除尘脱硫脱硝系统
脱硫脱硝除尘解决方案及措施

脱硫脱硝除尘解决方案及措施随着工业化进程的加快和环境污染的日益严重,脱硫脱硝除尘技术成为了工业企业必须面对的重要问题。
脱硫脱硝除尘技术是指利用化学或物理方法将燃煤、燃油等燃料中的硫、氮等有害物质去除,以及将工业废气中的颗粒物去除的技术。
本文将从脱硫脱硝除尘的重要性、技术原理、解决方案及措施等方面进行探讨。
一、脱硫脱硝除尘的重要性。
1.环境保护。
工业生产中产生的废气中含有大量的二氧化硫、氮氧化物等有害物质,这些物质对大气环境造成了严重的污染。
通过脱硫脱硝除尘技术的应用,可以有效地减少这些有害物质的排放,保护环境,净化空气。
2.健康保护。
工业废气中的有害物质不仅对大气环境造成污染,还会对人体健康造成危害。
例如,二氧化硫、氮氧化物等物质会引起呼吸系统疾病,颗粒物会对人体的呼吸系统和心血管系统造成危害。
因此,脱硫脱硝除尘技术的应用对于保护人体健康具有重要意义。
3.资源利用。
脱硫脱硝除尘技术可以有效地减少燃料中的有害物质的排放,提高燃料的利用率,减少资源的浪费,有利于可持续发展。
二、脱硫脱硝除尘技术原理。
1.脱硫技术原理。
脱硫技术主要是通过化学或物理方法将燃料中的硫化物去除。
常用的脱硫方法包括石灰石法、石膏法、氨法等。
其中,石灰石法是将石灰石喷入燃烧炉中与燃料中的硫化物发生化学反应,生成硫酸钙,从而达到脱硫的目的。
石膏法是将石膏喷入燃烧炉中与燃料中的硫化物反应生成硫酸钙,并将硫酸钙从烟气中除去。
氨法是将氨气喷入烟气中与燃料中的氮氧化物发生化学反应,生成氮和水。
2.脱硝技术原理。
脱硝技术主要是通过化学方法将燃料中的氮氧化物去除。
常用的脱硝方法包括选择性催化还原(SCR)和选择性非催化还原(SNCR)。
SCR是在催化剂的作用下,利用氨气与燃料中的氮氧化物发生还原反应生成氮和水。
SNCR是在高温条件下,利用氨气与燃料中的氮氧化物发生非催化还原反应。
3.除尘技术原理。
除尘技术主要是通过物理方法将工业废气中的颗粒物去除。
浅谈半干法脱硫及除尘系统
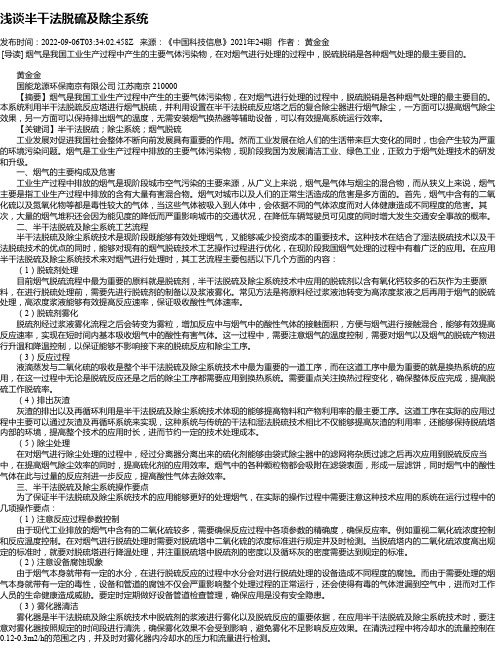
浅谈半干法脱硫及除尘系统发布时间:2022-09-06T03:34:02.458Z 来源:《中国科技信息》2021年24期作者:黄金金[导读] 烟气是我国工业生产过程中产生的主要气体污染物,在对烟气进行处理的过程中,脱硫脱硝是各种烟气处理的最主要目的。
黄金金国能龙源环保南京有限公司江苏南京 210000【摘要】烟气是我国工业生产过程中产生的主要气体污染物,在对烟气进行处理的过程中,脱硫脱硝是各种烟气处理的最主要目的。
本系统利用半干法脱疏反应塔进行烟气脱硫,并利用设置在半干法脱硫反应塔之后的复合除尘器进行烟气除尘,一方面可以提高烟气除尘效果,另一方面可以保持排出烟气的温度,无需安装烟气换热器等辅助设备,可以有效提高系统运行效率。
【关键词】半干法脱硫;除尘系统;烟气脱硫工业发展对促进我国社会整体不断向前发展具有重要的作用。
然而工业发展在给人们的生活带来巨大变化的同时,也会产生较为严重的环境污染问题。
