数控车床自动回转刀架英文文献以及翻译
车床介绍外文资料翻译中英文对照
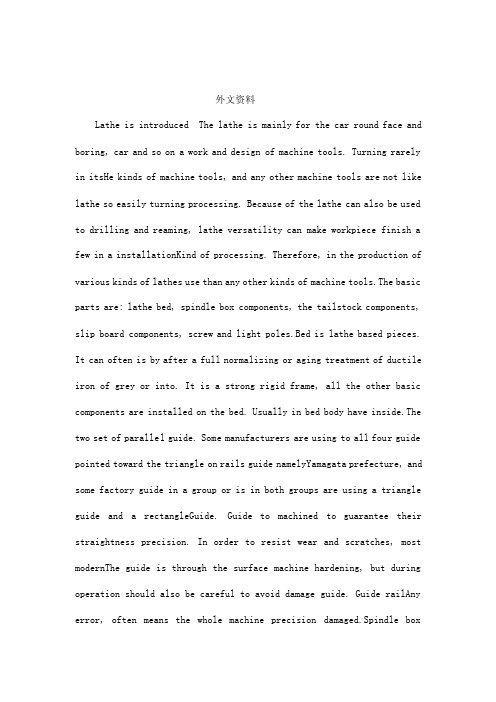
外文资料Lathe is introduced The lathe is mainly for the car round face and boring, car and so on a work and design of machine tools. Turning rarely in itsHe kinds of machine tools, and any other machine tools are not like lathe so easily turning processing. Because of the lathe can also be used to drilling and reaming, lathe versatility can make workpiece finish a few in a installationKind of processing. Therefore, in the production of various kinds of lathes use than any other kinds of machine tools.The basic parts are: lathe bed, spindle box components, the tailstock components, slip board components, screw and light poles.Bed is lathe based pieces. It can often is by after a full normalizing or aging treatment of ductile iron of grey or into. It is a strong rigid frame, all the other basic components are installed on the bed. Usually in bed body have inside.The two set of parallel guide. Some manufacturers are using to all four guide pointed toward the triangle on rails guide namelyYamagata prefecture, and some factory guide in a group or is in both groups are using a triangle guide and a rectangleGuide. Guide to machined to guarantee their straightness precision. In order to resist wear and scratches, most modernThe guide is through the surface machine hardening, but during operation should also be careful to avoid damage guide. Guide railAny error, often means the whole machine precision damaged.Spindle boxinstalled in the fixed position medial guide, usually left end of the bed. It provides power, and can make the workPieces of speed in turn. It basically consists of a installed in the hollow shaft and precision bearing a series of variable speed teethWheel similar to the truck gearbox together. Through the sliding gears, spindle can swim in the many kinds of rotating speed. mostlyCount lathe have 8 to 12 kinds of speed, general form. According to arrange series But in the modern machine just pull 2 ~ 4 handlesSo they can get all the speed. A growing trend is through the electrical or mechanical device withoutVariable.Due to the accuracy of machine tool depends largely on spindle, therefore, spindle structure size is larger, usually installedAfter the preloaded the heavy tapered roller bearings or ball bearings. Axis in a full-length through-hole throughout bar feeders, longThrough the hole by feeding. The size of the Lord when an important dimension is lathe, so when the work-piece must be when the principalThe materials, it confirms that can process the imum size of the blank bar feeders.The tailstock component mainly consists of three parts. The inside of the motherboard and lathe bed rails, can be in guide with the longitudinallyMobile. Floor has a can make whole the tailstock component clamping device at any position. The tailstock body installed in the endBoard, along some type of key slot in floor lateral movement, make the tailstock can and spindle box to the spindle is.The tailstock third part is the tailstock sleeve. It is a diameter usuallyat about 51 ~ 76mm 2 ~ 3 inchesThe steel hollow cylinder between. Through the handwheel and screw, the tailstock sleeve can in the tailstock body and move in a few longitudinal moveAn inch.The lathe with two dimensions specifications said. The first called lathe bed surface the largest machining diameter. This is in the latheCan the biggest diameter workpiece rotate. It is about two top attachment and guide rail of the distance of the nearest point two times. The second size is the imum distance between the two top. Lathe bed surface the largest machining diameter said on a latheThe biggest workpiece to turning diameter and the imum distance between the two top, said two top can be installed in betweenThe imum length of workpiece.Ordinary lathe is in the production of the most frequently used lathes type. They have all those front parts of SyracuseHeavy machine, and outside, all except for small knife tool sport has motor feed. They are usually the specifications: lathe bed face biggest process diameter for 305 ~ 610mm 12 to 24 inches; But, the bed surface the largest machining diameterAchieve 1270mm 50 inches and the distance between the two top 3658mm lathe to is not uncommon also. These carsBed most have scraps plate and a installed in internal cooling fluid circulation system. Small plain lathe bed face -- latheThe largest machining diameter usually less than 330mm 13 inches - is designed, and its bench-type lathe bed installation at workStations or on the cabinet.Although there are many USES, ordinary lathe is very useful, butthe machine tool and replacement and adjust to measure the work piece flowersFee much time, so they are not suitable for mass production application. Usually, their actual processing time less than its30% of total processing time. In addition, need skilled workers to operate ordinary lathe, the worker's salary highAnd difficult to hire. However, most of the time but operating workers spend on simply repeating adjustment and observation scraps process. Therefore, in order to reduce or totally not to hire this kind of skilled workers, hex lathe, threaded processing lathe and otherTypes of semi-automatic and automatic lathe has well developed, and has been widely applied in production.车床介绍车床主要是为了进行车外圆、车端面和镗孔等项工作而设计的机床。
机械类数控外文翻译外文文献英文文献数控.doc

Numerical ControlOne of the most fundamental concepts in the area of advanced manufacturing technologies is numerical control (NC).Prior to the advent of NC, all machine tools were manual operated and controlled. Among the many limitations associated with manual control machine tools, perhaps none is more prominent than the limitation of operator skills. With manual control, the quality of the product is directly related to and limited to the skills of the operator . Numerical control represents the first major step away from human control of machine tools.Numerical control means the control of machine tools and other manufacturing systems though the use of prerecorded, written symbolic instructions. Rather than operating a machine tool, an NC technician writes a program that issues operational instructions to the machine tool, For a machine tool to be numerically controlled , it must be interfaced with a device for accepting and decoding the p2ogrammed instructions, known as a reader.Numerical control was developed to overcome the limitation of human operator , and it has done so . Numerical control machines are more accurate than manually operated machines , they can produce parts more uniformly , they are faster, and the long-run tooling costs are lower . The development of NC led to the development of several other innovations in manufacturing technology:1.Electrical discharge machining.ser cutting.3.Electron beam welding.Numerical control has also made machine tools more versatile than their manually operated predecessors. An NC machine tool can automatically produce a wide variety of par4s , each involving an assortment of undertake the production of products that would not have been feasible from an economic perspective using manually controlled machine tools and processes.Like so many advanced technologies , NC was born in the laboratories of the Massachusetts Institute of Technology . The concept of NC was developed in the early 1950s with funding provided by the U.S Air Force .In its earliest stages , NC machines were able to make straight cuts efficiently and effectively.However ,curved paths were a problem because the machine tool had to be programmed to undertake a series of horizontal and vertical steps to produce a curve. The shorter is the straight lines making up the step ,the smoother is 4he curve . Each line segment in the steps had to be calculated.This problem led to the development in 1959 of the Automatically Programmed Tools (APT) language for NC that uses statements similar to English language to define the part geometry, describe the cutting tool configuration, and specify the necessary motions. The development of the APT language was a major step forward in the further development of NC technology. The original NC system were vastly different from those used punched paper , which was later to replaced by magnetic plastic tape .A tape reader was used to interpret the instructions written on the tape for the machine .Together, all /f this represented giant step forward in the control of machine tools . However ,there were a number of problems with NC at this point in its development.A major problem was the fragility of the punched paper tape medium . It was common for the paper containing the programmed instructions to break or tear during a machining process, This problem was exacerbated by the fact that each successive time a part was produced on a machine tool, the paper tape carrying the programmed instructions had to rerun thought the reader . If it was necessary to produce 100 copies of a given part , it was also necessary to run the paper tape thought the reader 100 separate times . Fragile paper tapes simply could not withstand the rigors of shop floor environment and this kind of repeated use.This led to the development of a special magnetic tape . Whereas the paper tape carried the programmed instructions as a series of holes punched in the tape , theThis most important of these was that it was difficult or impossible to change the instructions entered on the tape . To make even the most minor adjustments in a program of instructions, it was necessary to interrupt machining operations and make a new tape. It was also still necessary to run the tape thought the reader as many times as there were parts to be produced . Fortunately, computer technology become a reality and soon solved the problems of NC, associated with punched paper and plastic tape.The development of a concept known as numerical control (DNC) solve the paper and plastic tape problems associated with numerical control by simply eliminating tape as the medium for carrying the programmed instructions . In direct numerical control, machine tools are tied, via a data transmission link, to a host computer and fed to the machine tool as needed via the data transmission linkage. Direct numerical control represented a major step forward over punched tape and plastic tape. However ,it is subject to the same limitation as all technologies that depend on a host computer. When the host computer goes down , the machine tools also experience down time . This problem led to the development of computer numerical control.The development of the microprocessor allowed for the development of programmable logic controllers (PLC) and microcomputers . These two technologies allowed for the development of computer numerical control (CNC).With CNC , each machine tool has a PLC or a microcomputer that serves the same purpose. This allows programs to be input and stored at each individual machine tool. CNC solved the problems associated downtime of the host computer , but it introduced another problem known as data management . The same program might be loaded on ten different microcomputers with no communication among them. This problem is in the process of being solved by local area networks that connectDigital Signal ProcessorsThere are numerous situations where analog signals to be processed in many ways, like filtering and spectral analysis , Designing analog hardware to perform these functions is possible but has become less and practical, due to increased performance requirements, flexibility needs , and the need to cut down on development/testing time .It is in other words difficult pm design analog hardware analysis of signals.The act of sampling an signal into thehat are specialised for embedded signal processing operations , and such a processor is called a DSP, which stands for Digital Signal Processor . Today there are hundreds of DSP families from as many manufacturers, each one designed for a particular price/performance/usage group. Many of the largest manufacturers, like Texas Instruments and Motorola, offer both specialised DSP’s for certain fields like motor-control or modems ,and general high-performance DSP’s that can perform broad ranges of processingtasks. Development kits an` software are also available , and there are companies making software development tools for DSP’s that allows the programmer to implement complex processing algorithms using simple “drag ‘n’ drop” methodologies.DSP’s more or less fall into t wo categories depending on the underlying architecture-fixed-point and floating-point. The fixed-point devices generally operate on 16-bit words, while the floating-point devices operate on 32-40 bits floating-point words. Needless to say , the fixed-point devices are generally cheaper . Another important architectural difference is that fixed-point processors tend to have an accumulator architecture, with only one “general purpose” register , making them quite tricky to program and more importantly ,making C-compilers inherently inefficient. Floating-point DSP’s behave more like common general-purpose CPU’s ,with register-files.There are thousands of different DSP’s on the market, and it is difficult task finding the most suitable DSP for a project. The best way is probably to set up a constraint and wishlist, and try to compare the processors from the biggest manufacturers against it.The “big four” manufacturers of DSPs: Texas Instruments, Motorola, AT&T and Analog Devices.Digital-to-analog conversionIn the case of MPEG-Audio decoding , digital compressed data is fed into the DSP which performs the decoding , then the decoded samples have to be converted back into the analog domain , and the resulting signal fed an amplifier or similar audio equipment . This digital to analog conversion (DCA) is performed by a circuit with the same name & Different DCA’s provide different performance and quality , as measured by THD (Total harmonic distortion ), number of bits, linearity , speed, filter characteristics and other things.The TMS320 family DQP of Texas InstrumentsThe TLS320family consists of fixed-point, floating-point, multiprocessor digital signal processors (D[Ps) , and foxed-point DSP controllers. TMS320 DSP have an architecture designed specifically for real-time signal processing . The’ F/C240 is a number of the’C2000DSP platform , and is optimized for control applications. The’C24x series of DSP controllers combines this real-time processing capability with controller peripherals to create an ideal solution for control system applications. The following characteristics make the TMS320 family the right choice for a wide range of processing applications:--- Very flexible instruction set--- Inherent operational flexibility---High-speed performance---Innovative parallel architecture---Cost effectivenessDevices within a generation of the TMS320 family have the same CPU structure but different on-chip memory and peripheral configurations. Spin-off devices use new combinations of On-chip memory and peripherals to satisfy a wide range of needs in the worldwide electronics market. By integrating memory and peripherals onto a single chip , TMS320 devices reduce system costs and save circuit board space.The 16-bit ,fixed-point DSP core of the ‘C24x devices provides analog designers a digital solution that does not sacrifice the precision and performance of their system performance can be enhanced through the use of advanced control algorithms for techniquessuch as adaptive control , Kalman filtering , and state control. The ‘C24x DSP controller offer reliability and programmability . Analog control systems, on the other hand ,are hardwired solutions and can experience performance degradation due to aging , component tolerance, and drift.The high-speed central processing unit (CPU) allows the digital designer to process algorithms in real time rather than approximate results with look-up tables. The instruction set of these DSP controllers, which incorporates both signal processing instructions and general-purpose control functions, coupled with the extensive development time and provides the same ease of use as traditional 8-and 16-bit microcontrollers. The instruction set also allows you to retain your software investment when moving from other general-purp ose‘C2xx generation ,source code compatible with the’C2x generation , and upwardly source code compatible with the ‘C5x generation of DSPs from Texas Instruments.The ‘C24x architecture is also well-suited for processing control signals. It uses a 16-bit word length along with 32-bit registers for storing intermediate results, and has two hardware shifters available to scale numbers independently of the CPU . This combination minimizes quantization and truncation errors, and increases p2ocessing power for additional functions. Such functions might include a notch filter that could cancel mechanical resonances in a system or an estimation technique that could eliminate state sensors in a system.The ‘C24xDSP controllers take advantage of an set of peripheral functions that allow Texas Instruments to quickly configure various series members for different price/ performance points or for application optimization.This library of both digital and mixed-signal peripherals includes:---Timers---Serial communications ports (SCI,SPI)---Analog-to-digital converters(ADC)---Event manager---System protection, such as low-voltage and watchdog timerThe DSP controller peripheral library is continually growing and changing to suit the of tomorrow’s embedded control marke tplace.The TMS320F/C240 is the first standard device introduced in the ‘24x series of DSP controllers. It sets the standard for a single-chip digital motor controller. The ‘240 can execute 20 MIPS. Almost all instructions are executed in a simple cycle of 50 ns . This high performance allows real-time execution of very comple8 control algorithms, such as adaptive control and Kalman filters. Very high sampling rates can also be used to minimize loop delays.The ‘ 240 has the architectural features necessary for high-speed signal processing and digital control functions, and it has the peripherals needed to provide a single-chip solution for motor control applications. The ‘240 is manufactured using submicron CMOS technology, achieving a log power dissipation rating . Also included are several power-down modes for further power savings. Some applications that benefit from the advanced processing power of the ‘240 include:---Industrial motor drives---Power inverters and controllers---Automotive systems, such as electronic power steering , antilock brakes, and climatecontrol---Appliance and HV AC blower/ compressor motor controls---Printers, copiers, and other office products---Tape drives, magnetic optical drives, and other mass storage products---Robotic and CNC milling machinesTo function as a system manager, a DSP must have robust on-chip I/O and other peripherals. The event manager of the ‘240 is unlike any other available on a DSP . This application-optimized peripheral unit , coupled with the high performance DSP core, enables the use of advanced control techniques for high-precision and high-efficiency full variable-speed control of all motor types. Include in the event manager are special pulse-width modulation (PWM) generation functions, such as a programmable dead-band function and a space vector PWM state machine for 3-phase motors that provides state-of-the-art maximum efficiency in the switching of power transistors.There independent up down timers, each with it’s own compare register, suppo rt the generation of asymmetric (noncentered) as well as symmetric (centered) PWM waveforms.Open-Loop and Closed-Loop ControlOpen-loop Control SystemsThe word automatic implies that there is a certain amount of sophistication in the control system. By automatic, it generally means That the system is usually capable of adapting to a variety of operating conditions and is able to respond to a class of inputs satisfactorily . However , not any type of control system has the automatic feature. Usually , the automatic feature is achieved by feed.g the feedback structure, it is called an open-loop system , which is the simplest and most economical type of control system.inaccuracy lies in the fact that one may not know the exact characteristics of the further ,which has a definite bearing on the indoor temperature. This alco points to an important disadvantage of the performance of an open -loop control system, in that the system is not capable of adapting to variations in environmental conitions or to external disturbances. In the case of the furnace control, perhaps an experienced person can provide control for a certain desired temperature in the house; but id the doors or windows are opened or closed intermittently during the operating period, the final temperature inside the house will not be accurately regulated by the open-loop control.An electric washing machine is another typical example of an open-loop system , because the amount of wash time is entirely determined by the judgment and estimation of the human operator . A true automatic electric washing machine should have the means of checking the cleanliness of the clothes continuously and turn itsedt off when the desired degised of cleanliness is reached.Closed-Loop Control SystemsWhat is missing in the open-loop control system for more accurate and more adaptable control is a link or feedback from the output to the input of the system . In order to obtain more accurate bontrol, the controlled signal c(t) must be fed back and compared with the reference input , and an actuating signal proportional to the difference of the output and the input must be sent through the system to correct the error. A system with one or more feedback pat(s like that just described is called a closed-loop system. human being are probably the most complex and sophisticated feedback control system in existence. A humanbeing may be considered to be a control system with many inputs and outputs, capable of carrying out highly complex operations.To illustrate the human being as a feedback control system , let us consider that the objective is to reach for an object on aperform the task. The eyes serve as a sensing device which feeds back continuously the position of the hand . The distance between the hand and the object is the error , which is eventually brought to zero as the hand reacher the object. This is a typical example of closed-loop control. However , if one is told to reach for the object and then is blindolded, one can only reach toward the object by estimating its exact position. It isAs anther illustrative example of a closed-loop control system, shows the block diagram of the rudder control system ofThe basic alements and the bloca diagram of a closed-loop control system are shown in fig. In general , the configuration of a feedback control system may not be constrained to that of fig & . In complex systems there may be multitude of feedback loops and element blocks.数控在先进制造技术领域最根本的观念之一是数控(NC)。
