硫酸盐电镀锡添加剂的探讨
改善硫酸盐电镀液性能的添加剂

有 着较 好 的匹 配结 合 , 使 界面 问 的空 隙 面积 大 为减
少。 而 陶瓷 类材 料则不 然 , Al 。 O。 是 一种硬 而脆 的颗
P ) 一 P P S四种 镀层 中耐蚀 性 能 最好 的是 ( N i — Mo — P) 一
P P S ; 在较 高 温度 腐蚀 条件 下 , ( Ni — Mo — P ) 一 P P S镀层 的腐蚀 速率 是 Ni — P 、 Ni — Mo — P的 1 / 4和 ] / a 。 参 考文 献 :
改善 硫 酸 盐 电镀 液 性 能 的添 加 剂
在硫 酸盐 电镀 锡 、 镍、 铜、 铬、 铁、 钌、 铑、 铁一 锌合
加剂 可 以大 大增 加硫 酸盐 电镀 液 电镀 的 阴极 电流密
金 及锡一 锌合 金 等 电镀 液 中 添加 有 效 数 量 的 一种 添
加剂 , 可 以扩 大 阴极 电 流 密度 范 围 、 改 善 镀 层 的外
使得 P P S与基 体合 金镀 层 紧密结 合 , 减 少 了镀 层 的 孔 隙率 , 使镀 层表 面 平整 , 从而提 高 了合金 镀 层的耐
蚀性 能 。
郭忠 诚 , 杨显万 , 刘鸿康 , 等 . S i C微粒对 N i — W— S i C 复
合镀 层 工 艺 及 性 能 的影 响 [ J ] .化 工 冶 金 , 1 9 9 7 , 1 8
电流 电镀 时试 片 出现 黑 色烧 焦 镀 层 , 高 电流 密度 端
烧焦 1 2 mm 宽 。 当加 入 1 0 g / L 羟 乙基 磺 酸钠 ( 以羟
酸 根作 为 主要 的 阴离 子 , 这类 电解 液在 使 用 上受 到 许 多 限制 , 虽 然有 时加 入 了一 些 添加 剂 改 善 了镀 层
高深镀力硫酸镀锡光剂配方工艺

PM-2000高分散能力硫酸盐镀锡配方工艺(周生电镀导师)一、工艺性能PM-2000酸性镀锡光亮剂是专为电子电镀及高性能五金电镀而设计。
配方工艺操作极其简单,可以称为傻瓜式添加剂。
亮度不够添加光亮剂,走位不佳添加开缸剂。
这种设计不会导致光亮剂过量,工人操作起来非常简单。
周生电镀导师: [@Q]: /3/8/0/6/8/5/5/0/9/主要特点:1、镀层结晶细致、色泽银白,可作为仿银镀层,光亮电流密度范围宽。
2、可焊性和抗变色性好,镀锡产品经长时间贮存仍有良好的可焊性,镀层经高温老化后无变色现象,可代替锡铅合金镀层。
3、镀液分散能力强,低电流区效果佳,电流效率高。
4、能与目前使用的大多数同类光亮剂兼容,可直接加入。
5、本品无氟无铅,是环保型电镀产品。
(微)(Xin):(1)(3)(6)(5)(7)(2)(0)(1)(4)(7)(0)二、工艺配方和操作条件和WX)(广-告-长*期*有*效)我们的配方平台帮助了很多中小企业提高产品技术水平,也有不少个人因此创业成功,帮助国内企业抢占国外知名企业市场,提升国产占有率是我们长期追求的目标。
三、镀液的配制在新配槽中加镀液容积70%左右的蒸馏水或去离子水,在搅拌条件下,缓缓加入化学纯级硫酸,放冷到45℃左右时,加入化学纯或电镀特定级硫酸亚锡。
搅拌使溶解,加水至规定体积,过滤,加入计算量的PM-2000主光剂和走位剂,搅拌均匀后即可试镀。
四、镀液的维护1、平时补充光亮剂和走位剂,消耗量都约为200~400mL/KAH。
温度超过28度时添加剂消耗量要增加。
2、两种添加剂的添加比例约为1:1。
对于复杂工件走位剂的添加量应增大10%。
走位剂应及时添加,否则主光剂的消耗量会增加30%以上,并且锡镀层的抗氧化能力下降。
3、镀液配制和补加必须用蒸馏水或去离子水。
要防止CL-的带入,所以镀件前处理最好用硫酸。