烟气是工业生产过程中排放的主要气体污染物,现阶段我国为发展清洁工业、绿色工业,正致力于烟气处理技术的研发和升级。
一、烟气的主要构成及危害工业生产过程中排放的烟气是现阶段城市空气污染的主要来源,从广义上来说,烟气是气体与烟尘的混合物,而从狭义上来说,烟气主要是指工业生产过程中排放的含有大量有害混合物。
烟气对城市以及人们的正常生活造成的危害是多方面的。
首先,烟气中含有的二氧化硫以及氮氧化物等都是毒性较大的气体,当这些气体被吸入到人体中,会依据不同的气体浓度而对人体健康造成不同程度的危害。
其次,大量的烟气堆积还会因为能见度的降低而严重影响城市的交通状况,在降低车辆驾驶员可见度的同时增大发生交通安全事故的概率。
二、半干法脱硫及除尘系统工艺流程半干法脱硫及除尘系统技术是现阶段既能够有效处理烟气,又能够减少投资成本的重要技术。
这种技术在结合了湿法脱硫技术以及干法脱硫技术的优点的同时,能够对现有的烟气脱硫技术工艺操作过程进行优化,在现阶段我国烟气处理的过程中有着广泛的应用。
烟气脱硝除尘脱硫装置存在问题分析与改进

烟气脱硝除尘脱硫装置存在问题分析与改进烟气脱硝、除尘和脱硫装置是用于处理燃煤电厂、石油化工厂等工业烟气中的二氧化硫和颗粒物的重要设备。
在实际运行中,这些装置存在一些问题,影响其脱硝、除尘和脱硫效果。
本文将分析这些问题,并提出改进方案。
1. 脱硝效果不佳:由于燃煤电厂和石油化工厂烟气中的氮氧化物含量较高,传统的选择性催化还原脱硝装置难以达到满意的脱硝效果。
改进方案是引入SCR(选择性催化还原)装置,通过在脱硝系统中添加氨水或尿素等还原剂,在催化剂的催化作用下,将烟气中的氮氧化物脱硝为氮气和水。
2. 除尘效果差:传统的机械除尘器对于烟气中的小颗粒物无法有效捕集,导致排放的颗粒物浓度超出环境排放标准。
改进方案是采用静电除尘器,通过电离烟气中的颗粒物,使其被带电极板吸附并集中处理。
3. 脱硫效果欠佳:传统的烟气脱硫装置采用喷雾吸收法,将烟气通过喷嘴,与石灰石浆液结合产生石膏,从而达到脱硫效果。
喷雾吸收法存在脱硫效果不稳定、能耗高等问题。
改进方案是引入湿式电除尘脱硫技术,通过湿式电除尘器将烟气中的含硫化合物捕集并进行脱硫处理。
4. 能耗高:传统的烟气脱硝除尘脱硫装置能耗较高,增加了运行成本。
改进方案是优化设备结构,减少能耗。
可以采用高效的换热设备,利用烟气中的热能进行蒸汽或热水产生,从而减少对外部热能的依赖。
5. 设备维护困难:传统的烟气脱硝除尘脱硫装置由于结构复杂,设备维护困难。
改进方案是采用 modulized 设计,将脱硝、除尘和脱硫装置模块化,方便设备维护和更换。
烟气脱硝除尘脱硫装置存在的问题主要包括脱硝效果不佳、除尘效果差、脱硫效果欠佳、能耗高和设备维护困难等。
通过引入新技术、优化设备结构和 modulized 设计,可以改善装置的性能,提高其脱硝、除尘和脱硫效果,降低运行成本,并方便设备维护。
除尘脱硫脱硝一体化
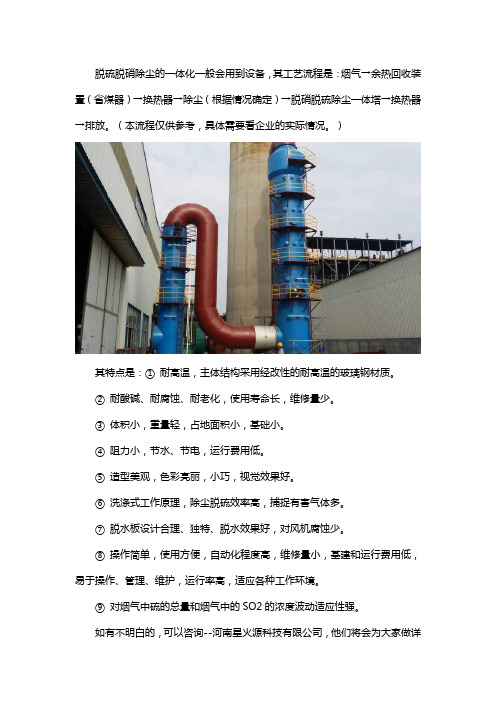
脱硫脱硝除尘的一体化一般会用到设备,其工艺流程是:烟气→余热回收装置(省煤器)→换热器→除尘(根据情况确定)→脱硝脱硫除尘一体塔→换热器→排放。
