主轴回转误差测量技术及其仪器调研报告

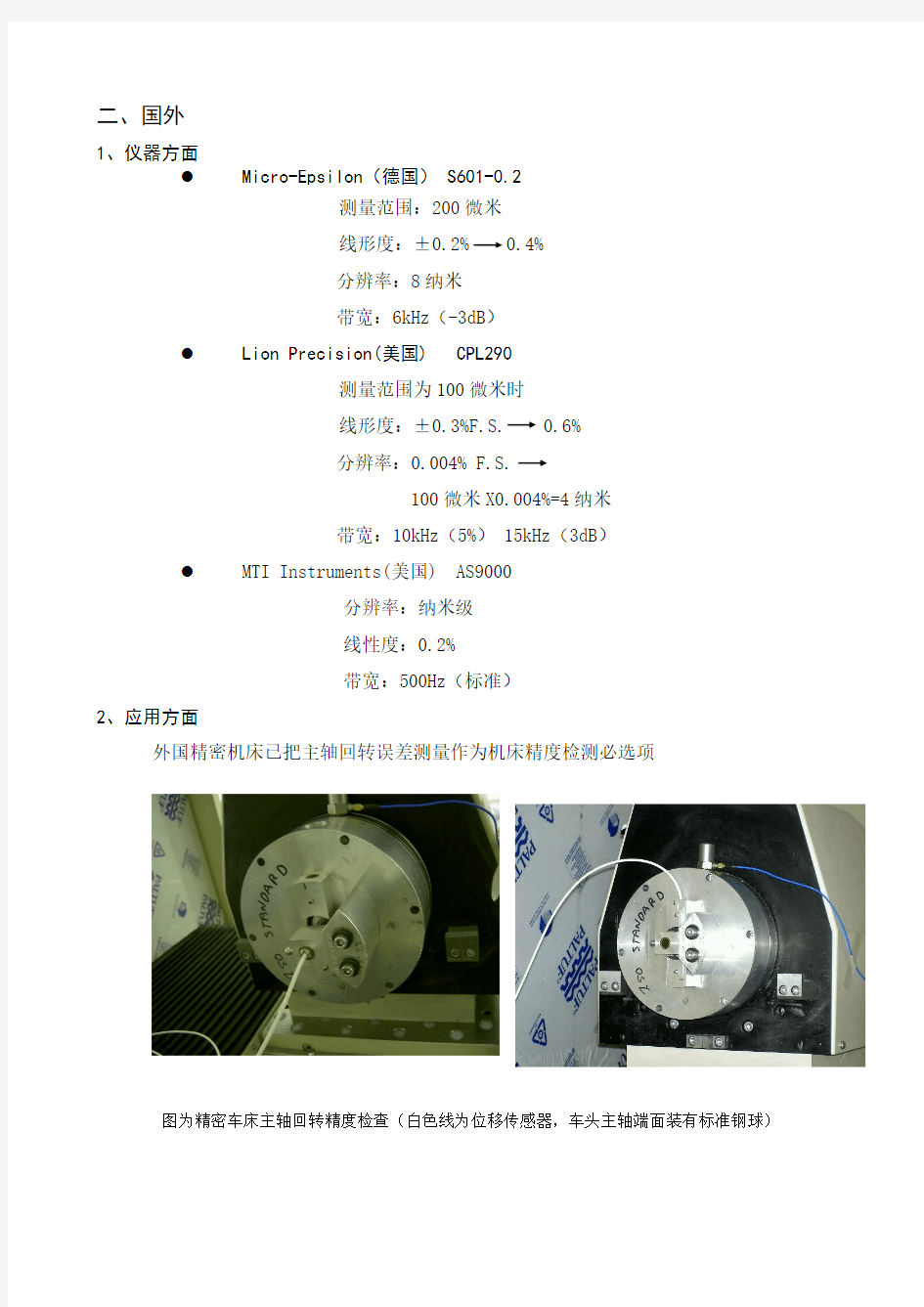
主轴回转误差测量技术及其仪器调研报告
主轴的性能对产品质量的影响至关重要。当认识了主轴的性能,就可以预测和控制零件的加工精度;工件的位置精度、粗糙度和表面光洁度都与主轴性能有关。因此,工况下测量主轴的性能是很必要的,只有测量主轴回转才能从更深层面上来控制加工质量,进而加深对机床的了解。通过测试可以优化主轴转速,通过温升曲线可获知机床的预热时间,通过冲击试验前后数据的对比分析,可检查主轴的损坏程度。
我公司此方面存在的问题
目前公司机床主轴装配上只能依赖师傅经验,无法动态测试主轴回转轴心轨迹,亦无法知道机床主轴在磨削受力、温度变化的动态特性。为提高机床产品精度,为机床主轴加工生产装配提供理论依据,此项试验研究急需开展!
一、国内现状
1、仪器方面
目前国内仪器研制方面主要停留在软件开发方面,数据处理硬件亦无成熟稳定产品,并且需要自行配套传感器及装夹夹具和标准钢球。主要厂家有:
北京派莱博
测头直径:测头工作面有效直径3mm
测量范围:40微米~140微米(间隙)
线形度:±0.05% 0.1%
分辨能力:1纳米
带宽: DC 500Hz
DC 3kHz
2、应用方面
国内做主轴轴心轨心测试的主要停留在高校实验室和一些研究所,还有一些飞机制造等精密主轴回转使用。一方面夹具是自行设计,软件自行开发,另一方面是进口国外成熟的仪器。
二、国外
1、仪器方面
●Micro-Epsilon(德国) S601-0.2
测量范围:200微米
线形度:±0.2% 0.4%
分辨率:8纳米
带宽:6kHz(-3dB)
●Lion Precision(美国) CPL290
测量范围为100微米时
线形度:±0.3%F.S. 0.6%
分辨率:0.004% F.S.
