第七章 第三节 高速压力机分解
液压与气压传动--第07章 典型液压传动系统精讲

5、快退
当滑台在死挡铁上 停留一定时间后,时间 继电器发出使滑台快退 的信号。1YA失电,2YA 得电,阀7处于右位。 进油路:由泵2-阀3- 阀7右位-液压缸右腔; 回油路:由缸左腔-阀 10-阀7右位-油箱。由 于此时空载,系统压力 很低,泵输出的流量很 大,滑台向左快退。
6、原位停止
挡块压下原位行 程开关,1YA、2YA、 3YA都失电,阀7 处 于中位,滑台停止运 动,泵通过阀7中位 卸载。
4、主缸泄压后快速返回
保压结束后,时间 继电器使电磁铁2YA 得 电,先导阀右位接入系 统,主缸上腔泄压。压 力降低后预泄换向阀下 位接入系统,控制油路 使主缸换向阀处于右位 工作,实现上滑块的快 速返回。
充液筒内液 面超过预定位置时, 多余油液由溢流管 流回油箱。单向阀 4用于主缸换向阀 由左位回到中位时 补油;单向阀5用 于主缸换向阀由右 位回到中位时排பைடு நூலகம் 至油箱。
(5)起升回路
起 升 回 路
重物下降时,手动 换向阀18切换至右位工 作,液压马达反转,回 油经阀19的液控顺序阀, 阀18右位回油箱。
(5)起升回路
起 升 回 路
该液压系统的特点是: ①因重物在下降 时以及大臂收缩和变 幅时,负载与液压力 方向相同,执行元件 会失控,为此,在其 回油路上必须设置平 衡阀。 ②采用手动弹簧复位的多路换向阀来 控制各动作。换向阀常用M型中位机能。当 换向阀处于中位时,各执行元件的进油路 均被切断,液压泵出口通油箱使泵卸荷, 减少了功率损失。
第一节 组合机床动力滑台液压系统
一、概述 组合机床能完成钻、扩、铰、镗、 铣、攻丝等加工工序。动力滑台是组合 机床的通用部件,上面安装有各种旋转 刀具,通过液压系统使滑台按一定动作 循环完成进给运动。 液压动力滑台对液压系统性能的主 要要求是速度换接平稳,进给速度稳定, 功率利用合理,效率高,发热少。 二、YT4543型动力滑台液压系统工作原理 滑台技术参数: 工作压力: 4~5 MPa 最大进给力: 4.5×104 N 进给速度: 6.6~660 mm/min。
第7章 数控机床的液压与气压系统

P
1
2
3
4
5
6
7
8
9
10
Pa
图7-4 活塞式空气压缩机工作原理 1-弹簧 2-排气阀 3-吸气阀 4-气缸 5-活塞 6-活塞杆 7-十字头滑块 8-滑道 9-连杆 10-曲柄
空气压缩机按输出 压力大小可分为:低压 空压机(0.2~1MPa)、中 压 空 压 机 (1.0 ~ 10MPa) 、 高压空压机(10~100MPa) 和 超 高 压 空 压 机 (>100MPa);按输出流量 (排量)可分为:微型 (<lm3 / min) 、 小 型 (1 ~ l0m3 / min) 、中型(10 ~ l00m3 / min) 和 大 型 (>l00m3 / min) 空 气 压 缩 机。图7-5为空气压缩机 图7-5 空气杖缩机的类型 的几种见类型,表7-2是 空气压缩机的型式与性 a) 活塞式 b) 转子式 c) 离心式 d) 轴流式 能比较。
7.1.1 液压传动的工作原理
图7-1是液压千斤顶的工作原 G 理图。需要千斤顶工作时,向上 提起杠杆1则活塞2被提起,液压 7 缸3下腔中压力减小,单向阀5关 1 闭,单向阀4导通,油箱里的油液 被吸人到液压缸3中,这是吸油过 6 2 程;随后,压下杠杆1,活塞2下 11 3 移,液压缸3下腔中压力增大,迫 使单向阀4关闭,单向阀5导通, 5 4 9 高压油液经油管11流人液压缸6的 下腔中,推动活塞7向上移动,这 10 是压油过程。如此反复操作便可 将重物8提升到需要的高度。在此 过程中,控制阀9处于截止状态。 图7-1 液压传动的工作原理 打开控制阀9,则活塞6下腔中的 油 液 在 重 物 作 用 下 排 回 油 箱 1-杠杆 2、7-活塞 3、6-液压缸4、5-单向阀
