炉温曲线测试规范
炉温曲线测量管理规程-新版

XXX有限公司文件编号:批准:实施日期:2020.01.01 JJHT/ZLZD-03-2020(02D)版次:A/2 编写:XXX 发放部门:XXX炉温曲线测量管理规程1.目的:指导回流焊锡工艺以及胶水固化的回流炉之温度的设定。
2.适用范围适用于电子分厂SMT生产车间,采用熔点为200-220℃的无铅焊膏、以及使用环氧树脂类型胶水(红胶)进行固化的生产3.定义:无4.职责工程:工程师判断温度profile的正确性。
品质:质量部IPQC按照规定要求监督和检查温度profile的执行情况,并如实记录温度。
生产:生产部技术员按照规定要求设定和测量温度并负责制作测温板5.工作内容5.1炉温测量时间5.1.1 生产线转换机种,过炉前必须测量温度profile。
5.1.2 回流炉维修保养后,开机生产前必须测量温度profile。
5.1.3 回流炉停机4小时以上,开机生产前必须测量温度profile。
5.1.4 同一机种除了开始的时候测量温度profile,回流焊没有中途出现5.1.2、5.1.3、修改炉温和软件、硬件故障等条件下每12H测一次温度profile。
5.1.5 工艺工程师的要求测量温度profile条件下需测量profile。
5.2 测量所需工具5.2.1 高温锡线:成分大致Pb90Sn10,熔点温度约304度5.2.2 PCB:和生产产品类似的PCB。
5.2.3 热电偶:K型,温度测量范围-200~1250℃,精度±1.5℃。
5.2.4 烙铁:烙铁温度可以达到450℃。
5.2.5 手钻:直径约1mm的钻头5.2.6 测温仪:温度profile专用测量仪器。
5.3 测温板的制作:5.3.1 本司规定在温度profile测量中测量3点温度,分别为PCB表面温度、BGA底部温度(如果无其它测量点,BGA测量两点),如果产品中有CPU插座等温度敏感元件也必须测量一点。
如果PCB有其它特殊的地方也需要在该点测量温度。
SMT炉温曲线测试规范方案
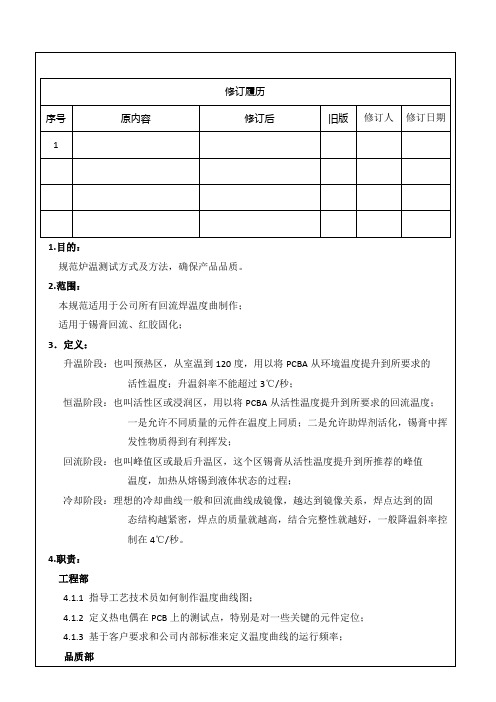
首件确认回流焊的参数设置(可根据公司标准核对),并对曲线进行核对;生产部炉后目检人员定时确认回流焊温度设定是否有更改;5.程序:工具和材料准备:1)高温锡丝(PB88/SN10/AG2---250-300℃)2)红胶(NS3000E、BA-856)3) 热电偶(T-TYPE------350℃)4)测温仪(KIC2000/3000)5)电烙铁6)PCBA (成品板)锡膏工艺炉温测试5.2.1 热电偶探测点位置选取:(图一)工艺工程师应根据PCBA具体情况和关键元件的特殊要求来决定测试点位置,一般情况按以下选取点位:1)各种类型的BGA\QFN;2)PLCC、QFP、TOSP类型元件;3)在一块PCB吸热容量最大和最小的元件;4)湿敏感元件;5)以前制程中从未遇过的异型元件;6)PCBA中元件过密处选点;7)PCBA上均匀分布处选点,可以发现PCBA上不同位置上的温度偏差;(图一)测试点的选取5.2.2 热电偶的选取:(图二)探头须完好,且耐高温;5.2.3 热电偶的焊接:5.2.3.1 .用热传导性较好的胶固定热电偶,用高温锡丝固定应尽量使焊点小而且要光滑,焊点不能跨越3个焊盘,这样可以减少热传导从而提高温度的准确性;(图二、热电偶导线选取)5.2.3.2. 用吸锡带将要焊电偶的焊盘清理干净5.2.3.3. 然后把电偶探头放在所需要焊接的地方,均匀加热(如图三)(图三、电偶焊接指导)5.2.3.4. 再加锡使锡均匀扩散到焊盘处,焊好后将电偶导线分开(如图二OK的)5.2.3.5 正常情况电偶焊在元件焊点上,但是考虑湿敏感元件潜在的危险,故要将探头固定在元件的本体上,测量本体温度(因为元件本体与焊点温度很可能不一致,如图四)(图四、湿敏感元件)5.2.3.6. BGA 焊热电偶方法比较特殊,需要测量BGA内部的温度,要在PCB上打孔(如图五)5.2.3.7. 