4、阴阳极铜棒最好镀上一层锡,以防止铜杂质进入镀液。
镀件掉入槽中,要时捞出。
电镀加工:酸性硫酸盐镀锡故障及其处理方法:镀层有白雾
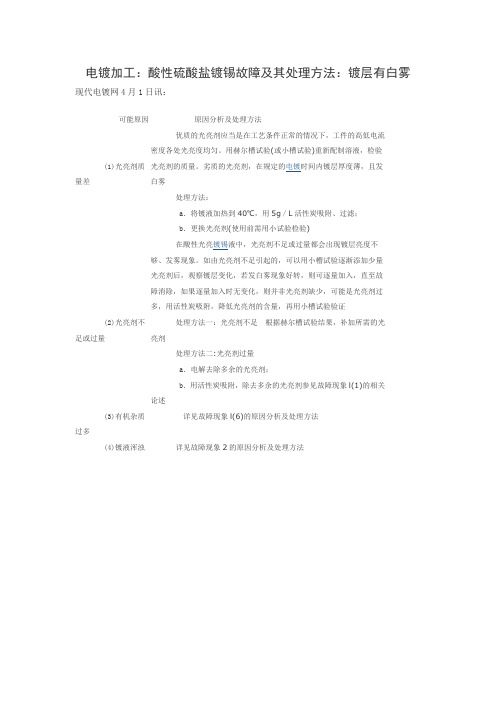
电镀加工:酸性硫酸盐镀锡故障及其处理方法:镀层有白雾现代电镀网4月1日讯:
可能原因原因分析及处理方法
(1)光亮剂质量差
优质的光亮剂应当是在工艺条件正常的情况下,工件的高低电流密度各处光亮度均匀。
用赫尔槽试验(或小槽试验)重新配制溶液,检验光亮剂的质量。
劣质的光亮剂,在规定的电镀时间内镀层厚度薄,且发白雾
处理方法:
a.将镀液加热到40℃,用5g/L活性炭吸附、过滤;
b.更换光亮剂(使用前需用小试验检验)
(2)光亮剂不足或过量
在酸性光亮镀锡液中,光亮剂不足或过量都会出现镀层亮度不够、发雾现象。
如由光亮剂不足引起的,可以用小槽试验逐渐添加少量光亮剂后,观察镀层变化,若发白雾现象好转,则可逐量加入,直至故障消除,如果逐量加入时无变化,则并非光亮剂缺少,可能是光亮剂过多,用活性炭吸附,降低光亮剂的含量,再用小槽试验验证
处理方法一:光亮剂不足根据赫尔槽试验结果,补加所需的光亮剂
处理方法二:光亮剂过量
a.电解去除多余的光亮剂;
b.用活性炭吸附,除去多余的光亮剂参见故障现象l(1)的相关论述
(3)有机杂质
过多
详见故障现象l(6)的原因分析及处理方法
(4)镀液浑浊详见故障现象2的原因分析及处理方法。
硫酸盐型光亮纯锡电镀添加剂特性

硫酸盐型光亮纯锡电镀添加剂哪家好?ASN-168属于硫酸盐型光亮纯锡电镀工艺,适用于滚镀、挂镀。
本工艺采用先进独特的电镀添加剂,可以在很宽的操作温度范围内,获得均匀的光泽纯锡镀层。
本工艺获得的纯锡镀层中有机物含量极少,具有极其优异的可焊性能,被广泛应用于电子电镀工业领域,适用于线路板、铜排、IC三极管、LED支架、四方针、铜带、端子等精密电子产品电镀。
➢ASN-168硫酸盐型光亮纯锡电镀工艺特性1.镀液稳定,容易控制。
2.阳极溶解均匀,锡离子稳定。
3.出光速度快,电镀效率高,电流范围特宽。
4.深镀能力与整平性优良,光亮范围宽。
5.镀层结晶细致光亮,长时间储存仍可保持极佳的焊锡性及抗蚀性。
➢ASN-168硫酸盐型光亮纯锡电镀工艺设备要求镀槽 PVC、PE、PP或耐酸玻璃纤维衬里的不锈钢槽(使用前应用5%的硫酸清洗)。
整流器直流输出电压为6V,最大波纹系数为5%。
阳极至少含99.99%纯锡做阳极,阳极钩用钛材或覆Monel,阳极袋用PP或Dynel。
温控镀液温度必须维持在建议范围内。
加热/冷却可用Teflon、铅或钛材料制造。
搅拌挂镀要用阴极移动,速度为1.5~3.0 m/min。
过滤挂镀必须过滤,用10μm 的PP或Dynel滤芯,不能用滤纸或纤维素过滤。
➢ASN-168硫酸盐型光亮纯锡电镀工艺镀液组成与操作条件项目单位范围最佳硫酸亚锡(滚镀) g/L 16-30 20硫酸亚锡(挂镀) g/L 20-40 30硫酸g/L 140-200 150(82ml)ASN-168纯锡开缸剂ml/L 10-30 20ASN-168纯锡光泽剂ml/L 1-3 2电流密度A/dm2 0。
5-25 2(建议依Sn2+定)温度℃3-25 滚镀5 挂镀15,阳极面积:阴极面积≥1:1➢ASN-168硫酸盐型光亮纯锡电镀工艺镀液配制1.往经彻底清洗的镀槽中注入1/3的纯水。
2.在搅拌下,加入计算量的硫酸。
3.待温度降至30度在搅拌下加入计算的硫酸亚锡。
酸性硫酸盐镀锡故障及其处理方法

酸性硫酸盐镀锡故障及其处理方法酸性硫酸盐镀锡故障及其处理方法:光亮锡镀层的可焊性差可能原因原因分析及处理方法(1)镀层厚度太薄铜合金基体镀锡或钢基体镀铜后镀锡,锡与铜互相接触,存在一个铜、锡界面,金属之间互相渗透,形成合金扩散。
