电子油门踏板设计DFMEA分析
汽车制动系统设计DFMEA案例分析
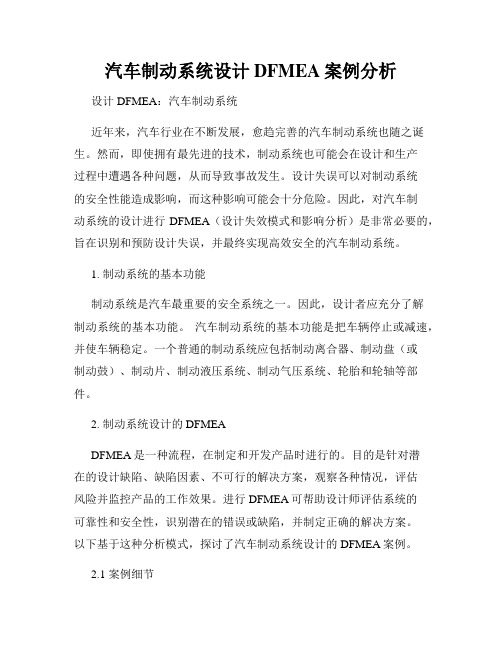
汽车制动系统设计DFMEA案例分析设计DFMEA:汽车制动系统近年来,汽车行业在不断发展,愈趋完善的汽车制动系统也随之诞生。
然而,即使拥有最先进的技术,制动系统也可能会在设计和生产过程中遭遇各种问题,从而导致事故发生。
设计失误可以对制动系统的安全性能造成影响,而这种影响可能会十分危险。
因此,对汽车制动系统的设计进行DFMEA(设计失效模式和影响分析)是非常必要的,旨在识别和预防设计失误,并最终实现高效安全的汽车制动系统。
1. 制动系统的基本功能制动系统是汽车最重要的安全系统之一。
因此,设计者应充分了解制动系统的基本功能。
汽车制动系统的基本功能是把车辆停止或减速,并使车辆稳定。
一个普通的制动系统应包括制动离合器、制动盘(或制动鼓)、制动片、制动液压系统、制动气压系统、轮胎和轮轴等部件。
2. 制动系统设计的DFMEADFMEA是一种流程,在制定和开发产品时进行的。
目的是针对潜在的设计缺陷、缺陷因素、不可行的解决方案,观察各种情况,评估风险并监控产品的工作效果。
进行DFMEA可帮助设计师评估系统的可靠性和安全性,识别潜在的错误或缺陷,并制定正确的解决方案。
以下基于这种分析模式,探讨了汽车制动系统设计的DFMEA案例。
2.1 案例细节应用DFMEA对新型汽车制动系统进行评估。
制动系统的开发人员已确定了一系列的模式,包括安装端口、材料、制动系统的阀门、抽吸和压力泵、筒和活塞,以及几个不同的操作组件。
同时,汽车制动系统设计还考虑了传动控制、电子系统和机械系统等方面,以确保高效安全的设计。
2.2 评估模式评估模式是DFMEA的重要组成部分。
为了进行制动系统的评估,需要确定系统中的各个子部件,并评估每个子系统的失效模式。
失效模式是指系统中可能发生的错误模式或缺陷,例如材料错误,设备质量问题或人员操作不当等。
每个失效模式都伴随着一个或多个潜在的后果,因此,准确评估失效模式是必要的。
2.3 评估影响对于每种失效模式,需要评估其潜在的影响。
汽车电子油门设计FMEA

汽车电子油门设计FMEA汽车电子油门是现代汽车中的重要组成部分,其设计和功能的稳定性对汽车的性能和安全起着至关重要的作用。
为了确保汽车电子油门的可靠性和稳定性,设计团队需要进行一项称为失效模式及其影响分析(Failure Mode and Effects Analysis,FMEA)的过程。
FMEA是一种系统性的方法,用于识别和评估设计中的潜在失效模式,并通过设计控制措施和预防措施减少或消除这些失效模式及其负面影响。
在进行电子油门设计FMEA时,以下是一些可能需要考虑的关键部分和潜在失效模式:1.电子油门传感器:电子油门传感器是电子油门系统的核心部分,用于测量踏板的位置和驾驶员对油门的控制。
潜在失效模式可能包括传感器故障、信号漂移或失真等。
设计控制措施可能包括使用高质量的传感器、冗余传感器以及通过监控系统来验证传感器的准确性。
2.电子油门执行器:电子油门执行器是将电子控制信号转换为机械运动的装置。
潜在失效模式可能包括执行器卡住、振动过大或执行器内部元件故障等。
设计控制措施可能包括使用高质量的执行器、采用重要元件的冗余设计以及增加执行器的冗余。
3.控制单元:电子油门的控制单元负责接收来自传感器的信号,并通过电子油门执行器控制发动机转速。
潜在失效模式可能包括控制单元故障、软件错误或通信中断等。
设计控制措施可能包括采用高可靠性的控制单元、多层次软件设计和增加通信冗余性。
4.电源供应:电子油门需要一个稳定可靠的电源供应来确保正常运转。
潜在失效模式可能包括电源断电、电压波动或电源线路短路等。