一般针对复杂的产品至少需要5个测试点以上,简单的产品至少需3-4个测试点即可;5.2.3.8. 在测试探头约10MM处须用高温胶固定,避免在使用过程中内应力过大造成断开,对于穿过PCB的的热电偶每隔50-80MM用高温胶固定,不能从元件上走线,在PCB尾部将所有的导线整理在一起并固定;(如图六)(图五、BGA 装热电偶方法)(图六、PCBA装热电偶方法)5.2.3.9. 探测头的插头上必须标明这根线的序号和其测试的元件位置,对于拼版PCB需标明拼版号,分板定义为:按PCB流向先从左到右再从上到下,依次为“板1”“板(图示七)2”“板3”“板4”以次类推(如图七板的流向举例说明:如U1位置,则标明为“U1T”拼版则标“1U1T”以次类推;5.2.3.10 测温板的选择:通常选与所生产的产品一致的测温板,如无发实现,则选相似厚度、尺寸的测温板,元件要相似才更精确(如BGA的产品必须要用实物板);5.2.4炉温曲线测试:5.2.4.1 炉温曲线运行频率:在以下情况需做温度曲线;A 换产品时;B 连续生产没有换线的情况下,每天交接班时;C 长时间停线需要重新确认新线体时;D 客户有特殊要求时;。
炉温测试仪回流温度曲线技术要求

炉温测试仪回流温度曲线技术要求一般而言,回流温度曲线可分为三个阶段:预热阶段、回流阶段、冷却阶段。
①预热阶段:预热是指为了使锡水活性化为目的和为了避免浸锡时进行急剧高温加热引起部品不具合为目的所进行的加热行为。
•预热温度:依使用锡膏的种类及厂商推荐的条件设定。
一般设定在80~160℃范围内使其慢慢升温(最佳曲线);而对于传统曲线恒温区在140~160℃间,注意温度高则氧化速度会加快很多(在高温区会线性增大,在150℃左右的预热温度下,氧化速度是常温下的数倍,铜板温度与氧化速度的关系见附图)预热温度太低则助焊剂活性化不充分。
•预热时间视PCB板上热容量最大的部品、PCB面积、PCB厚度以及所用锡膏性能而定。
一般在80~160℃预热段内时间为60~120see,由此有效除去焊膏中易挥发的溶剂,减少对元件的热冲击,同时使助焊剂充分活化,并且使温度差变得较小。
•预热段温度上升率:就加热阶段而言,温度范围在室温与溶点温度之间慢的上升率可望减少大部分的缺陷。
对最佳曲线而言推荐以0.5~1℃/sec的慢上升率,对传统曲线而言要求在3~4℃/sec以下进行升温较好。
②回流阶段:•回流曲线的峰值温度通常是由焊锡的熔点温度、组装基板和元件的耐热温度决定的。
一般最小峰值温度大约在焊锡熔点以上30℃左右(对于目前Sn63 - pb 焊锡,183℃熔融点,则最低峰值温度约210℃左右)。
峰值温度过低就易产生冷接点及润湿不够,熔融不足而致生半田,一般最高温度约235℃,过高则环氧树脂基板和塑胶部分焦化和脱层易发生,再者超额的共界金属化合物将形成,并导致脆的焊接点(焊接强度影响)。
•超过焊锡溶点以上的时间:由于共界金属化合物形成率、焊锡内盐基金属的分解率等因素,其产生及滤出不仅与温度成正比,且与超过焊锡溶点温度以上的时间成正比,为减少共界金属化合物的产生及滤出则超过熔点温度以上的时间必须减少,一般设定在45~90秒之间,此时间限制需要使用一个快速温升率,从熔点温度快速上升到峰值温度,同时考虑元件承受热应力因素,上升率须介于2.5~3.5℃/see之间,且最大改变率不可超过4℃/sec。
炉温测试规范
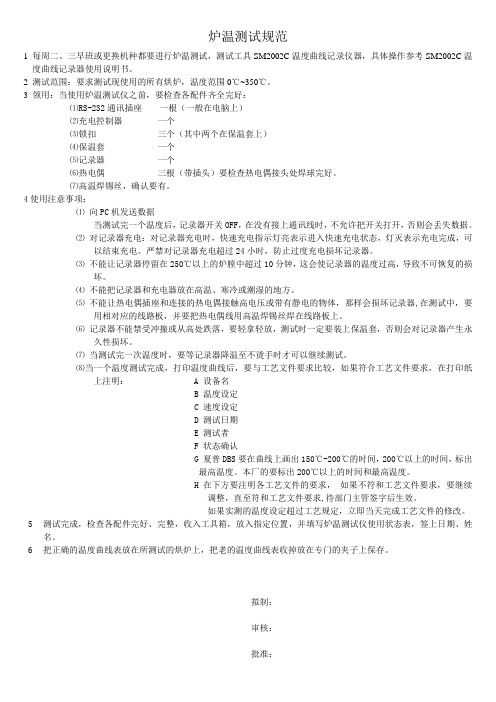
炉温测试规范1 每周二、三早班或更换机种都要进行炉温测试,测试工具SM2002C温度曲线记录仪器,具体操作参考SM2002C温度曲线记录器使用说明书。
