液压油缸生产工艺流程
液压油缸活塞杆耐蚀500小时镀铬工艺方法附设备工艺参数1

液压油缸活塞杆耐蚀500小时镀铬工艺方法附设备工艺参数1工艺流程研磨操作--装挂-擦洗除油--喷淋水洗--反刻--镀无裂纹铬B(DCCFLC =脉冲自由分层裂纹铬15分)-冲洗--下挂--研磨处理--上挂--擦洗除油--喷淋水洗--反刻--镀无裂纹铬B(* DCSLC =脉冲单层铬15分)-镀微裂纹铬A(DCMCLC =脉冲直流微开裂分层铬35分)-冲洗-下挂-研磨抛光-检验研磨标准--Ra值 2.0-10Rz值12-20 微英寸反刻处理:时间45秒硬铬反刻工艺反腐蚀槽应该包含以下:时间:液压杆反刻20-45秒(2)活塞杆电镀铬工艺B-B/A双槽镀第一槽(DCCFLC =脉冲自由分层裂纹)B工艺:铬酐:250-350g/l 最佳值280硫酸:1.8-2.5g/l三价铬:2.5-5g/l添加剂A(DW-032A):20ml/l添加剂B(DW-032B):10g/l无氟抑雾剂C(DW-026): 0.05~0.15ml/l温度:55-59°电流密度:35-50A/dm2 阶梯给电5-10A/dm2, 5分正常电流10分电镀时间:10-15分占空比:60-80最佳70KAH消耗 A 50ml/l B 0.25- 0.5g/l 无氟抑雾剂C 0.01ml/l第二槽(DCMCLC =脉冲直流微开裂分层铬)A铬酐:220-280g/l 最佳值250硫酸:1.8-2.5g/l三价铬:2.5-5g/l添加剂A(DW-032A):60-80ml/l无氟抑雾剂C(DW-026): 0.05~0.15ml/l温度:55-57°电流密度:50-90A/dm2,阶梯给电5-10A/dm2, 5分,正常电流30分占空比:80-90最佳80反向无电镀时间:35分KAH消耗 A 50ml/l 无氟抑雾剂C 0.01ml/l电沉积双脉冲镀铬电源工艺参数电源电流:6000A电压18v 双脉冲电源双脉冲电沉积工艺的参数为:J ( 正向脉冲 ) 35-50A/dm 2正向占空比百分数 60 -80% 最佳70%正向脉冲工作时间 100ms正向周期 50 msJ ( 正向平均 ) 45 A/dm 2J ( 反向脉冲 ) 25-35 A/dm 2反向占空比百分数 20-40% 最佳30%反向脉冲工作时间 10ms反向周期 2 msJ ( 反向平均 ) 30 A/dm正反向脉冲频率f=200-300HZ。
液压子站工艺流程

液压子站工艺流程液压子站是一种用于控制液压系统的设备,它包括液压泵、阀门、油箱、油管、油缸等组件。
液压子站工艺流程是指液压子站的制造过程,包括设计、加工、装配、调试等环节。
下面将详细介绍液压子站工艺流程的各个环节。
1. 设计阶段液压子站的设计是整个工艺流程的第一步。
设计师根据客户的要求和液压系统的工作条件,确定液压子站的工作压力、流量、阀门类型、泵的选型等参数。
设计师还需要绘制液压子站的总装图、布置图、管路图等设计图纸,确保液压子站的各个部件能够合理布置和安装。
2. 加工阶段液压子站的加工是指对各个部件的加工制造过程。
液压泵、阀门、油箱、油管、油缸等部件都需要经过精密的加工工艺。
加工过程中需要使用各种机床设备,如车床、铣床、钻床等,对各个部件进行精确的加工和加工。
3. 装配阶段液压子站的装配是将加工好的各个部件进行组装。
这个阶段需要严格按照设计图纸和装配工艺要求进行。
首先是对各个部件进行清洗和检查,然后按照总装图进行组装。
在装配过程中需要使用各种工具和设备,如扭矩扳手、液压扳手、千斤顶等,确保各个部件的装配质量和紧固力。
