车轮踏面擦伤深度的简易测算方法
车辆轮对尺寸检测作业指导书
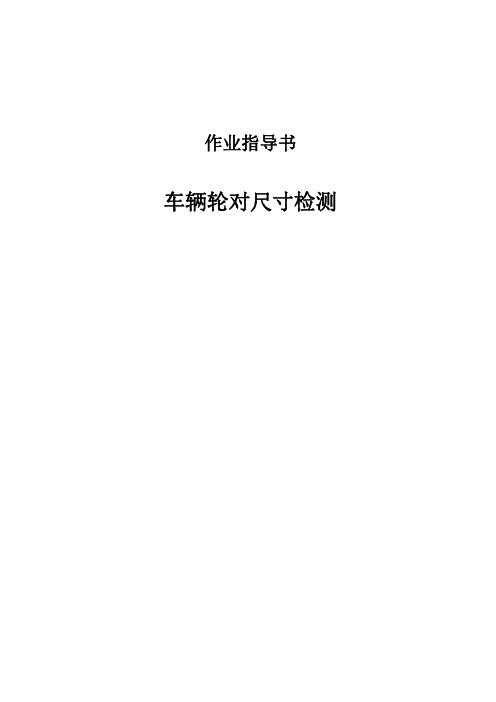
----安全风险提示: 测量车轮踏面擦伤,踏面定位测头不置于踏面擦伤最 深处,易造成测量数据不准确。防止措施:测量车轮踏面擦伤,踏面定位测头 须置于踏面擦伤最深处,再进行测量。
8 / 15
3.5 踏面剥离长度检测 沿车轮圆周方向,用刻度尺在踏面上剥离处测量踏面剥离长度。如图 9。
图9
----安全风险提示: 测量车轮踏面剥离,不除去两端宽度小于 10mm 的部分, 将剥离前期未脱落部分计算在内,易造成测量数据不准确。防止措施:测量车 轮踏面剥离,须除去两端宽度小于 10mm 的部分,剥离前期未脱落部分不计算在 内,再进行测量。
2 / 15
二、检测作业示意流程图
踏面圆周磨耗深度
测量准备 确认信号 车轮尺寸检测 整理工具 台账记录
轮缘厚度 轮辋厚度 轮缘垂直磨耗 踏面剥离长度 踏面擦伤深度
轮辋宽度 车轮外侧碾宽 踏面外侧缺损
轮对内距 车轮直径
3 / 15
三、作业程序、标准及示范
1.准备工作 根据测量需要准备相应测量工具:LLJ-4B 型车轮第四种检查器、轮对内距 尺、轮径尺、钢直尺。 1.1 检查车轮第四种检查器检定标记(或鉴定合格证)不过期,外观技术状 态良好,要求配件齐全、测量尺框灵活、作用良好、刻度线须清晰、尺身无弯 曲变形。如图 1
≤2
车轮踏 面剥离 长度
滚动 轴承
滑动 轴承
1处 2 处(每 1 处均) 1处
2处
≤50 ≤40 ≤70
≤60
1.沿圆周方向测量。 2.测量时规定如下: (1)两端宽度不足 10mm 的,不计算在内。 (2)长条状剥离其最宽处不足 20mm 的, 不计算在内。 (3)2 块剥离边缘相距小于 75mm 时,每处 长不得超过 35mm;多处小于 35mm 的剥离, 其连续剥离总长度不大于 350mm。 (4)剥离前期未脱落部分,不计算在内。
在线式车轮踏面磨耗及擦伤检测方法研究

摘 要: 介绍了利用激光器和C D 摄像机对车轮踏面磨耗及擦伤 C
进行在线检测的方法 , 着重论述 了测试数 据的处理及光平面方程的
建立 , 进行 了实例验证 。 最后给 出了数 据分析 结果 。 并
2 检测系统构成及检测原理
检 测 系 统 采 用 激 光 器 和 直 线
光 学 透 镜 产 生 线 性 激 光 束 , 射 在 照
在 轮 对 踏 面 几 何 尺 寸 检 测 中 , 进 行 光平 面 对准 分 析 及 内外 侧光 平 使 图像 处 理 的 目的是 要 得 到清 晰 准确 面 符 合 程 序 分 析 , 得 最 终 确 定 的
线 运 行 的 车 轮 踏 面 , 车轮 通 过 检 当 测 区时 , 轮 踏面 被激 光束 照射 , 车
关键 词 ;车轮 t踏面 ,磨耗 ,擦伤 ;图像处理 t在线测量
形成 激 光轮 廓 线 , CCD摄 像 机 动
1 检测参数定义
