半导体工艺第八章
半导体物理-第8章-半导体表面和MIS结构PPT课件

E fs
空穴势阱,多子空穴被吸引
Ev
至表面附近,因而表面空穴 浓度高于体内,形成多子积
(1)积累层(VG<0) 累,成为积累层。
(Vs<0) 表面微分电容
.
Cs
rs0
LD
exp2qkV0Ts
20
8.2.3 各种表面层状态
(2)平带状态
Ec
E fM
Ei
E fs
Ev
(2)平带(VG=0)
VG=0时,能带无弯曲,无空
LD
(
q2 pp0
1
)2
2rs0k0T
F (q,n V p 0 ) {[ q e) x V q p V 1 ] ( n p 0 [e q x ) V q p V 1 ( ]1 2 }
k 0 T p p 0
k 0 Tk 0 T p p 0 k 0 Tk 0 T
.
13
分别称为德拜长度 ,F函数。 则
2Vs
1/ 2
采用耗尽近似
Vs
.
q
N
A
.
15
带入可得
Qs 2rqs0L D k0TF(q k0TV s,n ppp00) 当金属电极为正,即Vs>0,Qs用负号; 反之Qs用正号。
.
16
在单位表面积的表面层中空穴的改变量 为
p0 (p pp p 0)d x0 p p 0 [e x k q 0 T p )V 1 (]dx
.
10
在半导体内部,电中性条件成立,故
(x)0
即
nD pA np0pp0
带入可得
d d 2 V 2x rq s 0{ p p 0 [e x k q 0 T p )V 1 ] ( n p 0 [ek q x 0 T )V p 1 ](}
半导体工艺教案第八章

第九章掺杂【教学内容及教学过程】8.1引言8.1.1刻蚀的概念刻蚀(Etching)是把进行光刻前所淀积的薄膜(厚度约在数百到数十纳米)中没有被光刻胶覆盖和保护的部分,用化学或物理的方式去除,以完成转移掩膜图形到薄膜上面的目的,如图8⁃1所示。
图8-1刻蚀图形转移示意图1)湿法刻蚀是利用合适的化学试剂将未被光刻胶保护的晶圆部分分解,然后形成可溶性的化合物以达到去除的目的。
2)干法刻蚀是利用辉光(Glow Discharge)的方法产生带电离子以及具有高浓度化学活性的中性原子和自由基,这些粒子和晶圆进行反应,从而将光刻图形转移到晶圆上。
8.1.2刻蚀的要求1.图形转换的保真度高2.选择比3.均匀性4.刻蚀的清洁8.2刻蚀工艺8.2.1湿法刻蚀最早的刻蚀技术是利用溶液与薄膜间所进行的化学反应,来去除薄膜未被光刻胶覆盖的部分,从而达到刻蚀的目的。
这种刻蚀方式就是湿法刻蚀技术。
湿法刻蚀又称湿化学腐蚀,其腐蚀过程与一般化学反应相似。
由于是腐蚀样品上没有光刻胶覆盖部分,因此,理想的腐蚀应当是对光刻胶不发生腐蚀或腐蚀速率很慢。
刻蚀不同材料所选取的腐蚀液是不同的。
1)湿法刻蚀的反应生成物必须是气体或能溶于刻蚀剂的物质,否则会造成反应生成物沉淀,从而影响刻蚀正常进行。
2)湿法刻蚀是各向异性的,刻蚀中腐蚀液不但浸入到纵向方向,而且也在侧向进行腐蚀。
3)湿法刻蚀过程伴有放热和放气过程。
1)反应物扩散到被刻蚀材料的表面。
2)反应物与被刻蚀材料反应。
3)反应后的产物离开刻蚀表面扩散到溶液中,随溶液被排除。
8.2.2干法刻蚀干法刻蚀是以等离子体来进行薄膜刻蚀的一种技术。
在干法刻蚀过程中,不涉及溶液,所以称为干法刻蚀。
1)物理刻蚀是利用辉光放电将气体(比如氩气)解离成带正电的离子,再利用偏压将带正电的离子加速,轰击在被刻蚀薄膜的表面,从而将被刻蚀物质的原子轰击出去。
2)化学刻蚀又叫做等离子刻蚀,它与物理刻蚀完全不同,它是利用等离子体,将反应气体解离,然后借助离子与薄膜之间的化学反应,把裸露在等离子体中的薄膜,反应生成挥发性的物质而被真空系统抽离。
半导体器件物理课件——第八章
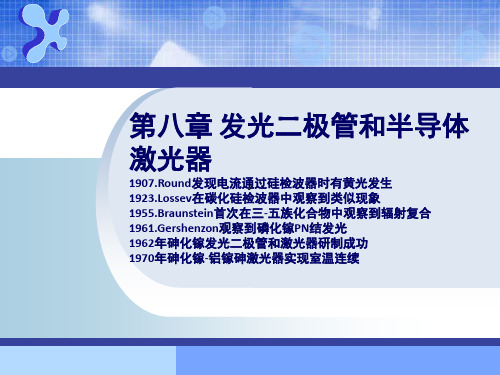
GaAs, n ,p 所30以它们是制造LE
8.3.2量子效率
2.辐射效率 • 发生辐射复合的电子数与总的注入电子数比:
r
Ur U r Unr
Ur
n
r
U nr
n
nr
r
1
1r
nr
r
(8-16) (8-17) (8-18) (8-19)
8.3.2量子效率
三种可能的复合过程
Ec
Et
R1
Ev
R3 浅施主能级Ed
8.1.1辐射复合
.带间辐射复合
带间辐射复合是导带中的电子直接跃迁到价带与价带中的空穴复合。发射的光子的能量接近等于半 导体材料的禁带宽度。
由于半导体材料能带结构的不同,带间辐射复合又可以分为直接辐射复合和间接辐射合两种:
导带
导带
价带
价带
图8-1 带间复合:(a)直接 能隙复合(b)间接能隙复合
8.1.1 辐射复合
8.3.2量子效率
• 1.注射效率
h
Eg
h > Eg Eg
h < Eg
(a)
(b)
图8-12 带尾对带带复合的影 响;(a)型,(b) 型
r
In
In I p Irec
8.3.2量子效率
注射效率就是可以产生辐射复合的二极管电流在二极管的总电流中所占的百 分比。
• 根据(8-15)式提高注射效率的途径是:
h
Eg
En exc
NEp
(8-8)
式中 NE表p 示吸收或放出能量为 的E p 个N声子。
8.1.1辐射复合
5.激子复合
束缚激子:
若激子对杂质的结合能为
E
,则其发射光谱的峰值为
半导体物理第八章