100微米X0.004%=4纳米
带宽:10kHz(5%) 15kHz(3dB)
●MTI Instruments(美国) AS9000
分辨率:纳米级
线性度:0.2%
带宽:500Hz(标准)
2、应用方面
外国精密机床已把主轴回转误差测量作为机床精度检测必选项
图为精密车床主轴回转精度检查(白色线为位移传感器,车头主轴端面装有标准钢球)
三、美国LION主轴误差测量仪详细技术资料
主要功能:可采集跟踪主轴瞬时转速变化、轴心轨迹、轴向位移,热变形
配置:电涡流传感器及配套夹具、标准钢球及相关配套夹具、操作控制箱、处理软件。
温升:温度升高是影响机床性能的最大误差源。当机床发热,会明显的温度升高、发生变形。温度的变化改变机床的状态、倾斜度、定位精度和加工圆孔的深度。
不均匀的受热会对机床结构产生破坏,导致主轴的倾斜。这些变化进而影响圆孔的位置精度、粗糙度和表面的加工质量。
通过机床温升测试,可以知道机床的热稳定时间。
粗糙度:同步误差运动来自于主轴转动但是不同于粗糙度的成因。它关系到机床切削圆孔的能力,下图是主轴切削圆孔的粗糙度图和误差运动图的对比。
测量同步运动误差有助于描述和认识各种主轴的特性,这样你就很清楚哪个轴最符合当前的工作要求。而且,通过测试可以考察主轴工作不正常时其性能是否受到影响,是否可以继续使用。
表面加工质量:同步运动误差在主轴连续转动的位置是非重复变化的,它直接影响零件的表面加工质量,在极坐标图中有所体现。
测量同步运动误差能够帮助我们描述并认识主轴的特性,这样你就很清楚哪个轴最符合当前的工作要求。而且,它也是一项很重要的确保主轴性能良好的冲击测试。
主轴误差分析仪系统
硬件:主轴误差分析仪的特色在于高精度的电容传感器系列。这些传感器提供二种可选的灵敏度、纳米级的分辨率和可选的温度模块。一根电缆线连接传感器和软件,软件不需要操作者把数据导入,自动直接读取校准数据。
精密标准钢球粗糙度达到纳米级,被装夹在机床刀架或者卡盘上。探测头被牢固的装夹在电容探测器上,定位精度高,确保测试结果的可靠性。分析仪上的七个温度传感器可以帮助你更好的了解机床温度在不同位置的变化情况,比如:床身周围、主轴、床身、工作台等。
软件:主轴误差分析仪软件采集来自传感器的数据,然后计算运动误差,最后以数值和
图形的格式显示结果。软件界面上可同时显示四个测试窗口,而且每个窗口都可以全屏显示。测试数据可以存档,以方便日后查阅和与以后的测试结果作对比分析。软件包括外形轮廓窗口、图像显示窗口、探测器安装窗口和系统诊断窗口,此外还附带完整的在线帮助功能。
性能测试
精密的传感器和工件:高性能、非接触式的电容传感器探测头装夹在一个鸟巢状的装置上,该装置可以测量精密标准钢球的动态位移。精密标准钢球装夹在主轴刀架或者车床卡盘上。
俯视图
五个坐标轴的测量:一个传感器被安装在Z轴方向上测量位移变化,一对传感器成90°被分别安装在X轴、Y轴方向上测量各自的运动变化情况,第二对X轴、Y轴方向的传感器被装夹起来测量第二个标准钢球。上述X轴、Y轴方向传感器测量结果组合在一起就得到了主轴的倾斜度。
分析与显示:当主轴回转时,有专门的软件完成读取传感器的读数,对结果进行分析,并在显示屏上生成报告,显示屏上显示测量的数值、极坐标图或者直角坐标图。
主轴误差分析仪可测的一些性能指标
径向回转灵敏度:径向回转灵敏度反映了互成90°的两个探测器的位移值。探测器分别测量回转轴在X轴、Y轴方向的位移,生成极坐标图。当主轴回转时,径向回转灵敏度测试为磨床、铣床、钻床的加工过程提供有效的指导作用。
固定的径向灵敏度:固定的径向灵敏度反映了X轴方向的位移,并在极坐标轴显示这些数据,X轴方向的位移和主轴角度位置相关。
在车削过程中,工件在主轴上旋转;在磨削过程中,比如表面磨床,砂轮和工件的接触点固定在某个位置。此时固定的径向灵敏度测试为这些过程提供有效的指导作用。
固定的倾斜灵敏度:通过X轴或Y轴的一对探测器,可以测得主轴的倾斜度,并可以在极坐标下或者三维坐标下显示出不同角度位置的倾斜情况。测试结果可以很好的预测沿主轴
轴线方向各个位置的性能。当工件远离主轴表面时,通过倾斜度测量可以减少误差。
轴:轴运动误差反映了Z轴方向传感器测得的位移值,传感器测量主轴的轴向位移。传感器测量X轴方向或者Y轴方向或者指数信号或者编码器信号可以测得主轴角度位置的数据。此外,轴运动误差除了可以在极坐标下和直角坐标系下表示,还可以在示波器上显示。
FFT(快速傅里叶变换):单个的传感器可以完成快速傅里叶变换分析测试,并能把测试结果表示成幅值—频率图,即频谱图。该频谱图每秒钟更新一次,显示最新的FFT结果。FFT 数据在分辨轴承频率、共振频率、转速和结构振动时需要用到。
温度稳定性:稳定性测试主要是测量主轴回转产生的热量所造成的影响。测试是在主轴回转过程中进行的,温度稳定性随着机床和工件之间的相对位置的改变而变化,这些变化影响机床的一些性能,比如: 工件距离主轴表面的距离、圆孔的位置、圆孔的深度等。该测试也很容易把X、Y轴运动从众多复杂的倾斜运动中区分出来。
自动化测试:会生成一个连续的测试电子数据表,检查不同时间或不同的主轴转速时的性能,测试信息可以链接到Excel电子数据表格中,方便以后画图、打印、参考和为客户分析时用。
温度变化误差(TVE): TVE测试机床由于周围的温度变化而相对工件的运动情况,该测试无需主轴回转,只需供给机床停止运转所需的耗能即可。因为周围温度变化缓慢,加上机床聚集的热量传递到周围需要一定的时间,所以此测试耗时长达24小时。该测试需要X、Y、Z轴方向的传感器辅助工作。
机床主轴回转精度实验报告
机床主轴回转精度实验报告 姓名: 学号: 实验时间: 课程名:制造技术基础 实验室:金切实验室 机械制造及其自动化 2012
一、实验概述 随着机械制造业的发展,对零件的加工精度要求越来越高,由此对机床精 度要求也越来越高。作为机床核心——主轴部件的回转误差运动,直接影响机床的加工精度,它是反映机床动态性能的主要指标之一,在《金属切削机床样机试验规范》中已列为机床性能试验的一个项目。多年来,国内外一直在广泛开展对主轴回转误差运动测量方法的研究,并取得一定的成果。 研究主轴误差运动的目的,一是找出误差产生的原因,另一是找出误差对 加工质量影响的大小。为此,不仅对主轴回转误差运动要能够进行定性分析,而且还要能够给出误差的具体数值。 二、实验目的 1.通过实验,熟悉机床主轴运动误差的表现特征、评定方法、及测定技术、产生原因及对机床加工精度的影响。使同学加深理解工艺装备运动精度与加工误差的关系; 2.理解主轴回转误差的测量数据处理技术与基本原理。 三、实验要求 1.实验员演示主轴回转误差测量的全过程,讲解主轴回转精度的定义、主轴回转误差测量原理和测量仪器的操作方法; 2.同学观察实验过程,记录实验数据,并学习使用MATLAB完成实验数据处理,将实验数据处理过程的计算和结果写入实验报告。 四、报告内容 1.简述实验系统的组成结构与原理;
2. 什么是主轴回转误差运动?造成机床主轴回转运动误差的因素可能有哪些? 3.实验数据记录与处理 数据采样时间固定为2ms; 测量距离单位为mm; 4.采用Matlab绘制极坐标误差带圆图并打印 1)从采样记录文件按单周采样点数(n)截取数据; 2)打开matlab,使用file->Import导入数据文件,数据将保存在data变量中; 3)使用命令x=(0 : 2*pi/n : 2*pi-2*pi/n )生成极坐标刻度,并进行转置x=x’; 4)使用polar(x,data)命令,绘制极坐标图。
