轴承套圈的贝氏体淬火简介
关于贝氏体

关于贝氏体:(1)上贝氏体为过冷奥氏体在550~400℃温区等温形成的一种组织,由铁素体和渗碳体组成,在光学显微镜下观察,呈羽毛状。
上贝氏体常沿奥氏体晶界形核,向晶内发展。
从电子显微照片上可以看到:在平行的铁素体条间有短棒状或串珠状渗碳体断续分布,其硬度为35~45HRC。
上贝氏体的铁素体内含有一定程度的过饱和碳量,具有体心立方点阵,与奥氏体保持严格的晶格学位向关系,过去认为是西山关系,进一步研究证明为K-S关系,其惯习面为(111)A。
在磨光的试样表面呈现浮凸。
上贝氏体机械性能低劣,使用价值不大。
(2)下贝氏体下贝氏体为过冷奥氏体于400~200℃温区形成的一种组织。
其组织形态与上贝氏体明显不同,类似于片状马氏体的回火组织。
在光学显微镜下呈黑色片状(针状或竹叶状),互成一定角度。
在电子显微镜下观察或X 射线结构分析:这种组织乃是由过饱和α固溶体与其长轴成50~60o角度分布的碳化物质点形成。
其硬度为45~50HRC。
双面金相分析表明:下贝氏体铁素体的立体形态为双凸镜状。
下贝氏体铁素体具有较高的碳过饱和度,有的含碳量高达0.2%,晶体结构为体心立方点阵。
其内部析出的碳化物不是渗碳体,而是ε相(Fe2.4C),属六方晶系。
下贝氏体中铁素体与母相奥氏体保持严格的晶体学位向关系(K-S关系),惯习面为(225)A。
其亚结构为高密度位错,在磨光的试样表面亦呈现浮凸。
可见,下贝氏体形成亦具有切变特征。
下贝氏体具有优良的强韧性,硬度和耐磨性也很高,缺口敏感性和脆性转变温度较低,是一种理想的淬火组织,具有很高的实用价值。
因此,以获得这种组织为目的的等温淬火工艺,在生产中得到了广泛的应用。
上贝氏体的渗碳体是以片状分布在界面,很大程度上降低了材料的塑性和韧性,而下贝氏体中的渗碳体则是以弥散的质点相分布在基体中,有很到的强韧性,所以通常为得到下贝氏体组织。
等温淬火法将加热的工件放入温度稍高于Ms点的硝盐浴或碱浴中,保温足够长的时间使其完成贝氏体转变,获得下贝氏体组织。
钢的淬火介绍

钢的淬火介绍
淬火是将钢件加热到Ac3(亚)或Ac1(过)以上30-50℃,经过保温,然后在冷却介质中迅速冷却,以获得高硬度组织的一种热处理工艺。
其目的在于提高材料的硬度和耐磨性,常应用于工具、模具、量具和滚动轴承的制造。
淬火后的组织为马氏体、下贝氏体。
淬火工艺中淬火冷却速度决定了材料的质量,理想的冷却速度是两头慢中间快,以便减少内应力。
1 常用淬火法
1)单液淬火(普通淬火)
在一种淬火介质中连续冷却至室温,如碳钢水冷。
缺点: 水冷,易变形,开裂.。
油冷:易硬度不足,或不均。
优点: 易操作,易自动化。
2)双液淬火
先在冷却能力较强的介质中冷却到300℃左右,再放入冷却到冷却能力较弱的介质中冷却,获得马氏体。
对于形状的碳钢件,先水冷,后空冷。
优点: 防低温时M相变开裂。