4. 调试阶段液压子站装配完成后需要进行调试。
调试是为了验证液压子站的工作性能和安全性能。
首先是对液压系统进行压力测试,检查泄漏和压力损失情况。
然后进行流量测试,检查各个阀门和泵的工作流量是否符合要求。
最后进行动作测试,检查各个油缸和执行元件的动作是否准确、灵活。
在调试过程中需要使用各种测试仪器和设备,如压力表、流量计、液压试验台等,确保液压子站的工作性能和安全性能。
5. 验收阶段液压子站经过调试后需要进行客户验收。
客户验收是指将液压子站交付给客户使用前的最后一道工序。
客户需要对液压子站的工作性能和安全性能进行验收,确保液压子站符合客户的要求和使用要求。
在验收过程中需要提供相关的技术资料和使用说明书,以便客户能够正确使用和维护液压子站。
通过以上的工艺流程,液压子站的制造过程得以完成。
液压缸的结构及机械加工工艺分析
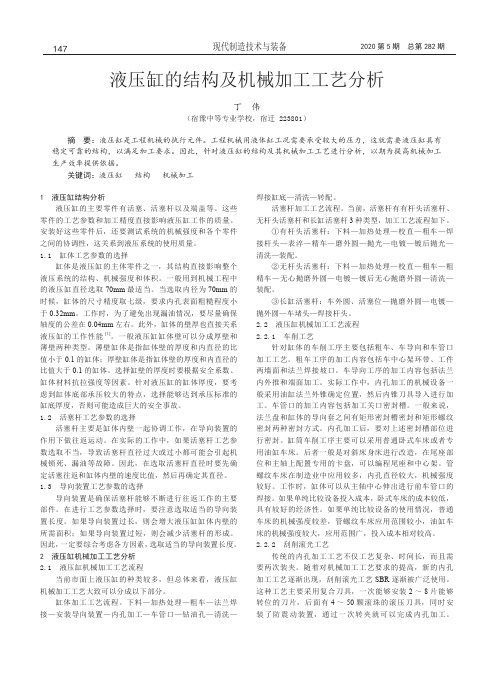
1 液压缸结构分析液压缸的主要零件有活塞、活塞杆以及端盖等。
这些零件的工艺参数和加工精度直接影响液压缸工作的质量。
安装好这些零件后,还要测试系统的机械强度和各个零件之间的协调性,这关系到液压系统的使用质量。
1.1 缸体工艺参数的选择缸体是液压缸的主体零件之一,其结构直接影响整个液压系统的结构、机械强度和体积。
一般用到机械工程中的液压缸直径选取70mm最适当。
当选取内径为70mm的时候,缸体的尺寸精度取七级,要求内孔表面粗糙程度小于0.32mm。
工作时,为了避免出现漏油情况,要尽量确保轴度的公差在0.04mm左右。
此外,缸体的壁厚也直接关系液压缸的工作性能[1]。
一般液压缸缸体壁可以分成厚壁和薄壁两种类型。
薄壁缸体是指缸体壁的厚度和内直径的比值小于0.1的缸体;厚壁缸体是指缸体壁的厚度和内直径的比值大于0.1的缸体。
选择缸壁的厚度时要根据安全系数、缸体材料抗拉强度等因素。
针对液压缸的缸体厚度,要考虑到缸体底部承压较大的特点,选择能够达到承压标准的缸底厚度,否则可能造成巨大的安全事故。
1.2 活塞杆工艺参数的选择活塞杆主要是缸体内壁一起协调工作,在导向装置的作用下做往返运动。
在实际的工作中,如果活塞杆工艺参数选取不当,导致活塞杆直径过大或过小都可能会引起机械锁死、漏油等故障。
因此,在选取活塞杆直径时要先确定活塞往返和缸体内壁的速度比值,然后再确定其直径。
1.3 导向装置工艺参数的选择导向装置是确保活塞杆能够不断进行往返工作的主要部件。
在进行工艺参数选择时,要注意选取适当的导向装置长度。
如果导向装置过长,则会增大液压缸缸体内壁的所需面积;如果导向装置过短,则会减少活塞杆的形成。
因此,一定要综合考虑各方因素,选取适当的导向装置长度。
2 液压缸机械加工工艺分析2.1 液压缸机械加工工艺流程当前市面上液压缸的种类较多,但总体来看,液压缸机械加工工艺大致可以分成以下部分。
缸体加工工艺流程。
下料—加热处理—粗车—法兰焊接—安装导向装置—内孔加工—车管口—钻油孔—清洗—焊接缸底—清洗—转配。
液压油缸加工工艺流程

