船体分段吊装工艺
浅谈船体分段复杂吊装方案自动化设计方法及运用
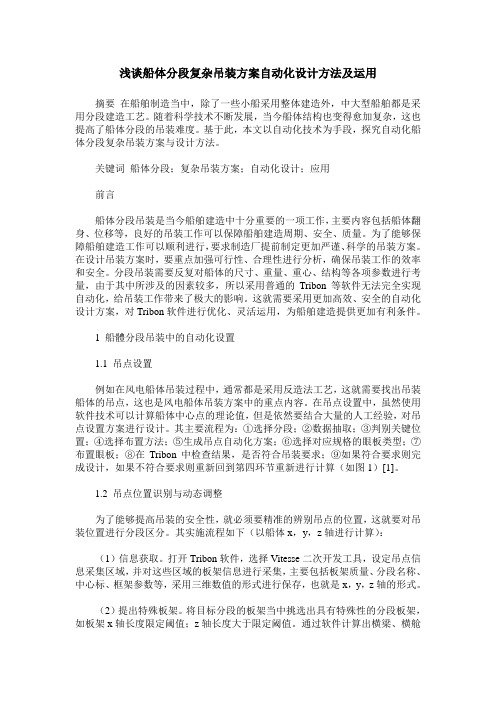
浅谈船体分段复杂吊装方案自动化设计方法及运用摘要在船舶制造当中,除了一些小船采用整体建造外,中大型船舶都是采用分段建造工艺。
随着科学技术不断发展,当今船体结构也变得愈加复杂,这也提高了船体分段的吊装难度。
基于此,本文以自动化技术为手段,探究自动化船体分段复杂吊装方案与设计方法。
关键词船体分段;复杂吊装方案;自动化设计;应用前言船体分段吊装是当今船舶建造中十分重要的一项工作,主要内容包括船体翻身、位移等,良好的吊装工作可以保障船舶建造周期、安全、质量。
为了能够保障船舶建造工作可以顺利进行,要求制造厂提前制定更加严谨、科学的吊装方案。
在设计吊装方案时,要重点加强可行性、合理性进行分析,确保吊装工作的效率和安全。
分段吊装需要反复对船体的尺寸、重量、重心、结构等各项参数进行考量,由于其中所涉及的因素较多,所以采用普通的Tribon等软件无法完全实现自动化,给吊装工作带来了极大的影响。
这就需要采用更加高效、安全的自动化设计方案,对Tribon软件进行优化、灵活运用,为船舶建造提供更加有利条件。
1 船體分段吊装中的自动化设置1.1 吊点设置例如在风电船体吊装过程中,通常都是采用反造法工艺,这就需要找出吊装船体的吊点,这也是风电船体吊装方案中的重点内容。
在吊点设置中,虽然使用软件技术可以计算船体中心点的理论值,但是依然要结合大量的人工经验,对吊点设置方案进行设计。
其主要流程为:①选择分段;②数据抽取;③判别关键位置;④选择布置方法;⑤生成吊点自动化方案;⑥选择对应规格的眼板类型;⑦布置眼板;⑧在Tribon中检查结果,是否符合吊装要求;⑨如果符合要求则完成设计,如果不符合要求则重新回到第四环节重新进行计算(如图1)[1]。
1.2 吊点位置识别与动态调整为了能够提高吊装的安全性,就必须要精准的辨别吊点的位置,这就要对吊装位置进行分段区分。
其实施流程如下(以船体x,y,z轴进行计算):(1)信息获取。
打开Tribon软件,选择Vitesse二次开发工具,设定吊点信息采集区域,并对这些区域的板架信息进行采集,主要包括板架质量、分段名称、中心标、框架参数等,采用三维数值的形式进行保存,也就是x,y,z轴的形式。
船体分段吊装工艺探索分析

船体分段吊装工艺探索分析一、引言船体分段吊装工艺是指将船舶整体结构分为几个大块进行吊装组装的工艺,是船舶建造过程中的关键环节。
它不仅直接关系到船舶建造周期和质量,还影响着船舶的性能和安全。
对船体分段吊装工艺进行探索分析,可以有效提高船舶建造效率,保证船体各部分之间的组装连接质量,提高船舶整体结构的稳定性和安全性。
本文将从工艺流程、工艺优化和安全管理三个方面进行船体分段吊装工艺的分析探索。
二、工艺流程的分析船体分段吊装工艺的工艺流程主要包括分段设计、吊装设备选择、现场操作等环节。
分段设计是整个工艺流程的重要环节,它需要根据船舶设计图纸和各结构部件的特点,确定每个分段的大小、形状和重量,以便后续的吊装和组装。
对吊装设备的选择也至关重要,合适的吊装设备可以保证吊装过程的顺利进行,同时确保吊装操作的安全。
现场操作是工艺流程中的关键环节,在吊装过程中需要严格按照操作规程进行操作,确保分段的精准吊装和准确组装。