耗 为 B、 轮 直 径 为 C、 缘 厚 度 为 态 拍 摄 激 光 束 的 精 确 位 置 , 现 物 车 轮 实 D、 缘 高 度 为 、 辋 宽 度 为 , 轮 轮 其 体 几 何 尺 寸 的 精 确 测 量 。 检 测 原
外侧 图 像 见 图 3( 侧 图像 略 ) 外 。
、
二值 数 学 形 态 学 算 法 等 来 提 取 边
缘 。 到 只 有单 像 素 宽 的 精 确 轮 廓 图 4 图像 经边缘提取后的精确轮廓曲线 得
曲线 。 如 图 4 示 。 所
4 检测结果分析
CCD摄 像 机 采 集 到 的 原 始 图 像 经过 图 像处 理后 产生 细 化后 的 图
的 检 测 参 数 的 定 义 如 图 i 示 。图 精 度 为 ±03mm I 缘 厚 度测 量 范 激 光器和 C D摄像 机相互 之 间需 所 . 轮 C
车轮踏面擦伤原因分析及措施

车轮踏面擦伤原因分析及措施车轮踏面擦伤是车辆在运行之中发生的主要故障之一,危害性极大.严重危及着列车的运行安全,影响铁路运输的提高。
因此,分析轮对踏面擦伤原因及制定预防措施已成为现场亟待解决的问题。
1.车轮擦伤的原因分析1.1司机操纵不当在长大下坡道时,司机将小闸推向缓解位,使车辆制动机车缓解.这种用车辆制动拖住机车的方法会增加车辆制动力;另一方面,由于长大货物列车的增加,列车在进入列检所停车时,采用了二次停车,此时,由于部分车辆没有缓解,车轮产生滑行,造成擦伤。
1.2温度条件变化原因严寒季节钢轨面上有冰雪、霜冻、油污,使轮对与钢轨的粘着系数降低,制动力大于粘着力,造成车轮擦伤。
1.3车站调车作业时使用单侧铁鞋车辆从驼峰上溜放下来受到单侧铁鞋的阻力后,有铁鞋一侧的轮对被垫起,而另一侧的轮对由于停止转动与钢轨产生剧烈摩擦,造成轮对踏面擦伤。
1.4车辆制动机故障、部分配件作用不良冬季气温下降,三通阀油脂凝固或风道凝结水进入风管内,造成三通阀滑动部分因摩擦阻力增大,在列车紧急制动时作用缓慢不良或不起作用,造成列车制动快慢不一致,制动压力高低不均而造成车辆车轮擦伤。
1.5空重车装置调整不正确运用部门根据车辆每轴平均载重确定“空车位”和“重车位”,使车辆产生不同的制动力。
如果空车运行,而车辆的空重车手炳至于重车位时,将使制动力大于粘着力,造成车轮滑行,擦伤轮对。
1.6闸瓦自动间隙调整器故障或调整不当现场车辆在做定期检修时,还须对闸调器做减小间隙、增大间隙实验。
该项实验常常被简化,造成制动缸活塞行程过长或过短,如果行程过短时,致使制动力增大,出现闸瓦紧抱车轮,甚至抱死车轮,造成车轮严重擦伤。
1.7制动波速不一致由于目前我国客、货车的种类比较多,而且各种阀反映速度不相同。
车辆在运行中,将120阀和103型分配阀与GK三通阀混编在一起,或将104型分配阀GL型三通阀混编在一起,在运用中使行制动与缓解时,由于制动波速不同,致使车轮擦伤。
LLJ-4A车轮第四种检查器使用方法

LLJ-4A 车轮第四种检查器一、概述LLJ-4A 型铁道车辆车轮第四种检查器,是测量车辆轮缘、踏面相关尺寸及缺陷的一种专用检测量具。
