涂装前处理说明及作用介绍
第一部分:涂装前处理的目的和必要性 前处理膜

涂装前处理产品的一般理论第一部分:涂装前处理的目的和必要性前处理膜的作用和功能要求涂装前处理的目的,是为了有效地解决涂层和基材的结合力和耐候性问题。
因此涂装前处理对有复杂的防锈防腐目标的涂装项目特别必要和重要。
无论磷化液或我司704系列产品,都只作为前处理液发挥其功能。
前处理液的主要功能如下:A.生成的前处理膜,本身与基材必须具备很好的结合力和耐侯性。
可避免除油除锈后的带水工件,在干燥过程中生成浮锈,以保证涂层的结合力和耐侯性。
B.前处理膜同时还需具备增强涂层的结合力和耐侯性的功能。
我司膜层因还能与涂层表面发生螯合交联反应,其增强特性大大优于磷化膜。
C.前处理膜的耐酸碱腐蚀性强弱,不是最主要的考察内容。
因为涂装工艺的耐酸碱腐蚀性能力,主要是由耐酸碱腐蚀性极强的有机树脂来完成。
前处理的主要检测指标如下:A.盐雾实验和点滴实验:目的是检测膜层抗纵向腐蚀的能力。
因为该指标对确定前处理膜层的防腐能力非常重要,因此被广泛地使用。
B.划格法或划叉法的盐雾实验和硫酸铜点滴实验:目的是检测前处理膜层抗横向腐蚀的能力。
因为该指标对涂层结合力和耐久性非常重要,因此被广泛地使用。
无论是作为前处理膜层,还是与涂层同时被检验,我司产品均大大好于磷化。
涂装前最基本要求通常是:被涂装的表面必需是干燥和干净的。
因此,要求前处理膜层必须具有相当的防锈性能,以适应涂装前的干燥和转序工艺。
现有的最普及的解决“被涂装表面干燥和干净”的前处理方法是磷化,即通过磷化形成一层磷化膜,经干燥后,在磷化膜上做涂装。
磷化是形成磷化膜的过程,磷化过程使用的产品叫磷化液。
磷化液是酸性的,因此磷化过程就难免有很多的缺陷,如:产生大量的沉渣、气体、酸雾等,生产环境恶劣。
我司涂装前处理液704系列是中性的,处理过程无沉渣、气体、酸雾产生,无毒、安全、环保;通过SGS国际环保认证,符合欧盟RoHS指令;使用简单,和原有磷化工艺基本一致,不需要增加任何设备;还可用于铸铁涂装前处理。
涂装前处理说明及作用介绍

涂装前处理说明及作用介绍
一、涂装前表面处理(前处理或预处理)
各类材料或制品(或工件),在涂装前对其清除各类污物、整平及覆盖某类化学转化膜的任何准备工作,统称为涂装前表面处理,简称前处理(预处理)。
涂装前处理主要包括除油(脱脂)、除锈、表面调整、磷化(钢铁件)、氧化(铝制件)、和钝化封闭。
二.前处理的作用
1.提高涂层对材料表面的附着力
材料表面有油脂、污垢、锈蚀产物、氧化皮及旧涂膜时,直接涂装会造成涂膜对基材的附着力很弱,涂膜易整片剥落或产生各种外观缺陷。
有时将各类污垢和锈蚀产物清理干净以后,涂膜附着力仍不理想。
要想进一步提高涂膜附着力,则可采取打磨粗化,化学转化膜(化学覆膜),偶联剂处理等。
2.提高涂层对金属基体的腐蚀防护保护能力
钢铁生锈以后,锈蚀产物中含有很不稳定的铁酸(α-FeOOH),它在涂层下仍会锈蚀扩展和蔓延,使涂层迅速被破坏而丧失保护功能(比如公司员工宿舍铁门)。
如果将其进行除锈处理,把铁锈除尽以后再涂装,则涂层防护性就大大提高了。
