年产1万吨异丙苯反应及烃化液工艺设

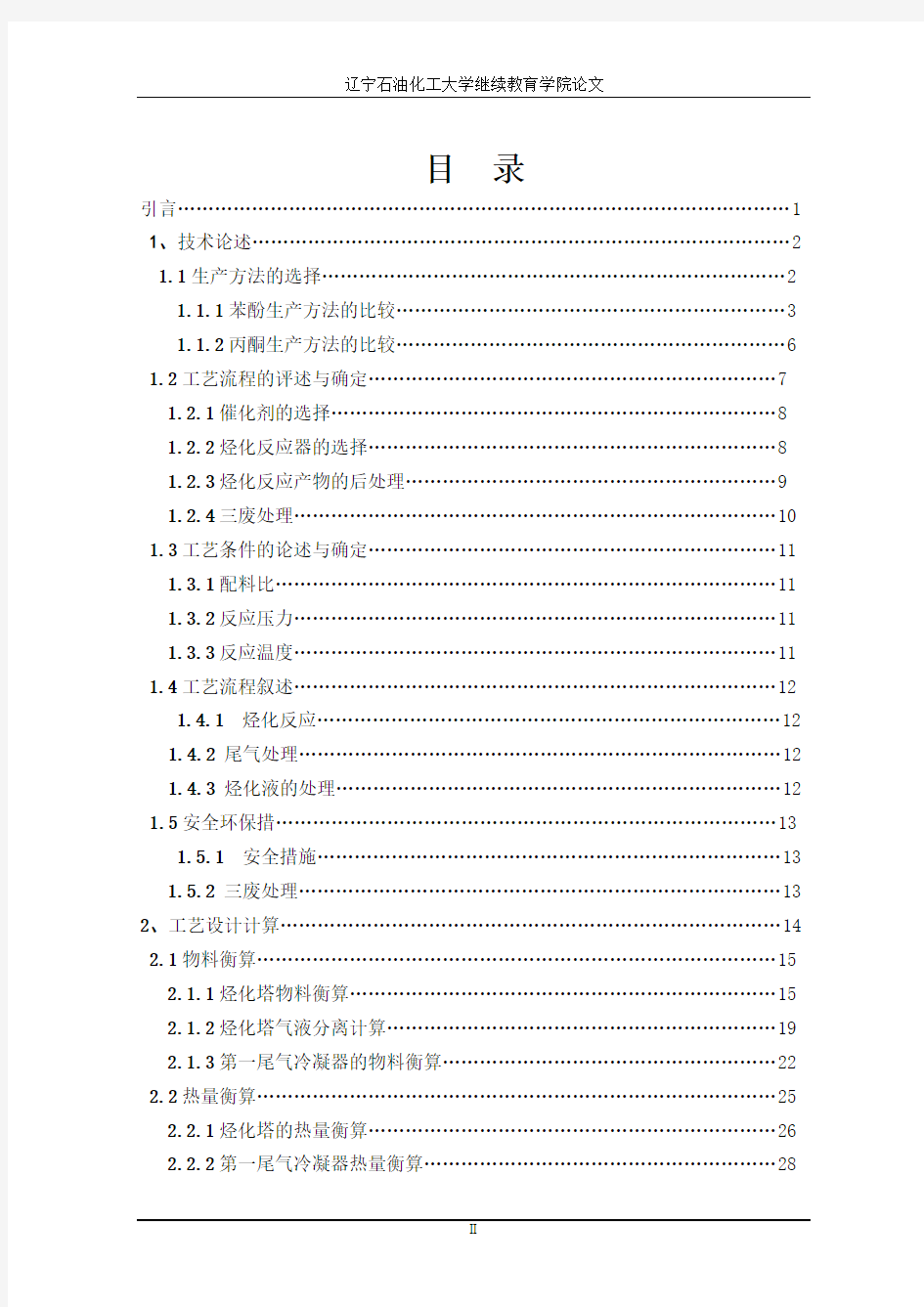
年产1万吨异丙苯反应及烃化液工艺设计
【摘要】苯酚是重要的有机合成原料之一。丙酮也是一种重要的有机合成化工原料,广泛应用于醋酸纤维素、无烟火药、油漆、涂料和药物方面,它还是一种良好的溶剂。天然丙酮满足不了经济发展的需要,大多合成。制备丙酮的方法有多种,如异丙醇法、发酵法、异丙苯法等。目前,异丙苯法是生产苯酚和丙酮的最主要的方法。本设计是年产1万吨的异丙苯反应及烃化液后处理工艺设计,设计年产量1万吨,年开工7200小时,设计反应压力0.12MPa,设计反应温度95℃。通过计算求得装置的产量等具体参数,并计算出所需设备的型号以及具体参数。【关键词】异丙苯烃化反应后处理
目录
引言 (1)
1、技术论述 (2)
1.1生产方法的选择 (2)
1.1.1苯酚生产方法的比较 (3)
1.1.2丙酮生产方法的比较 (6)
1.2工艺流程的评述与确定 (7)
1.2.1催化剂的选择 (8)
1.2.2烃化反应器的选择 (8)
1.2.3烃化反应产物的后处理 (9)
1.2.4三废处理 (10)
1.3工艺条件的论述与确定 (11)
1.3.1配料比 (11)
1.3.2反应压力 (11)
1.3.3反应温度 (11)
1.4工艺流程叙述 (12)
1.4.1烃化反应 (12)
1.4.2尾气处理 (12)
1.4.3烃化液的处理 (12)
1.5安全环保措 (13)
1.5.1 安全措施 (13)
1.5.2 三废处理 (13)
2、工艺设计计算 (14)
2.1物料衡算 (15)
2.1.1烃化塔物料衡算 (15)
2.1.2烃化塔气液分离计算 (19)
2.1.3第一尾气冷凝器的物料衡算 (22)
2.2热量衡算 (25)
2.2.1烃化塔的热量衡算 (26)
2.2.2第一尾气冷凝器热量衡算 (28)
2.2.3烃化液冷却器热量衡算 (29)
2.3设备工艺设计计算 (30)
2.3.1烃化反应器工艺计算 (30)
2.3.1.1塔径D (30)
2.3.1.2 塔高H (30)
2.3.2 反应器换热器计算 (31)
2.3.3烃化液冷却器计算 (31)
2.3.4烃化塔第一尾气冷凝器计 (32)
2.3.5沉降罐估算 (32)
2.3.6事故放料罐选 (33)
2.3.7烃化反应器接管计算 (33)
2.3.8 泵的选择 (34)
主要参考文献 (36)
致谢 (37)
工艺流程图 (38)
引言
苯酚是重要的有机合成原料之一,广泛应用于合成塑料(如酚醛树脂)、纤维(如锦纶、聚酰胺纤维)医药、农药和燃料中间体等工业生产中。随着有机合成工业,特别是塑料和合成纤维工业的迅速发展,苯酚的需求量逐年增加。
苯酚的生产最早起源于从煤焦油中提取天然苯酚,所以苯酚又叫石碳酸。这是由朗格在1834年发现的。在第一次世界大战前,生产苯酚主要采用这种方法。后来由于酚醛树脂用途日益发展,苯酚的需求量猛增,天然苯酚远远不能满足需求,合成苯酚应运而生。
丙酮也是一种重要的有机合成化工原料,广泛应用于醋酸纤维素、无烟火药、油漆、涂料和药物方面,它还是一种良好的溶剂。天然丙酮满足不了经济发展的需要,大多合成。制备丙酮的方法有多种,如异丙醇法、发酵法、异丙苯法等。在异丙苯法问世之前,主要用发酵和异丙醇法生产。
目前,异丙苯法是生产苯酚和丙酮的最主要的方法。异丙苯法生产苯酚和丙酮的工艺路线最早由前苏联实现工业化,于1949年建成了第一座异丙苯法合成苯酚丙酮的工厂。1954年开始,美国市场出现了异丙苯法合成的苯酚。发展到20世纪60年代中期,异丙苯法合成苯酚量已经占世界苯酚总产量的50%,目前已占90%以上。
我国对异丙苯法合成苯酚丙酮的研究是从1958年开始的,并在1970年实现了万吨规模的工业生产。经过十几年来我国广大科技人员的努力,已基本掌握了异丙苯法生产苯酚丙酮的技术,形成了具有自己特色的工艺流程。
通过研究计算年产1万吨苯酚丙酮装置,采用催化剂主要是金属卤化物〔AlCl3〕,同时采用一个反应器的流程。烃化反应中的AlCl3用量选用3%。烃化液的组成大约为:异丙苯30%、苯60%、其他10%。本设计采用压力:0.12MPa。本设计确定反应温度控制在95℃。气体空塔速度:0.15 m∕s,设备生产强度:200 Kg·h-1·m-3,丙烯转化率:96 %(mol),苯转化率:35 %(mol)。主、副反应分配率:异丙苯(主反应)95%(mol),二异丙苯(副反应)3.5%(mol),三异丙苯(副反应)1.5%(mol)。通过计算本设计完全满足了生产要求,并符合安全环保标准。
1、技术论述
1.1生产方法的选择
1.1.1苯酚生产方法的比较
(1)磺化法
磺化法是最早合成苯酚的方法,1923年美国孟山都公司研制投产。具体方法是将苯与浓硫酸发生磺化反应生成苯磺酸,再与亚硫酸钠反应生成苯磺酸钠,然后用氢氧化钠碱熔生成苯酚钠,最后经酸化生成苯酚、反应方程式如下;
磺化
+ H
2
SO
4
+ H
2
O
2
SO
3
2 + SO
2
+ H
2
O 320 ~350℃
+ 2 NaOH(S) + Na
2
SO
3
+ H
2
O
碱熔
酸化
2
+ H
2
O 2 + Na
2
SO
3此种方法设备简单,产率较高,适合于中小规模的生产。但需要消耗大量的浓硫酸和烧碱,而且对设备的腐蚀相当严重,且副产大量的亚硫酸钠,利用价值很小,且造成很大的污染。因此,这种方法在国际上已经淘汰,不再发展。
(2)氯化法
1924年,美国道化学公司研制成功了用氯苯水解法合成苯酚。方法是苯被氯气氯化生成氯苯,氯苯再在高温高压和催化剂的作用下被稀碱液水解得苯酚钠,苯酚钠再经酸化既得苯酚。反应方程式如下:
l
2
+ HCl
SO3H
SO3H SO3Na
SO3Na ONa
ONa OH
水 解
+2 NaOH + NaCl + H 2O
酸 化
+ HCl + NaCl
此种方法需要大量的氯,这些氯主要来源于电解食盐水,因此耗能较大:反应中有HCl 存在,腐蚀相当严重:水解条件相当苛刻,温度要达到
400℃,压强高达30Mpa,能耗大。虽然在污染问题上得到了一定的改善,取代了磺化法,但仍旧没有被广泛采用。
(3)拉西法(氧氯化法)
这种方法首先由德国的拉西研究的,故称拉西法。它是对氯化法的改良。具体方法是将盐酸、空气和苯的混合物通过固体氯化铜催化剂进行氧氯化反应,生成氯苯,再用过热水蒸气将氯苯水解成苯酚和盐酸。在第二个反应中生成的盐酸,可供第一个反应使用。反应方程式如下: CuCl 2(S )
2 + H 2
O
水 解
2O (g ) + HCl
