双头专用车床液压系统设计
机床液压系统的设计
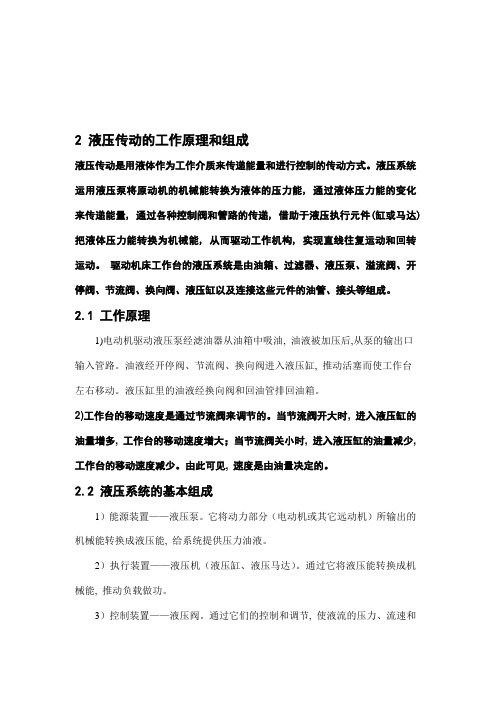
2 液压传动的工作原理和组成液压传动是用液体作为工作介质来传递能量和进行控制的传动方式。
液压系统运用液压泵将原动机的机械能转换为液体的压力能, 通过液体压力能的变化来传递能量, 通过各种控制阀和管路的传递, 借助于液压执行元件(缸或马达)把液体压力能转换为机械能, 从而驱动工作机构, 实现直线往复运动和回转运动。
驱动机床工作台的液压系统是由油箱、过滤器、液压泵、溢流阀、开停阀、节流阀、换向阀、液压缸以及连接这些元件的油管、接头等组成。
2.1 工作原理1)电动机驱动液压泵经滤油器从油箱中吸油, 油液被加压后,从泵的输出口输入管路。
油液经开停阀、节流阀、换向阀进入液压缸, 推动活塞而使工作台左右移动。
液压缸里的油液经换向阀和回油管排回油箱。
2)工作台的移动速度是通过节流阀来调节的。
当节流阀开大时, 进入液压缸的油量增多, 工作台的移动速度增大;当节流阀关小时, 进入液压缸的油量减少, 工作台的移动速度减少。
由此可见, 速度是由油量决定的。
2.2 液压系统的基本组成1)能源装置——液压泵。
它将动力部分(电动机或其它远动机)所输出的机械能转换成液压能, 给系统提供压力油液。
2)执行装置——液压机(液压缸、液压马达)。
通过它将液压能转换成机械能, 推动负载做功。
3)控制装置——液压阀。
通过它们的控制和调节, 使液流的压力、流速和方向得以改变, 从而改变执行元件的力(或力矩)、速度和方向, 根据控制功能的不同, 液压阀可分为村力控制阀、流量控制阀和方向控制阀。
压力控制阀又分为益流阀(安全阀)、减压阀、顺序阀、压力继电器等;流量控制阀涉及节流阀、调整阀、分流集流阀等;方向控制阀涉及单向阀、液控单向阀、梭阀、换向阀等。
根据控制方式不同, 液压阀可分为开关式控制阀、定值控制阀和比例控制阀。
4)辅助装置——油箱、管路、蓄能器、滤油器、管接头、压力表开关等.通过这些元件把系统联接起来, 以实现各种工作循环。
5)工作介质——液压油。
卧式双面铣削组合机床的液压系统设计
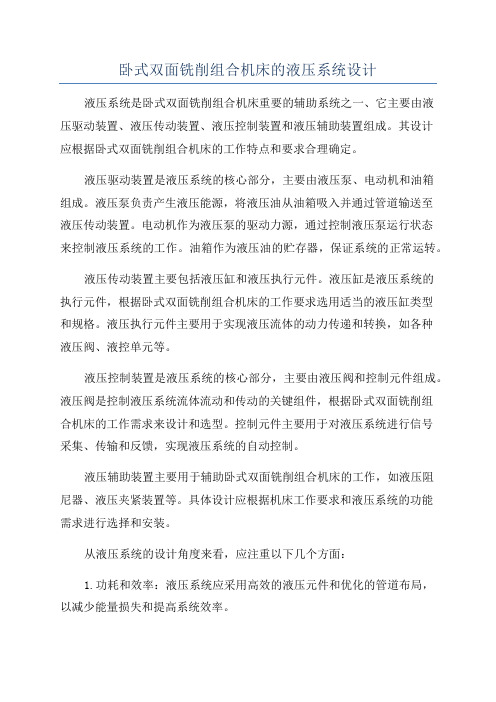
卧式双面铣削组合机床的液压系统设计液压系统是卧式双面铣削组合机床重要的辅助系统之一、它主要由液压驱动装置、液压传动装置、液压控制装置和液压辅助装置组成。
其设计应根据卧式双面铣削组合机床的工作特点和要求合理确定。
液压驱动装置是液压系统的核心部分,主要由液压泵、电动机和油箱组成。
液压泵负责产生液压能源,将液压油从油箱吸入并通过管道输送至液压传动装置。
电动机作为液压泵的驱动力源,通过控制液压泵运行状态来控制液压系统的工作。
油箱作为液压油的贮存器,保证系统的正常运转。
液压传动装置主要包括液压缸和液压执行元件。
液压缸是液压系统的执行元件,根据卧式双面铣削组合机床的工作要求选用适当的液压缸类型和规格。
液压执行元件主要用于实现液压流体的动力传递和转换,如各种液压阀、液控单元等。
液压控制装置是液压系统的核心部分,主要由液压阀和控制元件组成。
液压阀是控制液压系统流体流动和传动的关键组件,根据卧式双面铣削组合机床的工作需求来设计和选型。
控制元件主要用于对液压系统进行信号采集、传输和反馈,实现液压系统的自动控制。
液压辅助装置主要用于辅助卧式双面铣削组合机床的工作,如液压阻尼器、液压夹紧装置等。
具体设计应根据机床工作要求和液压系统的功能需求进行选择和安装。
从液压系统的设计角度来看,应注重以下几个方面:1.功耗和效率:液压系统应采用高效的液压元件和优化的管道布局,以减少能量损失和提高系统效率。
2.安全性:在设计液压系统时,应考虑到系统的安全性,采取相应的安全措施,如选用可靠的液压阀、安全阀等,并设置安全保护装置。
3.可靠性和可维护性:液压系统的设计应考虑到其可靠性和可维护性,方便日常的维护和检修工作。
4.自动控制:液压系统的设计应考虑到其自动控制功能的要求,可以通过采用液压控制元件和控制系统来实现。
总之,液压系统的设计应根据卧式双面铣削组合机床的工作要求和液压系统的功能需求进行合理的配置和选型,以实现系统的高效、安全、可靠的运行。
双头专用车床液压系统设计
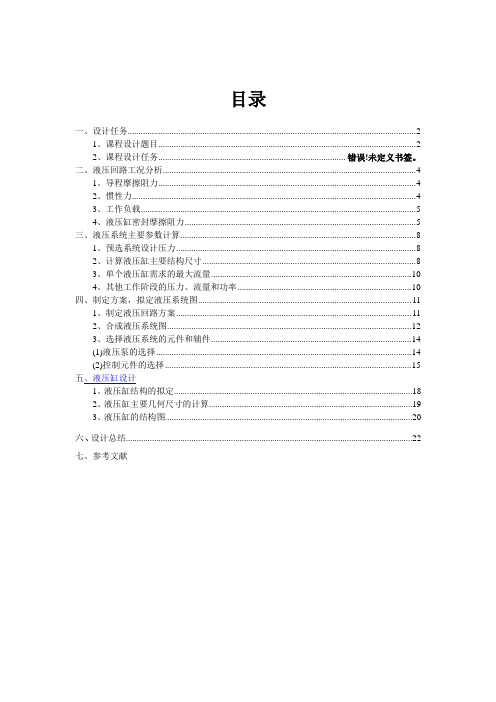
目录一、设计任务 (2)1、课程设计题目 (2)2、课程设计任务................................................................................... 错误!未定义书签。