在高温下,这种现象尤为明显。
铜基体对锡有较好的渗透作用,渗透速度较快,而锡也向铜合金基体渗透,随着时间的推移,扩散的结果是在原来的界面上形成了两个不同金相组成的扩散层,一个由Cu3Sn组成,靠近铜基体一边;靠近锡镀层一边,其组成为Cu6Sn5。
因为铜的熔点较高(为1083℃),故Cu3Sn 和Cu6Sn5的熔点都要比纯锡(232℃)高得多,超过700℃。
所以铜锡合金层很难在焊接温度下熔化,即不易和溶化了的铅锡焊料互相渗透,形成一个新的合金,因此表现出来的焊接性差。
如果镀锡层的厚度较厚,那么较薄的铜锡合金层还不足以影响焊接性;如果镀锡较薄,在3μm以下,随着Cu-Sn扩散带的逐步增长,锡层变得更薄,镀件就表现出扩散层合金的特征,必然会导致工件焊接性能下降。
另一方面裸露在空气中的锡层表面会缓慢氧化,锡镀层的真实厚度变薄,锡的氧化物阻碍了锡层与焊料之间的互相溶解和锡层的熔化。
以上两种因素导致原来就很薄的锡镀层可焊性差,焊接用的工件的锡镀层厚度一般要求在10μm左右,至少为5~6tμm处理方法:据镀层的特定性能,设定电流和时间,确保镀层厚度满足后工序深加工的要求续:上述故障现象可能原因原因分析及处理方法(2)光亮剂性质的影响不同的光亮剂虽然都能得到同样光亮的锡镀层,但焊接性能差别较大,应合理选择光亮剂处理方法:合理选择适合本产品加工特性的光亮剂(3)基体表面光洁度的影响试验发现,基体表面光洁度对镀层的焊接性能有较大的影响,即表面光洁度好的比表面粗糙者有好的焊接性。
这是因为基体金属光洁度越好,镀层的结晶就越细致紧密。
另外,镀层表面不洁净,易产生白雾的镀层,经高温老化后,其焊接性差处理方法:基体金属表面粗糙的工件,抛光后再电镀(4)镀液老化的影响将老镀液和新配的镀液镀出的锡镀层进行可焊性对比试验,结果新配制的镀液镀出的工件有更好的可焊性。
电镀液中添加剂的选择与电镀工艺的优化研究

电镀液中添加剂的选择与电镀工艺的优化研究绪论电镀液是电化学镀液中的重要组成部分,它对电镀工艺和镀层质量起着至关重要的作用。
电镀液中的添加剂作为一种功能性化学品,可以改善电镀工艺参数、提升镀层质量和增加电镀液的寿命。
本文旨在研究电镀液中添加剂的选择与电镀工艺的优化,以期提供一些参考和指导。
一、电镀液中添加剂的选择电镀液中的添加剂种类繁多,主要包括增溶剂、缓蚀剂、亲和剂、运移剂、聚合剂等。
在选择电镀液中的添加剂时,应综合考虑以下几个方面:1. 电镀物质的性质:不同的电镀物质对电镀液中添加剂的要求不同。
例如,镀铜需要添加聚合剂以提高镀层的结晶性和平整度,而镀镍则需要缓蚀剂以降低镀层的氢吸收能力。
2. 加工要求:电镀液中的添加剂还应根据加工要求进行选择。
例如,对于金属件表面需要良好的亲和性时,可以添加亲和剂提高电镀层的附着力和一致性。
3. 环境要求:在选择电镀液中的添加剂时,还应考虑环境要求,尽量选择环境友好型添加剂。
例如,选择无机添加剂或者可降解的有机添加剂,以减少对环境的污染。
二、电镀工艺的优化除了选择合适的电镀液中的添加剂外,电镀工艺的优化也是提高电镀质量的关键。
1. 电镀参数的优化:电镀参数包括电流密度、温度、pH值等,这些参数的设定对电镀液中添加剂的活性影响较大。
合理地调整这些参数,可以提高电镀液中添加剂的效果,进而优化电镀工艺。
2. 电极材料的选择与处理:电极材料对电镀质量和电镀液中添加剂的性能起到重要作用。
正确选择电极材料,并进行适当的处理和预处理,可以改善电极界面的活性,提升电镀质量。
3. 电镀液的搅拌和过滤:电镀液中的添加剂在电镀过程中容易发生分解和沉积,影响其效果。
适当地搅拌和过滤电镀液,可以防止添加剂的分解和沉积,保持电镀液的稳定性。
