光亮剂成分检测
910酸铜光亮剂

910硫酸铜光亮剂
一、特点
·可获得完美的镜面光泽。
·光亮性、整平性能提高。
特别是在低电流的情况下光泽更加完美。
·操作温度范围很广(18~35℃),在高温态状下(40℃)也可以进行电镀。
·填平效果好。
·光亮剂消耗少,经济实惠。
·不会受光亮剂分解的影响。
二、溶液成分
四、添加剂的作用
酸铜910 C开缸剂:开缸剂不足时,镀层高、中电流密度区出现凹凸起伏
的条纹。
含量过多时镀层出现起雾现象。
开缸剂含适量
的910B主光剂和湿润剂。
酸铜910 A主光剂:910 A主光剂含量过低时,整个电流密度区的填平度会
下降;含量多时,镀层出现针孔,低电流密度区没有填
平度,与其他位置的镀层有明显分界,但仍光亮。
酸铜910B主光剂:910B主光剂含量不足时,镀层高电流密度区极容易烧焦;
含量过多时,镀层出现起雾现象且填平能力下降,低电
流密度区光亮度变差。
六、添加剂的消耗:。
酸性镀铜光亮剂

酸性镀铜光亮剂酸性镀铜光亮剂的研究可以追溯到20世纪40年代。
最早采用的光亮剂是硫脲和硫脲的衍生物。
当时被称为初级光亮剂(prima — ry brightener)。
并同时加入少量的表面活性剂作为润湿剂(wet — ring agent)。
最初采用的整平剂是有机染料。
有机染料被称为第二级添加剂(secondary addition agents)。
有机多硫化物(organic poly sulfide compound)的研究和利用大大提升了酸性镀铜工艺的性能。
近廿多年来通过对表面活性剂、有机多硫化物、染料等成分的筛选和组合,获得了高光亮和整平的镀层。
酸性光亮镀铜工艺已基本完善。
(一)有机染料的研究状况有机染料是酸性镀铜工艺中最早采用的整平剂和第二级添加剂。
采用的有机染料品种较多。
有吩嗪染料、嚼嗪染料、三苯甲烷染料、二苯甲烷染料、噻嗪染料、酞菁染料、酚红染料等。
Udy — lite 公司、Payton 公司、Lea-Ronal 公司、M&T 公司、oxy 公司、 Bell 实验室等都进行了很多的研究。
下面分别介绍这几类染料的结构、代表物质和使用浓度。
1.酸铜光亮剂常用的染料(1)吩嗪染料(phenazine dyes) 吩嗪染料是指分子结构中含有C6 H4:Nz :C6 H4吩嗪基团的染料。
通式其中 R 1、R 2——H 、甲基、乙基;X ——Cl 一、Br 一、l 一、F 一、SO 42一,NO 3—等;Z ——苯、萘及其衍生物。
代表物如下。