设计控制措施可能包括采用多电源系统、应急电源备份以及使用电源管理模块来监控和稳定电源供应。
5.环境条件:汽车电子油门需要在各种环境条件下工作,包括高温、低温、高湿度等。
潜在失效模式可能包括环境温度过高导致电子元件故障、湿度引起腐蚀或电路短路等。
设计控制措施可能包括选择适应各种环境条件的元件和材料、加强密封性和使用冷却系统或加热系统来控制温度。
汽车底盘DFMEA-制动踏板带角传感器
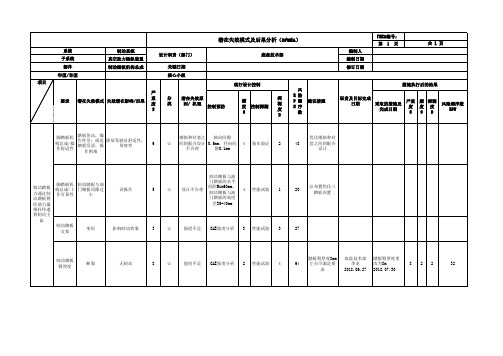
不合理
隙0.1mm
优化销轴和衬 48 套之间的配合
设计
制动踏板 力通过制 动踏板臂 经助力器 推杆传递 到制动主
缸
脚踏板机 制动踏板与油
构总成/工 门踏板间隙过
作可靠性
小
制动踏板 支架
变形
误操作 影响制动效果
制动踏板与油
门踏板的水平
5
☆
设计不合理
间距Min60mm, 制动踏板与油
4
性能试验
1
门踏板的高度
潜在失效模式及后果分析(DFMEA)
项目
系统 子系统
部件 年型/车型
制动系统 真空助力操纵装置 制动踏板机构总成
设计职责(部门)
关键日期 核心小组
要求
功 能
严
潜在失效模式 失效潜在影响/后果
重 度
S
分 潜在失效原
类
因/ 机理 控制预防
底盘技术部
现行设计控制
频 度 控制探测 O
探 测 度 D
风 R险 P顺 N序
有部分信号
连杆与底座旋
6
☆ 转配合尺寸不 优化配合公差 2 设计评审 3
36
合理
户要求的
信号
ECU报故障
6
☆
踏板回位不畅
调整踏板弹簧 回位力
3 设计评审
2
36
信号不稳定
6
☆
高低温环境的 选用符合要求
影响
的元器件
2
高低温试 验
2
24
踏板外观
踏板外观 美观,无 生锈迹象
制动踏板表面 影响制动踏板寿命,
腐蚀
影响美观
5
踏板总成表面 无电镀要求
新版dfmea系统分析案例

新版DFMEA系统分析案例案例背景一家汽车制造公司正在推出一款全新的SUV车型,为了确保车辆的质量和可靠性,公司决定采用新版的DFMEA(设计失效模式和影响分析)系统进行系统分析。
DFMEA是一种在设计阶段评估和减少系统风险的方法,它能够识别潜在的失效模式、分析其影响和严重性,并提供相应的改进措施。
系统分析步骤步骤一:定义系统首先,团队需要明确系统边界、系统功能和设计要求。
在这个案例中,团队需要定义SUV车型的关键系统和子系统,例如发动机、悬挂系统、制动系统、安全气囊等。
步骤二:识别失效模式在这一步骤中,团队需要对每个系统和子系统逐一进行分析,识别潜在的失效模式。
以发动机系统为例,可能的失效模式包括发动机无法启动、发动机自动熄火等。
步骤三:分析影响和严重性对于每个失效模式,团队需要评估其对系统和用户的影响,并确定其严重性。
影响可以包括安全风险、性能降低、故障率增加等。
严重性通常可以按照某个评估标准进行定量评估,例如使用1-10的等级评定。
步骤四:确定改进措施针对每个失效模式和其严重性,团队需要制定相应的改进措施。
例如,在发动机无法启动的失效模式下,可能的改进措施包括增加备用电池、加强电路连接等。
步骤五:实施改进措施在这一步骤中,团队需要逐一实施确定的改进措施,并对其进行记录和追踪。
例如,在实施了增加备用电池的改进措施后,团队需要跟踪发动机启动失效模式的发生率,以评估该措施的有效性。
案例分析结果通过对SUV车型各个系统和子系统的分析,团队得出以下结论:•发动机系统中,发动机自动熄火失效模式对车辆安全性有较大影响,严重性评级为8,建议增加燃油供给系统的检测和报警机制。
•悬挂系统中,悬挂系统异常噪声失效模式对乘坐舒适度和驾驶体验有较大影响,严重性评级为7,建议改进悬挂系统的阻尼设计。