二、液压回路工况分析 (4)1、导程摩擦阻力 (4)2、惯性力 (4)3、工作负载 (5)4、液压缸密封摩擦阻力 (5)三、液压系统主要参数计算 (8)1、预选系统设计压力 (8)2、计算液压缸主要结构尺寸 (8)3、单个液压缸需求的最大流量 (10)4、其他工作阶段的压力、流量和功率 (10)四、制定方案,拟定液压系统图 (11)1、制定液压回路方案 (11)2、合成液压系统图 (12)3、选择液压系统的元件和辅件 (14)(1)液压泵的选择 (14)(2)控制元件的选择 (15)五、液压缸设计1、液压缸结构的拟定 (18)2、液压缸主要几何尺寸的计算 (19)3、液压缸的结构图 (20)六、设计总结 (22)七、参考文献一、设计任务1、课程设计题目某厂欲自行设计制造一台专用车床,用于压缩机连杆两端长轴颈的车削加工。
根据加工工件尺寸较长的特点,拟采用的加工工艺方案为:工件固定,刀具旋转并进给。
车床主要由床身[布有相互平行的V形导轨和平导轨各一条(见图1-1)]和左右两个车削动力头组成,其总体布局如图2-2所示。
工件装夹于床身中部。
两个独立的动力头,通过机械传动带动主轴及刀具旋转实现车床的主运动;进给运动要求采用液压缸实现,即在床身上安装两个液压缸,使其活塞杆与各动力头下部相连,通过液压缸往复运动驱动动力头实现车床的进给运动。
车床加工工件时,车削动力头的进给工作循环为:快进→工进→快退→停止。
已知:移动部件重约是G=15kN;各车削动力头的最大切削进给抗力(轴向力)估值为Fe=10kN;主切削力(切向力)Fz=35kN。
要求动力头的快速进、退速度相等,V1=Vmax=3m/min;错误!未找到引用源。
双面组合铣床液压系统设计

双面组合铣床液压系统的设计摘要本双面组合铣床是从德国引进的抬起运输通过式气缸体铣钻自动生产线中一台专用加工设备,用于某轿车汽油发动机气缸体上发动机气缸体上发动机安装结合面、汽油泵及机油过滤器结合面、发动机安装结合面等部位的铣削加工。
本次设计液压系统步骤为明确设计要求进行工况分析、初定液压系统的主要参数、拟定液压系统原理图、计算和选择液压元件、估算液压系统性能、绘制工作图和编写技术文件。
本次设计采用高低压双泵供油。
实现了液压泵与负载要求的流量匹配,在传递动力的同时,提高了系统的传动性能和效率,因而是一个节能液压系统。
相互并联的各个回路中的电磁换向阀的进油路与总的回油路相连。
各泄油口与总的泄油回路相连,故各回路中进油、回油及泄油互不干扰,通过在各路上设置单向阀,以分割回路,达到防止回路间相互干扰的目的。
采用带阻尼器的Y型中位机能电磁换向阀,减小了换向冲击,提高了换向平稳性。
由电气行程开关作为系统中各换向阀的信号源。
故本系统基本上是一个行程控制多缸顺序动作系统,位置和行程调整方便,电气互锁动作可靠。
该组合机床及其液压系统运行平稳,振动、噪声及温升较小,工作可靠。
关键词:双面组合铣床;液压系统;设计AbstractThe double-sided milling machine is a special processing equipment,which is used in an automatic production line of Milling and Drilling passed by the lift transport cylinder block from Germany. It can be used in the milling of the surface of engine mounting junction, fuel pump and oil filters junction, engine installation junction and so on.the steps ,which is needed in the design of the hydraulic system ,are clear to the requirements of design and working conditions,choose the main parameters of the hydraulic system initially ,make an initial draft of hydraulic system schematics, calculation and selection of hydraulic components,estimate the efficiency of hydraulic system, working drawings and