【精美排版】劣质成本分析1657695316
产品质量问题的成本效益分析

产品质量问题的成本效益分析在当今竞争激烈的市场环境中,产品质量问题是企业面临的一个重要挑战。
对于企业来说,理解和分析产品质量问题所带来的成本和效益至关重要,这不仅关系到企业的短期利润,更影响着企业的长期发展和声誉。
产品质量问题所产生的成本是多方面的。
首先,最直接的就是生产过程中的废品和次品成本。
当产品不符合质量标准时,这些不合格的产品无法正常销售,企业在原材料、劳动力和生产设备等方面的投入就完全浪费了。
而且,废品和次品的产生还会导致生产效率的降低,因为工人需要花费时间和精力去处理这些不合格产品,从而影响了整个生产线的进度。
其次,质量问题可能引发的退货和换货成本也不容忽视。
如果消费者购买到有质量问题的产品,他们有权要求退货或换货。
这不仅增加了企业的物流和处理成本,还可能导致消费者对企业的信任度下降,影响企业的品牌形象和未来的销售。
再者,售后服务成本也是质量问题带来的一大负担。
当产品出现质量问题时,企业需要投入人力、物力去为消费者提供维修、保养等售后服务。
这不仅需要耗费大量的时间和资源,还可能因为无法及时解决问题而引发消费者的不满和投诉。
此外,质量问题还可能导致企业面临法律诉讼的风险。
如果产品的质量问题对消费者造成了人身伤害或财产损失,企业可能需要承担巨额的赔偿责任,甚至可能面临法律制裁,这对企业的财务状况和声誉将造成极大的打击。
然而,解决产品质量问题也需要投入一定的成本。
企业可能需要改进生产工艺、引进先进的检测设备、加强员工培训等,这些都需要资金的支持。
但从长远来看,解决质量问题所带来的效益也是显著的。
提高产品质量可以增加客户满意度和忠诚度。
当消费者购买到质量可靠的产品时,他们更有可能成为企业的回头客,并向他人推荐企业的产品,从而为企业带来更多的销售机会。
而且,高质量的产品能够提升企业的品牌形象和声誉,使企业在市场竞争中脱颖而出。
减少质量问题还能够提高生产效率和降低生产成本。
通过改进生产工艺和流程,减少废品和次品的产生,企业可以更有效地利用原材料和生产设备,提高生产效率,从而降低单位产品的生产成本。
产品质量不良成本表
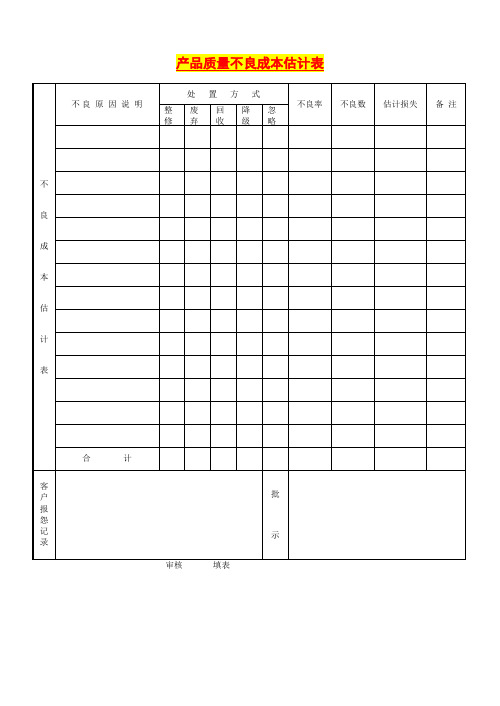
不合格品管理程序培训总结主要工作程序:
1 不合格品的发生进料检验过程中,检验人员发现的不符合标准要求的采购原材料、外加工产品,库存超期的重检中发现的不合格原材料、外加工产品;过程检验和出货检验中发现的不合格、库存成品超期重检发现的不合格品;