液压油缸加工工艺流程图1、缸筒:a、备料(无缝钢管)→检验(材质证明书等)→调质(外包:部分零件)→车(车外圆、架子口、镗止口、法兰止口等)→调质硬度检测→焊(焊接管接头座、法兰等附件)→镗孔或珩磨(粗镗、精镗、滚压)→车(孔卡槽或内外螺纹)→钳工(钻油口)→检验→防锈入库b、备料(锻件)→检验(材质证明书、探伤等)→焊(毛坯对接焊)→焊接探伤→车(粗车)→调质(外包:部分零件)→车(车外圆、架子口、镗止口、法兰止口等)→调质硬度检测→焊(焊接管接头座、法兰等附件)→镗孔或珩磨(粗镗、精镗、滚压)→车(孔卡槽或内外螺纹)→钳工(钻油口)→检验→防锈入库2、活塞、导向套:a、备料(铸件、锻件)→检验(材质证明书、锻件探伤等)→粗车→精车→检验→防锈入库b、备料(圆钢)→检验(材质证明书等)→粗车→精车→检验→防锈入库3、活塞杆:a、备料(圆钢)→检验(材质证明书等)→车(粗车)→调质(外包:部分零件)→调质硬度检测→车(粗、精车)→磨(精磨外圆)→电镀(外包:镀硬铬)或表面热处理(外包:部分零件)→抛光→检验→防锈入库b、备料(锻件)→检验(材质证明书、探伤等)→材料探伤→车(粗车)→调质(外包:部分零件)→调质硬度检测→车(粗、精车)→磨(精磨外圆)→电镀(外包:镀硬铬)或表面热处理(外包:部分零件)→抛光→检验→防锈入库4、缸头、杆头:a、备料(圆钢)→检验(材质证明书等)→车(粗车)→调质(外包:部分零件)→调质硬度检测→车(粗、精车含球头、内外螺纹)→锯→铣→镗(镗内孔)→钳工(钻油杯孔或油口)→检验→防锈入库b、备料(铸钢:正火处理)→检验(材质证明书等)→车(粗车)→调质(外包:部分零件)→调质硬度检测→车(粗、精车含球头、内外螺纹)→锯→铣→镗(镗内孔)→钳工(钻油杯孔或油口)→检验→防锈入库c、备料(锻件)→检验(材质证明书、探伤等)→车(粗车)→调质(外包:部分零件)→调质硬度检测→车(粗、精车含球头、内外螺纹)→锯→铣→镗(镗内孔)→钳工(钻油杯孔或油口)→检验→防锈入库5、孔卡、轴卡、丝圈、压帽:a、备料(圆钢)→检验(材质证明书等)→车(粗车)→调质(外包)→调质硬度检测→车(粗、精车)→钻(孔卡、压帽)→铣→磨(孔卡、轴卡)→检验→防锈入库b、备料(锻件)→检验(材质证明书、探伤等)→车(粗车)→调质(外包)→调质硬度检测→车(粗、精车)→钻(孔卡、压帽)→铣→磨(孔卡、轴卡)→检验→防锈入库6、缸体焊(缸头与缸筒焊接)→焊缝保温去应力→焊接探伤→防锈入库7、装配熟悉装配图(含出厂试验大纲等技术文件)→零部件(含密封件、工装)清理→零部件清洗→零部件配装→零部件精洗→密封件装配→零部件组装→标识标牌→检查试验装置→出厂试验→喷漆→装箱→发货。
设备制造产品生产工艺简述

设备制造产品生产工艺简述公司属于通用设备制造业,主要生产轮式装载机、农机驱动桥系列产品,每一道生产工序都要经检验合格后,方可进入下一道工序。
其中,轮式装载机生产工艺主要是将各类原材料按照施工样图用切割机进行切割下料,检验合格后,进行机加工,用焊机进行阻焊、电焊,外形尺寸无损检验后,进行磷化外协加工,运回公司内,进行喷底漆,装配,或直接采用外购件、外协件、标准件、电气件进行总装,试车,喷面漆,凉干验收合格后入库。
其中,农机驱动桥系列产品生产工艺主要是装配。
生产工艺流程图如下:下料机加工焊接磷化(外协)外购件喷底漆外协件装配(总装)标准件试车电气件喷面漆入库主要工艺流程简述:(1)机加工,外购钢材经检验后进行机械加工,机械加工的工序主要由车、铣、钻、攻丝、数控加工中心加工等工序。
①车床加工由普通车床和数控车床完成,主要加工轴、孔套等部件;②铣床加工由普通铣床和数控铣床完成,主要加工平面及精密中心距的孔,数控铣床也可镗孔和钻孔;③钻床加工由摇臂钻床完成,利用钻头和定位工装,对工件进行钻出固定孔及攻丝的底孔;④攻丝加工由攻丝机完成,主要工件上攻制螺纹孔;⑤数控加工中心加工,主要加工形状较为复杂的板簧类零件,可一次装夹定位完成铣、镗、钻、攻、铰等多个工序。
⑥抛丸处理,利用抛丸机清理工件表面,设备型号为Q3730,将表面的氧化皮及锈蚀清理干净,清理完后用角磨机手工打磨干净工件上的毛刺。