drawing preparation of technical documents.The design uses double pump to produce a high and low pressure oil. To achieve the pump and required load in flow matching, while in the transmission power to improve the performance and efficiency of the transmission system, which is an energy-efficient hydraulic system. The oil return line is connected to the total of the electromagnetic valve of each parallelled individual oil loop . The total of the drain port is connected to the drain circuit, and therefore the inlet of the circuit, the drain back to the oil and non-interfering, in all the way through a one-way valve to split the circuit, to prevent mutual interference between ed with a Y-type damper median function solenoid valve, reducing the commutation impact and improve the commutation smoothness. the electrical limit switch valve as the system of each source. So the system is basically a multi-cylinder stroke control system with sequence of actions, location and easy adjustment travel, reliable action of electrically interlocked.The combination of machine tools and hydraulic system running smoothly, vibration, noise and temperature rise is small, work reliablely.Key words :double-sided milling machine; hydraulic system; design目录摘要 (I)Abstract..................................................................................................................................................... I I 目录 (1)绪论 (2)1.液压传动的发展 (3)1.1液压系统的发展与现状 (3)1.2液压系统的组成 (5)1.3 液压系统方案拟定 (5)2执行元件的工况分析 (7)2.1 题目及原始参数 (7)2.3 执行元件的工况分析 (8)3执行元件主要参数的确定 (9)3.1初选执行元件的工作压力 (9)3.2计算液压缸主要参数的公式 (10)3.3计算液压缸的主要参数、工作压力、流量及功率 (11)4.双面组合铣床液压系统 (15)4.1主机功能结构 (15)4.2液压系统及其原理图 (17)5、液压元件的选择 (20)5.1 动力元件的选择 (21)5.2选择液压阀及油路中相关附件 (23)5.3冷却器的选择与安装 (24)6.液压辅件的选择 (26)6.1油箱的设计: (27)6.2阀块的设计: (28)6.3管件的选择: (29)6.4其他零件的选择: (31)6.5液压油的选用 (31)7.液压系统的安装、调试及使用与维护 (32)7.1 液压系统调度前的准备工作 (33)7.2 液压系统调度步骤 (33)7.3 液压系统的验收 (34)7.4液压设备的维护及检修 (34)结语 (36)致谢 (37)参考文献 (38)绪论本双面组合铣床是从德国引进的抬起运输通过式气缸体铣钻自动生产线中一台专用加工设备,用于某轿车汽油发动机气缸体上发动机气缸体上发动机安装结合面、汽油泵及机油过滤器结合面、发动机安装结合面等部位的铣削加工。