数控车床丝杠螺距误差的补偿
项目数控车床丝杠螺距误差的补偿 一、工作任务及目标 1.本项目的学习任务 (1)学习数控车床丝杠螺距误差的测量和计算方法; (2)学习数控车床螺距误差参数的设置方法。 2.通过此项目的学习要达到以下目标 (1)了解螺距误差补偿的必要性; (2)掌握螺距误差补偿的测量和计算方法; (3)能够正确设置螺距误差参数。 二、相关知识 滚珠丝杠螺母机构 数控机床进给传动装置一般是由电机通过联轴器带动滚珠丝杆旋转,由滚珠丝杆螺母机构将回转运动转换为直线运动。 1、滚珠丝杠螺母机构的结构 滚珠丝杠螺母机构的工作原理见图1;在丝杠1 和螺母 4 上各加工有圆弧形螺旋槽,将它们套装起来变成螺旋形滚道,在滚道内装满滚珠2。当丝杠相对螺母旋转时,丝杠的旋转面经滚珠推动螺母轴向移动,同时滚珠沿螺旋形滚道滚动,使丝杠和螺母之间的滑动摩擦转变为滚珠与丝杠、螺母之间的滚动摩擦。螺母螺旋槽的两端用回珠管 3 连接起来,使滚珠能够从一端重新回到另一端,构成一个闭合的循环回路。
2、进给传动误差 螺距误差:丝杠导程的实际值与理论值的偏差。例如PⅢ级滚珠丝杠副的螺距公差为0.012mm/300mm。 反向间隙:即丝杠和螺母无相对转动时丝杠和螺母之间的最大窜动。由于螺母 结构本身的游隙以及其受轴向载荷后的弹性变形,滚珠丝杠螺母机构存在轴向间隙,该轴向间隙在丝杠反向转动时表现为丝杠转动α角,而螺母未移动,则形成了反向间隙。为了保证丝杠和螺母之间的灵活运动,必须有一定的反向间隙。但反向间隙过大将严重影响机床精度。因此数控机床进给系统所使用的滚珠丝杠副必须有可靠的轴向间隙调节机构。 图2为常用的双螺母螺纹调隙式结构,它 用平键限制了螺母在螺母座内的转动,调整时只要扮动圆螺母就能将滚珠螺母沿轴 向移动一定距离,在将反向间隙减小到规定的范围后,将其锁紧。
机床主轴的回转误差运动测试(精)
实训三机床主轴的回转误差运动测试 1.实验目的 加工高精度的机械零件,对机床主轴的回转精度有非常高的要求。测量机床主轴的误差运动可以了解机床主轴的回转状态,分析误差产生的原因。通过机床主轴回转误差运动测试,要求学生: (1) 了解机床的主轴回转误差运动的测试方法。 (2) 熟悉传感器的基本工作原理。 (3) 掌握传感器的选用原则及测试系统的基本组成。 (4) 熟悉并掌握仪器的基本操作方法。 (5) 基本掌握数据处理与图像分析方法。 2.实验原理 本实验使用两种方法进行误差运动测试: (1) 带机械消偏的单向法直角座标显示的误差运动测试,见本实验的背景材料 中的图1-9。 (2) 电气消偏单向法圆图像显示的回转轴误差运动测试,见本实验的背景材料 中的图1-13。 3.实验对象 以C6140普通车床的回转主轴为研究对象,测试其在回转情况下的误差运动。根据测试数据,用图像分析方法表示误差运动,分析误差运动产生的原因。 4.主要实验仪器和设备 (1) C6140普通车床 (2) 回转精度测试仪 (3) 涡流测振仪 (4) 信号发生器 (5) 双踪示波器 (6) 数字式万用表 (7) 可调偏心的测量装置
5.实验步骤 1.1.1 5.1 带机械消偏的单向法直角座标显示的回转轴误差运动测试 (1) 按照仪器的操作说明,熟悉系统所用各仪器控制面板上的旋钮、按键的作 用及操作方法; (2) 按照原理框图正确地将系统中各仪器的信号线连通; (3) 调整标准盘1(作为补偿信号)和标准盘2(作为误差的测量信号)的偏心量, 标准盘2的偏心量e2应尽可能小,仅稍大于被测量轴回转误差值,以保证得到信号即可,偏心量一般调整到0.03mm~0.05mm;标准盘1的偏心量e1应尽可能调大,大到使被测量轴回转误差值相对于偏心量可以忽略不计,及得到一个接近于纯偏心信号的光滑曲线,但因受涡流传感器工作间隙的限制,偏心量无法无限制地加大,一般调到0.40mm~0.60mm即可,并使e1和e2相差180o; (4) 经指导老师检查系统连接正确后,接通电源预热仪器; (5) 按测振仪使用要求调整好涡流传感器的工作间隙; (6) 调整好机床转速,启动机床; (7) 调整测振仪灵敏度,使之满足下面的关系式:e1.k1传感.k1测振仪= e2.k2传感.k2测振 仪 (8) 将满足以上关系式的两路输出信号经加法器(借用回转精度测试仪后面板 上的加法器,此时应将总接口插板抽出)相加,在示波器上得到误差曲线,曲线上最高点与最低点的高度差即为圆度误差的相对值,曲线最大的垂直度即为粗糙度的相对值; (9) 标定,方法为:用正弦信号发生器输出一标准正弦信号,使其幅值为测振 仪当前档位(如30um档)的满量程输出的电压值,将该正弦信号送入加法器输入端,在示波器上得到一幅值为A mm的正弦信号,则该测量系统的标定系数为30um/A mm; (10) 求出绝对误差=相对误差(mm)×30um/A mm; (11) 停机床、关仪器,并拆除仪器的所有连接线,整理现场。 1.1.2 5.2 电气消偏单向法圆图像显示的回转轴误差运动测试 (1) 按照仪器的操作说明,熟悉系统所用各仪器控制面板上的旋钮、按键的作 用及操作方法; (2) 按原理框图正确连接好系统,仅用误差测量信号(即标准盘2的信号), 并将回转精度测试仪的总接口板插入插座中; (3) 经指导老师检查连线无误后,接通电源预热仪器; (4) 调整好机床转速,启动机床;
主轴动态回转精度测试介绍
主轴动态回转精度测试介绍 一、前言 数控机床主轴组件的精度包含以下两个方面:1.几何精度-主轴组件的几何精度,是指装配后,在无负载低速转动(用手转动或低速机械转速)的条件下,主轴轴线和主轴前端安装工件或刀具部位的径向和轴向跳动,以及主轴对某参考系统(如刀架或工作台的纵、横移动方向)的位置精度,如平行度和垂直度等;2.回转精度-指的是主轴在以正常工作转速做回转运动时,轴线位置的变化。 二、主轴回转精度的定义 主轴在作转动运动时,在同一瞬间,主轴上线速度为零的点的联机,称为主轴在该瞬间的回转中心线,在理想状况下,主轴在每一瞬间的回转中心线的空间位置,相对于某一固定的参考系统(例如:刀架、主轴箱体或数控机床的工作台面)来说,应该是固定不变的。但实际上,由于主轴的轴颈支承在轴承上,轴承又安装在主轴箱体孔内,主轴上还有齿轮或其它传动件,由于轴颈的不圆、轴承的缺陷、支承端面对轴颈中心线的不垂直,主轴的挠曲和数控机床结构的共振等原因,主轴回转中心线的空间位置,在每一瞬时都是变动的。把回转主轴的这些瞬间回转中心线的平均空间位置定义为主轴的理想回转中心线,而且与固定的参考坐标系统联系在一起。这样,主轴瞬间回转中心线的空间位置相对于理想中心线的空间位置的偏离就是回转主轴在该瞬间的误差运动。这些瞬间误差运动的轨迹,就是回转主轴误差运动的轨迹。主轴误差运动的范围,就是所谓的「主轴回转精度」。由此可见,主轴的回转精度,说明回转主轴中心线空间位置的稳定性特点。 三、主轴回转精度量测 3.1 主轴回转误差运动的测量与研究目的 对主轴回转误差运动的测量和研究有两方面的目的:
(1).从设计、制造的角度出发,希望通过测量研究找出设计、制造因素与主轴误差运动的关系,及如何根据误差运动的特点,评定主轴系统的设计和制造质量,同时找出产生误差运动的主要原因,以便做进一步改善。 (2).从使用的角度出发,希望找出主轴运动与加工精度和表面粗糙度的关系,及如何根据误差运动的特点,预测出数控机床在理想条件下所能加工出的工件几何与表面粗糙度,给选用数控机床及设计数控机床提出依据。 3.2 主轴回转精度之测试方法 主轴回转精度之测量方法,有直接测量法与间接测量法(试件法)两大类,其中直接测量法又有静态与动态测量两种方式。 (1).静态测试法- 在主轴锥孔中插入精密之测试棒,用量表接触试棒的表面和端面,轻轻旋转主轴量测在不同角度上的读值。优点:测量方法简单,容易操作,能检验出主轴锥孔中心线与回转中心线是否同心;缺点:不能反映主轴在实际工作转速下的误差运动,且不能反映该误差运动可能造成的加工形状误差及对表面粗糙度的影响。 (2).动态测试法- 以标准试棒偏心安装,在径向固定两互相垂直的位移传感器,再轴向另安装一垂直方向的位移传感器,其信号经放大器输入示波器,测量旋转敏感方向的主轴误差运动。 3.3 运动误差图名词解释 (1).总误差运动(Total Error Motion)-以足够多的圈数记录下的全部误差极坐标图,它代表主轴在一定转速下的误差运动情形。 (2).平均误差运动(Average Error Motion)-是总误差运动极坐标图的平均轮廓线,代表该机台在理想切削条件下所能加工出零件的最好圆度。
丝杠传动误差实验
丝杠传动机构定位误差测量实验 一、实验目的: 1、了解光栅测量原理。 2、了解丝杠传动机构定位误差的种类和测量方法。 二、实验内容 1. 测量丝杠传动机构的定位误差。 2.计算丝杆螺距误差和螺距累积误差。 三、实验数据及处理: 测量数据和误差处理如下: 理论值去程理论值回程回程误差实际螺距螺距偏差螺距累加误差0.000 0.000 0 0.000 0 4.000 3.795 -4.000 -3.830 -0.035 3.795 -0.205 -0.205 8.000 7.812 -8.000 -7.818 -0.006 4.007 0.007 -0.198 12.000 11.812 -12.000 -11.816 -0.004 4 0 -0.198 16.000 15.806 -16.000 -15.818 -0.012 3.994 -0.006 -0.204 20.000 19.809 -20.000 -19.813 -0.004 4.003 0.003 -0.201 24.000 23.797 -24.000 -23.813 -0.016 3.997 -0.003 -0.204 28.000 27.772 -28.000 -27.814 -0.042 3.995 -0.005 -0.209 32.000 31.772 -32.000 -31.805 -0.013 4 0 -0.209 36.000 35.784 -36.000 -35.792 -0.008 4.012 0.012 -0.197 40.000 39.777 -40.000 -39.775 0.002 3.987 -0.013 -0.210 44.000 43.768 -44.000 -43.781 -0.013 3.991 -0.008 -0.218 48.000 47.768 -48.000 -47.759 0.009 4 0 -0.218 52.000 51.764 -52.000 -51.752 0.012 3.996 -0.004 -0.221 56.000 55.770 -56.000 -55.749 0.021 4.006 0.006 -0.215 60.000 59.767 -60.000 -59.747 0.020 3.997 -0.003 -0.218 64.000 63.756 -64.000 -63.740 0.016 3.989 -0.011 -0.229 68.000 67.743 -68.000 -67.745 -0.002 3.987 -0.013 -0.232 72.000 71.737 -72.000 -71.750 -0.013 3.994 -0.006 -0.238 76.000 75.738 -76.000 -75.743 -0.005 4.001 0.001 -0.237 80.000 79.748 -80.000 -79.743 0.005 4.010 0.010 -0.227 84.000 83.741 -84.000 -83.743 -0.002 4.007 0.007 -0.220 88.000 87.736 -88.000 -87.741 -0.005 3.995 -0.005 -0.225 92.000 91.738 -92.000 -91.743 -0.005 4.002 0.002 -0.223 96.000 95.736 -96.000 -95.742 -0.006 4 0 -0.223 100.000 99.738 -100.000 -99.732 0.006 4.002 0.002 -0.221 104.000 103.747 -104.000 -103.730 0.017 4.009 0.009 -0.212 108.000 107.746 -108.000 -107.727 -0.019 3.999 -0.001 -0.213 112.000 111.756 -112.000 -111.722 0.034 4.010 0.010 -0.203 116.000 115.747 -116.000 -115.722 0.020 3.988 -0.012 -0.215 120.000 119.777 -120.000 -119.712 0.058 4.030 0.030 -0.185
机床主轴回转误差运动测试(精)
综合实验一机床主轴的回转误差运动测试 1、实验目的 加工高精度的机械零件,对机床主轴的回转精度有非常高的要求。测量机床主轴的误差运动可以了解机床主轴的回转状态,分析误差产生的原因。通过机床主轴回转误差运动测试,要求学生: (1) 了解机床的主轴回转误差运动的测试方法。 (2) 熟悉传感器的基本工作原理。 (3) 掌握传感器的选用原则及测试系统的基本组成。 (4) 熟悉并掌握仪器的基本操作方法。 (5) 基本掌握数据处理与图像分析方法。 2、实验原理 本实验使用两种方法进行误差运动测试: (1) 带机械消偏的单向法直角座标显示的误差运动测试,见本实验的背景材料中的图 1-9。 (2) 电气消偏单向法圆图像显示的回转轴误差运动测试,见本实验的背景材料中的图 1-13。 3、实验对象 以C6140普通车床的回转主轴为研究对象,测试其在回转情况下的误差运动。 根据测试数据,用图像分析方法表示误差运动,分析误差运动产生的原因。 4、主要实验仪器和设备 (1) C6140普通车床 (2) 回转精度测试仪 (3) 涡流测振仪 (4) 信号发生器 (5) 双踪示波器 (6) 数字式万用表 (7) 可调偏心的测量装置 5、实验步骤 5.1 带机械消偏的单向法直角座标显示的回转轴误差运动测试 (1) 按照仪器的操作说明,熟悉系统所用各仪器控制面板上的旋钮、按键的作用及操 作方法; (2) 按照原理框图正确地将系统中各仪器的信号线连通;