此种方法操作条件温和,但HCl 有水存在时腐蚀性特别严重,温度大于150℃时,用搪瓷材料防腐已经不够了,维修费用较高,所以应用不广泛。 (4)环己烷法
美国科学设计公司采用苯和氢生成环己烷,环己烷在催化剂的作用下被空气氧化成环己醇,环己醇再脱氢生成苯酚。反应方程式如下: Ni
2
Cl —ONa ONa OH OH
催化剂
2
Ni
+ 3H 2
此法所需的氢由脱氢反应生成,并循环使用,
原料只需要苯和空气,来源丰富。这种方法如果工业化成功,将是很好的方法。
澳大利亚的孟山都公司小试成功,建成了2
万吨/年的工厂,但后来又改成了异丙苯法,此法没有实现工业化。 (5)苯直接氧化法
苯在催化剂作用下直接被氧化生成苯酚。反应方程式如下
催化剂 此法一步完成,反应简单,但催化剂选择性低,中间产品复杂,且产品收率较低。
研究多年,未实现工业化。如果能找到合适的催化剂和反应条件,将是种理想的的方法。 (6)甲苯氧化法
这是唯一不以苯为原料的方法,1955年美国道化学公司开发的。方法是以甲苯为原料,钴盐做催化剂,用空气氧化生成苯甲酸,再以铜盐为催化剂,将苯甲酸用空气进行液相氧化得到苯酚。反应方程式如下:
2,钴盐催化剂
℃,—OH OH OH —OH
CH 3 COOH
2,Cu 盐催化剂 240℃ +CO 2
1978年美国鲁姆斯公司提出了以甲苯为原料的气相苯甲酸脱羧基法制苯酚的新工艺,它克服了液相法副产焦油和残渣多的缺点。
国际上此法与异丙苯法是目前竞争最激烈的。但在理论上,脱羧降解要尽量少用,因为能源利用不合理。在国外,甲苯较便宜,比苯便宜20%~30%,它的成本较低,具有很强的竞争力。而在我国。甲苯和苯价格相当,此法使用较少。 (7)异丙苯法
异丙苯法发展比较晚,但是发展最快,近几十年来得到了迅速的发展。具体方法是苯和丙烯以AlCl 3
或固体磷酸为催化剂,进行烷基化反应(工业上又称烃化反应)生成异丙苯,异丙苯在液相加热,通入空气,进行催化氧化而生成过氧化氢异丙苯,再用酸分解成苯酚和丙酮。具体反应方程式如下:
① 烃化反应
CH 3
AlCl 3
或 H
3PO 4
+ CH 3CH =CH 2 CH 3 ② 氧化反应
CH 3 CH 3
+ O 2 催化剂
33 ③ 酸分解
CH 3 O
COOH H ++H 3C-C-CH 3 CH 3
COOH
OH
OH COOH
此种方法腐蚀明显减轻,污染也减轻,技术也相当成熟。最大的优点就是可以联产丙酮,它也是重要的有机原料之一,并且原料苯和丙烯来源丰富可以利用石油炼制的副产物,经济合理。
1.1.2 丙酮生产方法的比较
生产丙酮的方法基本上分为两大类:一类是以植物为原料的发酵法;一类是以石油为原料的合成法。直到20世纪30年代,淀粉仍然是生产丙酮的原料。一般情况下,每生产1吨丙酮大约需要11~12吨的淀粉或60~66吨的糖蜜。由于发酵法生产丙酮需要大量的含淀粉植物,但是原料来源有限,所以逐渐被以石油为原料的合成法替代。目前使用的合成法主要有异丙醇法、液化石油气氧化法、丙烯醇法、异丙苯法等。
(1)异丙醇法
将异丙醇催化脱氢或催化氧化脱氢生成丙酮。反应方程式如下:
异丙醇催化脱氢:
OH ZnO O
H 3C-CH-CH
3
CH
3
CCH
3
+ H
2
350~400℃
异丙醇催化氧化脱氢:
OH 催化剂 O
CH
3-CH-CH
3
+
2
1
O
2
CH
3
CCH
3
+ H
2
O
丙酮收率为85%~90%,收率低是此法的一个缺点。
(2)液化石油气氧化法
采用液化石油气(丙烷-丁烷)为原料,将它与空气按一定的比例混合,在加热加压下反应,产物除了丙酮外,还得到醇、醛、酸等有机化合物。
缺点是收率低,耗能大。
(3)丙烯醛——异丙醇法
丙烯在铜催化剂下气相氧化生成丙烯醛,丙烯醛与异丙醇在MgO-ZnO混合催化剂作用下反应得到丙烯醇和丙酮,异丙醇用空气氧化生成丙酮和过氧化氢,最后用钨酸作催化剂由过氧化氢与丙烯醇制取甘油。具体反应方程式如下:
Cu
CH 2=CHCH 3 + O 2 CH 2=CH-CHO + H 2O
OH Mg-ZnO O CH 2=CH-CHO + CH 3-CH-CH 3 CH 2=CHCH 2OH +CH 3CCH
OH O
CH 3-CH-CH 3 + O 2 CH 3CCH +H 2O 2
CH 2=CHCH 2OH + H 2O 2 钨酸
理论上每生产1mol 甘油就可以得到2mol 丙酮 (4)异丙苯法
反应过程在苯酚的生产方法中介绍过了。
以上介绍的几种生产丙酮的方法各有特点,发酵法较落后,但在有副产的蜜糖的情况下仍可以采用。在合成法中以异丙醇和异丙苯法为常见,异丙苯法可以在一个装置中同时生产苯酚和丙酮,也成为生产丙酮的主要方法。
通过以上几种方法的对比,可以确定采用异丙苯法来合成苯酚和丙酮 1.2工艺流程的评述与确定
异丙苯法生产苯酚丙酮的过程可分为四个工序:①烃化 丙烯、苯合成异丙苯的过程 ②氧化 异丙苯氧化生成过氧化异丙苯的过程 ③酸分解 在酸的作用下,过氧化氢异丙苯分解生成苯酚和丙酮的过程 ④精制分离 精制苯酚和丙酮的过程
本设计重点在烃化工序。
烃化的工艺过程大致由五个部分组成:催化剂的制备;原料预处理;烃化反应器;烃化反应产物的后处理;三废处理。烃化工序工艺流程的确定主要是催化剂和反应器的选择。 1.2.1催化剂的选择
所用的催化剂主要是金属卤化物(如AlCl 3)和强无机酸(如固体磷酸),在工业上采用的催化剂就是这两种。这两种方法在工艺条件和工艺流程等方面都有很大的差别,各有优缺点。 (1)磷酸气相法
CH 2–OH |
CH –OH (甘油)
| CH 2–OH
它是20世纪40年代开发的,采用固体磷酸催化剂生产异丙苯的工艺流程主要是美国环球油品公司开发的技术。此法的优点是无强腐蚀,无污水对环境保护有利;设备材质防腐要求不高,易解决;流程简单,设备台数少;单位产品耗能低;易于大型化。它的不足之处在于选择性低,收率低,因为磷酸法没有反烃化方应,使生成的副产物多;在高温高压下反应,要求设备、泵等密封严密,并且要耐高温,加工难度大,投资高;催化剂易失活,要求反复再生。
磷酸法对于装置规模较大时(年产10万吨以上),它的优越性才突出,而且此法对设备材质要求也高。对于本设计规模较小,优越性不太突出,并且国内的设备材质等也难以满足要求,所以不采用此法。
(2)液相三氯化铝法
这种方法也是40年代开发的。催化剂是AlCl
3的一种络合物,由烷基苯、AlCl
3
和盐酸组成。此法技术成熟,工艺条件温和。
它的优点弥补了磷酸法的不足,收率较高些,有反烃化的效果。但一直存在着设备腐蚀和污水处理的问题。本设计就是采用此法。
1.2.2 烃化反应器的选择