对工艺流程的分析可以发现,在每个环节都存在着一定的复杂性和技术难度,需要工程技术人员具备丰富的经验和专业知识,才能顺利完成各项工作。
为了提高工艺流程的效率和质量,需要不断探索和优化各个环节,提高工艺流程的整体水平。
三、工艺优化的探索在船体分段吊装工艺中,工艺优化是提高工艺流程效率和质量的关键。
针对分段设计环节,可以通过优化设计方案,减少分段数量和提高分段结构的统一性,从而减少吊装次数和减轻工艺负担。
对吊装设备的选择也可以通过技术更新和设备更新,提高设备的吊装能力和操作灵活性,从而提高工艺流程的效率和安全性。
在现场操作环节,可以通过培训操作人员和引入先进的智能化技术,提高操作人员的技术水平和操作的精准度,确保吊装和组装过程的顺利进行。
工艺优化的探索需要在实际的工作中不断进行尝试和总结,同时结合船舶建造的实际情况,提出切实可行的优化方案。
需要密切关注吊装技术和设备技术的发展趋势,及时引进并应用先进的技术和设备,为工艺优化提供技术支撑。
船体分段吊装工艺探索分析

船体分段吊装工艺探索分析船舶在建造过程中需要进行船体分段吊装工艺,这是一个非常重要的环节,直接关系到船体分段的安全和质量。
为了更好地探索船体分段吊装工艺,本文将对该工艺进行深入分析和探索。
一、船体分段吊装工艺的重要性和现状船体分段吊装工艺对于船体建造来说意义重大。
船舶的建造通常是将船体分为若干个标准的分段,然后在船台上逐个吊装、组装并焊接成最终的船体形态。
成功的船体分段吊装工艺可以保障船体的整体结构完整性和质量,提高船舶建造的效率和安全性。
目前,船体分段吊装工艺在船舶建造中已经得到了广泛的应用,但也存在一些问题和挑战。
在吊装过程中容易出现分段变形、损坏等情况,对建造质量和进度造成影响。
对船体分段吊装工艺的探索和分析就显得尤为重要。
船体分段吊装工艺的探索和分析,需要深入研究其中的技术要点和难点。
具体来说,船体分段吊装工艺涉及到吊装设备的选择、吊装方案的制定、吊装过程的控制等多个方面。
在吊装设备的选择上,需考虑到分段的重量、形状、重心位置等因素,选择合适的起重机、吊索等设备。
在吊装方案的制定上,需考虑到吊装的顺序、角度、速度等因素,确保吊装过程的稳定和安全。
在吊装过程的控制上,需建立起一套完善的操作程序和安全预案,以应对各种突发情况。
船体分段吊装工艺中存在的难点也不容忽视。
在吊装过程中如何防止分段发生倾斜或旋转,如何避免分段与起重设备之间发生碰撞等问题都需要认真思考和解决。
为了更好地探索船体分段吊装工艺,我们可以从以下几个方向进行深入分析和研究。
可以从船体分段的设计和制造入手,优化分段的结构和形状,减少分段的重心偏移,提高分段的整体稳定性和可吊装性。
可以从吊装设备和技术方案入手,研究各种吊装设备的特性和适用范围,设计出更科学、更安全的吊装方案,提高吊装效率和质量。
可以从吊装过程的控制和管理入手,建立起一套完善的吊装作业程序和安全管理制度,提高吊装作业的安全性和可控性。
可以从吊装工艺的标准化和规范化入手,制定出统一的吊装操作规程和标准,提高吊装作业的一致性和可操作性。
船体分段吊装工艺探索分析
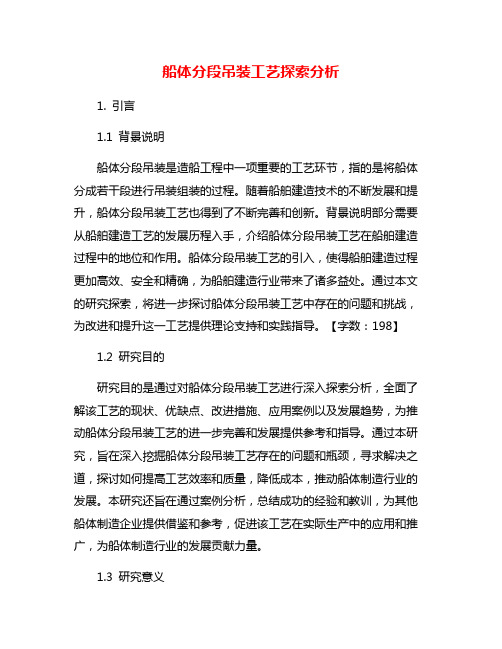
船体分段吊装工艺探索分析1. 引言1.1 背景说明船体分段吊装是造船工程中一项重要的工艺环节,指的是将船体分成若干段进行吊装组装的过程。