4. 清洗和剥离工艺的改进:在电镀过程中,清洗和剥离工艺也对电镀质量起着重要作用。
优化清洗和剥离工艺,可以减少残留的电镀液和添加剂,从而提高镀层的纯净度和质量。
电镀加工:酸性硫酸盐镀锡故障及其处理方法:镀层色泽均匀,但光亮度不足
电镀加工:酸性硫酸盐镀锡故障及其处理方法:镀层色泽均匀,但光亮度不足现代电镀网4月1日讯:可能原因原因分析及处理方法(1)光亮剂不足酸性镀锡光亮剂是一种组合光亮剂,一般由主光亮剂、辅助光亮剂、乳化剂、扩散剂、稳定剂、特种添加剂及溶剂等成分构成,其中最主要的是主光亮剂、辅助光亮剂和乳化剂三种,选择三者的化学成分、保持三者的配比平衡是光亮剂成功的关键。
各类光亮剂在镀液中能提高阴极极化作用,使镀层细致光亮。
光亮镀锡层比普通镀锡层稍硬,并仍能保持足够的延展性,其可焊性及耐蚀性良好。
当光亮剂含量不足时,不能获得镜面光亮镀层;当光亮剂过多时,镀层发黄、发黑、变脆、脱落,有时甚至镀不上镀层,严重影响镀层的结合力和可焊性。
因此,添加剂应少加、勤加,用赫尔槽调整光亮剂的比例处理方法:据光亮剂说明书的补加标准,按电量(kA·h)的消耗量进行补加,并用赫尔槽试验校正(2)硫酸亚锡含量过高硫酸亚锡是酸性镀锡的主盐,提高浓度在允许的范围内可提高阴极电流密度上限,加快沉积速度。
但是若浓度过高,分散能力下降,光亮区缩小,镀层色泽变暗,结晶粗糙;若浓度过低,生产效率下降,镀层易烧焦处理方法:稀释镀液,分析调整镀液成分至标准值(3)电镀时间过短镀层亮度与镀层的厚度有一定的关系,如电镀时间过短,镀层太薄,光亮度差处理方法:延长电镀时间,保证镀层厚度和光亮度(4)温度过高光亮镀锡温度一般在10~20℃下进行,如果温度超过25℃,就会影响镀层的光亮度,超过30℃,不利于光亮剂吸附,而且载体光亮剂析出,使其他光亮剂失效。
亚锡盐的氧化水解和光亮剂消耗均随温度升高而加快,若温度过高(超过35℃),Sn2+氧化速度加快,镀液浑浊,镀层粗糙,光亮剂消耗增加,光亮区变窄,严重时镀层变暗,出现花斑,可焊性降低。
低温有利于整体光亮及良好的均镀性,但温度过低,工作电流密度范围缩小,镀层易烧焦。
加入稳定剂能提高使用温度的上限值处理方法:采用制冷或停镀,降低镀液温度至标准值续:故障现象l可能原因原因分析及处理方法(5)金属杂质过多 Cu2+、Fe2+、As3+、Sb3+是酸性镀锡液中的有害杂质,含量过多,镀液浑浊,镀层发暗、孔隙多、结晶粗糙。
硫酸盐镀锡(硫酸盐无光亮镀锡和光亮镀锡工艺规范)
(4)稳定剂 镀液不稳定、易浑浊是硫酸盐镀锡的主 要缺点。如果不加稳定剂,镀液在使用或放置过程中,颜 色逐渐变黄,最终发生浑浊、沉淀。镀液混浊后,镀层光 泽性差、光亮区窄、可焊性下降,难以镀出合格产品;且 该混浊物呈胶体状态,难以除去和回收,导致锡盐浪费。 镀液混浊的原因相当复杂,一般认为主要是镀液中Sn4+离 子的存在及其水解的结果。即Sn4+离子浓度达到一定值时, 将发生水解反应:
早期,光亮镀锡Байду номын сангаас的获得是将暗锡镀层经232℃以上“重 熔”处理。从20世纪20年代起人们就开始探索直接光亮电镀 锡的方法,但直到1975年英国锡研究会采用了以木焦油作为 光亮剂,才为光亮镀锡工业化奠定了基础。近年来,镀锡光 亮剂的研究很活跃,性能优良的添加剂不断涌现,我国在这 方面的研究也取得了较大的进展。
8
9
上述结构通式中的Rl、R2、R3,和R4分别代表不同的取代基。 对同一结构,改变R,可以得到多种不同的有机化合物,它 们都有一定的增光作用。主光亮剂大多不溶于水。
b.辅助光亮剂 实验证明仅仅使用主光亮剂并不能获得 高质量的光亮镀层,需要同时添加脂肪醛和不饱和羰基化合 物,如甲醛、乙二醛、苄叉丙酮、丙烯酸、异丁烯酸、丙烯 酰胺等。这些添加剂称为辅助光亮剂,能与主光亮剂一起协 同作用,使晶粒细化,有增光作用。
