化学镀铜与直接电镀工艺
化学镀铜与直接电镀工艺
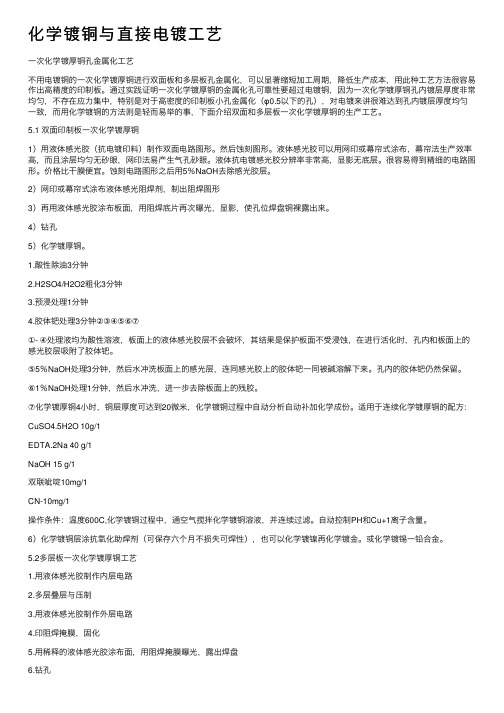
化学镀铜与直接电镀⼯艺⼀次化学镀厚铜孔⾦属化⼯艺不⽤电镀铜的⼀次化学镀厚铜进⾏双⾯板和多层板孔⾦属化,可以显著缩短加⼯周期,降低⽣产成本,⽤此种⼯艺⽅法很容易作出⾼精度的印制板。
通过实践证明⼀次化学镀厚铜的⾦属化孔可靠性要超过电镀铜,因为⼀次化学镀厚铜孔内镀层厚度⾮常均匀,不存在应⼒集中,特别是对于⾼密度的印制板⼩孔⾦属化(φ0.5以下的孔),对电镀来讲很难达到孔内镀层厚度均匀⼀致,⽽⽤化学镀铜的⽅法则是轻⽽易举的事,下⾯介绍双⾯和多层板⼀次化学镀厚铜的⽣产⼯艺。
5.1 双⾯印制板⼀次化学镀厚铜1)⽤液体感光胶(抗电镀印料)制作双⾯电路图形。
然后蚀刻图形。
液体感光胶可以⽤⽹印或幕帘式涂布,幕帘法⽣产效率⾼,⽽且涂层均匀⽆砂眼,⽹印法易产⽣⽓孔砂眼。
液体抗电镀感光胶分辨率⾮常⾼,显影⽆底层。
很容易得到精细的电路图形。
价格⽐⼲膜便宜。
蚀刻电路图形之后⽤5%NaOH去除感光胶层。
2)⽹印或幕帘式涂布液体感光阻焊剂,制出阻焊图形3)再⽤液体感光胶涂布板⾯,⽤阻焊底⽚再次曝光,显影,使孔位焊盘铜裸露出来。
4)钻孔5)化学镀厚铜。
1.酸性除油3分钟2.H2SO4/H2O2粗化3分钟3.预浸处理1分钟4.胶体钯处理3分钟②③④⑤⑥⑦①- ④处理液均为酸性溶液,板⾯上的液体感光胶层不会破坏,其结果是保护板⾯不受浸蚀,在进⾏活化时,孔内和板⾯上的感光胶层吸附了胶体钯。
⑤5%NaOH处理3分钟,然后⽔冲洗板⾯上的感光层,连同感光胶上的胶体钯⼀同被碱溶解下来。
孔内的胶体钯仍然保留。
⑥1%NaOH处理1分钟,然后⽔冲洗,进⼀步去除板⾯上的残胶。
⑦化学镀厚铜4⼩时,铜层厚度可达到20微⽶,化学镀铜过程中⾃动分析⾃动补加化学成份。
适⽤于连续化学镀厚铜的配⽅:CuSO4.5H2O 10g/1EDTA.2Na 40 g/1NaOH 15 g/1双联呲啶10mg/1CN-10mg/1操作条件:温度600C,化学镀铜过程中,通空⽓搅拌化学镀铜溶液,并连续过滤。
7电镀和化学镀

镀层具备良好性能的基本条件:
1、与基体金属结合牢固,附着力好; 2、镀层完整,结晶细致,孔隙少; 3、镀层厚度分布均匀。
7.1 电镀的基本原理与工艺
一、电镀的基本原理
电镀反应是一种典型的电解反应。 电镀:电化学+金属学
金属离子阴极还原时,其沉积电位等于它的平 衡电位与过电位之和。
在电镀中,过电位主要由电化学极化和浓差极 化产生的。
缺点:
可镀制的金属(合金体系)有限; 镀液昂贵,稳定性差,镀制成本高。
化学镀技术在化工、电子、石油等工业中有着极为重要的地位。
还原剂是化学镀溶液中的主要成分之一。
还原剂对镀层的性能有着显著的影响。
化学镀溶液常用的还原剂: 次磷酸盐、甲醛、肼、硼氢化物、胺基硼烷及其衍生物等。
二、化学镀镍
活化:
将敏化处理后的制品浸入含有氧化剂的溶液中,使其表面形成胶体状微粒沉积层 的过程。
还原处理:
用一定浓度的化学镀时所用的还原剂溶液将制品表面残留的催渗剂还原干净,以 免影响后面的化学镀溶液的过程。
预处理完后的非金属制品就可以进行化学镀,在形成一定厚度的 金属镀层以后,再进行电镀,使获得的镀层加厚,即可完成非金属 的电镀。
