DCS集散控制系统学习教程
DCS系统基础教程

4、 DCS的控制程序是由谁执行的? DCS的控制决策是由过程控制站完成的,所以控
制程序是由过程控制站执行的。
5、 过程控制站的组成如何? DCS的过程控制站是一个完整的计算机系统,主
要由电源、CPU(中央处理器)、网络接口和I/O组 成
6、 I/O是什么? 控制系统需要建立信号的输入和输出通道,这就是 I/O。DCS中的I/O一般是模块化的,一个I/O模块上 有一个或多个I/O通道,用来连接传感器和执行器 (调节阀)。
二、EPKS系统介绍 ❖ 1.操作员站安装 ❖ 1.1环境要求 ❖ ◆操作系统:WINDOWS 2000 Professional (英
文)+SERVICE PACK 3 或更高。 ❖ ◆应用软件: IE 6.0或更高; ❖ ◆屏幕分辨率:不小于1280*1024;24位或32位真
彩色
❖ ◆C盘空间不少于10G的硬盘空间。 ❖ ◆建立一个名为ps_user的用户,并且让此用户具有
低了—控制器, 网络, 和服务器的负荷.
Experion PKS 服务器特点
❖ 可以使用标准的,开放的硬件。降低硬件 及备件成本。加快硬件更新速度
❖ 内含历史数据库,提供长期的数据存储 ❖ 高级报警管理 ❖ 支持基于服务器和画面的微软脚本Basic
语言-VBScript ❖ 通过Honeywell的专有DSA (Distributed
13、I/O信号是如何分类的? 常用的I/O信号一般分为:AI、AO、DI和DO。 AI--模拟量输入信号 AO--模拟量输出信号 DI--数字量输入信号 DO--数字量输出信号
14、什么是DCS的开放性? DCS的开放性是指DCS能通过不同的接口方便地及第 三方系统或设备连接,并获取其信息的性能。这种 连接主要是通过网络实现的,采用通用的、开放的 网络协议和标准的软件接口是DCS开放性的保障。我 公司目前采用的DCS系统有很好的开放性。
DCS控制系统培训讲义(艾默生Deltav)教学教材

DeltaV系统的控制网络采用TCP/IP的通讯协议 ,系统自动分配各节点的IP地址。每套DeltaV系统 可支持最多120个节点。
一套DCS一般分为以下几大部分:
•过程站(PS:Process Station):主要功 能是完成现场数据采集和控制,它是系统的核心 部分。
•操作站(OS:Operator Station):主要功 能是完成监视、操作、过程管理,实现人机对话。
•通讯网络(LAN:Local Area Network): 主要功能是实现在各连接物理设备之间的数据传 递。
编程的一般步骤:
•网络组态:设置固定IP地址,每个DCS厂家 有自己的固定IP设置。Deltav系统的网络组态, 在安装软件时自动设置完成,不需要更改。
•工作站/操作站组态:组态工程师站和操作 员站。(例如一台工程师站,两台操作员站)
•硬件组态:组态电源类型,CPU类型,卡件 类型(AI、AO、DI、DO)根据实际应用进行组态 类型。
红庙锅炉DCS控制系统 培训讲义
艾默生Deltav系列