①二乙基藏红偶氮二甲基苯胺,商品名:健那绿②二乙基藏红偶氮二甲基酚,商品名:健那黑③藏红偶氮苯酚,商品名:健那蓝上述有机染料的使用浓度为0.0015~0.05g /L ,最佳用量为0.015g /L 。
这几种染料既可单独使用,也可以混合使用。
共用量之和仍然为0.0015~0.05g /L 。
吩嗪染料的作用在于极大地改善光亮剂的整平能力并且扩大光亮范围。
镀银添加剂

镀银添加剂(光亮剂)镀银镀银层比镀金价格便宜得多,而且具有很高的导电性,光反射性和对有机酸和碱的化学稳定性,故使用面比黄金广得多。
早期主要用于装饰品和餐具上,近来在飞机和电子制品上的应用越来越多。
镀银最早始于l800年,第一个镀银的专利是1838年由英国伯明翰的Elkington 兄弟提出的,所用的镀液为碱性氰化物镀液,与他们发明的碱性氰化物镀黄金体系很类似。
一个多世纪以来,镀银液的基本配方和当年的配方差别不大,仅仅是提高了银配位离子浓度以达到快速镀银的目的而已。
氰系镀液过去的主要缺点是使用的电流密度小,现在这个问题也解决了,高效镀银使电流密度可高达10A/dm,光亮镀银可达1.5~3A/dm,其镀面光滑而无需再打光,也可镀厚。
近年来快速发展起来的电子元器件的高速选择性镀银,如引线框架的选择性镀银,采用喷射镀的方法。
所用的电流密度高达300~3000A/dm,镀液中氰化银钾[KAg(CN)2]的浓度也高达40~7 5g/L,阳极采用白金或镀铂的钛阳极,这样在1s内即可镀上约4~5μm的银层,它已能满足硅芯片和银焊垫之间用铝线来键合(Bonding)。
镀银最早用的光亮剂二硫化碳是Milword和Lyons在1847年发表的专利中提出的,现在还在使用,仅稍加改变而已。
用二硫化碳做光亮剂并不能得到全光亮的银层,且加入镀液后要等一段时间才会发生作用,估计真正的光亮剂是二硫化碳与镀液中的CN一反应生成的取代尿素、硫脲、胍、硫化物、氰胺化物(cyanamide)及其他种硫化物中的某些化合物。
1913年,Frary报道二硫化碳与乙醚、各种酸、氰和亚硫酸的混合物可作为硫氰酸盐镀银的光亮剂,也发现黄原酸钾和砷、锑、锡的硫化物也是有效的光亮剂。
后来发现硫脲也是一种镀银光亮剂。
当其用量达35~40g/L时,其光亮度可超过二硫化碳衍生物。
1939年,Weiner发现从硫代硫酸钠镀液中可以获得光亮的镀银层,证明硫代硫酸钠本身就是一种优良的光亮剂。
不锈钢电解液光亮剂
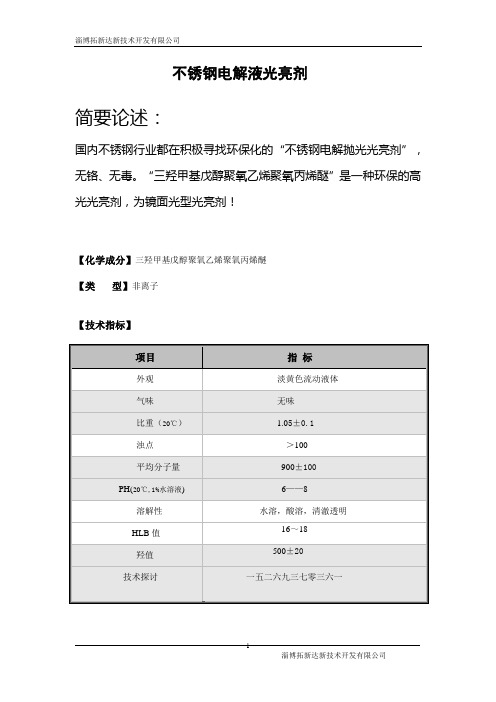
不锈钢电解液光亮剂
简要论述:
国内不锈钢行业都在积极寻找环保化的“不锈钢电解抛光光亮剂”,无铬、无毒。
“三羟甲基戊醇聚氧乙烯聚氧丙烯醚”是一种环保的高光光亮剂,为镜面光型光亮剂!