随着船舶建造技术的不断发展和提升,船体分段吊装工艺也得到了不断完善和创新。
背景说明部分需要从船舶建造工艺的发展历程入手,介绍船体分段吊装工艺在船舶建造过程中的地位和作用。
船体分段吊装工艺的引入,使得船舶建造过程更加高效、安全和精确,为船舶建造行业带来了诸多益处。
通过本文的研究探索,将进一步探讨船体分段吊装工艺中存在的问题和挑战,为改进和提升这一工艺提供理论支持和实践指导。
【字数:198】1.2 研究目的研究目的是通过对船体分段吊装工艺进行深入探索分析,全面了解该工艺的现状、优缺点、改进措施、应用案例以及发展趋势,为推动船体分段吊装工艺的进一步完善和发展提供参考和指导。
通过本研究,旨在深入挖掘船体分段吊装工艺存在的问题和瓶颈,寻求解决之道,探讨如何提高工艺效率和质量,降低成本,推动船体制造行业的发展。
本研究还旨在通过案例分析,总结成功的经验和教训,为其他船体制造企业提供借鉴和参考,促进该工艺在实际生产中的应用和推广,为船体制造行业的发展贡献力量。
1.3 研究意义船体分段吊装工艺是船舶建造中至关重要的一个环节,它直接关系到船体各个部分的吊装、拼装和安装。
船体分段吊装工艺的研究意义主要表现在以下几个方面:1. 提高生产效率:船体分段吊装工艺的合理设计和实施,可以有效地提高船体制造的生产效率。
通过优化吊装工艺,减少吊装时间和劳动力成本,从而提高生产效率和降低制造成本。
2. 提高建造质量:船体分段吊装工艺的研究可以帮助优化船体的组装顺序和方法,提高船舶各部件的装配精度和稳固性,从而提高船舶的建造质量和整体性能。
3. 促进技术创新:通过深入研究船体分段吊装工艺,可以促进船舶建造工艺的创新和发展,推动相关技术的进步和应用,为船舶制造业的发展提供技术支撑和保障。
船体分段吊装工艺的研究意义在于提高生产效率、提高建造质量、促进技术创新,为船舶制造业的可持续发展提供技术支持和保障。
船体分段制作工艺流程

船体分段制作工艺流程船体分段现场制造工艺流程生产范围大组立是船舶制造的一种生产管理模式,是船体分段装配的一个生产阶段。
就是将零件和部件组成分段的生产过程。
人员搭配大组立生产以班为单位,一个班一般分为三到四个班组,一个班组的成员有一个组长、三个师傅、六个徒弟、两个电焊工、一个打磨工。
图纸资料大组立相关图纸有零件明细表、产品完工图、制作工艺、焊接工艺等。
工具割枪、米尺、线垂、千斤顶、水平尺、水平管、花兰螺丝、铁锤、铁楔、角尺、电焊机、自动二氧化碳焊接、打磨机机舱双层底大组立机舱双层底工艺流程胎架或平台准备——铺内底板——构件安装位置划线——构件安装——焊接——管铁舾装安装焊接——外板安装——焊前检查——构件与外板焊接——打磨——密性实验——交验装配作业标准分段长:L <±4mm分段宽: B <±4mm分段高:H <±4mm分段方正度:(内底板四角水平)<±8mm(加测机座内底板水平)货舱双层底大组立工艺流程胎架或平台准备——内底板拼装——自动二氧化碳焊接——构件安装位置划线——内底纵骨安装焊接——构件小组(肋板)安装焊接——舾装——补漆¬外底板拼装——焊接——构件安装位置划线——外底纵骨装焊——组装完成——焊接——打磨——舾装——完工检查——报验装配作业标准分段长:L <±4mm分段宽:B <±4mm分段高:H <±3mm分段方正度:<4mm (内、外底板对角线差值)分段扭曲度:<±8mm (内底板四角水平)纵骨端平面度:<±4mm内、外底板中心线偏差<±3mm内、外底板肋位线偏差<±3mm货舱顶边水舱大组立货舱顶边水舱分段工艺流程胎架或平台准备——斜板拼装——焊接——构件安装位置划线——斜板纵骨安装焊接——构件(肋板)安装焊接——舾装——补漆¬甲板拼装——焊接——纵骨装焊——组装完成——焊接——打磨——舾装——完工检查——报验装配作业标准分段长: L <±4mm分段宽: B <±4mm分段高: H <±4mm分段方正度:(测上甲板)<4mm分段扭曲度:(上甲班)<±8mm纵骨端平面:<±4mm货舱舭部大组立工艺流程胎架或平台准备——斜底板拼装——焊接——构件安装位置划线——斜底纵骨安装焊接——构件小组(肋板)安装焊接——舾装——补漆¬外底板拼装——焊接——构件安装位置划线——外底纵骨装焊——组装完成——焊接——打磨——舾装——完工检查——报验装配作业标准分段长: L <±4mm分段宽: B <±4mm内底高:H1±3mm舭部尖顶高:H2±4mm分段方正度:(测斜板)<4mm分段扭曲度:(测斜板)<±8mm。
浅谈船舶在上层建造分段中的重要流程

浅谈船舶在上层建造分段中的重要流程摘要:本文详细描述了船舶上层建筑分段建造工艺流程、总组合拢工艺及合拢后整体校正工艺,提出建造船必须规范建造工艺流程,制定各流程质量标准,提高建造精度,才能确保上层建筑分段分道建造,船台整体吊装的质量和周期。
关键词:船舶建造上层建造分段1.上层建筑分段建造储备工艺1.1材料起水、吊运工艺要求(1)材料起水吊运按我司场地起重设备条件,采用磁吸吊进行板材起水吊运;(2)磁吸吊吊运板材要求每次起吊一张钢板。
1.2材料堆放工艺要求(1)板材吊运至钢板堆场后,要求根据板材船级社认证等资料进行分类摆放,摆放时要求每张板材端部的船级社认证、炉批号、规格等信息必须可视,以确保后续板材检验及记录。
(2)板材堆放过程中,板材放落前,要求对下面一张板材表面进行杂质清洁,并沿板材宽度方向垫放3条以上垫木。
1.3材料吊运上线方式及工艺板材上预处理线的吊运方式为磁吸吊,磁吸吊吊运板材要求每次起吊一张钢板。
2.材料预处理工艺要求2.1预处理涂装工艺要求材料预处理工艺要求严格按照《车间底漆质量控制》,对材料外观检验、温度、相对湿度、钢板温度、盐分、清洁度、粗糙度及漆膜厚度等指标进行控制;2.2材料预处理后检验要求(1)双面检查板材是否存在麻点。
(2)材料流出预处理线后,材料吊运方式为磁吸吊吊运,磁吸吊吊运板材要求每次起吊一张钢板。
(3)材料流出预处理线后,要求对材料按批次、船级社认证、炉批号、规格等进行分类堆放,并显示材料端头板材信息,便于后续检验和记录。
3.分段板材和型材下料工艺3.1数控下料(HGG型材流水线)。
技术中心提供数控下料指令,加工作业区使用等离子数控切割机按指令进行下料。
等离子数控下料切割过程精度控制要求:(1)数控切割机参数确定。
上建分段下料阶段加工作业区根据本厂数控切割机自身的切割精度统计数据,按照FPSO上建板材厚度,确定满足下料精度要求的“割缝补偿”参数,确保零件下料尺寸偏差范围为0-2mm。
6-1 分段建造的方法
船 体 装 配
第一节 分段建造的方法
两个预备概念 ——
÷ 船体装配的定义 ÷ 船体装配的工作内容
将加工合格的船体零件 组合成部件、分段、总 段直至船体的工艺过程
船体装焊