(本流程仅供参考,具体需要看企业的实际情况。
)
其特点是:①耐高温,主体结构采用经改性的耐高温的玻璃钢材质。
②耐酸碱、耐腐蚀、耐老化,使用寿命长,维修量少。
③体积小,重量轻,占地面积小,基础小。
④阻力小,节水、节电,运行费用低。
⑤造型美观,色彩亮丽,小巧,视觉效果好。
⑥洗涤式工作原理,除尘脱硫效率高,捕捉有害气体多。
⑦脱水板设计合理、独特、脱水效果好,对风机腐蚀少。
⑧操作简单,使用方便,自动化程度高,维修量小,基建和运行费用低,易于操作、管理、维护,运行率高,适应各种工作环境。
⑨对烟气中硫的总量和烟气中的SO2的浓度波动适应性强。
如有不明白的,可以咨询--河南星火源科技有限公司,他们将会为大家做详
细的解答。
SNDR氨法脱硫脱硝除尘

SNDR氨法脱硫脱硝除尘SNDR氨法脱硫脱硝原理2NH3–H2O+SO2=(NH4)2SO3+H2O2(NH4)2SO3+2NO=2(NH4)2SO4 +N2↑(NH4)2SO3+1/2O2=(NH4)2SO44(NH4)2SO3+2NO(2)=4(NH4)2SO4+N2↑SNDR氨法脱硫脱硝的优点î 脱硫脱硝共用一台反应塔î 防止氨、气溶胶、亚微米粉粒子的逃逸î 适应烟气量和烟气含硫量的变化î 适应烟气中粉尘含量的变化î 不需要催化装置,投资、运行费用低î 系统阻力低,设备占地面积小。
SNDR除尘原理粉尘随烟气进入脱硫塔后,快速与吸收液混合作用,并在脱硫塔中发生剧烈扰动,同时使粉尘的表面由原来的气—固界面被液—固界面代替,粉尘的表面由水膜代替气膜,产生吸附,凝聚现象,并在尘粉间形成液桥,从而增强了亚微米粉尘捕集能力。
在烟气返向过程中,粉尘穿越两层循环液膜时又进一步增强了捕集效果,提高了除尘系统的总除尘效率。
SNDR脱硫脱硝的特点(1)脱硫效率高。
在脱硫塔内,氨水与烟气充分接触,属于气-液反应,瞬时完成,相同反应条件下,是反应速率最快的。
(2)同步多功能一体化。
具有良好的脱硫和除尘功能,同时NO产生瞬间反应成氮气和水完成脱硝功能。
(3)液气比值小。
(4)系统阻力小由于反应塔属于喷射塔,塔本体阻力比填料塔阻力小,仅为填料塔阻力的1/3。
经过阻力计算以及多次实际应用,测试证明塔本体阻力小于1000Pa。
(5)脱硫反应温度区间可变范围大在40℃~180℃反应塔内,脱硫效率依然能够达到95%以上。
液体pH值控制在生成(NH4)2SO3范围之内,进而降低了设备的腐蚀(已有反应塔使用10年以上的范例)。
循环液的温度越高,硫铵的溶解度越大,运行中一般控制在使循环液接近饱和结晶的浓度以下,使其在塔外结晶,有效避免堵塞现象。
除尘、脱硫、脱硝工艺原理及流程

除尘、脱硫、脱硝工艺原理及流程随着气候变化和环境保护意识的增强,我国对空气质量的要求越来越高。
因此,烟气净化技术成为了重要的环保工程,其中包括除尘、脱硫和脱硝三个方面。
下面,让我们了解一下这些技术的原理和流程。
一、除尘除尘是烟气净化中最基础和最常见的一步处理。
它通过与高速运动的烟气产生作用,使烟气中的固体颗粒被收集到除尘器内,以达到净化空气的目的。
常见的除尘设备有静电除尘器、袋式除尘器、湿式除尘器、离心除尘器等。