第一章、Deltav系统概述 第二章、Deltav系统网络 第三章、Deltav系统硬件 第四章、Deltav软件及操作
第一章、Deltav概述
第一节、 锅炉控制方案概述 第二节、 Deltav 系统概述
第一节、 锅炉控制方案概述
随着自控技术的发展并结合我公司从事锅 炉自控系统设计的多年经验,我公司可为用户提 供三种锅炉自控解决方案: 一、 常规热工二次仪表 和智能仪表控制方案
DCS集散控制系统学习教程

DCS集散控制系统学习教程幻灯⽚1第⼆章集散控制系统(D C S)幻灯⽚22.1D C S的形成、发展和特点2.1.1D C S的概念集散控制系统(D i s t r i b u t e d C o n t r o l S y s t e m)亦称分布式控制系统(简称D C S),是结合多种先进技术⽽形成的,对⽣产过程进⾏集中监测、操作、管理和分散控制的⼀种控制技术,是随着现代⼤型⼯业⽣产⾃动化的不断发展和过程控制要求的⽇益复杂应运⽽⽣的⼀种综合控制系统,是完成过程控制、过程管理的现代化设备。
幻灯⽚3国外称集散控制系统是4C技术的产物。
这4C就是指控制技术(C o n t r o l)、计算机技术(C o m p u t e r)、通信技术(C o m m u n i c a t i o n)、和C R T(C a t h o d e R a y T u b e)技术。
D C S既不同于分散的仪表控制,⼜不同于集中式计算机控制系统,是4C技术相互渗透发展⽽产⽣的。
幻灯⽚42.1.2D C S的发展情况过程控制设备的发展历史,⼤概有以下⼏个阶段:30年代——机械式仪表现场操作;40年代——⼤型⽓动式仪表控制室操作;50年代——⽓动单元组合仪表控制室操作;60年代——电动单元组合仪表;70年代——集散控制系统。
即经过了就地分散控制――模拟仪表集中控制――计算机集中控制――计算机分散控制(D C S)⼏个阶段。
集散控制系统从诞⽣之⽇起,已经历了三代,⽬前的第四代正在发展之中。
幻灯⽚5●D C S开创期:1975~1980年●代表产品:H o n e y w e l l,T D C2000●F O X B O R O,S p e c t r u m●B a i l y,N-90●恒河,C E N T U M这些第⼀代的集散控制系统以微处理器为基础的过程控制单元,实现多种控制功能算法,并实现分散控制;采⽤带显⽰器的操作站,与过程控制单元分离,实现集中监视、集中操作、信息综合管理;采⽤较先进的冗余通信系统、⽤同轴电缆作为传输媒质,实现控制单元与操作站的通信,已具有D C S的基本特点(即分散控制,集中管理),是D C S的雏形。
DCS系统入门培训
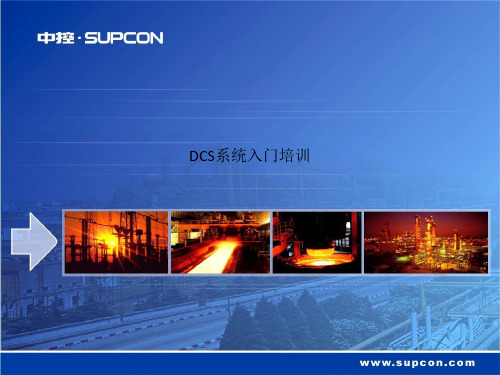
Input (Anolog Input、Digital Input)
控制器处理:线性转换、限幅、滤波、小信号切除等
控制器
I/O卡件:D/A转换
Output (Anolog Output、Digital Output)
现场调节阀、电池阀、电机等:4-20mA、DO….