3)分级淬火
工件加热后迅速投入温度稍高于Ms点的冷却介质中,(如言浴火碱浴槽中)停2-5分(待表面与心部的温差减少后再取出)取出空冷。
应用:小尺寸件(如刀具淬火) 防变形,开裂。
优点: 工艺简单,操作容易。
缺点:在盐浴中冷却,速度不够大,只适合小件。
4)等温淬火
将加热后的钢件放入稍高于Ms温度的盐浴中保温足够时间, 使。
老师傅经验分享:预防和控制轴承套圈淬火变形、开裂、胀缩

老师傅经验分享:预防和控制轴承套圈淬火变形、开裂、胀缩作者:范仲和,在洛阳轴承厂技术中心从事金属材料和热工工艺研究及轴承失效分析工作,有着40多年的工作经验。
《金属加工》资深专家、作者。
来源:《金属加工(热加工)》杂志这篇文章主要分析了轴承套圈淬火变形、开裂、胀缩的产生原因和预防措施。
轴承钢套圈淬、回火后的变形和尺寸胀缩一直影响着热处理产品质量。
近年来,轴承行业热处理应用了贝氏体、马氏体与贝氏体的复合淬火新工艺,因淬火后套圈变形、开裂及胀缩量难以控制,同一批产品胀缩量忽大忽小差别较大,产品合格率较低,只能采取增大下一工序磨削加工的留量来满足产品的胀缩量,这样既浪费了材料也消耗了人工工时,所以有些企业只能放弃先进的贝氏体淬火工艺改回原马氏体淬火。
轴承钢套圈淬火变形、开裂、胀缩量产生的原因受很多因素影响,是一个相当复杂的问题。
下面分别讨论这些缺陷的产生原因及其应采取的解决办法。
1.淬火变形、开裂和尺寸胀缩轴承钢套圈在淬火时材料中的应力未达到弹性极限,材料只发生弹性变形,应力超过弹性极限而低于材料的强度极限时,则发生塑性变形;应力达到强度极限,材料就发生断裂。
因此,材料的变形和开裂是在应力大小和材料的性能指标两个因素作用下发生的。
淬火过程不可避免要出现淬火应力,包括热应力和组织应力。
在操作过程中还可能带来零件机械的碰撞产生应力,这些应力分布不均匀,在应力集中处可能比平均应力大许多倍;同时,由于材质的不均匀性和材料缺陷,使其各部位的强度指标也能悬殊许多倍,而且在材质薄弱处也往往正是应力集中处,因此,应力超过材料强度极限则发生局部断裂,亦即裂纹。
由于淬火应力和体积变化,引起零件各部分尺寸均匀变化而不改变零件形状,称尺寸胀缩。
由于不均匀的淬火应力,而使零件形状改变者,即常说的淬火变形。
套圈的径向不均匀变形大小(长、短轴之差值),通常叫套圈的椭圆度;套圈的轴向不均匀变形,通常叫翘曲变形(见图1),轴向均匀变形叫蝶形变形(见图2)。
轴承套圈冷处理工艺
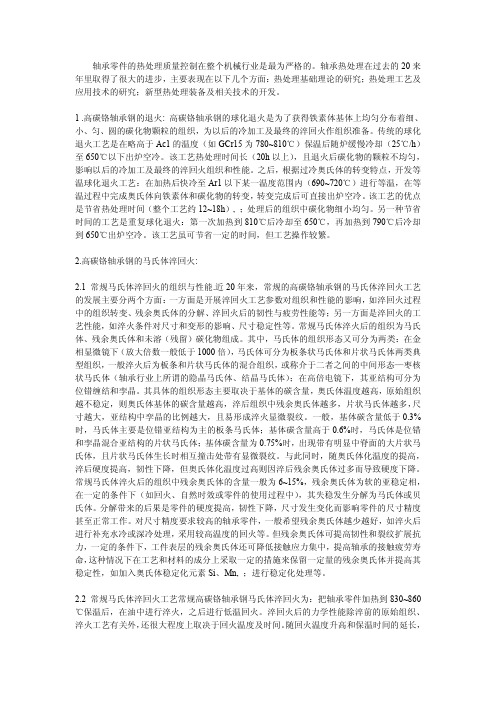
轴承零件的热处理质量控制在整个机械行业是最为严格的。
轴承热处理在过去的20来年里取得了很大的进步,主要表现在以下几个方面:热处理基础理论的研究;热处理工艺及应用技术的研究;新型热处理装备及相关技术的开发。
1.高碳铬轴承钢的退火:高碳铬轴承钢的球化退火是为了获得铁素体基体上均匀分布着细、小、匀、圆的碳化物颗粒的组织,为以后的冷加工及最终的淬回火作组织准备。