•制动系统中,制动距离过长失效模式对行车安全性有较大影响,严重性评级为9,建议优化刹车片材料和刹车系统的液压传动机制。
结论随着汽车制造业的快速发展,确保车辆质量和可靠性变得至关重要。
dfmea案例
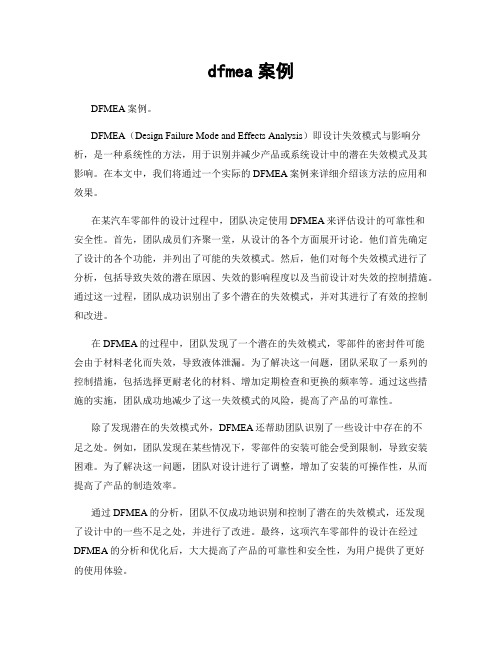
dfmea案例DFMEA案例。
DFMEA(Design Failure Mode and Effects Analysis)即设计失效模式与影响分析,是一种系统性的方法,用于识别并减少产品或系统设计中的潜在失效模式及其影响。
在本文中,我们将通过一个实际的DFMEA案例来详细介绍该方法的应用和效果。
在某汽车零部件的设计过程中,团队决定使用DFMEA来评估设计的可靠性和安全性。
首先,团队成员们齐聚一堂,从设计的各个方面展开讨论。
他们首先确定了设计的各个功能,并列出了可能的失效模式。
然后,他们对每个失效模式进行了分析,包括导致失效的潜在原因、失效的影响程度以及当前设计对失效的控制措施。
通过这一过程,团队成功识别出了多个潜在的失效模式,并对其进行了有效的控制和改进。
在DFMEA的过程中,团队发现了一个潜在的失效模式,零部件的密封件可能会由于材料老化而失效,导致液体泄漏。
为了解决这一问题,团队采取了一系列的控制措施,包括选择更耐老化的材料、增加定期检查和更换的频率等。
通过这些措施的实施,团队成功地减少了这一失效模式的风险,提高了产品的可靠性。
除了发现潜在的失效模式外,DFMEA还帮助团队识别了一些设计中存在的不足之处。
例如,团队发现在某些情况下,零部件的安装可能会受到限制,导致安装困难。
为了解决这一问题,团队对设计进行了调整,增加了安装的可操作性,从而提高了产品的制造效率。
通过DFMEA的分析,团队不仅成功地识别和控制了潜在的失效模式,还发现了设计中的一些不足之处,并进行了改进。
最终,这项汽车零部件的设计在经过DFMEA的分析和优化后,大大提高了产品的可靠性和安全性,为用户提供了更好的使用体验。
综上所述,DFMEA作为一种系统性的方法,能够帮助团队全面地识别并减少产品或系统设计中的潜在失效模式及其影响。
通过对失效模式的分析和控制,团队不仅可以提高产品的可靠性和安全性,还能够发现设计中的不足之处,并进行相应的改进。
DFMEA设计潜在失效模式及后果分析范本

4
64
长时间使用,材料摩损严 选择合适的材料,
重
优化踏板结构
2
材料试验,疲劳试 验,设计评审
4
64
迟滞力过大
踏点到旋转中心的距离短
设计符合客户要求 得结构
2
设计计算,评审。
3
54
踏板回位不畅,可 10 Z
能发生驾驶员想减
材料选择不当
选择合适的摩擦材 料
2
材料试验
3 60
速但不能减速
迟滞机构的表面粗糙度大
差
结构和电路
2
EMC试验
3 54
两路信号不同步 ECU报错,车辆不 8 能正常行驶
线性度不符合要求 高低温环境的影响
规定霍尔管在磁 场中的位置
2 初始性能
3 54
选用符合要求的电 子元器件
3
高低温存储试验, 高低温循环试验, 热冲击试验
3
63
配合过紧导致两个霍尔管 设计合理的定位结 安放的高度位置不一致 构
在踏板寿命期 无信号输出 内要保证踏板 旋转角度内需 要输出满足客 户要求的信号
ECU报错,车辆不 8 能正常行驶
☆ 过电压,短接,反接引起 优化电路,增加过
元器件损坏
压保护
2
过压试验,短接试 验,反接试验
3
48
环境潮湿导致短路
采用密封好的结构 3 防水试验
3 72
抗外界电气环境干扰性能 设计抗干扰性好的
有力的感觉,不易
弹簧力偏小
设计合理弹簧力值
2
设计计算,评审。 弹簧检测
2
36
控制车辆速度
内外压簧其中一只失效
选择合适得弹簧参 数及材料
电子燃油泵系统 DFMEA 范本.