执行器
DCS输入信号
➢ 热电阻; ➢ 热电偶; ➢ 0~10mA、4~20mA电流; ➢ 0~5V、1~5V电压; ➢ 开关量(数字量)输入;即现场干触点或电平信号; ➢ 其他信号;
微分作用(D)
➢ 原理:根据将来趋势调节
➢ 提高稳定性, 使比例和积分强度可以 增加,提高控制性能。
➢ 虽然理论上很完美, 但受搞频噪声影响严重, 实际中除了惯性大的 对象(温度)以外, 用得较少
PID对控制性能影响
➢ 控制器增益 Kc或比例度PB 增益增大(即Kc 增大或比例度PB下降),调节作用增强,但稳定性下降;
强度关系 P越大,比例越 弱
积分时间Ti Ti越大,积分越弱
微分 改进控制性能
微分时间Td Td越大,微分越强
被控对象特性分类
➢ 流量:一般响应速度较快,宜用PI ➢ 压力:响应速度既有快的,也有慢的,PI ➢ 液位:一般精度要求不高,可用P ➢ 温度:典型的慢对象,控制精度要求高,建议采用
PID
从人工控制到自动控制
➢ 操作人员: 通过长期实践,积累阀门调节的经验
➢ 自动控制专家: 将这些经验转化为数学语言,让计算机(DCS主控卡 )代替人脑调节阀门。 ——通过编程,使计算机具有了一定的智能
PID(比例、积分、微分)
定量地解决了: (1) 关多少? (2) 持续多少时间? (3) 关闭速度为多少? (4) …
DCS基础知识培训讲义

DCS系统组成与结构
系统组成
包括过程控制级、监控操作级和 管理决策级三个层次,每个层次 由相应的硬件和软件组成。
结构特点
采用分布式结构,将控制功能分 散到各个智能节点上,通过网络 实现节点之间的信息交换和协调 控制。
DCS基础知识培 训讲义
目录
• DCS概述与基本原理 • 硬件设备及接口技术 • 软件配置与组态设计 • 网络通信与数据传输技术 • 系统维护与故障排除方法分享 • DCS发展趋势及新技术应用前景探讨
01
CATALOGUE
DCS概述与基本原理
DCS定义及发展历程
DCS(Distributed Control System )即分布式控制系统,是一种基于微 处理器技术的控制系统,具有分散控 制、集中监视、操作和管理等功能。
大数据技术可以帮助DCS处理海量数据,挖掘有 价值的信息,优化控制策略,提高生产效率。
融合应用
云计算和大数据技术的融合将为DCS提供更强大 的数据处理和分析能力,推动工业智能化发展。
人工智能技术在DCS中创新应用案例分享
故障诊断与预测
通过人工智能技术,DCS可以实现故障的早期发现和预测,减少 停机时间,提高设备利用率。
工作原理及数据传输方式
工作原理
DCS通过实时数据采集、处理和控制算法运算,实现对被控对象的精确控制。 同时,通过网络将各个节点的状态信息和数据汇总到上位机,进行集中监视和 管理。
数据传输方式
DCS采用标准的通信协议和接口,支持多种数据传输方式,如以太网、现场总 线等,确保数据的实时性、可靠性和安全性。
2024年DCS培训教程
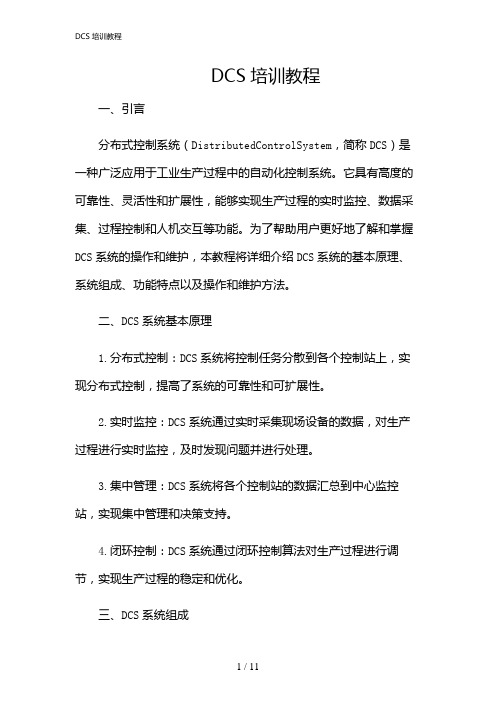
DCS培训教程一、引言分布式控制系统(DistributedControlSystem,简称DCS)是一种广泛应用于工业生产过程中的自动化控制系统。
它具有高度的可靠性、灵活性和扩展性,能够实现生产过程的实时监控、数据采集、过程控制和人机交互等功能。
为了帮助用户更好地了解和掌握DCS系统的操作和维护,本教程将详细介绍DCS系统的基本原理、系统组成、功能特点以及操作和维护方法。
二、DCS系统基本原理1.分布式控制:DCS系统将控制任务分散到各个控制站上,实现分布式控制,提高了系统的可靠性和可扩展性。
2.实时监控:DCS系统通过实时采集现场设备的数据,对生产过程进行实时监控,及时发现问题并进行处理。
3.集中管理:DCS系统将各个控制站的数据汇总到中心监控站,实现集中管理和决策支持。