【化学成分】三羟甲基戊醇聚氧乙烯聚氧丙烯醚
【类型】非离子
【技术指标】
【性能与应用】
1、金属化学抛光、电化学抛光的新型高光光亮添加剂,可取代铬酸酐,与铬系电解抛光液相比,更环保,使用寿命更长;与传统有机光亮剂、缓蚀剂相比,光亮度更高,槽液性能更长效持久!在不锈钢领域的电化学抛光液中应用较多,西方国家主要使用该活性剂用于“不锈钢领域的电化学抛光液中”,可以取得环保、长效、稳定、高光的效果,在中国越来越多的厂家逐渐重视了该剂的应用;
2、属于高分子表面活性剂,具有独特的性能,起泡力极低,分散力好,具有较好的低温流动性,易于配制抗低温的表面活性产品;
3、用于化纤油剂中作高档平滑剂使用;
4、金属加工液中,作润滑剂使用,在低泡或无泡性的场合应用较多,比如高速磨削液。
5、在其它行业,作乳化分散剂使用
6、在淬火剂中,作成膜剂使用,调节传热速度,以取得合适的硬度及强度。
荧光增白剂检测标准

荧光增白剂检测标准荧光增白剂是一种广泛应用于纺织、造纸、洗涤剂等行业的化学品,它能够吸收紫外光并发射出蓝光,从而使物体表面产生荧光效应,达到增加亮度、改善色泽的效果。
然而,荧光增白剂的使用也带来了一些质量和环境问题,因此对其进行检测和监管显得尤为重要。
荧光增白剂的检测标准主要包括对其成分、含量、性能等方面的要求。
首先,对荧光增白剂的成分进行分析是十分必要的。
不同的荧光增白剂可能含有不同的化学成分,有些成分可能对人体健康和环境造成危害,因此需要对其成分进行准确的鉴定和分析。
其次,对荧光增白剂的含量进行检测也是至关重要的。
合理的荧光增白剂含量可以达到预期的增白效果,但过高或过低的含量都会影响产品的质量和环境的安全。
此外,荧光增白剂的性能也需要进行全面的评估和检测,包括其增白效果、稳定性等方面的指标。
在进行荧光增白剂的检测时,需要严格按照相关的标准和方法进行操作,以确保检测结果的准确性和可靠性。
常用的荧光增白剂检测方法包括高效液相色谱法、气相色谱法、紫外-可见分光光度法等。
这些方法在对荧光增白剂的成分和含量进行检测时具有一定的优势和适用性,但在实际操作中也需要严格控制各项条件,避免外界因素对检测结果的影响。
除了对荧光增白剂本身进行检测外,还需要对其在实际产品中的使用情况进行监测和评估。
例如,在纺织品中使用的荧光增白剂需要经过洗涤耐久性测试,以确保其在多次清洗后仍能保持良好的增白效果。
同时,还需要对荧光增白剂残留情况进行监测,避免其对环境和人体健康造成潜在的危害。
总的来说,荧光增白剂的检测标准涉及到成分分析、含量检测、性能评估等多个方面,需要采用一系列严格的方法和标准进行操作。
只有通过科学、准确的检测手段,才能确保荧光增白剂的安全使用和环境友好性,为相关行业的健康发展提供有力的支持。
光亮剂的基本介绍

宏其纺织助剂:光亮剂的基本介绍光亮剂也成为亮光剂或表面处理剂,也是一道处理产品的工序,很多产品在加工的工艺完成以后表面会有油渍或者是在加工中有稍微的损伤导致产品外表面很难看,也有些产品在加工后光洁度达不到市场要求,这时候就要用亮光剂来进行修复。