如果在洁净的钢铁表面,经磷化处理,形成磷酸锌盐化学转化膜,则涂层防护性就大幅度提高了。
3.提高基体表面平整度
一般材料表面粗糙度(以前称光洁度)达到4~6级。
但大于6级,表面
过分光滑则对附着力不利,反而又需打磨粗化。
与材料平整度相关的一项涂层重要性能指针是鲜映性(即涂膜成像清晰度——象高级轿车)。
汽车涂装前的表面处理技术

中间涂层的材料选择
环氧树脂
环氧树脂具有优良的耐腐蚀性能和附着力, 广泛用于汽车中间涂层。
丙烯酸树脂
丙烯酸树脂具有较好的耐候性和保色性,适 用于室外环境的汽车涂装。
聚氨酯
聚氨酯涂层具有良好的耐磨性和柔韧性,适 用于需要较高弹性的场合。
氨基树脂
氨基树脂具有较高的硬度和光泽度,适用于 需要高硬度的场合。
中间涂层的涂装工艺
前处理
涂装前需要对底材进行彻底清洁,去 除油污、锈迹和杂质。
涂布
采用涂布机或手工涂布的方式将中间 涂层涂装于底材表面。
固化
在一定的温度和湿度下进行固化,使 涂层与底材紧密结合。
检验与修整
对涂装好的中间涂层进行质量检验, 对缺陷进行修整。
04
面层涂装
面层涂装的作用
保护作用
美化外观
汽车涂装前的表面处理技术
目录
• 表面预处理 • 电泳涂装 • 中间涂层涂装 • 面层涂装 • 涂装后处理
01
表面预处理
清除杂质
去除油污
清除尘埃
使用清洗剂清除汽车表面油污,如机 油、润滑油等,以确保涂装质量。
用干净的布擦拭汽车表面,去除尘埃 和污垢,保证涂装表面的清洁度。
去除锈迹
对于生锈的部位,需进行除锈处理, 可以采用砂纸打磨或化学除锈剂。
。
涂料粒子带电
在电泳涂装过程中,涂料粒子通 过电解作用获得电荷,从而在电
场中移动。
涂膜形成
带电的涂料粒子在工件表面沉积 并形成涂膜,通过控制电泳参数 和涂装环境,可获得均匀、致密
的涂膜。
电泳涂装设备
电泳槽
用于容纳涂料和工件的 设备,一般由不锈钢或
聚乙烯制成。
涂装技术第三章前处理
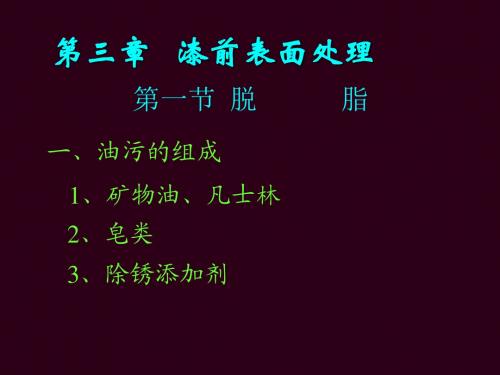
3、脱脂方法
4、工序间的配合
6
六、质量评价
1、水浸润法 2、观察磷化膜法 3、除油率法 七、常见问题及解决方法 1、脱脂效果不佳
7
(1)脱脂剂选择不当 (2)脱脂时间太短 (3)脱脂剂浓度偏低 (4)脱脂温度偏低 (5)喷射压力低 (6)喷嘴堵塞,流量不足 (7)浸渍脱脂的机械作用力小 (8)工作液中含油量太高 (9)脱脂后水洗不彻底
17
第三节 涂装前磷化处理
一、磷化的定义 磷化处理是指金属表面与含磷酸二氢盐的酸性溶液接 触,发生化学反应而在金属表面生成稳定的不溶性无 机化合物膜层的一种表面化学处理方法,所生成的膜 称为磷化膜。 二、磷化的作用 1、在彻底脱脂的基础上,提供清洁、均匀、无油脂的表面。 2、增强了有机涂膜对基材的附着力。 3、提供了稳定的不导电的隔离层,具有抑制腐蚀的作用。
使用脱漆剂的注意事项:
3、几种脱漆剂配方
16
二氯甲烷 24% 丙酮 46% 三氯醋酸10% 磷甲酚12% 水8%
丙酮9.6% 石蜡1.2% 乙醇4.8% 乙二醇缩甲醛52.5%甲苯28.4%硝棉3.5%
丙酮10%
乙醇10%
乙二醇缩甲醛50%
硝棉30%
丙酮10%
石蜡4%