4.闭环控制:DCS系统通过闭环控制算法对生产过程进行调节,实现生产过程的稳定和优化。
三、DCS系统组成1.控制站:控制站是DCS系统的核心部分,负责对现场设备进行监控和控制。
每个控制站通常包括处理器、输入/输出模块、通信模块等。
2.现场设备:现场设备包括传感器、执行器、变送器等,用于采集现场数据和执行控制指令。
3.通信网络:通信网络是连接各个控制站和现场设备的纽带,负责数据的传输和交换。
常见的通信网络有以太网、串行通信等。
4.操作站:操作站是DCS系统的人机交互界面,用于显示生产过程的实时数据和报警信息,以及进行操作和监控。
5.数据库服务器:数据库服务器用于存储和管理DCS系统的历史数据和配置信息。
四、DCS系统功能特点1.高可靠性:DCS系统采用冗余设计,保证系统的高可靠性。
在某个控制站或通信网络发生故障时,其他控制站可以接管其工作,确保生产过程的正常运行。
2.灵活性:DCS系统采用模块化设计,可以根据生产过程的需要进行灵活配置和扩展。
同时,DCS系统支持多种通信协议和接口,方便与其他系统进行集成。
3.开放性:DCS系统采用开放式架构,支持多种操作系统和编程语言,方便用户进行二次开发和定制。
DCS集散控制系统课件教学教材
DCS在大美煤炭深加工项目中的应用
• 甲醇制烯烃(I/O点4919个) • 聚乙烯(I/O点1637个) • 聚丙烯(I/O点3037个) • 公用工程(I/O点2824个)
DCS在大美尾气综合利用项目中的应用
中央控制室
甲
醇 制 烯 烃 现 场 控 制 室
聚 乙 烯 现 场 控 制 室
聚 丙 烯 现 场 控 制 室
自控术语定义
• 联锁:某一参数达到规定值或某一设备启、停 或开、关时,联动或闭锁对另一设备的控制。
• FO:故障状态打开的阀门(气关阀) • FC:故障状态关闭的阀门(气开阀)
• 调节器正反作用:当给定值不变,被控变量测 量值增加时,控制器的输出也增加,称为“正 方向”;或者当测量值不变,给定值减小时。 控制器的输出增加称为“正方向”。反之称为 “反方向”。
自控术语定义
• 有源 : 信号源本身可以输出信号,不需要负 载电源,可直接驱动阻性负载, 例如,四线 制的仪表,两线为电源线,两线为信号线,信 号回路不能再接电源。信号回路需要接电源, 否则信号源将无信号输出,例如,两线制变 送器,需要在信号回路中接入电源。
• 无源 : 信号回路需要接电源,否则信号源将 无信号输出,例如,两线制变 送器,需要在 信号回路中接入电源。(针对模拟量)
回 用 水 现 场 控 制 室
烯 烃 循 环 水 现 场 控 制 室
空 分 现 场 控 制 室
锅 炉罐 装区 置现 现场 场控 控制 制室 室
系 统 构 成 例
DCS控制系统简图
工程师站
操作员站
交换机 控制器
I/O卡件
现场仪表
DCS特点介绍
DCS是分布式控制系统(Distributed Control System)的 简称,国内一般习惯称为集散控制系统。它是一个 由过程控制级和过程监控级组成的以通信网络为纽 带的多级计算机系统,综合了计算机Computer)、通 讯(Communication)、显示(CRT)和控制(Control)等4C 技术,其基本思想是分散控制、集中操作、分级管 理、配置灵活、组态方便,DCS特点如下。
DCS系统教程_已看范文
第一章概述第一节集散控制系统的发展概况一、过程控制装置的发展1、过程控制装置概念过程控制装置是实现生产过程自动控制的一类仪器仪表装置,通过过程控制装置实现对生产过程的获取、观察、转换、处理(计量、调节、控制),从而解释生产过程物质运动和能量交换。
过程控制装置一般可分成五大类:(1)自动检测装置;(2)自动显示装置;(3)集中控制装置;(4)自动调节装置;(5)执行器装置。
过程控制装置从最初的自励式、基地式仪表到单元组合式仪表、以及20世纪80年代以后发展的智能化数字仪表、集散控制系统和现场总线,已发展了半个多世纪。