2 测试范围:要求测试现使用的所有烘炉,温度范围0℃~350℃。
3 领用:当使用炉温测试仪之前,要检查各配件齐全完好:⑴RS-232通讯插座一根(一般在电脑上)⑵充电控制器一个⑶锁扣三个(其中两个在保温套上)⑷保温套一个⑸记录器一个⑹热电偶三根(带插头)要检查热电偶接头处焊球完好。
⑺高温焊锡丝,确认要有。
4使用注意事项:⑴向PC机发送数据当测试完一个温度后,记录器开关OFF,在没有接上通讯线时,不允许把开关打开,否则会丢失数据。
⑵对记录器充电:对记录器充电时,快速充电指示灯亮表示进入快速充电状态,灯灭表示充电完成,可以结束充电。
严禁对记录器充电超过24小时,防止过度充电损坏记录器。
⑶不能让记录器停留在250℃以上的炉膛中超过10分钟,这会使记录器的温度过高,导致不可恢复的损坏。
⑷不能把记录器和充电器放在高温、寒冷或潮湿的地方。
⑸不能让热电偶插座和连接的热电偶接触高电压或带有静电的物体,那样会损坏记录器,在测试中,要用相对应的线路板,并要把热电偶线用高温焊锡丝焊在线路板上。
⑹记录器不能禁受冲撞或从高处跌落,要轻拿轻放,测试时一定要装上保温套,否则会对记录器产生永久性损坏。
⑺当测试完一次温度时,要等记录器降温至不烫手时才可以继续测试。
⑻当一个温度测试完成,打印温度曲线后,要与工艺文件要求比较,如果符合工艺文件要求,在打印纸上注明: A 设备名B 温度设定C 速度设定D 测试日期E 测试者F 状态确认G 夏普DBS要在曲线上画出150℃-200℃的时间,200℃以上的时间,标出最高温度。
本厂的要标出200℃以上的时间和最高温度。
H 在下方要注明各工艺文件的要求,如果不符和工艺文件要求,要继续调整,直至符和工艺文件要求,待部门主管签字后生效。
如果实测的温度设定超过工艺规定,立即当天完成工艺文件的修改。
炉温测试板制作及曲线测试规范
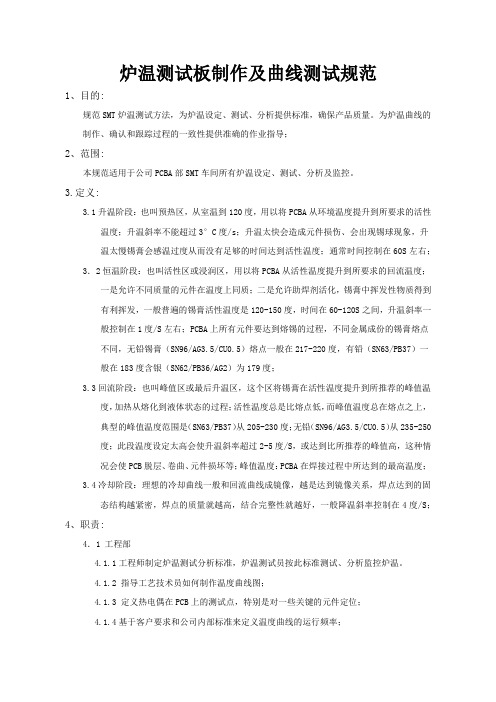
炉温测试板制作及曲线测试规范1、目的:规范SMT炉温测试方法,为炉温设定、测试、分析提供标准,确保产品质量。
为炉温曲线的制作、确认和跟踪过程的一致性提供准确的作业指导;2、范围:本规范适用于公司PCBA部SMT车间所有炉温设定、测试、分析及监控。
3.定义:3.1升温阶段:也叫预热区,从室温到120度,用以将PCBA从环境温度提升到所要求的活性温度;升温斜率不能超过3°C度/s;升温太快会造成元件损伤、会出现锡球现象,升温太慢锡膏会感温过度从而没有足够的时间达到活性温度;通常时间控制在60S左右;3.2恒温阶段:也叫活性区或浸润区,用以将PCBA从活性温度提升到所要求的回流温度;一是允许不同质量的元件在温度上同质;二是允许助焊剂活化,锡膏中挥发性物质得到有利挥发,一般普遍的锡膏活性温度是120-150度,时间在60-120S之间,升温斜率一般控制在1度/S左右;PCBA上所有元件要达到熔锡的过程,不同金属成份的锡膏熔点不同,无铅锡膏(SN96/AG3.5/CU0.5)熔点一般在217-220度,有铅(SN63/PB37)一般在183度含银(SN62/PB36/AG2)为179度;3.3回流阶段:也叫峰值区或最后升温区,这个区将锡膏在活性温度提升到所推荐的峰值温度,加热从熔化到液体状态的过程;活性温度总是比熔点低,而峰值温度总在熔点之上,典型的峰值温度范围是(SN63/PB37)从205-230度;无铅(SN96/AG3.5/CU0.5)从235-250度;此段温度设定太高会使升温斜率超过2-5度/S,或达到比所推荐的峰值高,这种情况会使PCB脱层、卷曲、元件损坏等;峰值温度:PCBA在焊接过程中所达到的最高温度;3.4冷却阶段:理想的冷却曲线一般和回流曲线成镜像,越是达到镜像关系,焊点达到的固态结构越紧密,焊点的质量就越高,结合完整性就越好,一般降温斜率控制在4度/S;4、职责:4.1 工程部4.1.1工程师制定炉温测试分析标准,炉温测试员按此标准测试、分析监控炉温。