乙醇20%
甲苯65.5%
水0.5%
三、磷化的分类 1、根据磷化液分类:磷酸锌系、磷酸锰系、磷酸铁系 2、根据磷化温度分类:高温磷化(80℃以上 )、 中温磷化(50~70 ℃)、低温磷化(40 ℃以下) 3、根据磷化施工方法:喷淋式、浸渍式、喷浸结合、涂刷式 4、根据磷化膜质量:重量型(7.5g/m2以上)、 中量型(4.3~7.5g/m2)、轻量型(1.1~4.3g/m2)、 特轻量型(0.3~1.1g/m2)
涂装前处理

前言我们所讲的前处理是漆前的表面处理,是指工件在涂底漆钱,对工件表面进行的处理,如除油、除锈、钝化、磷化等工艺。
目的是使经过处理的工件表面,变得更易漆膜附着,减少漆膜下的腐蚀,达到腐蚀效果。
漆前表面处理包括三个方面:清除表面的各种污物,以保证涂层具有良好的防腐蚀性能以及涂层涂层与被涂物表面有良好的附着能力。
污垢分为无机污垢和有机污垢两大类,金属的腐蚀产物(铁锈与氧化皮)、焊渣、姓啥碱斑、灰尘以及水垢等属于无机污垢,这些污垢的存在不仅影响涂层的附着力、外观、涂层耐潮湿性及耐腐蚀性,而且锈蚀会在漆膜下蔓延。
各种油污及旧漆膜则属于有机污垢。
当被涂物存在各种油污未洗净就涂装,则将对漆膜与被涂物的结合力产生有害影响,严重时漆膜成片脱落,因此在涂装前要清除掉背涂物表面的各种污物。
对清洗过的被涂物表面进行各种化学处理,以提高漆膜前的附着力和耐腐蚀性。
如对钢铁件进行磷化处理,对铝制件进行氧化处理,对塑料制件进行化学处理以提高塑料制件与漆膜的结合力,等等。
采用机械方法消除被涂物机械加工缺陷和创造漆膜所需的表面粗糙度(光洁度),被涂物表面光洁度一般要求4-6级,低于4级时所得漆膜表面粗糙无光,如果光洁度高于6级,则太光滑,将影响涂层附着力,需要用砂纸打磨来增大粗糙度,提高附着力。
第一节金属的除油工件在制造过程中,由于机械加工和防锈的需要,要经常接触各种润滑油、拉延油、防锈油以及磨光剂、抛光剂等,在搬运过程中也常然上油污。
因此油污是是被涂金属工件进入涂装车间最常见的污垢。
在涂装前洗净被涂物上得油污的工序叫除油又称脱脂。
最常见的除油方法有碱液清洗,表面活性剂清洗,乳化液清洗,有机溶剂清洗等,清洗的原理是借助清洗剂的物理和化学作用力去除油污。
一、油脂的来源及种类:1、油脂的分类:根据他们与碱反应的特性可分为两类:可与碱反应生成肥皂的皂化油如动植物油,和不能和碱反应生成肥皂的非皂化油如凡士林、润滑油、石蜡等矿物油。
2、油脂的来源主要是金属在加工(润滑油、润滑脂、拉延油、切削油、乳化液、抛光剂磨光剂等)贮运(悬链的润滑剂级沥青等)过程中,由于防锈的需要带来的油污。
涂装前处理、电泳培训教材

3、电泳工艺参数 电泳液成分参数 电泳条件
漕液特性参数 电泳特性参数
固体分含量18-23%,颜基比1016%,溶剂含量0.5-1.0%
电泳液温度((28±2)℃)、泳涂时间 (2~3min)、泳涂为变电压工作模 式:一段电压100-140V; 二段电 压:200-280V
pH值5.7~6.1,电导率10001800μs/cm
由于浸渍处理方式具有高的生产效率和高的磷化处理 质量,因此在汽车车身磷化处理工艺中应用最为广泛.
