻机的大量推广应用只是在近些年,一大批国内外各种品牌、大小吨位、型号的系列旋挖钻机同时在使用,如:三一重工SR220、280、360、420Ⅱ,中联重科ZR220、250、280、360A、420,土力机械SR60、65、70、80、100,宝峨BG20、25、30、40,徐工XR220、280、360、460,上海金泰SH25、30、36等,一大批重点项目的桩基工程均由旋挖桩机完成,如:国信金融大厦、中国人寿大厦、腾讯滨海大厦、百度大厦、阿里云大厦、阿里巴巴大厦、东门新苑、农科香堤绿洲家园、、动漫大厦、海王星辰大厦、百郦大厦等等。
旋挖机的使用,加快了桩基施工进度,减少了泥浆使用量,节省了工程造价,提升了现场文明施工水平。
旋挖钻机自动化水平高,适应能力强。
但受不同钻机的机械性能、人员操作水平、现场技术管理能力等存在的差异,特别是受场地地层条件的影响,加之行业尚未编制相关旋挖钻孔桩施工技规范,没有形成系统的工法研究,施工过程中大量的旋挖成桩的质量问题也随之产生,桩底沉渣过厚即是较普遍的质量通病之一。
桩底沉渣超标或过厚对桩基质量将产生严重的影响,主要体现在:沉渣过厚严重制约桩端承载力的发挥和增大桩的沉降位移,对桩基上层建筑整体结构安全会造成巨大不良隐患。
鉴于以上问题,现行桩基规范对钻孔灌注桩孔底沉渣厚度提出了明确要求。
在《建筑桩基技术规范》(JGJ94-2008)中,规定端承桩沉渣厚度≤50mm,摩擦桩沉渣厚度≤100mm,许多地方性行业规范也出台明确规定对此进行约束。
然而在实际施工中,由于对旋挖钻机操作人员培训不够,现场技术管理人员对施工工序把握不严,特别是受复杂地层的影响,造成桩底沉渣超标问题依然严峻。
因此,如何在旋挖钻孔桩施工过程中预防桩孔沉渣的产生,合理选择桩孔的二次清孔工艺,保证孔底沉渣满足设计和规范要求,成为困扰业界对旋挖钻机的客观评价和使用前景。
本文结合深圳地区旋挖钻孔灌注桩施工情况,分析了旋挖桩孔底沉渣产生的原因,提出了几种有效的二次清孔方法,论述了不同清孔方法的特点,提出了综合优化选择的方法。
2 旋挖桩桩底沉渣原因分析及控制措施旋挖钻孔灌注桩桩底沉渣可能产生于旋挖钻机施工的钻进成孔、安放钢筋笼、灌注混凝土等多个环节中,分析认为沉渣产生的原因大致分为以下几类:2.1 桩孔孔壁塌落2.1.1原因分析桩孔孔口填土层不稳定塌落孔内;泥浆比重过低,悬浮能力差;提升钻具太快,形成孔内向上的抽吸作用;提钻时孔内泥浆液面下降,未及时补充孔内泥浆;钻具提放刮碰孔壁;下放钢筋笼刮碰孔壁;终孔后未及时灌注砼,孔壁浸泡时间过长。
2.1.2控制措施孔口安放钢护筒保护孔口,护筒长度根据地层条件,适当加长;加大泥浆比重,提高泥浆的粘度,减少孔底沉淀;控制旋挖每回次进尺,严禁钻筒打满提钻,避免抽吸现场;钻具提高孔口前,及时补充孔内泥浆,保持泥浆液面高度;钻具提放时保持对中,慢提、慢放,防止刮碰;下放钢筋笼保持对中、垂直;终孔后及时灌注桩身混凝土,减少辅助作业时间。
2.2 泥浆沉淀2.2.1原因分析泥浆性能参数不合格,护壁效果不佳;灌注前等待时间过长,泥浆发生沉淀;泥浆含砂率高。
2.2.2控制措施配制合适参数的泥浆,并及时检测、调整泥浆性能;缩短灌注等待时间,避免泥浆沉淀;设置泥浆沉淀池或者泥浆分离器将泥浆中泥砂沉淀分离,并调整泥浆性能。
2.3 钻孔残留2.3.1原因分析钻具钻底变形或者磨损过大,渣土泄露生成沉渣;钻底结构本身限制,如钻齿布置高度、间距等原因造成渣土残留过多生成沉渣。