结构预装焊 船舶总装
部件装焊 分段装焊
总组装
一、分段类型与建造方法
分段(section):
由零、部件组装而成的船体局部结构。
插入法
(4)框架法(frame method of assembling)
先将纵、横构件组装成箱形框架,再与板列组装在一起形成分段。 ① 特点: 【顺口溜】 纵横组装框架, 钢板拼成板列; 适合平直分段, 便于自动焊接。 ② 优点 可变立焊为俯焊,便于框架焊接采用机械化;工作面得以扩展;有利 于减小焊接变形;缩短分段制造周期。 ③ 缺点 板列和框架之间的协调较困难;不适用非格子状框架的分段;要吊运 分段。 ④ 适用范围
船体分段装配实录
返回小结
返回4
四、分段制造过程中的精度要求和检验方法
1、胎架检验 作用:使分段的装配和焊接工作具有良好的条件。 2、画线检验 其操作应对照分段工作图,依据草图、样条、样板等,先用 激光经续仪画出角尺基准线,然后画出各种结构线、开口线 和大接缝线,按分段焊接表,画出断续焊焊段尺寸,提交检 验。 3、平面和曲面分段检验 4、立体分段检验 对分段的外形尺寸、构件尺寸、构架位置、零件数量、装配 精度和焊接质量的检验。 5、完工检验 对分段进行尺度和外形测量之后的完整性检验。
分离法
(2)放射法(cell method of assembling) 按照从中央向四周的放射状方向,依此交替地装配纵、横 构件并焊接。 ① 特点: 中间构件先装。 【顺口溜】 中间构件要先装, 再向前后左右靠; 边装边焊变形小, 相互配合安排好。 ② 优点 引起分段变形较小;装配作业面积大,进度快。 ③ 缺点 工作连续性差,需要起吊设备和人员随时配合吊装。 ④ 适用范围 曲率变化大、钢板较薄的分段。
浅谈船舶分段吊装工艺
浅谈船舶分段吊装工艺发布时间:2021-01-21T03:15:35.251Z 来源:《中国科技人才》2021年第2期作者:雷励[导读] 在现代造船生产活动中,为了减少船舶制造的周期,大多数船厂都会采用的分段建造这种工艺方法,分段建造时,为保证结构焊接质量,提高分段施工效率,很多分段需要以反造或侧造的流程进行建造,尽可能地将仰角焊位和立角焊位转化为平角焊位施工。
启东中远海运海洋工程有限公司江苏南通 226200摘要:在现代造船生产活动中,为了减少船舶制造的周期,大多数船厂都会采用的分段建造这种工艺方法,分段建造时,为保证结构焊接质量,提高分段施工效率,很多分段需要以反造或侧造的流程进行建造,尽可能地将仰角焊位和立角焊位转化为平角焊位施工。
待分段建造完成之后,再进行二次吊运进行搭载合拢。
因此,分段的吊装作业成为船舶建造过程中的一个重要环节,为保证分段建造过程的安全生产,吊装工艺应综合考虑计算,以免分段在吊装过程中发生严重变形和损坏,造成事故。
关键词:分段建造;重量重心;吊耳设计分段吊装是指利用起重设备对船舶分段结构件进行起吊、移位、翻身、安装等作业。
作为分段建造过程中的一项重要工作,吊装作业关心着船舶建造的安全性、便捷性、高效性,甚至影响船舶建造的周期。
因此,在进行分段吊装工艺方案设计时,要对分段的重量尺寸、坐胎方向布局、起重设备性能、吊绳卸扣配备等各方面因素综合考虑,从而得出最合理、最优化的吊点布置方案,保证吊装作业高效进行,保障船舶建造安全生产。