2 状态标识制造过程中的产品和进货检查的产品被判定为不合格时,由制造部班组长、品质部检验员对不合格产品进行标识、隔离,防止混料、转入下道工序。
3 信息传递检验人员开出《不合格品处置单》后立即传递到相关责任部门,外购产品由采购部以传真、电话、邮件等方式通知供应商,并要求供应商对不合格内容进行确认回复。
劣质成本
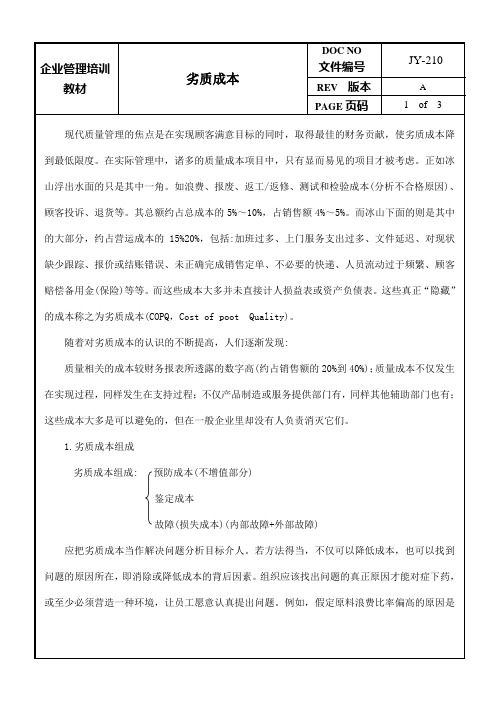
如果能够根据劣质成本项目,依其金额的大小,可以制作排列图,然后制订改进的优先顺序,这是十分有效的,当然要花费很大的功夫。团队在初期时不妨选定其中一个目标项目,例如现场的返工等,然后针对此项目收集资料,估算劣质成本的实际金额大小。
随着对劣质成本的认识的不断提高,人们逐渐发现:
质量相关的成本较财务报表所透露的数字高(约占销售额的20%到40%);质量成本不仅发生在实现过程,同样发生在支持过程;不仅产品制造或服务提供部门有,同样其他辅助部门也有;这些成本大多是可以避免的,但在一般企业里却没有人负责消灭它们。
1.劣质成本组成
劣质成本组成:预防成本(不增值部分)
现代质量管理的焦点是在实现顾客满意目标的同时,取得最佳的财务贡献,使劣质成本降到最低限度。在实际管理中,诸多的质量成本项目中,只有显而易见的项目才被考虑。正如冰山浮出水面的只是其中一角。如浪费、报废、返工/返修、测试和检验成本(分析不合格原因)、顾客投诉、退货等。其总额约占总成本的5%~10%,占销售额4%~5%。而冰山下面的则是其中的大部分,约占营运成本的15%20%,包括:加班过多、上门服务支出过多、文件延迟、对现状缺少跟踪、报价或结账错误、未正确完成销售定单、不必要的快递、人员流动过于频繁、顾客赔偿备用金(保险)等等。而这些成本大多并未直接计人损益表或资产负债表。这些真正“隐藏”的成本称之为劣质成本(COPQ,Cost of poot Quality)。
2.劣质成本分析步骤
六西格玛管理的观点认为,质量差错率越小质量水平越高,其预防成本曲线会下移。随着质量水乎的提高,由3σ→6σ水平,损失成本下降,预防和鉴定成本也在下降(曲线下移)。造成总质量成本降低的最好方法是降低劣质成本。
不良成本分析报告

一、2014年2月以来的不良成本如下:
返工费用 报废费用 索赔费用 顾客退货品运费 客诉处理差旅费 其它不良成本 本月总不良成本:元 本月总成本:元 本月不良成本率:% 月度不良成本率:% 本季度总成本 本季度不良成本:元 本季度不良成本率:% 不良成本率控制目标:≤3%
1月
0.00 #REF! 0.00 0.00 0.00
0.00
#REF! 0.00 0.00% 3.00%
2月
3月
0.00
3076.92
#REF!
#REF!