15
(5) 其它添加剂 目前仍有不少产品使用无光亮酸性镀锡。 该类镀液多选择明胶、β-萘酚、甲酚磺酸等为添加剂,以使镀 层细致、可焊性好。
萘酚起提高阴极极化、细化晶粒、减少镀层孔隙的作用。 由于这类添加剂是憎水的,含量过高时会导致明胶凝结析出, 并使镀层产生条纹。
明胶主要作用是提高阴极极化和镀液分散能力、细化晶粒。 与β-萘酚配合时有协同效应,使镀层光滑细致。明胶过高会降 低镀层的韧性及可焊性,故镀锡层要求高可焊性时不应采用明 胶,即使普通无光亮镀锡溶液,明胶的加入量也要严加控制。
硫酸盐电镀锡
硫酸盐电镀锡1·前言光亮硫酸盐镀锡电流效率高,沉积速度快,可在室温下工作,且原料易购,成本较低,同时锡镀层柔软、孔隙小,既可作表面装饰性镀层如代银等,也可作可焊性镀层。
因此,光亮硫酸盐镀锡在电子工业和轻工业中应用很广泛。
然而,其工艺中存在着二价锡易氧化及添加剂分解造成镀液混浊及性能恶化、镀层光亮区变窄等问题,故需对其进行改进。
2·镀液各成分作用及工艺流程2.1镀液中各成分作用光亮硫酸盐镀锡液主要成分为硫酸亚锡和硫酸,生产中其含量随所采用的添加剂不同而不同。
2.1.1镀液中主要成分的作用2.1.1.1硫酸亚锡硫酸亚锡为主盐,含量一般控制在40~100g/L。
但生产实验结果表明,高浓度硫酸亚锡虽然可以提高阴极电流密度,加快沉积速度,但使镀液分散能力明显下降,且使镀层结晶粗、光亮区域变小,甚至大大缩短了镀液的处理周期。
SnSO4含量控制在20~60g/L为宜,若取下限,可以通过加快镀液循环速度及电极(阴极或阳极)移动速度等办法进行“补偿”,仍可镀出优良产品,但不宜过低。
2.1.1.2硫酸硫酸具有降低亚锡离子的活性、防止其水解、提高镀液导电性能及阳极电流效率等作用。
当硫酸量不足时,亚锡离子易氧化成四价锡。
从动力学的观点分析,当有足够的H2SO4时,可以减慢二价锡的水解,稳定镀液,实际生产中H2SO4含量一般在80~150mL/L。
2.1.2添加剂镀锡光亮剂一般是由主光剂、辅助光亮剂、载体光亮剂复配制成。
2.1.2.1主光剂酸性光亮镀锡光亮剂的种类繁多,归纳起来可分为两大类:第1类主要是芳醛、芳酮、酯类及不饱和有机酸烯的衍生物,第2类主要是西佛碱类(基本结构单元为-CH=N—CH=CH-或-CH=CH-CH=N-),由乙醛与邻甲丙胺缩合而成,是酸性光亮镀锡有效的增光剂,能单独使用,也可与第l类光亮剂配合使用,当与第1类光亮剂配合使用时,能显著拓宽光亮区,有效消除镀层白雾。
有机光亮剂的光亮作用主要表现为在阴极上的吸附,阴极上的吸附过强或过弱均无法获得理想的光亮镀层。
电流密度对硫酸盐光亮镀锡的影响
电流密度对硫酸盐光亮镀锡的影响高箐遥;王守绪;陈苑明;陈世金;何为;彭勇强【摘要】在电流密度为0.01~0.05 A/cm2的条件下进行光亮锡镀.研究了电流密度对阴极过电位、电流效率及镀层厚度的影响,并用SEM和XRD对镀层的表面形貌和晶粒的择优取向进行了表征.结果表明:随着电流密度的增大,阴极过电位和镀层厚度不断增加,电流效率先增大后减小.在较低的电流密度下得到的镀层表面较为均匀、致密;当电流密度高于0.03 A/cm2时,镀层表面出现较多孔隙,粗糙度增加.不同电流密度下,晶粒的择优取向不同.当电流密度高于0.03 A/cm2时,晶粒的择优取向由(101)晶面和(211)晶面向(220)晶面转变.【期刊名称】《电镀与环保》【年(卷),期】2019(039)003【总页数】4页(P7-10)【关键词】电流密度;光亮镀锡;硫酸盐【作者】高箐遥;王守绪;陈苑明;陈世金;何为;彭勇强【作者单位】电子科技大学材料与能源学院,四川成都610054;电子科技大学材料与能源学院,四川成都610054;电子科技大学材料与能源学院,四川成都610054;博敏电子股份有限公司,广东梅州514700;电子科技大学材料与能源学院,四川成都610054;奈电软性科技电子(珠海)有限公司,广东珠海519040【正文语种】中文【中图分类】TQ1530 前言在硫酸盐镀液中,当没有添加剂存在时,只能得到多孔、结合力差的枝晶镀层。