潜在失效模式及后果分析(设计DFMEA)99新秀电子燃油泵系统进油板组合子系统FMEA编号:RLSP005-2009 进油板零件DZRYB001.00.01.01设计责任部门:产品开发部页码:共 25 页第 1 页车型年/车辆类型:关键日期:2009.10.9 编制者XXX主要参与人XXX、XXX、XXX、XXX、XX日期(编制):2009.10.6(修订):潜在失效模式及后果分析(设计DFMEA)99新秀电子燃油泵系统进油板组合子系统FMEA编号:RLSP005-2009 销钉零件DZRYB001.00.01.02设计责任部门:产品开发部页码:共 25 页第 2 页车型年/车辆类型:关键日期: 2009.10.9 编制者XXX潜在失效模式及后果分析(设计DFMEA)99新秀电子燃油泵系统外壳装配子系统FMEA编号:RLSP005-2009 叶轮零件DZRYB001.00.02.01设计责任部门:产品开发部页码:共 25 页第 3 页车型年/车辆类型:关键日期: 2009.10.6 编制者XXX潜在失效模式及后果分析(设计DFMEA)99新秀电子燃油泵系统出油板组合子系统FMEA编号:RLSP005-2009 轴承(大)零件DZRYB001.00.02.02.01设计责任部门:产品开发部页码:共 25 页第 4 页车型年/车辆类型:关键日期: 2009.10.9 编制者XXX主要参与人XXX、XXX、XXX、XXX、XX日期(编制):2009. 10.6(修订):潜在失效模式及后果分析(设计DFMEA)99新秀电子燃油泵系统出油板组合子系统FMEA编号:RLSP005-2009 出油板零件DZRYB001.00.02.02.02设计责任部门:产品开发部页码:共 25 页第 5 页车型年/车辆类型:关键日期:2009.10.9 编制者XXX主要参与人XXX、XXX、XXX、XXX、XX日期(编制):2009. 10.6(修订)潜在失效模式及后果分析(设计DFMEA)99新秀电子燃油泵系统外壳组合子系统FMEA编号:RLSP005-2009 电枢组件零件DZRYB001.00.02.03设计责任部门:产品开发部页码:共 25 页第 6 页车型年/车辆类型:关键日期:2009.10.9 编制者XXX主要参与人XXX、XXX、XXX、XXX、XX日期(编制):2009. 10.6(修订)潜在失效模式及后果分析(设计DFMEA)99新秀电子燃油泵系统磁瓦装配子系统FMEA编号:RLSP005-2009 磁瓦弹性夹零件DZRYB001.00.02.04.02设计责任部门:产品开发部页码:共 25 页第 8 页车型年/车辆类型:关键日期: 2009.10.9 编制者XXX主要参与人XXX、XXX、XXX、XXX、XX日期(编制):2009.10.6(修订)潜在失效模式及后果分析(设计DFMEA)99新秀电子燃油泵系统连接器组合子系统FMEA编号:RLSP005-2009 止动器零件DZRYB001.00.02.04.03.01.01设计责任部门:产品开发部页码:共 25 页第 9 页车型年/车辆类型:关键日期: 2009.10.9 编制者XXX主要参与人XXX、XXX、XXX、XXX、XX日期(编制):2009.10.7(修订)潜在失效模式及后果分析(设计DFMEA)99新秀电子燃油泵系统连接器组合子系统FMEA编号:RLSP005-2009 单向阀弹簧零件DZRYB001.00.02.04.03.01.02设计责任部门:产品开发部页码:共 25 页第 10 页车型年/车辆类型:关键日期:2009.10.9 编制者XXX主要参与人XXX、XXX、XXX、XXX、XX日期(编制):2009.10.7(修订)潜在失效模式及后果分析(设计DFMEA)99新秀电子燃油泵系统连接器组合子系统FMEA编号:RLSP005-2009 单向阀头组件零件DZRYB001.00.02.04.03.01.03设计责任部门:产品开发部页码:共 25 页第 11 页车型年/车辆类型:关键日期: 2009.10.9 编制者XXX主要参与人XXX、XXX、XXX、XXX、XX日期(编制):2009.10.7(修订)潜在失效模式及后果分析(设计DFMEA)99新秀电子燃油泵系统连接器组合子系统FMEA编号:RLSP005-2009 