转炉炼钢煤气回收系统的分析
转炉煤气回收工艺简述

转炉煤气回收工艺简述伴随冶炼能力提升和技术发展,煤气从冶炼副产品变成富产品。
因为在过程所产生炉气中含量有大量一氧化碳,经过对炉气搜集、储存,又将这些一氧化碳作为燃气应用于生产之中。
高炉炼铁生产出铁水中有大量碳,当转炉温度>1700℃时,有大量碳被氧化,生成一氧化碳和二氧化碳,每一吨铁水可产生100m3一氧化碳,因为设备、技术等方面原因,只有60%-80%一氧化碳被回收。
在转炉炼钢前5分钟里,因为顶吹氧,大量纯氧气和高温铁水接触,在高温和充足氧气情况下,铁水中硅和氧气反应,燃烧生成氧化硅,这个反应有两个作用:一、铁水中大部分硅被氧化,生成钢渣脱离铁水。
二、硅燃烧放出大量热,提升了铁水温度。
(在这5分钟里所产生气体,不能回收)铁水温度升高后,氧气和碳反应生成一氧气化碳和二氧化碳,因为烟道几乎是密封,一氧化碳不会和外界氧气发生反应,所以烟道内一氧化碳保持它原状,铁水液面上气体温度可达成1700多度,高温气体进入一文,二文,然后进入旋流塔,在旋流塔中,高温气体上升,旋流塔上方有转炉浊环水向下喷淋,和煤气中灰尘凝结下落,达成洗涤煤气目标,同时使气体温度下降,40度气体进入一次除尘风机,对于进入一次除尘风机煤气,是用往返收还是放散,在线分析仪能够在一秒钟之内分析出结果,假如当初一氧化碳含量大于等于25%,且氧含量小于2%,那么就可回收,此时PLC自动控制打开旋转水封阀门,再打开三通阀(此时放散阀门被关闭)同时通往煤气柜阀门打开,开始回收煤气。
出了旋转水封煤气顺着管道进入预防回气水封(这里有四道,在正常回收情况下,为了减小对煤气阻力,这个水封没有水,当检修时,为了预防煤气柜内煤气回返,在水封里面注入适量水)再进入防沉降水封,(防沉降水封作用相当于膨胀节,起到管道伸缩作用,在管道变形时,相互不影响,不至于拉裂管道。
)当煤气进入煤气柜后,临时在里面存放,煤气柜容量大小决定了气柜内气体存留时间。
“断续回收,连续使用”是煤气回收基础状态。
转炉煤气回收工艺

转炉煤气回收工艺转炉煤气回收工艺是一种重要的环保技术,可以大量减少工业生产过程中的废气排放,这对于保护环境、减少污染、节约能源具有非常重要的意义。
转炉煤气回收工艺是将高温炼钢废气中的一部分可燃气体重新利用,使其燃烧后产生的热能可以继续用于炼钢工艺中。
这种自给自足的方式在钢铁行业中具有显著的优势,因为钢铁生产需要大量的热能来保持高温状态。
在传统的炼钢工艺中,高温炼钢废气中的大部分热能和可燃气体都是被浪费掉了,直接排放到大气中造成了严重的环境污染。
而采用转炉煤气回收工艺后,这些废气中的可燃气体可以被有效回收利用,从而达到节约能源、减少排放的目的。
转炉煤气回收工艺主要分为两个步骤:收集和利用。
首先,需要在炉膛的废气口处设置一个废气管道,将所有的高温炼钢废气收集起来。
在这个过程中,应该对废气管道进行良好的密封,避免废气的泄漏和外泄,从而确保废气能够稳定地流向后续的工艺流程中。
其次,将收集到的废气送入热风炉或燃烧炉中进行燃烧利用,将废气中的可燃气体转换成热能。
这个过程需要使用一些特殊的设备来控制废气的流量、温度和压力等参数,以确保废气燃烧的效果达到最佳状态。
通过这样的转炉煤气回收工艺,可以大大提高炼钢过程中的能效,降低工业生产过程中的废气排放,从而达到环保减排的目的。