除尘器的工作原理主要是利用电场作用、虑材拦截、冲击折减等原理进行粉尘的分离。
二、脱硫燃煤、燃油等热力发电和工业生产过程中,硫元素会与氧气形成二氧化硫(SO2)等有害气体,这些有害气体对环境和人体健康造成威胁。
因此,脱硫净化是非常重要的烟气净化步骤。
常用的脱硫技术包括吸收法、氧化-吸收法、诱导法、半干法、干法等。
吸收法是目前应用最广泛的技术,是烟气中SO2与吸收液中反应生成二氧化硫溶液的过程,其主要反应公式为CaCO3+SO2+0.5O2+H2O→CaSO4?2H2O+CO2。
三、脱硝脱硝技术主要是通过化学反应将NOx变为N2或N2O,以减少氮氧化物的排放。
目前,常用的脱硝技术有选择性催化还原(SCR)法、选择性非催化还原(SNCR)法、NH3氧化脱硝法等。
其中,SCR法利用了化学催化反应的原理,通过向烟气中喷射适当的氨水,在催化剂的作用下将NOx还原为N2和H2O。
NH3氧化脱硝法是通过将NH3气体与烟气中的NOx反应生成N2和H2O的方法。
以上就是除尘、脱硫、脱硝工艺的原理和技术流程,它们对于改善空气质量、保护大气环境起着至关重要的作用。
在实际应用中,需要根据不同的工艺特点和实际情况,采用合适的技术方案进行处理,以达到最佳的净化效果。
除尘、除灰、脱硫系统的运行及检修维护脱硫技术方案

技术卷除尘、除灰、脱硫系统的运行及检修维护技术文件第一章项目总述 (4)1总则 (4)1.1项目概况 (5)1.2项目基本设计条件 (10)2项目内容及界限划分(运行、检修维护范围) (11)2.1项目内容总述 (11)2.2项目运行范围 (11)2.3项目检修维护 (14)2.4项目界限划分 (17)第二章运行维护安全、质量目标及考核标准 (19)1总则 (19)2考核依据/引用文件 (19)3考核方式 (19)4考核内容与标准 (20)5附则 (20)6有关生产指标 (21)附表1 维护管理安全、质量目标 (21)附表2 维护管理考核标准 (22)附表3 设备维护质量与可靠性指标考核 (23)附表4 维护作业安全工作考核 (24)附表5 维护文明生产工作考核 (31)附表6 运行管理安全、质量目标 (32)附表7 运行管理考核标准 (33)附表8 运行安全工作考核 (35)附表9 运行文明生产考核标准 (38)第三章设备缺陷管理标准 (39)第四章日常维护、检修内容及要求 (40)1总则 (40)2项目内容 (40)3其它工作内容 (41)4检修维护目标 (41)第五章项目合同承包商服务范围 (45)1承包商维护范围 (45)2承包商运行工作范围 (49)第六章安全管理协议 (51)1承包商资质要求 (51)2招标人的安全责任 (51)3承包商的安全责任 (51)第七章项目材料消耗 (53)1物资管理规定 (53)2招标方负责提供的材料 (53)3承包商负责提供的材料 (54)第八章招标方提供的专用工具 (56)1锅炉专业专用工具: (56)2汽机专业专用工具: (58)3电气专业提供专用工具清单: (60)4输煤系统专用工具清单: (60)第九章项目综合管理 (62)1项目组织机构 (62)2岗位职责 (66)3日常检修维护管理制度 (69)4检修维护设备缺陷管理制度 (78)5检修维护安全文明施工制度 (80)第十章项目主要系统、设备检修规程 (85)第一节除尘、除渣系统 (85)1电除尘器检修技术标准 (85)2仓泵检修技术标准 (86)3气化风机检修技术标准 (87)4气力除灰系统管道检修技术标准 (88)5渣浆泵检修技术标准 (88)6带式输送机检修技术标准 (89)7渣仓检修技术标准 (90)8刮板捞渣机检修技术标准 (91)9散装机检修技术标准 (92)10空压机检修技术标准 (92)第二节脱硫系统 (93)1吸收塔体、设备检修规范 (93)2搅拌器检修规范 (96)3循环泵检修规范 (98)4氧化风机检修规程 (100)5振动给料机检修规程 (102)6称重皮带给料机检修规程 (102)7埋刮板输送机检修规程 (104)8湿式球磨机的检修规程 (105)9增压风机检修规程 (114)10烟气档板门规程 (116)11旋流站检修规程 (117)12真空皮带机检修规程 (118)13真空泵检修规程 (121)第三节防腐施工、验收规程 (123)1喷砂 (123)2底涂 (123)3衬胶 (123)4鳞片树脂施工 (125)第一章项目总述1 总则(1)本规范书适用于一期2×600MW机组工程B标段电除尘、除灰渣、脱硫系统装置的运行及检修维护。
锅炉烟气脱硫脱硝系统运行问题及处理措施

锅炉烟气脱硫脱硝系统运行问题及处理措施关键词:烟气脱硫脱硝工艺脱硫工艺国家对环保要求的逐渐提高,大部分锅炉厂针对烟气处理系统都进行了深入改造。
随即而来出现硫酸铵浆液结晶差,液态氨损耗大,脱硫塔喷头堵塞,脱销系统中氨水浓度较低以及氮氧化物指标不达标等一系列问题。
锅炉排出的烟气在脱硫上,工业锅炉目前常用氨法脱硫工艺,即烟气脱硫、氧化空气、硫铵、检修排空、工艺水等子系统。
如果采用一炉一塔进行全烟气脱硫,脱硫效率能达到98%以上。
在脱硝上,目前常用SNCR脱硝工艺,使用氨水作为还原剂,脱硫效率在50%以上,且NOx排放浓度控制在200mg/Nm3以下。
1锅炉烟气脱硫脱硝概述1.1脱硫工艺锅炉烟气脱硫,指的是除去烟气中的SO、SO2等硫化物,以满足保护环境的要求。
按照不同的工艺,可以分为石灰石-石膏脱硫、磷铵肥法脱硫、烟气循环流化床脱硫、海水脱硫、氨水洗涤法脱硫、电子束法脱硫等。
分析烟气脱硫工艺的特点,主要如下:第一,能够捕捉多种有害气体,从而提高脱硫效率;第二,脱硫过程节水节电、降低了运行成本;第三,脱硫设备操作简单、维修量少,能够适应复杂环境,有利于日常管理和维护;第四,不同工艺能够处理不同含硫量的烟气,或者采用联合工艺,能够提高脱硫效果。
1.2脱硝工艺锅炉烟气脱硝,指的是除去烟气中的硝化物NOx。
从脱硝工艺上来看,主要包括两种类型:一是从源头上治理,减少煅烧期间生成的NOx含量,常见如使用低氮燃烧设备;或者调整配料方案,使用矿化剂降低熟料温度;或者炉和管道分段燃烧,从而控制温度高低。
二是从末端治理,降低烟气中的NOx含量,目前应用广泛,常见如活性炭吸附脱硝、电子束脱硝、SCR技术、SNCR技术等。
