辊压机联合粉磨系统的调试及生产经验
挤压联合粉磨系统调试及生产体会

辊 压 机 小 仓
辊 压 机 打 散 分 级 机 磨 机
2 4 x 90 仓 容3 m 9024 0
HF G1 0 8 人料 粒 度  ̄ 8 m 动静 辊 电机 功 率 5 o W , 力 30 3 0/ 系统 压 力70 9O a C  ̄0 4 < 0m 0k 能 0 ~6t h .~ .MP
,
改进 , 比如 : 备 的角 度 安 装 调整 、 标 溜 子 的 耐磨 设 非
为 出磨 水泥 的质 量 稳定 奠定 了良好 的物 质 基础
设 备名 称
规 格 型 号
.
主 要 技 术 性 能
出辊 压 机 提 升 机 N 3 0 3 .5 E 0 x 5 功 率7 k 能 力3 0 9 5W 2 m/ h
为二期丁程的安装 、 调试 、 生产奠定 了良好的理论基础 。
1 . 组 织 分 2 科 学 2 1 2
由 于一 期 我 们 对 这 个 系 统 的操 作 比较 了解 在
.
二 期 凋试 中 ,我们 就 有 针 对性 的对 它改 动 的 部分 进
行 了研 究 : 大 的 改进 一 是 将磨 头 磨尾 收 尘 器分 开 较
泥 制 备 系统 采 用 的是 挤 压联 合 高 产 高细 开 路粉 磨 系
统 , 20 于 0 7年 7月 份 下 旬 一 次 带 料 试 车 成 功 , 过 五 经
置 是 否 有利 于 今 后 检修 等 ‘ .都 由专人 与 安装 公 面
司 沟 通 、 更 。 时 , 要 监 督 安 装 的 进 度 质 量 等方 变 同 还
南HF G 4 x 5增 加 到 HF G 4 x 0 即 辊 压 机 的 棍 C 10 6 C 10 8
辊压机生料终粉磨系统的生产调试及应用

辊压机生料终粉磨系统的生产调试及应用作者:吴君山么化民来源:《科技创新与应用》2013年第02期摘要:牡丹江北方水泥有限公司,其2#窑是由原牡丹江水泥厂自行设计的日产1848t/d熟料的预分解窑,生料制备为两台带烘干机的Φ3.0m×11m闭路磨系统,台时产量130t/h。
由于原生料制备系统产量低、出磨质量差、能耗高等问题,我单位引进一套Φ1800×1000生料辊压机终粉磨系统,台时产量200t/h。
现将该系统调试中出现的问题及解决方法与同仁分享。
关键词:辊压机;生产调试;应用1 工艺流程及主机设备表1.1 工艺流程简述从配料站来的混合料由胶带输送机(01)送至生料粉磨车间,胶带输送机上悬挂除铁器(02),将物料中混入的铁件除去;同时该皮带上装有金属探测器(03),发现有金属后气动三通阀(04)换向,将混有金属的物料由旁路卸出,以保证辊压机的安全运行。
不含金属的物料由气动三通经锁风阀(05)喂入V型选粉机(06),在V型选粉机中预烘干后,通过提升机(07)提升进入稳流仓(08),该稳流仓设有荷重传感器检测仓内料位,物料从稳流仓过饱和喂入辊压机(11)进行料床粉碎的挤压过程,挤压后料饼通过提升机(12)送入V型选粉机中打散、烘干、分级,细小颗粒被热风分选出来,粗颗粒与新喂入的混合料一同进入循环挤压过程。
V型选粉机中被打散分选出来的细颗粒被热风带至热风管道内继续烘干后进入XR选粉机(13),通过笼型转子进行分选,粗粉通过双层重锤锁风阀(13a)卸出至稳流仓(08)后继续挤压,选出的生料成品通过旋风除尘器(14)气料分离后,通过双层重锤锁风阀(14a)卸入生料成品输送斜槽(16)入生料库。
生料烘干热源来自窑尾废气,可通过电动阀门(20)控制窑尾热风量,同时冷风阀(21)可控制掺入冷风量,以控制入V型选粉机的热风温度。
生料磨系统含尘废气由旋风筒(14)经循环风机(15)排出后,一部分经调节阀(18)循环回V型选粉机进风管,大部分进入窑尾废气处理电收尘器(22),除尘净化后由风机排入大气。
辊压机联合粉磨系统介绍