压力机计算设计

一压力机主要技术参数二压力机运动学和动力学计算三电动机功率和飞轮的转动惯量的计算四、飞轮部分实际转动惯量五、齿轮啮合及齿轮强度的验算六、皮带轮传动的计算七离合器和制动器部分的计算八滑块部分计算九机身强度计算一压力机主要技术参数二 压力机运动学和动力学计算1﹑ 滑块行程和转角的关系 滑块行程S 由下式求得)]21(4)1[( αλαcos cos R S -+-= 式中:R —曲轴半径 mm R 250= α—曲轴转角 0-360度 L —连杆长度 mm L 1050= λ—连杆系数238.01050250===L R λ 在不同α值求得S 值列于下表: 单位(毫米)当发生公称力时,曲轴转角由下式求得:)(2)(222p p p S L R R L S L R R cos -+--++=α式中:p S —发生公称力时,滑块离下死点距离 mm S p 13= 代入得︒===-+⨯⨯--++=-70.169565.0 9565.0)131050250(25021050)131050250(2501222cos cos p p αα2、滑块速度与转角的关系)2sin 2(sin αλαω+⋅=R V式中 V —滑块的速度ω—曲柄等速旋转时的角速度, n n105.030=⋅=πωn —滑块每分钟行程次数 当滑块每分钟行程次数为10次/分秒弧度/05.110105.0105.0=⨯==n ω 秒毫米/5.26225005.1=⨯=⋅R ω根据上式可列下表: 单位(毫米/秒)3、滑块的加速度与曲转角的关系)2cos (cos 2αλαω+⋅-=R Jα—曲柄旋转角度 0-360度ω—曲柄等速旋转时的角速度, n n105.030=⋅=πωn —滑块每分钟行程次数 10次/分J —滑块加速度 米/秒2\由上式可知:当α=0度和α=180度时具有最大加速度Jmax=-1.0472×1.0472×250×(1+0.238)=-339.4m/s 24、曲柄上最大扭矩的计算 3.1摩擦力臂的计算)(μm m p M t +=式中: p —公称压力, kg p 630000= μm —摩擦当量力臂md d d m B A 04081.0 ]26.015.0238.086.0)238.01[(03.0 ])1[(20=+⨯+⨯+⨯=+⋅++=λλμμμ—摩擦系数, μ=0.06 A d —曲轴颈直径, mm d A 860= B d —球头直径, mm d B 150= 0d —曲轴支承颈直径, mm d 2600=)2cos (cos 2max αλαω+⋅-=R Jt m —理想当量力臂mR m t 0.088227 ))7.162sin(20.238.70.25(sin16)2sin 2(sin =︒⨯+︒=+=αλα 将以上数值代入上式:曲轴传递的扭矩:mKgf m m P M t k ⋅=+⨯=+=81270 )08827.004081.0(630000 )(μ对双点压力机,每个齿轮承受的扭矩为总扭矩的5/8=0.625 每个齿轮承受的扭矩M单 单个曲轴传递的扭矩:m kgf m m p M t g ⋅=⨯⨯⨯=+=50800 129.01063085)(853μ单5﹑ 传动轴上的扭距mkgf M m kgf i M M C K c .16560.1655806.597.081270==⨯=⋅=取低η6﹑离合器轴的扭距mkgf M m kgf i M M L C L .2220.780.221969.797.016560==⨯=⋅=取高η7﹑ 滑块上允许的载荷的确定传动系统的零部件是以曲轴上最大扭距K g Km P M ⋅=设计的.