按照市场的需求光亮剂可以分为:塑料光亮剂、轮胎光亮剂、镀镍光亮剂、不锈钢光亮剂、电镀光亮剂、酸铜光亮剂、镀锌光亮剂、皮革光亮剂、金属光亮剂等等。
光亮剂具有良好的内外润滑性、表面光亮性、互熔性、防粘性;对颜料和填料具有良好的分散性等一系列的性能;同时光亮剂具有加工质量高、速度快、效果明显,被加工后的零件表面光亮照人,可解决人工抛光不能解决的问题。
光亮剂在塑料中又可以起到润滑剂、增量剂、脱模剂等,也可以用作玻璃纸的抗静电剂等。
随着科技的发展,光亮剂也在越来越多的行业中应用开来。
除了工业、食品、装饰等行业,光亮剂也用在了农业生产中。
比如研制肥料光亮剂,用惰性物质包裹在肥料表面,不仅增加了肥料的亮度和硬度,还起到了缓释养分,提高肥料利用率的功效。
而适用于有机肥、有机-无机复合肥、生物有机肥、复混肥及各种复合肥的着色和表面光亮处理。
只需在肥料造粒后,在滚筒冷却过程中加入即可,方便快捷,同时也大大提高了肥料生产的便捷性。
光亮剂产品剖析一般采用红外光谱(FTIR)、核磁共振(1H NMR)、质谱(MS)、X衍射分析(XRD)、ICP-MS、X荧光光谱分析、离子色谱分析等手段。
通过这些测试手段可以很好的解析光亮剂的配方,对光亮剂中的成分作用有详细的了解,更方便各个企业进行研发,把握市场动态。
哲博检测依靠浙大学科优势和分析人才,拥有多种分析测试手段,积累了深厚的化工产品剖析经验,通过专业、可靠、综合性的分离和检测手段对未知物进行定性鉴定与定量分析,为科研及生产中调整配方、新产品研发、改进生产工艺提供科学依据,同时可以根据客户需求,提供后期跟踪技术性指导。
振光不锈钢光亮剂配方
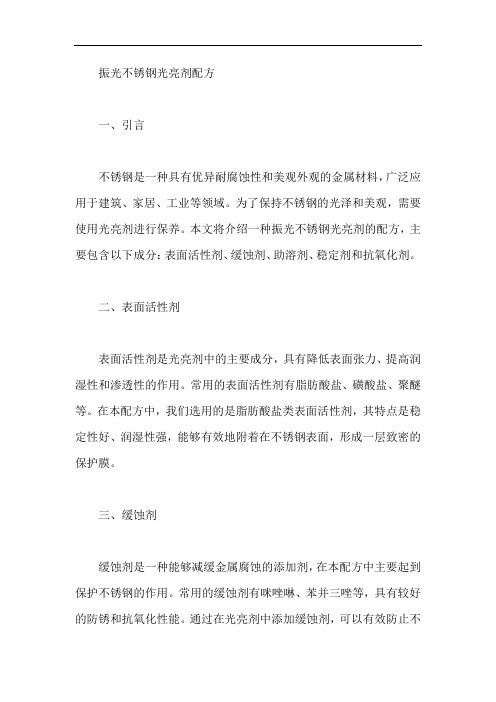
振光不锈钢光亮剂配方一、引言不锈钢是一种具有优异耐腐蚀性和美观外观的金属材料,广泛应用于建筑、家居、工业等领域。
为了保持不锈钢的光泽和美观,需要使用光亮剂进行保养。
本文将介绍一种振光不锈钢光亮剂的配方,主要包含以下成分:表面活性剂、缓蚀剂、助溶剂、稳定剂和抗氧化剂。
二、表面活性剂表面活性剂是光亮剂中的主要成分,具有降低表面张力、提高润湿性和渗透性的作用。
常用的表面活性剂有脂肪酸盐、磺酸盐、聚醚等。
在本配方中,我们选用的是脂肪酸盐类表面活性剂,其特点是稳定性好、润湿性强,能够有效地附着在不锈钢表面,形成一层致密的保护膜。
三、缓蚀剂缓蚀剂是一种能够减缓金属腐蚀的添加剂,在本配方中主要起到保护不锈钢的作用。
常用的缓蚀剂有咪唑啉、苯并三唑等,具有较好的防锈和抗氧化性能。
通过在光亮剂中添加缓蚀剂,可以有效防止不锈钢表面受到氧化和腐蚀,从而保持其光泽和美观。
四、助溶剂助溶剂是一种能够提高光亮剂的渗透性和分布性的物质,使光亮剂更好地附着在不锈钢表面。
常用的助溶剂有醇类、醚类等有机溶剂。
在本配方中,我们选用的是醇类助溶剂,其特点是渗透性好、挥发性适中,能够使光亮剂更好地分布在不锈钢表面。
五、稳定剂稳定剂的作用是防止光亮剂在储存和使用过程中发生氧化和分解,提高光亮剂的稳定性和耐久性。
常用的稳定剂有抗氧化剂、金属离子螯合剂等。
在本配方中,我们选用的是抗氧化剂作为稳定剂,能够有效延缓光亮剂的氧化过程,保证其稳定性和耐久性。