以SNCR 脱硝工艺为例,在小型机组中的脱硝效率为80%以上,在大型机组中的脱硝效率为25%-40%,常用于低氮燃烧技术的辅助处理手段,优势在于占地面积小、工程造价低,而且适用于老厂改造工程。
2脱硫脱硝系统存在问题及处理措施2.1硫酸铵结晶颗粒小及处理2.1.1主要原因主要原因是因为进入脱硫塔烟道处防腐层脱落到浓缩段,堵塞二级循环泵喷头,使得脱硫塔浓缩段温度太高。
- 1、下载文档前请自行甄别文档内容的完整性,平台不提供额外的编辑、内容补充、找答案等附加服务。
- 2、"仅部分预览"的文档,不可在线预览部分如存在完整性等问题,可反馈申请退款(可完整预览的文档不适用该条件!)。
- 3、如文档侵犯您的权益,请联系客服反馈,我们会尽快为您处理(人工客服工作时间:9:00-18:30)。
除尘、脱硫、脱硝部分一、采购内容:
2台75t/h循环流化床锅炉除尘、脱硫、脱硝系统设计、制造、供货及安装调试。
二、基础资料
1、燃料(校核煤种由需方另行提供)
1)锅炉设计煤种的工业分析
2)锅炉设计煤种的元素分析
2、锅炉煤质粒度要求
煤粒度0-10mm。
3、石灰石(脱硫剂)
石灰石成分:CaCO3含量93%
石灰石粒度:0-1mm
钙硫比:2-3
生石灰
生石灰成分:CaO含量>90%
T60活性实验≤4分钟
粒径:160-250目,制备采用轻烧立窑生产,创面新鲜,库存时间不大于72小时4、主要工艺参数
本期工程装设两台75t/h次高温次高压循环流化床燃煤锅炉。
锅炉为全钢架结构,锅炉为半露天布置。
额定蒸汽流量75t/h
额定蒸汽温度485℃
额定蒸汽压力 5.29MPa.g
给水温度104℃
排烟温度135℃
额定工况下锅炉设计效率≥89%
锅炉运转层标高7m
三、脱硫系统
3.1设计原则及工艺系统选择
本期工程执行《火电厂大气污染物排放标准》GB13223-2011。
烟尘排放浓度≤30mg/m3
S0
排放浓度为≤100mg/m3
2
针对严格的环保标准,结合循环流化床锅炉自身优势,根据煤种含硫量,初始SO
2理论排放浓度约为1773mg/Nm3。
我们选用炉内石灰石脱硫(干法)+炉后半干法法脱硫。
通过相关计算进行二级脱硫系统效率合理分配。
排放浓度<750mg/Nm3,半干法脱硫效本工程炉内脱硫效率按照60%设计,脱硫后SO
2
率按照88%设计,二级脱硫系统复合脱硫效率可以达到95%以上,保证烟囱SO
排放浓度
2
≤100mg/Nm3。
炉内脱硫剂采用石灰石粉。
CFB锅炉的分离器结构设计,低温燃烧技术(约850-950℃),使得炉内石灰石脱硫(干法)成为其特有的低成本脱硫技术。
结合CFB锅炉燃烧控制优化技术(燃烧温度、燃烧氧量、高分离效率、石灰石喷入位置优化),炉内石灰石脱硫(干法)效率可稳定的运行达到80%以上。
半干法脱硫在锅炉出口和除尘器之间建设一座脱硫塔,脱硫剂采用生石灰并经消化后喷入脱硫塔,脱硫灰在脱硫塔与除尘器之间多次循环。
吸收剂和副产物均为干态,没有废水;相对湿法脱硫,本系统烟温降低有限,3.2脱硫系统工艺配置
3.2.1炉内石灰石脱硫系统
本工程配套炉内石灰石脱硫系统,要求石灰石纯度>93%,石灰石粒度0~1mm,水分含量<0.5%。
炉内石灰石脱硫系统设一座石灰石粉仓,粉仓容积40m3,满足2台锅炉1天的石灰
