设计失效模式与失效效应
设计失效模式及效应分析(DFMEA)

6
Development of a Design FMEA 设计FMEA的开始 设计 的开始
First Step of DFMEA: IDENTIFY DESIGN INTEND 第一步 : 确定设计意图 “Listing of what design is expected to do and what is expected not to do” “列出设计期望做什么和不期望做什么?
FMEA Date (Orig.) ______(Rev.)____ehicle(s)____________________
7
8 Core Team__________________________________________________________________________________________________________________________
Subsystem Level
Frame Function: –Provides stable attachment for seat support Potential Failure Mode(s) Structural failure seat support Excessive deflection of seat support Function: –Provides pleasing appearance Potential Failure Modes(s) Finish (shine)deteriorates Paint chips
Component Level Upper Frame
DFMEA(设计失效模式与效应分析)-20121123

※ RPN(風險順序數):計算並記錄糾正後的RPN值的結果。
14
設計FMEA分析步驟
15
設計FMEA嚴重度評估標準
16
設計FMEA發生率評估標準
17
設計FMEA難檢度評估標準
18
設計FMEA改善對策提出時機
The timing to provide solution / 提出改善對策之時機
以利追蹤
※ Planning Stage(設計階段):填上依據目前所進行分析標的物所處之開發階段 ※ Design Responsibility (設計責任):填入負責的設計與開發之工程師全名
※ Prepared By(編制者):填入負責編制DFMEA的工程師的姓名
※ Part Name/Program(系統、子系統或零部件的名稱及編號):填入適當的分析級別並
12
設計FMEA分析表說明(Ⅲ)
※ POTENTIAL CAUSE(S) / MECHANISM(S) OF FAILURE(失效的潛在原因或機理) :填入每一
個失效模式的所有可以想到的失效原因或失效機理。
※ DESIGN CONTROLS(現行設計管制):填入已經完成或承諾要完成的預防措施、設計確認
DFMEA(設計失效模式與效應分析)
Design Failure Mode and Effect Analysis
1
什麽是FMEA ?
※
FMEA是一種系統方法,使用制式表格及問題解決
方法以確認潛在失效模式及其效應,並評估其嚴重度、 發生度、難檢度(探測/偵測)及目前管制方法,從而計算
風險優先指數(RPN),最後採取進一步改善方法,如此
持續進行,以達防患失效模式及效應發生於未然
失效模式与效应分析

上失效模式与效应分析(failure modes and effects analysis, FMEA)¾又名:潜在失效模式与效应分析(PotentialfaiIUre modes and effects analysis),失效模式、影响与危害性分析(failure modes, effects, and criticality analysis, FMECA)A概述失效模式与效应分析(FMEA)是一步步地识别在设计、生产或装配过程以及最终产品和服务中全部可能失效的一种方法。
“失效模式”意思是可能产生某些失效的方式或模式。
失效是任何的错误或者缺陷,尤其是那些影响顾客的、潜在的或实际的。
“效应分析”指的是争论这些失效的后果或效应。
这些失效依据他们结果的严峻性、发生的频率以及被检测到的简洁度优先排序。