合金电镀在结晶致密性、镀层孔隙率、外观色泽、硬度、耐蚀性、 耐磨性、导磁性、减磨性和抗高温性等方面远远优于单金属电镀。 一般说来,合金镀层最少合金组分的质量分数应在1%以上。
一、合金电镀的基本原理
实现合金电镀的必要条件: 1、两种金属中至少有一种金属能单独从其盐的水溶液中沉积出来; 2、两种金属共沉积时,它们的析出电位要十分接近或相等:
镀层纯度高达99.5%。
钢板镀铜工艺

钢板镀铜工艺一、钢板镀铜工艺流程1. 预处理钢板镀铜工艺的第一步是预处理。
首先,需要对钢板表面进行去油脱脂,以去除表面的油污和杂质,保证镀铜层的附着力。
其次,对钢板进行酸洗,去除表面的氧化皮和铁锈,保证镀铜时的表面光洁度。
2. 化学镀铜在预处理完成后,钢板进入化学镀铜的环节。
化学镀铜是利用电化学原理,在钢板表面镀上一层铜金属。
首先,将钢板置于含有铜离子的电解液中,通过外加电流,在钢板表面沉积铜金属。
化学镀铜需要控制电流密度、温度、PH值、搅拌等参数,以保证镀铜层均匀致密。
3. 电镀铜化学镀铜完成后,钢板还需要进行电镀铜。
电镀铜是将化学镀铜层进一步增厚,提高镀铜层的厚度和导电性能。
在电镀铜过程中,需要控制电流密度、温度、PH值等参数,以保证镀铜层的均匀性和致密性。
4. 后处理钢板经过化学镀铜和电镀铜后,需要进行后处理。
首先是清洗,去除表面的电解液残留和杂质,保证镀铜层的纯净性。
其次,需要进行烘干,以去除表面的水分,防止镀铜层氧化。
5. 检验包装最后,对镀铜的钢板进行检验,检查镀铜层的厚度、致密性和导电性能等指标,合格后进行包装,以便于运输和使用。
二、钢板镀铜工艺参数1. 电流密度电流密度是指单位面积上通过的电流量,通常用安培/平方分米(A/dm2)来表示。
在化学镀铜和电镀铜过程中,需要根据钢板的尺寸和形状,确定合适的电流密度,以保证镀铜层的均匀性和致密性。
2. 温度镀铜液的温度对镀铜层的厚度和致密性有重要影响。
通常情况下,温度越高,镀铜层的厚度越大,但难以控制镀铜层的均匀性。
因此,在实际生产中,需要根据钢板的材质和形状,确定合适的镀铜液温度。
3. PH值镀铜液的PH值对镀铜层的均匀性和致密性也有重要影响。
通常情况下,PH值越高,镀铜层的厚度越大,但也容易产生气泡和不良现象。
因此,需要在实际生产中,通过调整镀铜液的PH值,以获得合适的镀铜效果。
4. 搅拌在化学镀铜和电镀铜过程中,需要保持镀铜液的搅拌,以保证镀铜层的均匀性和致密性。
化学镀铜的目的及工艺流程介绍

化学镀铜的目的及工艺流程介绍化学镀铜(Eletcroless Plating Copper)通常也叫沉铜或孔化(PTH)是一种自身催化性氧化还原反应。
首先用活化剂处理,使绝缘基材表面吸附上一层活性的粒子通常用的是金属钯粒子(钯是一种十分昂贵的金属,价格高且一直在上升,为降低成本现在国外有实用胶体铜工艺在运行),铜离子首先在这些活性的金属钯粒子上被还原,而这些被还原的金属铜晶核本身又成为铜离子的催化层,使铜的还原反应继续在这些新的铜晶核表面上进行。
化学镀铜在我们PCB制造业中得到了广泛的应用,目前最多的是用化学镀铜进行PCB的孔金属化。
化学镀铜的主要目的是在非导体材料表面形成导电层,目前在印刷电路板孔金属化和塑料电镀前的化学镀铜已广泛应用。