滑块上允许负载在滑块行程范围内变化的, 滑块行程在下死点13mm 处滑块的允许压力称其公称力,即滑块的公称力P=P g =6300000KN,当017 α时,kKg m M P =a(度)16.72030405060708090m (cm)12.914.5419.1623.0826.1628.329.4929.7229.08Pg(KN)630558.941424.16352.123310.665287.17275.585273.45279.47 (吨)630559424352310287276273280三 电动机功率和飞轮的转动惯量的计算1、 连续行程时,一次行程功的计算根据“曲柄压力机设计”一书中的公式:]57.1973.054.1[1S m S S S S K SP E P P g μ+-=式中:Pg —公称压力 (吨) Pg=630吨 S —滑块行程(毫米) S=500mm S P —滑块公称力行程(毫米) S P =13mmm μ—摩擦当量力臂(毫米) m μ=40.814mm K 1—经验系数。
《压力加工设备》第七章2013-7剪切机

(2)刀片尺寸
刀刃长度
刀片断面高度
h’=(0.65~1.5)hmax
刀片断面宽度
剪切次数—理论剪切次数大于实际剪切次数,表征剪切能力。
5、 平 行 刀 片 剪 切 机 结 构
(1) 曲 柄 连 杆 上 切 式 剪 切 机
1-机架 2-曲轴 3-上刀台平衡油缸(传动侧)4-上刀台平衡油缸 (操作侧) 5-压板 6-上刀台行程扩大装置 7-连杆 8-上刀台压紧 油缸 9-上刀台连杆垫块 10-上刀台本体 11-下刀台 12-下刀台夹 紧油缸 13-下横梁
1-刀架 2-曲柄轴 3-摆杆 4-传动齿轮 ①剪刃作平面运动,切口质量好; ②运动特性差,最大剪切速度2.2m/s; ③传动机构多,复杂; ④剪切轧件厚度h 小于6mm。
4、曲柄偏心式飞剪机
1-小齿轮 2、11-传动导架的齿轮 3、4-铰链 5-双臂曲柄轴的曲柄 头 6-连杆 7-摆杆 8-刀架 9-双臂曲柄轴 10-导架 12-偏心轴 13、 14-传动偏心轴的齿轮 15-刀片 16-滚动轴承
2、上切式斜刀片剪切机
特点:下刀片固定不动,上刀片向下运动剪切轧件。
配置:单独设置或组成独立的剪切机组。 齿轮转动方式:
a-单面传动 b-双面传动 c-下传动
3、下切式斜刀片剪切机
上刀片固定不动,下刀向上运动剪切轧件。
设置:连续作业线上 应用:剪切板带的头部、尾部、分卷和剪切掉有缺陷的部分 驱动方式:
应用及工作制度:连续式热带钢精轧机组前切头,只有剪 切机构,启动工作制; 板带横切机组切定尺,有剪切机 构、空切机构及匀速机构,连续工作制。
工作原理:飞剪的剪切机构是
由刀架、偏心套筒、摆杆组成 的四连杆机构。当偏心套筒 (曲柄)转动时,刀架在剪切 区域内做近似平移运动,刀片 能垂直或近似垂直于轧件,所 以剪切断面比较平整。 空切机构:摆杆2的摆动支点铰 接在可升降的立柱3上,3下降, 两剪刃不相遇,实现空切。
机械基础第七章 轮系

这种由一系 列相互啮合的齿 轮组成的传动系 统称为轮系。 称为轮系。 称为轮系
第七章 轮系
第一节 轮系分类及应用
1.了解轮系的分类。 2.了解轮系的特点及应用。
第七章 轮系
如图所示的铣床滑移齿轮变速箱、汽车 变速器是如何实现变速和变向的?它们属于 哪种轮系呢?有何特点?
铣床滑移齿轮变速箱
∴nⅣ=n1 × Z1/ Z2 × Z3/ Z4× Z5/ Z6 nⅣ= 1000×1/40×18/54×24/32=6.25(转/分)
第七章 轮系
【例2】在图示定轴轮系,主动轴Ⅰ上采用一个三联滑移齿轮,若已知轴Ⅰ的转速n1 例 =1000转/分,Z1=28,Z2=56,Z3=48,Z4=56,Z5=20,Z6=30,Z7=60,Z8=20,求从动轴 Ⅲ有几种转速?最快转速、最慢转速各是多少?图示情况下轴Ⅱ的转速是多少? 【解】轮系的传动路线:
Z2 Z4
56×57
当n1=50r/min时,砂轮架移动速度为: V=n1 Z1Z3 Ph=50× 28×38×3=50(mm/min)
Z2 Z4
56×57
因丝杠为右旋,砂轮架向右移动(如图所示)。
第七章 轮系
2.末端是齿轮齿条传动的计算 .
