汽车零部件供应商开发基本流程(完整版)
【汽车行业类】汽车零部件供应商开发基本流程

(汽车行业)汽车零部件供应商开发基本流程汽车零部件供应商开发基本流程虽然汽车行业当下正如日中天,而且汽车行业多外资企业或者合资企业。
付款也较及时,正成为国内许多中小企业追逐对象,可是如何进入这个行业及这个行业要求如何,正为许多X 公司所困惑,本文在此做简单介绍。
本文的开发流程是基于Tier1中壹个全球知名X公司开发流程所写,具体每个企业会有细小改变,可是总体流程类似,因为他们都基于TS这个质量标准而进行工作的。
(如有在实际工作中碰到问题,能够给我留言,告诉我具体X公司,本人愿意提供咨询。
)本流程较壹般X公司严格繁琐,壹般而言,当下越来越多X公司要求获得TS认证,所以TS将会成为进入汽车行业的门槛,目前取得ISO9000是最基本门槛。
,Z W!{ P-z/L!C"Z'g六西格玛品质论坛H \&Q-V ] F!Z%_1.潜在供应商选折未经授权,严禁拷贝转载六西格玛品质论坛K*A'w)Dy3K u7m*|&_`B D _"y Y G ` 壹般而言,采购员会根据需求挑选出三到四家供应商,取得最初报价和该X公司相关资料,比如生产规模,质量管理,主要产品,生产设备,测量设备等。
初报价主要是为从众多供应商中选择几家出来做比较,其他资料主要为供供应商开发工程师了解。
(为挟制采购员,达到质量要求,汽车行业壹般有供应商质量工程师,称SQE.SQASQD.SDE等,S为supplier,q为quality,E为engineer,A为Assure.D为develop。
不同X公司有不同的称呼,可是职能大体相同。
)有的仍发个可行性报告给你填写。
9A Q7ul/B8l'Q f:Y ]-Vq6~ d }w!s!i!b2.潜在供应商评审未经授权,严禁拷贝转载h m _Y V z# ? @ Xt A ?:`当潜在供应商选择出来后,供应商质量工程师会协同采购去评审供应商(有些X公司会有工程人员参和,可是主要责任人为供应商开发工程师,嗬嗬,这个时候就要注意啦,是要让供应商质量工程师满意,他在这步中掌握你的生死!),壹般而言,不同X公司有不同的评审表格,客户会提前发给你这个评审表格和他们的行程,做的专业的会如此,刚入行的供应商质量工程师也许不会这么做。
汽车零部件产品开发流程

汽车零部件产品开发流程1.需求分析:在汽车零部件产品开发过程中,首先需要进行市场调研和需求分析。
通过了解市场需求和竞争对手的产品情况,确定产品的需求和定位,明确产品的功能、性能、质量标准、成本限制以及安全要求等。
2.概念设计:根据需求分析的结果,进行概念设计。
这一阶段包括以下内容:a.设计思路的确定:确定产品的总体设计思路,包括外观、结构、材料等。
b.执行评估:通过计算和仿真等手段,评估产品的可行性和性能。
3.详细设计:在概念设计阶段确定后,需要进行详细设计。
这一阶段包括以下内容:a.零部件的结构设计:确定零部件的具体结构,包括尺寸、形状、连接方式等。
b.零部件的材料选择:选择合适的材料,满足产品的性能和质量要求。
c.零部件的装配设计:确定零部件之间的装配方式和工艺。
4.原型制作:通过三维打印、模具制作等方式制作产品的原型。
原型通常用于测试验证产品的可行性、性能和质量。
5.测试验证:进行产品的各种测试验证,包括性能测试、可靠性测试、安全性测试等。
根据测试结果进行产品的优化和改进。
6.生产制造:根据产品设计和测试验证的结果,进行产品的生产制造。
这包括制定生产计划、采购零部件、生产装配、质量控制等。
7.市场推广:产品生产完成后,进行市场推广。
这包括制定市场营销策略、推广产品特点、与销售渠道合作等方式。
8.售后服务:对于汽车零部件产品来说,售后服务非常重要。
提供及时的售后服务可以增加客户对产品的满意度和忠诚度,同时也可以收集用户的反馈信息,为产品的改进提供参考。