连接器件零件DZRYB001.00.02.04.03.01.04设计责任部门:产品开发部页码:共 25 页第 12 页车型年/车辆类型:关键日期:2009.10.9 编制者XXX主要参与人XXX、XXX、XXX、XXX、XX日期(编制):2009.10.7(修订)潜在失效模式及后果分析(设计DFMEA)99新秀电子燃油泵系统连接器组合子系统FMEA编号:RLSP005-2009 金属板零件DZRYB001.00.02.04.03.01.05设计责任部门:产品开发部页码:共 25 页第 13 页车型年/车辆类型:关键日期: 2009.10.9 编制者XXX主要参与人XXX、XXX、XXX、XXX、XX日期(编制):2009.10.7(修订)潜在失效模式及后果分析(设计DFMEA)99新秀电子燃油泵系统连接器组合子系统FMEA编号:RLSP005-2009 安全阀弹簧零件DZRYB001.00.02.04.03.01.05设计责任部门:产品开发部页码:共 25 页第 14 页车型年/车辆类型:关键日期:2009.10.9 编制者XXX主要参与人XXX、XXX、XXX、XXX、XX日期(编制):2009.10.7(修订)潜在失效模式及后果分析(设计DFMEA)99新秀电子燃油泵系统轴承固定架装配子系统FMEA编号:RLSP005-2009 右接线片零件DZRYB001.00.02.04.03.02.01 设计责任部门:产品开发部页码:共 25 页第 15 页车型年/车辆类型:关键日期: 2009.10.9 编制者XXX主要参与人XXX、XXX、XXX、XXX、XX日期(编制):2009.10.7(修订)潜在失效模式及后果分析(设计DFMEA)99新秀电子燃油泵系统轴承固定架装配子系统FMEA编号:RLSP005-2009 右电感组件零件DZRYB001.00.02.04.03.02.01 设计责任部门:产品开发部页码:共 25 页第 16 页车型年/车辆类型:关键日期: 2009.10.9 编制者XXX主要参与人XXX、XXX、XXX、XXX、XX日期(编制):2009.10.7(修订)潜在失效模式及后果分析(设计DFMEA)99新秀电子燃油泵系统轴承固定架装配子系统FMEA编号:RLSP005-2009 右碳刷接线片零件DZRYB001.00.02.04.03.02.03 设计责任部门:产品开发部页码:共 25 页第 17 页车型年/车辆类型:关键日期: 2009.10.9 编制者XXX主要参与人XXX、XXX、XXX、XXX、XX日期(编制):2009.10.7(修订)潜在失效模式及后果分析(设计DFMEA)99新秀电子燃油泵系统轴承固定架装配子系统FMEA编号:RLSP005-2009 左接线片零件DZRYB001.00.02.04.03.02.04 设计责任部门:产品开发部页码:共 25 页第 18 页车型年/车辆类型:关键日期: 2009.10.9 编制者XXX主要参与人XXX、XXX、XXX、XXX、XX日期(编制):2009.10.7(修订)潜在失效模式及后果分析(设计DFMEA)99新秀电子燃油泵系统轴承固定架装配子系统FMEA编号:RLSP005-2009 左电感组件零件DZRYB001.00.02.04.03.02.06 设计责任部门:产品开发部页码:共25 页第 19 页车型年/车辆类型:关键日期:2009.10.9 编制者XXX主要参与人XXX、XXX、XXX、XXX、XX日期(编制):2009.10.8(修订)潜在失效模式及后果分析(设计DFMEA)99新秀电子燃油泵系统轴承固定架装配子系统FMEA编号:RLSP005-2009左碳刷接线片零件DZRYB001.00.02.04.03.02.06 设计责任部门:产品开发部页码:共 25 页第 20 页车型年/车辆类型:关键日期: 2009.10.9 编制者XXX主要参与人XXX、XXX、XXX、XXX、XX日期(编制):2009.10.8(修订)潜在失效模式及后果分析(设计DFMEA)99新秀电子燃油泵系统轴承固定架组合子系统FMEA编号:RLSP005-2009 