DFMEA(Design Failure Mode and Effects Analysis,设计失效模式及后果分析)
dfmea的功能和要求

dfmea的功能和要求
DFMEA是Design Failure Mode and Effects Analysis 的缩写,即设计失效模式和影响分析。
它是一种系统性的方法,用于识别和
评估产品设计过程中可能出现的失效模式,以及这些失效模式对产
品性能、安全性和可靠性的影响。
DFMEA的主要功能和要求包括以
下几个方面:
1. 识别潜在的失效模式,DFMEA的主要功能之一是通过系统性
的方法识别可能出现的失效模式,包括设计、制造、装配和使用过
程中的各种失效模式。
这有助于在产品设计阶段就能够预见和避免
潜在的问题,提高产品的可靠性和安全性。
2. 评估失效影响,DFMEA要求对每种可能的失效模式进行评估,包括失效的严重程度、频率以及可能的影响范围。
这有助于确定哪
些失效模式对产品性能和安全性的影响最为严重,从而有针对性地
进行改进和控制。
3. 制定改进措施,DFMEA要求在识别和评估失效模式的基础上,制定相应的改进措施,以降低失效的可能性,减小失效的影响,从
而提高产品的可靠性和安全性。
4. 文档化和跟踪,DFMEA要求对识别的失效模式、影响和改进措施进行详细的文档化,并建立跟踪机制,以确保改进措施的有效实施和持续改进。
总的来说,DFMEA的功能和要求旨在通过系统性的方法识别和评估潜在的失效模式,从而在产品设计阶段就能够预见和避免可能出现的问题,提高产品的可靠性和安全性。
同时,DFMEA也要求制定改进措施,并建立文档化和跟踪机制,以确保产品设计的持续改进和优化。
DFMEA(设计失效模式与效应分析)-20121123

※ RPN(風險順序數):計算並記錄糾正後的RPN值的結果。
14
設計FMEA分析步驟
15
設計FMEA嚴重度評估標準
16
設計FMEA發生率評估標準
17
設計FMEA難檢度評估標準
18
設計FMEA改善對策提出時機
The timing to provide solution / 提出改善對策之時機
以利追蹤
※ Planning Stage(設計階段):填上依據目前所進行分析標的物所處之開發階段 ※ Design Responsibility (設計責任):填入負責的設計與開發之工程師全名
※ Prepared By(編制者):填入負責編制DFMEA的工程師的姓名
※ Part Name/Program(系統、子系統或零部件的名稱及編號):填入適當的分析級別並
12
設計FMEA分析表說明(Ⅲ)
※ POTENTIAL CAUSE(S) / MECHANISM(S) OF FAILURE(失效的潛在原因或機理) :填入每一
個失效模式的所有可以想到的失效原因或失效機理。
※ DESIGN CONTROLS(現行設計管制):填入已經完成或承諾要完成的預防措施、設計確認
DFMEA(設計失效模式與效應分析)
Design Failure Mode and Effect Analysis
1
什麽是FMEA ?