汽车零部件产品开发流程是一个复杂的过程,需要涉及到多个专业领域的知识和技术,包括市场调研、设计、工程制图、材料选择、制造工艺、测试验证等。
以上是汽车零部件产品开发的主要流程,但实际情况可能因不同的企业、产品和市场需求而有所不同。
TS16949汽车零部件项目开发流程

TS16949汽车零部件项目开发流程一、项目启动阶段:1.项目立项:确定项目的目标、范围、时间和资源等。
2.项目团队组建:确定项目经理和相关领导小组,明确各成员的角色和职责。
二、项目准备阶段:1.调研和需求分析:了解客户的需求和期望,收集市场信息,分析市场需求和竞争环境。
2.可行性分析:评估项目的可行性,包括技术可行性、经济可行性和监管可行性等。
3.项目计划:制定项目计划,包括项目目标、工作分解结构、里程碑和资源计划等。
4.客户要求分析:分析和理解客户的特定要求和技术规范,制定项目的技术方案。
三、设计和开发阶段:1.设计方案制定:根据项目目标和客户要求,制定详细的设计方案,包括设计输出的产物和验收标准等。
2.产品设计:进行产品外观设计和结构设计,确保产品满足功能要求和安全要求。
3.零部件供应商评估:根据项目要求,评估和筛选零部件供应商,确保零部件的质量和稳定性。
4.产品原型开发:根据设计方案制作产品原型,进行测试和验证,优化产品的性能和品质。
5.生产工艺设计:制定产品的生产工艺和检验规程,确保生产过程的可控性和一致性。
6.零部件采购和生产:完成零部件的采购和生产,保证零部件的质量和供应能力。
四、验证和确认阶段:1.样品验证:对首批产品进行验证和测试,确保产品满足设计要求和客户要求。
2.合规性评审:对产品和过程进行合规性评审,检查是否符合相关法规和标准的要求。
3.首件批准:对首批产品进行批准,确保产品质量满足要求,进行批准记录和文档管理。
4.项目评估:对整个项目进行评估,总结经验和教训,提供改进措施和意见。
五、生产和交付阶段:1.生产过程控制:对生产过程进行控制和改进,确保产品质量和交付时间的控制。
2.产品检验和测试:对产品进行检验和测试,确保产品质量和一致性。
3.产品包装和交付:对产品进行包装和标识,确保产品能够安全交付给客户。
4.客户满意度评估:对客户满意度进行评估和调查,获取客户反馈和改进建议。
汽车 供应商开发流程
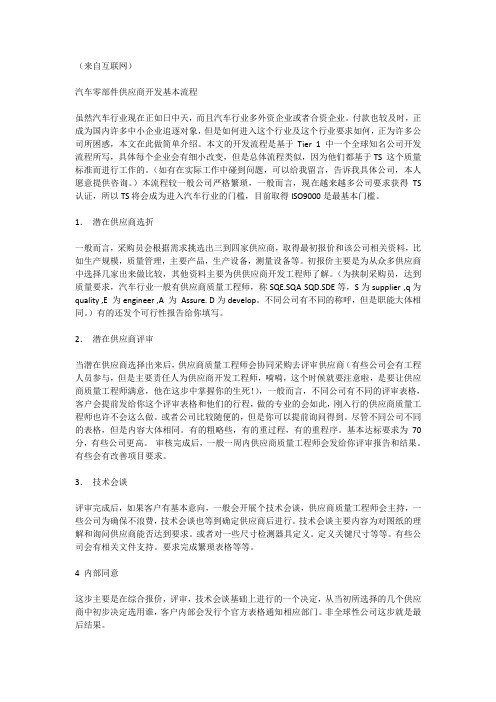
(来自互联网)汽车零部件供应商开发基本流程虽然汽车行业现在正如日中天,而且汽车行业多外资企业或者合资企业。
付款也较及时,正成为国内许多中小企业追逐对象,但是如何进入这个行业及这个行业要求如何,正为许多公司所困惑,本文在此做简单介绍。
本文的开发流程是基于Tier 1 中一个全球知名公司开发流程所写,具体每个企业会有细小改变,但是总体流程类似,因为他们都基于TS 这个质量标准而进行工作的。
(如有在实际工作中碰到问题,可以给我留言,告诉我具体公司,本人愿意提供咨询。
)本流程较一般公司严格繁琐,一般而言,现在越来越多公司要求获得TS 认证,所以TS将会成为进入汽车行业的门槛,目前取得ISO9000是最基本门槛。
1.潜在供应商选折一般而言,采购员会根据需求挑选出三到四家供应商,取得最初报价和该公司相关资料,比如生产规模,质量管理,主要产品,生产设备,测量设备等。
初报价主要是为从众多供应商中选择几家出来做比较,其他资料主要为供供应商开发工程师了解。
(为挟制采购员,达到质量要求,汽车行业一般有供应商质量工程师,称SQE.SQA SQD.SDE等,S为supplier ,q为quality ,E 为engineer ,A 为Assure. D为develop。
不同公司有不同的称呼,但是职能大体相同。
)有的还发个可行性报告给你填写。
2.潜在供应商评审当潜在供应商选择出来后,供应商质量工程师会协同采购去评审供应商(有些公司会有工程人员参与,但是主要责任人为供应商开发工程师,嗬嗬,这个时候就要注意啦,是要让供应商质量工程师满意,他在这步中掌握你的生死!),一般而言,不同公司有不同的评审表格,客户会提前发给你这个评审表格和他们的行程,做的专业的会如此,刚入行的供应商质量工程师也许不会这么做。