波峰焊炉温曲线测试操作规程
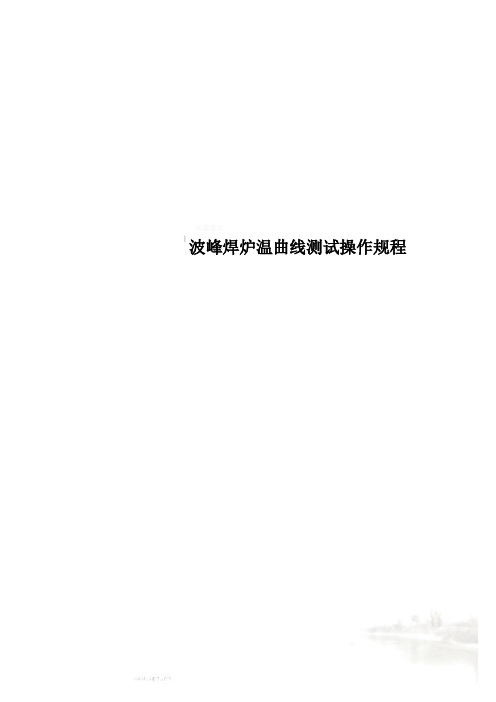
波峰焊炉温曲线测试操作规程Q/HXX/XX-XXXX-XX/XX-XXXX 波峰焊炉温曲线测试操作规程2014年12月01日发布2014年12月05日实施1.1.为规范产品波峰焊接制程,确保产品焊接的可靠性。
对波峰炉温进行监控,以提高产品质量。
适用范围:公司所有经波峰焊接产品之炉温曲线测量。
作业时间:3.1新产品试流时须进行测试;波峰现有3条线体,周一和周五每条线各测试一次,因炉温测试仪器需与车间共用,需与SMT车间错开测试时间。
测温板的制作公司波峰焊接产品,全部都是放在载具上过炉,故测试放在载具上的PCB板DIP插件焊点的温度曲线。
选取测试点一般选取三个及以上的焊点进行测试。
焊点位置按照如下要求选取:4.1.1波峰非焊接面DIP焊点,用于测试过炉时PCB锡反面的温度。
4.1.2引脚密集、焊盘孔小的DIP器件。
曲线参数标准设定(SAC-3JS温区)5.1.1锡膏型号:Define Your Own Spec。
熔点:183波峰炉:SAC-3JS(2温区)5.1.2 预热段温度110—145℃预热时间:30—60s回流段温度 183℃以上回流时间:2—5s最高温度:233--255℃曲线参数标准设定(MWSI温区)5.2.1锡膏型号:Define Your Own Spec。
熔点:183波峰炉:MWSI温区(3温区)5.2.2预热段温110—145℃预热时间:40—60s回流段温度 183℃以上回流时间:2—5s最高温度:233--255℃曲线参数标准设定(MPS-400B温区)5.3.1锡膏型号:Define Your Own Spec。
熔点:183波峰炉:选择性波峰焊MPS-400B(4温区)5.3.2 预热段温度110-145℃预热时间:40—60s全球偏好:设置测量单编辑制程界限:硬件状态:显示开始测试温度曲线:按照浏览温度曲线:管退出:退出软件图二温度:摄氏产品开始测试时的最高温度:33℃±2℃温度测试硬件:SlimKIC 2000,数据储存语言:中文简体-Simplify 工程师密码:不勾选图三6.4 编辑制程曲线(图四)制程界限名称:若要新添加制程界限,可自行命名。
回焊炉温度曲线量测规范
A.升温斜率(25-150℃):<4.0℃/Sec (200-250℃): <2.0℃/Sec
B.浸泡时间: (155℃-190℃): 60-120Sec
C.回流时间: (over217℃):60-120Sec
D.最高温度:焊点温度>230℃
(Peak Temperature参照下图,BGA类最高温度Target:240℃)
Falling slope
25℃-125℃
Above150℃
140℃-160℃
Peak-130℃
<4℃/S
60-120sec
<4℃/S
设定二:
Rising slope
Reflow time
Peak temperature
Falling slope
25℃-125℃
Above125℃
125℃-150℃
Peak-130℃
D.最高温度
焊点最高温度:>210℃
BGA零件温度:<220℃
其它零件温度:<235℃
E.冷却斜率:BGA上表面球要大于1.0℃/sec
4.3.3无铅Sn3.0Ag0.5Cu制程检验标准
检查项目
A.升温斜率(25-150℃):<3.0℃/Sec (200-250℃): <1.5℃/Sec
B.浸泡时间: (155℃-190℃): 60-120Sec
217升温速度3℃/S以下冷却速度<3℃/S
217℃以上60-120sec
190
155