(3) 调整标准盘1(作为补偿信号)和标准盘2(作为误差的测量信号)的偏心量,标准盘2 的偏心量e2应尽可能小,仅稍大于被测量轴回转误差值,以保证得到信号即可,偏心量一般调整到0.03mm~0.05mm;标准盘1的偏心量e1应尽可能调大,大到使被测量轴回转误差值相对于偏心量可以忽略不计,及得到一个接近于纯偏心信号的光滑曲线,但因受涡流传感器工作间隙的限制,偏心量无法无限制地加大,一般调到0.40mm~0.60mm即可,并使e1和e2相差180o; (4) 经指导老师检查系统连接正确后,接通电源预热仪器; (5) 按测振仪使用要求调整好涡流传感器的工作间隙; (6) 调整好机床转速,启动机床; (7) 调整测振仪灵敏度,使之满足下面的关系式:e1.k1传感.k1测振仪= e2.k2传感.k2测振仪 (8) 将满足以上关系式的两路输出信号经加法器(借用回转精度测试仪后面板上的加 法器,此时应将总接口插板抽出)相加,在示波器上得到误差曲线,曲线上最高点与最低点的高度差即为圆度误差的相对值,曲线最大的垂直度即为粗糙度的相对值; (9) 标定,方法为:用正弦信号发生器输出一标准正弦信号,使其幅值为测振仪当前 档位(如30um档)的满量程输出的电压值,将该正弦信号送入加法器输入端,在示波器上得到一幅值为A mm的正弦信号,则该测量系统的标定系数为30um/A mm; (10) 求出绝对误差=相对误差(mm)×30um/A mm; (11) 停机床、关仪器,并拆除仪器的所有连接线,整理现场。 5.2 电气消偏单向法圆图像显示的回转轴误差运动测试 (1) 按照仪器的操作说明,熟悉系统所用各仪器控制面板上的旋钮、按键的作用及操 作方法; (2) 按原理框图正确连接好系统,仅用误差测量信号(即标准盘2的信号),并将回转 精度测试仪的总接口板插入插座中; (3) 经指导老师检查连线无误后,接通电源预热仪器; (4) 调整好机床转速,启动机床; (5) 调整基圆: (6) 回转精度测试仪产生基圆的原理:将测振仪的输出信号接入回转精度测试仪的S 输入端,由带通III从该信号选出与主轴同频的一次谐波,为了消除机床振动所引起的一次谐波的幅值变化对基圆的影响,用限幅放大器对一次谐波进行限幅,再用带通I选出稳定的一次谐波,然后将一次谐波分为两路,一路经移相器B移相90o,另一路不移相,将两路信号送示波器垂直输入端(Y端)和水平输入端(X端)叠加而产生基圆。 (7) 基圆的调整:首先根据机床转速n确定带通III和带通I所要通过的一次谐波的频 率。 (8) 调节带通III的频率粗调开关,使一次谐波的频率包括在开关所指的频率范围内, 如机床n=900转/分,则频率f=900/60=15Hz,粗调开关置在30位置。调整频率微调电位器,直到示波器上出现的正弦信号的幅值为最大(将带通III的输出端与示波器的Y端相连)。带通I的调整与带通III相同。 (9) 将示波器的X、Y端分别接回转精度测试仪的X、Y输出端,调节移相器B的移 相旋钮,使输出输入端相差90o(在示波器上得到一正椭圆图形),再调整增益电位器改变其幅值,在示波器上得到一个真圆,这个圆就是基圆。 (注意:调整基圆时一定将移相器A的增益关断)
机床主轴回转精度实验报告什么是主轴回转精度.docx
机床主轴回转精度实验报告|什么是主轴回转精度 机床主轴回转精度实验报告 姓名:学号:实验时间:课程名:制造技术基础 实验室:金切实验室 机械制造及其自动化 2012 一、实验概述 随着机械制造业的发展,对零件的加工精度要求越来越高,由此对机床精度要求也越来越高。作为机床核心——主轴部件的回转误差运动,直接影响机床的加工精度,它是反映机床动态性能的主要指标之一,在《金属切削机床样机试验规范》中已列为机床性能试验的一个项目。多年来,国内外一直在广泛开展对主轴回转误差运动测量方法的研究,并取得一定的成果。 研究主轴误差运动的目的,一是找出误差产生的原因,另一是找出误差对加工质量影响的大小。为此,不仅对主轴回转误差运动要能够进行定性分析,而且还要能够给出误差的具体数值。二、实验目的 1. 通过实验,熟悉机床主轴运动误差的表现特征、评定方法、及测定技术、产生原因及对机床加工精度的影响。使同学加深理解工艺装备运动精度与加工误差的关系; 2. 理解主轴回转误差的测量数据处理技术与基本原理。 三、实验要求 1. 实验员演示主轴回转误差测量的全过程,讲解主轴回转精度的定义、主轴回转误差测量原理和测量仪器的操作方法; 2. 同学观察实验过程,记录实验数据,并学习使用MATLAB 完成实验数据处理,将实验数据处理过程的计算和结果写入实验报告。 四、报告内容 1. 简述实验系统的组成结构与原理; 2. 什么是主轴回转误差运动?造成机床主轴回转运动误差的因素可能有哪些? 3. 实验数据记录与处理数据采样时间固定为 2ms ;测量距离单位为 mm ; 4. 采用Matlab 绘制极坐标误差带圆图并打印 1)从采样记录文件按单周采样点数(n)截取数据; 2)打开matlab ,使用file->Import导入数据文件,数据将保存在data 变量中;3)使用命令 x=(0 : 2*pi/n : 2*pi-2*pi/n )生成极坐标刻度,并进行转置x=x’; 4)使用polar (x ,data )命令,绘制极坐标图。
主轴回转精度的测定
实验主轴回转精度的测定 一、 概述 随着机械制造业的发展,对零件的加工精度要求越来越高,由此对机床精度要求也越来越高。作为机床核心——主轴部件的回转误差运动,直接影响机床的加工精度,它是反映机床动态性能的主要指标之一,在《金属切削机床样机试验规范》中已列为机床性能试验的一个项目。多年来,国内外一直在广泛开展对主轴回转误差运动测量方法的研究,并取得一定的成果。 研究主轴误差运动的目的,一是找出误差产生的原因,另一是找出误差对加工质量影响的大小。为此,不仅对主轴回转误差运动要能够进行定性分析,而且还要能够给出误差的具体数值。 过去流行的测试与数据处理方法,是传统的捷克VUOSO双向测量法和美国LRL单向测量法。前者适用于测试刀具回转型主轴径向误差运动,后者适用于测试工件回转型主轴径向误差运动。两种方法都是在机床空载或模拟加工的条件下,通过对基准球(环)的测量,在示波器屏幕上显示出主轴回转而产生的圆图象。将圆图象拍摄下来便可用圆度样板读取主轴径向误差运动数值。这种测试方法虽然能够在试验现场显示图形,直观性强,便于监视机床的安装调试,但也存在一些不足,如基准钢球的形状误差会复映进去,不能反映切削受载状态,存在一定的原理误差等。所以测量精度难以提高,实际应用受到一定限制。 经过多年的研究,目前主轴误差运动主轴误差运动的测试与数据处理方法有了很大的改进,引入频镨分析理论和FFT变换技术,通过用计算机来进行测量数据处理,使整个测量过程更方便、数据处理更科学、测量结果更正确。 二、 实验目的 1.了解机床主轴回转误差运动的表现形式、定义、评判原则、产生原因及对机床加工精度的影响。 2.懂得主轴回转误差的测量方法及实验原理。 三、 主轴径向误差运动的测试原理及方法 1.主轴回转误差运动 主轴回转时,在某一瞬时,旋转的线速度为零的端点联线为主轴在该瞬时的回转中心线。理想情况下,主铀回转中心线的空间位置,相对于某一固定参考系统应该是不随时间变化的。实际人由于主轴轴颈不圆、轴承存在缺陷、主轴挠曲、轴支承的两端对轴颈中心线不垂直以及振动等原因,使得主轴回转中心线在每一瞬 时都是变动的。因而,在进行测试数据处理时, 往往只能以回转主轴各瞬时回转中心线的空间 平均位置作为回转主轴的“理想”中心线。主 轴瞬时回转中心线的空间位置相对理想中心线 空间位置的偏差,也就是回转主轴的瞬时误差。 瞬时误差的变化轨迹也就称为回转误差运动。 如图2-l所元,若o1o1,……,o i o i为主轴各瞬 图2-1主轴瞬时回转误差 时的回转中心线,oo为它们在空间的平均位置, 即理想回转中心线,那么,δ0,……,δi便是主轴的瞬时回转误差,误差的范围也可大致看成是主铀的回转精度。 可以想象,主轴瞬时回转中心线对其理想中心线的偏移有五种可能,即沿x,y,z三个坐标方向的移动和绕x和y铀的转动。为了完全描述主轴回转中心线的误差,理论上要采
1机床主轴回转轴线的运动误差可分解为.