2、磷化控制的工艺参数
总酸度
总酸度偏低,不能充分生成磷化膜;总酸度过高,沉渣发生量 增多,附着在磷化膜面上形成磷化缺陷。
游离酸度
游离酸度过高不能成膜,易出现黄锈;游离酸度 过低,磷化 液的稳定性差,易生成额外的沉渣。
4、磷化除渣装置
伴随着磷化膜的生成,磷化沉渣也产生,这是不可避的.磷化渣在溶液中含量过高
,就会附着在工件上,影响涂膜的性能.同时,沉渣被带入电泳槽,会破坏槽液的稳定性,
特别对超滤器使用寿命影响很大.所以要对磷化液进行除渣处理.
在汽车生产线上一般采用全浸式磷化处理,其槽容量较大.
因此大部分采用连续沉降方式.全浸式磷化槽底部一般设
器,有单袋、双袋、四袋、六袋等形式
除油装置
脱脂过程中,工件表面油脂被脱脂处理后进入 脱脂槽中,在一定工作温度
下,部分油分从脱脂液中分离后浮在脱脂液表面上.容易造成工件清洗后
的二次污染,而且这些油分在脱脂槽中的浓度大约超过5g/L时,脱脂液的
性能和寿 命受到很大影响.
油水分离装置有离心分离式、加热油水分离式、吸附分离式、电化学
电导率:是控制电泳漆膜层质量的关键指标之一.电导率过高,成膜速度快, 膜厚且易产生桔皮和表面粗糙等现象.电导率较高时,可采用较低的电压和温 度;反之则要相应提高电压和温度.
金属表面涂装前处理的应用
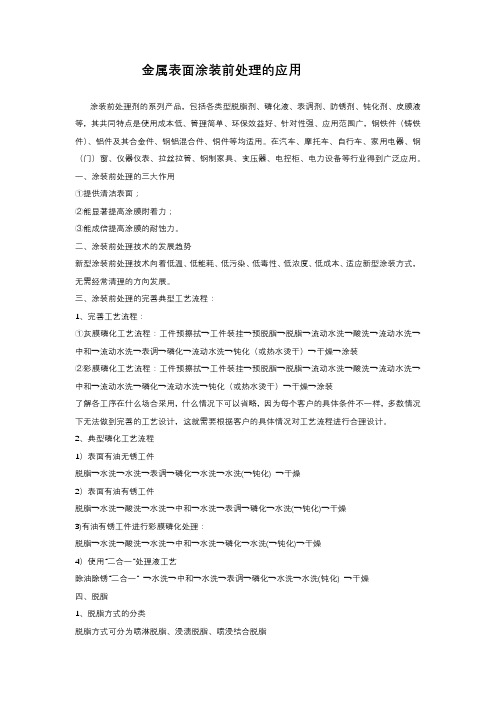
金属表面涂装前处理的应用涂装前处理剂的系列产品,包括各类型脱脂剂、磷化液、表调剂、防锈剂、钝化剂、皮膜液等,其共同特点是使用成本低、管理简单、环保效益好、针对性强、应用范围广,钢铁件(铸铁件)、铝件及其合金件、钢铝混合件、铜件等均适用。
在汽车、摩托车、自行车、家用电器、钢(门)窗、仪器仪表、拉丝拉管、钢制家具、变压器、电控柜、电力设备等行业得到广泛应用。
一、涂装前处理的三大作用①提供清洁表面;②能显著提高涂膜附着力;③能成倍提高涂膜的耐蚀力。
二、涂装前处理技术的发展趋势新型涂装前处理技术向着低温、低能耗、低污染、低毒性、低浓度、低成本、适应新型涂装方式,无需经常清理的方向发展。
三、涂装前处理的完善典型工艺流程:1、完善工艺流程:①灰膜磷化工艺流程:工件预擦拭→工件装挂→预脱脂→脱脂→流动水洗→酸洗→流动水洗→中和→流动水洗→表调→磷化→流动水洗→钝化(或热水烫干)→干燥→涂装②彩膜磷化工艺流程:工件预擦拭→工件装挂→预脱脂→脱脂→流动水洗→酸洗→流动水洗→中和→流动水洗→磷化→流动水洗→钝化(或热水烫干)→干燥→涂装了解各工序在什么场合采用,什么情况下可以省略,因为每个客户的具体条件不一样,多数情况下无法做到完善的工艺设计,这就需要根据客户的具体情况对工艺流程进行合理设计。