在采用烃化反应器的型式时必须考虑以下几点:本反应是气液非均相反应,要保证气液充分接触,使反应顺利进行;反应很易达到平衡,混反影响不大;反应液有强烈的腐蚀性;AlCl
3
络合物在高温下长期使用,易生成树脂,堵塞管道。
如果采用填料塔,气液相接触较好,有利于传质,接触面更新较快,有利于反
应的继续进行。但反应温度不可避免局部过高,AlCl
3
络合物就会结成树脂,堵塞填料,所以不用填料塔。
如果采用有搅拌器的反应槽,搅拌对传质和表面更新都有利,但是有反应
AlCl
3+3H2O→Al(OH)
3
+HCl,有HCl存在,腐蚀严重,而且对搅拌器不好防腐,所以
也不采用这种方法。
根据以上几个特点,采用结构简单的鼓泡空塔,其结构简单,不易堵塞,易于作防腐处理。由于烃化液和AlCl
3
络合物得比重差不大,采用气态丙烯鼓泡进料的办法就可以使络合物在整个反应区域内分布得比较均匀,也可使苯和丙烯充分接触。采用气态丙烯还有一个主要因素是保证苯过量,丙烯不足,从而减少多烷基苯的生成。对于反应的换热装置也不装在内部,而是在塔外(如夹套等),否则要作防腐处理,很复杂。
目前主要有采用一个反应器和采用两个反应器的流程。国内烃化流程都是采用一个反应器。烃化反应和反烃化反应在同一个反应器中进行。缺点是生成的多烷基苯多,不能实现反应的最佳化。为了避免生成过多的多烷基苯,必须使反应在过量苯存在下进行,这样造成了反应器生产能力下降,也增加了烃化液精馏分离塔的负荷。为了克服这一缺点,让烃化反应和反烃化反应分别在不同的反应器中进行,即采用两个反应器。
采用两个反应器在国外已经工业化了。一个进行烃化反应,一个进行反烃化反
的消耗定额②异丙苯收率提高,反应器成产能应。此法优点①可进一步降低AlCl
3
力提高。两个反应分别在两个反应器中进行,都可以实现反应的最佳化,多异丙苯含量降低,异丙苯收率提高,同时反应器的生产能力也提高了③降低了精馏塔的负荷,减少了苯干燥塔和脱苯塔的一次投资和操作费用。采用两个反应器,即使丙烯与苯环的分子比增大,多异丙苯增加也不多,而异丙苯产量可有明显的提高。这样苯过量不大,减少了精馏塔负荷;同时因进料苯和剩余苯减少,处理它的苯干燥塔和脱苯塔也可以减小,一次投资降低;苯流量小,动力操作费用也减少。
这些都说明采用两个反应器比采用一个反应器优越的多,但在我国两个反应器的工艺还不成熟,技术条件不具备。所以本设计采用一个反应器的流程,即鼓泡塔反应器,物料并流。
1.2.3 烃化反应产物的后处理
烃化反应器出来的烃化液和三氯化铝络合物必须分离开,并将烃化液精制,以得到异丙苯。一般都采用沉降、水洗和中和进行处理。
(1)反应混合物的沉降
络合物具有较大的比重(烃化液比重是0.86,络合物比重是1.2~1.3),所以采用一般的沉降器就可以将它们分离。原来采用两个沉降器串联,反应液出料进入第一沉降器,沉降下来的络合物返回烃化器。研究发现采用两个沉降器有很多的缺点:①设备庞大,生产能力低。沉降槽内络合物靠自重回流,流速很慢,约为0.2m/s,所以沉降回流的管子造的都很粗。为了保证沉降时间足够,络合物能较多的沉降下来,沉降槽的体积都很大,用两个大槽设备庞大,造价高,空间占用也大。要保证充分的沉降时间,就使生产周期延长,势必造成生产能力下降。②精制更困难。因为第一沉降槽内温度和络合物浓度都较高,易生成副产物,而且停留时间长,给杂质的生成提供了机会,给精制带来了更大的困难。
可见采用沉降、冷却、再沉降的流程不合理。
现改为烃化液冷却到60~65℃,再沉降。先冷却避免烃化液和络合物在高温下长时间的接触生成更多的副产物。沉降时间1小时左右,时间缩短,生产能力提高。沉降1小时,能保证充分的沉降,若延长沉降时间对沉降效果的影响并不明显,反而降低了生产能力。
(2)烃化液的水洗和中和
烃化液在沉降后还含有少量的三氯化铝,因为三氯化铝在烃化液中有一定的溶解度。为了去除这部分络合物,可以采用水洗和碱中和的办法。
①水洗(在空塔中水洗)
AlCl
3 +3H
2
O Al(OH)
3
+ 3HCl
②中和(碱洗):水洗后的烃化液中基本没有三氯化铝了,但是溶液呈酸性,还需要用氢氧化钠中和,即碱洗,也采用空塔。
1.2.5 三废处理
用三氯化铝催化剂生产异丙苯的这一工艺流程最大的缺点是,过程中排出大量的污水,要经过处理才能排放,使得流程复杂,动力消耗增加。
污水中主要的有害物质是芳烃和Al(OH)
3。Al(OH)
3
的分离很困难,可采用简单
蒸馏的方法回收芳烃,并把含有Al(OH)
3的污水作为浮选剂,这种方法要保证Al(OH)
3
溶解。
废气是烃化尾气,里面没反应的丙烷送去做燃料。
废渣有焦油,规模小时可以烧掉,规模大时要分离出来回收利用。
1.3. 工艺条件的论述与确定
烃化反应是一个汽液相反应,主要工艺条件是反应温度、反应压力和催化剂的用量、原料的配比等。
1.3.1 配料比
即丙烯与苯核的分子比,实际上是反应器进料中烃基(这里指异丙基,它不只包括丙烯,还包括进料中带入的二异丙苯中的异丙基,因为在反烃化反应中异丙基也起到丙烯的作用)和苯核(苯和异丙苯、多异丙苯中的苯核)分子数目之比,习惯称做分子比。
烃化生成二异丙苯和三异丙苯的速度比异丙苯的快。随着分子比的上升,异丙苯增加,但是多异丙苯的含量增加更快,所以不仅造成了多异丙苯的循环量大,而
且也会增大烃焦油量;若分子比很小,芳烃过量很多,异丙苯的产量很低,生产能力小,而且有大量的苯没有反应,苯的转化率太低会增加精馏系统的负荷,增大了操作费用和一次性投资。
为了得到异丙苯和抑制多元异丙苯的生成,采用控制丙烯的含量,让芳烃过量,但不能过量太大。综合考虑苯的一次转化率、收率、设备生产能力等因素,工业生产中所选用的较佳的丙烯/苯=0.4~0.6。本设计采用的分子比是0.5左右,经研究得到这时烃化液的组成大约为:异丙苯30%、苯60%、其他10%。
1.3.2反应压力
烃化反应式:C
6H
6
(l)+CH
2
=CHCH
3
(g) C
6
H
5
(C
3
H
7
)(l)
此反应是气相分子数减少的反应,压力上升有利于丙烯的溶解,也使苯的转化率上升。但因为常压下烃化反应的转化率已接近100%(以丙烯的转化率计,因为丙烯不足),反应压力的影响不显著。
压力上升时反应液的泡点也上升,使反应温度上升导致催化剂失活,对烃化反应不利,甚至使反应不能进行,从这方面看加压不利。为保证温度不大于120℃(避免催化剂失活)要求压力不大于6Kgf/cm2。
综合考虑,稍加一点压,只是为了克服阻力损失。所以本设计采用压力:
0.12MPa。
1.3.3反应温度
烃化反应是放热反应。根据热力学和动力学分析,温度上升,反应平衡常数下降,但反应速率上升,副反应速率也上升;温度下降,反应平衡常数上升,但反应速率下降。