(2)半成品巡检,机械加工过程中要进行巡检,保证产品质量,检测重点、主要尺寸,防止出现批量不合格件。
(3)焊接,主要是组焊和电焊,其中组焊是将各组件依次摆放到工装上,调整工件位置,按照图纸进行装配,然后进行点固、打磨、焊接成型。
(4)磷化过程进行外协,公司只做好机罩(薄板件),联系泰安专门的磷化酸洗厂完成该工序。
(5)喷漆,主要是防锈底漆涂装和表面涂装。
在喷漆房内喷涂,人工将工件推进喷漆房,关上喷漆房大门,启动控制柜,进行喷漆作业。
挖机油缸原理
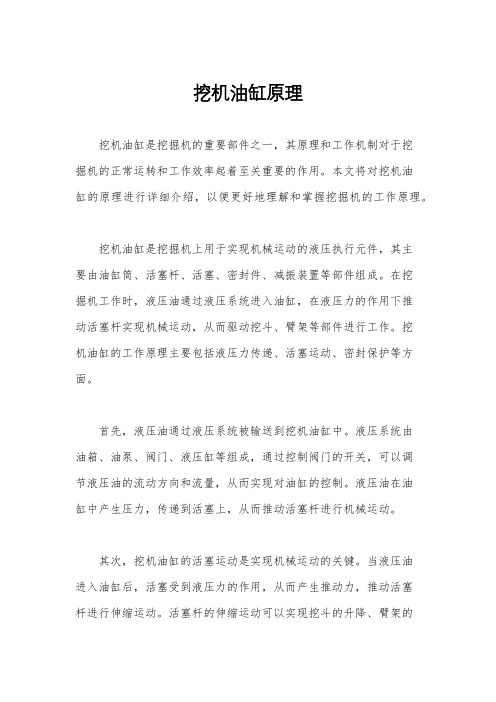
挖机油缸原理挖机油缸是挖掘机的重要部件之一,其原理和工作机制对于挖掘机的正常运转和工作效率起着至关重要的作用。
本文将对挖机油缸的原理进行详细介绍,以便更好地理解和掌握挖掘机的工作原理。
挖机油缸是挖掘机上用于实现机械运动的液压执行元件,其主要由油缸筒、活塞杆、活塞、密封件、减振装置等部件组成。
在挖掘机工作时,液压油通过液压系统进入油缸,在液压力的作用下推动活塞杆实现机械运动,从而驱动挖斗、臂架等部件进行工作。
挖机油缸的工作原理主要包括液压力传递、活塞运动、密封保护等方面。
首先,液压油通过液压系统被输送到挖机油缸中。
液压系统由油箱、油泵、阀门、液压缸等组成,通过控制阀门的开关,可以调节液压油的流动方向和流量,从而实现对油缸的控制。
液压油在油缸中产生压力,传递到活塞上,从而推动活塞杆进行机械运动。
其次,挖机油缸的活塞运动是实现机械运动的关键。
当液压油进入油缸后,活塞受到液压力的作用,从而产生推动力,推动活塞杆进行伸缩运动。
活塞杆的伸缩运动可以实现挖斗的升降、臂架的伸缩等工作动作,从而完成挖掘机的工作任务。
另外,挖机油缸的密封保护也是非常重要的。
挖机油缸在工作时需要承受高压液压力的作用,因此需要采用高强度的密封件进行密封保护,以防止液压油泄漏和外部杂质进入,保证油缸的正常工作。
同时,挖机油缸还需要配备减振装置,以减少振动和冲击,延长油缸的使用寿命。
总的来说,挖机油缸的工作原理主要包括液压力传递、活塞运动、密封保护等方面。
了解和掌握挖机油缸的工作原理,有助于更好地维护和使用挖掘机,提高工作效率,延长设备的使用寿命。
希望本文对于读者能够有所帮助,谢谢阅读!。
油缸制造工艺
工艺流程图13、液压油缸和系统制造工艺说明13.1 、液压缸缸体加工工艺1、目的:控制操作过程,确保加工质量符合图纸要求2、制造过程中执行的标准:JB4730压力容器无损检测JB/2370.13-88 磨料种类,粒度选择GB1031表面粗糙度磨参数及其数值JISB6911 钢铁的正火与退火处理Q/ZB75机械加工通用技术条件Q/WYG0814-1997过程控制程序Q/WYG0816.1-1997机械加工检验Q/WYG0816.2-1997热处理零件检验Q/WYG0816.3-1997无损检验Q/WYG0814.10-1997工序质量控制点管理3、深孔加工、深孔光整珩磨及埋弧自动焊接技术重要工艺特色油缸缸体内孔加工工序被确立为关键工序质量控制点。
为保证其全过程受控,专门编制了《工序控制点明细表》、《工序质量分析表》、《作业指导书》、《机械加工工序卡》、《深孔加工质量监控记录》并严格按照要求实施作业,加工全过程在严格受控状态下进行。
(1)、缸体的精镗工序组合刀具内孔切削加工的稳定性和可靠性,直接影响到加工缸体的母线直线度、孔加工精度及表面粗糙度。
缸体内孔加工切削的稳定性主要靠刀具本身结构的合理设计,我公司使用的组合刀具有效支承长度是加工缸体内孔直径的 2 倍或 2 倍以上。