L=N末·π·m·Z末=N1 · 所有主动轮齿轮连乘积 ·π·m·Z末 (mm) 所有从动轮齿轮连乘积 所有主动轮齿轮连乘积 ·π·m·Z末 (mm/min) 所有从动轮齿轮连乘积
40 × 100 × 20 × 30 = −10 20 × 20 × 30 × 20
= (−1) 3
“-”号表示首、末两轮转向相反。
第七章 轮系
【例2】如图所示空间定轴轮系,已 】 知主动轮的转速n1=1000r/min,各齿 轮的齿数Z1=1, Z2=40, Z3=20, Z4=80, Z5=20,Z6=60,求总的传动 比i16?
高速切削与高速机床分解
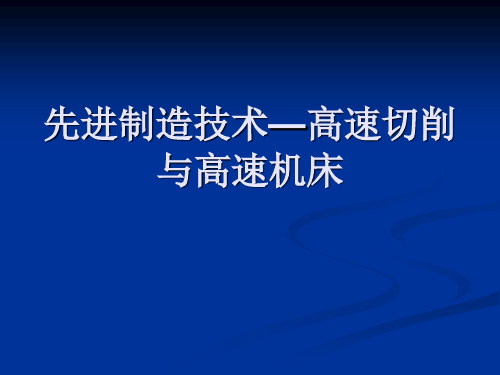
高速切削加工的研究
(2)床身部件
为了适应粗精加工、轻重切削和快速移动,同时保证高精度,高速 切削机床必须具有足够的刚度、强度和阻尼特性以及高的热稳定性。 大部分机床都采用高质量、高刚性和高抗张性的灰铸铁作为支撑部 件材料,有的公司还在底座中添加高阻尼特性的聚合物混凝土,以增加 其抗振性和热稳定性,不但保证了机床精度稳定,也可防止切削时刀具 振颤;也有采用封闭式床身设计,整体铸造床身,“箱中箱”结构或对 称床身结构并配有密布的加强筋,如法国Forest line公司的高架三龙门五 坐标Mi2numac 30TH数控铣床;德国DeckelMaho公司的桥式结构或龙门 结构的DMC系列高速立式加工中心,使机床获得了在静态和动态方面更 大限度的稳定性。
1996年首次研制出采用直线电机驱动的3D铣削中心;
2000年研制出采用直线电机驱动的最优化的铣削中心。
高速切削加工的研究
1. 高速切削机理研究
高速切削机理是高速切削技术应用和发展的理论基础。 研究成就比较突出的是美国洛克希德导弹和空间公司的科 学家罗伯特· 金(RobetI1King) 和麦克唐纳(Mcd1nddJ),从 理论上证实了高速切削的可行性和优越性。他们的研究主 要在切屑成形理论、金属断裂、突变滑移、绝热剪切以及 各种材料的切屑成形方面。
的20多年时间里,没有人对此进行深入系统的研究。
直到50 年代末期, 美国工程师Robert L.Vaughan才开始
继续Salomon的研究工作,从切屑形成过程和切屑形态的变化, 说明了高速切削时切削机理将发生变化,切削过程将变得容 易和轻松。此后美国、日本、英国等国家才先后有人开始高
速切削机理及相关技术的研究,其中以德国Darmstadt工业大
《机械设计基础》第7章 蜗杆传动

tanγ= z1/q d1 = q m q是d1与m的比值,不一定是整数。 m一定时,q越小(或d1越小)导程角γ越大,传动效率 越高,但蜗杆的强度和刚度降低。 设计蜗杆传动,在刚度准许的情况下,要求传动效率高 时q选小值;要求强度和刚度大时q选大值。
蜗杆直径系数q
q = d1/m
P1----蜗杆传动输入功率,kW;ks----为散热系数,根据箱体周围通风 条件,一般取ks =10~17[w/(m2·℃)];自然通风良好地方取大值,反 之取小值; η----传动效率;A----散热面积m2。 t0----周围空气温 度℃ 通常取20℃; [t1]----许可的工作温度,通常取70~90℃。
齿圈与轮芯用铰制孔螺栓联接。由于装拆方便,常用尺寸较大或磨损后 需要更换蜗轮齿圈的场合.