六、抗氧化剂抗氧化剂的作用是防止光亮剂中的有效成分在高温、氧气等条件下发生氧化反应,从而保证光亮剂的稳定性和长效性。
常用的抗氧化剂有多酚类、胺类等化合物。
在本配方中,我们选用的是多酚类抗氧化剂,具有较好的热稳定性和抗氧化性能,能够有效延缓光亮剂的氧化过程。
七、结论本文介绍了一种振光不锈钢光亮剂的配方,主要包含表面活性剂、缓蚀剂、助溶剂、稳定剂和抗氧化剂等成分。
这些成分相互协同作用,能够有效保持不锈钢的光泽和美观,防止其氧化和腐蚀。
镀锡添加剂成分分析,配方工艺及技术开发

镀锡添加剂成分分析,配方工艺及技术开发光亮硫酸镀锡添加剂由光亮剂、分散剂、稳定剂等组成。
光亮剂由有机酸、芳香酮、醛等复配而成;分散剂主要是壬基酚聚氧乙烯醚,对光亮剂起分散和增溶作用;稳定剂由磺酸、络合剂等组成,能稳定Sn2+,降低其氧化速度。
禾川化学是一家专业从事精细化学品分析、研发的公司,具有丰富的分析研发经验,经过多年的技术积累,可以运用尖端的科学仪器、完善的标准图谱库、强大原材料库,彻底解决众多化工企业生产研发过程中遇到的难题,利用其八大服务优势,最终实现企业产品性能改进及新产品研发。
样品分析检测流程:样品确认—物理表征前处理—大型仪器分析—工程师解谱—分析结果验证—后续技术服务。
有任何配方技术难题,可即刻联系禾川化学技术团队,我们将为企业提供一站式配方技术解决方案!1 光亮剂目前,国内外使用的酸性镀锡光亮剂大都是由主光亮剂(甲醛或苯甲醛)、载体光亮剂(非离子型表面活性剂如OP系列) 和辅助光亮剂(苄叉丙酮) 复配而成。
国产光亮剂主要是AB 型,A 组分主要成分是润湿剂和甲醛(甲醛最佳量为5~ 10 ml/ L),B 组分主要成分是苄叉丙酮。
由于采用载体光亮剂的型号、质量不一样,光亮剂的配方和附加剂(萘酚、烟酸、对(间、邻) 苯二酚、酚磺酸、二氨基二苯甲烷)不同,其性能各有差异。
1.1主光亮剂主光亮剂一般具有以下结构:只要方框内的结构保持不变,方框外的取代基Rl、R2可以改变,复配生成的有机化合物都有光亮效果。
醛类的吸附能力比酮类和酯类强,这与醛基中羰基的化学活性特别高是一致的,在羰基连有共扼双键存在时,共扼双键上的电子云可移到羰基上,从而提高羰基的化学活性,提高了羰基上的电子云密度,从而提高了吸附Sn2+能力,但是吸附性过强,脱附电位很负,超过H+的析出电位的添加剂,在使金属锡离子沉积的同时,也伴随着大量氢气的产生,结果电流效率下降,镀层的光亮度变差。
所以只有吸附性较强、脱附电位在析出电位之前的添加剂才有增光的效果。
- 1、下载文档前请自行甄别文档内容的完整性,平台不提供额外的编辑、内容补充、找答案等附加服务。
- 2、"仅部分预览"的文档,不可在线预览部分如存在完整性等问题,可反馈申请退款(可完整预览的文档不适用该条件!)。
- 3、如文档侵犯您的权益,请联系客服反馈,我们会尽快为您处理(人工客服工作时间:9:00-18:30)。
光亮剂成分检测
微谱分析指通过微观谱图(气相色谱、液相色谱、热谱、能谱、核磁共振谱等)对产品所含有的成分进行定性和定量的一种配方分析方法。
配方分析在日本,欧美应用比较广泛,而在国内,目前处于起步阶段。