传统的球化退火工艺是在略高于Ac1的温度(如GCr15为780~810℃)保温后随炉缓慢冷却(25℃/h)至650℃以下出炉空冷。
该工艺热处理时间长(20h以上),且退火后碳化物的颗粒不均匀,影响以后的冷加工及最终的淬回火组织和性能。
之后,根据过冷奥氏体的转变特点,开发等温球化退火工艺:在加热后快冷至Ar1以下某一温度范围内(690~720℃)进行等温,在等温过程中完成奥氏体向铁素体和碳化物的转变,转变完成后可直接出炉空冷。
该工艺的优点是节省热处理时间(整个工艺约12~18h),;处理后的组织中碳化物细小均匀。
另一种节省时间的工艺是重复球化退火:第一次加热到810℃后冷却至650℃,再加热到790℃后冷却到650℃出炉空冷。
该工艺虽可节省一定的时间,但工艺操作较繁。
2.高碳铬轴承钢的马氏体淬回火:2.1常规马氏体淬回火的组织与性能.近20年来,常规的高碳铬轴承钢的马氏体淬回火工艺的发展主要分两个方面:一方面是开展淬回火工艺参数对组织和性能的影响,如淬回火过程中的组织转变、残余奥氏体的分解、淬回火后的韧性与疲劳性能等;另一方面是淬回火的工艺性能,如淬火条件对尺寸和变形的影响、尺寸稳定性等。
常规马氏体淬火后的组织为马氏体、残余奥氏体和未溶(残留)碳化物组成。
其中,马氏体的组织形态又可分为两类:在金相显微镜下(放大倍数一般低于1000倍),马氏体可分为板条状马氏体和片状马氏体两类典型组织,一般淬火后为板条和片状马氏体的混合组织,或称介于二者之间的中间形态—枣核状马氏体(轴承行业上所谓的隐晶马氏体、结晶马氏体);在高倍电镜下,其亚结构可分为位错缠结和孪晶。
gcr15钢制圆锥滚子轴承套圈的热处理工艺
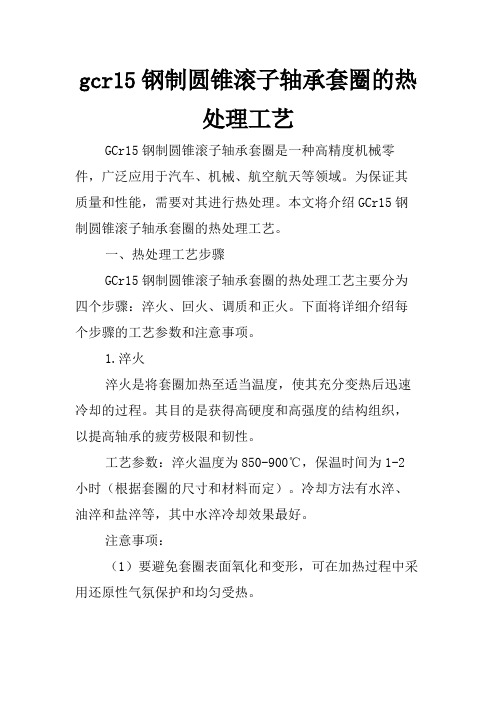
gcr15钢制圆锥滚子轴承套圈的热处理工艺GCr15钢制圆锥滚子轴承套圈是一种高精度机械零件,广泛应用于汽车、机械、航空航天等领域。
为保证其质量和性能,需要对其进行热处理。
本文将介绍GCr15钢制圆锥滚子轴承套圈的热处理工艺。
一、热处理工艺步骤GCr15钢制圆锥滚子轴承套圈的热处理工艺主要分为四个步骤:淬火、回火、调质和正火。
下面将详细介绍每个步骤的工艺参数和注意事项。
1.淬火淬火是将套圈加热至适当温度,使其充分变热后迅速冷却的过程。
其目的是获得高硬度和高强度的结构组织,以提高轴承的疲劳极限和韧性。
工艺参数:淬火温度为850-900℃,保温时间为1-2小时(根据套圈的尺寸和材料而定)。
冷却方法有水淬、油淬和盐淬等,其中水淬冷却效果最好。
注意事项:(1)要避免套圈表面氧化和变形,可在加热过程中采用还原性气氛保护和均匀受热。
(2)选用适当淬火介质,控制淬火速度和温度,以保证套圈的组织和硬度均匀。
2.回火回火是将淬火后的套圈加热至中温(通常在250-450℃之间)保温一段时间后冷却的过程。