化学镀铜层的物理化学性质与电镀法所得铜层基本相似。
化学镀铜的主盐通常采用硫酸铜,使用的还原剂有甲醛、肼、次磷酸钠、硼氢化钠等,但生产中使用最普遍的是甲醛。
化学镀铜的工艺流程:一、镀前处理1.去毛刺钻孔后的覆铜泊板,其孔口部位不可避免的产生一些小的毛刺,这些毛刺如不去除将会影响金属化孔的质量。
最简单去毛刺的方法是用200~400号水砂纸将钻孔后的铜箔表面磨光。
机械化的去毛刺方法是采用去毛刺机。
去毛刺机的磨辊是采用含有碳化硅磨料的尼龙刷或毡。
一般的去毛刺机在去除毛刺时,在顺着板面移动方向有部分毛刺倒向孔口内壁,改进型的磨板机,具有双向转动带摆动尼龙刷辊,消除了除了这种弊病。
2.整孔清洁处理对多层PCB有整孔要求,目的是除去钻污及孔微蚀处理。
以前多用浓硫酸除钻污,而现在多用碱性高锰酸钾处理法,随后清洁调整处理。
孔金属化时,化学镀铜反应是在孔壁和整个铜箔表面上同时发生的。
如果某些部位不清洁,就会影响化学镀铜层和印制导。
化学镀工艺

2.1化学镀铜
化学镀铜液采用硫酸铜作主盐, 以甲醛为还原剂, EDTA二钠盐和酒石酸钾钠组成的双络合剂体系, 稳定剂主要由亚铁氢化钾和α,α′-联吡啶组成;该体系具有稳定性好、使用寿命长、操作温度宽、成本低等特点。化学镀铜优化后的工艺参数为:镀液配方为KNaC4H4O6·4H20:40g/l,NaOH:9g/l,Na2CO3 :42g/l,CuSO4·5H20:14g/l,NiCl2:4g/l,HCHO(37%):53ml/l;pH=12~13(NaOH 溶液调节);温度为(60±2) ℃;装载量为6.7~10dm2/ L;搅拌方式为电磁搅拌。镀覆完毕抽虑,用去离子水清洗,在真空干燥箱中烘干。试验结果表明,该配方镀覆速度快,镀层性能好;配方的作用原理是铜离子与甲醛的氧化还原反应:
1.5 解胶
镀件基体经过胶体钯活化后,表面吸附的是以钯原子为核心的胶团,为使金属钯能起催化作用,需要将吸附在钯原子周围的二价锡胶体层去除以显露出活性钯位置,即进行解胶处理。解胶处理一般采用体积浓度100mL/L的盐酸在40~45℃处理0.5~1min,或用20~25g/L的醋酸钠溶液常温下处理10min。
1.3 敏化
敏化处理是使粗化后的有机基体(或除油后的无机基体)表面吸附一层具有还原性的二价锡离子Sn2+,以便在随后的活化处理时,将银或钯离子由金属离子还原为具有催化性能的银或钯原子。敏化液配方为:SnCl2·2H2O:20g/l,浓HCl:40ml/l,少量锡粒;加入锡粒的目的是防止二价锡离子的氧化。
⑥表
面活性剂。粉末、颗粒、纤维状的镀件材料单体质量差异较大,加人到化学镀溶液中后,轻质的漂浮于镀液表面,较重的沉降于底层,即使充分搅拌也难以充分分散于镀液中,影响施镀效果;需要在镀液中添加适量的阴离子或非离子表面活性剂。加人表面活性剂可提高镀液对基体的浸润效果,使粉末、颗粒、纤维状镀件很好地分散于镀液中,形成比较稳定的悬浮液。表面活性剂的浓度在一定程度上直接影响粉末、颗粒、纤维状镀件表面上金属镀层的性能。表面活性剂含量过高时生产成本较高,且会产生较大的泡沫,较大的泡沫会吸附粉末、颗粒、纤维状的镀件材料导致化学镀难以进行,尚需再适当加人消泡剂。表面活性剂含量过低则会影响其在粉体表面的吸附,达不到充分浸润的效果,导致镀件表面活化程度降低,使金属难以沉积在镀件表面;一般情况下,表面活性剂添加量为镀液总质量的0.1~0.15%为宜。常用的表面活性剂有6501净洗剂、烷基苯磺酸盐,烷基磺酸盐,十二烷基脂肪酸盐,十二烷基脂肪酸盐+ 醋酸钠,AES, TX-9和TX-10等。表面活性剂的类型和混合比例对粉末、颗粒、纤维状的镀件材料表面化学镀的效果也有很大的影响。