双头车床液压系统设计[1]
![双头车床液压系统设计[1]](https://img.taocdn.com/s3/m/b49685dae009581b6ad9eb07.png)
某厂要设计制造一台双头车床,加工压缩机拖车上一根长轴两端的轴颈。
由于零件较长,拟采用零件固定,刀具旋转和进给的加工方式。
其加工动作循环是快进(Fast Feed)一工进(Working Feed)—快退(Fast Return)—停止(Stop)。
同时要求各个车削头能单独调整。
其最大切削力在导轨中心线方向估计为12kN,所要移动的总重量估计为15kN,工作进给要求能在0.020~1.2m/min范围内进行无级调速,快速进、退速度一致,为 4 m/min,试设计该液压传动系统。
图10.1为该机床的外形示意图。
图10.1双头车床外形示意图10.2.1 确定对液压系统的工作要求Define the Work Requirement of the Hydraulic System根据加工要求,刀具旋转由机械传动来实现;主轴头沿导轨中心线方向的“快进(Fast Feed)一工进(Working Feed)—快退(Fast Return)—停止(Stop)”工作循环拟采用液压传动方式来实现。
故拟选定液压缸作执行机构。
考虑到车削进给系统传动功率不大,且要求低速稳定性好,粗加工时负载有较大变化,故拟选用调速阀、变量泵组成的容积节流调速方式。
为了自动实现上述工作循环,并保证零件一定的加工长度(该长度并无过高的精度要求),拟采用行程开关及电磁换向阀实现顺序动作。
10.2.2 拟定液压系统工作原理图Draw up the Work Schematic Circuit of Hydraulic System该系统同时驱动两个车削头,且动作循环完全相同。
为了保证快速进、退速度相等,并减小液压泵的流量规格,拟选用差动连接回路。
在行程控制中,由快进转工进时,采用机动滑阀。
使速度转换平稳,且工作安全可靠。
工进终了时。
压下电器行程开关返回。
快退到终点,压下电器行程开关,运动停止。
快进转工进后,因系统压力升高,遥控顺序阀打开,回油经背压阀回油箱,系统不再为差动连接。
双面钻孔组合机床液压系统设计毕业设计

双面钻孔组合机床液压系统设计毕业设计1 绪论1.1 组合机床的发展现状及前景组合机床(transfer and unit machine)是根据工件加工需要,以大量通用部件为基础,配以按工件特定形状和加工工艺设计的专用部件和夹具,组成的一种高效的半自动或自动专用机床[5]。
在我国,组合机床发展已有28年的历史,其科研和生产都具有相当的基础,应用也已深入到很多行业。
是当前机械制造业实现产品更新,进行技术改造,提高生产效率和高速发展必不可少的设备之一。
它的特征是高效、高质、经济实用,因而被广泛应用于工程机械、交通、能源、军工、轻工、家电等行业[8]。
我国传统的组合机床及组合机床自动线主要采用机、电、气、液压控制,它的加工对象主要是生产批量比较大的大中型箱体类和轴类零件(近年研制的组合机床加工连杆、板件等也占一定份额),完成钻孔、扩孔、铰孔,加工各种螺纹、镗孔、车端面和凸台,在孔内镗各种形状槽,以及铣削平面和成形面等[5]。
随着技术的不断进步,一种新型的组合机床——柔性组合机床越来越受到人们的青睐,它应用多位主轴箱、可换主轴箱、编码随行夹具和刀具的自动更换,配以可编程序控制器(PLC)、数字控制(NC)等,能任意改变工作循环控制和驱动系统,并能灵活适应多品种加工的可调可变的组合机床。
另外,近年来组合机床加工中心、数控组合机床、机床辅机(清洗机、装配机、综合测量机、试验机、输送线)等在组合机床行业中所占份额也越来越大。
由于组合机床及其自动线是一种技术综合性很高的高技术专用产品,是根据用户特殊要求而设计的,它涉及到加工工艺、刀具、测量、控制、诊断监控、清洗、装配和试漏等技术。
我国组合机床及组合机床自动线总体技术水平比发达国家要相对落后,国内所需的一些高水平组合机床及自动线几乎都从国外进口。
工艺装备的大量进口势必导致投资规模的扩大,并使产品生产成本提高。
因此,市场要求我们不断开发新技术、新工艺,研制新产品,由过去的“刚性”机床结构,向“柔性”化方向发展,满足用户需求,真正成为刚柔兼备的自动化装备[16]。
双头钻床的控制系统设计讲解