该技术甚至是很多国家的成长途径。
二战之后的日本,就走的引进技术,分析还原,消化吸收,然后技术创新的道路。
韩国等国家也是如此,从欧美获取技术,学习,实践,赶超。
化学镀镍在化工机械、宇宙航空等领域中应用广泛。
随着生产中对功能及装饰性镀层的要求越来越高。
如何研制出更新的镀镍光亮剂已引起人们的极大兴趣。
在目前研制出的4代镀镍光亮剂中,第2代光亮剂镀层质量差,色泽偏淡米黄色。
第3代镀镍光亮剂以1,4-丁炔二醇与环氧类化合物的缩合物为代表,镀层光亮平整,应用广泛,但出光速度慢,分解产物多。
20世纪80年代末研制出的第4代光亮剂,其中初级光亮剂一般为柔软剂,如武汉风帆电镀公司的柔软剂中含有C12H11NO4S2和C2H3SO3Na的混合物,次级光亮剂以吡啶衍生物和丙炔醇衍生物及炔胺类化合物为典型代表,镀液稳定,分解产物少,但应用缺乏普通性。
上述光亮剂绝大多数应用于电镀镍工艺中,化学镀镍上使用的光亮剂报道较少。
本文研制的化学镀镍光亮剂在实际生产中的运用表明,对镀层有明显的增光和整平作用。
试验
工艺流程
试样→镀前预处理→水洗→化学镀→水洗→镀后处理→检验→成品。
镀液组成及工艺条件
NiSO4·6H2O 25~30g/L
络合剂40~50ml/L
稳定剂0.5~1.0ml/L
NaH2PO2·H2O 28~35g/L
光亮剂1~6ml/L
装载量 1.2~4.8dm2/L
pH值 4.4~4.8
温度85~90℃
络合添加剂为有机酸的混合物,稳定剂为重金属盐,光亮剂为2种重金属盐和有机酸盐的混合物。
镀层性能测试
1)显微硬度厚度的测定采用HX-1型显微硬度计测试。
2)镀层耐磨性测定耐磨试验在M-2000型磨损试验机上进行,上块材料为GCr15,硬度59HRC,下环是被测试样。
负荷500N,转速400r/min,20号机油润滑,持续磨损1h。
试样磨损前后质量用FA1004电子天平称量。
3)耐腐蚀性测定在5%NaCl溶液、10%H2SO4溶液和10%HCl溶液中进行全浸试验,浸入时间为144h。
4)镀层表面形貌及成分测定分析仪器:日本岛津EPMA-1600电子探针X射线波谱仪。
分析参数为加速电压15kV,样品电流50mA,X射线分光晶体LiF、PET、L55A。
5)镀层组织及结构测试采用日本理学3015型X射线衍射仪分析和测试。
成分及结构
镀层成分
高磷含量化学镀镍工艺道了高磷含量化学镀镍工艺的研究,最佳工艺条件下
获得了磷质量分数为23%的高磷合金镀层。
本工艺在5种试验条件下镀层中的磷质量分数分布见图1。
光亮剂使用后获得的高磷合金镀层,磷含量随着光亮剂用量的增加而提高。
在镀液组成和操作温度相同时,通过对比试验表明,不含光亮剂时镀层中的磷质量分数为8.237%。
光亮剂用量2ml/L时,磷质量分数为15.812%。
当光亮剂用量为6ml/L时,镀层中磷质量分数提高到39.026%。
而且镀层中没有光亮剂的成分,从而确定光亮剂没有参加化学反应。
但提高了镀层中磷的含量,说明光亮剂对镀液中磷的沉积有积极的促进作用。
镀层镀态下的相结构