反应温度对烃化反应的平衡影响不大,提高温度对平衡常数影响不大。温度低,反应速率慢;温度高,反应速率提高,但是副反应速率提高更快。当温度大于120℃时,催化剂三氯化铝络合物不耐高温,会发生结焦现象形成树脂,使催化剂失活,反而使反应速率急剧下降。温度高,也可引起丙烯聚合,副反应增加。目前烃化反应器换热的方法是用未反应的苯汽化带出反应放出的热。所以反应温度就是在反应压力下一定组成混合物的泡点。混合物的组成大约为:异丙苯30%、苯60%、副产品10%,反应压力为0.12 MPa时混合液的泡点是97.5℃,一般控制在95~100℃,本设计确定反应温度控制在95℃。
1.4 工艺流程叙述
1.4.1烃化反应
烃化反应是在95℃、0.12MPa下进行的,是放热反应,反应热主要靠苯蒸发带出,其余热利用反应器的夹套换热器与水换热。
1.4.2尾气处理
从烃化塔T
116
顶部出来的气体叫尾气,其中有苯、丙烯、异丙苯等组分,尾气
出来后首先经过第一气液分离器V
117,分离后气相进入第一尾气冷凝器E
120A
,气相出
料再经过第二尾气冷凝器E
120B 换热后进入第二气液分离器V
121
,气体去尾气吸收塔。
从第一气液分离器V
117,第一尾气冷凝器E
120A
,第二气液分离器V
121
出来的液体回流
至沉降罐V
119。为了保证液体顺利回流,在沉降罐V
119
上部同冷凝器进料管连通,保
证压力平衡。
1.4.3烃化液的处理
从烃化塔出来的液体叫烃化液,其中含有苯、异丙苯、多异丙苯和AlCl
3
络合
物等,经过产品冷却器E
118冷却后进入沉降罐V
119
,由于烃化液与络合物比重不同而
分层,沉降在下部的络合物通过出料管回到烃化塔T
116
循环使用。络合物残渣通过
沉降罐V
119
排渣口定期排掉,进行回收处理。烃化液从沉降罐上部溢流出来进入水
洗塔T
122
,从下部进料,水从水洗塔上部喷入,逆流洗涤,残留在烃化液中的三氯
化铝溶解到水中,污水流至污水池V
127
,烃化液经水洗后由塔上部出来,经碱洗泵
P
123AB 同碱混合,碱洗,送入碱洗塔T
124
,碱洗后的烃化液分层后送到烃化液储罐中待
精馏。分层后的碱液重新抽回碱洗泵P
123AB
循环使用,待碱浓度降到小于3.5%时排放
到污水池V
127
,重新补充新碱。污水送入处理系统进行处理。
1.5.安全环保措施
1.5.1 安全措施
生产异丙苯过程的原料和产品都是易燃易爆物品,所以安全生产是本工序的头等大事。
①严禁烟火。
②所有设备都作接地处理,以防出现静电火花。
③电器仪表都为防爆型。
④烃化反应器设有防爆膜,以防温度、压力急剧上升时发生意外情况。系统设有事故放料罐,以作应急处理。
⑤工厂内不得穿化纤制作的服装,鞋不得钉铁钉,以防出现静电火花。
1.5.2 三废处理
用三氯化铝作催化剂这一工艺流程最大的缺点就是排出大量的污水。处理这部分污水使流程复杂并增加了动力消耗。烃化过程中排出污水来源于烃化液的水洗、中和、尾气水洗中和和苯干燥时排放的水层。污水中主要有害物质是芳烃(苯和异丙苯)和Al(OH)
3
,含量分别在1000~2000ppm左右。
因含Al(OH)
3使污水的处理较为困难,因为Al(OH)
3
是一种两性的氢氧化合物,
在强酸或强碱介质中呈水溶解状态,它能与水、芳烃形成一种乳状物,比重介于水
和芳烃之间,影响了水层和油层的分离和回收,造成污水处理困难。
最简单的处理方法是采用蒸馏的办法回收污水中的芳烃,并把含有Al(OH)
3
的
污水作为浮选剂。但是采用这种方法的前提是pH在4左右,这时Al(OH)
3
处于溶解状态,经验数据证明,采用这种方法回收芳烃可保持在90%以上。
在生产过程中还要排除废渣,主要是沉降罐排放出来的废络合物,这些废渣进入催化剂回收系统。烃化反应产生的焦油送去精制分离。
尾气处理方法是将尾气经过碱洗、水洗后压缩入燃料系统,即解决了污染问题,又节约了能源。
2、工艺设计计算
2.1物料衡算
物料流程简图:
化学反应方程式
主反应: C 6H 6+CH 2=CHCH 3 C 6H 5(C 3H 7)
副反应:C 6H 6+2CH 2=CHCH 3 C 6H 4(C 3H 7)2 C 6H 6+3CH 2=CHCH 3 C 6H 3(C 3H 7)3 有关物质的分子式与分子量列于表1中。
表1 物质的分子式与分子量表
2.1.1烃化塔物料衡算
衡算基准:以每小时物料质量为基准。
(1)生产能力
CM产量ω
CM
=10000×103/7200=1388.9 kg/h =11.57 kmol/h
(2)进料量的计算
①丙烯原料的进料量
理论上1mol丙烯生成1mol CM。
∵ω
丙烯·进
×转化率(丙烯)×分配率(CM)×后处理收率=异丙苯产量
∴ω
丙烯·进
= 11.57/95%/95%/96% =13.35 kmol/h = 560.9 kg/h
ω
丙烷·进= ω
丙烯·进
/丙烯纯度×丙烷纯度 = 302.0kg/h=6.86 kmol/h
②苯原料进料量
苯单耗=0.8吨苯/吨(CM)
消耗苯量=反应掉苯量+损失苯量,假设损失苯量≈0
∵ω
苯·进×转化率(苯)=苯单耗×ω
CM
∴ω
苯·进
=1388.9×0.8/35% =3174.6 kg/h = 40.70 kmol/h
ω
甲苯·进=ω
苯·进
/苯纯度×甲苯纯度=32.10kg/h=0.35 kmol/h
③新催化剂的加入量
已知新Cat量/CM=3吨(AlCl3)/100吨(CM)=0.03
ω
AlCl3·新=ω
CM
×0.03=1388.9×0.03=41.67 kg/h =0.31 kmol/h
ω
=CM·新=ω
AlCl3·新
/ AlCl
3
纯度×=CM纯度=86.17 kg/h =0.53 kmol/h
ω
≡CM·新=ω
AlCl3·新
/ AlCl
3
纯度×≡CM纯度=38.84 kg/h =0.19 kmol/h
④催化剂的总加入量
假设循环Cat的组成与新加入的Cat组成相等。
已知循环Cat量/ω
CM
=35吨(Cat络合物)/100吨(CM)=0.35
ω
Cat·循=ω
CM
×0.35=1388.9×0.35=486.12 kg/h
ω
AlCl3·循=ω
Cat·循
×25%=121.53 kg/h =0.91 kmol/h
ω
=CM·循=ω
Cat·循
×51.7%=251.32kg/h =1.55 kmol/h
ω
≡CM·循=ω
Cat·循
×23.3%=113.27 kg/h =0.56 kmol/h
∴ω
Cat·进=ω
AlCl3·新
+ω
AlCl3·循
=163.2kg/h =1.22 kmol/h
ω
=CM·进=ω
二CM·新
+ω
=CM·循