不仅如此,这种技术还可以大幅降低企业的用能成本,减少经营成本,提高企业的经济效益,具有非常积极的社会和经济意义。
总之,转炉煤气回收工艺是一项非常重要的绿色技术,可以促进钢铁产业的可持续发展,实现环保减排、节约能源的目标。
随着环保意识的提高和技术的不断进步,相信这种技术在未来的发展中将会得到更广泛的应用和推广。
转炉煤气的回收与利用

转炉煤气的回收与利用1,转炉煤气的特性;1.转炉煤气是一种无色、无味的有毒气体,发热量为7117.56~8373.64千焦/m,燃点为600~700℃,密度为1.25~1.29㎏/nm⒊煤气中含有50﹪以上的一氧化碳,若发生泄露极易造成人员中毒。
转炉煤气与空气在有限空间内,混合成一定比例后,遇到明火或高温就会发生爆炸。
其在空气中爆炸极限为12.5%~75%。
2. 转炉煤气的三大特性为:易中毒﹑易着火﹑易爆炸。
另外,转炉煤气还具有腐蚀性﹝生成硫酸、碳酸﹞、与尘毒危害等特性。
2,转炉煤气系统使用现状;在采用吹氧冶炼的氧气转炉炼钢过程中,其烟气量、烟气成分和烟气温度随冶炼阶段呈周期性变化。
烟尘中金属铁约占13%,Fe0约占68.4%,特别在吹炼中期CO体积分离高达80%以上,一般情况下,转炉煤气成分中CO的体积分数约达 55%~66%,当CO在60%左右是,其热度可达8MJ/m3,而每吨钢烟尘量一般为10~20㎏∕t。
由此可见,转炉煤气中CO 含量很高,烟尘中铁含量也很高,具有很高的回收利用价值。
1.国内外概况和发展趋势;随着氧气转炉炼钢生产的发展,炼钢工艺的日趋完善,相应的除尘技术也在不断的发展完善。
目前,氧气转炉炼钢的净化回收主要有2种方法,一种是煤气湿法﹙OG法﹚净化回收系统,一种是煤气干法﹙LT法﹚净化回收系统。
日本新日铁和川崎公司于上世纪60年代联合开发研制成功OG法转炉煤气净化回收技术。
OG法系统主要由烟气、冷却、净化、煤气回收和污水处理等部分组成。
其烟气经冷却烟道进入烟气净化系统,烟气净化系统包括2级文氏管、脱水器和水雾分离器,烟气经喷水处理后,除去烟气中的烟尘,带烟尘的污水经分离、浓缩、脱水等处理,污泥送烧结厂作为烧结原料,净化后的煤气被回收利用。
系统全过程采用湿法处理,该技术存在的缺点:一是处理后的煤气含尘量较高,达100㎎/m3以上,要利用此煤气,需在后部设置湿法电除尘器进行精除尘,将其含尘质量浓度降至10㎎/m3 以下;二是系统存在二次污染,其污水需进行处理;三是系统阻损达,所以能耗大,占地面积大,环保治理及管理难度较大。
转炉炼钢煤气回收

“LT”法系统主要是由蒸发冷却塔、静电除尘器、除尘风机、切换站、煤气冷却器等几部分组成。 转炉1500℃的高温烟气经汽化冷却烟道冷却至800~1000℃后,然后进入烟气净化系统。烟气净化系统
由蒸发冷却塔和圆筒型静电除尘器组成,烟气温度通过蒸发冷却器后降至170~200℃,同时通过调质处理, 降低了烟尘的电阻率,收集了粗粉尘。烟气经过这一初步处理后,进入圆筒型静电除尘器,进行进一步净 化,使其含尘质量浓度降至15mg/m3以下,从而达到最佳的除尘效率。
2.2 主要设备及工作原理
汽化冷却烟道:
转炉汽化烟道(也称为余 热锅炉)是转炉炼钢的主要配 套设备之一,该设备在工作时 要最大限度地收集高温烟气, 高温烟气的温度在1400摄氏度1600摄氏度,这些烟气在循环 泵产生的负压作用下,在汽化 烟道内流通,带有火星未燃烧 尽的钢渣进入燃烧室,之后烟 道内的温度在800摄氏度左右, 然后烟气随着烟道出口进入蒸 发冷却塔。
莱钢从2002年底开始酝酿转炉采用干法除尘技术。2003年完成施工图设计和控制系统的软件编程。 2004年7月建成投产, 对3*120t转炉使用了干法除尘,而投产后10天就达到设计能力,并持续稳定地生产。 至今三套“LT”系统均已通过了考核验收。
2) 缺点: (1)系统复杂,从而要求设备、仪表仪器质量高,以满足生 产要求;对施工质量要求也高; (2)要求管理和操作水平高,必须对管理和操作人员进行较 完善的培训,并在实际生产中达到熟练操作和维护;并且要 与炼钢工艺操作紧密配合和协调,杜绝野蛮操作; (3)一次投资高。
“OG”法工艺系统缺点:
由于该系统全过程采用湿法处理,技术存在以下几个缺点: 一是处理后的煤气含尘量较高,高达100mg/m3,要利用此煤气,需进一步净化方能使用; 二是系统存在二次污染,其污水需进行处理; 三是系统阻损大,所以能耗大,占地面积大,环保治理及管理难度较大。
转炉负能炼钢与煤气回收技术范本(2篇)

转炉负能炼钢与煤气回收技术范本炼钢是钢铁生产过程中的关键环节,炼钢负能是指在炼钢过程中产生的废热和废气。
钢铁行业是我国重要的工业部门,但同时也是主要的能源消耗和环境污染源之一。
为了实现钢铁行业的可持续发展,转炉炼钢过程中的废热和废气应得到充分利用和净化。
炼钢转炉是目前钢铁生产中常用的设备之一。
转炉炼钢是利用转炉炉膛中高温燃烧的氧气与铁水进行反应,将铁水中的杂质氧化脱除,从而得到高质量的钢水的一种冶炼方法。
然而,在转炉炼钢过程中,产生了大量的废热和废气,如果不能有效利用和处理,将造成能源的浪费和环境的污染。
炼钢转炉废热的回收利用是一种有效的能源回收利用方式。
转炉炉膛中废气含有大量的热能,通过炉膛的余热锅炉回收废气中的热能,可以用来产生蒸汽或热水,用于工业生产或供暖。
此外,转炉炉膛中的废气中还含有一定浓度的炉尘和有害物质,需要通过除尘器等设备进行净化处理,以减少对大气环境的不良影响。
炼钢转炉煤气回收技术是一种节能减排的重要手段。
在转炉炼钢过程中,炉膛中需要加入大量的燃料,其中包括煤炭。
煤炭的燃烧产生了大量的废气,其中含有大量的热能和有害物质。
通过合理设计煤气回收系统,可以回收废气中的热能,并通过余热锅炉产生蒸汽或热水。
同时,废气中的有害物质也需要通过除尘器等设备进行净化处理,以保护环境和人类健康。
转炉负能炼钢与煤气回收技术的范本是针对以上问题提出的一种解决方案的指导性文件。
以下是其中一些关键技术的范本介绍:1. 转炉废热回收技术范本:转炉炉膛中的废气通过余热锅炉回收技术进行能源回收。
关键技术包括: 余热锅炉的合理设计和选型、废气预处理和净化技术、余热锅炉运行的控制和优化等。
2. 转炉煤气回收技术范本:煤气回收系统设计的关键技术包括: 废气净化和除尘技术、废气热能回收技术、余热锅炉的选型和运行控制等。
融化煤气的回收利用是其中的重要环节之一,其关键技术包括: 融化煤气的净化和回收、融化煤气的利用方式和设备的设计等。
转炉负能炼钢与煤气回收技术
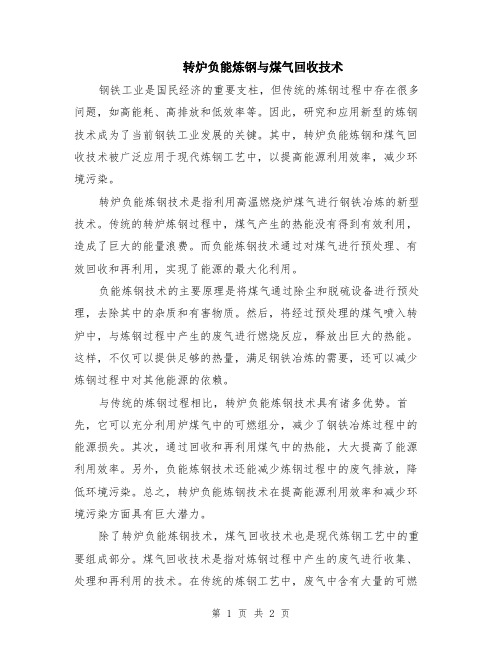