一、填空 1.机床主轴回转轴线的运动误差可分解为、、。 径向圆跳动、端面圆跳动、倾角摆动 2.在刨削加工时,加工误差的敏感方向为方向。 垂直方向(z方向) 3.在顺序加工一批工件中,其加工误差的大小和方向都保持不变,称为;或者加工误差按一定规律变化,称为。 常值系统误差;变值系统误差 4.零件的加工质量包含零件的和。 加工精度;表面质量 5. 车削加工时主轴的三种回转运动误差中()会造成工件的圆度误差。 (1)纯径向跳动(2)纯轴向跳动(3)倾角摆动 (1)纯径向跳动 6.加工盘类工件端面时出现近似螺旋表面是由于造成的。 主轴端面圆跳动 7.在车床上加工细长轴,一端用三爪卡盘装夹,另一端用固定顶尖,工件出现弯曲变形的 原因一是细长工件刚度较差,在切削力作用下产生弯曲;二是由于。 采用死顶尖,工件在切削热作用下的热伸长受阻而产生的弯曲。 8.在车床上加工细长轴,一端用三爪卡盘装夹,另一端用固定顶尖,试分析 采取克服弯曲变形的措施是、。 采用浮动顶尖,大进给量反向切削 9.机床导轨导向误差可分为: 水平直线度、、、。 垂直直线度扭曲(前后导轨平行度)导轨与主轴轴线平行度 10.在车削加工时,加工误差的敏感方向为方向 水平 11.分析影响机械加工因素的方法有、 单因素法统计分析法
12.在顺序加工加工一批工件中,其加工误差的大小和方向都保持不变,称为;或者加工误差按一定规律变化,称为。 常值系统误差变值系统误差 13.零件的加工质量包含零件的和。 机械加工精度表面质量 二、选择题 1. 通常用系数表示加工方法和加工设备,胜任零件所要求加工精度的程度。(1)工艺能力(2)误差复映(3)误差传递 (1)工艺能力 2.下述刀具中, 的制造误差会直接影响加工精度。 (1)内孔车刀(2)端面铣刀(3)铰刀(4)浮动镗刀块 (3)铰刀 3.在接触零件间施加预紧力,是提高工艺系统()的重要措施。 (1)精度(2)强度(3)刚度(4)柔度 (3)刚度 4.在车床静刚度曲线中,加载曲线与卸载曲线 (1)重合(2)不重合 (2)不重合 5.零件的加工精度包括: (1)尺寸公差、形状公差、位置公差 (2)尺寸精度、形状精度、位置精度 (2)尺寸精度、形状精度、位置精度 6.尺寸精度、形状精度、位置精度之间的联系是 (1)形状公差<尺寸公差<位置公差 (2)位置公差<形状公差<尺寸公差 (3)尺寸公差<形状公差<位置公差 (4)形状公差<位置公差<尺寸公差 (4)形状公差<位置公差<尺寸公差
机床传动误差测量方法
机床传动误差测量方法 1.引言 机床的传动误差是指在机床传动链的输入轴驱动完全准确且为刚性的条件下,其输出轴的实际位移与理论位移之差。机床上实现工件表面成形所需复合运动的传动链——“内联系”传动链的两末端执行元件之间必须始终严格保持符合给定要求的运动关系。传动链的传动精度是指其传递运动的准确程度,可用传动误差来衡量。由于机床实际存在传动链误差,导致工件表面成形运动轨迹存在误差,最终反映到被加工工件上即引起成形表面的形状误差等。由于机床传动链主要由齿轮副、蜗轮蜗杆副、螺纹副等组成,因此传动链误差主要来源于这些传动元件的加工精度及安装精度。从运动学角度来讲,一切引起瞬时传动比偏离给定传动要求的因素均是传动链误差的来源。 对机床传动误差的测量是对传动误差进行有效补偿的前提,因此机床传动误差的精密测量一直是机械传动技术的一项重要研究课题。机床传动误差的基本测量方法是在机床的相关部位安装传感器,借助于采用机、光、电原理的测量仪器并应用误差评定理论对机床传动系统各环节的误差进行测量、分析及调整,从而找出误差产生的原因及变化规律。 2.传感器的选用 根据传动链末端元件的运动性质正确、合理地选用、安装传感器是准确测量传动链运动精度的必要条件。根据工作原理,机床传动误差测量常用传感器可分为以下几类: (1)光栅传感器 光栅传感器的最大优点是信号处理方式简单,使用方便,测量精度高(国外著名厂家如德国Heidenhain、西班牙Fagor等公司制造的光栅传感器精度可达1μm/m);缺点是光栅尺价格较昂贵,对工作环境要求较高,玻璃光栅尺的线胀系数与机床不一致,易造成测量误差。 (2)激光传感器 激光传感器(包括单频和双频激光)具有较高的测量精度,但测量成本也较高,对环境条件变化(如温度、气流、振动等)较敏感,在生产现场使用时必须采取措施保证测量的稳定性和可靠性。 (3)磁栅传感器 磁栅尺可分为线状(有效测量长度3m)和带状(有效测量长度可达30m)两种型式,其优点是制造成本较低,安装使用方便,线胀系数与机床相同;缺点是测量精度低于光栅尺,由于磁信号强度随使用时间而不断减弱,因此需要重新录磁,给使用带来不便。 (4)感应同步器 感应同步器的优点是制造成本低,安装使用方便,对工作环境条件要求不高;缺点是信号处理方式较复杂,测量精度受到测量方法的限制(传统测量方法的测量精度约为2~5μm)。 目前常用的几类机床传动误差测量传感器的部分应用情况见表1。 表1 几类常用传感器的部分应用情况 传感器类型-应用单位-测量分辨率:线位移(μm)-测量分辨率:角位移(角秒) 光栅传感器-东京大学,汉江机床厂-2,2-1 激光传感器-单频激光:北京机床所,东京大学-0.632-/ 激光传感器-双频激光:成都工具研究所,上海机床厂-0.158-/ 磁栅传感器-东京大学,重庆大学,华中理工大学,汉江机床厂,美国威斯康星大学-2-1 感应同步器-山东工业大学,汉川机床厂-1,2-0.72
机床设备误差调整方法
机床设备误差调整方法 1 设备精度的误差来源 1.1 主轴回转精度的主要误差源 1.1.1 主轴的加工误差 主轴上两个轴颈之间有同轴度误差。主轴锥孔相对轴颈有同轴度误差。轴颈有圆度误差。轴承的轴向定位面与主轴轴线有垂直度误差。 1.1.2 轴承的加工误差 滚动轴承的滚动体之间有尺寸误差及圆度误差;内圈孔相对滚道有偏心;内圈滚道有圆度误差;前、后轴承之间有同轴度误差等。 滑动轴承有内、外圆的圆度误差和同轴度误差;前、后轴承之间有同轴度误差;轴承孔与轴颈之间有尺寸误差等。 1.1.3 相配零件的加工误差及其装配质量 箱体上的轴承孔有圆度误差;与轴承外圈相配合时有尺寸误差;轴向定位端面与孔的中心轴线有垂直度误差。主轴上锁紧与调整轴承间隙的螺母有端面平面度误差;螺母端面与螺纹中心轴线之间有垂直度误差;螺纹之间存在联接误差等。 轴承衬套隔圈两端面有平行度误差。装配中,轴承间隙调整是否合适,直接对主轴回转精度有明显影响。 1.2 导轨导向精度的主要误差源