碳刷弹簧零件DZRYB001.00.02.04.03.02.07设计责任部门:产品开发部页码:共25 页第 21 页车型年/车辆类型:关键日期: 2009.10.9 编制者 XXX主要参与人XXX、XXX、XXX、XXX、XX日期(编制):2009.10.8(修订)潜在失效模式及后果分析(设计DFMEA)99新秀电子燃油泵系统轴承固定架组合子系统FMEA编号:RLSP005-2009 碳刷零件DZRYB001.00.02.04.03.02.08设计责任部门:产品开发部页码:共 25 页第 22 页车型年/车辆类型:关键日期: 2009.10.9 编制者XXX主要参与人XXX、XXX、XXX、XXX、XX日期(编制):2009.10.8(修订)潜在失效模式及后果分析(设计DFMEA)99新秀电子燃油泵系统轴承固定架组合子系统FMEA编号:RLSP005-2009 轴承固定架零件DZRYB001.00.02.04.03.02.09设计责任部门:产品开发部页码:共 25 页第 23 页车型年/车辆类型:关键日期: 2009.10.9 编制者XXX主要参与人XXX、XXX、XXX、XXX、XX日期(编制):2009.10.8(修订)潜在失效模式及后果分析(设计DFMEA)99新秀电子燃油泵系统轴承固定架组合子系统FMEA编号:RLSP005-2009 轴承(小)零件DZRYB001.00.02.04.03.02.09-1 设计责任部门:产品开发部页码:共 25 页第 24 页车型年/车辆类型:关键日期: 2009.10.9 编制者XXX主要参与人XXX、XXX、XXX、XXX、XX日期(编制):2009.10.8(修订)潜在失效模式及后果分析(设计DFMEA)99新秀电子燃油泵系统外壳组合子系统FMEA编号:RLSP005-2009 外壳零件DZRYB001.00.02.04.03.03设计责任部门:产品开发部页码:共 25 页第25 页车型年/车辆类型:关键日期: 2009.10.9 编制者XXX潜在失效模式及后果分析(设计DFMEA)99新秀电子燃油泵系统磁瓦组合子系统FMEA编号:RLSP005-2009 磁瓦零件DZRYB001.00.02.04.01 设计责任部门:产品开发部页码:共 25 页第 7 页车型年/车辆类型:关键日期: 2009.10.9 编制者XXX主要参与人XXX、XXX、XXX、XXX、XX。
dfmea案例

DFMEA案例背景介绍DFMEA(Design Failure Mode and Effects Analysis)是一种用于产品设计和开发过程中的风险评估方法。
它旨在识别和评估设计过程中可能存在的潜在故障模式及其对产品性能和可靠性的影响,以便制定相应的风险控制和改进措施,确保产品的质量和安全性。
案例描述本案例以电动汽车的电池管理系统设计为例,通过DFMEA方法来评估设计过程中的潜在故障和对电池管理系统性能的影响。
1. 制定DFMEA项目计划首先,制定DFMEA项目计划。
明确项目目标、参与人员和资源分配,确定每个阶段的时间表和里程碑。
2. 确定设计功能确定电池管理系统的设计功能,即系统需要实现的功能和性能指标。
例如,确保电池充电和放电过程的安全性、性能和效率。
3. 识别潜在故障模式通过团队讨论和技术文献调研,识别可能导致故障的潜在模式。
例如,电池温度过高、电池充电过程中的电流过大等。
4. 评估故障严重性对于每个潜在故障模式,评估其对电池管理系统性能的影响严重性。
根据影响的程度,分为低、中、高三个等级进行评估。
5. 评估故障原因和控制措施对于每个潜在故障模式,分析造成故障的原因,并制定相应的控制措施。
例如,对于电池温度过高的故障模式,可以通过安装温度传感器并设计合适的散热系统来控制温度。
6. 评估故障检测和容错措施对于每个潜在故障模式,评估故障的检测和容错措施。
例如,对于电池充电过流的故障模式,可以通过设计电流传感器和过流保护装置来检测和避免过大的电流。
7. 定义风险优先级根据故障严重性、故障概率和故障检测和容错措施的可靠性,定义每个故障模式的风险优先级。
优先级高的故障模式应该得到更加紧急的关注和处理。
8. 实施改进措施根据风险优先级,制定并实施相应的改进措施。