化学镀工艺流程详解
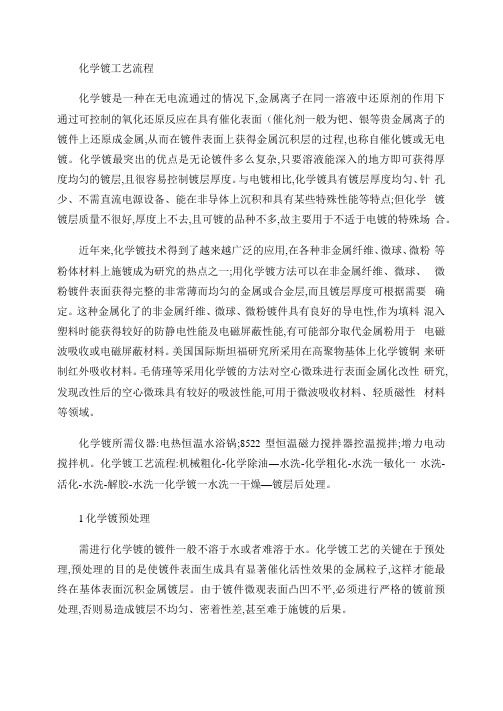
化学镀工艺流程化学镀是一种在无电流通过的情况下,金属离子在同一溶液中还原剂的作用下通过可控制的氧化还原反应在具有催化表面(催化剂一般为钯、银等贵金属离子的镀件上还原成金属,从而在镀件表面上获得金属沉积层的过程,也称自催化镀或无电镀。
化学镀最突出的优点是无论镀件多么复杂,只要溶液能深入的地方即可获得厚度均匀的镀层,且很容易控制镀层厚度。
与电镀相比,化学镀具有镀层厚度均匀、针孔少、不需直流电源设备、能在非导体上沉积和具有某些特殊性能等特点;但化学镀镀层质量不很好,厚度上不去,且可镀的品种不多,故主要用于不适于电镀的特殊场合。
近年来,化学镀技术得到了越来越广泛的应用,在各种非金属纤维、微球、微粉等粉体材料上施镀成为研究的热点之一;用化学镀方法可以在非金属纤维、微球、微粉镀件表面获得完整的非常薄而均匀的金属或合金层,而且镀层厚度可根据需要确定。
这种金属化了的非金属纤维、微球、微粉镀件具有良好的导电性,作为填料混入塑料时能获得较好的防静电性能及电磁屏蔽性能,有可能部分取代金属粉用于电磁波吸收或电磁屏蔽材料。
美国国际斯坦福研究所采用在高聚物基体上化学镀铜来研制红外吸收材料。
毛倩瑾等采用化学镀的方法对空心微珠进行表面金属化改性研究,发现改性后的空心微珠具有较好的吸波性能,可用于微波吸收材料、轻质磁性材料等领域。
化学镀所需仪器:电热恒温水浴锅;8522型恒温磁力搅拌器控温搅拌;增力电动搅拌机。
化学镀工艺流程:机械粗化-化学除油―水洗-化学粗化-水洗一敏化一水洗-活化-水洗-解胶-水洗一化学镀一水洗一干燥—镀层后处理。
1化学镀预处理需进行化学镀的镀件一般不溶于水或者难溶于水。
化学镀工艺的关键在于预处理,预处理的目的是使镀件表面生成具有显著催化活性效果的金属粒子,这样才能最终在基体表面沉积金属镀层。
由于镀件微观表面凸凹不平,必须进行严格的镀前预处理,否则易造成镀层不均匀、密着性差,甚至难于施镀的后果。
1.1化学除油镀件材料在存放、运输过程中难免沾有油污,为保证预处理效果,必须首先进行除油处理,去除其表面污物,增加基体表面的亲水性,以确保基体表面能均匀的进行金属表面活化。
化学镀简介
能,晶粒细,无孔,耐蚀性好。 5. 化学镀工艺设备简单,不需要电源、输出系统及辅助
电极,操作时只需把工件正确悬挂在镀液中即可。 6. 化学镀溶液稳定性较差,寿命短,成本高。
化学镀的条件
1. 镀液中还原剂的还原电位要显著低于沉积金属的电位。 2. 镀液不产生自发分解。 3. 调节溶液PH值、温度时,可以控制金属的还原速率,
比较单纯 比较小 比较小 大 长 不均匀 导体 低
相当复杂 大 大 小 短 非常均匀 导体、非导体 高
化学镀镍的基本原理
化学镀镍的发展
1944年,Brenner和Riddell进行了第一次实验室实验,开 发了可以工作的镀液并进行了科学研究。