=337.49kg/h =2.08 kmol/h
ω
≡CM·进=ω
三CM·新
+ω
≡CM·循
=152.11 kg/h =0.75 kmol/h
(3)出料量的计算
丙烷和甲苯、AlCl
3
不参加反应。
ω丙烷·出=ω丙烷·进=302.0 kg/h =6.86 kmol/h
ω甲苯·出=ω甲苯·进=32.1 kg/h =0.35 kmol/h
ωAlCl3·出=ωAlCl3·进=163.2 kg/h =1.22 kmol/h
ω丙烯·出=ω丙烯·进(1-丙烯转化率)=22.43 kg/h =0.534 kmol/h
ωCM·生成=ω丙烯·进×丙烯转化率×分配率(CM)=12.18 kmol/h =1461.02 kg/h ω=CM·生成=ω丙烯·进×丙烯转化率×分配率(=CM)×1/2=0.23 kmol/h =36.33 kg/h ω≡CM·生成=ω丙烯·进×丙烯转化率×分配率(≡CM)×1/3 =0.064 kmol/h =13.07 kg/h
∴ω
CM·出=ω
CM·生成
=12.18 kmol/h =1461.02 kg/h
ω=CM·出=ω=CM·进+ω=CM·生成= 2.08+0.23=2.31 kmol/h =374.22 kg/h ω≡CM·出=ω≡CM·进+ω≡CM·生成=0.75+0.064=0.814 kmol/h =166.06 Kg/h
ω苯·出=ω苯·进-ω苯·反应=ω苯·进-{ωCM·生成+ω=CM·生成+ω≡CM·生成}
=40.70-{12.18+0.23+0.064}=28.23 kmol/h =2201.63 kg/h 说明:与按苯的转化率计算相比有些误差,误差出在苯有损失,而在计算中先
把这部分忽略了。
整理数据列于表2中。
表2 烃化塔物料衡算表
异丙苯生产工艺
发明人:Dennis J. Ward, South Barrington, Ⅲ. 委托人:UOP Inc.,Des Plaines,Ⅲ. 申请时间:Apr. 19, 1976. Appl. No.: 678, 005 摘要 一种能减少苯与丙烯催化烷基化生产异丙苯的能耗的工艺。丙烯和苯在烷基化 反应器内反应,反应流出物分成两部分,第一部分再循环至反应器的入口,第二 部分输送到一个分离异丙苯产物,二异丙苯,三异丙苯和过剩的苯的分离器中。 一部分过剩的苯回收到烷基化反应器中,另一部分与二异丙苯,三异丙苯混合后 输送到烷基转移反应器中,将其流出物引入到一个独立的反应器中。由于减少了 分离部分过剩苯所需能量和回收了部分过剩的苯至烷基化反应器,所以这种工艺 与之前的工艺流程相比,能量消耗大大减少了。 附图: 11 3 Butyl benzene 12 10 Benzene Drag Transalkylation Propane 9 13 Cumene Reaction Zone Propylane 1 5 6 11 16 2 7 15 4 Alkylationg 14 Separation Zone Reactiong Zone Propylane Oligomes 8 Benzene
交叉引用相关的专利申请 这篇专利申请在一定程度上是一篇正处于审理中的,编Ser. No. 557010(在1975年3月10号提出,现已放弃)的专利申请的延续。 该项发明的背景 该项发明提出了一种在烷基化催化剂的存在下由苯和丙烯生产异丙基苯的改进工艺,也涉及在转移烃化催化剂的存在下利用二异丙苯,三异丙苯和苯通过烷基转移生产异丙苯工艺。 本发明广泛适用于烷基化芳烃的生产,这些化合物是有用的在自己和更频繁地在后续其他化合物的化学合成。本发明特别适用于生产异丙苯(异丙基苯),异丙苯是制备苯酚,丙酮、甲基苯乙烯、苯乙酮的重要反应物。该项工艺发明的另一种用途是制备对异丙基甲苯,它能氧化生成对甲苯酚。该工艺的进一步应用是在一类被取代的芳香族化合物的烷基化反应中,比如:苯酚,在它与异丁烯烷基化反应生成邻叔丁基苯酚和对叔丁基酚(两者在合成树脂领域都有重大用途)时,就能应用到该工艺。 综上所述,本发明在制备异丙苯工艺中有着特别的应用。在一般商业生产异丙苯的过程中,将液态苯和液态丙烯投入反应器中,使之与烷基化催化剂接触下,在一个或多个反应器中发生相同的烷基化反应是一种惯例。为了减少苯的二烃基化合物的产生,通常我们将反应器中苯与丙烯的摩尔比由4:1提高至16:1,最好是8:1。在之前的工业化生产中利用两个相抵触的反应生产异丙苯产生了一些问题,其中之一就是产生了上文所说的二烃基化合物,比如:二异丙苯、三异丙苯,而不是所需的单烷基化产物。这种竞争反应通过采用如上所述的大摩尔量过剩的苯来控制。其他的竞争反应导致了异丙苯产量的损失,因为一部分反应物丙烯形成丙烯的低聚物,如在一定程度上会出现丙烯二聚物和三聚物,即使有大量过剩的苯存在。将丙烯三聚物和一些丙烯四聚物与异丙苯一起加热,由于这些烯烃的存在,这种产生低聚物的反应(异丙苯氧化制备苯酚的反应)必须控制到最小,这样才能获得高纯度的产品。 烷基化芳香族化合物的烷基化反应在自然条件下是放热的,反应器的温度会迅速增高。放热反应导致温度的增高,同样也会导致副反应的产生,从而增加异丙苯的残留产物。在过去已经习惯通过在多个单独的区域和使用骤冷剂之间的几个连续的烷基化区催化反应来控制温度上升。这种骤冷剂是为了在反应混合物进入每个连续的区域时控制温度,因此在每一个区域内温度都会上升。反应器从进口到出口温度的增加也通过控制苯的摩尔量的过量来控制,苯充当散热器吸收烷基化反应所释放的热量。因此,向反应器增加苯的摩尔过剩量,与相应的稀释丙烯反应物,不仅提供了更多的芳香族化合物发生烷基化和减少低聚物的产生和烷基化的副产品,也减少了在一个或多个烷基化反应器中因过度温升造成不良副产物的形成。
苯酚和丙酮的生成
第九章苯酚和丙酮的生产练习题 ㈠、填空题 1、﹙﹚和﹙﹚是重要的基本有机化工原料。 2、﹙﹚法是生产苯酚和丙酮最重要的方法。 3、苯酚的生产方法有﹙﹚﹙﹚﹙﹚﹙﹚﹙﹚。4、在苯酚的生产方法中,﹙﹚是目前苯酚的首选方法。 5、丙酮的生产方法有﹙﹚﹙﹚﹙﹚和﹙﹚。 6、丙酮的生产原料主要有﹙﹚﹙﹚﹙﹚等。 7、异丙苯的生产工业上广泛采用﹙﹚法,该法采用﹙﹚反应器。8、异丙苯氧化是一个﹙﹚过程,属于﹙﹚反应。 9、异丙苯氧化的工艺条件有﹙﹚﹙﹚﹙﹚﹙﹚﹙﹚。 10、异丙苯氧化反应器为﹙﹚。 11、影响过氧化氢异丙苯分解的因素主要有﹙﹚﹙﹚﹙﹚﹙﹚。 ㈡、选择题 12、在异丙苯的生产工业上,﹙﹚的催化剂活性较高,但其液相呈酸性。对设备、管道的腐蚀性很强。 A、三氯化铝法 B、硫酸法 C、三氯化铁法 D、磷酸-硅藻土气相法 13、为防止过氧化氢异丙苯的分解,生产中有两种方法,一是加入﹙﹚溶液,稳定过氧化氢异丙苯,二是采用﹙﹚作催化剂。 A、NaoH B、Na2CO3 C、碱类 D、盐类 14、影响过氧化氢异丙苯分解的工艺条件有﹙﹚。 ①催化剂用量②反应温度③反应压力④原料组成 A、①②③ B、①②④ C、②③④ D、①②③④ 15、实际生产中,过氧化氢异丙苯分解,大多采用﹙﹚催化剂。 A、硫酸 B、二氧化硫 C、强酸性磺酸阳离子交换树脂 D、硝酸 16、异丙苯氧化反应器为﹙﹚。 A、固定床催化反应器 B、内冷却型鼓泡氧化塔 C、釜式反应器 D、外冷却型鼓泡床反应器 ㈢、判断题 17、甲苯氧化法是生产苯酚和丙酮最重要的方法。﹙﹚ 18、丙酮的生产原料主要有丙烯、淀粉、异丙醇等。﹙﹚