该种检查器以车轮踏面滚动圆(即距车轮内侧面70mm 处的基线)为测量基准,符合铁道部的有关规定及国际上通用的测量方法。
即轮缘厚度的测点与车轮踏面滚动圆的距离始终保持恒定,不会因踏面的磨耗而改变。
二、测量功能该检查器可测量:1) 踏面圆周磨耗;2) 轮缘厚度;3) 轮缘垂直磨耗;4) 轮缘高度;5) 轮辋宽度;6) 轮辋厚度;7) 踏面擦伤深度和长度;8) 踏面剥离深度和长度;9) 车钩闭锁位钩舌与钩腕内侧距离三、结构形式(见图一)L主尺N踏面磨耗测尺尺框,踏面磨耗测尺4.轮缘高度测量定位面5.尺框紧固螺钉6.轮辅宽度测尺「止钉8.轮辎厚度测尺9.轮缘厚度测尺10•轮缘厚度尺尺框1踏面磨耗尺紧固螺钉12.主尺背面滚动圆定位线丨工定位角铁丨4■踏面磨耗尺框背面滚动圆刻线1 5•轮缘厚度测头16■垂直磨耗测头17•定位挡块1 &踏面磨耗测头图一检查器由以下部分构成:(1)主尺。
①为直角形,其垂直尺身(又称轮辋厚度测尺⑧)正面刻有长度双刻度线,水平尺身的背面刻有车轮滚动圆定位刻线⑫,踏面圆周磨耗测尺③和轮缘厚度测尺⑨,通过踏面圆周磨耗测尺框②和轮缘厚度测尺框⑩组合在一起,从而形成整体的联动结构形式。
(2) 踏面磨耗测尺尺框:上有-10〜19mm刻线,分度值为1 mm。
(3) 踏面磨耗测尺:上有0〜1 mm刻线,分度值为0.1 mm。
( 4)轮缘高度测量定位面。
( 5)尺框坚固螺钉:可将尺框在水平方向定位。
(6)轮辋宽度测量:上有123〜145 mm 刻线,分度值为1 mm。
( 7 )止钉。
(8)轮辋厚度测尺:上有0〜75 mm刻线,分度值为1 mm。
为保证车轮检查器测量操作的稳定和数据准确可靠,在轮辋厚度测尺⑧的背面装有定位角铁。
( 9)轮缘厚度测尺:上有0〜1 mm 刻线,分度值为0.1 mm。
lm型。车轮踏面检测标准

lm型。
车轮踏面检测标准
lm型车轮踏面检测标准
一、踏面形状
1.踏面应呈圆柱形,表面光滑,无明显的凹陷、凸起或变形。
2.踏面直径应符合规定,偏差应在允许范围内。
3.踏面的圆度、圆柱度等形位公差应符合相关标准要求。
二、踏面磨损
1.踏面磨损程度应不超过规定值,否则应及时更换车轮。
2.踏面磨损情况应均匀分布,无局部严重磨损现象。
3.踏面磨损深度和磨损面积应定期检测,并记录检测结果。
三、踏面裂纹
1.踏面表面应无裂纹、开裂等现象。
2.若发现踏面裂纹,应及时采取措施进行修复或更换车轮。
四、踏面硬度
1.踏面硬度应符合相关标准要求,以保证车轮的使用寿命和安全性。
2.若发现踏面硬度异常,应及时进行硬度检测和分析,并采取相应措施。
五、踏面粗糙度
1.踏面粗糙度应符合相关标准要求,以保证车轮的摩擦性能和制动性能。
2.若发现踏面粗糙度异常,应及时进行粗糙度检测和分析,并采取相应措施。
铁路货车车轮动、静态检测技术
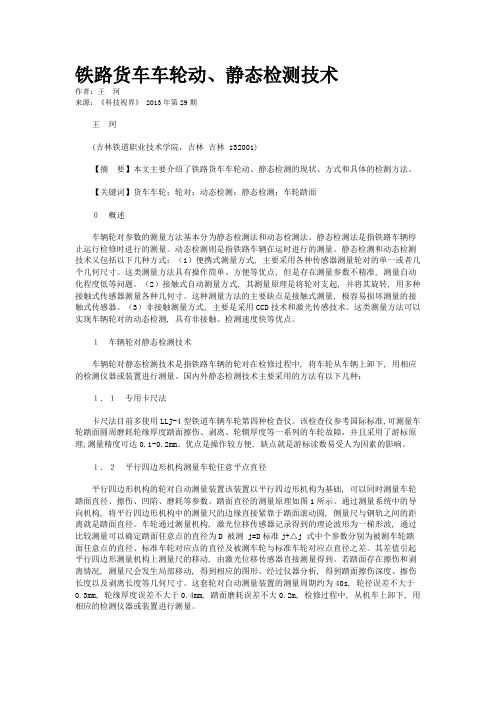