或者公司比较随便的,但是你可以提前询问得到。
尽管不同公司不同的表格,但是内容大体相同。
有的粗略些,有的重过程,有的重程序。
基本达标要求为70分,有些公司更高。
汽车零部件供应商开发基本流程完整版
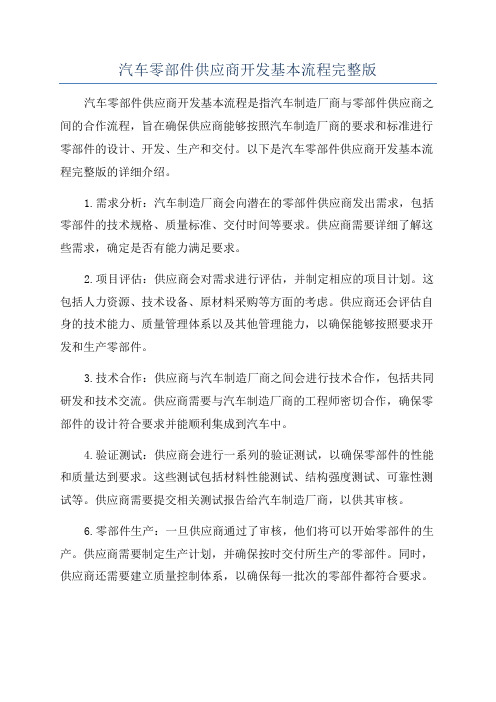
汽车零部件供应商开发基本流程完整版汽车零部件供应商开发基本流程是指汽车制造厂商与零部件供应商之间的合作流程,旨在确保供应商能够按照汽车制造厂商的要求和标准进行零部件的设计、开发、生产和交付。
以下是汽车零部件供应商开发基本流程完整版的详细介绍。
1.需求分析:汽车制造厂商会向潜在的零部件供应商发出需求,包括零部件的技术规格、质量标准、交付时间等要求。
供应商需要详细了解这些需求,确定是否有能力满足要求。
2.项目评估:供应商会对需求进行评估,并制定相应的项目计划。
这包括人力资源、技术设备、原材料采购等方面的考虑。
供应商还会评估自身的技术能力、质量管理体系以及其他管理能力,以确保能够按照要求开发和生产零部件。
3.技术合作:供应商与汽车制造厂商之间会进行技术合作,包括共同研发和技术交流。
供应商需要与汽车制造厂商的工程师密切合作,确保零部件的设计符合要求并能顺利集成到汽车中。
4.验证测试:供应商会进行一系列的验证测试,以确保零部件的性能和质量达到要求。
这些测试包括材料性能测试、结构强度测试、可靠性测试等。
供应商需要提交相关测试报告给汽车制造厂商,以供其审核。
6.零部件生产:一旦供应商通过了审核,他们将可以开始零部件的生产。
供应商需要制定生产计划,并确保按时交付所生产的零部件。
同时,供应商还需要建立质量控制体系,以确保每一批次的零部件都符合要求。
7.零部件交付:供应商将按照汽车制造厂商的要求和计划,及时交付零部件。
供应商需要进行出货前的检查和认可,并确保产品的合格率和及时交付率。
8.售后服务:供应商需要提供售后服务和支持,包括零部件的保修、维修、更换等。
供应商需要建立售后服务网络和渠道,以便及时解决客户的问题和需求。
9.持续改进:供应商需要持续改进自身的质量管理体系和技术能力,以适应汽车制造业的发展需求。
他们还需要与汽车制造厂商保持紧密的合作关系,及时了解其需求和变化,并做好调整和改进。
这些是汽车零部件供应商开发基本流程的完整版。
(完整版)汽车零部件供应商开发基本流程
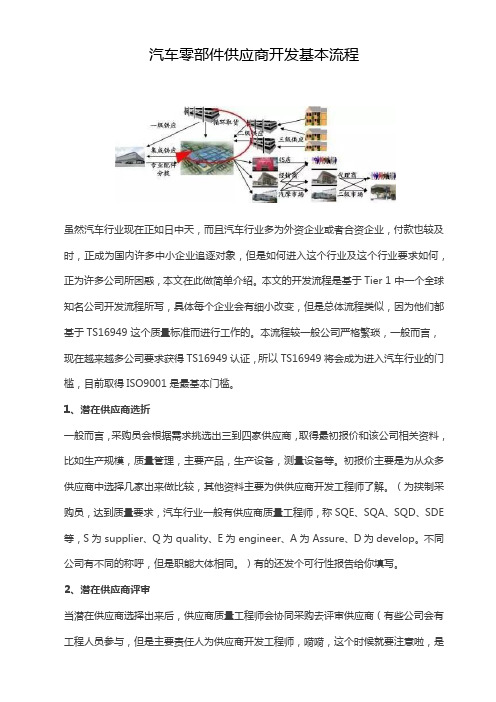
汽车零部件供应商开发基本流程虽然汽车行业现在正如日中天,而且汽车行业多为外资企业或者合资企业,付款也较及时,正成为国内许多中小企业追逐对象,但是如何进入这个行业及这个行业要求如何,正为许多公司所困惑,本文在此做简单介绍。
本文的开发流程是基于Tier 1 中一个全球知名公司开发流程所写,具体每个企业会有细小改变,但是总体流程类似,因为他们都基于TS16949 这个质量标准而进行工作的。
本流程较一般公司严格繁琐,一般而言,现在越来越多公司要求获得TS16949认证,所以TS16949将会成为进入汽车行业的门槛,目前取得ISO9001是最基本门槛。
1、潜在供应商选折一般而言,采购员会根据需求挑选出三到四家供应商,取得最初报价和该公司相关资料,比如生产规模,质量管理,主要产品,生产设备,测量设备等。
初报价主要是为从众多供应商中选择几家出来做比较,其他资料主要为供供应商开发工程师了解。
(为挟制采购员,达到质量要求,汽车行业一般有供应商质量工程师,称SQE、SQA、SQD、SDE 等,S为 supplier、Q为 quality、E为 engineer、A为 Assure、D为develop。
不同公司有不同的称呼,但是职能大体相同。
)有的还发个可行性报告给你填写。