根据电子显微镜观察,镍磷合金镀层的结构随着磷含量的增加,从晶态向非晶态变化,大致情况是:含磷质量分数3%左右时为微细晶态,含磷质量分数5%左右时为微细晶态+非晶态,含磷质量分数7%以上为非晶态。
化学镀镍原理及应用指出,只有镀层成分在N-iP相图共晶点11%附近时,才能形成典型的非晶态组织。
通过X射线衍射分析(见图2)可以看出,低磷、高磷镀层两种测试结果在2H=45b处均出现了馒头峰,表明在两种情况下镀层都是非晶态结构。
但含8.5%P的低磷合金镀层的衍射峰比较尖锐,而含15.8%P的高磷合金镀层的衍射峰似馒头包状,且衍射峰向两侧漫散开来,是非晶态结构的显著特征。
镀层性能测试
光亮剂应用效果
工艺中使用光亮剂后,在反应过程中镀层表面的出光速度较快,一般只需
15~20min镀层便开始光亮,且镀层平整,结晶细致,达到了全光亮的效果。
镀液装载量对镀层的光亮度也有影响。
一般来说,随着镀液装载量的增加,镀层光亮度降低。
试验表明,为了获得光亮的镀镍层,镀液装载量以低于2.4dm2/L为佳。
同时,基体表面的光洁度愈高,出光速度就越快,获得的镀层表面光泽度也越好。
光亮剂对镀层显微硬度及磨损率的影响
镀液中光亮剂用量对镀层镀态下的硬度和磨损率的影响见图4,随着光亮剂用量的增加,镀层镀态下的显微硬度逐渐降低。
与化学镀镍层的物理和化学性能与磷含量的关系所述的镀层镀态下的硬度随磷含量的增加而降低是基本一致的。
光亮剂用量控制在3ml/L以下时,镀态硬度在440~500HV间。
镀层镀态下的磨损率随着光亮剂用量的增加而提高。
镀液中光亮剂用量为1~2ml/L时,镀层的磨损率略高于不加光亮剂时镀层的磨损率0.00384mg/cm2#h。
使用光亮剂后镀层硬度的降低和磨损率的提高,主要是由于非晶态高磷合金镀层中固溶态的磷原子增加所致。
光亮剂对镀层腐蚀率的影响
镀液中光亮剂用量对腐蚀率的影响见图5。
腐蚀结果表明,在5%NaCl溶液中,光亮剂对腐蚀率影响不大,且腐蚀速率较低。
因为高磷合金镀层随着磷含量的增加,使镀层的自钝化能力增加而使镀层表面富集一层磷,在腐蚀环境下形成完整致密的磷化钝化膜,对基体起到了很好的保护作用。
同时,由于非晶态结构无偏析、位错等缺陷,不能形成局部腐蚀电池,故耐腐蚀性好。
但10%HCl溶液对镀层腐蚀率影响较大,腐蚀率随着光亮剂用量的增加而增加。
一般情况下,镀层的耐腐蚀性随着磷含量增加而提高,但当含磷质量分数超过13%时,耐腐蚀性便有所降低。
光亮剂加入3ml/L后,镀层中磷质量分数已经超过了20%,从而大大降低了镀层的耐腐蚀性。
从耐腐蚀性角度考虑,为获得耐腐蚀性能好的镍磷合金镀层,光亮剂用量应控制在1~2ml/L为宜。
结论
(1)光亮剂使用后,获得了非晶态高磷合金镀层。
镀层中固溶磷原子的增加,起到了明显的增光效果,提高了装饰性镀层的表面质量。
(2)在反应过程中,镀层表面出光速度快,一般只需15~20min镀层便开始光亮。
且光亮剂用量少,持续出光时间长,镀液稳定可靠。
(3)光亮剂没有参加化学反应,对磷的沉积有积极的促进作用。
提高了镀层中的磷含量。
当磷含量过高时,会降低耐腐蚀性。
本工艺中光亮剂用量应控制在
1~2ml/L为宜。