2.3.2控制措施选用合适钻具,经常检查钻底结构;减小旋转底和固定底间隙;及时补焊保径条,更换磨损严重的边齿;合理调整钻齿布置角度、间距;增加清渣次数,减少桩底残留。
2.4清孔工艺2.4.1原因分析清孔时的抽吸作用造成垮孔;清孔时泥浆性能不达标,沉渣无法携带出孔底;清孔工艺选择不合理,沉渣无法清除干净。
2.4.2控制措施清孔时控制泵的抽吸力,减少对孔壁的冲击;清孔时换浆,并调整好泥浆性能指标;根据钻孔情况,选择适合的二次清孔工艺。
3 旋挖钻孔灌注桩二次清孔技术旋挖钻孔施工过程中应采取适当措施避免沉渣产生,在钢筋笼、灌注导管安放后,对沉渣过厚的桩孔,须选用合适的二次清孔工艺进行沉渣处理。
二次清孔是在完成旋挖成孔、下入钢筋笼和灌注导管后,利用灌注导管清除孔底沉渣的关键工序。
桩孔二次清孔工艺的合理选择,对清除孔底沉渣,保证桩身工程质量极其重要。
目前,业内旋挖桩桩孔二次清孔技术按泥浆循环方式可分为以下三类:泥浆正循环清孔、反循环清孔和钻具无泥浆循环清孔。
3.1 泥浆正循环清孔3.1.1 工艺原理泥浆正循环清孔工艺是普遍采用的一种清孔方式,是由泥浆泵泵送的泥浆经过胶管,与孔口的灌注导管连接,并把泥浆送到孔底;送到孔底的泥浆悬浮并携带孔底沉渣,再经过灌注导管与孔壁之间的环状空间返回地面,流入循环沟、沉淀池,然后进入泥浆池循环使用。
正循环二次清孔工艺原理见图1示。
图1 正循环二次清孔原理示意图泥浆正循环清渣运行时须注意以下事项:(1)选择合适的泥浆泵,泥浆流量过大,对孔壁冲刷大,容易塌孔;泥浆流量小,沉渣上升速度慢,清渣效果差,耗费时间长。
实际施工中,流量、扬程作为选择泥浆泵的依据,可根据桩孔直径大小配制功率在12~30KW之间的3PN泥浆泵。
(2)减少管道接口,避免管道直径剧烈变化、运行方向剧烈变化,减小泥浆循环系统中的沿程阻力和局部阻力消耗。
(3)泥浆循环过程中,泥浆循环系统中含有较多的粗颗粒或岩渣,会反复循环带入孔内,影响清孔效果。
应定期对沉淀池、泥浆池废渣进行清理,可加大、加长泥浆循环沟,并派专人沟内捞渣。
(4)清孔过程中,根据清渣效果适时上下提放、左右移动导管,加快扰动孔底沉渣,以达到快速清渣的效果。
3.2 泥浆旋流器正循环清孔3.1.1 工艺原理为减少正循环二次清孔过程中泥浆中粗颗粒含量大,提高泥浆性能指标,缩短清孔时间,提升清孔效果,在泥浆正循环清孔系统中,引进了泥浆旋流器辅助清孔,即:在泥浆泵泵送泥浆入孔底的胶管上,在地面串联泥浆旋流器,在泥浆被泵入孔底前将泥浆中的粗颗粒排出,预先进行浆渣有效分离,保证优质泥浆进入孔底,减少岩渣的重复带入,并有效地提高了泥浆的携渣能力,大大缩短清孔时间,既提高工效,又保证清孔效果。
泥浆旋流器二次清孔工艺平面布设见图2示。
图2 旋流器二次清孔原理示意图泥浆旋流器正循环二次清孔凭借旋流装置对泥浆进行有效分离,其操作简便、分离效果好,是普通泥浆正循环清孔系统的升级工艺,是我公司拥有的实用新型专利技术,同时被评为2011年度深圳市工程建设市级工法、广东省工程建设省级工法,具有实用性、有效性,为二次清孔提供了新的可靠选择。
泥浆旋流器正循环二次清孔时应注意:(1)派专人负责旋流器工作状态,观察排渣口是否堵塞;如出现旋流器进口部分吸入块石、牡蛎壳、水泥块等较大异物时,会使进浆速度降低,应及时清除。
(2)如果旋流器进口泥浆中的固相粗颗粒含量过高,或底流口阀门调节过小,会使旋流器过载,会导致底流口堵塞,可通过调节底部阀门,以保持底部排渣通畅。
(3)旋流器出渣口设置专门的排渣池,并及时进行清理排渣。