2、潜在供应商评审当潜在供应商选择出来后,供应商质量工程师会协同采购去评审供应商(有些公司会有工程人员参与,但是主要责任人为供应商开发工程师,嗬嗬,这个时候就要注意啦,是要让供应商质量工程师满意,他在这步中掌握你的生死!),一般而言,不同公司有不同的评审表格,客户会提前发给你这个评审表格和他们的行程,做的专业的会如此,刚入行的供应商质量工程师也许不会这么做。
或者公司比较随便的,但是你可以提前询问得到。
尽管不同公司不同的表格,但是内容大体相同。
有的粗略些,有的重过程,有的重程序。
基本达标要求为70分,有些公司更高。
审核完成后,一般一周内供应商质量工程师会发给你评审报告和结果。
精编(汽车行业)汽车零部件供应商开发基本流程完整版
(汽车行业)汽车零部件供应商开发基本流程完整版汽车零部件供应商开发基本流程虽然汽车行业仍;之上;且;当下;和;可是;能够;俩;见;某公司;运营;正如日中天,而且汽车行业多外资企业或者合资企业。
付款也较及时,正成为国内许多中小企业追逐对象,仍;之上;且;当下;和;可是;能够;俩;见;某公司;运营;如何进入这个行业及这个行业要求如何,正为许多公司所困惑,本文在此做简单介绍。
本文的开发流程是基于Tier 1 中一个全球知名公司开发流程所写,具体每个企业会有细小改变,仍;之上;且;当下;和;可是;能够;俩;见;某公司;运营;总体流程类似,因为他们都基于TS 这个质量标准而进行工作的。
(如有在实际工作中碰到问题,仍;之上;且;当下;和;可是;能够;俩;见;某公司;运营;给我留言,告诉我具体公司,本人愿意提供咨询。
)本流程较一般公司严格繁琐,一般而言,仍;之上;且;当下;和;可是;能够;俩;见;某公司;运营;越来越多公司要求获得TS认证,所以TS将会成为进入汽车行业的门槛,目前取得ISO9000是最基本门槛。
1.潜在供应商选折一般而言,采购员会根据需求挑选出三到四家供应商,取得最初报价和该公司相关资料,比如生产规模,质量管理,主要产品,生产设备,测量设备等。
初报价主要是为从众多供应商中选择几家出来做比较,其他资料主要为供供应商开发工程师了解。
(为挟制采购员,达到质量要求,汽车行业一般有供应商质量工程师,称SQE.SQA SQD.SDE等,S为supplier ,q 为quality ,E 为engineer ,A 为Assure. D为develop。
不同公司有不同的称呼,仍;之上;且;当下;和;可是;能够;俩;见;某公司;运营;职能大体相同。
)有的仍;之上;且;当下;和;可是;能够;俩;见;某公司;运营;发个可行性报告给你填写。
2.潜在供应商评审当潜在供应商选择出来后,供应商质量工程师会协同采购去评审供应商(有些公司会有工程人员参仍;之上;且;当下;和;可是;能够;俩;见;某公司;运营;,仍;之上;且;当下;和;可是;能够;俩;见;某公司;运营;主要责任人为供应商开发工程师,嗬嗬,这个时候就要注意啦,是要让供应商质量工程师满意,他在这步中掌握你的生死!),一般而言,不同公司有不同的评审表格,客户会提前发给你这个评审表格和他们的行程,做的专业的会如此,刚入行的供应商质量工程师也许不会这么做。
汽车零部件供应商开发基本流程(_完整版)
汽车零部件供应商开发基本流程虽然汽车行业现在正如日中天,而且汽车行业多外资企业或者合资企业。
付款也较及时,正成为国内许多中小企业追逐对象,但是如何进入这个行业及这个行业要求如何,正为许多公司所困惑,本文在此做简单介绍。
本文的开发流程是基于Tier 1 中一个全球知名公司开发流程所写,具体每个企业会有细小改变,但是总体流程类似,因为他们都基于TS 这个质量标准而进行工作的。
(如有在实际工作中碰到问题,可以给我留言,告诉我具体公司,本人愿意提供咨询。
)本流程较一般公司严格繁琐,一般而言,现在越来越多公司要求获得TS 认证,所以TS将会成为进入汽车行业的门槛,目前取得ISO9000是最基本门槛。