2013届毕业生毕业设计说明书题目: 双头钻床的控制系统设计学院名称:电气工程学院班级:自动F09042013 年5 月20 日目次1 概述 (1)1.1 课题研究背景及意义 (1)1.2 国内外发展现状 (2)1.3 设计任务及要求 (3)2 卧式双头钻床介绍 (4)2.1 送料装置和加紧装置 (4)2.2 动力头 (5)2.3 液压站 (5)2.4 机床辅助装置 (6)3 硬件电路设计 (6)3.1 卧式双头钻床的工艺流程 (6)3.2 主电路图 (7)3.3 卧式双头钻床各电动和液压系统油路的控制 (8)3.4 I/O分配及PLC选型 (12)3.5 硬件接线图 (13)4 系统软件设计 (14)4.1 卧式双头钻床的逻辑控制流程 (14)4.2 梯形图和指令表 (15)总结 (18)致谢 (19)参考文献 (20)1 概述可编程逻辑控制器,英文全称为Programmable Logical Controller ,通常被人们简称为PLC。
它是20世纪70年代以来以微处理器为核心,综合计算机技术、自动控制技术和通信技术发展起来的一种新型工业自动控制装置,它具有功能强、可靠性高、配置灵活、使用方便以及体积小、重量轻等优点。
基于以上优点以及PLC技术的不断发展,如今PLC已被广泛应用于自动化控制的各个领域。
钻床是机床的一种,是专门进行孔加工的机床。
追溯到上世纪七十年代初期,那时候世界上最先进的钻床依然还是用普通继电器来控制的。
但随着PLC技术的发展,人们逐渐将PLC应用于机床的控制当中。
相比之下,传统的继电器控制系统电气线路复杂,触点多,灵活性差,要想改变机床的加工工艺,就得改变硬件接线,长期使用后,故障率还高,故障排除困难,影响企业的正常生产。
因此普通继电器控制的机床越来越难以适应复杂多变的现代化生产过程。
而采用PLC 作为机床的控制器使得机床的效率和加工精度都得到了大大的提高,机床的性能也更趋完善,可靠性更高,功能更完善,故障率更低,故障排除更加容易,编程也简单。
钻、镗两用组合机床液压系统的设计(二)毕业设计
钻、镗两用组合机床液压系统的设计(二)毕业设计
2.液压系统组成
液压系统主要由以下组成部分构成:液压泵、液压缸、液压阀、压力表等。
在这些部
件中,液压泵是液压系统的重要原件,其主要作用是将机床所需的液体压力转换为动能,
供液压系统的其他部件使用。
液压缸是液压系统中的执行部件,其主要功能是根据系统的
压力变化,控制机床设备的运动、位置、速度等参数。
液压阀则是液压系统中的控制部件,其主要用途是根据操作员的指令,调节系统的压力、流量等参数,以控制液压缸的运动状态。
3.液压系统设计原则
设计一个合理稳定的液压系统,需要遵循以下原则:
(1)在设计过程中,需根据机床的工艺特点,合理选择液压泵、液压缸等液压装置的型号、规格。
(2)在进行设计时,需要对液压管路的长度、直径、弯曲处的变形程度等进行考虑,以确保系统的流通性与稳定性。
(3)需要根据液压系统的工作压力与流量,确定合适的液压阀的类型、规格、数量。
(4)在液压系统设计后,需要进行系统试验,以检验其稳定性、运行正常性、各部件的适用性等。
5.结论
本文通过对钻、镗两用组合机床液压系统的设计研究,得出了一系列液压系统方案和
设计原则。
在液压系统方案选择过程中,应结合机床的工艺特点、液压泵的选型、液压管
路的布置、液压阀的安装、液压油的使用等因素,并严格遵循相关液压系统设计标准,以
确保长期稳定、可靠的机床工作状态。
液压系统设计毕业设计
液压系统设计毕业设计1. 引言液压系统是一种通过液体传递力量和控制信号的技术,广泛应用于各个领域,包括机械工程、航空航天工程、能源工程等。
本文旨在设计一个满足特定需求的液压系统,以应用于某工程项目的毕业设计。
本文将详细介绍液压系统的设计过程和原理,包括工作原理、组成部分、性能指标和系统布局等方面。
2. 工作原理液压系统的工作原理基于两个基本定律:压力定律和帕斯卡定律。
液压系统通过液体在封闭系统中传递力量和信号。
当液体被加压时,会产生静压力,这个压力会被传递到液体中的每一个部分。
液压系统主要由以下几个组件组成:•液压泵:将电动机或发动机的动力转化为液压能量,提供液压流体的流动。
•液压缸或液压马达:通过液压系统的力量来完成工作。
•油箱:存储液压油,保持液压系统的温度和压力稳定。
•阀门:控制液体的流动,包括方向阀、流量控制阀和压力控制阀等。
•导管和连接件:连接液压系统的各个部件,传递液体。
3. 性能指标设计液压系统时,需要考虑以下性能指标:•动力输出:液压系统需要能够提供足够的动力来执行所需的工作任务。
•响应时间:液压系统的响应时间应该尽可能短,以确保工作的准确性和效率。
•系统效率:液压系统的效率应高,以减少能量损失和热量产生。