数控机床刀具设计论文中英文资料外文翻译文献综述
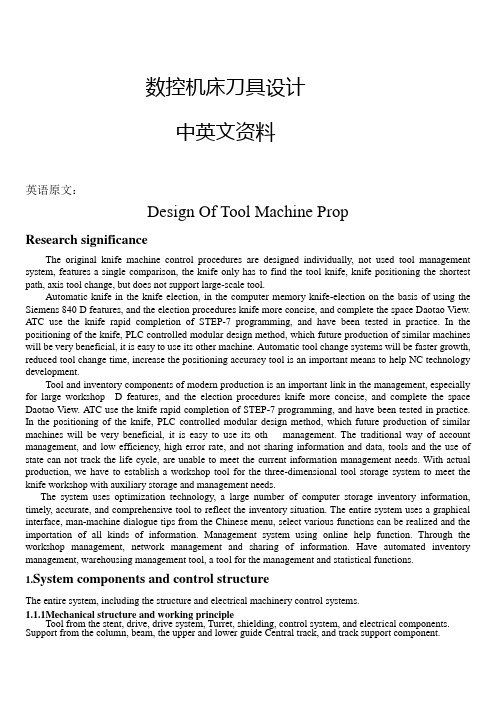
数控机床刀具设计中英文资料英语原文:Design Of Tool Machine PropResearch significanceThe original knife machine control procedures are designed individually, not used tool management system, features a single comparison, the knife only has to find the tool knife, knife positioning the shortest path, axis tool change, but does not support large-scale tool.Automatic knife in the knife election, in the computer memory knife-election on the basis of using the Siemens 840 D features, and the election procedures knife more concise, and complete the space Daotao View. ATC use the knife rapid completion of STEP-7 programming, and have been tested in practice. In the positioning of the knife, PLC controlled modular design method, which future production of similar machines will be very beneficial, it is easy to use its other machine. Automatic tool change systems will be faster growth, reduced tool change time, increase the positioning accuracy tool is an important means to help NC technology development.Tool and inventory components of modern production is an important link in the management, especially for large workshop D features, and the election procedures knife more concise, and complete the space Daotao View. ATC use the knife rapid completion of STEP-7 programming, and have been tested in practice. In the positioning of the knife, PLC controlled modular design method, which future production of similar machines will be very beneficial, it is easy to use its oth management. The traditional way of account management, and low efficiency, high error rate, and not sharing information and data, tools and the use of state can not track the life cycle, are unable to meet the current information management needs. With actual production, we have to establish a workshop tool for the three-dimensional tool storage system to meet the knife workshop with auxiliary storage and management needs.The system uses optimization technology, a large number of computer storage inventory information, timely, accurate, and comprehensive tool to reflect the inventory situation. The entire system uses a graphical interface, man-machine dialogue tips from the Chinese menu, select various functions can be realized and the importation of all kinds of information. Management system using online help function. Through the workshop management, network management and sharing of information. Have automated inventory management, warehousing management tool, a tool for the management and statistical functions.1.System components and control structureThe entire system, including the structure and electrical machinery control systems.1.1.1Mechanical structure and working principleTool from the stent, drive, drive system, Turret, shielding, control system, and electrical components. Support from the column, beam, the upper and lower guide Central track, and track support component.1) Drive for the system chosen VVVF method. Cone used brake motors, with VVVF by Cycloid reducer through sprocket drive.2) Drag a variable frequency drive system and control technology. VVVF adopted, will speed drive shaft in the normal range adjustment to control the speed rotary turret to 5 ~ 30mm in, the drive shaft into two, two under through sprocket, the two profiled rollers Chain driven rotating shelves. Expansion chain adopted by the thread tight regulation swelling, swelling the regular way. - Conditi D features, and the election procedures knife more concise, and complete the space Daotao View. ATC use the knife rapid completion of STEP-7 programming, and have been tested in practice. In the positioning of the knife, PLC controlled modular design method, which future production of similar machines will be very beneficial, it is easy to use its at six other Des V oeux a knife, can be categorized with some of knife auxiliary equipment, such as bits, such as turning tools.1.1.2.Electrical Control SystemThis tool storage systems is the main electrical control their shelves for operational control and position control. Operational control equipment, including operation of the start of braking control. Position Control is the main location and address of the shelves for testing.1) Electric Transmission horizontal rotary tool storage systems are the mechanical movements are repeated short-term work system. And the run-time system needs some speed, speed transmission needs, the system will use VVVF method can be used simple structure, reliable operation of the motor and frequency inverter.2) Control of the system is divided into two kinds of manual control and automatic control, manual control as a general reserve and debugging methods of work; ways to the system control computer (IPC) and the control unit (inverter contactor , etc.) consisting of a control system.3) location and positioning accuracy of the system automatically identify the site and location using a detection device tion, timely, accurate, and comprehensive tool to reflect the inventory situation. The entire system uses a graphical interface, man-machine dialogue tips from the Chinese menu, select various functions can be realized and the importation of all kinds of information. Management system using online help function. Through the workshop management, network management and sharing of information. Have automated inventory management, warehousing management tool, a tool for the management and statistical fu as proximity switches, relays through the plate-point isolation and the number plate recorded close to the switching signal acquisition and operation of Hutchison with a Optimal Path addressable identify the current location and shelves of the purpose of the shelf location. In order to enable a more accurate positioning system, adopted two photoelectric switches, to detect the two shelves of the two films.1.2.The functions of the knifeknife The is the role of reserves a certain number of tools, machine tool spindle in hand to achieve the fungibility a disc sc knife in the library with discoid knife, cutting tool along See how vertical arrangement (including radial and axial from knife from knife), along See how radial array into acute or arranged in the form of the knife. Simple, compact, more applications, but are ring-cutter, low utilization of space. Figure 2.7 a) to c). D features, and the election procedures knife more concise, and complete the space Daotao View. ATC use the knife rapid completion of STEP-7 programming, and have been tested in practice. In the positioning of the knife, PLC controlled modular design method, which future production of similar machines will be very beneficial, it is easy to use its. If the knife cutter knife is the type of library, the chain knives, and other means, in the form of the knifeand capacity according to the Machine Tool to determine the scope of the process.s, but are ring-cutter, low utilization of space. Figure 2.7 a) to c). D features, and the election procedures knife more concise, and com mon typesThe knife is a tool storage devices, the common knife mainly in the following forms:(1) the turret knifeIncluding the first level turret vertical turret and the first two, see Figure 2.6 a) and b):(2) the disc cutterDisc knife in the library with discoid knife, cutting tool along See how vertical arrangement (includingradial and axial from knife from knife), along See how radial array into acute or arranged in the form of theknife. Simple, compact, more applications, but are ring-cutter, low utilization of space. Figure 2.7 a) to c).D features, and the election procedures knife more concise, and complete the space Daotao View. ATC use theknife rapid completion of STEP-7 programming, and have been tested in practice. In the positioning of theknife, PLC controlled modular design method, which future production of similar machines will be verybeneficial, it is easy to use its. If the knife storage capacity must be increased to increase the diameter of theknife, then the moment of inertia also increased correspondingly, the election campaign long knife. Toolnumber not more than 32 general. Cutter was multi-loop order of the space utilization knife, but inevitablygiven the knife from complex institutions, applicable to the restricted space Machine Tool storage capacity andmore occasions. Two-disc structure is two smaller capacity knife on both sides of the sub-spindle place, morecompact layout, the number ofapply to small and medium-sizedprocessing center.(3) the chain knife Includingsingle-and multi-ring chain ringchain, chain link can take many forms change, see Figure 2.8 a) to c), the basic structure shown in Figure 2. 8 doFeatures: knife apply to the larger capacity of the occasion, the space of the small number of generally applicable to the tool in the 30-120. Only increase the length of the chain tool will increase the number should not be increased circumferential speed of its moment of inertia of the knife does not increase the disc as large.(4) linear combination knife and the knife libraryThe linear knife simple structure in Figure 2.9, tool single order, the capacity of small knife, used for CNC lathe and drill press on. Because the location of fixed knife, ATC completed action by the spindle without manipulator. The cutter knife is generally the turret combination turret with a combination of the disc cutter knife and the chain combination. Every single knife the knife certificates of smaller, faster tool change. There are also some intensive drum wheel, and the lattice-type magazine for the knife, the knife-intensive though.Small footprint, but because of structural constraints, basically not used for single processing center, the concentration used for FMS for the knife system.1.4 Tool storage capacityTool storage capacity of the first to consider the needs of processing, from the use of point of view,generally 10 to 40 knives, knife will be the utilization of the high, and the structure is compact.1.5 Tool options(1) choose to order processing tool according to the order, followed Add to the knife every knife in the Block. Each tool change, the order of rotation of a cutter knife on location, and remove the need knives, has been used by the cutter knife can be returned to the original Block, can also order Add Block, a knife. However, as the knife in the tool in different processes can not be repeated use of the knife must increase the capacity and lower utilization rate.(2) most of the arbitrary choice of the current system of using arbitrary NC election knives, divided into Daotao coding, coding and memory-cutter, three. Daotao coding tool code or knives or Daotao need to install the code used to identify, in accordance with the general principle of binary coding coding. Tool knife election coding method uses a special knife handle structure, and each of the coding tool. Each of the tool has its own code, thereby cutting tool can be in different processes repeatedly used, not to replace the tool back at the original knife, the knife capacity can be reduced accordingly. Memory-election this paper knife, in this way can knives and knife in the position corresponding to the Daotao memory of the PLC in the NC system, no matter which tool on the Inner knife, tool information is always there in mind, PLC . On the knife with position detection devices, will be the location of each Daotao. This tool can be removed and sent back to arbitrary. On the knife is also a mechanical origin, every election, the nearest knife selection.1.6.Control of the knife(1) the knife as a system to control the positioning axis. In the ladder diagram in accordance with the instructions for computing T code comparison of the output angle and speed of instructions to the knife the knife servo drive servo motor. Tool storage capacity, rotation speed, and / deceleration time, and other system parameters can be set in such a manner free from any outside influence positioning accurate and reliable but the cost is higher.(2) knife from the hydraulic motor drives, fast / slow the points, with proximity switches count and positioning. In comparison ladder diagram of the current storage system knife (knife spindle) and goals knife (pre-knife) and computing, then output rotation instructions, judging by the shortest path rotation in place. This approach requires sufficient hydraulic power and electromagnetic valve knife the rotational speed can be adjusted through the throttle. But over time may be oily hydraulic, oil temperature and environmental factors impact the change in velocity and accuracy. Not generally used in large and medium-sized machine tool change frequently.(3) the knife from AC asynchronous motor driven cam mechanism (Markov institutions), with proximity switches count, which means stable operation, and generally accurate and reliable positioning cam used in conjunction with a mechanical hand, ATC fast-positioning.2. ATC, the main types, characteristics, and the scope of application2.1 Auto Rotary ToolRotary Tool automatically on the use of CNC machine tool is a simpleinstallation of automatic tool change, the Quartet and 47.60 Turret Tool various forms, such as rotary turret were installed on four, six or more of the Tool , NCinstructions by ATC. Rotary Tool has two vertical and horizontal, relatively simple structure, applicable to economic CNC lathe.Rotary Tool in the structure must have good strength and stiffness, resistance to bear rough Cutting Tool in the cutting force and reduce the role of deformation and improve processing accuracy. Rotating Tool to choose reliable positioning programme structure and reasonable position, in order to ensure that each rotary turret to a higher position after repeated positioning accuracy (typically 0.001 to 0.005mm). Figure 2.1 shows the spiral movements of the Quartet Turret.Auto Rotary Tool in the simplest of ATC, is 180 º rotary ATC devices, as shown in Figure 2.2 ATC instructions received, the machine control system put ATC spindle control to the designated location at the same time, the tool movement to the appropriate location, ATC, with the rotary axis and at the same time, the knives matching tool; drawbars from Spindle Cutting Tools rip, ATC, will be the tool from their position removed; ATC, 180 º rotary tool spindle and the tool and tool away; ATC, the Rotary At the same time, thetool refocusing its position to accept Spindle removed from the cutting tool; Next, ATC, will be replaced with the cutter knives were unloaded into the spindle and tool: Finally, back to the original ATC, "standby" position. At this point, ATC completed procedures to continue to run. This ATC, the main advantage of simple structure,the less movement, fast tool change. The main disadvantage is that knives must be kept in parallel with the axis of the plane, and after the home side compared to the tool, chip and liquid-cutting knife into the folder, it is necessary to the tool plus protection. Cone knife folder on the chip will cause ATC error, or even damage knife folders, and the possibility of spindle. Some processing centre at the transfer, and the tool side. When the ATC command is called, the transfer-cutter knives will be removed, the machine go forward, and positioning with the ATC, in line with the position. 180 º "Rotary ATC devices can be used horizontal machine, can also be used for vertical machining centers.2. 2 ATC head-turret installedWith rotating CNC machine tool often used such ATC devices, with a few turret head spindle, each with a spindle on both knives, the first tower interim process can be automatic tool change-realization. The advantage is simple structure, tool change time is short, only about 2 s. However, due to spatial constraints, the number of spindle can not be too much, usually only apply to processes less, not to high precision machine tools, such as the NC drill, such as CNC milling machine. In recent years there has been a mechanical hand and the turret head with a knife for the automatic tool change ATC devices, as shown in Figure 2.3. It is in fact a turret head ATC, and the knife-ATC device combination. The principle is as follows:5 turret on the first two tool spindle 3 and 4, when using the tool spindle 4 processing tool, the manipulator 2 will be the next step to the need for the tool does not work on the tool spindle 3 until after the completion of this process , the first rotary turret 180 º, ATC completed. ATC most of their time and processing time coincidence, the only real tool change time turret transposition of the first time, this approach mainly used for ATC and NC NC drilling file bed.2. 3.Daidao system for the automatic tool changeFigure 2.4 shows the knife and the whole machine tool CNC machine tools for the appearance of Fig. Figure 2.5 shows the knife and split-type machine to the appearance of CNC machine tool plans.At this point, knife storage capacity, a heavier tool can, and often additional transport unit to complete the knife between the spindle and cutting tool transport.Daidao the knife from the ATC, the election knives, automatic loading and unloading machine tool and tool exchange institutions (manipulator), composed of four parts, used widely.Tool Automatic Tool Change When CNC tool code and the code in line with directives of the tool selected, the rotary cutter knives will be sent to the ATC position, waiting to grab manipulator. Random knife election is the advantage of the cutter knife in the order has nothing to do with the processing sequence, the same tool can be used repeatedly. Therefore, the relatively small number of knives, knife the corresponding smaller. Random elections knife on the tool must be coded to identify. There are three main coding.1. Tool coding. Adopt special knife handle structure coding, the drawbars on the knife handle back-endpackages such as spacing of the coding part of the lock-nut fixed. Coding diameter ring diameter of a size two,respectively, said that binary "1" and "0" to the two rings are different, can be a series of code. For example, there are six small diameter of the ring can be made to distinguish between 63 (26-1 = 63) of the coding tool. All of 0 normally not allowed to use the the manipulator system, the whole process more complicated ATC. We must first used in the processing of all installed in the standard tool on the knife handle in the machine outside the pre-size, according to a certain way Add to the knife. ATC, selected first in the knife knife, and then from ATC, from the knife from the knife or spindle, exchange, the new knife into the spindle, the old knife back into the knife.ATC, as the former two knives to accommodate a limited number can not be too many, can not meet the needs of complex parts machining, CNC machine tool Automatic Tool Change Daidao the use of the automatic tool change devices. The knife has more capacity, both installed in the spindle box side or above. As for the automatic tool change Daidao device CNC machine tool spindle box only a spindle, spindle components to high stiffness to meet the machining requirements. The number of establishments in larger knife, which can meet the more complex parts of the machining processes, significantly improving productivity. Daidao system for the automatic tool change applied to drilling centres and CNC machining centers. The comparison drawn Daidao automatic tool change system is the most promising.3.PLC control of the knife random mode of election3. 1Common methods of automatic election knifeAutomatic control of the knife CNC refers to the system after the implementation of user instructions onthe knife library automation process, including the process to find knives and automatic tool change [(63,71]. CNC Machining Center device (CNC) directive issued by the election knife , a knife, the tool required to take the knife position, said the election automatic knife. automatically elected knife There are two ways: randomsequence election knives and knife election method.3.1.1 order election knifeTool Selection order is the process tool according to the sequence of the insert knife, the use of knives in order to take place, used knives back at the original knife, can also order Add Block, a knife. In this way, no need Tool identification devices, and drive control is a relatively simple, reliable and can be used directly from the points of the knife machinery to achieve. But the knives in each of the tool in different processes can not be reused, if the tool is installed in accordance with the order of the knife, there will be serious consequences. Theneed to increase the number of knives and knife the capacity of the tool and reduce the utilization of the knife.3.1.2Random election knifeRandom election under the knife is arbitrary instructions to select the required tools, then there must be tool identification devices. Tool knife in the library do not have the processing in accordance with the order of the workpiece can be arbitrary storage. Each of the tool (or knife blocks) are for a code, automatic tool change, the rotary cutter, every tool have been the "tool identification device" acceptable identification. When CNCtool code and the code in line with directives of the tool selected, the rotary cutter knives will be sent to the ATC position, waiting to grab manipulator. Random knife election is the advantage of the cutter knife in the order has nothing to do with the processing sequence, the same tool can be used repeatedly. Therefore, the relatively small number of knives, knife the corresponding smaller. Random elections knife on the tool must be coded to identify. There are three main coding.1. Tool coding. Adopt special knife handle structure coding, the drawbars on the knife handle back-end packages such as spacing of the coding part of the lock-nut fixed. Coding diameter ring diameter of a size two, respectively, said that binary "1" and "0" to the two rings are different, can be a series of code. For example, there are six small diameter of the ring can be made to distinguish between 63 (26-1 = 63) of the coding tool. All of 0 normally not allowed to use the code, to avoid the cutter knife Block did not confuse the situation.2. Knife Block coding. On the knife Block coding, coding tool, and tool into line with the number of knives in the Block. ATC knife when the rotation, so that each knife seats followed through knowledge knife, knife found blocks, knives stopped the rotation. At this time there is no knife handle encoding part of the knife handle simplified.3. Annex coding methods. This style of coding keys, coded cards, coding and coding-disc, which is the most widely used coding keys. First to knives are attached to a tool of the show wrapped coding keys, and when the cutter knife to the store at knife in, so put the number of keys to remember knife Block Road, will be inserted into key to the coding Block next to the key hole in the seat for the knife to the numbers. ConclusionFocused on in today's manufacturing environment tool storage and management of new models and methods, practical application of good results in systems integration and optimization, and other aspects of operations will be further explored, so that it has a higher theoretical and practical level.译文:机床刀具设计课题研究意义机床原来的刀库控制程序是单独设计的,没有采用刀具管理系统,功能也比较单一,只实现了刀库刀具的找刀、刀库最短路径定位、主轴换刀,而且不支持大型刀具。