升温速度
<3℃/S
155~190℃: 60 ~ 120sec
Rising slope
Time between
波峰焊炉温曲线测试规
文件名称波峰焊炉温曲线测试规范生效日期页码3/6口处,并以少量红胶固定于PCB上(图4.3.1.2)。
测温端点皆不可以被定位红胶黏着覆盖。
(图4.3.1.2)。
3. 电解电容通孔一条: 选择电容负脚,测温点放置在负极通孔内部,且不可露出板面,如无则选择,则选择通孔零件的地脚。
4. Dwell time(触锡时间):靠近PC板中央托盘大开孔处钻孔(孔径约1.0mm),测温点需突出底面板面约1~1.5mm。
5. 选择最靠近托开孔的2颗BGA各一条, 量测点放置在距离托开孔较近处,需选择信号焊盘埋设。
6. DIMM区域一条: 于托架大开孔区(建议优先选取DIMM的位置)顶面选一连接大铜箔的贴片焊盘,可将零件移除用高温锡丝将测温端点焊于焊盘上。
(图4.3.1.2.7)7. 电解电容电解电容本体表面一条,测温端点以高温锡丝焊接于电解电容上方表面并以少量红胶(<0.4MM见方)进行固定,若板上无电解电容时则可不测。
(图4.3.1.2.8).8. 选择托开孔上方或最靠近托开孔的顶面SMT 区域,如QFP或SOP零件,需选择其一,使用高温锡丝将测温端点焊接于一支信号焊盘与零件脚中间,参考图4.2.1.2.2。
文件名称波峰焊炉温曲线测试规范生效日期页码5/64.5 用鼠标点击桌面“O-DA TAPRO”,输入效验码6个8,分别输入产品信息。
(客户、产品型号,线别、温区数量及温度、链条速度等等)4.6 将数据下载线与TC-60K II连接,点击“下载”等待下载完后关闭电源开关,提取产品温度曲线,并打印存档。
(保存在电脑指定位置,便于追溯)4.7 根据5.0项的要求分析产品温度曲线是否在标准范围内,如果产品参数测试不合格,依据标准参数重新设置波峰焊产品参数,待温度稳定后按4.10-4.12步骤重新设置测试,直到产品参数测试合格后方可以过炉生产。
4.8 产品在波峰焊接中如果出现有空焊、连锡不良时,应重新制定产品曲线参数。
炉温曲线标准
炉温曲线标准1.目的提供回流炉焊接曲线参考范围,确保产品焊接质量。
2.范围该工艺规范适用于SMT 回流炉生产单双面板。
3.定义无. 4.职责工艺工程师: 制定维护回流温度控制工艺规范, 在试产中过程中产品工艺工程师针对不同产品进行回流曲线设置, 曲线设置参数作为技术文件在量产后移交给制造部.工艺工程师在量产后根据产品品质状况进行优化回流曲线参数设置, 继续对炉温参数设置进行优化调整.现场工程师(设备/工艺) : 确认回流炉温度曲线是否正常.工艺技术员: 回流温度曲线测试.IPQC:确认回流曲线是否经过工程师确认,并发现异常情况进行反馈给工艺工程师. 5.作业内容5.1回流炉设定温度参照下表执行,不同的产品可参考该范围进行回流曲线设置。
锡铅合金焊接工艺:5.2回流炉温度曲线示意图:(锡铅焊接工艺参考曲线)250220℃180℃备注:该图形仅供参考,温度设定参考上表数据进行, 在实际测的曲线与该参数范围内有少许差异时, 工程师根据现场品质状况与测试板的状态进行现场分析确认, 如工程师判为合格则签字确认.5.3采用无铅焊料合金焊接的回流炉温度要求。
5.3.1无铅焊料合金的选择无铅焊料合金采用锡/银/铜(Sn/Ag/Cu,简称:SAC305),合金成份范围(重量%):Sn/(96.5%),Ag/(3.0%),Cu(0.5%) ,合金熔点:217℃`5.3.2回流焊接的峰值温度和220℃熔点以上的时间峰值温度范围:245℃+/-5℃;217℃熔点以上的时间:50秒-90秒;升温速度<3℃/秒;降温速度:-1℃/秒_-5℃/秒。
5.3.3. 助焊剂活化温度 150℃-180℃之间的保温时间为: 50-90秒.6.附件无第 2 页共2 页。