60~70年代,研究人员主要致力于改善镀液性能。
80年代后,镀液寿命、稳定性等得到初步解决,基本实 现镀液的自动控制。
原子氢态理论
1946年,Brenner和Ridder提出;1959年Gutgeit实验验证了该假说 1967年,苏联人对该理论又做了深入研究提出:还原镍的物质实质上就
是原子氢。
NaH2PO2→ Na++H2PO2-
1)镀液在加热时,通过次亚磷酸盐在水溶液中脱氢,形成亚磷酸根,同 时放出初生态原子氢
活化:
为了使待镀件获得充分活化的表面,以催化化学镀反应的进行。
化学镀铜基本原理
• 化学镀铜概述:
化学镀铜是电路板制造中的一种工艺,通常也叫沉铜, 是一种自身催化性氧化还原反应。首先用活化剂处理,使 绝缘基材表面吸附上一层活性的粒子通常用的是金属钯 (ba)粒子(钯是一种十分昂贵的金属),铜离子首先在 这些活性的金属钯粒子上被还原,而这些被还原的金属铜 晶核本身又成为铜离子的催化层,使铜的还原反应继续在 这些新的铜晶核表面上进行。
陶瓷化学镀铜工艺
陶瓷化学镀铜工艺
陶瓷化学镀铜工艺是一种常见的表面处理技术,广泛应用于陶瓷制品的生产过程中。
通过化学镀铜,可以在陶瓷表面形成一层均匀、光滑的铜层,不仅美观,还能增强陶瓷制品的硬度和耐磨性。
陶瓷化学镀铜的工艺过程主要包括准备工作、铜溶液配制、浸镀、电镀和后处理等环节。
在进行化学镀铜之前,需要对陶瓷进行清洁和打磨,以确保表面平整干净。
接着,根据具体工艺要求,配制合适的铜溶液,包括铜盐溶液、添加剂和稳定剂等成分,以保证镀层的质量和稳定性。
在浸镀阶段,将经过处理的陶瓷制品浸入铜溶液中,利用化学反应使铜离子还原析出,形成铜层。
浸镀时间和温度的控制对镀层的厚度和均匀性至关重要。
接下来是电镀环节,通过在陶瓷表面施加电流,进一步增加铜层的厚度和硬度。
最后,进行后处理工艺,包括清洗、抛光和保护处理,以提高镀层的光泽度和耐腐蚀性。
陶瓷化学镀铜工艺的优点在于可以实现对陶瓷表面的精细加工和装饰,提高产品的附加值和市场竞争力。
同时,镀铜层还可以提高陶瓷制品的导电性能,扩大其应用领域。
然而,需要注意的是,在进行化学镀铜过程中,要控制好各项参数,避免出现镀层不均匀、气泡等质量问题。
总的来说,陶瓷化学镀铜工艺是一项复杂而精密的技术,需要经过
严格的操作和控制才能达到理想的效果。
只有不断改进工艺,提高生产技术水平,才能更好地满足市场需求,推动陶瓷制品产业的发展。
希望通过不断的研究和实践,陶瓷化学镀铜工艺能够在未来得到更广泛的应用和推广。
电镀铜和化学镀铜的性能分析和影响因素
电镀铜的性能分析及影响因素(作者)摘要:关键词:英文摘要:0 绪论●电镀和化学镀概述在国民经济的各个生产和科学发展领域里,如机械、无线电、仪表、交通、航空及船舶工业中,在日用品的生产和医疗器械等设备的制造中,金属镀层都有极为广泛而应用。
世界各国由于钢铁所造成的损失数据是相当惊人的,几乎每年钢铁产量的,三分之一由于腐蚀而报废,当然电镀层不可能完全解决这个问题,但是良好的金属镀层还是能在这方面做出较大贡献的。
电镀和化学镀则是获得金属防护层的有效方法。
化学镀方法所得到的金属镀层,结晶细致紧密,结合力良好,它不但具有良好的防腐性能,而且满足工业某些特殊用途。