2、过程控制装置及控制系统的发展简述过程控制装置及控制系统的发展经历了四个阶段。
(1)50年代以气动单元组合仪表装置为主,出现了集中型气动仪表控制系统,通过成千上万的气路将现场信号与控制室仪表相接,实现自动控制。
(2)60年代,电子元件晶体管的产生,使电动单元组合仪表得以开发和应用。
它通过各种电气线路将控制室与现场仪表相连,实现电动仪表控制系统。
但其在安全火花防爆方面的缺陷,使得电动仪表控制系统的应用受到了限制。
(3)70年代,采用线性集成电路和小规模数字电路,发展了安全火花防爆型单元组合仪表(DDZ-III)、组装仪表和巡回检测装置,进一步提高电动仪表控制系统的可靠性和安全性,特别是电动单元组合仪表,易于远距离传输、集中显示和操作,便于和计算机连用,使之获得了日新月异的发展。
(4)80年代,采用微处理机和专用集成电路,将微机技术应用在仪表控制系统中,使工业自动化仪表向着数字化、智能化和分级化的方向发展,出现了集中管理分散控制式的控制系统装置以及数字化单元组合仪表,由一个装置控制数个到几十个回路,进行集中管理操作,从而实现对生产过程计算机控制。
二、集散控制系统的发展1、基本概念集散控制系统(Total Distributed Control System,简称DCS)是以满足现代化工业生产和日益复杂的控制对象的要求为前提,从生产综合自动化的角度出发,将微处理器作为核心的集中分散控制系统。
浙大中控DCS基础版教程(2024)
I/O模块类型及作用
2024/1/29
模拟量输入模块
将现场模拟量信号转换为数字信号,供控 制器处理。
模拟量输出模块
将控制器输出的数字信号转换为模拟量信 号,驱动现场执行机构。
开关量输入模块
接收现场开关量信号,将信号状态传输给 控制器。
开关量输出模块
根据控制器指令,输出开关量信号控制现 场设备。
9
控制器区
显示与控制器相关的信息和操作,如控制器状态、变量监控等。
2024/1/29
19
主界面布局及功能区域划分
2024/1/29
图形组态区
用于创建和编辑DCS系统的图形界面 ,包括流程图、趋势图、报警窗口等 。
脚本编程区
提供脚本编程环境,支持用户编写自 定义脚本实现复杂控制逻辑。
20
常用操作命令和快捷键使用
工具栏
位于菜单栏下方,提供常用操作 命令的快捷按钮。
17
主界面布局及功能区域划分
工作区
占据界面中心区域,用于显示和编辑DCS系统的各种元素。
状态栏
位于界面底部,显示当前登录用户、系统时间、版本号等信息。
2024/1/29
18
主界面布局及功能区域划分
工程管理区
用于管理DCS工程文件,包括新建、打开、保存、另存为等操作。
组态软件使用
熟悉浙大中控DCS组态软件的操作界面和基本功能,掌握 建立工程、绘制流程图、配置IO点、编写控制逻辑等步骤 。
控制策略组态
在组态软件中,根据控制策略的要求,配置相应的控制模 块、设定参数、连接信号等,完成控制策略的组态。
36
回路调试技巧和经验分享
调试前准备
检查硬件连接、确认IO点配置正确、 确保控制策略组态无误。
DCS第一章集散控制系统基本原理与其应用
值SV进行比较、运算,将结果以数字信号DS2的形式
输出,经D/A转换器后输出模拟信号AS2去控制执行器。
1.3.1 输入信号处理
• ➢为了实现计算机对生产过程的控制,需要将被控对 象的各种测、控变量按要求的方式送入计算机,以便 运算和处理。
• ➢被控对象所提供的信息是纷繁复杂的,其种类、性 质及大小等各不相同,因此需要通过某种装置将生产 过程中的各种被测变量转换成计算机能够接受的信号, 这种在计算机与生产过程之间,起着信号转换并向计 算机传送信息的装置称之为输入通道。输入通道的信 号处理包括数字量输入信号处理和模拟量输入信号处 理。
散的信息集中起来,进行集中的监视和操作,并实现高级
复杂规律的控制。其结构如图1.7所示。