1.2.1 受导轨几何精度的影响 导轨表面的不均匀磨损必将造成刀架溜板沿导轨运动时相对主轴运动产生较大的误差,并影响加工工件的尺寸精度和表面质量。对于直线导轨来说,导向精度主要受导轨垂直方向与水平方向内的直线度误差影响。 对于环形圆导轨来说,导向精度主要受导轨的平直度误差和导轨与主轴中心线的垂直度误差的影响。 1.2.2 受导轨间隙是否合适的影响 间隙不合适的导轨,由于缺乏必要的约束,或者约束过死,会造成运动部件在导轨上的横向摆动或者爬行现象,不能实现平稳、轻快地运动,影响导轨的导向精度。常见导轨间隙调整的方法有斜镶条调整法、压板移动调整法和磨刮压板接合面调整法等。1.2.3 受导轨自身刚度的影响 对于大型设备来说,导轨的刚度受底座支承状况影响较大。通过调整不同支承点的高度,可以改善导轨的精度状况。 1.3 传动链传动精度的主要误差源 一般机械设备中的传动链都是由齿轮与齿轮、齿轮与齿条、蜗轮与蜗杆、丝杠与螺母等传动副组成,传动误差是由动力输入环节向终端执行件进行传递进行累积。 设备维修过程中,传动精度常见的误差源是: (1)传动件的误差对设备传动精度有着主要的影响。 (2)相配零件的误差及其装配质量对传动精度有明显影响。
数控机床主轴旋转精度及测量方法
数控机床主轴旋转精度及测量方法 来源:对钩网 主轴是数控机床中的核心设备之一,担负着从机床电动机接受动力并将之传递给其他机床部件的重要责任。工作中,要求主轴必须在承担着一定的荷载量,以及保持适当的旋转速度的前提条件下,带动在其控制范围之内的工件或者刀具,绕主轴旋转中心线进行精确、可靠而又稳定的旋转。主轴的旋转精度直接决定了机床的加工精度。 主轴旋转精度的定义 机床主轴精度大小是以其瞬时旋转中心线与理想旋转中心线的相对位置来决定的。 在正常工作旋转时,由于主轴、轴承等的制造精度和装配、调整精度,主轴的转速、轴承的设计和性能以及主轴部件的动态特征等机械原因,造成了主轴的瞬时旋转中心线往往会与理想旋转中心线在位置上产生一定的偏离,由此产生的误差就是主轴在旋转时的瞬时误差,也称为旋转误差。而瞬时误差的范围大小,就代表主轴的旋转精度。加工过程中,主轴可能会延与轴垂直的方向发生径向跳动,延轴方向发生轴向窜动或以轴上某点为中心,发生角度摆动,这些运动都会降低主轴的旋转精度。 实际生产中,人们常常用安装于主轴前端的刀具或工件部位的定位面发生的三种运动的运动幅度来衡量和描述主轴精度,这三种运动分别是径向跳动、端面跳动和轴向窜动。主轴在工作转速时的旋转精度,也称为运动精度。 目前,我国已经制订并推行了国内统一的通用机床旋转精度检验标准,根据加工对象的精度要求确定不同的主轴精度标准。 主轴精度的测量和评定 静态测量和评定法:这是一种在低速旋转环境下测定主轴旋转精度的方法,又称为打表法。具体操作流程是,在无载荷条件下手动缓慢转动主轴,或控制主轴进行低速转动,利用千分表进行测量,测出最大度数和最小读数,计算出二者之差,即为主轴的旋转精度。由于静态测量是在低速旋转环境下,而不是在主轴实际工作速度下进行的测量,因此并不能够反映出真正的主轴旋转精度。 动态测量和评定法:这是一种在主轴实际的工作转速之下,采用非接触式测量装置,测出主轴旋转运动精度误差的方法,包括主轴振动及高速旋转时的运动精度误差。这种测量方法能够比较真实、全面地反映主轴的旋转精度情况。目前已普遍采用的测量方法是:将一个标准圆球安装在主轴上,再将两个位移传感器以互成直角的方式,安装在主轴运动的两个敏感方向上。主轴旋转时,两个位移
关于消除机床加工精度误差的原因与方法(精)
关于消除机床加工精度误差的原因与方法 摘要本文结合笔者的工作经验和实践基础对机床加工定位精度 误差进行了详细的探究;同时以实例为基础,提出了机床加工工件时出现的多 种误差,通过“现象”到“诊断”,详细的对这一过程进行了介绍,并提出了 相应的解决方案。 关键词机床加工;定位精度;误差 中图分类号TG659 文献标识码A 文章编号 1674-6708(2012)58-0026-02 基于数控机床具有加工产品互换性好、精度高之特点,具有加工的适应 性、功能的强大性,具有人为的每一项技术因素在产品的生产过程中被排除的 可见性,进而优化与合理的加工工艺、先进的数控设备得以实现,产品的数 量、质量得到最大程度的保证,产品的产出量达到了最大化程度。 加工产品精度系数的高低受多种因素所影响,以下精度指标为数控机床所 设限的两项内容:1)机床的每项几何精度,即机床的静态精度;2)机床各轴 的反向误差U、定位精度P、重复定位精度P等指标,即机床的动态精度。检测该动态精度的方式为VDI/DGQ3441法。对机床的定位精度P进行考核的计算公式如下所示: 机床定位精度P=6 数控机床坐标轴的长度L/300 数控设备运动轴传递形式在现阶段的界限约数为6m,运动轴传递形式大于 6m的几乎全部引用双电动机双齿轮齿条消隙机构装置作为传递运动部件。通过 引用双电动机双齿轮齿条消隙机构装置可避免与解除由于细长轴挠度变形进而 致使传递运动滞后现象的出现及定位精度误差的形成,运动部件的反向速度与 定位精度便可在很大程度上得以提升。运动轴传递形式小于6m的大多数引用了滚珠丝杆传递运动,预应力的结构可通过该类滚珠丝杆的螺母进行调整。 就传递运动滞后与定位精度不高而言,运动部件机械传动链过长、摩擦系 数太大等因素,也是造成它的核心影响因素。以激光仪器对数控机床运动轴精 度的验收进行检查,就检查轴的反向误差U、定位精度P等各项指标进行重点 提取。就传动件而言,可在设定的长度区间空间内采用系统软件,对定位精度 参数误差进行螺距补偿。产品的形位公差尺寸在产品的加工过程中取决于定位 精度,然而重复定位精度是考核机床加工产品精度的另外一个核心指标。尤其 是在加工轴线一致、孔径不同、换刀次数多的产品,对同一轴度存在要求的体 现的更为突出。定位精度可以采用系统对其进行补偿,但重复定位精度不为如此,重复定位精度将机床传动链整体的总体积累误差真实的反映了出来。就反 向误差而言,可采用系统对其进行补偿,当间隙大于等于0.15mm时,消除此误差的方法,最好是采用调整机械系统的预紧力对其进行消除。 1 基于反向误差的存在引起产品缺陷的出现 现象:就一台数控车轮车轴专用外圆而言,当磨削工件的半径和外圆直径 在交界处之后,明显的发现有清晰地过渡不圆滑痕迹的存在。 诊断:宽砂轮一次性切入磨削是此设备的一种磨削方式,工作台上安装了 砂轮修正器的金钢石笔,通过引用砂轮架X轴与工作台Z轴的复合插补运动, 以达到修正之后的砂轮的精度和形状与工件完全一致的目的,然后利用修正好 的砂轮对工件进行磨削。此工件因为存在着外圆形状的不一般性,对X轴有正 负方向运行的要求,在检查的过程中,明显的发现Z轴与X轴都存有清晰地反 向空间,Z轴和X轴在砂轮修正作反向运行时出现了瞬时停止的现象,致使痕