数控车床自动回转刀架英文文献以及翻译
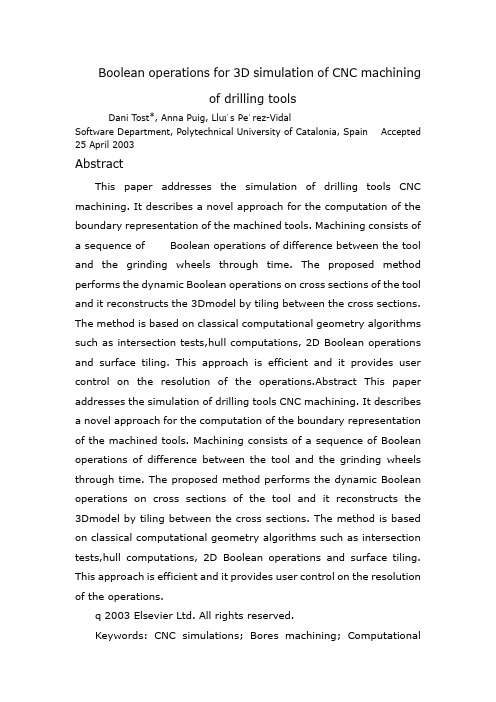
Boolean operations for 3D simulation of CNC machiningof drilling toolsDani Tost*, Anna Puig, Lluı´s Pe´rez-VidalSoftware Department, Polytechnical University of Catalonia, Spain Accepted 25 April 2003AbstractThis paper addresses the simulation of drilling tools CNC machining. It describes a novel approach for the computation of the boundary representation of the machined tools. Machining consists of a sequence of Boolean operations of difference between the tool and the grinding wheels through time. The proposed method performs the dynamic Boolean operations on cross sections of the tool and it reconstructs the 3Dmodel by tiling between the cross sections. The method is based on classical computational geometry algorithms such as intersection tests,hull computations, 2D Boolean operations and surface tiling. This approach is efficient and it provides user control on the resolution of the operations.Abstract This paper addresses the simulation of drilling tools CNC machining. It describes a novel approach for the computation of the boundary representation of the machined tools. Machining consists of a sequence of Boolean operations of difference between the tool and the grinding wheels through time. The proposed method performs the dynamic Boolean operations on cross sections of the tool and it reconstructs the 3Dmodel by tiling between the cross sections. The method is based on classical computational geometry algorithms such as intersection tests,hull computations, 2D Boolean operations and surface tiling. This approach is efficient and it provides user control on the resolution of the operations.q 2003 Elsevier Ltd. All rights reserved.Keywords: CNC simulations; Bores machining; Computationalgeometry; Boolean operations; Surface tiling1. IntroductionMost of the research on CNC in CAD is centered on theautomatic computation of tool paths [5,13]. Given a final tool design, the optimal trajectories of the tool and the grinding wheels must be computed yielding as final result the CNC code. Machining simulation and verification hasexactly the opposite goal: to calculate the tool starting from the CNC code and from a geometrical model of the machine, the wheels and the tool before machining. This simulation has three main applications [6]. First, it detects eventual collisions between the tool or any of the grinding wheels and the rest of the machine. It is important to avoid collisions because serious damages to the machines can follow. Next, simulation provides a means of visually verifying the efficiency of the trajectories, which may result in faster and cheaper processes. Finally, the simulation allows users to check if the surface of the resulting tool is effectively the desired one. In the routine practice of machining, experienced operators have enough skills to imagine the tool final shape by only reading the CNC code.However, they are generally not able to do so with new or non-standard designs. Therefore, the use of a simulation system decreases considerably the tool production cost because it avoids the trial and error process on the real machine with costly materials that is otherwise necessary.This paper addresses a particular type of CNC machining simulation: the grinding of bores and cutters. Conventional CAD systems do not provide a means of realizing this type of simulations and specific applications are needed. Until recently, most of thesimulation applications dealt only with the machining of 2D cross-sections of the tools and they were restricted to the main fluting operation [3]. Three dimensional applications are rather recent [4,23]. They provide a machining simulation for specific 5-axes machines and they are not applicable to general movements. This paper presents a novel approach for the computation of the external shape of the tools through a sequence of coordinated movements of the tool and the wheels on machines of up to 6-axes. The proposed method reduces the 3D problem to 2D dynamic Boolean operations followed by a surface tiling. The 2D solution involves different techniques of planar computational geometry: from intersections to hull computations.The paper is structured as follows. In Section 2 we review previous approaches on machining simulations.Section 3 describes briefly the contour conditions of the simulation. Finally, Section 4 describes the computation of Boolean operations and the results of the implementation are shown in Section 5.2. Previous workMachining can be considered a dynamic Boolean operation of difference between the grinding wheel and the tool. It is dynamic, because both the tool and the wheels move along time through rotations and translations.The Vector Cut [8,10], is probably the most referenced numerical control simulation method. It is an approximate solution that represents the frontier as a set of points and normal vectors that will be cut along the path of the grinding wheel. This method is effective for the simulation of sculptured surface polishing, but it is not extensible to complex motions of the tool and/or the grinding wheels. It is mainly useful to detect mistakes in the path suggestedby the presence of abnormally high or small cut vectors. Besides, except for the extension of Ref. [16], it does not yield directly a model of the bit to be machined.An alternative strategy for machining simulation consists of realizing a sequence of 3D static Boolean operations through time. The main drawback of this strategy is its high computational cost. According to Ref. [11], this is proportional to the number of discrete positions to the fourth. This puts it out of question, in practical terms.Another problem it shows is the granularity of the temporal discretization : it must be very fine if precision in the final tool is required. This means that very little material is cut off in each Boolean operation, and that may entail robustness problems in the computations. A possible method to avoid both problems is to discretize the initial tool model into a voxel or an octree model, [20], to perform all the sequence of Boolean operations on the discrete model and then reconstruct the machined surface, at the end. This approach benefits from the fact that the cost of discrete Boolean operations is much lower and the reconstruction phase at the end of the process is done as late as possible. This option requires the sequence of movements to be specified in terms of relative motion of the grinding wheel, while the tool and its discretization remain fixed. This prerequisite is not always valid and, in particular, it does not hold for the general case of 6-axes machines.Finally, another option taken into account is that of the computation of the volume swept by the tool and the grinding wheel in their motions. A geometric representation of this volume would allow performing only one Boolean difference operation between the two volumes. The main difficulty of this option is the computation of sweptvolumes. There are several references [1,2,21] on this subject, that contain methods generally applied in CAD for extrusions, collisiondetection, and other problems but none of them can be applied to the non-trivial case of simultaneous motion of the two solids in play.The strategy proposed herein overcomes the disadvantages of these methods. It consists of a double discretization of four dimensional space (3D þ time) that reduces the general problem to a sequence of 2D Boolean operations and 3D geometric reconstructions. This algorithm is fast and it provides user-control on simulation accuracy.3. Scene modelThere are different types of machine tools for the fabrication of bores and cutters. They share the same general structure but they differ in the number of degrees of freedom. The method proposed herein deals with machines up to six degrees of freedom. These machines have a static vertical axis (Z in Fig. 1 on which the grinding wheel set can move up and down. One tool is placed on a spindle (the toolholder), that may translate on three axes (X; Y and U) and rotate on two axes (W in relation to the wheel axis and A relative to its own axis). At the beginning of the process, a tool has a piecewise cylindrical or conical shape. Its final shape is the result of a sequence of machining operations consisting of simultaneous movements of the tool and the wheels. The wheel shape is also piecewise cylindrical or conical. It remains unchanged during the process.The machining process is divided into a set of operations, each one with a specific name in CNC jargon. Each operation is performed using a specific wheel. This information is written in the CNC file.Specifically, the main operations are (in their usual order):Fig. 1. 6-Axes machine tool.Fig. 2. Machining operations on a tool.* Fluting: performing the lateral helicoidal of straight grooves* Gashing: cuts in the tool head* Outer diameter sharpening: edge sharpening of the lateral grooves* End face sharpening: edge sharpening of the tool head cuts* Notching: direct cut in the tool head.Fig. 2 shows a real bore and it indicates the operations that have given its shape.Each operation performs several symmetrical cuts in the tool shape. The tool shown in Fig. 2, for instance, has three lateral grooves realized during the ‘Fluting’ operation. Each cut is performed through a sequence of movements. In the CNC code, each movement corresponds to a line instruction specifying the motion axes (X; Y;U; A; or W for the tool and Z for the wheel) along with the amount of rotation or translation to be performed for each edge.4. Machining simulation4.1. OverviewOur approach uses the fact that the tools have a tubular shape. It consists of discretizing the tool in axial sections, performing the machining operations on these crosssections and finally, reconstructing the surface of the tool by tiling between cross-sections. Before machining, the cross-sections are circles. Afterwards, they have a complex shape that may even have been split into separate connected shells at the tool end.The movements are divided into blocks, each one corresponding to an CNC operation or even to one cut within an operation. The machining process is performed sequentially for each block. Therefore, as many intermediate models are created as instruction blocks exist. The initial tool is taken as input of the first machining process. Theresulting tool is used in the second block processing and so on. The surface reconstruction step can be performed on any of these intermediate models or, alternatively only on the last one.Therefore, the simulation process of each instructions block is composed of two steps:* A 2D Boolean operation process, that receives as input: (i) the tool representation, (ii) the machining wheel representation, (iii) a list of movements and that gives as output a new representation of the tool cross-sections.* A tiling process that completes the tool representation with the triangulation between contours.The second step, surface tiling, is a classical subject in computer graphics [14]. It consists of two related problems: (i) establishing correspondences between contours (branching problem) and (ii) searching correspondent vertices to form tiles (correspondence problem). Several solutions have been published to solve both problems based on minimizing the distance between successive contours [7,17] and interpolating in between contours [12]. The method used herein is an extension of these algorithms that adds to these criteria the constraint of tiling between segments of the contour corresponding to the same machining operation. This extension is described in depth in Ref. [22].4.2. Machining of the tool cross-sectionsThe computation of the new shape of tool cross section consists of three steps:* Computation through time of the intersections of the wheel cross sections and the external contour of the tool section. Bothsections are circular and, due to their relative orientation, their intersection is a segment. Therefore, the result of this step is a set of segments.* Calculation of the hulls of the segments set. These hulls are polygonal approximations of wheel cuts on the tool section.* Reconstruction of the tool cross section contour given its original shape and the hull curves.The pseudo-code algorithm below illustrates this process. Let st be the tool cross section at the beginning of the process, where the wheel and ml the movements list. The wheel is discretized into a set of circular cross-sections switch (procedures FirtSectWheel and NextSectWheel). The movement of switch and st is decomposed into a a set of successive positions (inner loop). For each position, the intersection between sw and st is computed in the procedure InterSect. If there is intersection, then the corresponding segment segm is stored in the segments list seglist. Then, the geometry of st, sw and seglist is updated to next positions in the procedure UpdateGeom. The position of st is reset at its initial location for each new wheel section. After all the wheel sections have been processed, the hulls of the segment list are computed in CompHulls and then clipped against the initial contour of st with the procedure Reconstruct.procedure CrossSection Machining(st: tSection,wh: tWheel, ml: tMovList)varsw: tSectionsegm: tSegmentseglist: tSegmentListhulls: tHullListfvarInitSegList(seglist)sw U FirstSectWheel (wh)while ValidSection(sw) doendo f mov U FALSEwhile : endo f mov doInterSect(st,sw, &segm, &status)if status ! InsertSegment(segm, seglist) endifUpdateGeom(ml, &st, &sw, &seglist, &endo fmov)endwhilesw U NextSectWheel(wh,sw)ResetToolPosition(&st)endwhileCompHulls(slist, &hulls)Reconstruct(hulls, &st)fprocedure4.2.1. Updating geometryEach movement instruction is realized at constant speed. Therefore, a movement can be decomposed into n constant intervals of translation in X; Y; Z and U along with rotation in W and A : δA=ΔA/n,δW=ΔW/n,δX=ΔX/n,δY=ΔY/n,δU=ΔU/n andδZ=ΔZ/n.As mentioned in Section 3, a line movement can be composed of several simultaneous instructions. Most of the tool movements are composed of translations and axial rotations, which are independent. Therefore, the order in which the update of each movement is done is irrelevant. However for conical tools with a round end called ‘ball nose’, simultaneous axial translations and colum n angle rotations are necessary. These two movements are obviously not independent. Thiscan be a source of error (Fig. 3) because the real machine rotates the tool column angle at the same time as it translates it along its axis, while in the simulation, for each time interval, the tool is first rotated and next translated along its axis. However, in these cases the original CNC is already decomposed as a set of very small movements with a resolution very similar to the one needed in the machining. Therefore, these movements are not further decomposed in the machining.The global coordinate system in which the geometry is expressed along time is sketched in Fig. 4. The axis coincide with the machine axis X; Y and Z at the tool home position at the beginning of machining. Let ct(xtk, ytk;,0.0)be the coordinates of the tool section center at instant k: The components of the normal vector of the section are ntk(nxtk, nytk,0.0). It should be noted that nxtk =cos(ωk) and nytk= sin(ωk); being vk the column angle of the tool at instant k: The updated values of these coordinates at k +1.Fig. 3. Non equivalent transformations.Fig. 4. Coordinate system, axes and motion.5. Conclusions and future workThis paper describes a novel method for the simulation of drilling tools CNC machining. Our approach simplifies the 4D (space t time) Boolean operations between the tool and the wheels by reducing them to a sequence of intersections between 2D perpendicular cross-sections along time. Specifically, the method discretizes the toolinto cross-sections and simulates machining on the cross sections. Next, the shape of the tool is recomputed by tiling between contours.The primary advantage of this approach is its simplicity. It addition, it provides user-control on the resolution of the simulation: spacing between crosssections as well as time interval between consecutive intersections.Starting from this work, new research and development lines are opened. Specifically, we are working on global pipelines that would put into the same process automatic CNC computation and tool verification. With such pipelines, given a final tool description, theCNC code to create it would be automatically computed, next using the CNC code as input, tool machining would be simulated. Finally, differences between the input and the output model could be computed and shown.钻探工具数控加工三维仿真的布尔运算摘要本文旨在对钻探工具数控加工的仿真研究。
数控机床改造中英文对照外文翻译文献