转炉负能炼钢与煤气回收技术钢铁工业是国民经济的重要支柱,但传统的炼钢过程中存在很多问题,如高能耗、高排放和低效率等。
因此,研究和应用新型的炼钢技术成为了当前钢铁工业发展的关键。
其中,转炉负能炼钢和煤气回收技术被广泛应用于现代炼钢工艺中,以提高能源利用效率,减少环境污染。
转炉负能炼钢技术是指利用高温燃烧炉煤气进行钢铁冶炼的新型技术。
传统的转炉炼钢过程中,煤气产生的热能没有得到有效利用,造成了巨大的能量浪费。
而负能炼钢技术通过对煤气进行预处理、有效回收和再利用,实现了能源的最大化利用。
负能炼钢技术的主要原理是将煤气通过除尘和脱硫设备进行预处理,去除其中的杂质和有害物质。
然后,将经过预处理的煤气喷入转炉中,与炼钢过程中产生的废气进行燃烧反应,释放出巨大的热能。
这样,不仅可以提供足够的热量,满足钢铁冶炼的需要,还可以减少炼钢过程中对其他能源的依赖。
与传统的炼钢过程相比,转炉负能炼钢技术具有诸多优势。
首先,它可以充分利用炉煤气中的可燃组分,减少了钢铁冶炼过程中的能源损失。
其次,通过回收和再利用煤气中的热能,大大提高了能源利用效率。
另外,负能炼钢技术还能减少炼钢过程中的废气排放,降低环境污染。
总之,转炉负能炼钢技术在提高能源利用效率和减少环境污染方面具有巨大潜力。
除了转炉负能炼钢技术,煤气回收技术也是现代炼钢工艺中的重要组成部分。
煤气回收技术是指对炼钢过程中产生的废气进行收集、处理和再利用的技术。
在传统的炼钢工艺中,废气中含有大量的可燃物质和热能,没有得到有效利用。
而煤气回收技术通过对废气的处理,可以使其达到清洁排放标准,并回收其中的可燃物质和热能。
煤气回收技术的主要原理是通过收集废气,并进行除尘、脱硫等处理,使之达到环保要求。
然后,将处理后的废气中的可燃物质和热能回收利用,提供给炼钢过程中的各项能源需求。
这样,不仅可以减少对其他能源的依赖,还可以减少废气排放,保护环境。
煤气回收技术的应用对钢铁工业的可持续发展具有重要意义。
转炉炼钢煤气回收系统的分析

、
煤气回收系统流程 图 二 、气体分析仪 的作用 三、回收阀组 系统作用 气 体分析在整个煤气 回收系统 中是不可缺少的设备之 一, 回收阀组包 括旁通 阀、三通阀、水封 阀三部分组成 , 在 对
通 过对转炉烟气 的气体分析可 以对其 中的 C 0含量进行检 查, 达 到用户使用标准 , 同时对氧气 的检测可 以使得煤气 能够 安全 使 用。 根 据炼钢工 艺过程 中的检测 , 在氧气含量达到爆 炸极限 范围以下时煤气含量完全 能够符合用户使用标准( 除特 殊情 况 以外,如分析仪检 测出现异 常或工 艺条件改变等 ) ,故氧 气分 析仪是炼钢 煤气 回收气体检测 中的重 中之重 。 当前煤气 回收系统 中氧气分 析仪检测 的设 备主要有取 样 分析和 在线分析 仪两种 。 取样分析仪具有一定 的滞后情况,逐 渐 退出炼钢 煤气 回收检测 的舞 台; 而在线激光分析仪具有相应 时间短 , 分析准确 ,便于维护等特 点,得到广大用户的积极相 应 ,逐渐 占领了气体 分析 的舞 台。 在当前运用 的主要以激光 吸收光谱 ( D L A S ) 技术为主 ,利 用激光能量被气 体分子 “ 选 频” 吸收光谱 的原理来测量气体浓 度 ,由半导体激光器发射出特 定波长的激光 束 ( 仅能被被测气 体吸收) ,穿过被测气体 时,激强度 的衰减与被测气体 的浓度 成一定 的函数关 系 , 因此。 通过测量激光强度衰 L A S ) 技术 利用 激光 能量 被气体分 子“ 选频 ”吸收光谱的原理来测量气体浓度,由半导体激光器