FMEA的目的是从有最高的、优先级的开头来实行行动消退或者削减失效。
FMEA通常把当前有关失效的学问以及所实行的行动文档化,用于持续的改进。
FMEA用于设计中预防失效的发生,之后又用于正在进行的过程操作中的掌握。
抱负地说, FMFA 开头于产品的概念设计阶段,贯穿于产品或服务的整个生命期中。
FMEA在19世纪40年月最早被应用于美国的军队中,然后在航空和自动化行业得到进一步的进展应用。
一些行业已经把FMEA的标准正规化,下面是一个综述。
在实行FMEA过程之前,需通过其他的参考资料和培训,从而学习更多关于组织和行业的标准和具体的方法。
>适用场合•当一个产品或服务正在被设计或者重复设计时,在QFD之后或者在设计完成之后;•当以全新的方式应用现有的过程、产品或服务时;•在形成新的或改进过程的掌握方法以前;•当对现有的过程、产品或服务方案改进的时候;•当分析现有的过程、产品或者服务失效缘由时;•贯穿于过程、产品或者服务的生命期中定期进行检查。
>实施步骤这只是一个也许的过程,具体的细节则随着组织或行业的标准而有所变化。
设备潜在失效模式及效应分析

设备潜在失效模式及效应分析设备潜在失效模式及效应分析(FMEA)是一种系统性的方法,用于识别设备潜在的失效模式及其可能的影响。
这种方法可以帮助组织预测设备可能出现的问题,从而采取预防性措施来避免这些问题的发生。
在进行设备潜在失效模式及效应分析时,首先需要确定设备要分析的功能或特性。
然后,对于每一个功能或特性,需要识别所有可能的失效模式。
失效模式是指设备在执行其功能或特性时可能发生的故障方式。
一旦失效模式被确定,下一步就是对每种失效模式进行评估,确定其可能的影响。
这些影响可以涉及到安全、质量、生产效率、环境和成本等方面。
通过对失效模式和其影响进行分析,可以确定哪些失效模式是最严重的,从而可以优先采取措施来预防或减轻这些失效的影响。
设备潜在失效模式及效应分析对于预测设备可能出现的故障非常有益。
通过这种分析,组织可以采取有效的措施来避免或减少设备故障可能造成的负面影响。
这不仅可以提高设备的可靠性和可用性,还可以降低维护成本,提高生产效率,保护员工安全,保护环境等。
总之,设备潜在失效模式及效应分析是一种重要的工具,可以帮助组织预测设备可能的故障,并制定相应的预防措施。
这种分析方法不仅可以提高设备的可靠性和可用性,还可以降低维护成本,提高生产效率,保护员工安全和环境等方面都具有重要作用。
设备潜在失效模式及效应分析(FMEA)是一种系统性的方法,用于识别设备潜在的失效模式及其可能的影响。
这种方法可以帮助组织预测设备可能出现的问题,从而采取预防性措施来避免这些问题的发生。
在进行设备潜在失效模式及效应分析时,首先需要确定设备要分析的功能或特性。
然后,对于每一个功能或特性,需要识别所有可能的失效模式。
失效模式是指设备在执行其功能或特性时可能发生的故障方式。
失效模式的识别可以通过对设备的历史数据、技术文档、专家意见等进行调研,以找出设备可能存在的各种故障情况。
一旦失效模式被确定,下一步就是对每种失效模式进行评估,确定其可能的影响。
风险评估技术-失效模式和效应分析(FMEA)及失效模式、效应和危害度分析(FMECA)

失效模式和效应分析(FMEA及失效模式、效应和危害度分析(FMECA)1 概述失效模式和效应分析(Failure Mode and Effect Analysis ,简称FMEA)是用来识别组件或系统未能达到其设计意图的方法。
FMEA 用于识别:•系统各部分所有潜在的失效模式(失效模式是被观察到的是失误或操作不当);•这些故障对系统的影响;• 故障原因;• 如何避免故障及 /或减弱故障对系统的影响。
失效模式、效应和危害度分析(Failure Mode and Effect and Criticality Analysis ,简称 FMECA)拓展了 FMEA 的使用范围。
根据其重要性和危害程度,FMECA 可对每种被识别的失效模式进行排序。
这种分析通常是定性或半定量的,但是使用实际故障率也可以定量化。
2 用途FMEA 有几种应用:用于部件和产品的设计(或产品) FM EA ;用于系统的系统FMEA ;用于制造和组装过程的过程 FMEA ;服务FMEA和软件FMEA。
FMEA/ FMECA 可以在系统的设计、制造或运行过程中使用。