中英文对照外文翻译文献(文档含英文原文和中文翻译)原文:The Numerical Control Engine Bed TransformsHarvey B.M ackey First numerical control system development summary brief hi story and tendency.In 1946 the first electronic accounting machine was born the world,this indicated the humanity created has been possib le to strengthen and partially to replace the mental labor the tool. It with the humanity these which in the agricultu re, the industry society created only is strengthens the phy sical labor the tool to compare, got up the quantitive leap ,entered the information society for the humanity to laythe foundation.After 6 years, in 1952, computer technology applied to t he engine bed , the first numerical control engine bed were born in US. From this time on, the traditional engine bed has had the archery target change. Since nearly half centu ry, the numerical control system has experienced two stages and six generation of development.1.1 Numerical control (NC) stage (1952 ~ 1970)The early computer operating speed is low, was not big to then science computation and the data processing influence ,but could not adapt the engine bed real-time control reques t.The people can not but use numeral logic circuit "to buil d"to become an engine bed special purpose computer to take the numerical control system, is called the hardware connecti onnumerical control (HARD-WIRED NC), Jian Chengwei numerical c ontrol (NC). Along with the primary device development, this stage has had been through repeatedly three generations, na mely 1952 first generation of -- electron tube; 1959 second generation of -- transistor; 1965 third generation -- small scale integration electric circuit.1.2 Computer numerical control (CNC) stage (in 1970 ~ presen t)In 1970, the general minicomputer already appeared and th e mass production. Thereupon transplants it takes the numeric al control system the core part, from this time on entered the computer numerical control (CNC) the stage ("which should have computer in front of the general" two characters to ab breviate). In 1971, American INTEL Corporation in the world first time the computer two most cores part -- logic units and the controller, used the large scale integrated circuit technology integration on together the chip, called it the m icroprocessor (MICROPROCESSOR), also might be called the centr al processing element (to be called CPU).The microprocessor is applied to 1974 in the numerical c ontrol system. This is because minicomputer function too stro ng, controlled an engine bed ability to have wealthily (therefore once uses in controlling the multi- Taiwan engine bed at that time, called it group control), was inferior to use d the microprocessor economy to be reasonable. Moreover then small machine reliability was not ideal. The early microproce ssor speed and the function although insufficiently are also high, but may solve through the multi-processor structure. Because the microprocessor is the general-purpose calculator core part, therefore still was called the computer numerical control.In 1990, PC machine (personal computer, domestic custom had called microcomputer) the performance has developed tothe very high stage, may satisfiedly take the numerical cont rol system core part the request. Thenumerical control system henceforth entered based on the PC stage. In brief, the computer numerical control stage has also experienced three generations. Namely 1970 fourth generat ion of -- minicomputer; 1974 five dynasties -- microprocessor and 1990 sixth generation -- (overseas was called PC-BASED) based on PC.Also must point out, although overseas already renamed as the computer numerical control (namely CNC).Also must point out, although overseas already renamed as the computer numerical control (namely CNC), but our countr y still the custom called the numerical control (NC). Theref ore we daily say "numerical control", the materially already was refers to "computer numerical control".1.3 the numerical control future will develop tendency1.3.1 open style continues to, to develop based on the PC sixth generation of directionThe software and hardware resources has which based on P C are rich and so on the characteristic, the more numerical controls serial production factory can step onto this path. Uses PC machine to take at least its front end machine, pr ocesses the man-machine contact surface, the programming, the association .Question and so on net correspondence, undertakes the num erical control duty by the original system. PC machine has the friendly man-machine contact surface, will popularize to all numerical controls system. The long-distance communication, the long-distance diagnosis and the service will be more common.1.3.2 approaches and the high accuracy developmentThis is adapts the engine bed to be high speed and the high accuracy direction need to develop.1.3.3 develops to the intellectualized directionAlong with the artificial intelligence in the computer do mainunceasing seepage and the development, the numerical control system intellectualized degree unceasingly will enhance.(1) applies the adaptive control technologyThe numerical control system can examine in the process some important information, and the automatic control system related parameter, achieves the improvement system running sta tus the goal.(2) introduces the expert system instruction processingThe skilled worker and expert's experience, the processing general rule and the special rule store in the system, take the craft parameter database as the strut, the establishmenthas the artificial intelligence the expert system.(3)introduces the breakdown to diagnose the expert system(4) intellectualized numeral servo driveMay through the automatic diagnosis load, but the automat ic control parameter, causes the actuation system to obtain the best movement.Second, engine bed numerical control transformation necessi ty.2.1 microscopic looks at the transformation the necessityFrom on microscopic looked below that, the numerical cont rol engine bed has the prominent superiority compared to the traditional engine bed, moreover these superiority come from the computer might which the numerical control system contain s.2.1.1 may process the traditional engine bed cannot proce ss the curve, the curved surface and so on the complex com ponents.Because the computer has the excellent operation ability, may the instant accurately calculate each coordinate axis ins tant to be supposed the movement physiological load of exerc ise, therefore may turn round thesynthesis complex curve or the curved surface.2.1.2 may realize the processing automation, moreover is the flexible automation, thus the efficiency may enhance 3 ~ 7 times compared to the traditional engine bed.Because the computer has the memory and the memory prope rty, may the procedure which inputs remember and save, thenthe order which stipulated according to the procedure automat ic carries out, thus realization automation. The numerical co ntrol engine bed so long as replaces a procedure, may reali ze another work piece processing automation, thus causes the single unit and the small batch of production can automate, therefore is called has realized "flexible automation".2.1.3 processings components precision high, size dispersion d egree small, makes the assembly to be easy, no longer needs "to make repairs".2.1.4 may realize the multi- working procedures centralism, r educes the components in engine bed between frequent transpor ting.2.1.5 has auto-alarm, the automatic monitoring, automatic comp ensation and so on the many kinds of autonomy function, thu s may realize long time nobody to safeguard the processing.2.1.6 advantage which derives by above five.For example: Reduced worker's labor intensity, saved the labor force (a person to be possible to safeguard the multi - Taiwan engine bed), reduced the work clothes, reduced the new product trial manufacturing cycle and the production cycl e, might to the market demand make rapid reaction and so o n.Above these superiority are the predecessor cannot imagine, is an extremely significant breakthrough. In addition, the en gine bed numerical control carries out FMC (flexible manufact ure unit), FMS (flexible manufacture system) as well as CIMS (computer integration manufacture system) and so on the enter prise becoming an information based society transformation foundation. The numerical control technology already became the manufacturing industry automation the core technology and the foundation technology.2.2 great watches the transformation the necessityFrom on macroscopic looked that, the industry developed c ountry armed forces, the airplane weapon industry, in the en d of the 70's, at the beginning of the 80's started the l arge-scale application numerical control engine bed. Its essen ce is, uses the information technology to the traditional in dustry (including the armed forces, airplane weapon industry) carries on the technological transformations. Except that uses outside the numerical control engine bed, FMC, FMS in the m anufacture process, but also includes in the product developm ent carries out CAD, CAE, CAM, the hypothesized manufactureas well as carries out MIS in the production management (ma nagement information system), CIMS and so on. As well as in creases the information technology in its production product, including artificial intelligence and so on content. Because uses the information technology to the country foreign troops, the airplane weapon industry carries on the thorough transfor mation (to call it becoming an information based society), f inally causes them the product in the international military goods and in the goods for civilian use market the competit ive power greatly is the enhancement. But we in the informa tion technology transformation tradition industry aspect compar ed to the developed country to fall behind approximately for 20 years. Like in our country engine bed capacity, numerical control engine bed proportion (numerical control rate) to 199 5 only then 1.9%, but Japan has reached 20.8% in 1994, therefore every year has the massive mechanical and electrical products import. This also on from on macroscopic explained the engine bed numerical control transformation necessity. Tho rd, the numerical control transformation content and superiorl y lacks3.1 Transformation industry startingIn US, Japan and Germany and so on the developed countr y, their engine bed transforms took the new economical growt h profession, thrives abundantly, is occupying the golden age .As a result of the engine bed as well as the technical u nceasing progress, the engine bed transformation is "the eter nal" topic. Our country's engine bed transformation industry, also enters from the old profession to by the numerical c ontrol technology primarily new profession. In US, Japan, Ger many, have the broad market with the numerical control techn ological transformations engine bed and the production line, has formed the engine bed and the production line numerical control transformation new profession. In US, the engine be d transformation industry is called the engine bed regenerati on(Remanufacturing) industry. Is engaged in the regeneration ind ustry famous company to include: The Bertsche engineering fir m, the ayton engine bed company, Devlieg-Bullavd (are valuabl e) serves the group, the US equipment company and so on. T he American valuable company has set up the company in Chin a. In Japan, the engine bed transformation industry is calle d the engine bed to reequip (Retrofitting) industry. Is enga ged in the reequipment industry famous company to include: B ig indentation project group, hillock three mechanical companies, thousand substitute fields labor machine company, wild engineering firm, shore field engineering firm, mountain this engineering firm and so on. 3.2 Numerical control transformat ion contentThe engine bed and the production line numerical control transformation main content has following several points: First is extensively recovers the function, to the engine bed, the production line has the breakdown partially to carr y on the diagnosis and the restoration;Second is NC, the addend reveals the installment on the ordinary engine bed, or adds the numerical control system, transforms the NC engine bed, the CNC engine bed;Third is renovates, for increases the precision, the effi ciency and the automaticity, to the machinery, the electricit y partially carries on renovates, reassembles the processing to the machine part, extensively recovers the precision; Does not satisfy the production request to it the CNC system to carry on the renewal by newest CNC;Fourth is the technology renews or the technical innovati on, for enhances the performance or the scale, or in order to use the new craft, the new technology, carries on the b ig scale in the original foundation the technology to renew or the technical innovation, the great scope raises the leve l and the scale renewal transformation. The new electri cal system transforms after, how carries on the debugging as well as the determination reasonable approval standard, also is the technology preparatory work important link. The debugg ing work involves the machinery, the hydraulic pressure, the electricity, the control, and so on, therefore must carry onby the project person in charge, other personnel coordinate. The debugging step may conform to simplicity to numerous, fr om infancy to maturity, carries on from outside to in, afte r also may the partial overall situation, after first the s ubsystem the 3.3 The numerical control transformation superior ly lacks 3.3.1 reduced investment costs, the date of deliv ery are short With purchases the new engine bed to comp are, may save 60% ~ 80% expense generally, the transformatio n expense is low. Large-scale, the special engine bed especi ally is specially obvious. The common large-scale engine bed transforms, only spends the new engine bed purchase expense 1/3, the date of delivery is short. But some peculiar circu mstances, like the high speed main axle, the tray automatic switching unit manufacture and the installment too requires a lot of work, costs a great deal of money, often transforms the cost to enhance 2 ~ 3 times, with purchases the new engine bed to compare, only can economical invest about 50 %.3.3.2 machine capability stable are reliable, the structure i s limitedUses foundation and so on lathe bed, column all is heav y but the firm casting component, but is not that kind of welding component, after the transformation engine bed perform ance high, the quality is good, may take the new equipment continues to use many years. But receives the original mecha nism the limit, not suitably makes the unprecedented transfor mation. 3.3.3 familiar understood the equipment, is advantag eous for the operation serviceWhen purchases the new equipment, did not understand whether the new equipment can satisfy its processing request. Th e transformation then otherwise, may precisely calculate the engine bed the processing ability; Moreover, because many yea rs use, the operator already understood to the engine bed c haracteristic, uses and services the aspect to train the tim e in the operation short, effective is quick. The transforma tion engine bed as soon as installs, may realize the capaci ty load revolution. 3.3.4 may fully use the existing condi tionMay fully use the existing ground, does not need to lik e buys when the new equipment such to have reto construct the ground. 3.3.5 may use the newest control technology enhances the production equipment the automated level and the efficiency, improves the equipment quality and the scale, alters to the old engine bed now the horizontal engine bed. Fourth, numerical control system choiceWhen the numerical control system mainly has three kind of types, the transformation, should act according to the sp ecial details to carry on the choice.4.1 Step-by-steps the open system which the electrical ma chinery drivesThis system servo drive mainly is step-by-steps the elect rical machinery, the power step-by-steps the electrical machin ery, the battery solution pulse motor and so on. Entering s ends out which by the numerical control system for instructi on pulse, after the actuation electric circuit control and t he power enlargement, causes to step-by-step the electrical m achinery rotation, through gear vice- and ball bearing guide screw vice- actuation executive component. So long as the control command pulse quantity, the frequency as well as the circular telegram order, then may control the executive compo nent movement the displacement quantity, the speed and the h eading. This kind of system does not need the physical loca tion and the velocity feedback which obtains to the input e nd, therefore called it the open system, this system displac ement precision mainly decided in step-by-steps the electrical machinery angular displacement precision, transmission part and so on gear guide screw pitches the precision, therefore the system displacement precision is low.This system structure simple, debugging service convenient, work reliable, cost low, is easy to reequip successfully.4.2 The asynchronous motor or the direct current machine drive, diffraction grating survey feedback closed loop numer ical control system .This system and the open system difference is: Physical location feedback signal which by position detector set and so on the diffraction grating, induction synchromesh obtains, carries on the comparison as necessary with the given value, two interpolations enlargements and the transformation, the ac tuation implementing agency, by the speed which assigns turns towards the elimination deviation the direction movement, unti l assigns the position and the feedback physical location in terpolation is equal to the zero. The closed loop enters fo r the systemEnters for the system complex in the structure compared to the split-ring, the cost is also high, requests strictly to the environment room temperature. The design and the debu gging is all more difficult than the open system. But mayobtain compared to the split-ring enters for a system higher precision, quicker speed, actuation power bigger characteristic target. May act according to the product specification, decid ed whether uses this kind of system.4.3 The direct current servo electrical machinery drives, encoder feedback semi-closure link numerical control system .Half closed-loop system examination part installs in among passes in the moving parts, indirectly surveys the executive component the position. It only can compensate a system ring circuit interior part of part the error, therefore, its prec ision compared to closed-loop system precision low, but its structure and the debugging all compares the closed-loop syst em to be simple. In makes the angular displacement examinati on part and the speed examination part and the servo electr ical machinery time a whole then does not need to consider the position detector set installs the question.The current production numerical control system company fa ctory quite are many, overseas famous company like German SI EMENS Corporation,Japanese FANUC Corporation; Native corporation like China Mount Everest Corporation, Beijing astronautics eng ine bed numerical control system group company, Central China numerical control company and Shenyang upscale numerical contr ol country engineering research center.When choice numerical control system mainly is each kind of precision which the engine bed must achieve after the nu merical control transformation, actuates the electrical machine ry the power and user's request.Fifth in the numerical control transformation the mainmechanical part reequips the discussionA new numerical control engine bed, must achieve in the design that, Has the high static dynamic rigidity; Movement vice- between friction coefficient small, the transmission is ceaseless; The power is big; Is advantageous for the operati on and the service. When engine bed numerical control transf ormation should meet the above requirements as far as possib le. Cannot think the numerical control installment and the o rdinary engine bed connects in has met the numerical control engine bed requirements together, but also should carry on t he corresponding transformation to the major component to ena ble it to achieve the certain design request, can obtain th e anticipated transformation goal. 5.1 skids guide railSaid to the numerical control lathe that, the guide rail besides should have the conventional lathe guidance precision and the technology capability, but also must have good bears the friction, the attrition characteristic, and the reduction but sends the dead area because of the friction drag. At t he same time must have the enough rigidity, by reduces the guide rail to distort to processes the precision the influen ce, must have the reasonable guide rail protection and the lubrication.5.2 gearThe common engine bed gear mainly concentrates in the headstock and the gear box.In order to guarantee the transmission precision, on the numerical control engine bed uses the gear precision class i s all higher than the ordinary engine bed. Must be able to achieve the ceaseless transmissionin the structure, thus transforms time, the engine bed maingear must satisfy the numerical control engine bed the reque st, by guarantees the engine bed processing precision.5.3 skids the guide screw and the ball bearing guide screwThe guide screw transmission relates directly to the tran smission chain precision. The guide screw selects mainly is decided requests and drives the torque request in the job p recision. Is not used by job precision request Gao Shike skids the guide screw, but should inspect the original guide screw attrition situation, like the pitch error and the pitc h accumulative error as well as matches the nut gap. The o rdinary circumstances skid the guide screw to be supposed no t to be lower than 6 levels, the nut gap oversized then r eplaces the nut. Uses skids the guide screw relative ball b earing guide screw price to be low, but satisfies the pre cision high components processing with difficulty.The ball bearing guide screw rubs loses slightly, the ef ficiency is high, its transmission efficiency may above 90%; Precision high, the life is long; When start moment of forc e and movement the moment of force approaches, may reduce t he electrical machinery to start the moment of force. Theref ore may satisfiedly compare the high accuracy components proc essing request. 