其主要目的是调节淬火后套圈的硬度和韧性。
工艺参数:回火温度根据需求而定,通常在200-400℃。
保温时间可根据套圈的尺寸和厚度而定,一般为1-2小时。
冷却方式一般自然冷却即可。
注意事项:(1)回火时间和温度要适当,过长或过短都会影响套圈的性能。
(2)要避免回火过度导致套圈的硬度和强度下降。
3.调质调质是将回火后的套圈再次淬火并再次回火来达到优化微观组织的目的,同时使其保持高硬度的同时提高韧性。
工艺参数:调质温度根据需求而定,通常在500-650℃。
保温时间一般为1-2小时。
淬火介质通常选择油淬。
回火温度和时间要根据套圈的尺寸和厚度而定,一般在200-400℃下进行,保温时间为1-2小时。
注意事项:(1)保证套圈淬火均匀,避免质量差异。
(2)回火过程中要避免过度回火,导致硬度和强度下降,降低轴承寿命。
4.正火正火是将套圈加热至适当温度(一般在840-900℃之间),保温一段时间后进行自然冷却。
轴承钢的热处理

轴承钢的热处理
轴承钢是用于制造轴承零件的一种特殊钢材,具有高强度、高硬度和良好的耐磨性能。
对于工艺,是非常重要的工艺环节,直接影响到轴承零件的性能和使用寿命。
轴承钢的热处理主要包括回火、淬火、正火等工艺。
在制造轴承零件时,必须根据不同的要求和工件的结构,选择适当的热处理工艺。
下面介绍一下轴承钢的热处理工艺及其影响。
回火是热处理工艺的一种,主要是通过加热和保温,使材料内部的应力得以释放,晶粒尺寸适当调整,提高材料的韧性和耐磨性。
回火工艺中,需要根据具体情况选择适当的回火温度和时间,以及冷却方式,以保证材料的性能。
淬火是轴承钢热处理工艺中的一种重要工艺,通过将材料加热至适当的温度后急冷,使其快速冷却,使组织变质,提高硬度和强度。
淬火工艺对材料性能的影响很大,需要根据具体要求选择适当的淬火温度和时间,以及冷却介质。
正火是轴承钢热处理中的另一种重要工艺,通过加热材料至适当的温度后保温,使组织发生调整,提高材料的韧性和强度。
正火工艺也需根据要求选择适当的温度和时间,以及冷却方式。
除了以上几种热处理工艺外,还有一些特殊的热处理方法,如表面强化热处理、渗碳热处理等,这些方法可以进一步提高轴承钢的性能,延长使用寿命。
总的来说,轴承钢的热处理对于提高材料的性能和使用寿命至关重要。
在制造轴承零件时,必须根据具体要求和工件的结构选择适当的热处理工艺,确保材料具有理想的性能,满足使用要求。
同时,在热处理过程中,需要严格控制各项参数,确保热处理效果达到最佳。
只有这样,才能保证轴承钢的质量和可靠性,真正发挥轴承零件的作用。
大功率风电轴承用纳米贝氏体钢化学成分设计与组织性能调控

大功率风电轴承用纳米贝氏体钢化学成分设计与组织性能调控本文依托国家863课题,对大功率风电主轴轴承用贝氏体渗碳钢的热处理工艺进行了优化,并进一步优化了化学成分。