消费 电子
2 0 1 3 年 7月下
C o n s u me r E l e c t r o n i c s Ma g a z i n e 技 术 交 流
转炉炼钢煤气回收系统的分析
转炉负能炼钢与煤气回收技术

转炉负能炼钢与煤气回收技术是一种利用工厂废气中的高温高压煤气进行能源回收的技术。
在传统的转炉炼钢过程中,大量的煤气会产生,并直接排放到大气中,造成能源的巨大浪费和环境的污染。
而通过对煤气进行回收利用,不仅可以减轻环境负荷,还能够降低能源成本,提高能源利用效率。
本文将介绍转炉负能炼钢与煤气回收技术的原理、应用以及存在的问题和挑战。
转炉负能炼钢是一种常用的炼钢工艺,其核心原理是利用煤气在高温高压条件下与炉料中的矿石和还原剂发生燃烧和反应,从而使炉料中的铁和矿石还原成金属铁。
在传统的转炉负能炼钢过程中,煤气是燃烧掉的,只产生热能,而通过煤气回收技术,煤气中的能源可以被有效利用。
煤气中的主要组分是一氧化碳、氢气、甲烷等可燃气体,其热值很高,可以用来发电、供热等方面。
煤气回收技术主要包括废气再利用和废气发电两种方式。
废气再利用是指将煤气作为热源加热转炉内的炉料,提高炉料的温度,加快冶炼过程。
废气发电是指将煤气中的能源转化成电能,通过发电机向企业供电或者并入电网,以实现能源的再利用。
无论是废气再利用还是废气发电,都能够有效减少转炉负能炼钢过程中的能源消耗,提高能源利用效率。
转炉负能炼钢与煤气回收技术在钢铁工业中得到了广泛的应用。
以国内一些大型钢铁企业为例,很多企业在进行转炉炼钢过程中都引进了煤气回收技术。
通过煤气发电,这些企业可以降低电力采购成本,提高能源利用效率;同时,由于燃烧过程中产生的废气不再排放到大气中,大大减少了对环境的污染。
然而,转炉负能炼钢与煤气回收技术也存在一些问题和挑战。
首先,煤气回收技术需要有先进的设备和技术支持,对企业的投入较大,对一些小型钢铁企业而言可能难以承担。
其次,煤气回收技术在实施过程中需要解决一些技术难题,如煤气的净化和处理问题,燃烧稳定性问题等。
此外,由于煤气回收技术的广泛应用,也会带来新的环境问题,如废气的排放标准和处理问题等。
总之,转炉负能炼钢与煤气回收技术是一项具有巨大潜力和发展前景的科技成果。
- 1、下载文档前请自行甄别文档内容的完整性,平台不提供额外的编辑、内容补充、找答案等附加服务。
- 2、"仅部分预览"的文档,不可在线预览部分如存在完整性等问题,可反馈申请退款(可完整预览的文档不适用该条件!)。
- 3、如文档侵犯您的权益,请联系客服反馈,我们会尽快为您处理(人工客服工作时间:9:00-18:30)。
转炉炼钢煤气回收系统的分析
摘要:副产煤气的全部回收综合利用,是反映钢铁企业能源利用水平及节能降耗水平的关键指标,是实现负能炼钢和降低炼钢工序能耗的关键环节,同时能降低钢厂污染物排放总量,实现节能环保双赢,具有环境效益和经济效益。
本文主要对转炉炼钢煤气回收系统进行了分析。