苯酚丙酮生产工艺流程
苯酚丙酮制作工艺统计,世界上90%以上的苯酚采用异丙苯法生产。其工艺步骤是:苯和丙烯反应得到异丙苯;异丙苯经氧气或空气氧化,生成过氧化氢异丙苯(CHP);CHP分解生成苯酚和丙酮。该方法以KBR公司的苯酚法工艺最为典型。除从异丙苯生产高纯度苯酚和丙酮外,还回收副产物α-甲基苯乙烯(AMS)和苯乙酮(AP)。在该工艺中,异丙苯用空气氧化成CHP的效率高达95%以上,CHP被浓缩,并在酸催化剂存在下高产率(大于99%)地分解为苯酚和丙酮。AMS加氢为异丙苯,用于循环氧化或回收。带有AMS加氢的流程,吨异丙苯可生产1吨苯酚和吨丙酮。KBR苯酚工艺具有低能耗、低原材料消耗、低生产费用和低排放污染的特点。现已采用该工艺建设了30套生产装置,生产苯酚总能力超过280万吨/年。20世纪90年代底,Aristech公司和壳牌化学公司采用该工艺分别在美国建成10万吨/年和万吨/年装置,中国石化上海高桥分公司也引进了这一工艺。采用该工艺生产的苯酚占世界能力的50%以上。埃克森美孚公司还开发了由过氧化氢异丙苯(CHP)制取苯酚的催化精馏技术,塔器催化剂床层中采用Zr-Fe-W氧化物固体催化剂,转化率可达100%,苯酚和丙酮选择率高,而4-异丙苯基苯酚、α-甲基苯乙烯(AMS)二聚物及焦油等高沸点的联产杂质数量很少。该工艺对苯酚的选择性为%,稍低于采用硫酸为催化剂的传统工艺。反应器催化剂床层操作条件为:50~90、34Kpa、液时空速4h-1。联产物α-甲基苯乙烯和苯乙酮的选择性分别为%和%。该催化精馏工艺有效地将反应热用于丙酮精馏过程,将反应过程和精馏过程结合在一起,降低了能耗和投资。由于采用固体酸催化剂代替通用的硫酸催化剂,可免除产物的中和过程。甲苯-苯甲酸法先将甲苯液相氧化为苯甲酸,苯甲酸再转化为苯酚。具有甲苯原料来源广泛、流程简单等优点。目前采用的异丙苯法存在联产大量丙酮(丙酮和苯酚产率比为:1)问题,同时苯酚需精制而耗用能源。现正在开发苯直接氧化制苯酚的一步反应法。日本研究人员开发了利用贵金属催化剂的一步法工艺。首诺(Solutia)公司开发了采用一氧化二氮为氧化剂使苯直接催化氧化为苯酚的一步法工艺。最近日本先进工业科技国家研究院(AIST)开发了由苯一步法合成苯酚工艺,而常规工艺从苯开始需三个步骤,并且产生需处埋的废酸。AIST的工艺使用不锈钢外管和多孔α-氧化铝内管组成的反应器,关键元件是厚1μm的钯膜催化剂,用化学蒸气沉积法涂复在氧化铝管的外侧。膜由AIST与丸善石化公司和NOK公司共同开发。反应器置于加热至150~250的加热炉内,苯和氧气流过氧化铝内管,压力的氢气沿管外侧通过。氢被吸附在膜上,在此被离解和活化,然后通过氧化铝管内表面,活化的氢捕集管子内表面上的氧分子,生成活化的氧,活化的氧与苯环的双键反应通过苯环氧化物由苯生成苯酚。实验室中,在转化率低于3%时,生成苯酚的选择性大于90%。10%~15%转化率时,选择性大于80%。苯酚产率为每千克催化剂千克/时,随着工艺过程的改进,预计转化率还可提高。
异丙苯生产工艺设计
异丙苯生产工艺 发明人:Dennis J. Ward, South Barrington, Ⅲ. 委托人:UOP Inc., Des Plaines,Ⅲ. 申请时间:Apr. 19, 1976. Appl. No.: 678, 005 摘要 一种能减少苯与丙烯催化烷基化生产异丙苯的能耗的工艺。丙烯和苯在烷基化 反应器内反应,反应流出物分成两部分,第一部分再循环至反应器的入口,第二 部分输送到一个分离异丙苯产物,二异丙苯,三异丙苯和过剩的苯的分离器中。 一部分过剩的苯回收到烷基化反应器中,另一部分与二异丙苯,三异丙苯混合后 输送到烷基转移反应器中,将其流出物引入到一个独立的反应器中。由于减少了 分离部分过剩苯所需能量和回收了部分过剩的苯至烷基化反应器,所以这种工艺 与之前的工艺流程相比,能量消耗大大减少了。 附图: 11 3 Butyl benzene 12 10 Benzene Drag Transalkylation Propane 9 13 Cumene Reaction Zone Propylane 1 5 6 11 16 2 7 15 4 Alkylationg 14 Separation Zone Reactiong Zone Propylane Oligomes 8 Benzene
异丙基苯的生产 交叉引用相关的专利申请 这篇专利申请在一定程度上是一篇正处于审理中的,编Ser. No. 557010(在1975年3月10号提出,现已放弃)的专利申请的延续。 该项发明的背景 该项发明提出了一种在烷基化催化剂的存在下由苯和丙烯生产异丙基苯的改进工艺,也涉及在转移烃化催化剂的存在下利用二异丙苯,三异丙苯和苯通过烷基转移生产异丙苯工艺。 本发明广泛适用于烷基化芳烃的生产,这些化合物是有用的在自己和更频繁地在后续其他化合物的化学合成。本发明特别适用于生产异丙苯(异丙基苯),异丙苯是制备苯酚,丙酮、甲基苯乙烯、苯乙酮的重要反应物。该项工艺发明的另一种用途是制备对异丙基甲苯,它能氧化生成对甲苯酚。该工艺的进一步应用是在一类被取代的芳香族化合物的烷基化反应中,比如:苯酚,在它与异丁烯烷基化反应生成邻叔丁基苯酚和对叔丁基酚(两者在合成树脂领域都有重大用途)时,就能应用到该工艺。 综上所述,本发明在制备异丙苯工艺中有着特别的应用。在一般商业生产异丙苯的过程中,将液态苯和液态丙烯投入反应器中,使之与烷基化催化剂接触下,在一个或多个反应器中发生相同的烷基化反应是一种惯例。为了减少苯的二烃基化合物的产生,通常我们将反应器中苯与丙烯的摩尔比由4:1提高至16:1,最好是8:1。在之前的工业化生产中利用两个相抵触的反应生产异丙苯产生了一些问题,其中之一就是产生了上文所说的二烃基化合物,比如:二异丙苯、三异丙苯,而不是所需的单烷基化产物。这种竞争反应通过采用如上所述的大摩尔量过剩的苯来控制。