对最终优化出的主轴轴承圈用G23Cr2Ni2Si1Mo钢表面和心部的组织及性能进行了详细研究,并与经典的马氏体渗碳钢G20Cr2Ni4的组织和性能做了对比;研究了高碳纳米贝氏体轴承钢的显微组织,并探讨了轴承钢中未溶碳化物对纳米贝氏体相变的影响;研究了渗碳及高碳纳米贝氏体钢的滚动接触疲劳性能及其影响因素。
通过对G20Cr2Ni4SiMo 钢和G20Cr2Ni2SiMoAl钢渗碳后调质球化退火、表层组织和硬度以及心部力学性能的研究,最终优化出风电主轴轴承用贝氏体渗碳钢的球化退火工艺,并进一步优化了化学成分,最终确定了主轴轴承套圈可选用材料及热处理工艺。
渗碳合金钢G23Cr2Ni2Si1Mo,经渗碳淬火、高温回火及最终二次淬火(低温等温淬火)后,表面层获得了包含纳米贝氏体、马氏体、未溶球状碳化物及残余奥氏体的混合组织。
低温等温淬火试样与传统油淬试样做了对比。
结果表明,等温淬火试样比油淬试样获得了更高的表面残余压应力及较厚的表层残余压应力层,并且200oC等温4 h,8 h及24 h试样的表面耐磨性比油淬试样分别高40%,58%和12%,此外等温淬火试样心部冲击韧性比传统油淬试样提高了20.8%-33.3%。
对比研究了纳米贝氏体渗碳钢G23Cr2Ni2Si1Mo钢和马氏体渗碳钢G20Cr2Ni4的组织和性能。
结果表明,G23Cr2Ni2Si1Mo钢经渗碳及随后的在200?C低温等温淬火后,表层得到了纳米贝氏体和弥散分布的未溶碳化物颗粒。
与传统马氏体渗碳钢G20Cr2Ni4相比,贝氏体渗碳钢G23Cr2Ni2Si1Mo展现出更好的耐磨性和更高的滚动接触疲劳性能。
此外,G23Cr2Ni2Si1Mo钢的淬透性和综合力学性能均优于G20Cr2Ni4钢。
研究了新设计的高碳纳米贝氏体轴承钢GCr15Si1Mo的组织,并着重研究了该钢未溶碳化物对纳米贝氏体相变的影响,结果表明:GCr15Si1Mo钢经低温等温淬火处理后,得到由纳米贝氏体、马氏体、未溶碳化物和残余奥氏体组成的混合组织。
轴承钢球采用的热处理方法
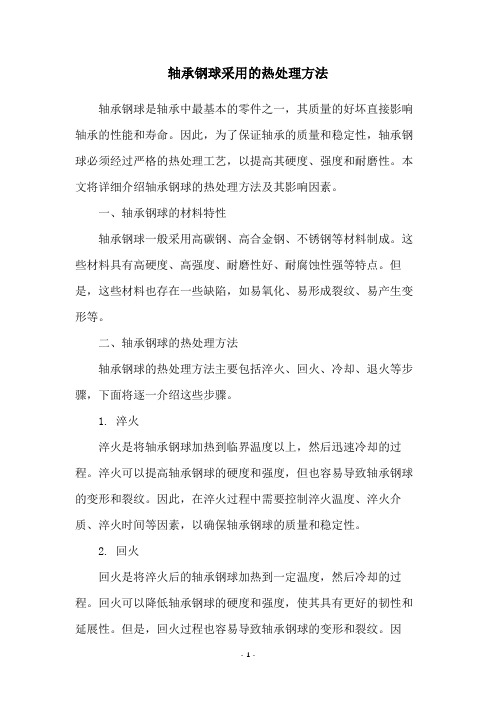
轴承钢球采用的热处理方法轴承钢球是轴承中最基本的零件之一,其质量的好坏直接影响轴承的性能和寿命。
因此,为了保证轴承的质量和稳定性,轴承钢球必须经过严格的热处理工艺,以提高其硬度、强度和耐磨性。
本文将详细介绍轴承钢球的热处理方法及其影响因素。
一、轴承钢球的材料特性轴承钢球一般采用高碳钢、高合金钢、不锈钢等材料制成。
这些材料具有高硬度、高强度、耐磨性好、耐腐蚀性强等特点。
但是,这些材料也存在一些缺陷,如易氧化、易形成裂纹、易产生变形等。
二、轴承钢球的热处理方法轴承钢球的热处理方法主要包括淬火、回火、冷却、退火等步骤,下面将逐一介绍这些步骤。
1. 淬火淬火是将轴承钢球加热到临界温度以上,然后迅速冷却的过程。
淬火可以提高轴承钢球的硬度和强度,但也容易导致轴承钢球的变形和裂纹。