0.00
0.00
0.00
0.00
0.00
0.00
0.00
0.00
#REF!
#REF!
4467384.87 2726150.55
#REF!
#REF!
3.00%
3.00%
7193535.42
#REF!
#REF!
3.00%
4月
5月
6410.26
8205.13
#R00
200.00
0.00
0.00
15000.00
0.00
0.00
#REF!
#REF!
4608836.28 3776529.60
#REF!
#REF!
3.00%
3.00%
8385365.88
#REF!
#REF!
3.00%
图表标题
6月
#DIV/0! 3.00%
1
0.8
0.6
0.4
0.2
0
1
2
3
4
5
4.00%
3.00% 2.00% 1.00%
劣质成本构成与分析
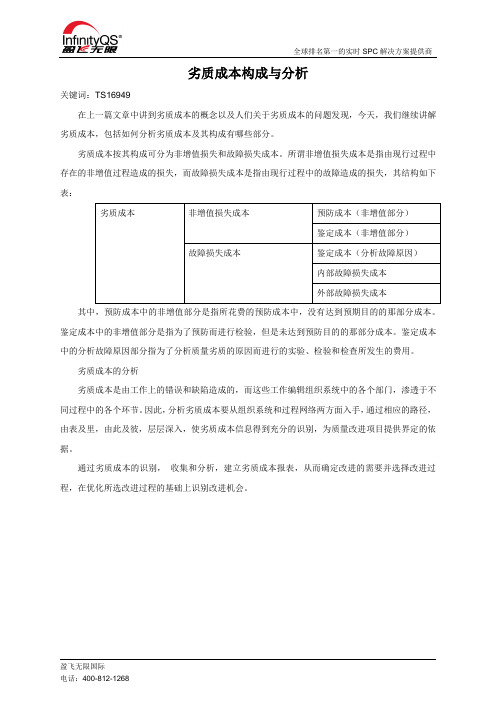
全球排名第一的实时SPC解决方案提供商
劣质成本构成与分析
关键词:TS16949
在上一篇文章中讲到劣质成本的概念以及人们关于劣质成本的问题发现,今天,我们继续讲解劣质成本,包括如何分析劣质成本及其构成有哪些部分。
劣质成本按其构成可分为非增值损失和故障损失成本。
所谓非增值损失成本是指由现行过程中存在的非增值过程造成的损失,而故障损失成本是指由现行过程中的故障造成的损失,其结构如下表:
其中,预防成本中的非增值部分是指所花费的预防成本中,没有达到预期目的的那部分成本。
鉴定成本中的非增值部分是指为了预防而进行检验,但是未达到预防目的的那部分成本。
鉴定成本中的分析故障原因部分指为了分析质量劣质的原因而进行的实验、检验和检查所发生的费用。
劣质成本的分析
劣质成本是由工作上的错误和缺陷造成的,而这些工作编辑组织系统中的各个部门,渗透于不同过程中的各个环节。
因此,分析劣质成本要从组织系统和过程网络两方面入手,通过相应的路径,由表及里,由此及彼,层层深入,使劣质成本信息得到充分的识别,为质量改进项目提供界定的依据。
通过劣质成本的识别,收集和分析,建立劣质成本报表,从而确定改进的需要并选择改进过程,在优化所选改进过程的基础上识别改进机会。
盈飞无限国际
电话:400-812-1268。
劣质成本分析

劣质成本分析[概要]简单介绍了质量成本的概念及构成、劣质成本的概念及构成以及一个劣质成本分析的示例。
[字数]4000。
[正文] 20世纪50年代,美国质量管理专家费根堡姆提出了质量成本的概念,首次把质量同企业经济效益联系起来。
随后朱兰提出了“矿中黄金”的概念,认为废品损失就像亟待开采的金矿,只要管理得当,降低废品费用就如同从金矿中开采出黄金,指出了质量成本分析的重要性。
在这些思想的引导下,发达国家相继开展了质量成本管理的理论与实践推广,不仅使企业获得重大效益,也使消费者得到实惠。
如今,质量成本管理已经成为指导企业进行质量改进、降低成本、提高效益的重要途径。
劣质成本(cost of poor quality:COPQ)分析是质量成本管理中的重要一环,也是六西格玛管理重要切入点,用于选择和评价六西格玛改进项目,明确项目预计的财务收益。
……劣质成本分析20世纪50年代,美国质量管理专家费根堡姆提出了质量成本的概念,首次把质量同企业经济效益联系起来。