加入特定的有机添加剂,可以抑制结晶生长,促进晶核生成,获得平整、光亮的镀层[1]。
国内外对硫酸盐电镀添加剂已经有了较多的研究[2-3],但有关电流密度对镀锡影响的研究较少。
本文在含有复合添加剂的硫酸盐镀液中,研究了电流密度对光亮镀锡的影响。
1 实验1.1 实验材料采用覆铜板作为基体材料,试样尺寸为55.0 mm×120.0 mm×1.2 mm。
1.2 工艺流程试样酸性除油水洗微蚀水洗活化光亮镀锡水洗吹干1.3 镀液组成及工艺条件硫酸亚锡24.2 g/L,浓硫酸53.0 mL/L,对苯二酚1.0 g/L,酒石酸钾钠80.0 g/L,二巯基苯并咪唑0.4 g/L,甲醛8.0 mL/L,辛烷基苯酚-10 1.5 mL/L,电流密度0.01~0.05 A/cm2,温度30℃。
- 1、下载文档前请自行甄别文档内容的完整性,平台不提供额外的编辑、内容补充、找答案等附加服务。
- 2、"仅部分预览"的文档,不可在线预览部分如存在完整性等问题,可反馈申请退款(可完整预览的文档不适用该条件!)。
- 3、如文档侵犯您的权益,请联系客服反馈,我们会尽快为您处理(人工客服工作时间:9:00-18:30)。
验为 10 级, 结合力合格; 该镀锡添加剂能还原镀液中的溶解氧和 Sn [ 中图分类号] TQ153. 1 [ 文献标识码] A
4+
2+ , 有效抑制 Sn 的氧化, 细化镀层结晶。
[ 关键词] 电镀锡; 光亮剂; 稳定剂; 钒酸盐; 苄叉丙酮; 极化曲线 [ 文章编号] 1001 - 1560 ( 2011 ) 06 - 0001 - 04
0
前
言
对比试验、 电化学测试和正交试验筛选出了镀锡添加 显著提高了镀锡溶液稳定性, 增加了 镀 层 的 光 亮 剂, 性, 且镀液不易浑浊, 泡沫很少, 电流密度范围较宽, 可 镀层细致光亮, 结合力优良。 室温下工作,
2 度 0. 5 ~ 5. 0 A / dm , 阳极为 99. 9 % 的锡板, 带电入槽,
。 用 不 含 添 加 剂 的 酸 性 镀 锡 溶 液, 由于
的交换电流密度大, 只能镀出疏松、 粗糙、 树枝状
或海绵状镀层; 在强酸性溶液中很难找到可以大幅度 抑制金属离子电沉积的配位剂。 而加入有机添加剂在 结晶生长点上有选择地吸附可以抑制结晶生长, 促进 晶核生成, 获得平整、 光亮的镀层
3
( 延长 56 d 以上 ) 。 这说明钒酸盐是一种良好的镀锡 8 稳定剂。 与镀液 3 比较可知, 加入光亮剂的镀液 7 , 稳定性降低; 同时, 酒石酸会提高镀液稳定性。 图 1 是 1 号镀液及不同钒酸盐含量的 7 号镀锡溶 液中的开路电位 -时间曲线, 研究电极为锡条。 由图 1 可以看出: 不含钒酸盐的 1 号镀液开路电位最低, 低于 - 0. 444 V; 钒酸盐从 0. 01 g / L 增加到 0. 05 g / L, 开路 电位明显提高, 从 - 0. 442 V 提高到 - 0. 439 V; 钒酸盐 从 0. 07 g / L 增加到 0. 13 g / L, 开路电位无明显变化。 以上情况说明, 加入 0. 05 g / L 钒酸盐, 镀液的开路电位 即可达最大值。 根据能斯特方程也知道, 加入钒酸盐 镀液中 Sn 后,