因此,在淬火过程中需要控制淬火温度、淬火介质、淬火时间等因素,以确保轴承钢球的质量和稳定性。
2. 回火回火是将淬火后的轴承钢球加热到一定温度,然后冷却的过程。
回火可以降低轴承钢球的硬度和强度,使其具有更好的韧性和延展性。
但是,回火过程也容易导致轴承钢球的变形和裂纹。
因此,在回火过程中需要控制回火温度、回火时间等因素,以确保轴承钢球的质量和稳定性。
3. 冷却冷却是将轴承钢球从高温状态迅速冷却的过程。
冷却可以降低轴承钢球的温度,使其达到淬火的要求。
但是,过快的冷却速度也容易导致轴承钢球的变形和裂纹。
因此,在冷却过程中需要控制冷却介质、冷却时间等因素,以确保轴承钢球的质量和稳定性。
4. 退火退火是将轴承钢球加热到一定温度,然后缓慢冷却的过程。
退火可以消除轴承钢球的应力,使其达到更好的塑性和韧性。
但是,过度的退火也容易导致轴承钢球的变形和裂纹。
因此,在退火过程中需要控制退火温度、退火时间等因素,以确保轴承钢球的质量和稳定性。
三、轴承钢球热处理的影响因素轴承钢球的热处理质量和稳定性受到多种因素的影响,下面将逐一介绍这些因素。
1. 材料成分轴承钢球的材料成分对热处理质量和稳定性有着重要的影响。
- 1、下载文档前请自行甄别文档内容的完整性,平台不提供额外的编辑、内容补充、找答案等附加服务。
- 2、"仅部分预览"的文档,不可在线预览部分如存在完整性等问题,可反馈申请退款(可完整预览的文档不适用该条件!)。
- 3、如文档侵犯您的权益,请联系客服反馈,我们会尽快为您处理(人工客服工作时间:9:00-18:30)。
3 贝氏体等温淬火
3.1 贝氏体淬火的组织与力学性能
高碳铬轴承钢经下贝氏体淬火后,其组织由下贝氏体、马氏体和残余碳化物组成。
其中贝氏体为不规则相交的条片,条片为碳过饱和的α结构,其上分布着与片的长轴成55~60°的粒状或短杆状的碳化物,空间形态为凸透镜状,亚结构为位错缠结,未发现有孪晶亚结构。
贝氏体的数量及形态因工艺条件不同而各异。
随淬火温度的升高,贝氏体条变长;等温温度升高,贝氏体条变宽,碳化物颗粒变大,且贝氏体条之间的相交的角度变小,逐趋向于平行排列,形成类似与上贝氏体的结构;贝氏体转变是一个与等温转变时间有关的过程,等温淬火后的贝氏体量随等温时间的延长而增加[5,19]。
高碳铬轴承钢下贝氏体组织能提高钢的比例极限、屈服强度、抗弯强度和断面收缩率,与淬回火马氏体组织相比,具有更高的冲击韧性、断裂韧性及尺寸稳定性,表面应力状态为压应力。
高的门坎值ΔKth和低的裂纹扩展速度da/dN则代表贝氏体组织不易萌生裂纹,已有的裂纹或新萌生的裂纹也不易扩展[2,19,20]。
一般认为,全贝氏体或马/贝复合组织的耐磨性和接触疲劳性能低于淬火低温回火马氏体,与相近温度回火的马氏体组织的耐磨性和接触疲劳性能相近或略高。