5.4 safe protectionThe effect must take the security as a premise. Transfor ms in the engine bed must take the corresponding measure ac cording to the actual situation, cuts noticeable. The ball b earing guide screw vice- is the precision part, when the wo rk must take strict precautions against the dust is speciall y the scrap and the hard sand grains enters the roller conveyer. On longitudinal guide screw also coca overall sheet i ron safety mask. The big carriage with skids two end surfac es which the guide rail contacts to have to seal, prevented absolutely the flinty granulated foreign matter enters the sl iding surface damage guide rail.Sixth, After the engine bed electrical system transformati on, to operates, the programmers inevitably brings the new r equest. Therefore ahead of time carries on new system knowle dge training to the operator and the programmers to be extr emely important, after otherwise will affect the transformatio n the engine bed rapid investment production. The training c ontent should include the new operation kneading board dispos ition, the function, the instruction meaning generally; New s ystem functional scope, application method and with old syste m difference; Maintenance maintenance request; Programming stan dard and automated programming and so on. The key point is makes, gets a good grasp of the operating manual and the p rogramming instruction booklet.the numerical control transforms se Transforms the scope according to each equipment differently, must beforehand desig n the connection partial transformations, if transforms comple tely, should design the electro-mechanical transformation conne ction, the operation kneading board control and the dispositi on, the interconnection partial contacts, the parameter measur ing point, services the position and so on, the request ope rates and services conveniently, reasonable, the line moves t owards, center the small junction smoothly few, the strong a nd the weak electrical noise is smallest, has the suitable allowance and so on. Partial transformation, but also needsto consider the new old system the performance match, the v oltage polarity and the size transformation, install the posi tion, the digital-analog conversion and so on, when the nece ssity must manufacture the transformation connection voluntaril y.veral examples1st, transforms the X53 milling machine with SIEMENS 810MIn 1998, the company invested 200,000 Yuan, with German Simens the 810M numerical control system, the 611A exchange servo drive system sds was the X53 milling machine carries on X, Y, the Z three axle numerical control transformation to a company's model; Retained the original main axle system and the cooling system; The transformation three axle has us ed the roller lead screw and the gear drive organization on the machinery. The entire transformation work including the m achine design, the electrical design, the PLC procedure estab lishment and the debugging, the engine bed overhaul, finally is the entire machine installment and the debugging. After t he milling machine transforms, processing effective stroke X/Y /The Z axis respectively is 88.0/270/28 billion mm; Maximum speed X/Y/The Z axis respectively is 5000/1500/800 mm/Min; Ma nual speed X/Y/The Z axis respectively is 3000/1000/500 mm/Mi n; The engine bed processing precision achieves ±0.001mm. The engine bed three coordinates linkage may complete each kind of complex curve or the curved surface processi ng.2nd, transforms the C6140 lathe with GSK980T and the exc hange servo drive system sds .In 2000, with Guangzhou numerical control plant production GSK980T numerical control system, the DA98 exchange servo uni t and 4 locations automatic tool rests to an electrical mac hinery branch factory C6140 lathe X, the Z two axes carries on the numerical control transformation; Retained the original main axle system and the cooling system; The transformation two axes have used the roller lead screw and with the ambu lacrum transmission system on the machinery. Entire transforma tion work including machine design, electrical design, engine bed overhaul and entire machine installment and debugging. Af ter the lathe transforms, processing effective stroke X/The Z axis respectively is 3.90/73 million mm; Maximum speed X/The Z axis respectively is 120.0/3 million mm/Min; The manual sp eed is 400mm/Min; Manual is fast is X/The Z axis respective ly is 120.0/3 million mm/Min; The engine bed smallest migrat ion unit is 0.001mm.3rd, transforms the X53 milling machine with SIEMENS 802SIn 2000, the company invests 120,000 Yuan, with German S imens the 802S numerical control system, step-by-steps the ac tuation system is the X53 milling machine carries on X, Y, the Z three axle numerical control transformation to company' s another model; Retained the original main axle system and the cooling system; The transformation three axle has used t he roller lead screw and the gear drive organization on the machinery. The entire transformation work including the machin e design, the electrical design, the engine bed overhaul, fi nally is the entire machine installment and the debugging. A fter the milling machine transforms, processing effective stro。
数控机床设备资料中英文对照

数控机床设备资料中英文对照数控机床设备资料中英文对照一:说明书名次解释:lubrication hole[机]润滑孔; [机]滑油孔; 加油孔; [机]注润滑油孔Pressure Lubrication[机]压力润滑; 强制润滑; [机]加压润滑lubrication device润滑装置; 润滑油; 润滑装配AUTO LUBE 自动润滑Spindle motor 主轴马达Hydraulic pump motor 油压马达Auto Cross feed motor 前后马达High Pressure Through Coolant刀具高压冷却系统once-through coolant system一次流过冷却系统Coolant through spindle油水分离机sp. through coolant主轴通过冷却液through coolant通过冷却剂coolant jet冷却剂喷嘴flood coolant motor洪水冷却电机base coolant/gun motor基地冷却剂/枪电动机mist collect motor雾收集电动机Coolant motor (for tools/chips) 切削水马达Chip conveyor motor 铁屑输送机马达ATC motor 储刀仓马达fan cooler风扇冷却器fan draught cooler冷风机fan cooler(for amp):风扇冷却器(对放大器(amplifier))containment fan cooler安全壳风机冷却器fan-draught cooler风扇冷却器fan unit 风扇设备风扇单元风扇装置panel cooling 嵌入式降温panel door 镶板门panel heating 板壁供热tool counter工具柜台MAGAZINE CW 刀库正转MAGAZINE CCW 刀库反转 ...COUNTER (计数器)TOTAL COUNTER(总计数器)Mate:配对物(伴侣)Rotation:旋转回转Caution:谨慎radiator brake:散热器制动air duster blow gun吹尘器喷枪air-blow pipe喷气管Air Blow:鼓风Overload:超载overload protection防止过载,超载防护information overload信息过载;信息超载;信息超负荷overload capacity过载容量overload operation超负荷运行,超载运行thermal overload relay热继电器;热过载继电器overload current[电]过载电流 ; 过载电流过负荷电流dis connect jumper pin in case of using sub op存保计划连接跳线针如果使用子运算(in case of using如果使用;usb op 子运算)disconnect jumper pin断开连接跳线针beta-i servo :β-i 伺服spindle amplifer:主轴放大器manual feed delay:手动进给延迟rigid tapping ontime:刚性攻丝准时z-axis cancel:z轴取消Current Tool Number现行刀具号Reset Current Tool恢复当前工具预设servo amp module伺服放大器模块optical fiber cable:光缆、光纤光缆sheet key板键Head sheet Key头型图要点key sheet键盘纸; 转印盘纸i series servo motor:i系列伺服电动机call light:警示灯lub. motor on :润滑泵接通(lubricant润滑剂motor-on signal马达接通信号ATC forward:ATC 向前ATC reverse :ATC反向Ball screw: 滚珠丝杠Binary code :二进制DETACH:分离,脱开Follow-up :位置跟踪Black format:程序段格式Tool post interference check:刀架碰撞检查Abnormal load detection:异常负载检测Manual handle interruption:手轮中断Ladder diagram:梯形图(阶梯,关系图)Tool counter:工具柜台Magazine:刀库Brake module:制动模块Machine side:机侧Twist pair:双绞线Main power source:主电源Wiring diagram:接线图Current:现时状态、现行状态Dual table :双工作台Spare:备用件、预置Aux:辅助Brake on:制动器Mist :雾状、雾Coolant tank capacity:冷却泵油箱容量Enclosure:外壳、套、附件Overload:过载Flag:标志Condition:条件Machine ready delay:机床准备延迟Encoder:编码器Etherent:以太网口Orientation:主轴定向Spindle positioning:主轴定位Fault:故障Motion:运转Dwell:停歇,保压Feed rate:进给率Interlock/start-lock:互锁/启动-锁Spindle speed arrival check:主轴速度到达检测concent for maintenance答应为维护AC reactor:交流电抗器APC:绝对位置编码器反馈(Absolute position encoder feedback)arm in position z-axis interlock:手臂位置Z轴互锁Pressure:压力,压强,是……压迫Pressure valve[机]压力阀; [机]压力值; 止回阀; [机]回压阀air pressure气压; 空气压力; [建]工作气压; [物]气源压力consuming volume耗用量Oil:油Oller:n. 轮胎式压路机Capacity: n. 能力;容量;资格,地位;生产力bearing capacity[力]承载能力; [力]承载力; [力]承重能力; 支持力oil type 油的类型pumping n. [机] 抽吸;脉动;抽气效应v. 抽水(pump的ing形式)pumping out抽空; 扬水; 排出; 泵出pumping frequency[电子]泵频; 抽运频率; 泵送频率interval:间隔间距class interval[统计]组距; 组区间; 级距; 标度分组间隔Time interval[天]时间间隔; [天]时间区间; 时距; [天]时段interval scale[统计]区间尺度; 等距量表; [计]等距尺度; 等距量尺capacity:容量consuming:adj. 消费的;强烈的v. 消耗(consume的ing形式distributor分配器metering n. 计量,[测] 测量;测光模式v. 以计量器计量(meter 的ing形式metering valve[机]计量阀; 限流阀; [机]限量阀; [机]配量阀metering jet量孔; [油气]测油孔; 计量喷流OPTION:选择(选择功能块)ARM:机械手ARM home position:机械手原点位置soft key cable:软键电缆PUNCH PANEL:开孔面板MOTHER BOARD:母版Name:名称Description:描述Connector:连接器二、操作面板中英文对照:ABS和REL——在法那克系统中,按这两个键分别来切换当前机床的相对坐标和绝对坐标ALL——全选,程序编辑时用PRGRM——程序(program)的缩写,用于查看程序NEXT——查看程序和查看参数时,下一页OPRT——在法那克系统中,选择编辑程序时,也就是按下PRGRM后,再按这个键,才能输入程序号HOST,CONECT——这两个是在系统与外界通信时用的,我没试过,不知道什么作用HELP——查看帮助信息SHIFT——换档键,有些键有两个字符,按下这个键,用来输入顶部那个字符ALTER——程序修改键,编辑程序时用INSERT——程序插入键,编辑程序时用EOB——程序结束符,在编辑程序时,没段程序结束时,要加这个符号CAN——取消键,用来取消输入INPUT——输入键,用来输入程序或参数POS——按此键显示当前机床位置画面PROS——按此键显示当前程序画面OFFSET——按此键显示刀具偏置画面SETTING——按此键显示刀具偏置设定画面SYSTEM——按此键显示系统信息及系统状态画面GRAPH——按此键显示加工时刀具轨迹的图形画面CUSTOM——按此键显示用户宏程序画面手动数据输入(MDI)直接数字控制方法(DNC)控制器单元或机控制器单元(MCU)法拉克:ALTER 修改程序及代码INSRT 插入程序DELET 删除程序EOB 完成一句(END OF BLOCK)CAN 取消(EDIT 或MDI MODE 情况下使用)INPUT 输入程序及代码OUTPUT START 输出程序及指令OFFSET 储存刀具长度、半径补当值AUX GRAPH 显示图形PRGRM 显示程序内容ALARM 显示发生警报内容或代码POS 显示坐标DGONS PARAM 显示自我诊断及参数功能RESET 返回停止CURSOR 光标上下移动PAGE 上下翻页三、常用缩写:启动start STRT停止stop ST运行run正转forward FWD反转reverse REV加速accelerate减速reduce RED低速low L中速medium M高速high H主轴方向spindle direction向前forward FWD向后backward向左left L向右 right R诊断:DGNOS信息:MSG操作员:OPER参数:PARAM目录:DIR取代:ALTER公共地线,公共线:COM四、其它常用词句中英文对照:金属切削 metal cutting机床 machine tool金属工艺学 technology of metals 刀具 cutter 摩擦 friction联结 link传动 drive/transmission轴 shaft弹性 elasticity频率特性 frequency characteristic 误差 error 响应 response定位 allocation机床夹具 jig动力学 dynamic运动学 kinematic静力学 static分析力学 analyse mechanics拉伸 pulling压缩 hitting剪切 shear扭转 twist弯曲应力 bending stress强度 intensity三相交流电 three-phase AC磁路 magnetic circles变压器 transformer异步电动机 asynchronous motor几何形状 geometrical精度 precision正弦形的 sinusoid交流电路 AC circuit机械加工余量 machining allowance 变形力 deforming force 变形 deformation应力 stress硬度 rigidity热处理 heat treatment退火 anneal正火 normalizing脱碳 decarburization渗碳 carburization电路 circuit半导体元件 semiconductor element 反馈 feedback发生器 generator直流电源 DC electrical source门电路 gate circuit逻辑代数 logic algebra外圆磨削 external grinding内圆磨削 internal grinding平面磨削 plane grinding变速箱 gearbox离合器 clutch绞孔 fraising绞刀 reamer螺纹加工 thread processing螺钉 screw铣削 mill铣刀 milling cutter功率 power工件 workpiece齿轮加工 gear mechining齿轮 gear主运动 main movement主运动方向 direction of main movement进给方向 direction of feed进给运动 feed movement合成进给运动 resultant movement of feed合成切削运动 resultant movement of cutting合成切削运动方向 direction of resultant movement of cutting 切削深度 cutting depth前刀面 rake face刀尖 nose of tool前角 rake angle后角 clearance angle龙门刨削 planing主轴 spindle主轴箱 headstock卡盘 chuck加工中心 machining center车刀 lathe tool车床 lathe钻削镗削 bore车削 turning磨床 grinder基准 benchmark钳工 locksmith锻 forge压模 stamping焊 weld拉床 broaching machine拉孔 broaching装配 assembling铸造 found流体动力学 fluid dynamics流体力学 fluid mechanics加工 machining液压 hydraulic pressure切线 tangent机电一体化 mechanotronics mechanical-electrical integration 气压 air pressure pneumatic pressure稳定性 stability介质 medium液压驱动泵 fluid clutch液压泵 hydraulic pump阀门 valve失效 invalidation强度 intensity载荷 load应力 stress安全系数 safty factor可靠性 reliability螺纹 thread螺旋 helix键 spline销 pin滚动轴承 rolling bearing滑动轴承 sliding bearing弹簧 spring制动器 arrester brake十字结联轴节 crosshead联轴器 coupling链 chain皮带 strap精加工 finish machining粗加工 rough machining变速箱体 gearbox casing腐蚀 rust氧化 oxidation磨损 wear耐用度 durability随机信号 random signal离散信号 discrete signal超声传感器 ultrasonic sensor集成电路 integrate circuit挡板 orifice plate残余应力 residual stress套筒 sleeve扭力 torsion冷加工 cold machining电动机 electromotor汽缸 cylinder过盈配合 interference fit热加工 hotwork摄像头 CCD camera倒角 rounding chamfer优化设计 optimal design工业造型设计industrial moulding design 有限元finiteelement滚齿 hobbing插齿 gear shaping伺服电机 actuating motor铣床 milling machine钻床 drill machine镗床 boring machine步进电机 stepper motor丝杠 screw rod导轨 lead rail组件 subassembly可编程序逻辑控制器 Programmable Logic Controller PLC 电火花加工 electric spark machining电火花线切割加工electrical discharge wire - cutting 相图phase diagram热处理 heat treatment固态相变 solid state phase changes有色金属 nonferrous metal陶瓷 ceramics合成纤维 synthetic fibre电化学腐蚀 electrochemical corrosion车架 automotive chassis悬架 suspension转向器 redirector变速器 speed changer板料冲压 sheet metal parts孔加工 spot facing machining车间 workshop工程技术人员 engineer气动夹紧 pneuma lock数学模型 mathematical model画法几何 descriptive geometry机械制图 Mechanical drawing投影 projection视图 view剖视图 profile chart标准件 standard component零件图 part drawing装配图 assembly drawing尺寸标注 size marking技术要求 technical requirements刚度 rigidity内力 internal force位移 displacement截面 section疲劳极限 fatigue limit断裂 fracture塑性变形 plastic distortion脆性材料 brittleness material刚度准则 rigidity criterion垫圈 washer垫片 spacer直齿圆柱齿轮 straight toothed spur gear 斜齿圆柱齿轮 helical-spur gear直齿锥齿轮 straight bevel gear运动简图 kinematic sketch齿轮齿条 pinion and rack蜗杆蜗轮 worm and worm gear虚约束 passive constraint曲柄 crank摇杆 racker凸轮 cams共轭曲线 conjugate curve范成法 generation method定义域 definitional domain值域 range导数\\\\微分 differential coefficient求导 derivation定积分 definite integral不定积分 indefinite integral曲率 curvature偏微分 partial differential毛坯 rough游标卡尺 slide caliper千分尺 micrometer calipers攻丝 tap二阶行列式 second order determinant逆矩阵 inverse matrix线性方程组 linear equations概率 probability随机变量 random variable排列组合 permutation and combination气体状态方程 equation of state of gas 动能 kinetic energy势能 potential energy机械能守恒conservation of mechanical energy 动量momentum桁架 truss轴线 axes余子式 cofactor逻辑电路 logic circuit触发器 flip-flop脉冲波形 pulse shape数模 digital analogy液压传动机构 fluid drive mechanism 机械零件 mechanical parts淬火冷却 quench淬火 hardening回火 tempering调质 hardening and tempering磨粒 abrasive grain结合剂 bonding agent砂轮 grinding wheel。
机械类数控车床外文翻译外文文献英文文献数控
数控加工中心技术开展趋势及对策原文来源:Zhao Chang-ming Liu Wang-ju (CNC Machining Process and equipment, 2002,China)一、摘要Equip the engineering level, level of determining the whole national economy of the modernized degree and modernized degree of industry, numerical control technology is it develop new developing new high-tech industry and most advanced industry to equip (such as information technology and his industry, biotechnology and his industry, aviation, spaceflight, etc. national defense industry) last technology and getting more basic most equipment. Numerical control technology is the technology controlled to mechanical movement and working course with digital information, integrated products of electromechanics that the numerical control equipment is the new technology represented by numerical control technology forms to the manufacture industry of the tradition and infiltration of the new developing manufacturing industry,Keywords:Numerical ControlTechnology, E quipment,industry二、译文数控技术和装备开展趋势及对策装备工业的技术水平和现代化程度决定着整个国民经济的水平和现代化程度,数控技术及装备是开展新兴高新技术产业和尖端工业〔如信息技术及其产业、生物技术及其产业、航空、航天等国防工业产业〕的使能技术和最根本的装备。
回转工作台设计外文翻译文献
回转工作台设计外文翻译文献(文档含中英文对照即英文原文和中文翻译)原文:Design and research direction of the rotary table Abstract:this paper introduces the basic content and the principle of the rotary table design, put forward the research direction of the rotary table, broaden the design idea of designer.Improve the efficiency of the rotary table design, shorten the development cycle of new type rotary table, through the study of this article is for the quality of products of pre-assessment, determine the scope of the production and processing of precision index provides an important basis.Keywords:rotary table;design and research;new ideas;developments0IntroductionOn April 11 to 16, 2011, the theme of "science and technology innovation to meet the crisis generation" of the 12th China international machine tool exhibition (CIMT2011) was held in Beijing. In an economic crisis haze dissipating, slow recovery under the background of international economy, China's economy healthy and rapid development pattern, is attracting more and more attention. In this exhibition, the knowledge of machine tools, tools, manufacturing enterprises at home and abroad Gather in Beijing, as the economic crisis after the baptism of machinery industry brought a feast full of imagination and creativity of science and technology. Is the exhibition of machine tool accessories exhibition In terms of product, high efficiency, high precision, high reliability, high life still is to develop the theme of pursuit. As for the machine tool accessories rotary table is no exception. Rotary table is divided into indexing table, and rotary table. Indexing table can only be completed dividing movement, there is no function of feed. Can be used with work as a whole, can also be used alone. Common positioning pin and rat tooth plate; Nc rotary table is the ideal matching accessories of all kinds of CNC milling machine and machining center. Turn back to the table design Process includeThe basic types of rotary table s not only the mechanical drive mechanism, and it also involves the mechanical and electrical control system, the design idea of the two parts as the demand of the market and customers, constantly update and perfect, therefore, the design and research direction of the rotary table directly affect the benefit and the rise and fall of theturntable production enterprises.1 The basic types of rotary table1.1General turntableRotary table is boring machine, drilling machine, milling machine and the slotting machine, and other important accessories, used for processing and there is a requirement for dividing hole, slot and slope, turn the workbench when processing, can be processing arc surface and groove, etc. According to the structure is divided into different levels turntable general turntable, lie the turntable and universal turntable.(1) water flat turntable: on the frustum of a cone with central hole workpiece positioning and clamping with T slots. Mesa engraved with 360 °on the outer periphery of uniform scribed line. Mesa between base and a worm pole - worm gear pair, ratio of 90:1 or 120:1, to drive and dividing, worm out from base with dial and segment at the end of the handwheel. Turn the handwheel to drive mesa, and the mesa cylindrical week scale (in degrees) and subdivision dial readout rotation Angle. Dividing accuracy is commonly + 60 ". Levels turntable worm out side can also be used coupling connected to machine transmission device, in order to realize the dynamic drive.(2) lie turntable, the base has two perpendicular installation base, make mesa can be level Also can be vertically.(3) the universal turret: mesa can be within the scope of 0 ° ~ 90 ° inclined at any Angle, make the workpiece at any Angle of space can be accurately adjusted.1.2 precision turntablePrecision turntable Used for processing or Angle measurement on precision machine tools. Common optical turntable, digital display turntable and super precision contrate gear plate of turntable.Optical rotary table: (1) on the spindle is equipped with glass or metal precision dial, the optical system to subdivide scale, amplification, through the eyepiece or screen Angle value.(2) digital turntable: mounted on the turntable spindle precision circular grating or round inductosyn and display unit by the number of words the Angle value. Theabove two precision turntable dividing precision up to + / - 1 ".(3) the ultra-precision end tooth disc turntable: use a pair of precision of research on 1440, 720 or 360 tooth face tooth disc dividing positioning, the indexing accuracy up to + / - 0.01 ", make a precise Angle measurement.2 The design parameters and the working principle of rotary tableRotary table design parameters include: rotary table, table size, total table high degree, bearing table, feed speed, turning back to speed range, fast speed rotary speed, electric power, rotary table, dividing precision and measurement system, etc. This study is based on mechanism of shaanxi institute of technology laboratory of general rotary work Stage, through to tear open outfit, clear the turntable within the department of mechanical transmission mechanism, it is a mesa, pedestal, worm gear, worm, positioning3 Rotary table of research ideas and methodsRotary precision of the rotary table is a main technical bottlenecks, if technology and breakthrough in the continent before it has problems, design and manufacture of our country turntable will by "manufacturing power" to "manufacturing power" transformation of a major step forward.3.1 mechanical partsMainly the mesa rotary table with body contact structure design and optimization, generally adopts the sliding and rolling two ways; Second worm and worm wheel design and optimization. In short, the mechanical design involves the various parts of the turntable and parts of process structure, mechanical properties and movement characteristics, etc. Our basic CAD/CAM/CAE technique was used to realize, such as using Pro/E5.0, SolidWorks, CAXA three-dimensional parameterized modeling software to a part of the rotary table zero structure simulation design and research; By using Pro/E5.0, MasterCAMX to make the simulation of machining parts and nc code generation, etc.; Using ANASYS parts for various parts for the turntable mechanical performance analysis, further optimize the structure of the process.3.2 control partTurntable control system design is also a key technical problems, implementation approach are: PLC control system, single-chip microcomputer control system andindustrial control system, three categories. Turn our manufacturing control system in the manual, mechanical and electrical automation, digital control stage of development, is climb the new peak, are at a higher level of information control intelligent direction development. Intelligent machine research and development and extensive application, will promote the rapid, healthy and sustainable development of turntable industry in China, and lead a profound change in the future manufacturing, turn back to the workbench products with new image and concept to attract the customers is the focus of every enterprise instead.3.3 rotary table of green manufacturing design and manufacture of rotary table should also adopt a variety of energy conservation and emissions reduction technology, to the userAnd advocating the meaning of low carbon and green manufacturing way. Traditional thinking and the change of production pattern is experiencing a deep carved, more and more machine tool accessories manufacturing enterprises have to shoulder social morality and responsibility given by the low carbon way, step into the governance and development of the road of scientific development, a green industry Revolution is here is machine tool industry rise. Through technical innovation, process optimization, reduce material and oil-water separation automatic recovery, dust collection and recycling, self-lubricating material application, such as less oil lubrication technology measures to reduce emissions, reduce the impact on the environment.4 ConclusionThe equipment manufacturing industry is the cornerstone of a country's industry, it is a new technology, the development of new products, and provided an important means of modern industrial production, is an indispensable strategic industries.Even the developed industrialized countries, also attaches great importance to.Mechanical, electrical and data processing system and the combination of numerical control technology, leading the new production and processing.In 2011, is China's first year of "twelfth five-year" plan. "Twelve five" period, I have to to the national economy in various fields to carry out the scientific outlook on development as the theme, to speed up the transformation of the mode of economic development as the main line,in-depth technical innovation and development mode change. Rotary table no longer so "machinery", become more and more" Bright", let us together look forward to the birth of intelligent rotary work table!Reference[1] Cui Xufang, zhou, the principle of nc rotary table and design [J], brick and tile, 2008, NO. 6:23-27;[2] Zhao Qun, processing center of rotary table parts structure analysis [J], equipment design and maintenance, 2002, NO. 5:35-36;[3] Yang jian, Liu Hu, dividing the experience of using rotary table [J], machinery manufacturing, 1998, NO. But - 6;[4] Yang Chunhua, Xu Yaokun, general improvement of rotary table [J], motorcycle technology, 2003, NO. So - 27;[5] Sun Dezhou, double wedge ring - a new type of rotary table ball positioning [J], technology and equipment, 2005, NO. 4:8 2-84;[6] JiaoZhiXian Gu Ruihua, rotary table index [J], for the improvement of mechanical technicians, 1995, NO. I - 23.[7] Yang Huizhong, large rotary table in the installation and debugging of error separation and compensation technology research [J], machinery, VOL32, NO. Did - 24;[8] PangZhiWei, CNC boring machine adjustment [J] rotary table maintenance, equipment management and maintenance, 2007, NO. 59 3:59 -;[9]Chen Jiangang, the rotary table control system based on programmable controller design [J], machinery manufacturing, 2008 46-48 (1) : 36 to 39.[10] De Garmo EP, Black JT. Material and manufacturing process. Prentice - Hall, New York, 1957[11] Shigley JE. Mechanical engineering design. McGraw Hill, New York, 1986[12] the knowledge of the five-axis linkage CNC machine tools, machine 66 navigation network, 2007-12-28;[13] five-axis linkage CNC machine tools for die &mold the significance of (a), good mechanical and electrical network, the 2007-12-05;[14]Hwang,JiSeon,PhD.Five-axisNCmachiningofcompoundsculpturedsurfaces[M].P URDUEUNIVERSITY,1997.译文:回转工作台的设计与研究方向摘要:本文主要介绍了回转工作台设计的基本内容和思路,提出了回转工作台的研究方向,拓宽了设计人员的设计思路。