石耗量。
粉仓顶部设置库顶收尘器、料位计、真空压力释放阀,库顶收尘器用于净化罐车给粉仓装料时的含尘气体。
高低料位计用于控制粉仓料位高度并发出料位报警信号。
石灰石输送方式采用罗茨风机低压稀相气力输送。
粉仓底部设置2个卸料口,仓下配套气动插板阀、缓冲仓、变频旋转给料机和粉料输送装置。
粉料通过罗茨风机送入锅炉的炉膛,使石灰石粉迅速煅烧并发生固硫化学反应,达到脱硫目的。
输送管路采用无缝厚皮钢管,所有带料弯头均采用内衬陶瓷耐磨弯头。
3.2.2半干法脱硫+除尘系统采购范围
处理系统采用“半干法烟气脱硫+布袋除尘”工本工程循环流化床炉后烟气SO
2
艺,系统包括:烟气反应器及烟道系统、布袋除尘器系统、灰循环系统、吸收剂存储及输送系统、给水系统、自动控制系统等几部分组成;具体为自锅炉空预器出口外墙面至除尘脱硫系统出净烟气口烟道与引风机入口连接的法兰范围内工艺系统。
半干法脱硫烟气处理流程:锅炉→烟气循环流化床干法脱硫塔→布袋除尘器→引风机→烟囱。
半干法脱硫采用Ca(OH)
作脱硫剂,根据脱硫需要加入到脱硫塔内。
2
脱硫塔采用烟气循环流化床(CFB)反应原理,是半干法脱硫反应的核心设备。
单套烟气脱硫设备脱硫塔自下而上依次为进口段、塔底排灰装置、文丘里加速段、循环流化床反应段、顶部循环出口段。
脱硫后布袋采用(半)干法脱硫专用的低压脉冲布袋除尘器
半干法脱硫工艺在炉内脱硫的基础上进行设计,锅炉炉内脱硫后,出口硫含量为750mg/m3,半干法脱硫效率88%。
脱硫除尘后达到以下工艺指标(单台)Array
3.3主要设备选择(两台炉)
四、脱硝系统
4.1设计原则
4.1.1本项目采用SNCR选择性非催化还原烟气脱硝工艺,还原剂采用浓度20%氨水。
4.1.2脱硝工程目标:实现2台75t/h循环流化床锅炉最大连续工况(BMCR),初始烟
气NOx浓度≤250mg/Nm3,炉膛出口温度830—900℃工况下,脱硝后烟气NOx排放浓度≤100mg/Nm3,氨逃逸≤8mg/Nm3;
4.1.3脱硝公用系统按照2台炉公用设计,公用系统包括氨水储存、稀释水储存等;4.1.4脱硝工程建成投运后,无二次污染的产生;
4.1.5脱硝设施力求工艺流程简捷,维护操作方便,控制可靠,设备布置合理,结构紧凑,投资少,运行费用低,对锅炉负荷适应性强。
4.2工艺流程
本项目选用20%氨水作为还原剂的SNCR工艺。
氨水灌装时,槽车将氨水由外界运输到厂区内指定地点,通过氨水加注泵打到氨水储罐储存待用。
氨水储罐容积以满足2台炉B-MCR工况不少于5天需求量,以保证整个脱硝系统连续平稳运行。
在进行SNCR 脱硝时,氨水输送泵将20%的氨水从氨水储罐中抽出,在静态混合器中和工艺水混合稀释成5-10%的氨水(浓度可在线调节),输送到炉前SNCR喷枪处。
氨水通过喷枪雾化后,以雾状喷入炉膛内,与烟气中的氮氧化物发生化学反应,生成氮气,去除氮氧化物,从而达到脱硝目的。
4.3SNCR脱硝工艺系统组成
整套氨水-SNCR脱硝装置由氨水卸料与储存系统、氨水输送系统、稀释水系统、混合分配系统、喷射系统、自动控制系统组成。
4.4主要设备选择(两台炉)
五、全套电气柜、控制柜(控制柜见附件)。