波峰焊炉温曲线测试操作规程
Q/HXX/XX-XXXX-XX/XX-XXXX 波峰焊炉温曲线测试操作规程2014年12月01日发布2014年12月05日实施波峰焊炉温曲线测试操作规程共12页第1页1.目的:1.1.为规范产品波峰焊接制程,确保产品焊接的可靠性。
对波峰炉温进行监控,以提高产品质量。
2.适用范围:2.1公司所有经波峰焊接产品之炉温曲线测量。
3.作业时间:3.1新产品试流时须进行测试;波峰现有3条线体,每日周一和周五每条线各测试一次,因炉温测试仪器需与SMT车间共用,需与SMT车间错开测试时间。
4.测温板的制作公司波峰焊接产品,全部都是放在载具上过炉,故测试放在载具上的PCB板DIP插件焊点的温度曲线。
4.1选取测试点一般选取三个及以上的焊点进行测试。
焊点位置按照如下要求选取:4.1.1波峰非焊接面DIP焊点,用于测试过炉时PCB触锡反面的温度。
4.1.2引脚密集、焊盘孔小的DIP器件。
4.1.3引脚焊盘孔大的DIP器件。
4.2埋线给测温线分别编号,如1,2,3……。
1号测温线为探温热电偶,无需固定。
将测温线插入焊盘孔,打上适量红胶,用热风枪加热,直至红胶凝固。
对于4.1.1的测试点,将测温线搭在焊盘上,打上红胶,用热风枪加热固定。
测温板具体使用详见6.5。
5 曲线参数标准设定基于KIC2000测试仪,有铅制程。
5.1曲线参数标准设定(SAC-3JS温区)5.1.1锡膏型号:Define Your Own Spec。
熔点:183℃波峰炉:SAC-3JS(2温区)5.1.2预热段温度110—145℃预热时间:30—60s回流段温度 183℃以上回流时间:2—5s最高温度:233--255℃5.2曲线参数标准设定(MWSI温区)5.2.1锡膏型号:Define Your Own Spec。
熔点:183℃波峰炉:MWSI温区(3温区)5.2.2预热段温110—145℃预热时间:40—60s回流段温度 183℃以上回流时间:2—5s最高温度:233--255℃5.3曲线参数标准设定(MPS-400B温区)5.3.1锡膏型号:Define Your Own Spec。
- 1、下载文档前请自行甄别文档内容的完整性,平台不提供额外的编辑、内容补充、找答案等附加服务。
- 2、"仅部分预览"的文档,不可在线预览部分如存在完整性等问题,可反馈申请退款(可完整预览的文档不适用该条件!)。
- 3、如文档侵犯您的权益,请联系客服反馈,我们会尽快为您处理(人工客服工作时间:9:00-18:30)。
炉温曲线测试规范1.目的本规范规定了炉温曲线的测试周期、测试方法等,以通过定期的、正确的炉温曲线测试确定最佳的曲线参数,最终保证PCB装配的最佳、稳定的质量,提高生产效率和产品直通率。
2.定义2.1回流曲线在使用焊膏工艺方式中,通过固定在PCB表面的热电偶及数据采集器测试出PCB在回流焊炉中时间与温度的可视数据集合,根据焊膏供应商推荐的曲线,对不同产品通过适当调整温度设置及传输链的速度所得到的最佳的一组炉温设置参数。
2.2固化曲线在使用点胶或印胶工艺方式中,通过固定在PCB表面的热电偶及数据采集器测试出PCB在固化炉中时间与温度的可视数据集合,根据焊膏供应商推荐的曲线,对不同产品通过适当调整温度设置及传输链的速度所得到的最佳的一组炉温设置参数。
2.3基本产品指在一个产品系列中作为基本型的产品,该系列的其它产品都在此基础上进行贴装状态更改或对印制板进行少量的改版,一般情况下一个产品系列同一功能的印制板其图号仅在版本号上进行区分,如“***-1”与“***-2”或“***V1.1”与“***V1.2”等。
2.4派生产品指由于设计贴装状态更改、或印制板在原有基础上进行少量的改版所生成的其所改动的CHIP 类器件数量未超过50只、同时没有对外形尺寸大于□20mm×20mm的IC器件(不包括BGA、CSP等特殊封装的器件)的数量进行调整的产品。