镀液, 敞口放置于恒温水浴锅内, 溶液温度为 25 ~ 26 ℃, 记录镀液开始变为淡黄色或变混浊 所 需 的 时 间。 pH 值测量用霍尔槽 250 mL, 黄铜试片 100. 0 mm × 70. 0 mm × 0. 2 mm, 电流为 1 A, 时间为 3 min; 阴
2 极电流密度为 3 A / dm , 用称重法测定。用铜库仑计法
2
2. 1
结果与讨论
稳定剂对镀液稳定性的影响 一般会 硫酸盐镀锡溶液使用或放置一段时间后,
测定阴极电流效率。 ( 3 ) 阴极极化曲线 用 CHI660C 型电化学工作站 采用三电极体系进行测量, 研究电极为 A3 钢, 面积为
2 3. 8 mm2 , 辅助电极为铂电极, 面积为 25 mm , 参比电极
1 ) - - - - - )
-1
-1
)
· L -1) ρ( 抗坏血酸) / ( g · L -1) ρ( 聚乙二醇) / ( g · L ρ( 酒石酸) / ( g
-1
)
· L ρ( 苄叉丙酮) / ( g
-1
- ) - - 0. 19 - 0. 12 - 0. 03 0. 03 7 ( 黄) 13
2+ [5 ]
mm。前处理工艺流程: 一次除油 → 热水洗 → 冷水洗 → 酸洗→冷水洗→二次除油 → 热水洗 → 冷水洗 → 活化 → 冷水洗→去离子水洗。 其中, 一次除油为 50 g / L INT 10 化学除油粉, 65 ~ 70 ℃ , 时间 5 min; 二次除油为 35 30 g / L Na2 CO3 , 40 g / L Na3 PO4 ·12H2 O, 1 g / L NaOH, g / L OP -10 , 温度 80 ~ 85 ℃ , 时间 5 min; 酸洗采用 1 ∶ 1 的 HCl; 活化采用 145 g / L H2 SO4 溶液; 中和液为 10 % Na3 PO4 。 1. 2 镀锡工艺 154 g / L H2 SO4 。 其 基础镀液配方: 40 g / L SnSO4 , 中加入稳定剂 ( 5 种 ) 、 光亮剂 ( 由甲醛、 苄叉丙酮和复 合添加剂组成) 适量后, 以温度 10 ~ 35 ℃ , 阴极电流密
2+
聚乙二醇组成) 作镀锡溶液光亮剂。 为使苄叉丙 化剂、 酮能均匀地分散在镀液中, 必须要有合 适 的 分 散 剂。 光亮剂性能评定结果见表 2 。
表2
镀 ( 甲醛) / 液 ( mL · L -1) 号 1 2 3 4 5 6 7 8 9 K1 K2 K3 R 2 2 2 5 5 5 8 8 8 70. 5 83. 5 65. 5 18. 0
光亮剂性能评定的正交试验结果
ρ( 复合添 覆盖 加剂) / 析氢 光亮度 光亮区 总分 能力 -1 (g · L ) 1. 1 2. 1 3. 1 3. 1 1. 1 2. 1 2. 1 3. 1 1. 1 56. 5 87. 0 76. 0 30. 5 5 8 5 8 5 5 7 6 5 0 10. 0 9. 0 7. 5 9. 0 6. 0 8. 0 6. 0 0 0. 5 6. 5 3. 5 2. 5 7. 5 3. 0 5. 5 2. 5 0. 5 9 8 6 10 10 10 10 10 5 14. 5 32. 5 23. 5 28. 0 31. 5 24. 0 30. 5 24. 5 10. 5
表1
镀液种类 · L ( 石油醚) / ( mL · L ρ( 钒酸盐) / ( g
-1
配位能力, 且没有其他副作用。 石油醚、 钒酸盐、 抗坏 血酸、 聚乙二醇、 酒石酸 5 种稳定剂对镀液稳定性的影 响见表 1 ( 各镀液中含 5 mL / L 甲醛) 。
稳定剂对镀锡液恒温静置稳定性的影响