随后朱兰提出了“矿中黄金”的概念,认为废品损失就像亟待开采的金矿,只要管理得当,降低废品费用就如同从金矿中开采出黄金,指出了质量成本分析的重要性。
在这些思想的引导下,发达国家相继开展了质量成本管理的理论与实践推广,不仅使企业获得重大效益,也使消费者得到实惠。
如今,质量成本管理已经成为指导企业进行质量改进、降低成本、提高效益的重要途径。
劣质成本(cost of poor quality:COPQ)分析是质量成本管理中的重要一环,也是六西格玛管理重要切入点,用于选择和评价六西格玛改进项目,明确项目预计的财务收益。
1质量成本的概念及构成质量成本是为控制产品能维持在一定的质量水平状况下所支付的各项成本以及因为不能达到此质量水平而造成的各项损失成本的总和。
由此可见,质量成本由两部分构成,一是为达到产品既定的质量标准而支出的费用;二是由于质量低劣而造成的经济损失。
前者称为质量控制成本或符合性成本,包括预防成本和鉴定成本(预先审查);后者称为质量损失成本获非符合性成本,包括鉴定成本(查明故障)、内部损失成本和外部损失成本。
品质成本分析(品管培训学习资料)

☆品管培训教材资料☆品質成本分析品質管理的推行與實施,除了要做好品質保證外,其他有關的管理服務費用也要能有效的管理,整體的成本才會降到最低;全面品質管制也才可算是真正做好.因此如何有效的做好品質成本分析.檢討品質成本是全面品質管制的極為重要實施項目.在全面品質管理實施的初期,所需投入的費用極大,所以必頇在費用上确實檢討,使能在合乎經濟性.合理性.效果性的原則下來實施全面品質管制,以發揮品質管理的最大功效.分析品質成本不但可為全面品質管制活動效果的評價尺度,還可作為全面品質管制預算編成的基礎資料,并奠定特定制程之品質分析及改善措施之妥當性的檢查基礎,同時對經營管理之資料做成參考也有很大的幫助.一.品質成本的內容品質成本通常是指預防成本,評價成本,失敗成本三者的總合,這三種成本的總額要能達到最低點,品質管理才能說是真正做好.(1)預防成本一般所謂預防成本包括所有公司內.公司外的各種品管教育訓練費用及現場的品管座談會費用.品管圈活動費用.品管部門及品質管理委員會.品保委員會……等各小組的開會費用與品管的協調費用等為預防發生不良損失所花費的一切費用.(2)評價成本評價成本則包括各項的檢查費用如原材料的進貨檢驗費用.各制程的中間品的檢查費用.作業工程中的檢查費用.成品的檢查費用.制品的出貨檢查費用.品質監查費用.公司外品管專家的診斷費用等,為要評價品質的好壞所發生的一切費用.(3)失敗成本失敗成本可分為內部失敗成本與外部失敗成本.內部失敗成本是指制品未出貨前在公司內本身發生的,包括不良品,不同數量的差異.譬如原投入生產的是100的產品,但實際上卻只做出95,這5的差異損失費即為內部失敗成本;又如因檢驗時發生不合格而無法出貨這不良品所損失的費用亦屬內部失敗成本,其他如調查產生不良品調查費.不良品的修理費,設計變更的損失等均是.外部失敗成本是指產品出貨后,到市面上或顧客使用后才發生的各項抱怨.不良所帶來的損失,如不良品出貨后再退回公司的更換費與搬運費.出貨后不良品的報廢費用以及因設計錯誤或不良品本身的不良而發生制品責任問題所產生損失之賠償費用.