然而,为了提高可靠性,改进在设计阶段更容易实施。
FMEA/ FMECA 也适用于过程和程序。
例如,它被用来识别潜在医疗保健系统中的错误和维修程序中的失败。
FMEA/FMECA 可用来:•协助挑选具有高可靠性的替代性设计方案;•确保所有的失效模式及其对运行成功的影响得到分析;•列出潜在的故障并识别其影响的严重性;•为测试及维修工作的规划提供依据;• 为定量的可靠性及可用性分析提供依据。
它大多用于实体系统中的组件故障,但是也可以用来识别人为失效模式及影响。
FMEA 及 FMECA 可以为其他分析技术,例如定性及定量的故障树分析提供输入数据。
3 输入数据FMEA 及 FMECA 需要有关系统组件足够详细的信息,以便对各组件出现故障的方式进行有意义的分析。
信息可能包括:• 正在分析的系统及系统组件的图形,或者过程步骤的流程图;• 了解过程中每一步或系统组成部分的功能;• 可能影响运行的过程及环境参数的详细信息;• 对特定故障结果的了解;• 有关故障的历史信息,包括现有的故障率数据。
失效模式与效应分析
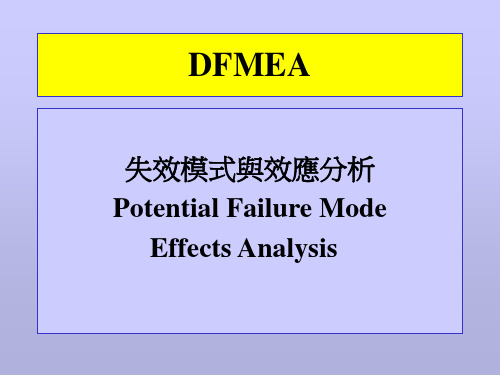
國際間采用FMEA之狀況
1.ISO9004 8.5節FMEA作為設計審查之要項。 2.CE標志,以FMEA作為安全分析方法。 3.ISO14000,以FMEA作為重大環境影響面
分析與改進方法。 4.QS9000以FMEA 作為設計與制程失效分
析方法。
設計FMEA之目的
1.幫助設計需求與設計方案的評估。 2.幫助初始設計對制造和裝配的需求。 3.在設計發展階段,增加失效模式和系統效應分析的次數。 4.提供另一項分析資訊,幫助設計驗證之規劃。 5.根據對顧客需求的影響性,列出失效模式的排序,並按序改
統或零件名稱或零件名稱和編號。 (3)設計責任者:填入OEM、部門和小組,也包括供應商名稱。 (4)準備者:填入準備FMEA責任工程師的姓名、電話號碼、公司。 A.系統FMEA範圍:
-底盤系統;-點火系統;-內部系統 B.子系統FMEA範圍
-底盤系統之前懸吊系統 C.零件範圍
-“Strut”為前懸吊系統之零件。
4.1980年修改為MIL-STD-1629A,延用至今 5.1985由國際電工委員會(IEC)出版之FMECA國際標準
(IEC812),即參考MIL-STD-1629A加以部份修改而成。
FMEA之特徵
1.是一項以失效為討論重點的支援性與輔助性的可靠度技術。 2.用表格方式進行工程分析,使產品在設計與制程規劃時,早
項目 功能
潛在 失效 模式
潛在 嚴 等 潛在原 發 現行預
失效 重 級 因設備 生 防設計
效應 度
失 效 度 管制
現行檢 難 風險 建議 負責
測設計 管制
檢 度
優先 數
措施
人與 日期
采行 措施
執行結果 S O D RPN
dfmea与pfmea的意思

dfmea与pfmea的意思
DFMEA和PFMEA是两种不同的质量管理工具,用于在产品开发和生产过程中预测并防止可能的故障。
DFMEA是指设计失效模式和效应分析,是在产品设计阶段进行的,旨在识别并排除因设计缺陷而可能引起的故障。
DFMEA的过程包括确定设计元素,识别潜在失效模式,评估失效的重要性和潜在后果,确定并实施预防措施。
PFMEA是指生产过程失效模式和效应分析,是在生产过程中进行的,旨在识别并排除由于生产过程中的缺陷而可能发生的故障。
PFMEA 的过程包括确定生产过程和控制计划,识别可能的失效模式,评估失效的严重性和潜在后果,确定并实施预防措施和监测措施。
DFMEA和PFMEA都是基于风险评估的方法,旨在识别并排除潜在的故障和缺陷。
通过采用DFMEA和PFMEA,企业可以及早发现并解决产品和生产过程中的问题,从而降低了质量成本、提高了生产效率,提高了客户满意度。
同时,DFMEA和PFMEA也是许多行业标准和法规所要求的必要工具,如医疗器械、汽车工业等。
总之,DFMEA和PFMEA是预防品质问题的重要工具,通过识别、评估潜在失效模式,优化设计和制造流程,防止品质问题并提升整体品质水平。
SATA7+6设计失效模式与效应分析DFMEA

邬彬
品質工程師 QE/QC Engineer(s)
毛银华
开發工程師 RD Engineer
核准人 Approved by
邬彬
專案號碼 Project No.