关键词:炼钢转炉除尘系统回收条件煤气回收量
引言
转炉煤气回收是把炼钢转炉生产过程中的副产品—一氧化碳含量进行回收再利用的生产工艺。
转炉生产时,氧抢顶吹脱碳过程中产生的一氧化碳高含量的烟气在经过冷却、除尘、分析、回收进煤气柜、精(电)除尘、利用(如发电)的全过程统称为转炉煤气回收再利用。
氧气顶吹转炉煤气的生成,主要来自铁水中碳的氧化,其产气量的大小也取决于铁水含碳量的大小,氧气顶吹转炉煤气产气量中,能够回收使用的部分称为实际回收量,回收煤气的炉数与冶炼炉数之比称为煤气回收率,煤气回收量及回收率与操作、技术水平有关。
这项工作的安全可靠性、科学回收性及产能提高性的技术,是转炉煤气回收的关键。
目前,全国很多转炉炼钢厂都实现了煤气的回收,由于该技术在各家企业运用的不同特点和采用的技术、工艺不同,煤气回收最终的产能也有较大的差异,效益也不尽相同。
对转炉炼钢煤气回收工艺分析
转炉煤气回收的成熟技术有氧气转炉煤气回收工艺(OG法) 和LT干式回收工艺,我国钢铁企业目前运行中的煤气回收系统多是在上述两种工艺原理基础上,根据自身情况改造设计而成的,其运行效率在不断提高。
氧气转炉煤气回收工艺
OG法回收转炉煤气在目前的世界炼钢领域是成熟"先进"可靠的技术,全世界已有200 多套设备投入生产运行,效果显著。
采用OG法回收的转炉煤气热值高"回收量大"除尘效率高,其设备寿命长"安全性好"自动化程度高。
OG法法工艺中,转炉烟气净化系统采用湿式未燃法‘比肖夫’系统,其流程为: 转炉烟气借风机吸力进入汽化冷却烟道,回收部分烟气余热。
从汽化冷却
烟道出来的烟气在上部进入‘比肖夫’除尘冷却装置,‘比肖夫’装置上部是一个洗涤塔,气液同向而行,进行降温和粗除尘。
然后,气体进入下部的可调文氏管进行精除尘,经除尘后的气体由下部返入筒体进行脱水,然后从中部引出#比肖夫$装置。
经降温除尘的净煤气经风机加压后通过三通切换阀,当烟气中的 CO 及 O含量符合回收要求时,则进入煤气储柜储存,需使用时进行精除尘和加压供用户使用。
在烟气不合格时,通过三通切换阀将烟气送至放散管点火放散。
LT干式回收工艺
LT法是德国鲁奇公司与蒂森公司合作开发的转炉烟气净化"回收"利用的干式工艺,其基本原理是: 当转炉吹炼时,O和C 之间发生反应产生含有高浓度 CO 和烟尘的转炉煤气( 烟气) 。
为了回收利用高热值的转炉煤气和减少污染,需对烟气进行净化,首先将转炉烟气经过废气冷却系统,然后进入蒸发冷却器,喷水蒸发使烟气得到冷却。
由于烟气在蒸发器中得到减速,使烟气中粗颗粒的粉尘沉降下来,通过链式输送机以及闸板阀将粉尘排出。
同时,烟气通过荒煤气管道导入设有4个电场的静电除尘器,在电场作用下使粉尘和雾状颗粒物吸附在收尘极板上,使烟气得到净化。
电除尘器下部的集灰用扇形刮灰器刮到位于其下部的链式输送机中,并送入中间料仓,然后通过气力输送系统再将干灰送到压块系统的集尘料仓中。
切换站由联锁控制,当符合煤气回收条件时,回收侧的钟型阀自动开启,高温净煤气进入煤气冷却器喷淋降温至约73摄氏度,然后送入煤气储柜。
经储柜后的煤气加压机将高洁度转炉煤气( 含尘10 mg/m3以下) 提供给用户使用。
吹炼前期和后期不符合回收要求的煤气,则自动开启放散侧钟型阀,通过放散塔点燃放散,以达到工业炉窑大气污染物的排放标准.