其他的竞争反应导致了异丙苯产量的损失,因为一部分反应物丙烯形成丙烯的低聚物,如在一定程度上会出现丙烯二聚物和三聚物,即使有大量过剩的苯存在。将丙烯三聚物和一些丙烯四聚物与异丙苯一起加热,由于这些烯烃的存在,这种产生低聚物的反应(异丙苯氧化制备苯酚的反应)必须控制到最小,这样才能获得高纯度的产品。 烷基化芳香族化合物的烷基化反应在自然条件下是放热的,反应器的温度会迅速增高。放热反应导致温度的增高,同样也会导致副反应的产生,从而增加异丙苯的残留产物。在过去已经习惯通过在多个单独的区域和使用骤冷剂之间的几个连续的烷基化区催化反应来控制温度上升。这种骤冷剂是为了在反应混合物进入每个连续的区域时控制温度,因此在每一个区域内温度都会上升。反应器从进口到出口温度的增加也通过控制苯的摩尔量的过量来控制,苯充当散热器吸收烷基化反应所释放的热量。因此,向反应器增加苯的摩尔过剩量,与相应的稀释丙烯反应物,不仅提供了更多的芳香族化合物发生烷基化和减少低聚物的产生和烷基化的副产品,也减少了在一个或多个烷基化反应器中因过度温升造成不良副产物
《苯酚丙酮生产工艺流程》
《苯酚丙酮生产工艺流程》-标准化文件发布号:(9556-EUATWK-MWUB-WUNN-INNUL-DDQTY-KII
苯酚丙酮制作工艺统计,世界上90%以上的苯酚采用异丙苯法生产。其工艺步骤是:苯和丙烯反应得到异丙苯;异丙苯经氧气或空气氧化,生成过氧化氢异丙苯(CHP);CHP分解生成苯酚和丙酮。该方法以KBR公司的苯酚法工艺最为典型。除从异丙苯生产高纯度苯酚和丙酮外,还回收副产物α-甲基苯乙烯(AMS)和苯乙酮(AP)。在该工艺中,异丙苯用空气氧化成CHP的效率高达95%以上,CHP 被浓缩,并在酸催化剂存在下高产率(大于99%)地分解为苯酚和丙酮。AMS加氢为异丙苯,用于循环氧化或回收。带有AMS加氢的流程,吨异丙苯可生产1吨苯酚和吨丙酮。KBR苯酚工艺具有低能耗、低原材料消耗、低生产费用和低排放污染的特点。现已采用该工艺建设了30套生产装置,生产苯酚总能力超过280万吨/年。20世纪90年代底,Aristech公司和壳牌化学公司采用该工艺分别在美国建成10万吨/年和万吨/年装置,中国石化上海高桥分公司也引进了这一工艺。采用该工艺生产的苯酚占世界能力的50%以上。埃克森美孚公司还开发了由过氧化氢异丙苯(CHP)制取苯酚的催化精馏技术,塔器催化剂床层中采用 Zr-Fe-W氧化物固体催化剂,转化率可达100%,苯酚和丙酮选择率高,而4-异丙苯基苯酚、α-甲基苯乙烯(AMS)二聚物及焦油等高沸点的联产杂质数量很少。该工艺对苯酚的选择性为%,稍低于采用硫酸为催化剂的传统工艺。反应器催化剂床层操作条件为:50~90、34Kpa、液时空速4h-1。联产物α-甲基苯乙烯和苯乙酮的选择性分别为%和%。该催化精馏工艺有效地将反应热用于丙酮精馏过程,将反应过程和精馏过程结合在一起,降低了能耗和投资。由于采用固体酸催化剂代替通用的硫酸催化剂,可免除产物的中和过程。甲苯-苯甲酸法先将甲苯液相氧化为苯甲酸,苯甲酸再转化为苯酚。具有甲苯原料来源广泛、流程简单等优点。目前采用的异丙苯法存在联产大量丙酮(丙酮和苯酚产率比为:1)问题,同时苯酚需精制而耗用能源。现正在开发苯直接氧化制苯酚的一步反应法。日本研究人员开发了利用贵金属催化剂的一步法工艺。首诺(Solutia)公司开发了采用一氧化二氮为氧化剂使苯直接催化氧化为苯酚的一步法工艺。最近日本先进工业科技国家研究院(AIST)开发了由苯一步法合成苯酚工艺,而常规工艺从苯开始需三个步骤,并且产生需处埋的废酸。AIST的工艺使用不锈钢外管和多孔α-氧化铝内管组成的反应器,关键元件是厚1μm的钯膜催化剂,用化学蒸气沉积法涂复在氧化铝管的外侧。膜由AIST与丸善石化公司和NOK公司共同开发。反应器置于加热至150~250的加热炉内,苯和氧气流过氧化铝内管,压力的氢气沿管外侧通过。氢被吸附在膜上,在此被离解和活化,然后通过氧化铝管内表面,活化的氢捕集管子内表面上的氧分子,生成活化的氧,活化的氧与苯环的双键反应通过苯环氧化物由苯生成苯酚。实验室中,在转化率低于3%时,生成苯酚的选择性大于90%。10%~15%转化率时,选择性大于80%。苯酚产率为每千克催化剂千克/时,随着工艺过程的改进,预计转化率还可提高。
简述苯酚丙酮
简述苯酚丙酮 1.1概述 1.1.1设计基础 苯酚和丙酮是重要的化工原料。在我国,今年来的苯酚,丙酮市场相当活跃。 作为一种重要的有机原料,苯酚的用途相当广泛。它主要用于制造酚醛树脂,双酚A,环氧树脂,苯胺胶,烷基酚等,同时也广泛用于医药,染料,农药,合成洗涤剂等行业。丙酮既是优良的有机溶剂,广泛用于油脂,油漆,火药,树脂,橡胶,照相软片等,也是重要的化工原料之一,用于生产有机玻璃,异丙醇,溶剂,甲氨基丙烯酸甲酯,丙酮氰醇,双酚等。 近年来,受电子通讯工业,汽车工业和建筑业发展的驱动,我国苯酚-丙酮市场相当活跃。苯酚-丙酮的下游产品迅速发展,需求强劲增加。 异丙苯法是目前世界上最重要的苯酚-丙酮生产方法,其生产能力约占世界苯酚生产能力的90%以上。异丙苯法生产苯酚丙酮的工艺以苯和丙烯为原料,发生加成反应生成异丙苯,然后将异丙苯氧化为过氧化氢异丙苯(CHP),再由过氧化氢异丙苯分解生成苯酚和丙酮。 1.1.2生产规模 年产苯酚-丙酮20万吨,其中丙酮37%(7.4万吨),苯酚63%(12.6万吨)1.1.3设计方案确定 原理:异丙苯法生产苯酚丙酮的工艺以苯和丙烯为原料,发生加成反应生成异丙苯,然后将异丙苯氧化为过氧化氢异丙苯(CHP),再由过氧化氢异丙苯分解生成苯酚和丙酮。另外,流程还有反烃化,生成二异三异产物的副反应发生。 其涉及的主要反应:
工艺流程说明: 苯酚丙酮装置的精制单元由丙酮精制系统和苯酚精制系统组成。此外,还包括丙酮汽提塔,苯酚回收塔和酚处理器等设备。在送来的分解液中除含有苯酚,丙酮,异丙苯,溶解水以外,还有少量乙醛,苯乙酮等酮类、а—甲基苯乙烯(AMS)等烃类及高沸物。分解液精粗丙酮塔进行切割分离,富含丙酮的轻组分自塔顶采出,进入丙酮精制塔进行丙酮精制,并在侧线得到产品丙酮;而富含苯酚的重组分自粗丙酮塔塔底采出,经粗苯酚塔,脱烃塔和苯酚精制塔得到产品苯酚。 1.1.4工艺技术路线 该设计主要要求得到年产量为7.4万吨的丙酮产品。 所以,丙酮的生产工艺流程如下: A.丙酮精制 精馏进料首先从初丙酮塔塔顶丙酮、水和比苯酚轻的组分作为精丙酮塔的进料,精丙酮塔用苛性钠处理除去醛类等低沸物,塔顶馏出物作为分解用的丙酮,侧线采出产品丙酮,塔釜液送回回收工段回收其有效成分。 其简要流程图:
苯酚丙酮装置简介和重点部位及设备.docx