※
FMEA是一種系統方法,使用制式表格及問題解決
方法以確認潛在失效模式及其效應,並評估其嚴重度、 發生度、難檢度(探測/偵測)及目前管制方法,從而計算
風險優先指數(RPN),最後採取進一步改善方法,如此
持續進行,以達防患失效模式及效應發生於未然
dfmea预防控制措施和探测措施
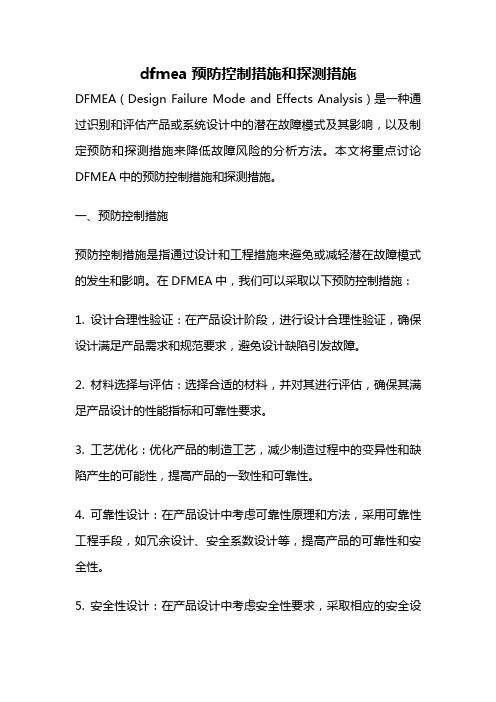
dfmea预防控制措施和探测措施DFMEA(Design Failure Mode and Effects Analysis)是一种通过识别和评估产品或系统设计中的潜在故障模式及其影响,以及制定预防和探测措施来降低故障风险的分析方法。
本文将重点讨论DFMEA中的预防控制措施和探测措施。
一、预防控制措施预防控制措施是指通过设计和工程措施来避免或减轻潜在故障模式的发生和影响。
在DFMEA中,我们可以采取以下预防控制措施:1. 设计合理性验证:在产品设计阶段,进行设计合理性验证,确保设计满足产品需求和规范要求,避免设计缺陷引发故障。
2. 材料选择与评估:选择合适的材料,并对其进行评估,确保其满足产品设计的性能指标和可靠性要求。
3. 工艺优化:优化产品的制造工艺,减少制造过程中的变异性和缺陷产生的可能性,提高产品的一致性和可靠性。
4. 可靠性设计:在产品设计中考虑可靠性原理和方法,采用可靠性工程手段,如冗余设计、安全系数设计等,提高产品的可靠性和安全性。
5. 安全性设计:在产品设计中考虑安全性要求,采取相应的安全设计措施,如防护装置、警告标识等,预防潜在的伤害和事故发生。
6. 标准化设计:采用标准化设计,遵循通用规范和标准,降低故障的发生和影响。
二、探测措施探测措施是指通过监测、测试和检验等手段,及时发现故障模式的存在和影响,以便采取相应的纠正措施。
在DFMEA中,我们可以采取以下探测措施:1. 过程监控:建立产品制造过程的监控机制,通过实时监测和控制关键工艺参数,及时发现制造过程中的异常情况和潜在故障。
2. 产品测试:对产品进行全面的功能测试和性能测试,确保产品符合规格要求,并能够在各种工作条件下正常运行。
3. 故障诊断:建立故障诊断系统,通过对故障模式的识别和分析,及时发现故障原因,并采取相应的修复措施。
4. 使用反馈:建立用户反馈机制,收集用户使用产品过程中的故障信息和意见反馈,及时发现和解决存在的问题。
DFMEA(Design Failure Mode and Effects Analysis,设计失效模式及后果分析)

DFMEA出自 MBA智库百科(/)DFMEA(Design Failure Mode and Effects Analysis,设计失效模式及后果分析)目录[隐藏]• 1 什么是DFMEA• 2 DFMEA基本原则• 3 DFMEA与PFMEA的关系• 4 形式和格式(Forms and Formats)• 5 我们应在何时进行设计失效模式及后果分析?• 6 我们应在什么时间进行设计失效模式及后果分析?•7 我们应在什么时间进行设计失效模式及后果分析?•8 我们应在什么时间进行设计失效模式及后果分析?•9 由谁进行设计失效模式及后果分析?•10 怎样进行设计失效模式及后果分析?•11 怎样进行设计失效模式及后果分析?•12 怎样进行设计失效模式及后果分析?•13 怎样进行设计失效模式及后果分析?•14 DFMEA的案例分析[1]o14.1 实施DFMEA存在的困难o14.2 实施DFMEA的准备工作o14.3 实施DFMEA的流程•15 相关条目•16 参考文献[编辑]什么是DFMEADFMEA是指设计阶段的潜在失效模式分析,是从设计阶段把握产品质量预防的一种手段,是如何在设计研发阶段保证产品在正式生产过程中交付客户过程中如何满足产品质量的一种控制工具。