●化学镀与电镀的优缺点化学镀与电镀比较具有以下优点:(1)镀层厚度比较均匀,化学镀液的分散力接近百分之百,无明显的边缘效应,几乎是基材形状的复制因此特适合形状复杂工件、腔体件、深孔件、盲孔件、管件内壁等表面施镀。
电镀法因受力线分布不均匀的限制是很难做到的。
(2)通过敏化、活化等前处理化学镀可以在非金属(非导体)如塑料、玻璃、陶瓷及半导体材料表面上进行,而电镀发只能在导体表面上进行。
因此,化学镀工艺是非金属表面金属化的常用方法。
也是非导体材料电镀前作导电底层的方法。
(3)工艺设备简单,不需要电源、输电系统及辅助电极,操作时只需要把工件正确的悬挂在镀液中即可。
(4)化学镀是靠基体材料的自催化活性才能起镀,其结合力一般优于电镀。
镀层有光亮或半光亮的外观。
晶粒细、致密、孔隙率低。
某些化学镀层还具有特殊的物理性能。
电镀也具有其不能为化学镀代替的优点:(1)可以沉积的金属及合金品种远多于化学镀。
(2)价格比化学镀低得多。
(3)工艺成熟,镀液简单、易于控制。
化学镀铜的应用领域及进展铜具有良好的导电、导热性能,质软而韧,有良好的压延性和抛光性能。
为了提高表面镀层和基体金属的结合力,铜镀层常用作防护、装饰性镀层的底层,对局部渗碳工件,常用镀铜来保护不需要渗碳的部位。
1)印刷线路板通孔金属化处理目前化学镀铜在工业上最重要的应用是印刷线路板(PrintedCircuit Board,简称PCB)的通孔金属化过程,使各层印刷导线的绝缘孔壁内沉积上一层铜,从而使两面的电路导通,成为一个整体。
化学镀铜配方组成,化学镀铜成分分析及生产技术工艺
化学镀铜配方组成,生产工艺及技术应用1 背景化学镀(Chemiealplating)又称自催化镀;(Autoeatalytieplating),是指在没有外加电流的条件下,利用溶液中的还原剂将金属离子沉积在具有催化活性的基体表面。
从本质上讲,它发生的是一种自催化的氧化还原反应,又可译为不通电电镀或无电解电镀。
是在基体表面上化学沉积形成金属或合金镀层的一种表面处理技术。
化学镀铜第一次工业应用开始于19世纪50年代中叶,此后化学镀铜技术被大量用于电子和涂装行业,其中印刷电路板的工业生产一度成为规模最大的应用领域。
化学镀铜技术继而被用于金属化工艺,在半导体电子行业等高技术领域扮演着越来越重要的角色,特别是近年来,超大规模集成电路由铝金属化发展为铜金属化工艺以来,化学镀铜技术更加受到关注。
禾川化学引进国外尖端配方解析技术,经过多年的技术积累,成功开发出新型化学镀铜配方技术;该化学镀铜镀层厚度均匀,无明显边缘效应,特别是对复杂形状的基体,在尖角或凹凸部位没有额外的沉积或沉积不足,在深孔、盲孔件、腔体件的内表面也能得到和外表面同样厚度的镀层,因而对尺寸精度要求高的零件进行化学镀铜特别有利;该镀层晶粒细、致密、空隙少,呈光亮或半光亮,比电镀层更加耐腐蚀;该镀铜技术无需电解设备及附件,工艺操作人员也无需带电操作,均可在所需部位镀出合乎要求的镀层。
该镀铜技术广泛应用于电子、汽车、航空等行业。
2化学镀铜常见组成典型的镀液成分主要由无机盐和有机添加剂组成。
无机盐包括CuCl2、CuSO4、氯离子,采用的主要有机添加剂包括促进剂(或称为光亮剂);抑制剂(表面活性剂,润湿剂,阻化剂)。