• ➢集散控制系统是一种典型的分级分布式控制结构。 • ➢监控计算机通过协调各控制站的工作,达到过程的
动态最优化。控制站则完成过程的现场控制任务。 • ➢操作台是人机接口装置,完成操作、显示和监视任
务。 • ➢数据采集站用来采集非控制过程信息。集散控制系
式。
• 1.1.2 硬件系统
•
计算机控制系统由工业控制机和生产过程
两大部分组成。工业控制机是指按生产过程控制的特
点和要求而设计的计算机(一般是微机或单片机),
它包括硬件和软件两部分。生产过程包括被控对象,
测量变送、执行机构、电气开关等装置。计算机控制
系统的组成如图1.2所示。
图1.2 计算机控制系统的组成框图
而易举的事。
•
由于DDC系统中的计算机直接承担控制任
务,所以要求实时性好、可靠性高和适应性强。为了
充分发挥计算机的利用率,一台计算机通常要控制多
个回路,那就要求合理地设计应用软件,使之不失时
- 1、下载文档前请自行甄别文档内容的完整性,平台不提供额外的编辑、内容补充、找答案等附加服务。
- 2、"仅部分预览"的文档,不可在线预览部分如存在完整性等问题,可反馈申请退款(可完整预览的文档不适用该条件!)。
- 3、如文档侵犯您的权益,请联系客服反馈,我们会尽快为您处理(人工客服工作时间:9:00-18:30)。
幻灯片1第二章集散控制系统(D C S)幻灯片22.1D C S的形成、发展和特点2.1.1D C S的概念集散控制系统(D i s t r i b u t e d C o n t r o l S y s t e m)亦称分布式控制系统(简称D C S),是结合多种先进技术而形成的,对生产过程进行集中监测、操作、管理和分散控制的一种控制技术,是随着现代大型工业生产自动化的不断发展和过程控制要求的日益复杂应运而生的一种综合控制系统,是完成过程控制、过程管理的现代化设备。
幻灯片3国外称集散控制系统是4C技术的产物。
这4C就是指控制技术(C o n t r o l)、计算机技术(C o m p u t e r)、通信技术(C o m m u n i c a t i o n)、和C R T(C a t h o d e R a y T u b e)技术。
D C S既不同于分散的仪表控制,又不同于集中式计算机控制系统,是4C技术相互渗透发展而产生的。
幻灯片42.1.2D C S的发展情况过程控制设备的发展历史,大概有以下几个阶段:30年代——机械式仪表现场操作;40年代——大型气动式仪表控制室操作;50年代——气动单元组合仪表控制室操作;60年代——电动单元组合仪表;70年代——集散控制系统。
即经过了就地分散控制――模拟仪表集中控制――计算机集中控制――计算机分散控制(D C S)几个阶段。
集散控制系统从诞生之日起,已经历了三代,目前的第四代正在发展之中。
幻灯片5●D C S开创期:1975~1980年●代表产品:H o n e y w e l l,T D C2000●F O X B O R O,S p e c t r u m●B a i l y,N-90●恒河,C E N T U M这些第一代的集散控制系统以微处理器为基础的过程控制单元,实现多种控制功能算法,并实现分散控制;采用带显示器的操作站,与过程控制单元分离,实现集中监视、集中操作、信息综合管理;采用较先进的冗余通信系统、用同轴电缆作为传输媒质,实现控制单元与操作站的通信,已具有D C S的基本特点(即分散控制,集中管理),是D C S的雏形。
幻灯片6●D C S成长过渡期:1980~1985年●代表产品:未变●第二代的主要特点是在原来产品的基础上进行改进,进一步提高可靠性并扩展和增强了功能。
●其特点是采用模块化、标准化设计,数据通信向标准化迁移,板级模块化,单元结构化,使之具有更强适应性和可扩充性;新开发的多功能过程控制站、增强型操作站采用了16位C P U及高分辨率C R T技术;通信系统已采用局域网络(从主从式的星形变为总线网络或环网通信),使系统通信围扩大,同时数据传输速率也大大提高;控制功能更加完善,它能实现过程控制、数据采集、顺序控制和批量控制功能。