数控机床外文翻译----刀具和刀夹
数控机床外文翻译----刀具和刀夹CUTTING TOOLS AND TOOLHOLDERSTo machine a workpiece successfully you must have :1.the correct kind of cutting tool or tool bit2.the right type of toolholder3.a tool with a sharp cutting-edge4.the cutting tool set or adjusted to the correct height and position.Cutting-tool materialsTool bits used on the lathe are made form one of six basic materials:water-hardening steels,high-speed steels,hard-cast,nonferrous alloys,sintered (cemented) carbides,ceramics,and diamonds. The selection of the material used depends upon many factors including:tool cost,size and design oftool ,metal-removal rate ,length of run ,finish and tolerance of part,and condition and capability of the machine tool . Because of these factors ,material selection is more often based on general experience than on precise evaluation . There are, however ,certain general characteristics of the different cutting-tool materials you should understand.Water-hardening Steels.These include the high-carbon tool steels (either plain carbon or those with minor additions of chromium , vanadium,or tungsten) .The different grades of water-hardening tool steels are classed as W steels in American Iron and Steel Institute’s system of classification . Tools made from these materials have very sharp ,smooth cutting-edges when properlyheat-treated. They are adequate for limited turning at arelatively low cutting speed or when old ,low-speed equipment ,such as a flat-belt lathe , is used .The main limitation of tools made form water-hardening steels is that they soften if the cutting-edge temperature exceeds approximately 300-400F during sharpening or cutting .A second disadvantage is low resistance to edge wear . High-speed Steels. High-speed steels offer great improvement in cutting efficiency over water-hardening tool steels .Tools made from high-speed steels retain enough hardness to machine at rapid rates even when the tool temperature reaches 1050F . They can be used even though they become dull red with heat . Upon cooling to room temperature , the original hardness of these steels does not change .Wear resistance of high-speed steels is much better than that of the carbon or alloy steels . This is due to the high carbide content ,especially in thehigher-alloy types of high-speed steel . Fully hardened , high-speed steels have greater resistance to shock than carbides or hard-cast alloys .There are two main types of high-speed steels designated in the American Iron and Steels Institute system , M steels (molybdenum base and T steels tungsten base . Tool bits made from these materials can be purchased already ground to various shapes . Unground tool bits called tool-bit blanks can also be purchased . These tool-bit blanks are made in standard size to fit the commonly used lathes . The common sizes are 3/16in square by 1 in long ,1/4in square by 2inlong ,5/16in square by 2-1/2in long ,and 3/8in square by 3in long . High-speedsteel tool bits are the type most used in the school machineshop .Hard-cast Alloy . These materials do not contain sufficient iron to be classed as steels . Rather , they are mainly alloys of cobalt , chromium , and tungsten with other elements added for special purpose . They reach full hardness in the as-cast condition , without heat treatment . The must be ground to size after casting . In terms of resistance to heat , wear ,shock ,and initial cost , cast alloys rank between high-speed steels and carbides .Hard-cast alloys are weaker in tension and more brittle than high-speed steels and thus are not suitable for severe shock loads . They are known by such commercial names as stellite , Rex alloy ,and tantung .Sintered Carbides . For efficient and high-speed machining ,best results can be obtained with sintered carbide tools . Carbide tools are available in solid form and as inserts which are either brazed or clamped in toolholders . Clamped inserts are usually round , square , or triangular in shape and have all edge is always available . These inserts can be rotated so that a sharp edge is always available . With modern machine tools and the proper grade of cemented carbide , it is possible to use cutting speeds 10 to 30 time faster than those feasible with high-speed steels .Carbides are suitable for most machining operations such as single-point turning , drilling ,milling , thread cutting, and reaming . Carbides should be used only when they can be supported rigidly and when the machine tool has adequate power and speed to enable their efficient use .Ceramic . With the exception of industrial diamonds , ceramic inserts are the hardest and strongest inserts available . They resistabrasive wear , chipping , and breakage . These inserts work best on very rigid machine tools and onwell-supported workpieces . For most operations , cutting fluids are not needed . Diamonds . Industrial diamonds that have either circular or facetedcutting-edges are used for light finishing cuts when an extremely high-quality surface finish required . Although a very smooth finish can be achieved using other cutting-tool materials , diamond turning can provide even smoother finishes with very small tolerances .TOOLHOLDERSThe toolholder holds the cutting tool rigid during cutting operations . Four types of toolholders are in general use .1 . The tool post with standard toolholders . The tool too post is comprised of the post , screw , washer , collar , and rocker . The washer fits the top slidee piece slot . The collar and the rocker elevate or lower the point of too . The screw clamps the toolholder in place .The standard toolholder for high-speed steel cutter bits comes in three common shapes : straight , right-hand offset or shank , and left-hand offset or shank . You can identify right-hand and left-hand offset holders by holding the setscrew end in your hand . If the shank bends to the right , it is a left-hand offset holder . The straight toolholder is fused for most work . The left-hand toolholder is used when you need to cut close to the chuck or lathe dog . The right-hand holder isused when feeding toward the tailstock of the lathe . The cutting-tool bit is held in each of these toolholders at an angle of 14 to 16.5 degrees . This is called the toolholder angle .Carbide toolholders also come in three styles and are similarin appearance to those mentioned above . The hole for the cutter bit , however , is parallel to the bottom edge of the holder .2. The open-side or heavy-duty tool block holds one tool ata time and consists of a T-slot clamp , a C-shaped block , and two or more tool clamping screws . Because this unit is very rigid , it is especially useful for heavy cuts . A tool bit can be mounted directly in the tool block or some type of carbide tooolholder can be used .3. The turret tool block or four-way toolholder consists of a swiveling block in which the tools are clamped Common turret block hold four tools . Each can be quickly swiveled into cutting position and clamped in place . Some turret blocks have eight tool stations . Frequently ,an open-side-type tool block is also mounted on the rear of the cross slide to add one additional cutting operation . With this arrangement , anywhere form five to nine different kinds of tools can be mounted and operated in sequence for turning , forming ,facing ,knurling , and cutting off duplicate parts .4. The quick-change-type tool system holds only one tool ata time , but three different sides can be used to position the tool . It consists of a quick-change tool post with a clamping lever and a series of toolholders for turning , facing ,boring , cutting off , threading , knurling , and thread cutting .Single-point Cutting ToolsTool Parts . Before you can grind a tool bit , you must become acquainted with some of the terms used to describe the various parts of the cutting tool .1 . The face is the top of the tool bit . It is the surface on which a part of the chip attaches as it is cut away form the workpiece .2. The cutting-edge is that part of the cutter bit which actually does the cutting .3. The nose is the corner or are formed by the side and end cutting-edge .4. The flank is the surface below the cutting-edge .5. The point is the part of the tool bit which is shaped to form the cutting-edge and face .Tool Angles .The following are important tool angles used for all single-point cutting tools .1.The side relief angle is the angle between the ground surface and the verticalside of the tool bit before it is ground . This angle was formerly called side clearance , and many machinists still use this term .The side relief angleprovides clearance between the cut surface of the work and the flank of tool .Tool wear reduces the effective side clearance angle .If the angle is too small, the cutter will rub and heat . If the angle is too large , the cutting-edge will be weak and the tool will have a tendency to dig into the workpiece.2.The end relief angle is the angle formed between the end of the cutting-edgeand a vertical line. It was formerly called front clearance. The end reliefangle provides clearance between the finished surface of the work and the tool. If this angle is too small, the tool will rub on the finished surface and produce a poor finish. Wear tends to reduce this angle. If the angle is too large , the tool may dig into the work , chatter, and fail through chipping . An angle of 8 to 15 is recommened for steel tools and 6 to 8 for carbide tools .If thetool is set above the center of rotation , the effective clearance angle is reduce . This must be considered in choosing the proper angle .3.The end cutting-edge angle provides clearance between the cutter and thefinished surface of the work .If this angle is too small, it may cause chatter. A small angle of about 6 is desirable on light finishing cuts, however, in order to produce a smooth finish .4.The side cutting-edge angle turns the chip away form the finishedsurface .Recommended angles are between 5 and 15 .5.The nose radius removes the fragile corner of the tool , prolongs tool life ,and improves finish . The radius may be large for maximum-strengthrough-cutting tools and may be reduced for light feeds . The larger the nose radius ,the better the finish as long as chatter dose not occur .Recommended nose radii are 0.010 to 0.030 in . or more for finishing cuts , and 1/30 to 1/2 in for roughing cuts .6.To help shape the cutting-edge and face , it is necessary to grind rake angleson a tool bit .Rake is an inclination form the vertical or horizontal .The two rake angles are back rake and side rake .Back rake , in a single-point feeding to the side , turns the chip away form the finished work and gives the tool a slicing action .A zero back rack tends to make a spiral chip , and a back rake angle greater than zero tends to stretch the spiral chip out into a helix . A back-rake angle of form 5 to 15 is used to keep chips form scratching the workpiece . High-speed steel tool bits are always ground with a positive rake .However , cementedcarbide tools may have either a positive or negative rake .Negative rake increases the shear angle at which the chip is formed , providing for a good chip and a good surface finish .Negative rake tools are generally used on a heavy-duty lathe that is operated at high speed with a heavy feed .Side rake refers to the angle between the face of the tool and a line that would represent the top of the unground tool bit as viewed form the end . Side rake controls the type of chip produced during machining as well as the direction in which the chip will travel .A tool with a small side-rake angle will produce shorter chips than one with a large rake angle .7 .The nose angle is the angle between the side-cutting edge and the end-cutting edge .Classes of Single-point T oolsDifferent shapes of tool bits are needed to do certain machining operations . Most tool bits are ground to cut in one direction only .The two common types are referred to as right cut and left cut .These were formerly called right-hand and left-hand tool bits .A right-cut single-point tool is one that , when viewed form the point end with the face up , has its cutting-edge on the right side .When the tool bits is placed in the lathe , the cutting-edge is on the left side .This tool bit cuts form the right to the left , or form the tailstock end toward the headstock of the lathe .A left-cut tool bit has the cutting-edge on the left when viewed form the point end with the face up . This tool bit is ground to cut form the left to the right or toward the tailstock of the lathe .Commonly used types of tool bits include the following:1.A roughing tool is a tool bit designed to take heavyroughing cuts to reducethe diameter of a workpiece to approximate size . Because finish is notimportant when roughing work , such a tool bit may be ground to almost a sharp point . However , the point is usually rounded very slightly to prevent its breaking down .2.A finishing tool is one that has a keenly ground cutting-edge which may behoned with an oilstone to produce a very smooth finish ,A finish toolgenerally has a larger rounded nose than a roughing tool .3.A roundnose cutting tool is a general-purpose tool used for many types ofwork .When ground flat on the top , it can be used for both right and left cuts and for turning brass . It may also be used to form a radius at the corner of a shoulder . Roundnose tool bits are used as finishing tools .4.The square-nose tool cuts on the end only . It is used for chamfering and forroughing cuts to square a shoulder .5.A cutoff or parting tool cuts on the end only and is used for cutting off stockor workpieces held in a chuck .6.Side-facing tools or side tools , as they are often called , are used forfinishing the ends of work square and smooth .A right-cut side-facing tool is always used to finish the end of a shaft . A left-cut side-facing tool may be used to finish the left side of a shoulder .Chip BreakersTo eliminate the problem of a continuous chip , a chip breaker is often ground on a high-speed steel tool bit .Chip breakers can either be ground on an off-hand grinding wheel , or in the case of the grooved chip breaker , it can be done with a thin grinding wheel on a surface grinder .A separate chip breaker is often used with insert-type carbide tools .Cutting ActionIn lathe turning , there are three basic cutting forces , the longitudinal force of the workpiece against the side of the tool , the radial force of the workpiece against the front of tool , and the tangential force of the workpiece against the top of the tool . The tangential cutting force is by far the greatest and has the most influence on the cutting action . This tremendous force is exerted against the cutting-edge . Pressures as great as a quarter-million pounds per square foot have been measured on large metal-cutting lathes . If the tool is shaped incorrectly or set at an incorrect angle ,it will dull rapidly .Here is what actually happens when cutting on the lathe ,As the workpiecemeets the cutting-edge of the tool bit , chips or a continuous ribbon of metal are wedged away from the material being machined ,On soft , ductile material , this wedging is continuous. On harder materials , the wedging force causes the metal to compress . Compression continues until a shearing point is reached , and the compressed metal is separated from the workpiece . This is repeated throughout the cutting operation .The shape is much more important than the actual sharpness of a cutting-edge . Lack of clearance permits the tool to drag on the workpiece , greatly increasing the pressure on the cutting-edge and interfering withtool performance .Too-large clearance angles make the tool weak and do not edge breaks off or wears out rapidly .Grinding a High-speed Steel Tool BitA tool bit is ground:1.To provide a sharp cutting-edge2. To obtain the correct or best shape for a particular operation3. To provide clearance away form the end of the tool bit4. To provide clearance away form the side of the tool bit5. To provide good chip movement over the face of the tool bit and away the cutting-edgeHere is the correct procedure for grinding a right-cut roundnose tool bit :1.Check the grinding wheels to make certain the faces of the wheels aredressed properly. It is difficult to grind good cutting tools on wheels that areuneven or have grooves in them. Use a bench or floor grinder that is used only for grinding cutting tools. Such a grinder should have a coarse-gritaluminum-oxide wheel on one side and a fine-grit wheel on the other side.Use the coarse-grit wheel for finishing the tool bit to shape. Then use thefine-grit wheel for finishing the tool bit.2.The tool grinder should be equipped with tool rests. Rest your hands on themto control the movement of the tool bit. Hold the tool bit firmly to keep itform bouncing around on the wheel. Do not grip it so tightly,however, that you have difficulty move it.3.Grind the side-relief angle to form the side-cutting-edge angle by holding thetool bit against the wheel, as shown in Fig 18. This angle should be about 6 for mild steel. Hold the tool bit against the wheel, and tilt the bottom inward to get this angle. As you grind, move the tool bit back and forth across the face of the wheel without changing its position. This helps to grind the tool faster and prevents grooving the wheel. As the tool bit heats up, dip it inwater to cool it. A beginner often makes the mistake of moving the tool bit up and down. This forms many different angles on the flank, and it becomesvery irregular. To avoid this, hold the tool bit in affixed position on the wheel.Move it back and forth, but never up or down.4.Grind the side-relief angle on the opposite side to form the shape of the toolbit, as shown in.5.To grind the end-relief angle, holds the tool with the and up. Swing the shankof the tool bit in a semicircle. Try to blend the end radius to meet the sides neatly and cleanly. Always ease up on the pressure when grinding theroundnose of the tool bit. If you fail to so this, you woll grind a largerroundnose tool than desired.6.To grind side rake for a right-cut tool bit, hold the tool bit, face or top, atright angles to the right side of the grinding wheel. Tilt thetool inward at the bottom. Hold it in this position until the wheel cleans up the entire face to the cutting-edge. To grind the side-rake angle for a left-cut tool bit, hold the tool bit