因为同类型产品的相似性的特点,所以的DFMEA阶段经常后借鉴以前量产过或正在生产中的产品相关设计上的优缺点评估后再针对新产品进行的改进与改善。
[编辑]DFMEA基本原则DFMEA是在最初生产阶段之前,确定潜在的或已知的故障模式,并提供进一步纠正措施的一种规范化分析方法;通常是通过部件、子系统/部件、系统/组件等一系列步骤来完成的。
最初生产阶段是明确为用户生产产品或提供服务的阶段,该阶段的定义非常重要,在该阶段开始之前对设计的修改和更正都不会引起严重的后果,而之后对设计的任何变更都可能造成产品成本的大幅提高。
DFMEA应当由一个以设计责任工程师为组长的跨职能小组来进行,这个小组的成员不仅应当包括可能对设计产生影响的各个部门的代表,还要包括外部顾客或内部顾客在内。
DFMEA培训资料

DFMEA培训资料一、DFMEA 简介DFMEA,即设计失效模式及后果分析(Design Failure Mode and Effects Analysis),是在产品设计阶段,用于识别潜在的失效模式及其可能产生的后果,并采取预防措施以降低风险的一种工具。
DFMEA 的目的是在产品设计过程中,通过系统的分析,提前识别可能出现的问题,从而在设计阶段就采取措施进行改进,以提高产品的质量、可靠性和安全性,降低成本,缩短开发周期。
二、DFMEA 的实施步骤1、确定分析的对象和范围明确要分析的产品或系统。
界定分析的边界和功能。
2、组建团队包括设计工程师、工艺工程师、质量工程师、售后工程师等相关人员。
确保团队成员具备相关的知识和经验。
3、收集相关信息产品的技术要求和规范。
类似产品的失效案例和经验教训。
客户的需求和期望。
4、识别潜在的失效模式从功能、性能、可靠性等方面考虑。
采用头脑风暴等方法,尽可能全面地列出可能的失效模式。
5、分析失效的原因深入探究导致失效模式发生的根本原因。
可以使用因果图、5Why 等工具。
6、评估失效的影响对产品的功能、性能、安全性、客户满意度等方面的影响。
确定影响的严重程度(S),通常采用 1 10 的评分标准。
7、评估失效发生的可能性考虑设计控制措施的有效性。
确定发生的频率(O),评分标准 1 10。
8、评估检测失效的难易程度现有检测手段的有效性。
确定检测度(D),评分 1 10。
9、计算风险优先数(RPN)RPN = S × O × D根据 RPN 值的大小,确定优先改进的项目。
10、制定改进措施针对高 RPN 值的失效模式制定相应的改进措施。
明确责任人和完成时间。
11、重新评估风险实施改进措施后,重新计算 RPN 值,评估改进效果。
三、DFMEA 中的关键概念1、失效模式产品或系统不能满足设计要求或预期功能的表现形式。
例如:零件断裂、功能失效、尺寸超差等。
2、失效原因导致失效模式发生的因素。
dfmea七步分析法

dfmea七步分析法DFMEA(Design Failure Mode and Effects Analysis),即设计失效模式及影响分析,是一种系统性的设计分析方法,旨在识别设计过程中潜在的失效模式及其可能的影响,以便采取针对性的措施来降低潜在的风险。
DFMEA可以帮助设计团队在产品设计阶段就预测、评估和规避潜在的失效风险,从而提高产品的可靠性和质量,降低产品研发和制造过程中的成本。
DFMEA通常按照七个步骤进行分析,这七个步骤分别是:定义分析范围、识别失效模式、识别失效影响、对失效模式和影响进行评估、制定和实施改进措施、跟踪和控制改进效果、记录和文档化分析结果。
下面将逐一介绍这七个步骤的内容和方法。
第一步:定义分析范围在进行DFMEA分析时,首先需要明确分析的范围和目标。