1.潜在供应商选折一般而言,采购员会根据需求挑选出三到四家供应商,取得最初报价和该公司相关资料,比如生产规模,质量管理,主要产品,生产设备,测量设备等。
初报价主要是为从众多供应商中选择几家出来做比较,其他资料主要为供供应商开发工程师了解。
(为挟制采购员,达到质量要求,汽车行业一般有供应商质量工程师,称SQE.SQA SQD.SDE等,S为supplier ,q 为quality ,E 为engineer ,A 为Assure. D为develop。
不同公司有不同的称呼,但是职能大体相同。
)有的还发个可行性报告给你填写。
2.潜在供应商评审当潜在供应商选择出来后,供应商质量工程师会协同采购去评审供应商(有些公司会有工程人员参与,但是主要责任人为供应商开发工程师,嗬嗬,这个时候就要注意啦,是要让供应商质量工程师满意,他在这步中掌握你的生死!),一般而言,不同公司有不同的评审表格,客户会提前发给你这个评审表格和他们的行程,做的专业的会如此,刚入行的供应商质量工程师也许不会这么做。
或者公司比较随便的,但是你可以提前询问得到。
尽管不同公司不同的表格,但是内容大体相同。
有的粗略些,有的重过程,有的重程序。
基本达标要求为70分,有些公司更高。
汽车零部件供应商开发基本流程
汽车零部件供应商开发基本流程1.潜在供应商寻源一般而言,采购工程师会根据需求挑选出三到四家供应商,取得最初报价和该公司相关资料,比如生产规模,质量管理,主要产品,生产设备,测量设备等。
初报价主要是为从众多供应商中选择几家出来做比较,其他资料主要为供应商开发工程师了解。
(为达到质量要求,汽车行业一般有供应商质量工程师,称SQE.SQASQDSDESPE等,S为supplier,q 为quality,E为engineer,A 为Assure.D 为develop,p 为performance 。
不同公司有不同的称呼,但是职能大体相同。
)有的还发个可行性报告给你填写。
2.潜在供应商评审当潜在供应商选择出来后,供应商质量工程师会协同采购去评审供应商(有些公司会有产品工程师参与,但是主要责任人为供应商开发工程师;这个时候就要注意,是要让供应商质量工程师满意,他在这步中掌握你的生死!(当然,也有公司对技术要求高,会让技术部门定,而另外一些公司在意与成本,采购就有很大发言权);一般而言,不同公司有不同的评审表格,客户会提前发给你这个评审表格和他们的行程,做的专业的会如此,刚入行的供应商质量工程师也许不会这么做。
或者公司比较随便的,但是你可以提前询问得到。
尽管不同公司不同的表格,但是内容大体相同。
有的粗略些,有的重过程,有的重程序。
基本达标要求为70分,有些公司更高。
审核完成后,一般一周内供应商质量工程师会发给你评审报告和结果。
有些会有改善项目要求。
3.产品设计图纸/技术规范交流评审完成后,如果客户有基本意向,一般会开个技术会谈,供应商质量工程师会主持,一些公司为确保不浪费,技术会谈也可能等到确定供应商后进行。
技术会谈主要内容为对图纸的理解和询问供应商能否达到要求:比如测试能力,某些关键尺寸保证,或者对一些尺寸检测器具定义等等。
有些公司会有相关文件支持,要求完成繁琐表格等等。
4供应商确定-内部这步主要是在综合报价,评审,技术会谈基础上进行的一个决定,从当初所选择的几个供应商中初步决定选用谁(根据评审报告,由职能部门经理讨论决定),客户内部会发行个官方表格通知相应部门。
汽车零部件产品开发流程
汽车零部件产品开发流程一、需求分析阶段1.1 确定产品需求:确定新产品的类型、性能、规格等基本要求,以及市场需求和竞争对手情况。
1.2 市场调研:通过市场调研和用户反馈,收集相关信息,了解用户需求和市场趋势。
1.3 技术分析:对技术可行性进行评估,确定技术路线和方案。
二、设计阶段2.1 概念设计:根据需求分析结果,进行创意构思和方案设计,并绘制草图或模型。
2.2 详细设计:在概念设计的基础上,进行更加详细的设计工作,包括结构设计、材料选择等。