制品出貨后因不良而降價或改裝的費用,因滯鎖積存制品的損失等均是.從以上各種成本的包括要點中,我們可以知道各企業要投入預防成本與評價成本,主要的是希望能管理失敗成本,使失敗成本降至最低,因此預防成本與評價成本亦可說是一項管理費用.所以,品質管理的本質之一就是要能把以上的總合的品質成本能降至最低,如此我們才能達到以最經濟的方法達成最大的功效.二.品質管理與品質成本之關系.(1)未實施品質管理時期未實施品質管理前的公司,其品質成本一定很大,而且所占的品質成本必多為失敗成本,這乃由于因尚未實施任何品質措施,所以往往產品并未做任何檢查,不論好壞均使之全數出貨,一直要等到顧客有抱怨反應時才做處理.因此所發生的產品更換.修理.賠償.降價.搬運等的費用,不但使產品信用損失,外部失敗成本也高得不得了,因內部未做檢查,內部失敗成本雖低,但是內外失敗成本加起來的總品質成本卻非常的高,因而造成制造成本的提高.(2)檢查的品質管理時期根據品質管理的進展過程,在這個時候,一般業界都會想到設立檢查單位,在各制程中安置了許多的檢查人員,并購買檢驗儀器,特別是對出貨之成品做全數檢查,所有的產品必頇都得經檢驗合格后才能出貨,因此出貨的不良品與外部抱怨立即顯著減少,外部失敗成本亦必隨之降低.但在另一方面卻由于嚴格的檢查產生了許多不良品無法出貨必頇修理.調整或報廢等的情形,內部失敗成本因此提高很多,再加上所增加的許多檢查費用(即評價成本的增加),因此總合品質成本降低并不多.由上所述,我們可以知道,若只靠檢查是無法做好品質管理的,因即使是做再嚴格的檢查也不能達到再發防止做好品質保證,而目前我國企業卻大部份都在做這種檢查式的品管.因此要想突破今天所面臨的瓶頭.困境.就必頇要從企劃.開發設計開始,制程,消費者.到制品達到最終目的為止的每階段都做好品質保證,并使保證能确實做好,公司內外的管理服務.以防止再發而不是以檢查做好品質保證,同時也要使管理服務的費用(品質成本)降至最低.因此,實施全面品質管制乃為當今企業生存竟爭的刻不容緩,必行之徑.(3)實施教育訓練的品質管理時期要實施全面品質管制,首先要對全公司全員實施教育訓練,并建立各項全面品質管制的體系,從基本上去改善企業體質,則全面品質管制才能發揮真正經營上的功效.品管教育從高階層開始至中階層干部到基層作業員,都有一系列的教育訓練課程,不但所有的人員要動員,各項資料,各種上課教材都要能配合,同時要建立全面品質管制的體系,譬如標準化體系,教育訓練體系,方針管理體系等,這一切的基礎是全面品質管制實施推動成功的重要關鍵.在實施TQM開始的一年到二年的期間,要投入很大的教育訓練費用,對全公司全員施予品管教育是極為重要的,但是,這項投資因所有的教育訓練方正在實施階段,所有的體系亦均正在建立之中,短時間內是不可能發揮多少效果的,由于教育訓練經費的大量投資且評價成本與失敗成本尚暫時未能降低,因此總合品質成本常會反而提高.(4)實施全面品質管制時期通常要到全面品質管制實施的第三年左右,所有人員的整體教育訓練已告一段落,各面體系亦已建立了,教育費用自然會立刻降低,這個時期以后的教育訓練就只頇對未接受過教育的新進人員,或晉升新職位者如經理升任廠長.副理升經理……等的再教育即可.在此時,教育訓練費用也就能穩定.又全公司的品管語言此時即可一致.公司整體就能有極大的功效發揮.