这包括明确分析的对象,例如产品的整体设计、某个单独的模块或零部件设计,以及分析的目的,例如降低设计阶段的失效风险、优化设计以提高可靠性和安全性等。
定义分析范围是为了确保分析的准确性和全面性,避免遗漏重要的失效模式和影响。
在定义分析范围时,可以使用以下方法:-选择合适的分析工具和表格,如FMEA表格,用于记录分析的内容和结果。
-划定分析的界限和范围,明确哪些部分需要进行分析,以及分析的深度和广度。
-明确分析的目的和预期的输出,例如识别潜在的失效模式和其影响、评估风险等。
第二步:识别失效模式识别失效模式是DFMEA分析的核心内容之一。
失效模式是指零部件、产品或系统在使用过程中可能发生的失效现象或状态。
识别失效模式需要考虑多方面的因素,例如设计、制造、装配、运行维护等。
通过识别失效模式,可以全面了解潜在的风险,为后续的分析和改进提供依据。
识别失效模式时,需要进行以下工作:-收集和整理相关的设计和技术文档,了解产品的结构和功能。
-研究类似产品或系统的失效案例和经验,总结常见的失效模式和原因。
-进行头脑风暴和讨论,梳理可能的失效模式,并对其进行分类和整理。
dfmea的rpn风险等级评价准则
dfmea的rpn风险等级评价准则
在DFMEA(Design Failure Mode and Effects Analysis)中,RPN(Risk Priority Number)是一种用于评估风险等级的方法。
RPN根据以下三个方面的评价指标计算得出:
1. Severity(严重性):评估潜在失效对系统功能和性能的影响程度。
常见的评价指标为数字等级(1-10),其中1表示对系统功能和性能没有明显影响,而10表示对系统功能和性能有极大的影响。
2. Occurrence(发生率):评估失效模式发生的概率或频率。
常见的评价指标为数字等级(1-10),其中1表示失效模式非常不可能发生,而10表示失效模式极有可能发生。
3. Detection(检测能力):评估当前设计或控制措施对失效模式的检测能力。
常见的评价指标为数字等级(1-10),其中1表示很容易检测到失效模式,而10表示很难或无法检测到失效模式。
根据以上三个方面的评价指标,RPN通过以下公式计算得出:
RPN = Severity ×Occurrence ×Detection
RPN的数值范围为1-1000,数值越高表示风险等级越高。
通常,评估准则如下:
- RPN ≤80:风险等级低,可以接受;
- 80 < RPN ≤160:风险等级中等,可能需要采取补救措施;
- 160 < RPN ≤320:风险等级高,需要采取有效控制措施;
- RPN > 320:风险等级很高,需要立即采取紧急控制措施。
需要注意的是,这些评估准则可能会有所变化,具体的评估准则应根据实际情况和组织内部的标准来确定。
dfmea定义
D-FMEA定义1. 简介故障模式与效应分析(Design Failure Mode and Effects Analysis,简称D-FMEA)是一种旨在通过识别和评估可能的故障模式及其潜在影响,从而改进和增强产品、系统或过程的可靠性的方法。
它是一种高效的风险管理工具,可以在产品设计阶段早期识别和纠正潜在的设计问题,并制定相应的预防和纠正措施。
2. D-FMEA的目的D-FMEA的目的是通过系统性分析和评估潜在的故障模式及其可能的影响,以降低风险并提高产品的可靠性。
它的主要目标包括:•识别和分析潜在的故障模式,了解其可能的原因和影响;•评估故障的严重程度、概率和检测能力;•确定并实施预防和纠正措施,以减少故障的发生和影响;•提供参考资料,指导和改进设计、生产和服务过程;•增强团队成员之间的合作和沟通。