2.1铜盐铜盐是化学镀铜的主盐,提供镀铜所需要的铜离子,可以使用CuSO4、CuC12、Cu(NO3)2、Cu(OH)2、(CH3COO)2Cu、酒石酸铜等二价铜盐;目前最常采用的铜盐为硫酸铜,化学镀铜溶液中铜盐的含量越高,镀速越快;但是当其含量继续增加达到某一定值后,镀速变化不再明显。
- 1、下载文档前请自行甄别文档内容的完整性,平台不提供额外的编辑、内容补充、找答案等附加服务。
- 2、"仅部分预览"的文档,不可在线预览部分如存在完整性等问题,可反馈申请退款(可完整预览的文档不适用该条件!)。
- 3、如文档侵犯您的权益,请联系客服反馈,我们会尽快为您处理(人工客服工作时间:9:00-18:30)。
一次化学镀厚铜孔金属化工艺
不用电镀铜的一次化学镀厚铜进行双面板和多层板孔金属化,可以显著缩短加工周期,降低生产成本,用此种工艺方法很容易作出高精度的印制板。
通过实践证明一次化学镀厚铜的金属化孔可靠性要超过电镀铜,因为一次化学镀厚铜孔内镀层厚度非常均匀,不存在应力集中,特别是对于高密度的印制板小孔金属化(φ0.5以下的孔),对电镀来讲很难达到孔内镀层厚度均匀一致,而用化学镀铜的方法则是轻而易举的事,下面介绍双面和多层板一次化学镀厚铜的生产工艺。
5.1 双面印制板一次化学镀厚铜
1)用液体感光胶(抗电镀印料)制作双面电路图形。
然后蚀刻图形。
液体感光胶可以用网印或幕帘式涂布,幕帘法生产效率高,而且涂层均匀无砂眼,网印法易产生气孔砂眼。
液体抗电镀感光胶分辨率非常高,显影无底层。
很容易得到精细的电路图形。
价格比干膜便宜。
蚀刻电路图形之后用5%NaOH去除感光胶层。
2)网印或幕帘式涂布液体感光阻焊剂,制出阻焊图形
3)再用液体感光胶涂布板面,用阻焊底片再次曝光,显影,使孔位焊盘铜裸露出来。
4)钻孔
5)化学镀厚铜。
1.酸性除油3分钟
2.H2SO4/H2O2粗化3分钟
3.预浸处理1分钟
4.胶体钯处理3分钟②③④⑤⑥⑦
①- ④处理液均为酸性溶液,板面上的液体感光胶层不会破坏,其结果是保护板面不受浸蚀,在进行活化时,孔内和板面上的感光胶层吸附了胶体钯。
⑤5%NaOH处理3分钟,然后水冲洗板面上的感光层,连同感光胶上的胶体钯一同被碱溶解下来。
孔内的胶体钯仍然保留。
⑥1%NaOH处理1分钟,然后水冲洗,进一步去除板面上的残胶。
⑦化学镀厚铜4小时,铜层厚度可达到20微米,化学镀铜过程中自动分析自动补加化学成份。
适用于连续化学镀厚铜的配方:
CuSO4.5H2O 10g/1
EDTA.2Na 40 g/1
NaOH 15 g/1
双联呲啶10mg/1
CN-10mg/1
操作条件:温度600C,化学镀铜过程中,通空气搅拌化学镀铜溶液,并连续过滤。
自动控制PH和Cu+1离子含量。
6)化学镀铜层涂抗氧化助焊剂(可保存六个月不损失可焊性),也可以化学镀镍再化学镀金。
或化学镀锡一铅合金。
5.2多层板一次化学镀厚铜工艺
1.用液体感光胶制作内层电路
2.多层叠层与压制
3.用液体感光胶制作外层电路
4.印阻焊掩膜,固化
5.用稀释的液体感光胶涂布面,用阻焊掩膜曝光,露出焊盘
6.钻孔
7.H2SO4/HF凹蚀处理
8.粗化,活化,NaOH解胶
9.化学镀厚铜20μm
一次化学镀厚铜有以下优点:①缩短加工周期,②可以制高精度电路图形,因为没有图形电镀工艺,消除了镀层突延所造成的图形失真,③金属化孔镀层厚度非常均匀,不存在电化学镀铜的镀液分散能力问题,从而提高了细微金属化孔的可靠性。