铁路货车车轮动、静态检测技术作者:王珂来源:《科技视界》 2013年第29期王珂(吉林铁道职业技术学院,吉林吉林 132001)【摘要】本文主要介绍了铁路货车车轮动、静态检测的现状、方式和具体的检测方法。
【关键词】货车车轮;轮对;动态检测;静态检测;车轮踏面0概述车辆轮对参数的测量方法基本分为静态检测法和动态检测法。
静态检测法是指铁路车辆停止运行检修时进行的测量。
动态检测则是指铁路车辆在运时进行的测量。
静态检测和动态检测技术又包括以下几种方式:(1)便携式测量方式, 主要采用各种传感器测量轮对的单一或者几个几何尺寸。
这类测量方法具有操作简单、方便等优点, 但是存在测量参数不精准, 测量自动化程度低等问题。
(2)接触式自动测量方式, 其测量原理是将轮对支起, 并将其旋转, 用多种接触式传感器测量各种几何寸。
这种测量方法的主要缺点是接触式测量, 极容易损坏测量的接触式传感器。
(3)非接触测量方式, 主要是采用CCD技术和激光传感技术。
这类测量方法可以实现车辆轮对的动态检测, 具有非接触、检测速度快等优点。
1车辆轮对静态检测技术车辆轮对静态检测技术是指铁路车辆的轮对在检修过程中, 将车轮从车辆上卸下, 用相应的检测仪器或装置进行测量。
国内外静态检测技术主要采用的方法有以下几种:1.1专用卡尺法卡尺法目前多使用LLJ-4型铁道车辆车轮第四种检查仪。
该检查仪参考国际标准,可测量车轮踏面圆周磨耗轮缘厚度踏面擦伤、剥离、轮辋厚度等一系列的车轮故障,并且采用了游标原理,测量精度可达0.1-0.2mm。
优点是操作较方便, 缺点就是游标读数易受人为因素的影响。
1.2平行四边形机构测量车轮任意平点直径平行四边形机构的轮对自动测量装置该装置以平行四边形机构为基础, 可以同时测量车轮踏面直径、擦伤、凹陷、磨耗等参数。
踏面直径的测量原理如图1所示。
通过测量系统中的导向机构, 将平行四边形机构中的测量尺的边缘直接紧靠于踏面滚动圆, 侧量尺与钢轨之间的距离就是踏面直径。
车轮踏面缺陷的判定方法及其产生原因的探讨
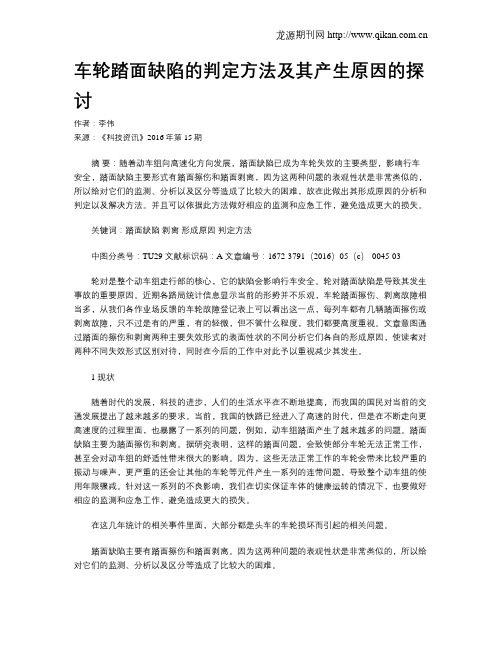
车轮踏面缺陷的判定方法及其产生原因的探讨作者:李伟来源:《科技资讯》2016年第15期摘要:随着动车组向高速化方向发展,踏面缺陷已成为车轮失效的主要类型,影响行车安全,踏面缺陷主要形式有踏面擦伤和踏面剥离,因为这两种问题的表观性状是非常类似的,所以给对它们的监测、分析以及区分等造成了比较大的困难,故在此做出其形成原因的分析和判定以及解决方法。
并且可以依据此方法做好相应的监测和应急工作,避免造成更大的损失。
关键词:踏面缺陷剥离形成原因判定方法中图分类号:TU29 文献标识码:A 文章编号:1672-3791(2016)05(c)-0045-03轮对是整个动车组走行部的核心,它的缺陷会影响行车安全。
轮对踏面缺陷是导致其发生事故的重要原因。