3. D-FMEA的步骤D-FMEA通常包含以下步骤:3.1 确定D-FMEA的范围确定D-FMEA的范围是指明分析的领域和具体对象。
这可以是一个产品、系统或过程。
准确定义范围是确保分析的有效性和准确性的关键步骤。
3.2 创建D-FMEA团队组建一个由专业人员组成的D-FMEA团队,该团队应包含具有相关专业知识和经验的成员。
团队成员应代表不同的领域,如设计、工程、质量控制等。
3.3 识别潜在的故障模式团队成员使用头脑风暴和其他适当的方法,识别可能的故障模式。
这包括产品功能的不正常失效或系统中的潜在问题等。
3.4 评估故障的严重程度、概率和检测能力团队对每个故障模式评估其严重程度、概率和检测能力。
严重程度指的是故障对产品或系统性能的影响程度,概率是指故障发生的可能性,检测能力是指故障是否可以被及早发现。
3.5 制定预防和纠正措施基于对潜在故障模式的评估,团队提出相应的预防和纠正措施。
预防措施旨在防止故障发生,而纠正措施旨在减少故障影响。
3.6 实施和跟踪措施团队将制定的预防和纠正措施纳入产品设计、开发和生产过程中,并跟踪实施的效果。
DFMEA评估
DFMEA评估概述DFMEA(Design Failure Mode and Effects Analysis,设计失效模式与效应分析)是一种系统性的方法,用于评估产品设计中的潜在失效模式和效应。
通过识别、评估和优化潜在的设计失效,可以减少产品设计过程中的风险,并提高产品质量和可靠性。
目的DFMEA评估的目标是在产品设计阶段尽早发现潜在的失效模式,并采取适当的措施来减轻或消除这些失效对产品性能和可靠性的影响。
通过实施DFMEA评估,可以:- 提前预测产品在使用过程中可能出现的问题;- 识别和分析潜在失效的原因和效应;- 评估失效的严重程度、容忍度和频率;- 优化设计,减少潜在失效的风险。
DFMEA评估过程DFMEA评估通常包括以下步骤:1. 选择评估的设计项目:确定需要进行DFMEA评估的设计项目,可以是整个产品、子系统或单个零部件。
2. 制定评估团队:组建一个具有相关专业知识和经验的评估团队,涵盖设计、工艺、制造和测试等领域。
3. 收集设计信息:收集和整理与设计项目相关的信息,包括设计相关文档、规范和标准等。
4. 识别失效模式:通过头脑风暴、经验分享和专家讨论等方式,识别与设计项目相关的潜在失效模式。
5. 评估失效的严重程度:对每个失效模式进行评估,确定其对产品性能和可靠性的影响程度。
6. 识别失效原因:分析每个失效模式的可能原因,找出导致失效的根本因素。
7. 评估失效的容忍度:评估每个失效模式是否被容忍,并确定容忍度的阈值。
8. 评估失效的频率:评估每个失效模式的发生频率,包括概率分析和经验估计。
9. 制定改进措施:为每个失效模式制定相应的改进措施,减轻或消除潜在的失效影响。
10. 跟踪实施情况:跟踪和记录改进措施的实施情况,并进行必要的调整和追踪。
总结DFMEA评估是一种重要的工具,可以帮助产品设计团队尽早发现和解决潜在的设计问题。
通过对潜在失效模式和效应的识别、评估和优化,可以提高产品设计的质量和可靠性,并降低产品开发过程中的风险。
DFMEA是什么意思
DFMEA是什么意思
DFMEA是什么意思
在设计和制造产品时,FMEA是一种可靠性设计的重要方法。
它实际上是FMA(故障模式分析)和FEA(故障影响分析)的组合。
它对各种可能的风险进行评价、分析,以便在现有技术的基础上消除这些风险或将这些风险减小到可接受的水平。
及时性是成功实施FMEA的'最重要因素之一,它是一个“事前的行为”,而不是“事后的行为”。
为达到最佳效益,FMEA必须在故障模式被纳入产品之前进行.