浇铸式:(图7-10c) 该型式仅用于成批生产的蜗轮。齿圈最小厚度c=2m,但不小于10 mm
§7-4 蜗杆传动的强度 计算 蜗杆传动的受力分析
蜗轮旋转方向的判定
蜗轮旋转方向,按照蜗杆的螺旋线旋向和旋转方
蜗杆传动的特 点
§7-2 蜗杆传动的主要参数和几何尺 寸 概念(图7-6)
连心线:蜗杆轴线与蜗轮轴线的公垂线。 中间平面:圆柱蜗杆轴线和连心线构成的平面。 所以中间平面内蜗杆与蜗轮的啮合相当于渐开线 齿轮与齿条(直线)的啮合
规定:设计计算以中间平面参数及其几何尺寸关系为准。 主要参数
1.模数m和压力角α;2.传动比i,蜗杆头数z1和蜗 轮齿数z2 ; 3.蜗杆导程角γ; 4.蜗杆分度圆直径d1和蜗杆直径系数q ;5.中心距a。
5.中心距a。
标准蜗杆传动其中心距计算公式:
a=
d1+d2 2
= m (q+z2) 2
第七章典型液压系统(1)

第七章典型液压系统(1)第七章典型液压系统★学习⽬的与要求了解液压技术在国民经济各⾏各业中的应⽤;熟悉各种液压元件在液压系统中的作⽤及各种基本回路的构成;掌握分析液压系统的步骤和⽅法。
根据给定的有关条件读懂液压传动系统(特别是中等以上复杂程度的液压传动系统)是学习液压传动课程的主要⽬的之⼀。任何⼀液压传动系统都是由⼀些液压元件、液压基本回路按照⼀定的负载要求设计⽽成,因此能否读懂和正确分析液压传动系统是对所学液压件及液压基本回路的结构、⼯作原理、性能特点、应⽤和液压基本知识的检验和综合。对给定的液压传动系统,在读懂的前提下,通过分析、对⽐,应能指出该系统在调速、调压、换向等⽅⾯的特点、不⾜,以致能提出改进的措施和建议。这样,不仅对熟悉和掌握具有该系统的设备有利,对类似的液压系统的设计也有帮助。
★重点:液压动⼒滑台是组合机床的通⽤部件,其液压传动系统是机床类的典型液压传动。通过对该液压系统特点的分析可了解⼀般机床液压传动的情况。因此要读懂、分析好动⼒滑台液压系统。
压⼒机械(设备)是体现液压传动功率重量⽐⼤这⼀突出优点的典型设备,它不同于⼀般机床的液压传动,为了得到较⼤的压制⼒⽽⼜不使机器体积过于庞⼤,⼀般都采⽤⾼压(10MPa~40MPa),甚⾄超⾼压(80MPa~150MPa)。因此对液压机液压系统要读懂、吃透,尤其对类似液压机都有的泄压、快速回程动作过程及主缸与顶出缸的互锁应深⼊理解并掌握。
★内容提要⼀、分析液压系统的步骤(⼀)了解设备对液压系统的要求;(⼆)以执⾏元件为中⼼,将系统分解为若⼲块——⼦系统;(三)根据执⾏元件的动作要求对每个⼦系统进⾏分析,搞清楚⼦系统由哪些基本回路组成;(四)根据设备对各执⾏元件间互锁、同步、顺序动作和防⼲扰等要求,分析各⼦系统的联系;
(五)归纳总结整个系统的特点。⼆、组合机床动⼒滑台液压系统(⼀)概述组合机床是由通⽤部件和专⽤部件组成的⾼效、专⽤、⾃动化程度较⾼的机床。它能完成钻、扩、铰、镗、铣、攻丝等加⼯⼯序和⼯作台转位、定位、夹紧、输送等辅助动作。动⼒滑台是组合机床的通⽤部件,上⾯安装有各种旋转⼑具,通过液压系统可使这些⼑具按⼀定动作循环完成轴向进给运动。1.YT4543型动⼒滑台动作循环快进—⼀⼯进—⼆⼯进—死挡铁停留—快退——原位停⽌2.YT4543型动⼒滑台液压系统组成由限压式变量叶⽚泵供油,⽤电液换向阀换向,⽤⾏程阀实现快进速度和⼯进速度的切换,⽤电磁阀实现两种⼯进速度的切换,⽤调速阀使进给速度稳定。3.组合机床动⼒滑台液压系统⼯作原理(1)差动快进1Y得电,电液换向阀处于左位,主油路经泵-单向阀13-液动阀12左位-⾏程阀8常位-液压缸左腔。回油路从液压缸右腔-阀12左位-单向阀3-阀8-液压缸左腔。