其基本结构由六部分组成,即局域网络、多功能现场控制站、增强型操作站、主计算机、网络连接器和系统管理站等。
幻灯片7●D C S完善期:80年代中后期●代表产品:H o n e y w e l l,T D C3000●F O X B O R O,I/A S E R I E S●B a i l y,I N F I-90●M o o r e,P A C S这阶段的特点是向开放式、标准化方向发展:实现了开放式的系统通信,向上能与M A P 和E t h e r n e t接口,或者通过网间连接器与其它网络联系,构成复合管理系统,并与不同制造商的产品能进行数据通信;向下支持现场总线,它使得过程控制或车间的智能变送器、执行器和本地控制器之间能实现可靠的实时数据通信。
幻灯片8●开放系统是第三代集散控制系统主要特征。
根据X/O P E N协会的定义,以规化与实际存在的接口标准为依据而建立的计算机系统、网络系统及相关的通信系统,这些标准可为各种应用系统的标准平台提供软件的可移植性、系统的互操作性、信息资源管理的灵活性和更大的可选择性。
●开放系统的基本特征如下:●可移植性(p o r t a b i l i t y)●互操作性(i n t e r o p e r a b i l i t y)●可适宜性(s c a l a b i l i t y)可得到性(a v a i l a b i l i t y)幻灯片9●D C S管控一体化时期:90年代初至今●代表产品:●H o n e y w e l l,T P S系统(T o t a l P l a n t S y s t e m)●P K S系统(P r o c e s s k n o w l e d g e S y s t e m)●F O X B O R O,I/A’S50/51系列控制系统I n v e n s y s●横河,C E N T U M-C S●A B B,A D V A N T系统O C S开放控制系统当今的D C S是生产过程控制系统与信息管理系统紧密结合的“管控一体化”的新一代集散型控制系统。
由于工厂、企业的信息集成和管理已经提到一定的高度,D C S系统的功能已不再只局限于生产过程的控制,在整个工厂、集团公司的管理中,D C S也能发挥相应的作用。
幻灯片10D C S发展趋势:向上发展:即向计算机集成制造系统(C I M S:C o m p u t e r I n t e g r a t e dM a n u f a c t u r i n g S y s t e m)、计算机集成过程系统(C I P S:C o m p u t e r I n t e g r a t e d P r o d u c t i o n S y s t e m)等信息化集成化系统发展。
向下发展:即向现场总线控制系统发展(F C S:F i e l d b u s C o n t r o l S y s t e m),把系统控制能力移到现场,使得控制得到最终的分散,减少了输入输出的接口,减少了机柜的空间和附属设备。
幻灯片112.1.3D C S的特点D C S集散控制是一个以通信网为纽带的集中显示、操作、管理、控制相对分散的多级计算机网络控制系统,由过程控制级、控制管理级和生产管理级所组成。
D C S具有通用性强、系统组态灵活、控制功能完善、数据处理方便、显示操作集中、人机界面友好、安装简单规化、调试方便、运行安全可靠等特点。
幻灯片12●分级递阶系统●垂直方向:至少分为两级——操作管理级和过程控制级。
水平方向:相互谐调的分级,把数据向上传送到管理级,同时接收操作管理级的指令,各个水平分级之间相互进行数据交换。
幻灯片13●分散控制●集中:D D C,一旦计算机出现故障,将造成过程操作的全部瘫痪。