设计FMEA(也记为d-FMEA ,Design Failure Mode and Effects Analysis )应在一个设计概念形成之时或之前开始,并且在产品开发各阶段中,当设计有变化或得到其他信息时及时不断地修改,并在图样加工完成之前结束。
其评价与分析的对象是最终的产品以及每个与之相关的系统、子系统和零部件。
需要注意的是,d-FMEA在体现设计意图的同时还应保证制造或装配能够实现设计意图。
因此,虽然d-FMEA不是靠过程控制来克服设计中的缺陷,但其可以考虑制造/装配过程中技术的/客观的限制,从而为过程控制提供了良好的基础。
【DFMEA是什么意思】。
- 1、下载文档前请自行甄别文档内容的完整性,平台不提供额外的编辑、内容补充、找答案等附加服务。
- 2、"仅部分预览"的文档,不可在线预览部分如存在完整性等问题,可反馈申请退款(可完整预览的文档不适用该条件!)。
- 3、如文档侵犯您的权益,请联系客服反馈,我们会尽快为您处理(人工客服工作时间:9:00-18:30)。
DFMEA出自 MBA智库百科(/)DFMEA(Design Failure Mode and Effects Analysis,设计失效模式及后果分析)目录[隐藏]• 1 什么是DFMEA• 2 DFMEA基本原则• 3 DFMEA与PFMEA的关系• 4 形式和格式(Forms and Formats)• 5 我们应在何时进行设计失效模式及后果分析?• 6 我们应在什么时间进行设计失效模式及后果分析?•7 我们应在什么时间进行设计失效模式及后果分析?•8 我们应在什么时间进行设计失效模式及后果分析?•9 由谁进行设计失效模式及后果分析?•10 怎样进行设计失效模式及后果分析?•11 怎样进行设计失效模式及后果分析?•12 怎样进行设计失效模式及后果分析?•13 怎样进行设计失效模式及后果分析?•14 DFMEA的案例分析[1]o14.1 实施DFMEA存在的困难o14.2 实施DFMEA的准备工作o14.3 实施DFMEA的流程•15 相关条目•16 参考文献[编辑]什么是DFMEADFMEA是指设计阶段的潜在失效模式分析,是从设计阶段把握产品质量预防的一种手段,是如何在设计研发阶段保证产品在正式生产过程中交付客户过程中如何满足产品质量的一种控制工具。
因为同类型产品的相似性的特点,所以的DFMEA阶段经常后借鉴以前量产过或正在生产中的产品相关设计上的优缺点评估后再针对新产品进行的改进与改善。
[编辑]DFMEA基本原则DFMEA是在最初生产阶段之前,确定潜在的或已知的故障模式,并提供进一步纠正措施的一种规范化分析方法;通常是通过部件、子系统/部件、系统/组件等一系列步骤来完成的。
最初生产阶段是明确为用户生产产品或提供服务的阶段,该阶段的定义非常重要,在该阶段开始之前对设计的修改和更正都不会引起严重的后果,而之后对设计的任何变更都可能造成产品成本的大幅提高。
DFMEA应当由一个以设计责任工程师为组长的跨职能小组来进行,这个小组的成员不仅应当包括可能对设计产生影响的各个部门的代表,还要包括外部顾客或内部顾客在内。
DFMEA的过程包括产品功能及质量分析、分析故障模式、故障原因分析、确定改进项目、制定纠正措施以及持续改进等6个阶段。
[编辑]DFMEA与PFMEA的关系DFMEA是指设计阶段的潜在失效模式分析,是从设计阶段把握产品质量预防的一种手段,是如何在设计研发阶段保证产品在正式生产过程中交付客户过程中如何满足产品质量的一种控制工具。
因为同类型产品的相似性的特点,所以的DFMEA阶段经常后借鉴以前量产过或正在生产中的产品相关设计上的优缺点评估后再针对新产品进行的改进与改善。
PFMEA如果在DFMEA阶段做的比较好的话那么在PFMEA阶段将不会出现影响较大的品质问题,但必竟是新产品往往都会出现自身特有的问题点,而这些问题也通常都是要经过长时间的量产或者是交付给客户后才发生或发现的品质问题,这就要通过PFMEA加以分析保证。