at the left side of the grinding wheel. Tilt the bottom inward, and let the grinding wheel clean up the entire face to the cutting-edge. There is noreason to grind the face of the tool bit below the shank at the front end. To do so wastes the expensive tool bit and results in a poorly shaped cutting tool.7.It is good practice to hone tool bits used for finishing work. Select amedium-fine oilstone. Apply a little kerosene or lard cutting oil to theoilstone. Move the cutting-edge back and forth against the oilstone. Be sure to hold the bit flat so as not to change any anglesWith a little practice, you will be able to grind a tool bit correctly. Remember, a well-ground bit is one that has proper tool angles together with flat, evenly ground surface.CARE OF LATHESKeep the lathe clean and well lubricated at all times. Like any precision machine, the lathe requires careful treatment. It will operate better and do accurate work as long as you care for it properly. Do not make the mistake of relying upon others to keep the lathe oiled and in good repair. Your own personal safety depends upon your ability to keep the lathe in a safe operating condition. The proper care of a lathe includes such things as cleaning, oiling, adjusting, and making minor repairs.Cleaning the latheClean the lathe thoroughly after each work period. Whenchips and dirt are left on ways, gears, and other moving parts, the surfaces become roughened and dented. This causes fast wear and makes it difficult to operate the parts. The following procedure is recommended for cleaning a lathe:1. Use a brush first to remove all chips.Most chips are razor sharp, so never use your hands.A 2in paintbrush or a small bench brush is convenient for this purpose. Move the tailstock to the right end of the bed.2. Wipe off all painted surfaces with a clean cloth or cotton waste. Oil left on the painted surfaces becomes hardened and steins the paint.3. Using the same cloth or cotton waste, remove oil and grease form all machined surfaces.4. Brush all chips form the chip pan, them wipe it clean.5. Before mounting a chuck, clean its inside threads with a wore thread cleaner. Wipe off the spindle threads, and place a drop or two of oil on them.6. Clean the spindle holes and taper shanks of centers before mounting them in place. If centers have burrs or rough spots on them, use a file or an oilstone to remove them before placing the centers in the spindle holes.7. Occasionally, clean the thread grooves of the lead screw with a piece lf cord. Place the cord around the lead screw. Adjust the gears to turn the lead screw at a medium sped. Start the lathe, and with the lead screw turning, move the cord back end forth as it feeds along the screw.8. When oiling a lathe, wipe off any oil that may spill or drip on the painted surfaces.9. Always make certain there is a light film of oil on the ways before you start to work.10. Adjust the cross-feed and compound slide gib screws to remove looseness or play between the parts. When you can move the cross-feed by grasping the tool post with your hand and moving it back and forth, it means the gib screws are too loose. Adjust each of the gib screws until a smooth movement is obtained on the cross-feed handle. When they are properly adjusted, it will not be possible to move the cross-feed by pulling or pushing on the tool post.11. Never lay tools or workpieces on the ways of a lathe. To do so destroys the accuracy of these precision handscraped surfaces.place your tools on to lathe board.12.When using a tool-post grinder, always protect the machined surfaces of the lathe by covering them. Abrasive particles from the grinding wheel can become imbedded in the surface bearings end soon destroy the accuracy of the lathe if surfaces are not covered during the grinding operation.13. Once a week wipe down the entire lathe with a Clean cloth dampened with kerosene. Do the painted surfaces first, then the machined surfaces. Wipe dry, and place a thin film of clean oil over all machined surfaces.Oiling and Greasing the LatheIt is important that the lathe be properly lubricated. An oiling or lubrication chart comes with each machine. Be sure to use the grades and kinds of oil and grease called for in the chart. Form the habit of oiling your lathe each day before you start work. Certain parts require daily oiling. Other parts should be oiled weekly or monthly as the chart says. Too often, when several persons use the same lathe, each one depends on the other, and the result is that no one does the oiling or maintenance.刀具和刀夹想顺利的加工工件,就必须做到:1.刀具或刀片的种类要恰当。
数控车床刀库设计参考文献英文
数控车床刀库设计参考文献英文DESIGN OF AN AUTOMATIC TOOL CHANGER WITH DISCMAGAZINE FOR A CNC HORIZONTAL MACHININGCENTERAbstract--Automatic tool changers (ATCs) are devices used in CNC machine tools to exchange the tool in the spindle with the tool in the magazine. In this paper, the design of the ATC of a CNC horizontal machining center which was realized for a CNC machine tool manufacturer is introduced. After examination of several alternatives, it was decided to implement the disc-type ATC. A magazine was designed with 24 tools with a maximum tool diameter of 150 mm and a maximum tool weight of 8 kgf. The designed ATC can change the closest tool within 4 s and thetool farthest away within 6 s. ? 1997 El~vier Science Ltd. All fights reserved 1. INTRODUCTIONAny machine tool manufacturer must either pay for the patent of any particular CNC machine tool, or design its own system to manufacture CNC machine tools. Buying a new technology is an expensive alternative, and it is not generally allowed to make any modifications and developments on the purchased system. The machine tool manufacturers refrain from selling new technologies developed by themselves, and they are generally willing to sell their abandoned technologies.Therefore, a particular CNC machine tool manufacturer has started research and development studies for the design and production of a newCNC horizontal machining center. It was required to design a new systemof ATC for this particular machine tool.An ATC can be defined as a device which can select and change tools from a tool storage magazine according to the commands given by the machine control unit.Various types of ATC with quite different working principles havebeen used in horizontal machining centers produced by the different machine tool manufacturers [1-17]. A tool storage magazine is generally either a chain type or a disc (carousel) type. However, nowadays, there are some other types of magazines such as spherical, cassette, etc. [17].Disc-type magazines may be categorized according to the functions of the discs.(1) In a "disc with a changer arm"-type magazine, the tools are changed by means of an arm which takes the tool from the magazine and exchanges it with the one in the spindle. Therefore, the disc has the functions of indexing and storing the tools only [1-5]. Some examples of this type are shown in Fig. l(a) [1], Fig. l(b) [1] and Fig. l(c) [5].(2) A "disc without a changer arm"-type magazine acts like a tool changer arm. The tools are changed by the disc itself [2, 6--8]. An example of this type is shown in Fig. 2 [1 ]. As shown in the figure,two disc magazines and two spindles mounted on a turret exist in this application.In an ATC with chain-type magazines [9-16], the tool is changed by a changer arm. Chain-type magazines may be categorized according to theorientation of the tools in the magazine with respect to the spindle axis as follows.(1) The axes of the tools on the magazine are perpendicular to the spindle axis and the magazine is on either the right- or left-hand side of the column. Therefore, in order to change the direction of the tools, an arm takes the tool and makes a rotation about a vertical axis to bring the new tool to the position parallel to the spindle axis as shown in Fig. 3(a) [13]. In another version of this type, the tool pots, where the tools are located, are rotated about their own axis to become parallel to the spindle axis, as shown in Fig. 3(b) [12]. The changer arm exchanges the tools between the tool pot and the spindle axis.(2) The axes of tools on the chain magazine are in a plane parallel to the spindle axis. As shown in Fig. 3(c) [12], there is only one position of the tool at which the cutting tool becomes parallel to the spindle axis, and the tool is changed at that position. There is an arm which exchanges the tools between the spindle and the magazine.(3) The axes of tools on the magazine are parallel to the spindle axis. The arm which is in between the spindle and the magazine takes the tool and does a linear motion to approach the spindle and exchange the tools as shown in Fig. 3(d) [16].In Table l, different ATCs and their minimum "tool to toolchange times" (T/T) are given based on the trade literature [2-5, 7-14]. In Table 1, "D+A", "D" and "C+A" designate "disc-type magazine with changer arm", "disc-type magazine without changer arm", and "chain-type magazine with changer arm", respectively. In disc magazines, as the number of tools increases, the diameter of the disc increases, which is an undesirable situation from the space point of view. However, in a chain type, the number of tools is approximately 1.5 times that of the tools in the disc type in the same space [18]. The ATC of the chain typecan store many tools in a very small space. However, the chain-type magazines are expensive compared with the disc-type magazines.2. DESIGN OF ATCIn the stage of clarifying the design specifications for a CNC machine tool, supply and demand in the particular market, potential customers' preferences, specifications of competitors' products which can be obtained from the related trade literature, price of CNC machine tools, etc. should be considered. In accordance with the desired features of the CNC machine tool, the design specifications of ATC are determined.By considering the basic design criteria as simplicity, relatively low cost, relative ease of manufacture, assembly, disassembly, maintenance, and availability of spare parts, a "disc magazine without changer arm"-type ATC was considered to be designed for the particular CNC horizontal machining center [19].Table I. Tool mass and tool change time data for automatic tool changers of various machine tools available in the marketAs shown in Fig. 4, the tool-changing cycle of the designed ATC includes the following basic steps.Step 1. The spindle approaches the magazine to insert the old tool into the tool pocket (Fig. 4(a)).Step 2. After the drawbar releases the old tool, the magazine goes forward along the A-A direction (Fig. 4(b)).Step 3. To bring the new tool into the tool changing position as soon as possible, the magazine is rotated in a clockwise or counterclockwise direction about its axis, depending on the relative position of the tool on the magazine (Fig. 4(c)).Step 4. The magazine is retracted back to insert the new tool into the spindle (Fig. 4(c)).Step 5. When the control unit takes the message from the spindle that the drawbar has been operated to draw the new tool safely, the spindle is let go to start the new machining cycle (Fig. 4(d)).After the decision concerning the type of ATC and the workingprinciple to be used, the specifications for the "disc magazine without changer arm"-type ATC were determined as follows [20]. 1. The number of tools stored (i.e. number of tool stations) in the magazine is 24.2. The maximum tool diameter is 100 mm when the adjacent tool pockets are full.3. The maximum tool diameter is 150 mm when the adjacent tool pockets are empty.4. The maximum weight of the tool including that of the tool holder is 8 kgf.5. The tool holder type is BT40 [21].6. Tool changing times are 4 s and 6 s for the closest and farthest tool on the magazine, respectively.In the following subsections, basic components of the particular ATC are presented.2.1. Disc magazineThe minimum diameter of the disc-type magazine is calculated by considering the specified number of tools to be stored and the maximum tool diameter. A distance between successive tools to be stored in the magazine should be left. The diameter of the disc magazine was calculated as 812 mm by leaving 6 mm between successive tools [19]. After the diameter of the disc magazine has been calculated, the shape of the disc magazine is determined. Low inertia has primary importancebecause of the frequency of acceleration and deceleration of the disc magazine. This can beobtained by using a light material. Aluminium is selected as the material for the disc magazine. A thin walled disc geometry with appropriate webbing which ensures necessary stiffness should be considered.The structure of the disc magazine was made as simple as possible to reduce the cost of the pattern to be used for casting the magazine. A simple sketch is shown in Fig. 5 [19].2.2. Sliding bodyIn any of the ATC systems, there have to be extraction andretraction motions to take the tool holder out of the spindle or to insert a new one. In the "disc without changer arm"-type ATC, the magazine should make a back and forth motion. This necessitates asliding body. These motions can easily be achieved by either a hydraulic or a pneumatic piston. In fact, there are some other methods of having a linear motion such as using a ball screw toconvert the rotary motion into linear motion. However, this methodis extremely expensive when only a simple repetitive motion cycle is required.As seen in Fig. 6, the sliding body was designed hollow to reduce the weight [19]. At the rear, there is a space for the encoder and the coupling inside the body. A pneumatic piston was selected and implemented to push and pull the sliding body. The very back of the body was closed with a lid to which the pneumatic piston was assembled. The slides of the sliding body were designed as square edge but not of dovetail type. The reason for using the square edge type of slide is the ease of manufacturing, price and limited space advantages.2.3. Shock absorbersFor each tool-change cycle, the magazine performsforward-backward motion by the sliding body, which takes up most of the cycle time. To reduce this time. higher traverse speeds are preferred. However, a problem arises concerning the deceleration, where an extremely high level of kinetic energy must be absorbed over a very short distance to stop the system without causing excessive shock loads or vibration. Shock absorbers can be used for this purpose.In the design, a pneumatic piston was used. Owing to the compressibility of the air, pneumatic pistons have sharply rising force characteristics towards the end of the stroke during the cushioning operation. Most of the energy is absorbed near the end of the stroke [22]. Therefore, shock absorbers are required. The pressure generated in front of the particular shock absorber piston remains constant throughout the entire stroke, as the velocity is reduced to zero owing to the specific spacing of the orifices. Consequently, the resisting force remains constant and uniform, and therefore linear deceleration is achieved [22].2.4. Clamping of the toolsThe tools on the disc magazine are kept in the pockets with clamps. The tool may be held between clamping jaws. The clamp is designed in such a way that a tool with a maximum weight can be safely held. Since the disc magazine rotates about its axis, the centrifugal force adds up to the weight of the tool. This is consideredduring the design of the clamping system. The tool pocket and clamping jaws are designed according to the tool-holder type specified. Clamping jaws should have appropriate mating surfaces which fit into the specified tool holder.The tools are kept in the pockets by a combination of leaf andhelical springs which have been designed to hold a tool with a maximum weight of 8 kgf safely [19]. The jaws have tapered surfaces which fit the tool holder of the BT40 [21].2.5. A shield to protect the tool holders from chipsIn design of an ATC, some protective measures are necessary. Ifany chip sticks on to the tapered surface of the tool holder beforeitis inserted into the spindle shaft, it will not be accurately seated in the spindle shaft and will cause run-out, inaccuracy and repeat-ability problems, and the chip may damage the spindle taper. To prevent these, the tool holders should be protected from the chips by a shield which opens just before the spindle reaches the tool change position (Fig. 7) [19]. The shield is kept closed during the machining processes.2.6. Motor and speed reductionThe rotation of the disc can be provided by using a motor and speed reducer combination. After the decision has been made for the type ofmotor, the power and torque requirements are calculated to select an appropriate motor.By considering the positional accuracy and the repeatability, an AC brushless servo motor was used for the rotation of the disc magazine [19]. The motor was selected which can give 4.5 Nm and 0.94 kW rated torque and rated power values, respectively, for At=60 K and 5.5 Nm and1.2 kW for At=-100 K. The motor has a rotational speed of 2000 rpm [23].2.7. Speed reductionSpeed reduction between the magazine and the motor may be provided through worm gear, planetary gear train, harmonic drive, etc. Abacklash-free reduction is necessary for accurate positioning of the tools relative to the spindle bore center while changing the tools. A timing belt is another method which can ensure a zero backlash power transmission. However, high reduction is very difficult to obtain with timing belts in a very small area. Very high reduction ratios canbe obtained with worm-gear sets in a very small area. However, wormgears have back lash problems. Moreover, for high reductions, the efficiency of the system decreases abruptly. If the reduction is done with a very low efficiency worm gear, the required capacity of the motor size gets bigger, which in turn increases the cost of the motor and its control system. In zero backlash worm gears, the worms are of split type and their tooth profiles are special [24].In planetary-gear systems of low prices, the back lash eliminationis obtained by just decreasing the center distance between the gearsuntil a minimum clearance condition is reached without too much noise or heating up. This normally causes high starting torque because of interference, and much lower running efficiency than the same with a normal backlash condition. There are only a few companies in the world which manufacture zero backlash planetary gear trains [25].The harmonic drive is another way of having a zero backlash reduction. The advantages of harmonic drive can be stated as follows[26].(1) The positional accuracy is quite good. The harmonic drivegearing's design ensures that approximately 10% of the total teeth are engaged at any point in time, which minimizes the effect of tooth-to-tooth error.(2) Because of the simple structure of the harmonic drive, it isvery easy to incorporate into a housing which is easy to manufacture, since the machining required is simple in-line boring and turning operations.(3) Since the harmonic drive has a very compact structure and very light weight, the assembly and disassembly are very easy. (4) It is cheaper than any other zero backlash gearing. Because of the above advantages and after the necessary calculations, the harmonic drive was selected and implemented in the ATC [26]. Assuming that half rotation of the disc magazine, including the time elapsed for acceleration and deceleration of it, is completed in 2 s, the rotational speed of the magazine is calculated as 16.67 rpm. This requires a 120:1 reduction toreduce the 2000 rpm motor output to 16.67 rpm magazine rotation. The harmonic drive was selected to obtain 50:1 reduction together with a spur gear pair providing 2.4:1reduction. The output shaft of the harmonic drive is connected to a pinion with the pitch circle diameter of 125 mm which meshes to a gear with a diameter of 300 ram. The gear is bolted on to the disc magazine [19].2.8. Encoder and control switchesThe position of the magazine is very important to insert the right tool into the spindle. This can be provided by using an absolute or incremental encoder. An encoder can also be used for counting the tool stations, which is necessary to index the required tool. Encoders are very sensitive devices which are capable of giving very precise output. If the cables of the encoder are affected by some means from the environment (i.e. interference), the message that is sent to the control unit will be different from its real value. Therefore, another method of counting the tools is recommended to support the encoder as a safety precaution. A switch to count the tools can be used for this purpose. The signals sent by the switch and the encoder are compared to prevent any mistake while indexing the tools. Absolute encoders are expensive when compared to theincremental encoders. As shown in Fig. 6, the positioning of the magazine was achieved by using an incremental encoder directly assembled on the axis of the disc magazine and not on the motor as is normal withservo drive. The angular positioning backlash problem was overcome by placing an incremental encoder directly connected to the disc magazine and situated within the sliding body.The incremental encoder was selected with 3600 lines per revolution.A proximity switch was placed on the sliding body near the disc magazine as a safety precaution. The switch is actuated by 24 dogs mounted on the disc magazine. So, for each tool, there is one dog which actuates the switch, thus enabling both counting of the tool stations and providing a signal to the control unit.Several switches are also required for control purposes. Since the ATC has a rotation axis, the control unit should be capable of recognizing the reference point of the rotation. Otherwise, the control unit does not know the positions of the reference tool and the other tools. Since an incremental encoder was used, a proximity switch was placed on the sliding body to set the home position. If an absolute encoder were used, there would be no need for a home switch since the absolute encoders know at which absolute position they are.A drawbar is a drawing unit, which is used in spindles to pull the tool holder. The ATC and drawbar should work sequentially, otherwise serious problems may occur. To synchronize the operation of the drawbar, the sliding body and rotation of the magazine, two limit switches were used for the front and rear positions of the sliding body to give reliability while changing tools. Anotherproximity switch was placed within the spindle which senses whether the drawbar unit is in its clamp position or not. If the switch is not actuated, it means that either the tool holder is not clamped or it is improperly clamped.The tool pocket which will pick the tool in the spindle must be unoccupied before the approach of the spindle, otherwise a crash occurs, which causes damage to the tools, spindle and magazine. To prevent such damage, a proximity switch was used to check whether the particular tool pocket was occupied (Fig. 7) [19]. 