110
水泥联合粉磨系统(双斗提机方案)
1. 水泥配料和V选的粗粉,用一台斗提机送入中 间仓; 2. 中间仓的物料进入辊压机挤压;挤压后的料 饼,单独用一台斗提机送入送入V型选粉机,进 行分选; 3. 细粉随风带入旋风筒收集入磨,粗粉循环挤 压; 4. 气流经循环风机返回V型选粉机进风口。 5. 进V选的溜子上设溜管除铁器和旁路三通阀; 6. 粉煤灰直接加入磨头或磨尾; 7. 球磨系统采用闭路系统,分选采用高效涡流 选粉机; 8. 磨内通风单独设除尘器和风机,方便调整磨 内通风量。
粉机,系统更简化、更节能; 2. 辊压机料饼中的一部分达到成品粒度的
细粉,经涡流选粉机直接分选为成品,一方面 增加了系统的能力,另一方面减少磨内过粉磨 现象。
3. 选粉风大部分循环,可以减少外排粉尘 总量。
因此,半终粉磨系统更能体现出节能和环保。
1. 系统能力不大时,可以采用单斗提方案,V型选粉机也 可以布置在中间仓顶部。 2. 磨机可以采用单仓磨。
❖ 2. 系统阻力小:
❖ 立磨系统在喷吹环处阻力很大,因此风机全压约10~11kPa;辊压机系
统仅为6~6.5kPa。
❖ 3. 系统节能,烘干能力弱:
❖ 立磨系统主风机装机功率3600~3800kW,辊压机系统循环风机功率
仅1600~1800kW。两者相差2000kW。
❖ 辊压机系统的风量仅为立磨系统的70%~75%,在相同的热源温度情 况下,辊压机系统的烘干能力较弱。在带余热发电情况下,最大烘干水分小 于5%。
❖ 2. 磨得细:
❖ 原料的易磨性、辊压机的选型、入辊压机综合水分等因素。
❖
辊压机的规格起决定作用。
❖ 3. 选得出:
❖ 烘干后细粉的水分、颗粒的分散性、选粉机的选型等因素。
辊压机联合粉磨工艺系统分析

辊压机联合粉磨工艺系统分析辊压机联合粉磨(或半终粉磨)工艺系统,其技术核心在本质上属于“分段粉磨”。
目前,国内水泥制成工序广泛应用由辊压机+打散分级机(动态分级设备)或V型选粉机(静态分级设备)+管磨机开路(或配用高效选粉机组成双闭路)组成的联合粉磨工艺系统(或由辊压机+V型选粉机(静态分级设备)+高效选粉机+管磨机组成的半终粉磨工艺系统),在实际运行过程中,由于各线生产工艺流程及设备配置、物料粉磨特性、水份等方面因素不尽相同,导致系统产量、质量及粉磨电耗等技术经济指标也参差不齐,本文拟对水泥联合粉磨单闭路(管磨机为开路)及双闭路系统(或半终粉磨系统)中各段常出现的工艺技术与设备故障模式进行探讨分析,并提出了相应的解决办法,仅供粉磨工程技术人员在日常工作中参考,文章中谬误之处恳望予以批评指正:一、辊压机系统故障模式:辊压机挤压效果差故障原因1:1. 被挤压物料中的细粉过多,辊压机运行辊缝小,工作压力低影响分析:辊压机作为高压料床(流动料床)粉磨设备,其最大特点是挤压力高(>150Mpa),粉磨效率高,是管磨机的3-4倍,预处理物料通过量大,能够与分级和选粉设备配置用于生料终粉磨系统。
但由于产品粒度分布窄、颗粒形貌不合理及凝结时间过快、标准稠度需水量大与混凝土外加剂相容性差等工作性能参数方面的原因,国内水泥制备工艺未采用辊压机终粉磨系统,辊压机只在水泥联合粉磨系统中承担半终粉磨(预粉磨)的任务,经施以双辊之间的高压力挤压后的物料,其内部结构产生大量的晶格裂纹及微观缺陷、<2.0mm及以下颗粒与<80um细粉含量增多(颗粒裂纹与粒度效应),分级后的入磨物料粉磨功指数显著下降(15-25%),易磨性明显改善;因后续管磨机一仓破碎功能被移至磨前,相当于延长了管磨机细磨仓,从而大幅度提高了系统产量,降低粉磨电耗。
但辊压机作业过程中对入机物料粒度及均匀性非常敏感,粒状料挤压效果好、粉状料挤压效果差,即有“挤粗不挤细”的料床粉磨特性;当入机物料中细粉料量多时会造成辊压机实际运行辊缝小,主电机出力少,工作压力低,若不及时调整,则挤压效果会变差、系统电耗增加。