第二节直接电镀
电子部十五所陈长生
1、概述
印制板孔金属化技术是印制板制造技术的关键之一,长期以来人们一直延用化学镀铜的方法,但是化学镀铜溶液中的甲醛对生态环境有危害,并且有致癌的潜在危险,同时化学镀铜溶液中的络合剂(如EDTA等)不易进行生物降解,废水处理困难,除此之外,化学镀铜溶液的稳定性较差,操作稍有不慎就会出现溶液分解,需对其进行严格的监控和维护,同时目前化学镀铜层的机构性能(如延伸率和抗拉强度等)都比不上电镀铜层。
而且化学镀铜工艺流程长,操作维护极不方便,因此迫使人们放弃原有的化学镀铜而研究开发新的孔金属化工艺,直接电镀技术就应运而生。
直接电镀的基本思想是1963年IBM公司Mr.RODOVSKY提出来的,近年来这项技术得到了迅速的发展和应用。
作为代替化学镀铜的直接电镀技术必须满足以下条件:
1)在非导体包括环氧玻璃布,聚酰亚胺,聚四氟乙烯等孔壁基材上,通过特殊处理形成一层导电层,以实现金属电镀。
同时还必须保证镀层与基体铜具有良好的结合力。
2)形成导电层所用的化学药水对环境污染小,易于进行"三废"处理,不会再造成严重污染。
3)形成导电层的工艺流程越短越好,而且要求操作范围应较宽,便于操作与维护。
4)能适应各种印制板的制作。
如高板厚/孔径比的印制板,盲孔印制板,特殊基材的印制板等。
直接电镀技术虽起步较早,以前工艺不成熟,应用较少,1983年以后加快了对新的直接电镀技术的研究与开发,先后出现了多种多样的直接电镀技术,各种不同的直接电镀系列药品相继商品化。
直接电镀技术按导电材料分类,基本上可归纳为三种类型。
1.钯系列(以钯或其化合物作为导电物质)
2.导电性能离分子系列[如聚呲咯(Pyrrole),聚苯胺(Polyaniline)]
3.碳黑系列
常见的直接电镀法列于表6-5.
表6-5常见的直接电镀法分类表
下面针对各种导电系列分别作简单介绍。
2、钯系列
2.1技术原理
钯系列方法是通过吸附Pd胶体或钯离子,使印制板非导体的孔壁获得导电性,为后续电镀提供了导电层,吸附钯胶体与过去化学镀铜前的活化处理所吸附的胶体钯不同,直接电镀用胶体钯层要致密,其中胶体钯粒子非常细腻约为10-25A,而传统胶体钯的粒子约为300A.通过在钯溶液中加入添加剂,使钯的吸附紧密,互相重合成为层状,以提高其导电性,通过选择合适的清洁整孔剂或助催化剂等方法来提高孔壁基材对导电钯的吸附量,而在铜上的吸附量减少。
为了进一步提高吸附钯膜的导电性,有多种方法,如硫化处理,稳定性处理或中和处理等。
利用钯作为直接电镀用的导电层的方法很多,例如Shipley公司的Crimson法,是采用pd-Sn胶体催化,通过改变整孔剂,使钯一锡胶体的吸附量提高了三倍,为了提高导电性,从胶粒中去除锡,使钯形成易导电的硫化钯。
Solu tech公司开发的Neopact法中使用的胶体钯不含Sn2+,而含有一种弱酸性可溶性有机聚合物,易清洗,通过后浸和选择剂处理后,将铜面上的Pd除去,同时微蚀铜表面,改善导电pd膜与孔壁的结合力以及电镀铜与基体铜的结合力,从而提高了工艺可靠性。
2.2工艺流程
形成导电pd层的方法不同,其工艺流程也不完全相同,表6-6简要介绍一下几种方法的工。