例如,对于优先级高的故障模式,可以进行重新设计、更换材料或改进生产工艺等。
9. 风险评估复审定期复审DFMEA,对已实施的改进措施进行评估和监控。
- 1、下载文档前请自行甄别文档内容的完整性,平台不提供额外的编辑、内容补充、找答案等附加服务。
- 2、"仅部分预览"的文档,不可在线预览部分如存在完整性等问题,可反馈申请退款(可完整预览的文档不适用该条件!)。
- 3、如文档侵犯您的权益,请联系客服反馈,我们会尽快为您处理(人工客服工作时间:9:00-18:30)。
内外压簧不能很好 给内外压簧设计
定位,有碰擦
定位结构
内外压簧之间间隙 根据内外压簧行
过小
程给出合理间隙
旋转配合位置摩擦 选择有自润滑性
系数太大
能的材料作为摩
高低温环境中,产 选擦 择副 合材 适料 的材
品变形
料,优化踏板结
灰尘进入导致摩擦 采用封闭构式结构
系数过大
材料选择不当
选择合适的材料
结构设计不合理 优化油门结构
扳手空间
间
验证
踏板安装孔位错误 3D验证
2 快速成型件 2
验证
油门踏板面 驾驶员误踩油 踏板的设计符 相对与刹车 门踏板
客户抱怨 7
合人体工程学 踏板位置正 驾驶员不能有
确
效快速切换油
客户抱怨 7
和整车安装 和整车配合有 支架完全配 间隙
踏板无法固定牢 靠
5
油门踏板面与 合理布置油门踏 2 快速成型件 2
7
驾驶员不容易稳 定踏板,驾驶员 6 脚容易脱离踏板
面
驾驶过程中感觉 不舒适
5
驾驶过程中感觉 不舒适,长时间 8
油门功能失效
发动机转速不能 下降,驾驶员无 10
法控制车辆
发动机转速不能 快速下降
7
G YS-3
灰尘进入导致摩擦 采用封闭式结构 系数过大
材料选择不当
选择合适的摩擦 材料
迟滞机构选择不合 设计合理的踏板
潜在失效模式及后果分析
系统
FMEA编号
子系统
(设计FMEA)
共
页第
页
电子油门
部件
车型年/车辆类型
核心小组
设计责任 关键日期
编制人 FMEA日期(编制)
(修订)
项目
功能 要求
潜在失效模式
严
失效的模式潜在 重
后果
度
S
级别
现有设计
潜在失效起因/机
理
现行设计控制预 防
频度O
现行设计控 制探测
措施结果
责任及
探测 度D
48
扰性能差
的结构和电路
不是需要的信 号
车辆行驶的速度 不符合驾驶员要 9 求,有安全隐患
高低温环境的影响 选用符合要求的 2 高低温存储 3
54
电子元器件
试验,高低
抗外界电气环境干 设计抗干扰性好 2
温EM循C试环验试 3
54
扰性能差
的结构和电路
线性度不符合要求 规定霍尔管在磁 2
初始性能 3
54
36
距离长
求得结构
评审。
踏板力太大
驾驶员踩踏不舒 适,驾驶员容易
产生疲劳 8
弹簧力偏高
设计合理弹簧力 2 设计计算, 3
48
值
评审。弹簧
高低温环境中,产 选择合适的材
2 材料检试测验, 4
64
品变形
料,优化踏板结
疲劳试验,
长时间使用,材料 选择合构适的材
2 材设料计试评验审, 4
64
摩损严重
料,优化踏板结
60 48 72 48 64 96 64 24 72 40 30 80 30 45 96 128 80 采用面接触
的方式产生 80 迟滞力,滑
块的材料采 90 用POM+PTFE 60 84 84
踏板自动回位
踏板回位速度
踏板能准确
慢
快速的回位
发动机转速不能 快速下降
7
YS-3
踏板在温湿度环境 选择耐高低温和 下材料性能改变 耐湿度的材料作 高低温环境中,产 为选迟择滞合机适构的材材料
阻燃
速率大
影响安全 10 G
材料选择不当 选择燃烧速率小 2
阻燃试验 3
60
的材料
扰性能差
的结构和电路
Z
踏板跌落造成元器 选用符合要求的
件损坏
电子元器件
4
元器件寿命低 选用符合要求的 3 电子元器件
接插件尺寸不合理 选择合理的配合 3 公差
EMC试验
3
48
跌落试验 3
96
疲劳试验 4
96
设计评审 2
48
有部分信号
ECU报错,车辆不 能正常行驶
8
踏板位置变化 产生信号变化
在踏板寿命 期内要保证 踏板旋转角 度内需要输 出满足客户 要求的信号
2 材料试验, 4
疲劳试验,
3 设粉计尘评试审验
3
2 材料试验, 3 振动试验