製造處工程人員 Manafacturing Engineer(s)
項目 & 功能/ 製程 & 要求
Item & Function/
发生ReP数qruoicre极esms e&低nts 很低
邬彬
專案號碼 Project No.
製造處工程人員 Manafacturing Engineer(s)
項目 & 功能/ 製程 & 要求
Item & Function/ Process &
Requirements
S
潛在失效模式 Potential Failure Mode
潛在失效效應 Potential Effect(s) of
度
1.首件检测 4 2.自检
3.IPQC巡检
毛圆圆
料號 P/N
核准日期 App. Date
其他人員 Others
SS3-13022-020
FMEA No. DFMEA- 0268
修訂日期Revised Date:
原始日期Original Date: 12.12.06
D
現行偵測設計(製程)管制 E
Current Design(Process)
S
OD
R
E
CE
P
V
CT
N
嚴
發難
風
重
生檢
險
度
度度
優
先
5
- 1、下载文档前请自行甄别文档内容的完整性,平台不提供额外的编辑、内容补充、找答案等附加服务。
- 2、"仅部分预览"的文档,不可在线预览部分如存在完整性等问题,可反馈申请退款(可完整预览的文档不适用该条件!)。
- 3、如文档侵犯您的权益,请联系客服反馈,我们会尽快为您处理(人工客服工作时间:9:00-18:30)。
RDPM 詳細記錄實際採行的改善措 施行動與有效日期
實施執行改善措施
設計工程師
RPN>=100 或 Sev>=9
NO
設計工程師
DFMEA審查
DQC RDPM:存檔於NPI Server DQC:審查核准匯入 xFMEA
完成/存檔
ห้องสมุดไป่ตู้
RDPM / DQC
第三章
實施DFMEA時機
第三章需求提出
第五章DFMEA表格說明-2
⑥
⑦
⑧ ⑨⑩
6. POTENTIAL CAUSE(S) / MECHANISM(S) OF FAILURE:
填入每一個失效模式的所有可以想到的失效原因或失效機理。
7. OCC:
描述發生度級別數著重在描述可能性的級別數之相對意義。
8. DESIGN CONTROLS:
填入已經完成或承諾要完成的預防措施、設計確認/驗證或其他活動。
歷程之具體表徵
名詞解釋
• 嚴重度(S, Severity)
•
• •
•
用以評估該失效模式對客戶或後製程影響之後果的嚴重程度。 發生度(O, Occurrence) 指某一特定的失效原因/機制在設計壽命內出現的可能性與機率。 難檢度(D, Detection) 失效造成的製品缺陷在離開製程前被檢驗出來的難易程度。 風險優先指數(RPN, Risk Priority Number) 是評估失效風險大小的指數;亦是嚴重度(S)和發生度(O) 及 難檢度(D)三項數字之乘積。 失效(Failure) 在規定條件下(環境、操作、時間),凡一個系統、子系統或其 中的模組、零組件不能完成既定功能或產品參數值和不能維持在 規定的上下限之間,以及在工作範圍內未能達到預定機能的現象。
Analysis 製程失效模式與效應分析
第一章DFMEA說明
• FMEA:一種失效分析手法,包含設計端的
DFMEA及製造端的PFMEA
• DFMEA:設計階段針對layout,機構,電子,包裝,
軟體,韌體…分析有哪方面會造成品質異常
• PFMEA:產線中人員,機器,材料,方法…分析有
哪些方面會造成產品潛在品質異常
④⑤
1. Design Item & Function/Requirements:
填入被分析項目的名稱和編號。
2. Potential Failure Mode:
對於一個特定項目及其功能,列出每一個潛在的失效模式。
3. Potential Effects(s) of Failure:
填入功能上之失效模式的效果或指為顧客感受到的失效模式對功能的影響。
12. RESPONSIBILITY AND TARGET COMPLETION DATE:
填入建議措施的責任組織的名稱和個人的姓名以及目標完成的日期
13. ACTIONS TAKEN:
填入在措施實施之後實際措施的簡要說明(但必須)以及生效日期。
14. SEV/OCC/ DET :
確定了預防/糾正措施以後,重新估算並記錄糾正後的嚴重度、發生度和難檢度值。
第一章
DFMEA簡介
第一章DFMEA簡介
• FMEA
Failure Mode and Effects Analysis 失效模式與效應分析
• DFMEA Design Failure Mode and Effects
Analysis 設計失效模式與效應分析
• PFMEA Process Failure Mode and Effects
第二章
DFMEA運作流程
第二章流程圖
設計失效模式與效應分析
DFMEA小組 Kick off meeting 責任單位 SPM 備註 SPM決定推行 DFMEA的小組成員 xFMEA撈取資料庫提供給 RDPM 確定各設計工程師執行 DFMEA時程 類似機種DFMEA表提供 DQC 召開DFMEA會議 DQC
– 當下列條件發生時則必須實施DFMEA分析
1. 新產品開發 2. 設計改良時 3. 客戶要求時
第四章
DFMEA產出方式
第四章DFMEA報告產出
ES
•DQC召集電子硬體、機構、 軟體、包材相關設計RD進行 產品潛在失效模式分析, 並 匯總、審查後匯入xfmea資料 庫 •類似機種由DQC從xfmea資 料庫轉出類似機種DFMEA報 告,供研發RD設計參考。
9. DET:
指與設計控制中所列的最佳探測控制相關聯的等級數。
10. RPN:
嚴重度數(S)和發生度數(O)及難檢度數(D)三項數字之乘積
第五章DFMEA表格說明-3
11
12
13
14 15
11. RECOMMENDED ACTION(S) :
針對高嚴重度((S)≥9 ) 、高RPN值(RPN≥100)或依顧客規定要求項 目進行預防/ 糾正措施的改善動作。
4. 嚴重度
填入評估潛在失效後果的嚴重程度等級,其評定準則和分級分為1—10級。
5. SCC(CLASSICICATION) :
針對RPN≥100 、嚴重度數(S)≥9 以及當產品和/或過程歸類為關鍵特性,標 識/註明那些可能需要附加的設計或程序控制的部件、子系統或系統的產品特 殊特性,其使用之標誌符號(*)參考關鍵特性管制程序。
15. RPN:
計算並記錄糾正後的RPN值的結果。
第六章
結語
結語
• FMEA是一種系統分析方法,類似PDCA:
1.Plan:作業從評估產品設計失效模式計劃開始 2.Do:如何透過設計控制避免失效 3.Check:多方面確認設計缺失 4.Action:針對設計缺失實施有效改善對策
• FMEA為工程人員智慧的匯聚,為全員思考
DFMEA設計失效模式 效應分析
DFMEA分析範例
• • • • • •
Requirement : 交女友 Potential Failure mode : 被女友甩 Potential cause : 外型不優 Design control : 找造型師改變造型 Recommended action : 換新髮型,改變穿著及打扮 Action taken : 換新髮型
EV/DV
•RD可於TTS上擷取各驗證單位( 應包含QTR, SIT, EMC, Safety, EA)測試後的Critical及Major bug
加入DFMEA報告追蹤確認是 否風險降低,並提供給DQC 更新到xfmea資料庫
11
第五章
DFMEA表格內容說明
第五章DFMEA表格說明-1
①
②
③
提交方塊圖
設計工程師 1.註明嚴重程度(關鍵重要) 2.關鍵特性管制程序
進行風險評估
NO
設計工程師
是否為關鍵特性
YES
設計工程師
RPN>=100 或 Sev>=9
YES
設計工程師
對RPN值最高的重點項目以 及關鍵特性規劃改善措施
記錄於DFMEA分析表
設計工程師
規劃建議改善措施
設計工程師
確定負責改善部門/個人
Thanks!
19