2.5全新产品指产品公司全新开发、设计贴装状态更改或印制板在原有基础上改版时所生成的其所改动的CHIP类器件数量超过50只、或对外形尺寸大于□20mm×20mm的IC器件的数量进行调整的产品。
凡状态更改中增加或减少了BGA、CSP等特殊封装的器件的产品均视为全新产品。
2.6测试样板指用来测试炉温的实装板,该板必须贴装有与用来测试的生产状态基本一致的元器件。
3.职责4.炉温测试管理4.1炉温测试周期:原则上工程师根据当月所生产的产品应每月测试一次,将测试结果记录在“炉温参数设置登记表”上,并将炉温曲线打印存档。
4.2原则上全新产品必须经过炉温测试,确定准确的炉温设置参数,但对批量小于100套的全新工程师可以根据原有的相似产品根据观察实物的焊接效果进行自行调整。
4.3全新产品在炉温测试时应领取新的测试样板,派生产品可采用原基本产品的测试样板进行炉温测试,以针对不同的产品及状态设置相应准确的炉温参数。
5.测试准备5.1炉温测试使用DataPaq炉温测试仪,热电偶使用K型。
5.2选择测温点。
热电偶应该安装在能代表PCB板上最热与最冷的连接点上(引脚到焊盘的连接点上),以及热敏感器件和其它高质量器件上,以保证其被足够地加热,一般测温点至少在三点及以上。
测温点按以下原则选择:1) 耐热性差的热敏感器件;2) 所贴装IC 器件中的BGA、CSP、较大质量的QFP 或PLCC 器件3) 部品贴装密度高的区域或有大面积敷铜(接地)的区域4) PCB 表面温度最高的区域(如贴装密度低的区域、PCB 边缘区域、低质量的CHIP 类器件等)5.3热电偶的固定方法。
热电偶固定的有以下四种方法:5.3.1使用高温焊锡,如银/锡合金,这个方法通常用于可以为作曲线和检验工艺而牺牲一块专门的参考板的运作,如图1所示。
应该注意的是保证最小的锡量,以避免影响曲线,如图2所示。
5.3.2开普顿(Kapton)或铝胶带,或者称为高温胶纸,它是最容易使用,但最不可靠的固定方法。
使用胶带作温度曲线时测温线不可过度弯曲,同时热电偶连接点在加热期间从接触表面提起,导致所量测到的温度曲线会上下飘游,经常显示很参差不齐的曲线,得到的温度数值会不准确。
但其因容易使用和不留下影响装配的残留物,使得开普顿或铝胶带成为一个受欢迎的方法。
5.3.3高温胶,如氰基丙烯酸盐粘合剂,高温胶的使用通常得到热电偶对装配的刚性物理连接。
缺点包括高温胶可能在加热过程中失效的可能性、作完曲线后取下时在装配上留下残留物;同时应该注意使用最小的胶量,因为增加热质量可能影响温度曲线的结果,如图3所示。
图1 适量的高温焊锡 图2 过量的焊锡 图3 过量的高温胶5.3.4压力型热电偶,夹持在线路板的边缘,使用弹力将热电偶连接点牢固地接触固定到正在作温度曲线的装配上。
压力探头快速、容易地使用,对PCB 没有破坏性。
5.3.5热电偶固定时不能将其正负两极在固定点之前直接接触,二者必须分离,如图4所示,否则所测试的温度并非固定点的温度,而是空气的温度,如图5、图6所示。
AB图4 正确的固定方式 图5 错误的固定方式图6 错误的固定方式6.炉温测试过程与要求6.1测试步骤6.1.1调整轨道宽度。
手工或自动调整轨道宽度大小,轨道宽度要大于PCB 宽度2-3mm 即可。
6.1.2设定各区温度及传输链速度。
工程师首次测试时可根据已有的与所测产品相似的产品的温度设置作适当修改后作为新的炉温设置参数及传输速度,然后按下START 键开始升温。
6.1.3温度测试。
待各温区温度上升至所设定的温度值并保持稳定20min 分钟后即可开始,测温时将热电偶按照顺序与数据收集器连接,然后将数据收集器放入绝缘外盒内,按下数据收集器上的激活开关,盖好绝缘外盒,将测试样板与绝缘盒依次放入回流炉内,开始测温。