国内常见的回收工艺流程
多数钢铁企业综合考虑目前国内同等型号转炉煤气回收工艺和公司实际情况,煤气净化回收多采用的工艺为: 转炉冶炼过程中的烟尘通过固定烟罩和冷却烟道经二文三脱煤气净化装置"风机"煤气柜及加压站到达用户,实现对煤气净化回收,不合格或不宜回收的煤气经处理后从烟囱达标排放,同时从冷却烟道和烟罩产生的蒸汽通过余热设施回收。
提高转炉煤气回收量的方法
实现转炉煤气回收的各个单位独有自己的煤气回收量增加的办法,总结起来主要有以下几点:控制煤气回收时炉口的空气吸人量,使烟气中的一氧化碳含量尽快达标;在转炉生产时化好初渣对煤气回收的影响也很大,化渣的好坏直接影响到转炉生产的平稳性,也是衡量转炉生产操作水平的主要标志,是转炉煤气量在生产初期平稳上升的重要因素。
转炉生产的稳定对一氧化碳含量的稳定有很大的关系,也是增加煤气回收量的保证。
在转炉钢水脱碳后期,可以适当将提罩时间后延,控制住炉口空气暂不让其进人,就可延长回收时间,从而增加煤气的回收量。
此外,在转炉生产时,风机一般有两个转速:转炉不生产或工序间隙时间是低速运行的,在转炉生产开始到结束期间是高速运行,这是降低转炉工序能耗的重要手段。
在转炉生产后期,可以根据各单位的实际情况摸索风机的第三速度来配合生产,是转炉煤气平稳下降,从而增加转炉煤气的回收量。
从上面的分析来看,这些手段有一个共同的特点,就是为了使转炉生产初期一氧化碳含量尽快达标,因此,在转炉生产后期要延缓一氧化碳含量不达标的时间,延长了回收的时间就增加了煤气回收量。
转炉煤气回收过程中需要注意的事项
转炉煤气回收是通过程序采集一氧化碳含量和氧含量实现自动控制的,绝对不允许手动强行进行回收,造成不合格气体进人煤气柜。
转炉煤气回收虽是通过程序实现自动回收,但每一炉都必须由人工确认,在收到人工确认后才启动回收程序,程序编制时就要求完整。
在人工确认后,旁通阀就进行关闭,关闭过程中阀体阀板密封冲洗水要同时打开,在阀体关闭到位后,冲洗水自动停止。
这样保持密封干净和不产生火花,水冲洗要在现场确认。
冲洗水的水流量要有显示,这就容易检查水冲洗的正常与否。
在烟气成分中的一氧化碳含量和氧含量达标、同时煤气柜条件又允许的情况下,程序设定要首先打开水封逆止阀,然后打开三通阀到回收位置,实现回收;在回收结束时,要先同时打开旁通阀和三通阀,然后关闭水封逆止阀,这是合理的程序。
在煤气回收的整个过程中,前后生产工艺、设备的匹配非常重要,一个环节做不好,将影响整个回收效果。
同时,做好工作联系制度的落实,加压站、煤气柜、除尘净化等岗位要时刻与有关的工序岗位进行联系,预防生产中的突发事情,从
实际的情况来看,转炉煤气回收系统要有比较齐全的应付突发故障的方法和手段,以确保安全回收。
结语
在当今能源缺乏的时代,如何做好现有资源的再利用是我们每一个济钢能源工作者的职责。
转炉煤气回收是一个比较成熟的工艺,但要进一步提升此工艺的安全技术操作水平,提高转炉煤气的回收量和利用率,我们要做的工作还很多,应持续不断地努力。
参考文献:
【1】郭素清. 转炉煤气在酒钢的综合利用[J]. 甘肃冶金. 2009(04)
【2】杜繁志,孙长启,刘宪会,马仁川. 优化加压和输送系统,提高转炉煤气回收量[J]. 冶金动力. 2011(04)
【3】武乐,杨国华. 新型炼钢转炉煤气净化回收系统[J]. 冶金能源. 2009(05)
【4】李建新,姜碧涛,底根顺,翟永臻,赵国英. 转炉煤气回收及综合利用[J]. 中国冶金. 2006(03)。