两者最终的目的都是一样的都追求产品质量的稳定及良品最大化,同时也为大量生产提供可行性的保证。
[编辑]形式和格式(Forms and Formats)•用户可能有他们所要求的特定格式或形式。
如果是这样,你只有征得他们的书面同意,才能采用其种格式。
•这是产品设计小组采用的一种分析方法,用于识别设计中固有的潜在失效模式,并确定所应采取的纠正措施。
•正式程序•着眼于客户•尽可能利用工程判断和详实的数据[编辑]我们应在何时进行设计失效模式及后果分析?•当还有时间修改设计时!•事后补作设计失效模式及后果分析只能当作一个练习而已[编辑]我们应在什么时间进行设计失效模式及后果分析?•设计失效模式及后果分析是产品质量先期策划和控制计划(APQP)中“产品设计和开发”阶段的产物•在分析了客户要求和形成初始概念之后进行•在过程失效模式及后果分析(PFMEA)之前,通常与可制造性设计(DFM)一道进行。
[编辑]我们应在什么时间进行设计失效模式及后果分析?•应成为概念开发的一个组成部分•是一个动态文件[编辑]我们应在什么时间进行设计失效模式及后果分析?从一种战略观点出发...在下列情形下,进行设计失效模式及后果分析DFMEA(或至少评审过去做过的DFMEA) :•是一种新的设计•在原设计基础上修改•应用条件或环境发生变化从一种战略观点出发...•客户的要求或期望改变•竞争环境、业务环境或法律环境发生变化•你公司负有设计责任,且PPAP(生产件批准程序) 的一些条件适用•实际发生失效[编辑]由谁进行设计失效模式及后果分析?•由对设计具有影响的各部门代表组成的跨部门小组进行o供应商也可以参加o切不要忘记客户•小组组长应是负责设计的工程师跨职能部门小组•5-9人,来自:o系统工程o零部件设计工程o试验室o材料工程o工艺过程工程o装备设计o制造o质量管理[编辑]怎样进行设计失效模式及后果分析?提要•组建跨职能部门设计失效模式及后果分析DFMEA小组•列出失效模式、后果和原因•评估o the severity of the effect (S) 影响的严重程度o the likelihood of the occurrence(O) 可能发生的机会o and the ability of designcontrols to detect failuremodes and/or their causes (D)探测出失效模式和/或其原因的设计控制能力[编辑]怎样进行设计失效模式及后果分析?提要•Calculate the risk priority number (RPN)to prioritize corrective actions 计算风险优先指数(RPN)以确定应优先采取的改进措施[编辑]怎样进行设计失效模式及后果分析?提要•Plan corrective actions 制订纠正行动计划•Perform corrective actions to improvethe product 采取纠正行动,提高产品质量•Recalculate RPN 重新计算风险优先指数(RPN)[编辑]怎样进行设计失效模式及后果分析?提要•先在草稿纸上进行分析;当小组达成一致意见后,再将有关信息填在设计失效模式及后果分析FMEA表上o use fishbone and tree diagramsliberally 充分利用鱼骨图和树形图o trying to use the FMEA form as aworksheet leads to confusionand messed-up FMEAs 若将FMEA表当做工作单使用,就会造成混乱,使FMEA一塌糊涂建议1. 组建一个小组并制订行动计划•绝不能由个人单独进行设计失效模式及后果分析,因为:o由个人进行会使结果出现偏差o进行任何活动,都需要得到其他部门的支持•应指定一个人(如组长)保管设计失效模式及后果分析FMEA表格o应将小组成员的姓名和部门填入设计失效模式及后果分析FMEA表格2. 绘制产品功能结构图•一种图示方法,其中包括:o用块表示的各种组件(或特性)o用直线表示的各组件之间的相互关系o适当的详细程度•结构图3. 