3. IMPLEMENTATION AND TEST OF AUTOMATIC TOOLCHANGERThe particular CNC horizontal machining center wasmanufactured and assembled. Each system was tested and runseparately or as a whole of the machine tool by the CNC machine tool manufacturer. At the end of the tests, it was reported that everything within the ATC was running without any problems. The designed ATC was tested for which the T/T for the closest tool is 4 s, whereas it is 6 s when the farthest tool is of concern. The particular machine tool was used in the production line in the particular CNC machine tool manufacturer without any reported problems relating to the designed ATC system.4. CONCLUSIONIn this paper, the working principle and the design criteria of an ATC with a disc magazine without a changer arm has been presented. This type of ATC has been found to be suitable for the particular CNC machine tool manufacturer when considering the design period,the compulsion being to enter the market as quickly as possible. The minimum T/T for the designed ATC, which is 4 s, is quite reasonable when compared with those given in Table 1. Therefore, the realized ATC system has provided a competitive position for the machining center in the market.Acknowledgements—The authors wish to express theirappreciation to TAKSAN Machine Tool Industry and Trade Co., Kayseri, Turkey, for support in the design and manufacturing of the particularATC. The authors also thank METU Prof. Dr Mustafa N. Parlar Education and Research Foundation, and METUCAD/CAM/ROBOTICS Center, Ankara, Turkey, for allowing theirfacilities to be used in this study.REFERENCES[1] A.N. Kobuladze and L.M. Prupis, Automatic tool changers for machining centers with horizontal spindles, Machines and Tooling 45(5), 56 (1974).[2]Sidepalsa Trade Literature. Sidepalsa Sistemas De Paletizacion, S.A., Spain.[3] NTC Trade Literature. NTC Nippei Toyama Corporation, Japan.[4] Olivetti Trade Literature. Olivetti Controllo Numerico SpA, Italy.[5] Mandelli Trade Literature. Mandelli SpA, Piacenza, Italy. [6] Bridgeport Trade Literature. Bridgeport Machine Tools, U.K. [7] White--Sundstrand Trade Literature. White-Sundstrand, White Consolidated Machine Tool Group, IL,U.S.A.[8] Leadwell Trade Literature. Leadwell Machine Tools, Taiwan.[9] Mazak Trade Literature. Yamazaki Mazak Corporation, Japan.[10]Burkhard+Weber Trade Literature. Burkhard+Weher GmbH Werkzeugmachinenfabrik, Reutlingen, Germany.[11]Matsuura Trade Literature. Matsuura Machinery Corporation,Fukui-City, Japan.[12] Mauser-Werke Trade Literature. Mauser-Werke GmbH, Oherndorf, Germany.[131 Hitachi Seiki Trade Literature. Hitachi Seiki Co. Ltd, Japan.[14] Mechanicy Trade Literature. Mechanicy, Czechoslovakia. [I 5] Cincinati Milacron Trade Literature, Cincinati Milacron, Cincinati, OH, U.S.A.[16] Hwacheon Trade Literature. Hwacheon Machinery, Seoul, South Korea.[17] Starrfrdsmachinen Trade Literature. Starrfrllsmachinen AG, Larigidesa Rigid Ltd, Switzerland.[18] Fudow Tool Pots Trade literature. Fudow Chemical Co. Ltd, Japan.[19] M.B. Ko~, Design of automatic tool changer for CNC machines.M.Sc. thesis, Mechanical EngineeringDepartmet, METU, Ankara, Turkey 1995.[20] TAKSAN Machine Tool Industry and Trade Co., Turkey,Private communication.。
- 1、下载文档前请自行甄别文档内容的完整性,平台不提供额外的编辑、内容补充、找答案等附加服务。
- 2、"仅部分预览"的文档,不可在线预览部分如存在完整性等问题,可反馈申请退款(可完整预览的文档不适用该条件!)。
- 3、如文档侵犯您的权益,请联系客服反馈,我们会尽快为您处理(人工客服工作时间:9:00-18:30)。
Boolean operations for 3D simulation of CNC machiningof drilling toolsDani Tost*, Anna Puig, Lluı´s Pe´rez-VidalSoftware Department, Polytechnical University of Catalonia, Spain Accepted 25 April 2003AbstractThis paper addresses the simulation of drilling tools CNC machining. It describes a novel approach for the computation of the boundary representation of the machined tools. Machining consists of a sequence of Boolean operations of difference between the tool and the grinding wheels through time. The proposed method performs the dynamic Boolean operations on cross sections of the tool and it reconstructs the 3Dmodel by tiling between the cross sections. The method is based on classical computational geometry algorithms such as intersection tests,hull computations, 2D Boolean operations and surface tiling. This approach is efficient and it provides user control on the resolution of the operations.Abstract This paper addresses the simulation of drilling tools CNC machining. It describes a novel approach for the computation of the boundary representation of the machined tools. Machining consists of a sequence of Boolean operations of difference between the tool and the grinding wheels through time. The proposed method performs the dynamic Boolean operations on cross sections of the tool and it reconstructs the 3Dmodel by tiling between the cross sections. The method is based on classical computational geometry algorithms such as intersection tests,hull computations, 2D Boolean operations and surface tiling. This approach is efficient and it provides user control on the resolution of the operations.q 2003 Elsevier Ltd. All rights reserved.Keywords: CNC simulations; Bores machining; Computationalgeometry; Boolean operations; Surface tiling1. IntroductionMost of the research on CNC in CAD is centered on theautomatic computation of tool paths [5,13]. Given a final tool design, the optimal trajectories of the tool and the grinding wheels must be computed yielding as final result the CNC code. Machining simulation and verification hasexactly the opposite goal: to calculate the tool starting from the CNC code and from a geometrical model of the machine, the wheels and the tool before machining. This simulation has three main applications [6]. First, it detects eventual collisions between the tool or any of the grinding wheels and the rest of the machine. It is important to avoid collisions because serious damages to the machines can follow. Next, simulation provides a means of visually verifying the efficiency of the trajectories, which may result in faster and cheaper processes. Finally, the simulation allows users to check if the surface of the resulting tool is effectively the desired one. In the routine practice of machining, experienced operators have enough skills to imagine the tool final shape by only reading the CNC code.However, they are generally not able to do so with new or non-standard designs. Therefore, the use of a simulation system decreases considerably the tool production cost because it avoids the trial and error process on the real machine with costly materials that is otherwise necessary.This paper addresses a particular type of CNC machining simulation: the grinding of bores and cutters. Conventional CAD systems do not provide a means of realizing this type of simulations and specific applications are needed. Until recently, most of thesimulation applications dealt only with the machining of 2D cross-sections of the tools and they were restricted to the main fluting operation [3]. Three dimensional applications are rather recent [4,23]. They provide a machining simulation for specific 5-axes machines and they are not applicable to general movements. This paper presents a novel approach for the computation of the external shape of the tools through a sequence of coordinated movements of the tool and the wheels on machines of up to 6-axes. The proposed method reduces the 3D problem to 2D dynamic Boolean operations followed by a surface tiling. The 2D solution involves different techniques of planar computational geometry: from intersections to hull computations.The paper is structured as follows. In Section 2 we review previous approaches on machining simulations.Section 3 describes briefly the contour conditions of the simulation. Finally, Section 4 describes the computation of Boolean operations and the results of the implementation are shown in Section 5.2. Previous workMachining can be considered a dynamic Boolean operation of difference between the grinding wheel and the tool. It is dynamic, because both the tool and the wheels move along time through rotations and translations.The Vector Cut [8,10], is probably the most referenced numerical control simulation method. It is an approximate solution that represents the frontier as a set of points and normal vectors that will be cut along the path of the grinding wheel. This method is effective for the simulation of sculptured surface polishing, but it is not extensible to complex motions of the tool and/or the grinding wheels. It is mainly useful to detect mistakes in the path suggestedby the presence of abnormally high or small cut vectors. Besides, except for the extension of Ref. [16], it does not yield directly a model of the bit to be machined.An alternative strategy for machining simulation consists of realizing a sequence of 3D static Boolean operations through time. The main drawback of this strategy is its high computational cost. According to Ref. [11], this is proportional to the number of discrete positions to the fourth. This puts it out of question, in practical terms.Another problem it shows is the granularity of the temporal discretization : it must be very fine if precision in the final tool is required. This means that very little material is cut off in each Boolean operation, and that may entail robustness problems in the computations. A possible method to avoid both problems is to discretize the initial tool model into a voxel or an octree model, [20], to perform all the sequence of Boolean operations on the discrete model and then reconstruct the machined surface, at the end. This approach benefits from the fact that the cost of discrete Boolean operations is much lower and the reconstruction phase at the end of the process is done as late as possible. This option requires the sequence of movements to be specified in terms of relative motion of the grinding wheel, while the tool and its discretization remain fixed. This prerequisite is not always valid and, in particular, it does not hold for the general case of 6-axes machines.Finally, another option taken into account is that of the computation of the volume swept by the tool and the grinding wheel in their motions. A geometric representation of this volume would allow performing only one Boolean difference operation between the two volumes. The main difficulty of this option is the computation of sweptvolumes. There are several references [1,2,21] on this subject, that contain methods generally applied in CAD for extrusions, collisiondetection, and other problems but none of them can be applied to the non-trivial case of simultaneous motion of the two solids in play.The strategy proposed herein overcomes the disadvantages of these methods. It consists of a double discretization of four dimensional space (3D þ time) that reduces the general problem to a sequence of 2D Boolean operations and 3D geometric reconstructions. This algorithm is fast and it provides user-control on simulation accuracy.3. Scene modelThere are different types of machine tools for the fabrication of bores and cutters. They share the same general structure but they differ in the number of degrees of freedom. The method proposed herein deals with machines up to six degrees of freedom. These machines have a static vertical axis (Z in Fig. 1 on which the grinding wheel set can move up and down. One tool is placed on a spindle (the toolholder), that may translate on three axes (X; Y and U) and rotate on two axes (W in relation to the wheel axis and A relative to its own axis). At the beginning of the process, a tool has a piecewise cylindrical or conical shape. Its final shape is the result of a sequence of machining operations consisting of simultaneous movements of the tool and the wheels. The wheel shape is also piecewise cylindrical or conical. It remains unchanged during the process.The machining process is divided into a set of operations, each one with a specific name in CNC jargon. Each operation is performed using a specific wheel. This information is written in the CNC file.Specifically, the main operations are (in their usual order):Fig. 1. 6-Axes machine tool.Fig. 2. Machining operations on a tool.* Fluting: performing the lateral helicoidal of straight grooves* Gashing: cuts in the tool head* Outer diameter sharpening: edge sharpening of the lateral grooves* End face sharpening: edge sharpening of the tool head cuts* Notching: direct cut in the tool head.Fig. 2 shows a real bore and it indicates the operations that have given its shape.Each operation performs several symmetrical cuts in the tool shape. The tool shown in Fig. 2, for instance, has three lateral grooves realized during the ‘Fluting’ operation. Each cut is performed through a sequence of movements. In the CNC code, each movement corresponds to a line instruction specifying the motion axes (X; Y;U; A; or W for the tool and Z for the wheel) along with the amount of rotation or translation to be performed for each edge.4. Machining simulation4.1. OverviewOur approach uses the fact that the tools have a tubular shape. It consists of discretizing the tool in axial sections, performing the machining operations on these crosssections and finally, reconstructing the surface of the tool by tiling between cross-sections. Before machining, the cross-sections are circles. Afterwards, they have a complex shape that may even have been split into separate connected shells at the tool end.The movements are divided into blocks, each one corresponding to an CNC operation or even to one cut within an operation. The machining process is performed sequentially for each block. Therefore, as many intermediate models are created as instruction blocks exist. The initial tool is taken as input of the first machining process. Theresulting tool is used in the second block processing and so on. The surface reconstruction step can be performed on any of these intermediate models or, alternatively only on the last one.Therefore, the simulation process of each instructions block is composed of two steps:* A 2D Boolean operation process, that receives as input: (i) the tool representation, (ii) the machining wheel representation, (iii) a list of movements and that gives as output a new representation of the tool cross-sections.* A tiling process that completes the tool representation with the triangulation between contours.The second step, surface tiling, is a classical subject in computer graphics [14]. It consists of two related problems: (i) establishing correspondences between contours (branching problem) and (ii) searching correspondent vertices to form tiles (correspondence problem). Several solutions have been published to solve both problems based on minimizing the distance between successive contours [7,17] and interpolating in between contours [12]. The method used herein is an extension of these algorithms that adds to these criteria the constraint of tiling between segments of the contour corresponding to the same machining operation. This extension is described in depth in Ref. [22].4.2. Machining of the tool cross-sectionsThe computation of the new shape of tool cross section consists of three steps:* Computation through time of the intersections of the wheel cross sections and the external contour of the tool section. Bothsections are circular and, due to their relative orientation, their intersection is a segment. Therefore, the result of this step is a set of segments.* Calculation of the hulls of the segments set. These hulls are polygonal approximations of wheel cuts on the tool section.* Reconstruction of the tool cross section contour given its original shape and the hull curves.The pseudo-code algorithm below illustrates this process. Let st be the tool cross section at the beginning of the process, where the wheel and ml the movements list. The wheel is discretized into a set of circular cross-sections switch (procedures FirtSectWheel and NextSectWheel). The movement of switch and st is decomposed into a a set of successive positions (inner loop). For each position, the intersection between sw and st is computed in the procedure InterSect. If there is intersection, then the corresponding segment segm is stored in the segments list seglist. Then, the geometry of st, sw and seglist is updated to next positions in the procedure UpdateGeom. The position of st is reset at its initial location for each new wheel section. After all the wheel sections have been processed, the hulls of the segment list are computed in CompHulls and then clipped against the initial contour of st with the procedure Reconstruct.procedure CrossSection Machining(st: tSection,wh: tWheel, ml: tMovList)varsw: tSectionsegm: tSegmentseglist: tSegmentListhulls: tHullListfvarInitSegList(seglist)sw U FirstSectWheel (wh)while ValidSection(sw) doendo f mov U FALSEwhile : endo f mov doInterSect(st,sw, &segm, &status)if status ! InsertSegment(segm, seglist) endifUpdateGeom(ml, &st, &sw, &seglist, &endo fmov)endwhilesw U NextSectWheel(wh,sw)ResetToolPosition(&st)endwhileCompHulls(slist, &hulls)Reconstruct(hulls, &st)fprocedure4.2.1. Updating geometryEach movement instruction is realized at constant speed. Therefore, a movement can be decomposed into n constant intervals of translation in X; Y; Z and U along with rotation in W and A : δA=ΔA/n,δW=ΔW/n,δX=ΔX/n,δY=ΔY/n,δU=ΔU/n andδZ=ΔZ/n.As mentioned in Section 3, a line movement can be composed of several simultaneous instructions. Most of the tool movements are composed of translations and axial rotations, which are independent. Therefore, the order in which the update of each movement is done is irrelevant. However for conical tools with a round end called ‘ball nose’, simultaneous axial translations and colum n angle rotations are necessary. These two movements are obviously not independent. Thiscan be a source of error (Fig. 3) because the real machine rotates the tool column angle at the same time as it translates it along its axis, while in the simulation, for each time interval, the tool is first rotated and next translated along its axis. However, in these cases the original CNC is already decomposed as a set of very small movements with a resolution very similar to the one needed in the machining. Therefore, these movements are not further decomposed in the machining.The global coordinate system in which the geometry is expressed along time is sketched in Fig. 4. The axis coincide with the machine axis X; Y and Z at the tool home position at the beginning of machining. Let ct(xtk, ytk;,0.0)be the coordinates of the tool section center at instant k: The components of the normal vector of the section are ntk(nxtk, nytk,0.0). It should be noted that nxtk =cos(ωk) and nytk= sin(ωk); being vk the column angle of the tool at instant k: The updated values of these coordinates at k +1.Fig. 3. Non equivalent transformations.Fig. 4. Coordinate system, axes and motion.5. Conclusions and future workThis paper describes a novel method for the simulation of drilling tools CNC machining. Our approach simplifies the 4D (space t time) Boolean operations between the tool and the wheels by reducing them to a sequence of intersections between 2D perpendicular cross-sections along time. Specifically, the method discretizes the toolinto cross-sections and simulates machining on the cross sections. Next, the shape of the tool is recomputed by tiling between contours.The primary advantage of this approach is its simplicity. It addition, it provides user-control on the resolution of the simulation: spacing between crosssections as well as time interval between consecutive intersections.Starting from this work, new research and development lines are opened. Specifically, we are working on global pipelines that would put into the same process automatic CNC computation and tool verification. With such pipelines, given a final tool description, theCNC code to create it would be automatically computed, next using the CNC code as input, tool machining would be simulated. Finally, differences between the input and the output model could be computed and shown.钻探工具数控加工三维仿真的布尔运算摘要本文旨在对钻探工具数控加工的仿真研究。