•系统可靠性:液压系统需要具备一定的可靠性,以确保长时间运行的稳定性。
•安全性:液压系统在设计上需要满足工作环境的安全要求,以防止意外事故的发生。
4. 系统布局设计在设计液压系统的布局时,需要考虑以下因素:•功能需求:根据所需的工作任务确定液压系统的功能需求,包括液压泵的选型、液压缸的布置等。
•空间约束:根据工作场地的限制,确定液压系统的尺寸和布局。
•连接方式:选择合适的连接方式和连接件,确保液压系统的连接可靠性。
•管道布置:设计合理的管道布置,避免过长或过短的管道对系统性能产生影响。
•安全设备:根据安全要求,选择合适的安全设备,如压力开关、液压阀等。
5. 结论通过本文的液压系统设计,我们能够满足特定需求的液压系统的毕业设计要求。
双面钻通卧式组合机床液压系统设计毕业设计
沈阳理工大学毕业设计(论文)题目:双面钻通卧式组合机床液压系统设计学院:机械与运载学院专业班级: 11焊接1班学生姓名:张顺指导教师:王强完成日期: 2013年7月12日毕业设计(论文)任务书毕业设计(论文)题目:双面钻通卧式组合机床液压系统设计。
主要内容:1.液压系统工况图分析。
2.液压系统原理图。
3.液压系统计算与选液压元件。
4.验算液压系统。
5.绘工作图和遍技术文件。
主要技术参数:工作循环:工件夹紧→左、右动力部件快进→左、右动力部件工进→左动力部件快退,右动力部件继续工进→左动力部件停止,右动力部件快退→左右动力部件皆停止,工件松开。
工件夹紧力为30000牛,两侧加工切削负载皆为15000牛,动力部件的重量皆为9.8×103牛,快进、快退速度为6m/min,快进行程为100mm。
工进速度为(20—1000)mm/min,左动力部件工进行程为50mm,右动力部件工进行程为80mm。
往复运动的加速、减速时间为0.2s,滑台为平导轨,静、动摩擦系数分别为0.2和0.1。
指导教师:院长签字:年月日双面钻通卧式组合机床液压系统设计论文作者:张顺指导教师:王强目录摘要 (2)外文摘要 (3)引言 (5)⒈液压系统的设计与计算 (6)1.1负载分析 (6)1.2件主要参数的确定 (8)1.3系统原理图 (9)1.4压元件 (14)1.5验算液压系统的性能 (18)⒉集成块的设计 (22)2.1底座设计 (22)2.2下块设计 (22)2.3上块设计 (22)2.4油孔直径的确定 (22)2.5油孔间最小间隙的确定 (23)结论 (24)致谢 (25)参考文献 (26)摘要对于设计双面钻通卧式组合机床的液压系统来说,基本任务是使该系统能够高效、稳定、快捷的完成孔加工问题。
我主要设了适合本机床工作循环和性能的液压系统,合理选用液压阀并设计安装了管接头的集成块。
首先对负载进行分析,确定执行元件(液压缸)的主要技术参数,再算出液压缸各工作阶段的工作压力、流量和功率。
- 1、下载文档前请自行甄别文档内容的完整性,平台不提供额外的编辑、内容补充、找答案等附加服务。
- 2、"仅部分预览"的文档,不可在线预览部分如存在完整性等问题,可反馈申请退款(可完整预览的文档不适用该条件!)。
- 3、如文档侵犯您的权益,请联系客服反馈,我们会尽快为您处理(人工客服工作时间:9:00-18:30)。
目录一、设计任务 (2)1、课程设计题目 (2)2、课程设计任务................................................................................... 错误!未定义书签。
二、液压回路工况分析 (4)1、导程摩擦阻力 (4)2、惯性力 (4)3、工作负载 (5)4、液压缸密封摩擦阻力 (5)三、液压系统主要参数计算 (8)1、预选系统设计压力 (8)2、计算液压缸主要结构尺寸 (8)3、单个液压缸需求的最大流量 (10)4、其他工作阶段的压力、流量和功率 (10)四、制定方案,拟定液压系统图 (11)1、制定液压回路方案 (11)2、合成液压系统图 (12)3、选择液压系统的元件和辅件 (14)(1)液压泵的选择 (14)(2)控制元件的选择 (15)五、液压缸设计1、液压缸结构的拟定 (18)2、液压缸主要几何尺寸的计算 (19)3、液压缸的结构图 (20)六、设计总结 (22)七、参考文献一、设计任务1、课程设计题目某厂欲自行设计制造一台专用车床,用于压缩机连杆两端长轴颈的车削加工。
根据加工工件尺寸较长的特点,拟采用的加工工艺方案为:工件固定,刀具旋转并进给。
车床主要由床身[布有相互平行的V形导轨和平导轨各一条(见图1-1)]和左右两个车削动力头组成,其总体布局如图2-2所示。
工件装夹于床身中部。