2、典型磷化工艺流程1)表面有油无锈工件脱脂→水洗→水洗→表调→磷化→水洗→水洗(→钝化) →干燥2)表面有油有锈工件脱脂→水洗→酸洗→水洗→中和→水洗→表调→磷化→水洗(→钝化)→干燥3)有油有锈工件进行彩膜磷化处理:脱脂→水洗→酸洗→水洗→中和→水洗→磷化→水洗(→钝化)→干燥4)使用“二合一”处理液工艺除油除锈“二合一”→水洗→中和→水洗→表调→磷化→水洗→水洗(钝化) →干燥四、脱脂1、脱脂方式的分类脱脂方式可分为喷淋脱脂、浸渍脱脂、喷浸结合脱脂1) 喷淋脱脂的特点、适用范围喷淋脱脂:将脱脂剂直接喷射到工件表面进行脱脂。
涂装前处理基本知识

3、除锈 作用:除去工件表面的锈蚀以及氧化皮。 除锈的方法 1)喷砂、抛丸除锈,一般适用于车架等承重件; 2)手工除锈:用砂布、铲刀等,适合小面积除锈; 3)酸洗除锈:如硫酸、盐酸、磷酸等进行除锈,这种 方式比较常见。
4
常用的酸 1)硫酸:成本低、挥发少、效果好,当浓度下降时,可升高温度来 保持除锈能力,但温度过高时回会产生氢脆和过蚀;一般浓度为 10-15%的水溶液、T=50-60℃、t=5-10min。 2)盐酸:常温,t=10-20 min,浓度为10-15%的水溶液,Fe含量< 120g/L。但由于盐酸挥发快,产生大量的酸雾,影响生产环境及 破坏设备,故很少单独使用。 3)磷酸:不产生过腐蚀和氢脆,可以得到一层有一定防锈能力的膜。 但成本较高,严重的锈蚀不易除去,溶解Fe的能力差,当Fe3+> 10g/L时,会产生大量的FeSO4沉淀,而影响除锈效果,需提高浓 度来解决;一般浓度为15-20%、T=40-60℃、t=5-10min,[Fe2+] < 50g/L。另外对磷化有一定的坏影响。 备注:都要使用酸用缓蚀剂,避免底材过度腐蚀。
8
常见的磷化膜电镜图
Zn/Ni/Mn三元系磷化 Zn系磷化 Fe系磷化
汽车行业普遍采用三元 体系的磷化,该类型磷 化膜耐碱性好 9
6、电泳涂装对前处理的要求 工件表面无油、无锈; 磷化膜均匀、细致,不发花、不挂灰、不发黄等; 磷化膜沉积量2-3g/m2,膜厚1-4µ m; 电泳失重:阳极电泳漆≤10%、阴极电泳漆≤ 8%; 工件、挂具的滴水电导小于50µ s/cm,同时PH值为中性, 一般控制在6-7.5。
1
2、除油 作用:清洗掉在粘附在工件表面的各种类型油污。 除油的方法 1)溶剂除油:用有机溶剂,如汽油、甲苯、二甲苯、三氯乙 烷 等,其特点是除油效率高,尤其对粘度高、滴落点高的油脂有 很好的效果。但由于劳动条件差、毒性大、防火要求高。 2)超声波除油:利用超声波发出的微波,通过震荡,将油污 从 底材表面上剥离。 3)电解除油:通过电解时产生的气体,将油污从底材表面上剥 离出来。 4)脱脂剂除油:利用含有表面活性剂的碱性物质对油污进行 浸 润、分散、乳化、增溶、溶解等作用达到去油的目的。目前此 方法最常用。
- 1、下载文档前请自行甄别文档内容的完整性,平台不提供额外的编辑、内容补充、找答案等附加服务。
- 2、"仅部分预览"的文档,不可在线预览部分如存在完整性等问题,可反馈申请退款(可完整预览的文档不适用该条件!)。