生料辊压机终粉磨系统产量低的原因及措施

生料辊压机终粉磨系统产量低的原因及措施1.设备问题:解决方案:-定期检查设备运行状态,及时进行维护和保养,确保设备运行正常。
-采购优质的设备,提高设备的使用寿命和工作效率。
2.材料问题:材料的质量是影响产量的关键因素。
如果原料中含有过多的杂质、石块或者过粗的颗粒,都会影响磨碎效果,从而导致产量降低。
解决方案:-严格控制原材料的质量,确保原材料的纯度和颗粒大小的均匀性。
-增加预磨设备,对原料进行预处理,使其更易于粉磨和磨碎。
3.磨球问题:磨球的选择和使用也是影响产量的重要因素。
如果磨球选择不当、磨球磨损严重或者磨球补充不及时,都会导致磨磨损增加和磨磨效果下降。
解决方案:-选择合适的磨球,根据生料的硬度和粒度,选择适当的规格和材质的磨球。
-定期检查磨球的磨损情况,及时进行更换和补充。
4.系统压力问题:解决方案:-根据生料的特性和磨磨系统的工作状态,合理调整系统的压力,保持系统的良好运行状态。
-定期检查系统的压力,及时处理压力过低或过高的情况,保证系统的正常运行。
5.运行参数问题:解决方案:-根据生料的特性和磨磨系统的工作状态,合理调整运行参数,提高磨碎效果和产量。
-定期检查运行参数,及时调整和优化参数设置,确保系统的正常工作。
综上所述,生料辊压机终粉磨系统产量低的原因可能有设备问题、材料问题、磨球问题、系统压力问题和运行参数问题等。
解决这些问题需要采取相应的措施,包括设备维护和保养、优化原料质量和预磨处理、选择合适的磨球、调整系统压力和优化运行参数等。
只有综合考虑所有的因素,才能解决产量低的问题,提高生料辊压机终粉磨系统的产量和效率。
辊压机在联合粉磨系统中需要改进的操作
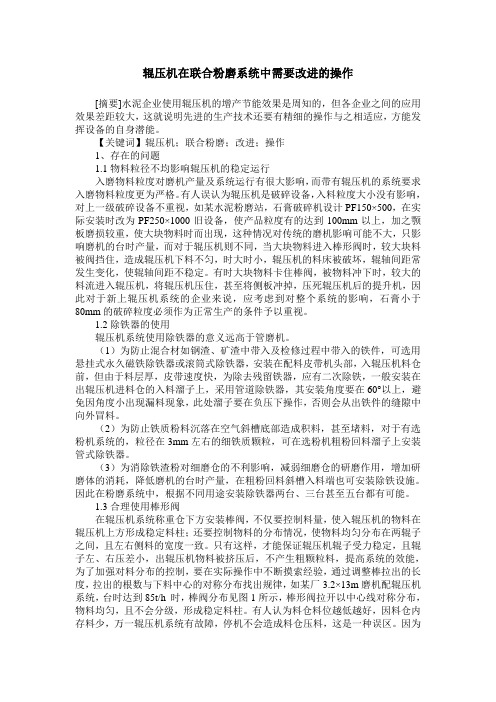
辊压机在联合粉磨系统中需要改进的操作[摘要]水泥企业使用辊压机的增产节能效果是周知的,但各企业之间的应用效果差距较大,这就说明先进的生产技术还要有精细的操作与之相适应,方能发挥设备的自身潜能。
【关键词】辊压机;联合粉磨;改进;操作1、存在的问题1.1物料粒径不均影响辊压机的稳定运行入磨物料粒度对磨机产量及系统运行有很大影响,而带有辊压机的系统要求入磨物料粒度更为严格。
有人误认为辊压机是破碎设备,入料粒度大小没有影响,对上一级破碎设备不重视,如某水泥粉磨站,石膏破碎机设计PF150×500,在实际安装时改为PF250×1000旧设备,使产品粒度有的达到100mm以上,加之颚板磨损较重,使大块物料时而出现,这种情况对传统的磨机影响可能不大,只影响磨机的台时产量,而对于辊压机则不同,当大块物料进入棒形阀时,较大块料被阀挡住,造成辊压机下料不匀,时大时小,辊压机的料床被破坏,辊轴间距常发生变化,使辊轴间距不稳定。
有时大块物料卡住棒阀,被物料冲下时,较大的料流进入辊压机,将辊压机压住,甚至将侧板冲掉,压死辊压机后的提升机,因此对于新上辊压机系统的企业来说,应考虑到对整个系统的影响,石膏小于80mm的破碎粒度必须作为正常生产的条件予以重视。
1.2除铁器的使用辊压机系统使用除铁器的意义远高于管磨机。
(1)为防止混合材如钢渣、矿渣中带入及检修过程中带入的铁件,可选用悬挂式永久磁铁除铁器或滚筒式除铁器,安装在配料皮带机头部,入辊压机料仓前,但由于料层厚,皮带速度快,为除去残留铁器,应有二次除铁,一般安装在出辊压机进料仓的入料溜子上,采用管道除铁器,其安装角度要在60°以上,避免因角度小出现漏料现象,此处溜子要在负压下操作,否则会从出铁件的缝隙中向外冒料。
(2)为防止铁质粉料沉落在空气斜槽底部造成积料,甚至堵料,对于有选粉机系统的,粒径在3mm左右的细铁质颗粒,可在选粉机粗粉回料溜子上安装管式除铁器。
辊压机及其挤压粉磨工艺系统的操作
辊压机及其挤压粉磨工艺系统的操作1 前言挤压粉磨工艺是国际八十年代中期新开发的新型节能粉磨技术。