1 舶分段建造时,生产现场的起重、运输能力的需要与分段的结构重量和外形尺寸相匹配,在进行船舶分段吊装方案设计之前,应该先行考虑这方面的因素,并在船舶分段划分阶段将这项工作落实到位。
分段结构重量是船舶进行划分时首先应考虑的因素,直接影响着后续的吊装运输作业。
因此,船舶分段重量应当精准预测,不得出现较大误差。
在对分段重量进行预测时,需从以下方面着手:充分计算船舶分段的船体结构和焊接量,不得有重量超差问题;分段上需要预装的舾装件、管装件、工装件等各类重量应进行统一性的计算;分段建造时需要搭设的临时脚手架及工装加强结构应该按照一定比例进行计算。
船体分段吊装工艺探索分析
船体分段吊装工艺探索分析摘要:在世界经济一体化的背景下,航海运输发挥了重要作用,使得各国之间的经贸往来越来越频繁。
这也使得船舶工业在近些年高速发展,创造了巨大的经济市场。
我国是世界上拥有比较先进造船技术的国家,能够使用多种不同的工艺来提高船舶的性能。
本文将对船体分段吊装工艺进行研究。
关键词:船体;分段吊装;吊装工艺引言:目前,分段吊装过程是船舶建造的关键环节。
船舶制造是我国十分重视的领域,正在不断加大资金和技术投入,并取得了良好的效果。
在船舶建造过程中,涉及到许多不同的工艺流程,其中吊装是十分重要的一个环节,将对船舶的整体质量构成比较重要的影响,因此就需要结合实际情况对船体分段吊装工艺进行优化。
1船体分段吊装工艺概述1.1船体分段吊装工艺内涵概述船体分段吊装是指施工单位使用起重设备对船体分段进行翻身或移位的作业工作,是船舶建造过程中的一项重要工作,对船体建造的安全、质量和周期起着至关重要的作用。
为保证吊装作业的顺利进行,大多施工单位均要在作业前进行严密的吊装方案设计。
吊装方案设计的可行性与合理性,直接决定了吊装工作能否安全、高效的进行。
船舶的建造是一个非常复杂的过程,目前比较成熟的工艺为分段建造,对每一段单独组织生产和规划,按照规定的时间,选取合理的地理环境建造,并最终在船坞等地方完成船舶的吊装和焊接,最终实现大型船舶的建造。
在上述过程中,船舶的分段吊装与焊接是一个非常关键的环节,该环节的质量直接决定了船舶建造是否成功。
1.2船体分段吊装工艺内容船体分段吊装工艺相对来说是一个比较复杂的工作,涉及到许多细节性操作,都会对整体工作的效果构成重要影响。
吊装过程中,一般被吊物的质量比较大,体积相对也比较大,这就给实际工作的展开带来了一些困难。
需要使用更加先进的吊装技术才能够完成吊装工作,降低危险性。
一般在实际船舶制造吊装工作中,都需要使用一些大型的辅助设备,确保被吊物的稳定传输。
吊装工作的区域比较密集,主要是在船坞内进行,船坞内还有其他工人进行焊接等工作,因此就有可能因为工作区域过于密集造成一定的危险性,需要能够对施工现场进行有序指导,才能够确保所有工作有条不紊的进行。
分段吊装工艺
56米金枪鱼钓船吊装工艺为了确保金枪鱼钓船主甲板以下分段安全吊装,特制定本工艺。
1.第1分段:艉~#1+150重量~ 吨长×宽×高 4.4×8.5×1.5m吊攀位置:#-5、#0肋骨左右舷对称各一个。
高度中心点现场定。
2.第2分段:#1+150~#13-150重量~ 吨长×宽×高 6.6×8.5×4.5m吊攀位置:#5、#10肋骨左右舷对称各一个。
高度中心点现场定。
3.第3分段:#13-150~ #27-150重量~ 吨长×宽×高7.7×8.5×4.1m吊攀位置:#16、#23肋骨左右舷对称各一个。