但润滑不良条件下(如煤浆或水这类介质),全BL 组织呈现出明显的优越性,具有比低温回火的M组织还要高的接触疲劳寿命,如水润滑时全BL组织的L10=168h,回火M组织的
L10=52h[21]。
3.2生产应用
3.2.5应用效果
BL组织的突出特点是冲击韧性、断裂韧性、耐磨性、尺寸稳定性好,表面残余应力为压应力。
因此适用于装配过盈量大、服役条件差的轴承,如承受大冲击负荷的铁路、轧机、起重机等轴承,润滑条件不良的矿山运输机械或矿山装卸系统、煤矿用轴承等。
高碳铬轴承钢BL 等温淬火工艺已在铁路、轧机轴承上得到成功应用,取得了较好效果。
(1)扩大了GCr15钢应用范围,一般地GCr15钢M淬火时套圈有效壁厚在12mm以下,但BL淬火时由于硝盐冷却能力强,若采用搅拌、串动、加水等措施,套圈有效壁厚可扩大至28mm左右。
(2)硬度稳定、均匀性好:由于BL转变是一个缓慢过程,一般GCr15钢需4h,GCr18Mo钢需5h,套圈在硝盐中长时间等温,表面心部组织转变几乎同时进行,因此硬度稳定、均匀性好,一般GCr15钢BL淬火后硬度在59~61HRC,均匀性≤1HRC,不象M 淬火时套圈壁厚稍大一些就出现硬度低、软点、均匀性差等问题。
(3)减少淬火、磨削裂纹:在铁路、轧机轴承生产中,由于套圈尺寸大、重量重,油淬火时M组织脆性大,为使淬火后获得高硬度常采取强冷却措施,结果导致淬火微裂纹;由于M淬火后表面为拉应力,在磨加工时磨削应力的叠加使整体应力水平提高,易形成磨削裂纹,造成批量废品。
而BL淬火时,由于BL组织比M组织韧性好得多,同时表面形成高达-400~-500MPa的压应力,极大地减小了淬火裂纹
倾向[19];在磨加工时表面压应力抵消了部分磨削应力,使整体应力水平下降,大大减少了磨削裂纹。
(4)轴承使用寿命提高:对于承受大冲击载荷的铁路、轧机轴承等,经M淬火后使用时主要失效形式为:装配时内套开裂,使用过程中受冲击外圈挡边掉块、内圈碎裂,而等温淬火轴承由于冲击韧性好、表面压应力,无论装配时内套开裂,还是使用过程中外套挡边掉块、内套碎裂倾向性大大减小,且可降低滚子的边缘应力集中。
因此,经等温淬火后比M淬火后平均寿命及可靠性提高。
SKF公司把高碳铬轴承钢贝氏体等温淬火工艺主要应用于铁路轴承、轧机轴承以及在特殊工况下使用的轴承,同时开发了适合于贝氏体淬火的钢种(SKF24、SKF25、100Mo7)[19]。
其淬火时采用较长的等温时间,淬后得到全下贝氏体组织。
近来SKF又研制出一种新钢种775V[22],并通过特殊的等温淬火得到更均匀的下贝氏体,淬后硬度增加的同时其韧性比常规等温淬火提高60%,耐磨性提高了3倍,处理的套圈壁厚超过100mm。
部分等温后得到M/BL复合组织的性能尚有争议,如BL的含量多少为最佳等。
即使有一最佳含量,在生产实际中如何控制,且复合组织在等温后还需进行一次附加回火,增加了生产成本。
FAG公司主要采用贝氏体分级淬火工艺,其具体的工艺状况不详。