- 3、如文档侵犯您的权益,请联系客服反馈,我们会尽快为您处理(人工客服工作时间:9:00-18:30)。
涂装前处理说明及作用介绍
涂装前处理是指在进行涂装工艺之前,对待涂物表面进行清洁、除锈、打磨等一系列处理工作的过程。
涂装前处理的目的是为了提高涂装质量和
涂层附着力,延长涂层的使用寿命,并提高涂装效率。
下面将详细介绍涂
装前处理的各个环节及其作用。
一、表面清洁
表面清洁是涂装前处理的第一步,其目的是去除表面的污垢、油脂和
其它附着物,保证涂层与基材之间的良好附着。
常用的表面清洗方法包括
溶剂清洗、水洗、喷砂清洗等。
溶剂清洗适用于金属表面,可采用酸洗、
碱洗、除油剂清洗等方法。
水洗适用于非金属表面,可采用清水冲洗、高
压水洗等方法。
喷砂清洗适用于表面有较重锈蚀的金属表面,可将表面的
锈蚀物、附着物彻底去除。
二、除锈处理
除锈处理是针对金属表面的处理工艺,其目的是去除金属表面的氧化
层和锈蚀物,保证涂层与基材之间的牢固结合。
除锈方法有机械除锈、化
学除锈、电化学除锈等。
机械除锈是利用机械设备如喷砂机、打磨机等将
金属表面的氧化层、锈蚀物等物理地去除。
化学除锈是利用化学药剂将金
属表面的氧化层、锈蚀物等化学地溶解除去。
电化学除锈是利用电化学原
理将金属表面的氧化层、锈蚀物等通过电解溶解除去。
三、打磨处理
打磨处理是为了提供一个光滑平整的表面,以便于涂装时涂层的均匀
附着。
常用的打磨方法有手工打磨、机械打磨等。
手工打磨适用于小面积
的表面处理,可以通过砂纸、砂轮等工具进行打磨。
机械打磨适用于大面
积的表面处理,可以通过砂带机、砂轮机等设备进行打磨。
四、除尘处理
除尘处理是为了保证涂装时的脏物不附着在涂层表面,影响涂层的外
观和质量。
除尘方法包括吹风除尘、物理拍打除尘、吸尘除尘等。
吹风除
尘是通过高压气流将表面的灰尘、杂质吹掉。
物理拍打除尘是通过物理手
段将表面的灰尘、杂质拍掉。
吸尘除尘是通过吸尘器将表面的灰尘、杂质
吸走。
五、底漆处理
底漆处理是为了提高涂装层的附着力,防止涂层与基材之间的化学反应。
底漆可以起到填平基材表面微小凹凸的作用,提高涂装层的平整度。
常用的底漆有多种类型,如防锈底漆、丙烯酸底漆、环氧底漆等。
根据涂
装需求,选择合适的底漆进行处理。
六、效果修整
效果修整是指对底漆处理后的表面进行修整,以提高涂装的外观效果。
根据涂装需求,可以进行抛光、喷砂、磨光等处理。
抛光是指运用机械设
备如抛光机对表面进行切削,去除表面的凹凸不平,提高表面的光滑度。
喷砂是指通过喷砂设备将表面喷射高速颗粒,以去除表面的凹坑、氧化物等。
磨光是指利用砂轮等磨料对表面进行磨削,去除表面的污垢、瑕疵等。
综上所述,涂装前处理是确保涂层质量和附着力的重要环节。
通过表
面清洁、除锈、打磨、除尘、底漆处理和效果修整等一系列处理工序,可
以提供一个良好的涂装基础,保证涂层的外观效果和使用寿命。
因此,在
进行涂装工艺之前,必须要进行严格的涂装前处理。