近期各路局统计信息显示当前的形势并不乐观,车轮踏面擦伤、剥离故障相当多,从我们各作业场反馈的车轮故障登记表上可以看出这一点,每列车都有几辆踏面擦伤或剥离故障,只不过是有的严重,有的轻微,但不管什么程度,我们都要高度重视。
文章意图通过踏面的擦伤和剥离两种主要失效形式的表面性状的不同分析它们各自的形成原因,使读者对两种不同失效形式区别对待,同时在今后的工作中对此予以重视减少其发生。
1 现状随着时代的发展,科技的进步,人们的生活水平在不断地提高,而我国的国民对当前的交通发展提出了越来越多的要求。
当前,我国的铁路已经进入了高速的时代,但是在不断走向更高速度的过程里面,也暴露了一系列的问题,例如,动车组踏面产生了越来越多的问题。
踏面缺陷主要为踏面擦伤和剥离。
据研究表明,这样的踏面问题,会致使部分车轮无法正常工作,甚至会对动车组的舒适性带来很大的影响。
因为,这些无法正常工作的车轮会带来比较严重的振动与噪声,更严重的还会让其他的车轮等元件产生一系列的连带问题,导致整个动车组的使用年限骤减。
针对这一系列的不良影响,我们在切实保证车体的健康运转的情况下,也要做好相应的监测和应急工作,避免造成更大的损失。
列车车轮踏面擦伤动态检测系统研究

0 引言
轮对是机车车辆走行部 主要部件, 其实际损伤 主要有踏面擦伤和踏面剥落 , 危害极大 , 不仅对车辆 和钢轨造成巨大的额外冲击荷载, 还是造成轮轴、 钢
轨、 轨枕 断裂 的主要 原 因之一 , 重制 约着列 车 的提 严
1 国内外常用车轮擦伤 动态在线检 测 系统
自上世纪 7 年代后期起 , O 世界各国研究人员都 已相继开展了车轮轮对踏面擦伤、 剥离 等损伤的动 态在线 检测工 作 的研 究 。其 中 , 步较 早 的 国家有 起
21 0 1年第1期 0
中图分类号 :. 7 r 24 I P 文献标识码 : A 文章编号 :O9— 5 2 2 1 )0- 0 4一 4 lO 2 5 (0 1 1 09 o
列 车 车轮 踏 面擦 伤 动态 检 测 系统 研 究
顾 明亮,王泽勇 ,周 伟 ,周小红
( 西南交通大学 光电工 程研究所 ,成都 6 0 3 ) 10 1
德 国、 日本 、 典 、 罗斯 、 国等 。 目前 国内外 常用 瑞 俄 美
速和轨道设施 的安全 , 同时使乘坐的舒适性变差 , 且 产生的巨大噪声严重侵扰了沿线区域居民生活 。 1 J
目前国 内对 车轮 踏 面擦 伤 的检 测 主要通过 列检
员的眼看、 锤敲、 耳听, 或是利用手持式车轮踏面测 量仪进行检查 , 这受人为因素及现场环境影响大, 劳 动强度大 , 且易造成漏检。而轮踏面擦伤动态在线 检测系统不仅可以实现对轮对 的检测 , 而且 自动化
- 1、下载文档前请自行甄别文档内容的完整性,平台不提供额外的编辑、内容补充、找答案等附加服务。
- 2、"仅部分预览"的文档,不可在线预览部分如存在完整性等问题,可反馈申请退款(可完整预览的文档不适用该条件!)。
- 3、如文档侵犯您的权益,请联系客服反馈,我们会尽快为您处理(人工客服工作时间:9:00-18:30)。