苯酚丙酮装置简介和重点部位及设备 一、装置简介 (一)装置发展及类型 1.装置发展 异丙苯法制备苯酚、丙酮是目前世界上获得苯酚、丙酮的主要技术路线,从20世纪50年代开始工业化到目前为止,世界上约90%的苯酚来自该路线,在世界苯酚工业中占主导地位,2002年世界苯酚产能约为720X104t/a,其中91%采用异丙苯法。 我国采用异丙苯法制备苯酚、丙酮始自20世纪60年代中期,国内第一套万吨级异丙苯法苯酚丙酮装置于1970年在燕化公司建成投产,1986年国内首套引进技术8X104t/a异丙苯 法苯酚丙酮装置在燕化公司建成投产,成为当时国内最大的苯酚丙酮生产装置。目前国内苯酚丙酮主要生产厂家有燕山石化、高桥石化、华字石化、吉林石化、广州建涛集团,所采用的工艺路线都是异丙苯法制备苯酚、丙酮。随着技术的不断发展、进步,苯酚丙酮装置生产规模不断扩大,目前国内单套装置最大产能为燕化公司16X104t/a苯酚丙酮装置,国内正在筹建的单套装置最大产能为20X104t/a。德国Ineos苯酚有限公司以生产能力为62.0X104t/a为世界之最。 随着催化剂和生产工艺的发展,大多数生产装置制取异丙苯工艺已从传统的AlCl3法转为固体磷酸或沸石催化法,我国四大生产厂家和正在筹建的生产装置皆采用后者。目前较先进的异丙苯制备苯酚工艺是
Allied/UOP工艺,由美国UOP公司和美国联合化学公司共同开发,全球已有11家苯酚生产厂家采用该工艺。 目前,世界许多生产厂家纷纷对苯酚的生产技术进行改进和开发新的生产工艺。通过对成熟的异丙苯制备苯酚工艺中催化剂和CHP分解、苯酚精制两个工艺的研究,朝着工艺路线更短,经济效益更好的方向发展。 2.装置的主要类型 异丙苯制备苯酚工艺分为三步: (1)苯和丙烯反应生成异丙苯,传统工艺为A1C13法,目前广泛使用的是沸石催化法,可采用气—液相法和液相法。 (2)异丙苯经氧气或空气氧化,生成过氧化氢异丙苯(CHP)。设备有塔式反应器和槽式反应器2种。 (3)CHP分解,生成苯酚和丙酮。反应工艺有一步分解和二步分解,又可有正压分解和负压分解。 (二)装置工序组成与工艺流程 1,装置工序组成 异丙苯法制备苯酚丙酮装置的基本工序为:烃化工序、氧化工序、精制工序、回收工序。 (1)烃化工序 苯与丙烯混合进入烃化反应器,在催化剂作用下进行烃化反应,生成异丙苯。反应生成的烃化液通过精馏得到成品异丙苯送至储罐,为下一道工序的原料。过程中废弃物烃化尾气排入火炬系统焚烧;副产物
年产1万吨异丙苯反应及烃化液工艺设
年产1万吨异丙苯反应及烃化液工艺设计 【摘要】苯酚是重要的有机合成原料之一。丙酮也是一种重要的有机合成化工原料,广泛应用于醋酸纤维素、无烟火药、油漆、涂料和药物方面,它还是一种良好的溶剂。天然丙酮满足不了经济发展的需要,大多合成。制备丙酮的方法有多种,如异丙醇法、发酵法、异丙苯法等。目前,异丙苯法是生产苯酚和丙酮的最主要的方法。本设计是年产1万吨的异丙苯反应及烃化液后处理工艺设计,设计年产量1万吨,年开工7200小时,设计反应压力0.12MPa,设计反应温度95℃。通过计算求得装置的产量等具体参数,并计算出所需设备的型号以及具体参数。【关键词】异丙苯烃化反应后处理
目录 引言 (1) 1、技术论述 (2) 1.1生产方法的选择 (2) 1.1.1苯酚生产方法的比较 (3) 1.1.2丙酮生产方法的比较 (6) 1.2工艺流程的评述与确定 (7) 1.2.1催化剂的选择 (8) 1.2.2烃化反应器的选择 (8) 1.2.3烃化反应产物的后处理 (9) 1.2.4三废处理 (10) 1.3工艺条件的论述与确定 (11) 1.3.1配料比 (11) 1.3.2反应压力 (11) 1.3.3反应温度 (11) 1.4工艺流程叙述 (12) 1.4.1烃化反应 (12) 1.4.2尾气处理 (12) 1.4.3烃化液的处理 (12) 1.5安全环保措 (13) 1.5.1 安全措施 (13) 1.5.2 三废处理 (13) 2、工艺设计计算 (14) 2.1物料衡算 (15) 2.1.1烃化塔物料衡算 (15) 2.1.2烃化塔气液分离计算 (19) 2.1.3第一尾气冷凝器的物料衡算 (22) 2.2热量衡算 (25) 2.2.1烃化塔的热量衡算 (26) 2.2.2第一尾气冷凝器热量衡算 (28)
苯酚的生产工艺与技术路线的选择
苯酚的生产工艺与技术路线的选择 2.1 苯酚生产工艺 在第一次世界大战以前,苯酚主要从煤焦油中提炼获得。目前苯酚的生产主要有七种方法,即异丙苯法、甲苯氧化法、苯直接氧化法、磺化法、氯苯水解法、拉西法、环己烷法等。除甲苯氧化法以甲苯为原料外,其余六种方法均以苯为原料。 2.1.1 异丙苯法 异丙苯法也叫异丙苯氧化法,…… 2.1.2 甲苯氧化法 甲苯氧化法也称甲苯-苯甲酸法,此法是唯一一种不用苯作原料合成苯酚的方法。…… 2.1.3 苯直接氧化法 苯直接氧化法是以苯为原料,直接氧化制取苯酚的方法,也称苯羟基化法。…… 2.1.4 磺化法 ……
2.1.5 氯苯水解法 …… 2.1.6 拉西法 …… 2.1.7 环己烷法 …… 2.2 苯酚生产工艺研究及进展 第一次世界大战以前,苯酚主要从煤焦油中提炼得到,随着苯酚需求量的不断增加,人们开始采用化学合成法生产苯酚。 最早的苯酚化学合成工艺是1923年由美国孟山都公司首次研究开发成功的苯磺化法,即由苯经磺化生产苯磺酸钠,再经水解得到苯酚。由于该方法腐蚀性强以及污染严重等原因,目前已经基本上被淘汰。此后又相继出现了氯苯法、甲苯氧化法、拉西法、环己烷法、异丙苯法以及苯直接氧化法等生产方法。 …… 2.2.1 异丙苯法的工艺改进及进展 对于异丙苯法苯酚生产工艺的改进主要集中在氧化工序的节能降耗、完善CHP提浓和分解工序等方面。 …… 2.2.2 苯直接氧化法的研究进展 ……
2.2.3 磺化法的研究进展 …… 2.2.4 Shell公司“Spam”新工艺 …… 2.3 苯酚生产工艺研究方向 传统的合成苯酚的方法存在浪费原料、副产物多、不利于环保等缺点。 …… 2.4 苯酚几种工艺路线的技术经济比较 目前,世界苯酚的生产主要是异丙苯法,还有甲苯氧化法、苯直接氧化法、磺化法、氯苯水解法等。几种苯酚生产工艺的原料消耗对比见下表。 表2.1 几种苯酚生产工艺的原料消耗对比表 表2.2 几种苯酚生产工艺的公用工程消耗对比表 2.5 苯酚生产工艺路线的选择 经过几十年的生产实践,优胜劣汰,有些路线尽管在世界上曾实现了工业化,但由于种种原因而逐渐被淘汰了。在国外,…… 2.6 苯酚质量指标 目前我国苯酚执行中华人民共和国国家标准GB/T339-2001,该标准是等效采用美国试验与材料协会标准ASTMD 2439-1996《精制苯酚》对GB339-1989工业合成苯酚的修订。 表2.3 苯酚质量指标表