主轴动态精度测试与分析
2018年9月 第46卷第17期 机床与液压 MACHINETOOL&HYDRAULICS Sep 2018 Vol 46No 17 DOI:10.3969/j issn 1001-3881 2018 17 016 收稿日期:2017-04-05 基金项目:国家科技重大专项(2014ZX04014021) 作者简介:刘志松(1994 ),男,硕士研究生,研究方向为机床可靠性和性能测试等三E-mail:liuzs@mail dlut edu cn三 主轴动态精度测试与分析 刘志松,刘阔,王永青,吴嘉锟,况康 (大连理工大学机械工程学院,精密与特种加工教育部重点实验室,辽宁大连116024) 摘要:主轴动态误差对加工精度有至关重要的影响,针对主轴动态误差进行了试验与分析三介绍了主轴动态误差的概念,采用主轴动态误差分析仪对主轴动态误差进行了采集,采集的数据包括主轴径向平均误差二径向异步误差二轴向平均误差二轴向异步误差以及轴向最小间隙三对某型号同类型三台立式加工中心分别进行了多转速情况下的测量,对比并分析了三台立式加工中心的测量结果三在转速为7500r/min时,三台立式加工中心径向异步误差分别为70二15二15μm;在转速升至6000r/min之后主轴最小径向间隙均有较大提升三试验结果表明:主轴动态精度受到机床工况和转速共同影响;在高速转动情况下,主轴径向最小间隙增大明显;加工时要根据工况合理安排转速,以保证加工质量三 关键词:主轴;动态误差;径向误差;轴向误差 中图分类号:TG659一一文献标志码:A一一文章编号:1001-3881(2018)17-072-4 TestandAnalysisonDynamicAccuracyofSpindle LIUZhisong,LIUKuo,WANGYongqing,WUJiakun,KUANGKang (KeyLaboratoryforPrecisionandNon-TraditionalMachiningTechnologyofMinistryofEducation,School ofMechanicalEngineering,DalianUniversityofTechnology,DalianLiaoning116024,China) Abstract:Thedynamicerrorofspindlehasanimportantinfluenceonmachiningaccuracy.Thedynamicerrorofspindlewastest? edandanalyzed.Theconceptofdynamicerrorofthespindlewasintroduced,anddynamicerroranalyzerofthespindlewasusedtocollectthedynamicerrors,includingradialaverageerrors,radialasynchronouserrors,axialaverageerrors,axialasynchronouserrorsandaxialminimumclearance.Threesametypeverticalmachiningcentersweremeasuredunderdifferentrotatingspeedsrespectively,andthemeasurementresultswerecomparedandanalyzed.Attherotatingspeedof7500r/min,Radialasynchronouserrorsofthreeverticalmachiningcentersare70,15and15μmrespectively.Aftertherotatingspeedincreasedto6000r/min,theminimumradialclearanceofthespindleincreasessignificantly.Theresultsshowthatthedynamicaccuracyofthespindlewasaffectedbytheworkingconditionandrotatingspeedofthemachine.Inthecaseofhigh?speedrotation,theradialminimumclearanceincreasesobviously.To ensurethequalityofmachining,therotatingspeedshouldbearrangedaccordingtotheworkingconditionreasonablywhenprocessing. Keywords:Spindle;Dynamicerror;Radialerror;Axialerror 0一前言 主轴作为精密加工机床的核心部件,影响着机床加工精度三机床的工作性能和寿命都会受到主轴动态误差的影响三加工工件的圆度二表面粗糙度和平面度都与主轴有关三通过对主轴动态精度进行测试和分析,为进一步提高机床的加工精度,研发改良型号的机床提供数据支持和理论保障三因此,主轴的动态误差测试具有重要意义三 国内外很多学者对主轴动态误差进行了大量的研究三孙艳芬[1]介绍了主轴回转误差的概念及其基本形式,分析了它对加工精度的影响三王莹等人[2]对主轴系统动态误差和热漂移误差进行了测试与分析三朱永生等[3]对主轴动态回转误差进行了实验研究,测试分析了主轴回转误差受转速的影响三许颖等人[4]研究了 主轴转速和温升对主轴动态误差的影响三刘阔等人[5]在不同的转速下对主轴的动态误差进行了测试,并对主轴动态误差随转速的变化进行了分析;包丽等人[6]结合模态对加工中心主轴动态误差进行了研究三靳岚等人[7]同时在两个方向上对主轴的回转误差进行动态测试三 以上研究对于主轴动态误差研究有着很大实用价值,实验往往对单一机床在一种测试方法下对主轴进行动态测试,缺乏对比,没有考虑到安装二工况对主轴精度的影响,不能发现同一类型机床产品主轴动态精度变化的普遍规律三 文中对同一批次二同一型号的3台立式加工中心,分别对主轴动态误差进行测试三主轴的动态误差测试主要包括径向动态误差二轴向动态误差二最小径