自1990年江苏省江阴市水泥厂国内第一台辊压机投产以来,在我国生产实际中应用已有多年的历史。
截止1995年11月的不完全统计,国内销售近二百台辊压机,已投产也有一百多台。
正如所有的新技术那样,辊压机在推广应用初期无论从设备还是工艺,都存在逐步认识与完善的过程,而经过几年的使用,经验得到积累,技术日臻完善。
随着辊面结构的改进和新技术新材料的应用,辊面磨损修复问题已逐步得到解决。
伴随着不同工艺系统的研究开发,挤压粉磨工艺的各项技术经济指标大幅度提高。
辊压机的操作方式也由于不同工艺流程,不同的物料情况,不同的设备配置方式而发生较大的变化,其突出特点之一就是在相同主电机功率条件下,辊压机液压系统的操作压力,料饼的厚度以及各种回料循环量等参数间的调节。
由压力和物料循环量的不同形成低压大循环和高压小循环为特征的操作方式。
辊压机设计参数之一就是单位辊宽线压力值,对Φ1000辊径的辊压机,单位辊宽线压力设计值为100kN/cm,正常操作在(40-80)kN/cm之间。
所谓低压一般为(40~60)kN/cm,高压为(60-80)kN/cm。
本文就不同情况下辊压机及其在不同工艺系统中的操作方式谈一些体会,以供使用辊压机的厂家参考。
2 辊压机操作参数的调整及其影响当一台辊压机应用于具体的工艺生产线中时,其规格参数,包括辊面形状、辊宽、线速度、装机功率以及液压系统最大操作压力均已确定。
喂入辊压机新鲜物料的物性,包括物料的形状、强度、温度、最大粒度、平均粒径及颗粒分布状况都已基本定型。
因而此时辊压机可以调整的参数,实际只有液压系统压力和辊压机出料的料饼厚度(即通过量)。
为不使主电动机的运行电流超过其额定电流,还必须对这两个参数的调整加以控制。
如果假设辊压机主电机电流保持不变,则液压系统的压力与料饼厚度呈反比例关系。
即增大通过量,增大料饼厚度,就必须降低液压系统的操作压力。
辊压机生料终粉磨系统的生产工艺流程
辊压机生料终粉磨系统的生产工艺流程辊压机生料终粉磨系统是水泥生产中的重要设备之一,其生产工艺流程对于水泥生产的质量和效率具有重要影响。
本文将从原料进料、破碎磨、预磨、精磨和尾料处理等方面介绍辊压机生料终粉磨系统的生产工艺流程。
一、原料进料辊压机生料终粉磨系统的原料主要包括石灰石、粘土和其他辅料。
这些原料首先通过输送设备进入到储料仓中,然后经过称重装置进行称重,按照一定的配比进料到辊压机破碎磨设备。
二、破碎磨辊压机生料终粉磨系统的破碎磨设备采用辊磨机进行破碎和磨矿。
原料经过破碎磨设备后,颗粒度得到一定程度的降低,形成初步的破碎矿粉。
破碎磨设备通过调节辊磨机的压力和进料量,控制破碎矿粉的粒度和产量。
三、预磨初步破碎矿粉经过破碎磨设备后,进入到预磨设备中进行进一步的磨矿。
预磨设备通常采用辊压机或球磨机,通过辊磨或球磨的方式对矿粉进行更细致的磨矿,提高磨矿效率和细度。
预磨设备的磨矿效果直接影响到后续精磨的效果和能耗。
四、精磨预磨后的矿粉进入到精磨设备中进行最后的精细磨矿。
精磨设备通常采用球磨机,通过添加适量的石膏和控制磨机的转速,使矿粉达到所需的细度要求。
精磨设备的磨矿效果和运行稳定性对水泥品质和能耗具有重要影响。
五、尾料处理精磨后的矿粉经过筛分设备进行筛分,将达不到细度要求的尾料重新送回到预磨设备进行再次磨矿,以提高磨矿效率和细度。
同时,通过风力输送装置将符合要求的终粉送入水泥仓进行储存和包装。
辊压机生料终粉磨系统的生产工艺流程包括原料进料、破碎磨、预磨、精磨和尾料处理等步骤。
通过合理控制每个环节的工艺参数,如进料量、磨矿压力、转速等,可以达到所需的水泥细度和产量要求。
同时,辊压机生料终粉磨系统的生产工艺流程还需要考虑能耗和设备维护等因素,以提高生产效率和降低生产成本。
辊压机球磨机联合粉磨工艺流程