2 200. 00 - - - - - - - 0. 23 - 0. 15 - 0. 04 0. 03 10 ( 黄) 20 3 - 0. 05 - - - - - - 0. 20 - 0. 13 - 0. 04 - 0. 04 104 ( 黄) 121 4 - - 4. 00 - - - - - 0. 22 - 0. 14 - 0. 05 0. 02 7 ( 红) 16 5 - - - 5. 00 - - - - 0. 21 - 0. 11 - 0. 03 0. 03 15 ( 黄) 25 6 - - - - 10. 00 - - - 0. 18 - 0. 13 - 0. 04 0. 02 11 ( 黄) 30 7 - 0. 05 - - - 0. 10 40. 00 - 0. 20 - 0. 13 - 0. 04 0. 01 71 ( 黄) 91 8 - 0. 05 - - 10. 00 0. 10 40. 00 - 0. 21 - 0. 11 - 0. 03 - 0. 01 75 ( 黄) 104
[ 收稿日期] 2010 11 29 [ 基金项目] 福建省泉州师范学院硕士学位授予权立项学 科建设项目资助 [ 通信作者] 尹国光, 副教授, 从事电镀、 化学复合镀研究, E -mail: ygg09@ 163. com 电话: 13505943416 ,
[6 ]
。 本工作通过老化
阴极移动进行电镀。
[ 4 ] 电流效率高, 镀层细致, 可焊性好, 应用广泛 。
基材处理 基材为 A3 钢, 尺寸为 40. 0 mm × 40. 0 mm × 0. 8
目前所使用的添加剂易使镀液性能不稳定、 变浑 浊、 泡沫多、 光亮区电流密度范围较窄。 普通硫酸亚锡 镀液很不稳定, 在常温下敞开放置几天后就开始变浑, 不到 10 d 就完全浑浊, 出现黄色沉淀, 再也不能镀出合 格的产 品 Sn
先变黄, 然后变浑浊、 产生白色胶状沉淀, 导致镀液电 阻增加、 分散能力降低、 镀层光亮性差。 硫酸盐镀锡溶 液变浑浊主要是由于 Sn 酸
[8 ] 2+
的氧化及 Sn
4+
( 部分 Sn4 + 来
为饱和甘汞电极 ( SCE ) 。 参数设置: 初始电位为 - 0. 4 V, 终止点位为 - 1. 0 V, 扫描速度为 10 mV / s。 1. 3. 2 镀层 镀层厚度为 10 μm。 通过划痕
1
硫酸盐电镀锡添加剂的探讨
尹国光,肖海明,曲仕文,张辛浩 ( 泉州师范学院化学与生命科学学院 ,福建 泉州 362000 ) [ 摘 要] 目前, 硫酸盐镀锡使用的添加剂易使镀液不稳定 、 变质、 多泡, 为此, 从镀液变黄和变浊时间以及 pH 值
等方面, 筛选合适的稳定剂和不同光亮剂组合 , 研究其对镀液性能的影响。 用电化学工作站测试钒酸盐含量对镀 锡溶液开路电位以及苄叉丙酮和复合添加剂含量对镀液阴极极化曲线的影响 。 通过划痕试验、 弯曲试验、 热震试 镀锡溶液开路电 验和盐雾试验检测了添加剂对镀液和镀层性能的影响 。结果表明: 当钒酸盐含量为 0. 05 g / L 时, 90 d 不浑浊; 当苄叉丙酮含量为 0. 10 g / L, 位明显提高, 添加 1 次能维持镀液 70 d 不变黄, 复合添加剂含量为 2. 3 g / L 时, 吸附电位范围在 - 0. 78 ~ - 0. 53 V, 阴极极化度提高, 获得镜面光亮锡镀层的电流密度范围为 0. 5 ~ 5. 0
2+ Sn4 + 有 的抗氧化能力或对 Sn ,
试验、 弯曲试验和热震试验检测 ( 2 ) 孔隙率及耐蚀性
按 QB / T 3823 - 99 中“1 贴
求稳定剂能提高 Sn
2+
滤纸法” 测试孔隙率。按 GB / T 10125 - 1997 测试镀层 的耐 中 性 盐 雾 NSS 试 验 性 能, 阴极电流密度为 2 A / dm2 , 锡镀层厚度均为 10 μm。