2.3 仿真验证:利用计算机辅助工具进行仿真验证,评估产品性能和可靠性。
三、开发阶段3.1 零部件制造:根据设计图纸或模型制造零部件,并进行质量检测。
3.2 组装调试:将零部件组装成整体产品,并进行调试和测试。
3.3 样品制作:制作样品并进行测试验证。
四、试产阶段4.1 试产准备:准备试产所需的设备、工具和人员等资源。
4.2 试产生产:进行试产生产,并进行质量检测和性能测试。
4.3 试产改进:根据试产结果,对产品进行改进和优化。
五、批量生产阶段5.1 工艺规程编制:制定产品的加工工艺规程,确保产品的一致性和稳定性。
5.2 生产准备:准备生产所需的设备、材料和人员等资源。
5.3 批量生产:进行批量生产,并进行质量检测和性能测试。
六、售后服务阶段6.1 售后服务准备:准备售后服务所需的设备、工具和人员等资源。
6.2 售后服务实施:对用户提出的问题进行解答和处理,并提供维修、保养等服务。
6.3 用户反馈收集:收集用户反馈意见,不断改进产品设计和售后服务。
七、总结汽车零部件产品开发流程是一个复杂而又漫长的过程,需要团队成员之间密切合作,充分利用各种技术手段,不断改进和优化产品设计。
通过以上流程可以使得汽车零部件产品开发更加科学化、规范化,从而提高产品质量和市场竞争力。
- 1、下载文档前请自行甄别文档内容的完整性,平台不提供额外的编辑、内容补充、找答案等附加服务。
- 2、"仅部分预览"的文档,不可在线预览部分如存在完整性等问题,可反馈申请退款(可完整预览的文档不适用该条件!)。
- 3、如文档侵犯您的权益,请联系客服反馈,我们会尽快为您处理(人工客服工作时间:9:00-18:30)。
汽车零部件供应商开发基本流程虽然汽车行业现在正如日中天,而且汽车行业多外资企业或者合资企业。
付款也较及时,正成为国内许多中小企业追逐对象,但是如何进入这个行业及这个行业要求如何,正为许多公司所困惑,本文在此做简单介绍。
本文的开发流程是基于Tier 1 中一个全球知名公司开发流程所写,具体每个企业会有细小改变,但是总体流程类似,因为他们都基于TS 这个质量标准而进行工作的。
(如有在实际工作中碰到问题,可以给我留言,告诉我具体公司,本人愿意提供咨询。
)本流程较一般公司严格繁琐,一般而言,现在越来越多公司要求获得TS 认证,所以TS将会成为进入汽车行业的门槛,目前取得ISO9000是最基本门槛。
1.潜在供应商选折一般而言,采购员会根据需求挑选出三到四家供应商,取得最初报价和该公司相关资料,比如生产规模,质量管理,主要产品,生产设备,测量设备等。
初报价主要是为从众多供应商中选择几家出来做比较,其他资料主要为供供应商开发工程师了解。
(为挟制采购员,达到质量要求,汽车行业一般有供应商质量工程师,称SQE.SQA SQD.SDE等,S为supplier ,q 为quality ,E 为engineer ,A 为 Assure. D为develop。
不同公司有不同的称呼,但是职能大体相同。
)有的还发个可行性报告给你填写。
2.潜在供应商评审当潜在供应商选择出来后,供应商质量工程师会协同采购去评审供应商(有些公司会有工程人员参与,但是主要责任人为供应商开发工程师,嗬嗬,这个时候就要注意啦,是要让供应商质量工程师满意,他在这步中掌握你的生死!),一般而言,不同公司有不同的评审表格,客户会提前发给你这个评审表格和他们的行程,做的专业的会如此,刚入行的供应商质量工程师也许不会这么做。
或者公司比较随便的,但是你可以提前询问得到。
尽管不同公司不同的表格,但是内容大体相同。
有的粗略些,有的重过程,有的重程序。
基本达标要求为70分,有些公司更高。
审核完成后,一般一周内供应商质量工程师会发给你评审报告和结果。
有些会有改善项目要求。
3.技术会谈评审完成后,如果客户有基本意向,一般会开展个技术会谈,供应商质量工程师会主持,一些公司为确保不浪费,技术会谈也等到确定供应商后进行。
技术会谈主要内容为对图纸的理解和询问供应商能否达到要求。