分散:不仅是分散控制,还包含其它含义,如人员分散,地域分散,功能分散,设备分散,操作分散等。
目的是使危险分散,提高设备的可利用率。
幻灯片14●自治和谐调性●D C S上各工作站独立自主地完成分配给自己的规定任务,具有控制功能分散,危险分散的特点,提高了系统的可靠性。
各站的容量可扩充,配套软件随时可组态加载,是一个能独立运行的高可靠性子系统。
各自独立的部分通过实时高可靠的工业控制局部网络传送各种信息并协调工作,实现整个系统的信息共享;根据系统的特性对各个工作站进行协调控制,从而完成控制系统的总体功能和优化控制。
幻灯片15●友好性●D C S的人机接口和软件面向工业控制技术人员、工艺技术人员和生产操作人员,操作方便,显示直观,了解生产状况直观。
D C S软件采用实用而简捷的人机会话系统,C R T高分辨率交互图形显示,复合窗口技术,画面丰富,纵观、控制、调整、趋势、流程图、回路一览、批量控制、计量报表、操作指导画面、菜单功能等均具有实时性。
平面密封式薄膜操作键盘、触摸式屏幕、鼠标器、跟踪球等操作设备使其更便于操作。
幻灯片16●适应性、灵活性和可扩充性●D C S的硬件和软件采用开放式、标准化和模块化设计,系统为积木式结构,具有灵活的配置,可适应不同用户的需要。
当工厂根据生产需要改变生产工艺和流程时,可改变系统的某些配置和控制方案,通过组态软件,进行一些填写表格式的操作即可实现。
幻灯片17●在线性与实时性通过人机接口和I/O接口,D C S对过程对象的数据进行实时采集、处理、记录、监视、操作控制,并包括对系统结构和组态回路的在线修改、局部故障的在线维护等,提高了系统的可用性。
幻灯片18●可靠性高可靠性、高效率和高可用性是D C S的生命力所在,系统在设计阶段就采用了一系列可靠性设计技术。
如:容错设计、冗余设计(硬件双重化)、在线故障排除设计以及一系列抗干扰措施,使系统的可靠性得到了全面的提高。
幻灯片192.1.4国D C S的发展情况D C S问世于1975年,生产厂家主要集中在美、日、德等国。
我国从70年代中后期起,首先以大型进口设备成套引入国外的D C S,首批有化纤、乙烯、化肥等项目。
当时,我国主要行业(如电力、石化、建材和冶金等)的D C S基本全部进口。
80年代初期在引进、消化和吸收的同时,开始了研制国产化D C S的技术攻关。
幻灯片20近十几年来,特别是“九五”以来,我国D C S系统研发和生产发展很快,崛起了一批优秀企业,但国外D C S产品在国市场中占有率还较高,其中主要是H o n e y w e l l和恒河公司的产品。
今后几年,D C S作为自动化仪表行业主要产品的地位不会动摇。
幻灯片212.2D C S的体系结构2.2.1D C S的体系结构概述D C S的结构是一个分布式系统,从整体逻辑结构上讲,是一个分支树结构。
其纵向结构分为过程控制级、控制管理级和生产管理级三级递阶结构。
整个系统由3部分构成,即集中管理部分、分散控制监测部分和网络通信部分。
幻灯片22D C S体系结构示意图:幻灯片23D C S系统层次化结构的形成,经历了20世纪60年代的中央计算机集中控制,20世纪70年代的两级自动化控制结构和其后的三层计算机控制系统三个阶段。
右图为三级计算机控制系统图。
幻灯片24D C S系统的体系结构按功能通常分为四级,第一级为直接控制级,第二级为过程管理级,第三级为产品管理级,第四级为经营管理级。
各级之间通过通信网络相连,各级部各站或单元由本级的通信网络进行通信联系。
幻灯片25D C S系统的功能分层图:幻灯片262.2.2D C S体系结构的各层功能D C S体系结构的各级功能,总体上可用下图表示:幻灯片27●直接控制级(过程控制级)在这一级上,过程控制计算机直接与现场各类装置(变送器、执行器、记录仪等)相连,对所连接的装置实施检测与控制,同时接收上层来的管理信息,并向上层传递装置的特性数据和采集到的实时数据。