列出每个组件的功能•功能系指该组件所起的作用•以下列形式说明功能:Verb + Object + Qualifier动词+宾语+修饰词•例如:o insulates core 使型芯绝缘o assures terminal position inconnector 确保端子与接头连接到位o protects tang from smashing, etc.防止柄脚被压碎,等•Don't forget auxiliary functions as wella primary functions 不要忘记基本功能和辅助功能•Often, components work together toperform a function 通常,多个组件一起行使某一功能•Hint: Use the Block Diagram! 提示:利用结构图!4. 列出质量要求•a customer want or desire 客户的期望或要求•could seriously affect customerperception 有可能严重影响客户的看法•could lead to a customer complaint 有可能导致客户投诉•Hint: Use QFD提示:使用质量功能展开5. 列出潜在的失效模式•a defect, flaw, or other unsatisfactorycondition in the product that iscaused by a design weakness 由设计缺陷造成的产品缺陷、瑕疵或其它令人不满意的情况•典型的失效模式- breaks - cracks破碎断裂- corrodes - sticks腐蚀粘结- unseats - deforms/melts未到位变形/熔化提示•从前两个步骤做起:o功能o质量要求•AIAG将失效模式定义为产品不能实现其设计意图的一种方式。
本教材所列第5个步骤中的提示通过列举功能和质量要求,扼要阐述了设计意图。
注明“无功能”的中间步骤则是指设计意图无法实现。
•用你自己的话,对下列情况举例说明:failure = no function失效=无功能failure = not enough function失效=功能不强failure = too much function失效=功能过强•同样:failure = no quality requirement, etc.失效=无质量要求,等•具体说明每种情况发生的方式:o使用“技术”术语具体说明o采用工程技术判断和/或分析o参考历史资料,如顾客户抱怨等o“组件或特性,导致无功能”•例如:线束夹+螺钉+车身面板上的孔眼•功能=固定线束•无功能=夹子不能将线束固定在车身面板上,失效模式:o夹子在弯头处出现裂纹或断裂o夹子从固定孔眼中脱落•功能不足=夹子不能将线束夹紧,失效模式:o夹子太大o夹子未锁定•功能过强=夹子将线束夹得过紧,失效模式:o夹子的金属边夹破了电线o夹子对不齐6. 推导各种失效模式的潜在后果•失效的结果(衍生物)•有可能后果o最终客户或中间客户o政府法规,或o系统层次中的某一部分•顾客的抱怨是有用的信息来源•其后果可能是:o功能完全丧失,或o性能或质量下降•许多失效模式有不止一种影响!•提示:从你在上面所提到的“无功能”情况出发•失效的后果通常表现为从直接后果到对客户的最终后果等一系列连锁反应•建议对每一种失效模式建立这种关系链,并记录在失效模式及后果分析FMEA表上o运用树形图(故障树)6. 说明•无功能=夹具不能将电线固定住•失效模式:夹具弯曲处出现裂缝•后果:线束松脱o可能缠住或绊住o可能丧失电气功能•功能不足=夹子不能将电线夹紧•失效模式:线束松动•后果:线束发出咔嗒声o客户感觉到嗓音•功能过强=夹子将线束夹的过紧•失效模式:夹具不对中•后果:使线束变形o有可能使接头移位o有可能使电气系统丧失功能6. 失效的后果•如果影响了安全或对政府法规的符合性,就应如实讲清。