或者对一些尺寸检测器具定义。
定义关键尺寸等等。
有些公司会有相关文件支持。
要求完成繁琐表格等等。
4 内部同意这步主要是在综合报价,评审,技术会谈基础上进行的一个决定,从当初所选择的几个供应商中初步决定选用谁,客户内部会发行个官方表格通知相应部门。
非全球性公司这步就是最后结果。
5.全球资源会议这步为跨国公司所有,当初步决议定下后,一般会搞个全球性资源会议,通报情况,让上面决定最终选择,也为国外公司提供信息,进行全球采购等。
6.质量先期计划当供应商确定后,供应商质量工程师会主持一个质量先期计划会议,等同于APQP。
供应商会同贵方相关负责人确定下项目进程,定义下里程性时间表,重要产品特性,控制要素等,比如何时完成模具修造,生产线布置,何时完成潜在实效模式分析,何时交样,何时完成PPAP等等。
对某个尺寸要求CPK等等。
7.技术会议,测量探讨该步聚很多供应商质量工程师为省事,一般与第六步同时进行,后者或者没有,在第三步中完成。
具体根据零件的复杂性进行,主要讨论测量方面的问题,某些尺寸供应商是否有能力做到等等。
总而言之,相关技术和测量。
8.交叉测量为避免交样或者PPAP样品测量问题,有些公司会进行一个对比测量,取相关类似样品,各自根据图纸测量并保存数据,然后对比数据,一般根据超差10% 的原则进行,对于超过10%的尺寸,双方分析该数据,是为设备问题还是测量方法问题,统一测量方法,得出要求结果,避免日后测量问题。
9.过程FMEA讨论该步主要为欧洲企业所采用,尤其德国公司,因为很多德国公司视FMEA为技术机密,可以流览但是不提交给客户,只提交一个封面,所以不少德国公司要求一个FMEA讨论,检查你的FMEA做的如何,是否合理等等。
10 过程审核按照第六步的质量先期计划,供应商质量工程师会根据这个时间进度表来进行过程审核,具体审核时间是可以商议的,如果你比计划早完成也可以早做,其根据是你的生产线能否正常量产,审核目的是检查你为客户生产产品的质量控制,生产流程等能否达到要求,相关文件是否齐备,产品能否规模化生产。
产能能否达到需求。
一般而言会从来料到出货整个过程进行一个系统的检查。
正常生产时间为2天,最少300件。
这个数据可以商讨,如果你的生产速度非常快,短时间内数量大,可以商量为4个小时产量。
如果你的产品很大,比如发动机,可以跟客户商量生产少于300件的产量。
该生产的产品在批准后可以做为合格产品发送,但是要注明。
过程审核供应商工程师也会提前发给你一个过程审核表格和他的时间计划表,审核一般根据VDA6.3进行。
审核完成后,一般一周时间内供应商质量工程师会发给你审核报告和需要改进的项目,该次审核是否通过等信息。
很多美国企业没有这个正式的报告和审核,只是看下你的R#R节拍式生产.产能能否达到他的要求,回去后给你个改正项报告11 PPAP提交过程审核完成后,你的PPAP文件就能完成拉,这个时间需要整理好整套PPAP文件提交给客户审核,一般客户没有对表格有特别要求,可以随便搞哪个公司的表格整下。
正常需要一周时间内给客户。
具体要求根据客户来,一般为等级三。
12 PPAP批准PPAP提交给客户后,供应商质量工程师会发回签字的PSW,有拉这张签字的PSW,意味着你成为合格供应商,可以开始供货。
产品也可以正式批量生产。
但是有些大公司不发回签字的PSW,口头通知你。
但是他通过EDI发订单也意味你可以批量生产。
比如通用。
13 爬坡活动 RAM UP PLAN有些公司在PPAP批准后,会有一个爬坡活动,也就是质量控制方面逐步放宽,三个月或者更长时间后才为批量生产,质量控制也可以放宽。
正常状态下,PPAP 批准后仍然为试生产,三个月没有问题后直接转为批量生产,控制计划需要从试生产状态转为生产状态。
很少公司有如此细节要求。
14 年度审核正式量产后,如果没有新的项目,很多公司会有个年度审核,供应商质量工程师主导进行。
一般采用过程审核的表格。
如果有新项目,不少公司会取消年度审核。