两个独立的动力头,通过机械传动带动主轴及刀具旋转实现车床的主运动;进给运动要求采用液压缸实现,即在床身上安装两个液压缸,使其活塞杆与各动力头下部相连,通过液压缸往复运动驱动动力头实现车床的进给运动。
车床加工工件时,车削动力头的进给工作循环为:快进→工进→快退→停止。
已知:移动部件重约是G=15kN;各车削动力头的最大切削进给抗力(轴向力)估值为Fe=10kN;主切削力(切向力)Fz=35kN。
要求动力头的快速进、退速度相等,V1=Vmax=3m/min;错误!未找到引用源。
工进速度无级调整范围为V2=错误!未找到引用源。
.02~1m/min.导轨的静、动摩擦因数分别为错误!未找到引用源。
s=0.2;错误!未找到引用源。
d=0.1。
(2)配置执行元件根据车床的总体布局及技术要求,选择缸筒固定的单杆活塞缸作为驱动车削动力头实现进给运动的液压执行元件。
(3)工况分析由于动力头的快速进退及工作进给阶段的速度已给定,不必进行运动分析。
故仅对液压缸作动力分析,即通过分析计算,确定液压缸总的最大外负载。
液压缸的受力简图如图1-2所示。
图1-1 车床总体布局示意图1,8一车削动力头;2,7一主轴;3,6一连杆轴颈;4一夹具;5一工件(连杆);9一导轨;10一床身题目要求:1.驱动装置:双作用单出杆活塞缸,头部用间隙式缓冲,尾部用可调缓冲。
2.安装方式:缸前,后盖采用法兰连接,用切向支座与机架固定,活塞杆移动。
3.控制方式:用行程阀快进与工进速度的换接。
设计要求:1.进行工况分析与计算,绘制工况图(包括速度图与负载图)。
2.拟定液压系统原理图,选择标准液压元件,绘制电磁铁动作循环表。
3.进行液压缸设计计算,图纸绘制。
上交材料:1.设计说明书一份。
2.液压系统原理图一张。
3.液压缸装配图及部分零件图一套。
二、液压回路工况分析1、导程摩擦阻力车床工进阶段的导轨受力见图2-2,取摩擦因数fd=1,可算得动摩擦阻力Ffd 1为NG G fF fF F dZdZfd 6036290sin 1.02)3515(1.02)3515(2sin221010331=︒⨯⨯++⨯⨯+=⨯+++=α图2-1 车床导轨受力分析简图车床空载快速进退阶段启动时,导轨受静摩擦阻力Ffs作用,区静摩擦因数fs=0.2,算得N G G f fF s s fs 362145sin 2.02152.02152sin 22101033=︒⨯⨯+⨯⨯=⨯+=α 加速阶段和恒速阶段的动摩擦阻力为N G G dd fd F 181145sin 1.02151.02152sin221010332=︒⨯⨯+⨯⨯=⨯+=αμμ2、惯性力取速度变化量0.02m/s m/min 2.1==∆ν,启动时间s 2.0t =∆。
算得故惯性力N G F 1532.002.081.915t g 103i =⨯⨯=∆∆⨯=ν3、工作负载液压缸拖动车削动力头进给时的工作负载为切削抗力Fe,已知kN 10e=F。
4、液压缸密封摩擦阻力作用于液压缸活塞上密封阻力Fm,用下式估算F Fe cmm1)(η-=式中ηcm-液压缸机械效率,95.0~90.0=ηcm。
取90.0=ηcm,算得启动时得静密封摩擦阻力N F F 10001090.011103e cmm =⨯⨯-=-=)()(η 恒速时的动密封摩擦阻力估取为静密封摩擦阻力的30%,即F Fms md%30=,即N F Fms md300%30==。
将上述计算过程综合后得到的各工作阶段的液压缸外负载结果列于表2-1和2-2,液压缸的负载循环图、速度循环图见图2。
表2-2 车削动力头液压缸外负载计算结果图2 液压缸的负载循环图、速度循环图由表2-1和表2-2可以看出,最大负载出现在工进阶段 ,其最大值为N F16336max=.三、液压系统主要参数计算1、预选系统设计压力本车床属于半精加工机床,负载最大时为慢速工进阶段,其他工况时载荷都不大,参考表3-1预选液压缸的设计压力MPap 31=。
2、计算液压缸主要结构尺寸为了满足动力头快速进退速度相等的要求并减小液压泵的流量,将缸的无杆腔作为主公作腔,并在快进时差动连接,则液压缸无杆腔与有杆腔的有效面积A 1与A2应满足A A 221=,即活塞杆直径d 和液压缸内径D 间应满足d=0.71D 。
为了提高动力头的工作平稳性,给液压缸设置一定回油背压。
表3-2 液压执行元件的背压力参考表表3-2,暂取背压0.3MPa ,上已取液压缸机械效率9.0=ηcm,则可算得液压缸无杆腔的有效面积m p P FA cm24616336)(1069.6310)23.03(9.02211-==-=⨯⨯-⨯η从而得液压缸内径mm m A D91091.01069.634441=⨯⨯=-==ππ按GB/T 2348-1993,将液压缸内径圆整为cm mm D10100==。