注 : 量 时 应 多次 测 量 取 其 平 均 值 。 测
2
使 用 踏 面 样 板 +塞 尺 测 量
首 先 , 车轮 踏 而 样 板 按 照 一 般 检 测 时 的 图 1 将 适应轮径尺测量踏面擦伤 一1 — 3现 场 检 修
现 场检修
铁 道机车车辆工人 第 4 21 年 4月 期 00
文 章 编 号 :0 7— 0 2 2 1 ) 4— 0 3—0 10 64 (000 01 3
车轮 踏 面擦 伤 深 度 的 简 易 测 算 方 法
冯 自立 王 心 红
( 车 青 岛 四 方 机 车 车 辆 股 份 有 限公 司技 术 工程 部 山 东 青 岛 2 6 3 ) 南 6 0 1
摘 要 : 对 铁 道 车 辆 在 运 行 中 因各 种 原 因车 轮 踏 面 产 生 的擦 伤现 象 , 文介 绍 针 本
了几 种 目前 常 用 的 踏 面 擦 伤 深 度 简 易测 算 方 法 , 以 指 导 轮 对 是 否 需要 进 行 镟 用
修处理。
关 键 词 : 轮 ; 面 ; 伤 ; 度 ; 算 车 踏 擦 深 测
图4
擦 伤 的 轮 对 踏 面
说明 :
( ) 于 车轮 踏 面 磨 耗 较 小 的轮 对 , 直 接 查 阅轮 对 卡 片 中 的 车 轮 直 1对 可 径 值 ; 于车 轮 踏面 磨 耗较 深 的 轮对 , 根 据经 验 在 卡 片 中所记 录 的 车轮 直 对 可 径 尺 寸上 减 去 一定 的 补 偿 值 , 般 情 况 下 , 一 在 8 5—8 0 mm 范 围 内 , 对 1 6 轮
和 修 复 车 轮 踏 面 擦 伤 是 车 辆 日常 运 用 中 一 项 非 常 重 要 的 工 作 。
检 查 车 轮 踏 面擦 伤 主要 从擦 伤 长度 和 深 度 两 方 面 进 行 , 二 者任 意 一 当 项 超 出检 修 限 度时 需 进行 踏 面 镟修 。检 测 时擦 伤 长度 沿 圆周 方 向 可使 用 直
中 图 分 类 号 : 20 2 U 7 . 文 献 标 识 码 : B 、
铁道 车 辆 在运 行 中由 于各 种 原 因经 常 会 出 现 车 轮 踏 面 擦 伤 现 象 , 车 对 辆 的安全 、 坐舒 适 度 、 音及 线 路 维 修 等 都 会 产 生 影 响 。 及 时 发 现 、 判 乘 噪 评
铁道机 车车辆工人 第 4 21 年 4月 期 00
放 置方 法 置于所 在擦 伤 处 的车轮 踏 面 上 , 用 塞 尺 测 出车 轮擦 伤 部 位 与 踏 再 面 检测 样板 间 的最 大值 d , 下 来将 踏 面样 板 移动 至非 擦 伤 部 位 , 塞 尺 1接 用 测 出该处 ( 面 圆周上 L擦 伤 部 位 轴 向位 置 接 近 区 域 ) 踏 面 样 板 间 的 间 踏 j 与 隙 d 则 擦伤 深 度为 d 与 c 2, l f 2的差值 , : 即 d=d l—d 如 图 2所 示 。 2,
图 2 使用 踏 面 样 板 和塞 尺 检 测 踏 面擦 伤