高度中心点现场定。
4.第4分段:#27-150~ #40+450重量~ 吨长×宽×高7.7×8.5×4m吊攀位置:#30、#37肋骨左右舷对称各一个。
高度中心点现场定。
5.第5分段:#40+450~#55-150重量~ 吨长×宽×高7.7×8.5×4 m吊攀位置:#45、#51肋骨左右舷对称各一个。
高度中心点现场定。
6.第6分段:#55-150~#69-150重量~ 吨长×宽×高7.7×8.5×4m吊攀位置:#58、#66肋骨左右舷对称各一个。
高度中心点现场定。
7.第7分段:#69-150~#85-150重量~ 吨长×宽×高8.8×7.5×4m吊攀位置:#73、#81肋骨左右舷对称各一个。
高度中心点现场定。
8.第8分段:#85-150~艏重量~ 吨长×宽×高4×2.4×4.3m吊攀位置:现场定。
9.在吊装肋位处舷侧肋骨与横梁用球扁钢加强,以防止吊装变形。
10.固定拉攀数量及位置数量及位置在分段离胎前一天由起重部门现场定。
- 1、下载文档前请自行甄别文档内容的完整性,平台不提供额外的编辑、内容补充、找答案等附加服务。
- 2、"仅部分预览"的文档,不可在线预览部分如存在完整性等问题,可反馈申请退款(可完整预览的文档不适用该条件!)。
- 3、如文档侵犯您的权益,请联系客服反馈,我们会尽快为您处理(人工客服工作时间:9:00-18:30)。
船体通用工艺------船体分段吊装工艺
船体分段吊装工艺
一、适用范围
1、适用于各种分段的吊装、翻身、移位、运输。
2、上建的整体吊装另见有关上层建筑整体吊装工艺。
二、工艺内容
随着生产规模不断扩大发展,所有工艺规程、施工细则、操作步骤、实施方法均应该制定相应的工艺文件。
以保证文明生产、提高产品质量。
船体的建造通常采用构件小组装、中组装(分段建造)、大组装(分段大合拢)的建造方式,有关建造中的吊装、翻身、移位、运输的起重工作须制定相应工艺文件,以保证船体建造和安全生产。
有关分段吊装、翻身、移位、运输工艺如下:
1.分段所采用的吊装、翻身眼板应进行专门的三化设计、即系列化、标准化、通用化。
并具有互换性和多次使用性,并有足够的强度和安全系数。
2.分段的划分,首先考虑分段的实际吊重(分段重量加上临时加强辅助材重量),应
符合吊车的许用负荷。
不得超过起重设备吊车的许用负荷。
3.在分段图中,标明吊装眼板、翻身眼板规格大小、安装位置及其数量。
4.眼板的焊接必须由二类以上的焊工施工。
焊接材料应用碱性焊条如结507及CO2
焊丝。
检验,验收。
5.分段吊装、翻身、移位、运输、堆放、上船台等起重工作均按照生产计划与作业场
地安排。
6.分段吊离胎架前,须检查,验收。
分段的实际吊重(分段重量加上临时加强辅助材
重量),应符合吊车的许用负荷,才可进行吊运工作。
7.分段起吊前,应检查分段吊运周围环境,人员情况,以确保安全,然后起吊。
8.分段到达堆放场地,要按照分段实际形状确定垫墩高度及垫墩位置,其最低高度不
低于600mm。
垫墩布置在分段有强构件结构位置,以避免分段变形、损坏。
9.分段翻身眼板确定,应预先在图纸中表明,并按下列要求进行:
a、根据分段尺寸、结构情况确定分段翻身方向(横翻、纵翻)。
b、翻身眼板位置要要考虑钢索与外板的相关位置,不损坏钢索。
c、吊车的安排,一般要根据生产场地设备配置情况而定。
-- 1 --。