因A A 221=,故活塞杆直径为mm D d 7110071.071.0=⨯==按GB/T 2348-1993,将活塞杆直径圆整为cm mm d770==.则液压缸有效实际面积为cm DA 5.7810222144=⨯==ππcm d D A 04.40710222222)(4)(4=-=-=ππcm A A A46.38221=-=由于动力头的最低工进速度很低,故需按νminmin 1qA ≥(式3-1)对缸的结构尺寸进行检验:将调速阀的最小稳定流量min /m 50qminL =和活塞最小进给速度m in /2m in /02.0mincm m ==ν代入式3-1,算得cm q252minmin 250==ν结果表明活塞面积可满足最低稳定速度的要求。
差动连接快进时,液压缸有杆腔压力p2必须大于无杆腔压力p1,其差值估取MPa pp p5.012=-=∆,并注意到启动瞬间液压缸尚未移动,此时0=∆p ;另外,取快退时的回油压力损失为0.6MPa 。
从而算得液压缸在工进阶段的实际工作压力MPa Pa AAp Fpcm47.247.25.7804.403.090.0163361010101064461221=⨯=⨯⨯⨯⨯+=+=--η 它正是系统工作循环中的最高压力。
3、单个液压缸需求的最大流量液压缸最大流量发生在快退阶段,算得单个液压缸的最大流量q 1为min /012.1212012304.40min/1032max 2max1L cmA q==⨯⨯==ν4、其他工作阶段的压力、流量和功率其他由下表可见,快退阶段工作时,输入功率最大,其值为W P594max1=.四、制定方案,拟定液压系统图1、制定液压回路方案a.调速方式与油源方案。
考虑到切削进给传动功率不是很大,低速时稳定性要求较高;加工期间负载变化较大,故采用限压式变量阀供油和调速阀联合的容积节流调速方案,且快进时液压缸差动链接,以满足系统高压小流量和低压大流量的工况特点,从而提高系统效率,实现节能,调速阀设置在进油路上,通过调节通流面积实现液压缸及其拖动的车削动力头的车削进给调速度大小;通过分别调整两个调速阀可使两个车削动力头获得较高同步精度。
b.方向控制方案。
由于系统流量不是太大,故选用三位五通“O”形中位机能的电磁换向阀作主换向阀;本机床加工的轴颈长度尺寸无特殊精度要求,故采用行程控制即活动挡块压下电器行程开关,控制换向阀电磁铁的通断电来实现自动换向和速度换接。
通过两个电磁铁换向阀的通断组合,可实现两个车削动力头的独立调节。
在调整一个时,另一个应停止。
c.速度换接方案。
快进和和工进的速度换接由二位二通行程阀和远控顺序阀实现,以简化油路,提高换接精度。
工进时进右路和回油路的隔离采用单向阀实现。
d.背压与安全保护。
为了提高液压缸及其驱动的车削动力头的运动平稳性,在液压缸工进时的回油路上设置一溢流阀,以使液压缸在一定的背压下运行。
为了保证整个系统的安全,在泵出口并联一溢流阀,用于防止过载。
e.辅助回路方案。
在液压泵入口设置吸油过滤器,以保证油液的清洁度;在液压泵出口设置压力表及多点压力表开关以便于个压力阀调压时的压力观测。
2、合成液压系统图将上述各液压回路方案进行综合即可组成专用车床的液压系统原理图,图中附表是电磁铁及行程阀的状态表。
以左侧动力头及液压缸21为例说明其工作原理。
a.快进按下启动按钮,电磁铁1Y A通电使换向阀13切换至左位。
由于快进时负荷较小,系统压力不高,故顺序阀9关闭,变量泵2输出最大流量。
此时,液压缸21为差动连接,动力头快进。
西戎的油液流动路线如下。
进油路:变量泵2→换向阀13(左位)→行程阀19(下位)→液压缸21无杆腔。
回油路:液压缸21有杆腔→换向阀13(左位)→单向阀11→行程阀19(下位)→液压缸21无杆腔。
b.工进当动力头快速前进到预定位置时,动力头侧面的活动挡块压下行程阀19,动力头开始车削工件。
此时系统压力升高,在顺序阀9打开的同时,限压式变量泵2自动减小其输出流量,以便与调速阀17的开口相适应。
系统中油液流动路线如下。
进油路:变量泵2→换向阀13(左位)→调速阀17→液压缸21无杆腔。
回油路:液压缸21有杆腔→换向阀13(右位)→顺序阀9→溢流阀(背压阀)→油箱。
c.快退在动力头工作进给到预定位置触动行程开关SQ1时,给出动力头快退信号,电磁铁1YA断电,2YA通电,换向阀13切换至右位,此时系统压力下降;变量泵2的流量又自动增大,动力头实现快退。