我公司经过多次技术论证和试验,当刀具支承长度小于内孔直径时,刀具加工时的切削稳定性较差,当刀具支承长度等于缸体直径时,刀具的切削稳定性明显提高。
当组合刀具支承长度大于 2 倍缸体内孔直径时,其切削稳定性就更可靠,整个组合刀具切削加工过程平稳,刀具按导向套的引导进行缸体深孔加工,保证了缸体加工精度、表面粗糙度和母线的直线度。
组合刀具另件加工精度是组合刀具整体性能符合设计要求的关键。
我公司组合刀具的制造、检验都选派有经验的、负责的专门人员把关,每个另件都必须满足设计提出的精度、形位公差要求,并且组合刀具总装后每道支承的径向跳动控制在0.01mm 以下,多道支承必须一次磨成,道与道之间的直径偏差控制在0.015mm以下,保证刀具母线直线度误差在 2 倍缸体直径长度上不大于0.015mm,刀具的直径尺寸与导向套过盈配合,精度为IT6 。
液压缸装配流程
液压缸装配流程一. 目的制定本作业流程,使液压缸装配作业符合规定要求。
二. 适用范围:本指导书规定了液压缸的检查、装配以及试验技术要求,适用于公司生产各类液压缸的装配作业,按本标准执行;三. 装配场地与环境:1. 油缸装配应在专门的工作间或装配区内进行,温度应保持在20~250C,应远离风口、粉尘、切削加工区,空气清新、无灰尘、无噪音;避免强光直射。
2. 装配间应备有安装平台及足够的工位器具、装配周转车、吊装与起重设备及以下专用基本设备。
a:装缸机;b:另件缸筒清洗机,用于加热清洗另件;c:试压设备,用于油缸试压;d:风管,用于清洗后的另件吹净吹干;3. 车间应设置装配工作台,台面上应铺设耐油橡胶板或铝板,避免另件产生碰撞伤与划痕,应配置另件安装架或安装筐。
4. 车间除配备常用工具外,应配备一些专用工具如力矩扳手,铅锤或铜锤、铜棒、尼龙棒、电热锅、风枪等。
5. 装配间吊装尽量使用吊装带,不用钢丝绳或麻绳,前者容易碰伤另件或器具,后者容易产生丝屑影响另件清洁度。
6. 应特别重视文明生产,工作有序,文明操作,堆放有序,地面清洁经常用废油洗刷,保持地面原色。
四.备料:1. 装配组织者必须根据装配图纸、操作技术规程,按规定的顺序及步骤进行装配作业,严格遵守工艺纪律。
2. 根据生产计划规定的台数按图纸与清单,使用周转车一次领完装配所需的自制件、密封件、标准件并进行检查。
做好标识a:自制加工件应检查外观质量,对有裂纹严重碰伤或划痕,电镀表面气孔针孔缺陷应提请检验复检,轻微的缺陷应进行修复。
自制加工件认真清理,各螺孔进行回攻,表面的锈斑,尖角毛刺应去尽,孔交接口应刮圆,应砂光,螺纹进退刀处薄边应修去,一般应修去1/4圈或修螺纹厚>0、5mm.b:检查密封件应检查规格并检查产期保质期,超过保质期的密封件不能安装,外表有缺陷的也不能安装。
c:领用的螺栓,螺母要注意强度等级是否符合图纸要求。
3. 检查修整后的另件进行认真的清洗,清洗剂用汽油或煤油,完工后应吹净吹干,堆放整齐,盖湿润无毛边布,避免新的粉尘与颗粒粘上,清洗后的另件应尽快装配,避免产生新的锈蚀。
液压油缸的生产工艺流程
液压油缸的生产工艺流程下载温馨提示:该文档是我店铺精心编制而成,希望大家下载以后,能够帮助大家解决实际的问题。