对于 踏 面有一 定磨 耗 的 轮对 , 可使 用 上 述 方 法 , 次 测 量 求 其 平 均 数 多
值; 而对 于 踏面 磨耗 较小 的 轮对 , 板 与踏 面 间 的 间隙接 近为 零 , 样 即可 将 d 2
看 作 为零 , 此 时 : 则 d=d 。 l 3 理 论 计算 车 轮 踏 面 擦 伤 的产 生 是 因 为 制 动 时 制 动装 置 抱死 轮对 , 车 轮踏 面与 钢 轨 问产 生 使 滑 动摩 擦 , 而 导致 车 轮 踏 面 擦 伤 。在 理 论 进 上, 当轮对 被 完 全 抱 死 时 , 伤 处 在 滚 动 圆 擦 截 面上应 为 一 直 线 段 , 他 情 况 下 , 伤 处 其 擦 在 滚 动 圆截 面上 应 为 一 曲线 段 , 段 直 线 段 该
图 3 擦 伤 深 度计 算 关 系
根据 三 角关 系有 :
一
l 一 4
现 场 检 修
铁 道机车车辆工人 第 4 21 年 4月 期 00
( / ) +( 2一d =( / ) 简 化 后 :L L 2 。 D/ ) D 2 , :4 d一 d 。 D 4
通过 分 析 发 现 : 中( d ) 式 4 的值 非 常 小 , 对 于 整 个 算 式 的平 衡 可 忽 略 相
尺 按最 长 范 围进 行 测 量 , 较 容 易 完 成 。 而 车轮 踏 面擦 伤 深度 检测 一 般情 比
况 下 采』 第 2种或 第 3种 检 查器 测量 , 于 未 配 备该 种 专用 仪 器 时 可 采 用 f j 对 下 述方 法 : 使用 轮 径 尺 测量 、 使用 踏 面 样 板 和塞 尺测 量 、 理论 计 算 。
不 计 , 此 车 轮 踏面 擦 伤 的 深 度 的简 易 算 法 如 下 : 因 d— L / D 。 例 如 , 一 24 有 2 0k h动 车 组 轮 对 , 踏 面 存 在 长 度 约 4 0 m/ 其 3 mm 的 擦 伤 ( 冈 4) 查 阅 卜 见 , 片 该 轮 对 滚 动 圆 直 径 为 8 5 i , 此 , 擦 伤 深 度 d 0 5 3 i 因 i m 其 .5 mm。
或 曲线 段 的长 度 即为擦 伤 长度 。 当 擦 伤 长 度 小 于 7 ll , 将 该 段 曲 0I 时 可 l n
线段 看 作为 直线 段 , 设擦 伤 长 度 为 £, 假 擦伤
深 度 为 d 查 出 最 近 轮 对 卡 片 上 所 记 录 的 轮 , 径 D, 出 滚 动 圆 半 径 R( 图 3 。 求 见 )
1 使 用 轮 径 尺 测 量 如 网 1 示 , 使 用 轮 径 尺 测 量 出 非 擦 伤 所 先 部 化 的 滚 动 圆 直 径 A, 用 轮 径 尺 测 量 出 通 过 使 擦 伤 中 心 部 位 的 滚 动 圆 直 B, 论 上 为 滚 动 理
圆上通 过 擦 伤 中心 部 位 的 直 径 , 般 为 车 轮 踏 一 擦伤 深 度最 大处 , 即擦 伤 部 位 上 最 小 的滚 动