而且由于全公司的管理已上軌道,在制程中,產品本來要全數檢查的,可能改為抽樣檢查即可改為抽樣即可;原先要一個鐘頭檢查一次的,可能變成四個鐘頭檢查一次,甚至可以不要檢查.檢查周期,檢查人員……等各項檢查費用,時間必大大減少,而且品質在企劃.設計.制程等各階段中就能做好,所產生的制品品質亦必精良,因此內部失敗成本及外部失敗成本也就會隨之降至最低.到了全面品質管制實施的第3~5年以后,全公司的各面體系大都已是建立完成,PDCA 管理循環轉動順利,配合教育訓練必當可很順利扎實的不斷運轉,產品的品質與技術水準亦必隨之日益精進,而使顧客能完全獲得滿足與安心感,提高產品信譽,使產品達到世界一流水準.三.推行全面品質管制必頇要的決心與毅力遺憾的是,一般企業的經營者,卻不易將眼光放遠.許多人在品管教育初期,見花費了教育訓練費用,卻未能馬上看到效果就終止了往后的所有教育訓練或品管工作.有些人則是在努力一.二年后,缺乏決心與毅力,半途而廢,如此以短期的近利去評價效果是很可惜的.這個時候,若其他競爭公司卻仍經常的接受系列的教育,吸收新知,成功的實施全面品質管制,其不斷的改進.突破.那麼兩者的產品品質的水準與市場必會有懸殊的差距.更甚者,可能會無法繼續生存競爭.在此,要特別強調的是,在這個全面品質管制實施的過程中,經營者尤其要能以長遠的眼光去前瞻,要認知全面品質管制并不是特效藥,它的目的是在于改善企業體質.所以,不但要投資,還要有耐心.決心.長期不斷的教育與改進,使技術.知識.人員.體系……等的軟體實力在全公司.全部門.全員穩固,其才能達成全面品質管制實施的真正效果,品管也才能在企業內生根茁長.。
劣质成本分析
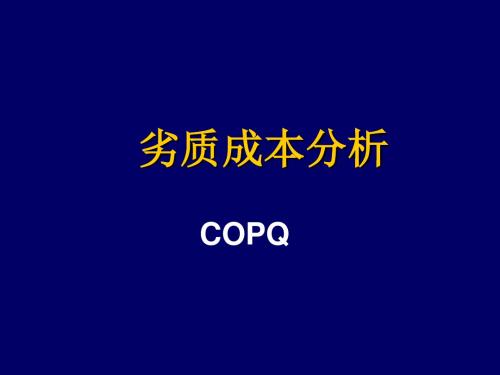
1.1 PAF模型
质量成本
投入成本 损失成本
预防成本:为预防故障所支付的费用
鉴定成本:为评定质量要求是否满足而进行的 试验、检验和检查所支付的费用
内部故障成本:由于产品或服务在交付前不能 满足质量要求所造成的损失
外部故障成本:由于产品或服务在交付后未 满足质量要求所造成的损失
1.2 COC模型
质量成本
产品成本 财务报告 资本支出
内部故障成本
不符合标准的产品 废品、返修和返工 再次检验 重新设计 过程修改 输入延迟 资源闲置
内部故障成本
备用物质 事故,公伤 旷工 供应商问题:废料
延迟交货 库存过多
废弃的计划
内部故障成本
逾期成本 错过的成交机会 帐单错误 重复运行 内审、外审的纠正措施
外部故障成本
1.确定过程
2.确定步骤
SIPOC过程——增值分析 (value added)
要求
SI
供方
输入
测量
要求
PO C
过程
输出
顾客
测量
C: 顾客的关键需求(产品/服务) O:关键过程输出(KPO) P:关键过程控制(KPC) I: 关键过程输入 (KPI) S:供方的关键要求 (资源)
特性
CTQ
CTQ critical-to-quality
步骤3:步骤分类
生产/质量成本 质量成本 劣质成本
预防成本 鉴定成本 内部故障成本 外部故障成本
1. 确定过程 2. 确定步骤
3. 步骤分类
步骤4:估算劣质成本
人工费 管理费 全部资源法 单位成本法 会计原理
1. 确定过程 2. 确定步骤
3. 步骤分类