辊压机球磨机联合粉磨工艺流程引言辊压机球磨机联合粉磨工艺是一种常用的矿石粉磨工艺,适用于金属矿山、非金属矿山等行业。
该工艺通过辊压机和球磨机的联合作业,能够更有效地将原料粉碎为所需的细度,提高产能和产品质量。
本文将详细描述辊压机球磨机联合粉磨工艺的步骤和流程。
工艺流程1. 原料准备在开始粉磨工艺之前,需要对原料进行准备和处理。
通常情况下,原料需要经过采掘、运输和储存等环节后才能使用。
在这些环节中,需要确保原料的质量和含水率符合要求,并进行必要的筛分、除尘等处理。
2. 辊压机预处理辊压机是辊式粉碎设备,主要用于将原料初步粉碎为适当大小的颗粒。
在辊压机预处理阶段,需要调整辊轮间隙和辊轮转速等参数,以控制颗粒的大小和形状。
辊压机通常采用两辊或四辊结构,通过辊轮的旋转和挤压作用,将原料压碎。
3. 球磨机精细磨矿球磨机是一种旋转式粉碎设备,主要用于将原料进一步粉碎为所需的细度。
在球磨机精细磨矿阶段,需要调整球磨机转速、填料比例和球体尺寸等参数,以控制粉矿的细度和产量。
球磨机通常由转筒、进料装置、出料装置、传动装置和电气控制系统等组成。
4. 辊压机球磨机联合作业在辊压机预处理和球磨机精细磨矿阶段之间,需要将辊压机和球磨机进行联合作业。
具体步骤如下:4.1 原料进料将经过辊压机预处理的原料通过输送带或斗式提升机等设备送入球磨机。
4.2 辊压机与球磨机协同工作在原料进入球磨机后,同时启动辊压机和球磨机,使其同时运行。
辊压机负责将原料初步粉碎,球磨机负责将原料进一步粉碎为所需的细度。
4.3 控制参数调整根据实际情况和生产要求,及时调整辊压机和球磨机的转速、进料量、出料量等参数,以控制粉矿的细度和产量。
4.4 粉矿出料经过联合作业后的粉矿通过球磨机的出料装置排出,并经过筛分装置进行筛分,得到所需的产品。
5. 粉矿处理经过辊压机球磨机联合作业后得到的粉矿需要进行处理和加工。
通常情况下,需要对粉矿进行干法或湿法分级、除尘、干燥等处理,以满足产品质量要求。
水泥粉磨辊压机调试计划
水泥粉磨辊压机调试计划下载温馨提示:该文档是我店铺精心编制而成,希望大家下载以后,能够帮助大家解决实际的问题。
文档下载后可定制随意修改,请根据实际需要进行相应的调整和使用,谢谢!并且,本店铺为大家提供各种各样类型的实用资料,如教育随笔、日记赏析、句子摘抄、古诗大全、经典美文、话题作文、工作总结、词语解析、文案摘录、其他资料等等,如想了解不同资料格式和写法,敬请关注!Download tips: This document is carefully compiled by the editor. I hope that after you download them, they can help yousolve practical problems. The document can be customized and modified after downloading, please adjust and use it according to actual needs, thank you!In addition, our shop provides you with various types of practical materials, such as educational essays, diary appreciation, sentence excerpts, ancient poems, classic articles, topic composition, work summary, word parsing, copy excerpts,other materials and so on, want to know different data formats and writing methods, please pay attention!水泥粉磨辊压机作为水泥生产线中的核心设备,其性能调试工作对于确保设备稳定运行、提升生产效率具有至关重要的作用。