3 振动试验, 4 疲劳试验
2 设计评审, 4 疲劳试验
2 材料试验, 4 疲劳试验,
3 设材计料评试审验,, 3 疲劳试验,
2 设材计料评试审验,, 3 疲劳试验,
4 设设计计评计审算,, 3 评审,疲劳
3 试材验料试验, 4 疲劳试验, 设计评审,
受力试验,
材料选择不当
选择增根强部型尼龙 材料
2
材摆料式试冲验击, 3 CAE分析,承
踏板结构不合理 设计合理的加强 4 C受AE力分试析验,,承 4
踏板应有足够 踏板能承受 使用过程中踏 的强度 过大的踏力 板断裂
车辆不能行使 8
G
筋结构和合理的
受力试验,
材料选择不当 选择踏增板强形型状尼龙 2 材摆料式试冲验击, 4
不能快速响应 7
踏板力过小
驾驶员踩踏油门
没有力的感觉,
不易控制车辆速 度
9
踏板传动结构和磁 设计合理的间隙 2 初始性能试 2
28
钢配合间隙过大
公差
验,设计评
弹簧力偏小
设计合理弹簧力 2 设计计审算, 2
36
值
评审。弹簧
内外压簧其中一只 选择合适得弹簧 2 材料检试测验, 4
72
失效
参数及材料
回位疲劳试
疲劳试验,
踏点到旋转中心的 设计符合构客户要 2 设设计计计评算审, 3
54
距离短
求得结构
评审。
材料选择不当
选择合适的摩擦 2
材料试验 3
60
材料
迟滞机构的表面粗 规定合理的表面 2 设计计算, 3
60
糙度大
粗糙度要求
评审。表面
踏板回位不畅,
迟滞机构选择不合 设计合理的踏板 2 粗设糙计度计测算试, 2
Z
电子元器件没有被 设计封闭的结构
保护
保护电路
4
盐雾试试验验, 3 耐化学腐蚀
84
材料选择不当 选择要求的材料 2
材试料验试验 3
54
材料应符合环 踏板使用的 踏板材料回收
境要求和法律 材料方便回
困难
资源浪费 4
部件材料没有标识 在材料明显处增 1
设计评审 1
4
加材料标识
法规
踏板材料能 踏板材料燃烧
构
设计评审
板的感觉 适 ,没有
噪音,振动
小
驾驶员踩踏踏 板的感觉
踏板自动回位
踏板在寿命 期内保证驾 驶员踩踏舒 适 ,没有 噪音,振动
小
踏板能准确 快速的回位
迟滞力过小
踏板面滑
踏板工作有噪 音
油门踏板在行 驶过程中产生
共振发出响 声,
速
发动机转速不易 稳定,耗油。
40
迟滞力过大
可能发生驾驶员 想减速但不能减
10
理
迟滞结构,采用
Z 高低温环境中,产 面选接择触合的适方的式材产
2
评审。 材料试验, 4
80
踏板在寿命
速
品变形
料,优化踏板结
疲劳试验,
长时间摩擦使摩擦 选择合构适的材
2 材设料计试评验审, 4
80
期内保证驾
表面摩擦系数增大 料,优化踏板结
疲劳试验,
驾驶员踩踏踏 驶员踩踏舒
7
G
灰尘进入导致摩擦 采用封闭构式结构 系数过大
4 设粉计尘评试审验,, 初始性能试
4
使用过程中弹簧力 计算选择合适的 3 验材料试验, 3
值下降过快
弹簧参数及材料
疲劳试验,
有异物进入
采用封闭式结构 3 设设计计评评审审 4
装配困难或无
油门的可装配 油门组装方 法装配
性
便且正确
装配容易出错
踏板不能顺利
场中的位置
两路信号不同 步
ECU报错,车辆不 能正常行驶
8
高低温环境的影响 选用符合要求的 3 高低温存储 3
63
电子元器件
试验,高低
配合过紧导致两个 设计合理的定位 2 初温始循性环能试试 3
42
霍尔管安放的高度
结构
验,振动试
位磁置片不易一碎致 选择钐钴材料和 3
材料验试验 2
42
表面镀镍处理
信号迟滞
刹车踏板之间 板面与制动踏板
验证
油门踏板面与 合面理之布间置的油距门离踏 2 快速成型件 2
刹车踏板之间 板面与制动踏板
验证
底座的不平整
图面纸之上间规的定距底离座 3 安装力矩下 2
的平面度
降试验
油门踏板面 油门踏板回位 油门踏板容易与 相对与车厢 速度慢 车厢内壁碰擦产
7
油门踏板面与 合理布置油门与 2 快速成型件 2
踏板迟滞机构设计 设计合理的踏板
不合理
迟滞结构
踏板迟滞机构材料 选择有自润滑性
选择不合理 能的材料作为迟
踏板在温湿度环境 选择滞耐机高构低材温料和
下材料性能改变 耐湿度的材料作
高低温环境中,产 为选迟择滞合机适构的材材料
品变形
料,优化踏板结