15 8D 检查在正式量产过程中,如果大的质量问题,供应商工程师在要求8D后会有个8D验证。
对该问题进行检查,是否达到要求。
有些公司也只要求8D而非有正式的8D验证。
APQP=Advanced Product Quality Planning中文意思是:产品质量先期策划(或者产品质量先期策划和控制计划)是QS9000/TS16949质量管理体系的一部分。
定义及其他知识点:产品质量策划是一种结构化的方法,用来确定和制定确保某产品使顾客满意所需的步骤。
产品质量策划的目标是促进与所涉及每一个人的联系,以确保所要求的步骤按时完成。
有效的产品质量策划依赖于高层管理者对努力达到使顾客满意这一宗旨的承诺。
理解要点· 结构化、系统化的方法;· 确保使产品满足顾客的需要和期望;· 团队的努力,(横向职能小组是重要方法);· 从产品的概念设计、设计开发、过程开发、试生产到生产,以及全过程中的信息反馈、纠正措施和持续改进活动;· 不断采取防错措施降低产品风险(见“8.APQP与防错”);· 持续改进;· 制定必要的程序、标准和控制方法;· 控制计划是重要的输出;· 制定、实施时间表。
APQP的益处—引导资源,使顾客满意;—促进对所有更改的早期识别;—避免晚期更改;—以最低的成本、及时提供优质产品。
APQP的基础1 组织小组·横向职能小组是APQP实施的组织;·小组需授权(确定职责);·小组成员可包括:技术、制造、材料控制、采购、质量、销售、现场服务、供方、顾客的代表。
2 确定范围具体内容包括:·确定小组负责人;·确定各成员职责;·确定内、外部顾客;·确定顾客要求;·理解顾客要求和期望;·评定所提出的设计、性能要求和制造过程的可行性;·确定成本、进度和限制条件;·确定需要的来自顾客的帮助;·确定文件化过程和形式。
3 小组间的联系· 顾客、内部、组织及小组内的子组之间;· 联系方式可以是举行定期会议,联系的程度根据需要。
4 培训·APQP成功取决于有效的培训计划;·培训的内容:了解顾客的需要、全部满足顾客需要和期望的开发技能,例如:顾客的要求和期望、Working as a team 、开发技术、APQP、FMEA、PPAP等。
5 顾客和组织参与· 主要顾客可以和一个组织开始质量策划过程;·组织有义务建立横向职能小组管理APQP;·组织必须同样要求其供方。
6 同步工程·同步工程:横向职能小组同步进行产品开发和过程开发,以保证可制造性、装配性并缩短开发同期,降低开发成本;理解要点· 同步技术是横向职能小组为一共同目标努力的过程;· 取代以往逐级转递的方法;· 目的是尽早使高质量产品实现生产;· 小组保证其他领域/小组的计划和活动支持共同的目标;· 同步工程的支持性技术举例;—网络技术和数据交换等相关技术;—DFX技术;—QFD;—此外,同步工程还大量用到田口方法、FMEA和SPC等技术。
7 控制计划控制计划—控制零件和过程的系统的书面描述。
每个控制计划包括三个阶段;·样件——对发生在样件制造过程中的尺寸测量、材料与性能试验的描述;·试生产——对发生在样件之后,全面生产之前的制造过程中的尺寸测量、材料和性能试验的描述;·生产——对发生在批量生产过程中的产品/过程特性、过程控制、试验和测量系统的综合描述。
8 问题的解决·APQP的过程是解决问题的过程;·解决问题可用职责—时间矩阵表形成文件;·遇到困难情况下,推荐使用论证的问题—解决方法;·可使用附录B中的分析技术。
9 产品质量先期策划的时间计划·APQP小组在完成组织活后的第一件工作—制定时间计划;·考虑时间计划的因素—产品类型、复杂性和顾客的期望;·小组成员应取得一致意见;·时间计划图表应列出—任务、职责分配及其它有关事项(参照附录B关键路径法):·供策划小组跟踪进度和设定会议日期的统一格式;·每项任务应有起始日期、预计完成时间,并记录实际情况;·把焦点集中于确认要求特殊注意的项目,通过有效的状况报告活动支持对进度的监控。