- 1、下载文档前请自行甄别文档内容的完整性,平台不提供额外的编辑、内容补充、找答案等附加服务。
- 2、"仅部分预览"的文档,不可在线预览部分如存在完整性等问题,可反馈申请退款(可完整预览的文档不适用该条件!)。
- 3、如文档侵犯您的权益,请联系客服反馈,我们会尽快为您处理(人工客服工作时间:9:00-18:30)。
2012牟NO.2 水泥助磨剂cement grinding aid 辊压机联合粉磨系统的调试及生产经验
李永琴,高先仕,刘丽芳 (山东山水水泥集团有限公司,山东济南250307)
文章编号:2218-9882(2012)02-0031-03 我公司新建设了一个年产1O0万t水泥粉磨站, 生产线采用 3.8m×12m水泥磨带辊压机闭路联合粉 磨系统。该系统2011年8月开机调试生产,后经过生 产实践,得到了不断完善和提高,目前运行情况良 好,生产基本正常。 1工艺流程及系统主机配置 辊压机联合粉磨系统全部采用DCS控制,并配 有工业监控电视,生产原料为回转窑熟料、石膏、 石灰石及混合材。主要产品为P・0 42.5级水泥和 P・C32.5级水泥。该系统工艺流程见图1,系统配置 见表1。
图1工艺流程 表1主机设备配置 设备名称 技术参数 料饼提升机 NSE500-36.4-530,输送量:530 ̄/h
VX2000,带料量:96~160t/h,选粉风 V形选粉机 量:150 000m。/h
双旋风筒选粉风量:120 000 ̄150 000m。/ 细粉分离器 h 循环风机 Y4—73一llNo17.8D,通风量:150 O00m3/h, 转速:985r/min 放风袋除尘器 FGM96—8,处理风量:46 000m。/h CLF140—65,通过能力:241 ̄350t/h, 产品粒度平均:<2mm占65%,<O.08ram 辊压机 占20%
3.8m×12m,生产能力:1lOt/h, 球磨机 主电动机功率:2 500kW
技术应用 O-Sepa N3000,选粉空气量:180 O00m ̄/h, 产量:95 ̄190t/h(320 ̄360m。/kg), 高效选粉机
最大喂料量:540t/h,转子转速: 120 ̄208r/min 磨尾高浓度 FGM128—2×8,处理风量:180 000m。/h, 袋除尘器 出口浓度:<30mg/m。(标态),阻力:
147O~1 770Pa 排风机 风量:180 O00m3/h,电动机功率:450kW, 转速:960r/min 出磨提升机 NSE500--38.45,输送量:500m。/h
2生产调试中所遇问题及其处理
2.1多次发生因磨尾滑履轴承温度高报警,高 至65℃磨机跳停事故,影响了水泥磨的正常运行。 分析原因:简体与衬板之间没安装隔热层, 物料在粉磨过程中产生大量的热能,高温的物料与 风将热量传递给磨机简体,磨机简体与滑环直接接 触,简体热量直接传递给滑环,测温点设在滑环 上,其所测温度为滑环温度而非瓦温,所以原先所 设定保护轴瓦的跳停温度65℃过低。经过一段时间 的运行和摸索,将设定温度定为70℃。 具体措施: ①加强稀油润滑站冷却装置的维护,每次停机 检修时,对稀油站过滤网进行清洗。 ②在出料端滑环罩底部两侧观察门上加轴流 风机,注意风机进口加过滤罩,确保鼓入清洁的空 气。 ③根据现场观察滑环油膜及滑履端部测温情 况,逐步提高设定温度。由原来的60"C报警65℃跳 停,改为65℃报警7O℃跳停。 ④增大0一Sepa选粉机的冷风量来降低回磨粗 粉的温度。 ⑤提高高浓度除尘器风机转速,加大磨机通风
3l
- 技术应用 水泥助磨剂cement grinding aid 2012耳NO.2