待测试样板及数据收集器从回流炉末端流出后,打开绝缘盒盖,按下Stop键,测温完毕。
6.1.4分析温度曲线。
将数据收集器与计算机RS232通讯口连接,打开DataPaq操作软件,点击“记录器下载”按钮,下载数据收集器内的数据,数据下载完毕后将自动打开文件。
根据所测试的炉温曲线与供应商推荐的炉温曲线进行对比,对需要调整的温区设置值或传输速度进行适当调整,使之满足供应商的推荐值。
当需要再次进行温度测试时,在重新设定参数并待温度调整至设定值后20min才能进行新一次的温度测试,以免炉膛内温度未完全稳定,导致温度测试不准确。
当温度曲线测试完成后,必须进行试生产,工程师应根据试生产产品的质量状况,持续观察产品的上锡效果、有无异常的连焊、虚焊、冷焊、立贴、锡珠等现象,可对炉温参数进行适当调整,以保证产品质量,保证工艺参数的最佳。
工程师在确定最佳的炉温参数后,应再次进行最终版的测试,测试后必须在炉温曲线文件中编辑“备忘录”,在“备忘录”中注明“贴装线、程序名、测试日期、温度及链速设置”等内容。
工程师在炉温测试完毕后应及时填写“炉温参数设置登记表”、“炉温测试登记表”,并打印出炉温曲线图。
“炉温测试登记表”、炉温曲线图等资料由工程科统一保存并存档,以供质量追溯。
6.2典型辅料的回流参数要求6.2.1焊膏常用的炉温曲线分为直线上升型(或三角型,如图7所示)与平台保温型(如图8所示):图7 直线上升型回流曲线 图8 平台保温型回流曲线确信爱法有铅焊膏RMA9086与无铅焊膏OM338推荐回流曲线:有铅焊膏RMA9086 无铅焊膏OM338直接上升式曲线,高密度板组装可能需要增加预热。
曲线可设置如下:-以60-120°C/min 上升至130-160°C。
-在130-160°C下保持0.5-2.0min。
-再以60-120°C/min 上升至210-225°C 峰值温度。
-超过 183°C = 40-60 secs。
-以 90-120°C/min的速度下降至室温。
直接上升式曲线,高密度板组装可能需要增加预热。
曲线可设置如下:-以0.8-1.7°C/sec 上升至135-160°C。
-以60-90 秒缓慢升温至180-190°C。
-以1-2°C/sec上升至230-250°C 峰值温度。
-超过 217°C = 45-90 secs。
-以 1.5 to 2°C 每秒下降至室温。
6.2.2贴片胶的炉温曲线。
我厂现常用的贴片胶分为点胶与印胶两种,点胶为贺利氏PD944,印胶为贺利氏PD955PHY.其峰值温度不超过150°C,在130°C以上的时间要求保持在120sec以上。
胶粘剂固化后拉脱强度要求:强度值 适用元器件 强度值 适用元器件≥15N 1005片式元件 ≥28N 2125-3225片式元件≥20N 1608片式元件 ≥25N 小外形晶体管.二极管等≥40N 钽电解ABCD ≥100N SOIC等小外形集成电路≥70N 功率型三极管6.3炉温参数变化引起不良的解决方法6.3.1虚焊:锡膏没有或没充分与器件引脚焊接,可通过提高回流焊温度或时间来解决。
6.3.2 连焊:通常降低回流区温度或时间来改善连锡现象。
6.3.3锡珠:由于预热区温度过高或经过时间短,导致锡膏中水分、溶剂未充分挥发,在回流区时飞溅而形成锡珠,因此降低预热区温度或时间、减少上升斜率可得以解决。
6.3.4焊点不光亮:焊点不饱满所导致的不光亮。
可降低回流区温度或加快链速解决。
锡膏未充分熔化导致的不光亮,可提升回流区温度或减慢链速解决。
6.3.5胶液主要不良为粘接强度不够(过波峰焊或转运过程中时易掉件),其解决方法是:由于固化温度和时间不够所造成的,提升温度或减慢传输速度。
因固化温度过高或时间长造成胶水老化所致,则此时降低温度或加快传输速度。