文档下载后可定制随意修改,请根据实际需要进行相应的调整和使用,谢谢!并且,本店铺为大家提供各种各样类型的实用资料,如教育随笔、日记赏析、句子摘抄、古诗大全、经典美文、话题作文、工作总结、词语解析、文案摘录、其他资料等等,如想了解不同资料格式和写法,敬请关注!Download tips: This document is carefully compiled by theeditor. I hope that after you download them,they can help yousolve practical problems. The document can be customized andmodified after downloading,please adjust and use it according toactual needs, thank you!In addition, our shop provides you with various types ofpractical materials,such as educational essays, diaryappreciation,sentence excerpts,ancient poems,classic articles,topic composition,work summary,word parsing,copy excerpts,other materials and so on,want to know different data formats andwriting methods,please pay attention!液压油缸是液压系统中的核心部件,其生产工艺流程如下:1. 材料准备在生产液压油缸之前,首先需要准备合适的材料,如钢材、密封件、油封、导向套等。
液压油缸轴电镀镍铁钴代铬镀层
液压油缸轴电镀镍铁钴代铬镀层液压缸是液压系统中重要的执行元件,用于执行往复运动,在工程机械中应用广泛。
液压缸活塞杆是液压缸的重要部件,它通常采用35、34号或无缝钢管做成实心杆或空心杆,为了进步耐磨性的防锈蚀,目前国内传统工艺是表面镀硬铬(镀层厚度0.02~0.05mm)并抛光,其表面粗糙度Ra为1.6~0.4μm。
由于镀铬对人、环境污染严重,属国家环保线值项目,且镀层不均匀,孔隙率高,轻易起皮,镀铬用度也比较高,不能满足生产上的需要,因此采用合适经济的镀层取代镀铬一直是工程机械行业的重要课题。
液压油缸轴镍钴铁代铬技术和工艺流程特点该技术属高效清洁表面处理技术工艺,能耗低,无电镀污泥产生,实现了废水零排放。
结合基础研究成果,目前已成功实现镍钴铁代铬表面工程新技术的产业化。
整个工艺流程分为镀前处理、电镀镍钴铁和镀后处理三部分,工艺流程如下:各主要工序的情况介绍如下:(1)电解除油1:15分钟,7-10A/dm2除去工件表面剩余的污渍,使表面净化。
(2)热水洗:55℃热水除皂化膜,洗涤用水可长期利用。
(3)电解除油2: 1-3分钟,7-10 A/dm2活化基体。
(4)冷水洗:常温,净化基体表面。
(5)活化酸洗:10%稀硫酸,15-30秒,活化基体表面。
最好使用活化酸盐dw(6)去离子水洗:净化表面,循环利用。
(7)电镀镍钴铁:3-8 A/dm2。
具体见工艺硫酸镍 200-300g/l氯化镍 30g/l硫酸钴 80g/l硫酸亚铁铵 30-120g/l硼酸 30g/lDw-2012A稳定盐120g/l 消耗量KAH 50-100 g/lDw-2012B硬化剂20-40ml/l消耗量KAH 50ml/lDw-2012C纳米晶流平剂20 ml/l消耗量KAH 50ml/lDw-2012D应力调节剂20 ml/l消耗量KAH10-50ml/lDw-2012E防针孔剂5-10 ml/l消耗量KAH10ml/lDw-2012F增白剂5 ml/l消耗量KAH5-15ml/l(8)去离子热水洗:55℃清洗镀后表面,用于补充主镀液位,无排放。