量,并适当增加喂料量,降低出磨物料温度。 采取上述措施后,实现了磨机的连续运转。下 一步考虑利用停机大修时问,在筒体与衬板之间加 一层隔热材料垫层,避免物料的热量直接传递给滑 环。 2.2辊压机故障多,白2011年8月19日至9月3同 辊压机跳停多达10次,不能连续稳定生产。 分析原因: ①辊压机电控系统程序为厂家新开发的软件, 首次应用,而且厂家调试人员对水泥粉磨生产不熟 悉,运行出现故障较多。辊压机压力波动很大,动 辊压力在6~14MPa波动,定辊压力在3~l3MPa波 动;辊缝突然上升至60mm,压力升至上限15MPa,辊 压机不跳停。 ②辊压机喂料装置中控显示开度与现场开度不 符,不能有效调控,导致喂料仓内物料瞬间卸下, 辊缝迅速增大,液压系统来不及加压,辊缝偏差就 达到设定的上限,保护系统自动卸压,频繁处于纠 偏状态,从而造成辊压机无法正常工作。 采取的措施: ①联系厂家对液压电控程序,根据实际情况 进行调整。经过多次调试,确定辊压机最佳控制参 数为:辊缝正常值25 ̄40mm,辊缝偏差7mm报警15mm 跳停。 ②对辊压机喂料装置开度进行校正,使中控 与现场开度大小吻合,能够稳定调控喂料量。调整 后,再没出现因偏差大导致辊压机跳停情况。 2.3磨尾吐渣口漏料和漏10mm的钢球,出磨提 升机入选粉机斜槽弯头处及选粉机风道内有钢球与 积料,走料不畅,增加了岗位工的劳动强度,同时 因二仓中的小钢球减少,降低了研磨能力,影响成 品的比表面积。 分析原因:停机检查磨机出磨篦板篦缝、篦板 间隙及回转筛筛孔,发现篦缝不规则,采购订货尺 寸为5mm,实际为7 ̄8mm;篦板间缝隙较大;回转筛 孔有儿处磨漏,能漏出小的钢球。 采取的措施:停机后用合适直径的钢筋塞焊较 大的篦缝与篦板间缝隙,补焊回转筛磨漏处。将磨 32一 尾挡料板加高30mm。处理后磨尾出渣口不再漏球和 漏料。 2.4辊压机喂料螺旋装置下料斜插板和法兰盘 被顶坏。 分析原因:辊压机喂料采用双进料装置,即两 个电动螺旋丝杆升降机,通过增大和减小斜插板的 开度来控制调整辊压机喂料量的大小,细粉多时减 小斜插板的开度,细粉少时增大斜插板开度,减小 辊压机振动,确保平稳运行。一次因空压机故障, 导致水泥磨磨尾高浓度袋式除尘器高压风供应不 足,提升阀板全部关闭,风机开着但水泥磨系统没 有了负压,磨头返尘,水泥磨机跳停。辊压机上部 气动棒闸因气缸的二位五通电磁导向阀无高压风不 能正常关闭。中控人员着急把下料螺旋装置关闭, 开度由80%关至0,把斜插板与丝杆法兰盘顶坏。 采取的纠正及预防措施:给新学员培训,遇到 磨机、辊压机跳停情况,先联系现场巡检工,在现 场先关手动棒闸,对辊压机进行盘车使溜至下料螺 旋装置内的料通过辊压机辊子后,再减小下料斜插 板开度,防止内部物料将下料挡板及螺旋法兰盘顶 坏。 2.5中控显示出磨风温温度低。 分析原因:水泥磨开机运行时,中控显示出磨 风温度最1' ̄25.8℃,最高50.7℃。经现场检查,出 磨负压风管道测温点处倾斜地焊了一段长300mm、 直径为一英寸的镀锌管, 管内安装一根wzP型 中16mmX650mm的热电阻, 插入倾斜镀锌管内的长 度为500mm,进入负压风管道测量出磨含尘负压风的 热电阻长度仅200mm,其余300mm在负压风管道外 部,这部分所测得接近外部环境温度,因此不能实 际反映风管内带料的风温。 采取的措施:将镀锌管截短200mm,进入负压 管道内的热电阻长度为400mm, 中控显示出磨负压 风温度升高了,温度在60~72℃之间,能够正确显 示出磨风温。 2.6 V形选粉机导流叶片角度调整不合适,对物 料的分散效果差、分离效率低、入磨物料粗。 分析原因:导流叶片自上至下共有4个,角度分 2012年NO.2 水泥助磨剂cement grinding aid 别是15。、15。、20。和l5。。这样通过v形选粉机 的风走上部,形成短路,风中的料不能经过由隔板 形成的多层风墙阻隔分离, 粗颗粒会随风进入细粉 分离器,入磨物料粒度较大,增加磨内负荷。 采取的措施:将自上至下4个P一 片角度分 别调至:0。、l0。、30。和30。。 l / 入磨物料 技术应用 80 u m筛筛余由50%下降为40%。 3调试生产中研磨体级配、工艺运行参 数和质量指标 负荷调试期间,根据磨机及减速器磨合时间的 要求制定了30%、60% ̄190%负荷试车计划。不同负荷 时钢球级配见表2。 表2不同负荷时磨机级配 一仓级配(t) 一仓平均 二仓平均 项目 总量(t) 中40 ①30 中25 中2O 合计 球径(mm) ①2O ①17 15 1O 合计 球径(mm)
30%负荷 2 6 4 3 15 28.00 5 7 7 19 38 l3.53 53 60%负荷 4 11 7 7 29 27.76 10 l4 15 38 77 l3.55 1O6 90%负荷 6 16 1O 11 43 27.67 l5 21 23 57 l16 l3.55 159
3,1 3O%的负荷试车48h。 ①生产P・0 42.5水泥配比:熟料I号39%、熟料 2号39%、石灰石5%、混合材A4%、混合材B7.5%和石 膏5.5%。 ②喂料量50t/h,循环风机转速330~350r/ min,辊压机辊缝24.5~29.5mm, 辊压机压力 6.5~8.5MPa,出磨气体压力~9O0~一1lOOPa, 磨尾 高浓度除尘器风机转速680 7lOr/min,选粉机转速 530r/min,一次风阀门开度55% ̄65%,二次风阀门 开度45% ̄55%。 ③质量指标:80 u m筛筛余:0.4%~0.6%,比表 面积:330 ̄350m /kg,SO 含量:2.0%~2.4%。 3.2 60%的负荷试车72h。 ①生产P・0 42.5水泥配比:熟料l号39%、熟料 2号39%、石灰石8%、混合材A4%、混合材B5%和石膏 5%。 ②喂料量80t/h,循环风机转速480~58Or/ m i n,辊压机辊缝2 5~3 4 m m,辊压机压力 6.5~7.9MPa,出磨气体压力一800~一920Pa,磨尾高 浓度除尘器风机转速750 ̄770r/min,选粉机转速545r/ min,一次风阀门开度80%,二次风阀门开度70%。 ③质量指标:80 m筛筛余:0.5%~0.7%,比表 面积:340 ̄350m /kg,SO 含量:2.0%~2.4%。 3.3 9O%的负荷试车96h。 ①生产P・0 42.5级水泥配比:熟料77%、石灰 石8%、混合材A5%、混合材B5%和石膏5%。 ②喂料量1 1Ot/h,电耗32kW・h/t,循环风机 转速490 ̄515r/min,辊压机辊缝33 ̄36mm,辊压机 压力7.3~7.6MPa,出磨气体压力一1000 ̄一1060Pa, 磨尾高浓度除尘器风机转速840r/min,选粉机转速 577r/min,一次风阀门开度80%,二次风阀门开度 70%。 ③质量指标:801.t m筛筛余:0.4%~0.6%,比 表面积:360 ̄380m /kg,SO 含量:2.0%~2.4%,3d 抗折和抗压强度分别为4.6MPa和25MPa,28d抗折和 抗压强度分别为8.5MPa ̄49MPa。 由以上试运行情况可看出,随研磨体的增加, 台时产量、产品比表面积和用风量逐渐增加。 4结束语 该生产线自201 1年8月投产并经生产调试后,现 各设备运行正常,产质量达到设计指标。由于原设 计放风袋除尘器灰斗内的料是入磨头的,经过多次 取样化验及检测,其筛余、比表面积和s0:;含量指标 均能够满足水泥质量标准要求,故将放风除尘器收 集的物料改入成品输送斜槽;同时,还掺加了0.02% 液体助磨剂,台时产量得到进一步提高。以上措施 实施后,生产P・0 42.5级水泥台时产量由11Ot/h 提高到120t/h。