ρx =−
εrε0
=
−
q εrε0
⎡⎣
pp0
e−qV /k0T −1
− np0
eqV /k0T −1 ⎤⎦
(5)
上式两边乘dV并积分,可得
∫ ∫ [ ( ) ( )] dV dx
dV
d⎜⎛ dV
⎟⎞
=
−
q
0 dx ⎝ dx ⎠ ε rε0
V 0
p p0 e−qV / k0T −1 − n p0 eqV / k0T −1 dV
3、VG > 0,表面处Ei与EF重合,表面本征型
E VG > 0
MI S
Ec Ei
++++++++++
EF
Ev
nS = ni exp[(ESF − Ei )/ kT] pS = pi exp[(Ei − ESF )/ kT]
表面处于本征型, VS >0.
pS = nS = ni
4、VG >>0,表面反型
VG-VT 由绝缘层承受。 ¾应用:MOSFET(MOS场效应晶体管)
¾ 前面讨论的是空间电荷区的平衡态,VG不变或者变化 速率很慢,空间电荷区载流子浓度能跟上VG的变化。
¾ 以下讨论非平衡状态-深耗尽状态, VG为高频信号或 者阶跃脉冲,空间电荷区少子来不及产生和输运。
5、VG >>0,加高频或脉冲电压,表面深耗尽。
¾深耗尽和反型是同一条件下不同时间内的表面状况 ¾深耗尽状态的应用:制备CCD等。
6、平带VS=0
对理想MIS结构VS=0时,处于平带。
8.2.2 表面空间电荷层的电场、电势和电容
第八章 半导体表面解析

第八章半导体表面§8-1 表面态与表面空间电荷区1. 表面态:在半导体表面,晶体的周期性遭破坏,在禁带中形成局域状态的能级分布,这些状态称为表面态;当半导体表面与其周围媒质接触时,会吸附和沾污其他杂质,也可形成表面态;另外,表面上的化学反应形成氧化层等也是表面态的形成原因。
2.施主表面态、受主表面态和复合中心表面态:当表面态起施主作用时称施主表面态,起受主作用时称受主表面态,起复合中心作用时则称复合中心表面态。
3.表面电荷和表面空间电荷区:半导体表面具有的施主态,可能是中性的,也可能向导带提供电子后成为正电荷,此时半导体表面也带正电荷。
反之,如果表面态为受主态时,半导体表面则可能带负电荷。
这些电荷称表面电荷,一般用Q ss表示。
表面电荷Q ss与表面态密度N s及表面态能级E s上的电子分布函数有关。
在热平衡条件下,半导体整体是电中性的。
表面电荷Q ss的存在使表面附近形成电场,从而导致表面附近的可动电荷重新分布,形成空间电荷Q sp,其数量与表面电荷相等,但带电符号相反,即有Q sp=-Q ss,以保持电中性条件。
表面空间电荷存在的区域称表面空间电荷区。
在半导体中,由于自由载流子的密度较小(和金属比),因此空间电荷区的宽度一般较大。
如:对表面能级密度为1011cm-2,载流子密度为1015cm-3的Ge,其空间电荷区的宽度约为10-4cm。
而对本征Ge,n i约为1013cm-3,其空间电荷区的宽度可达0.1cm。
半导体表面空间电荷区的存在,将使表面层的能带发生弯曲。
下面以具有受主型表面态能级E as的n型半导体为例,分析表面空间电荷区的形成。
如图8.1a所示,当电子占据受主型表面能级时,半导体表面产生负表面电荷,而在表面附近由于缺少电子而产生正表面空间电荷,从而在空间电荷区产生指向半导体表面的电场,引起表面区附近的能带向上弯曲。
如果用eV s表示表面区能带弯曲量,则V s为表面势。
第八章半导体表面与MIS结构
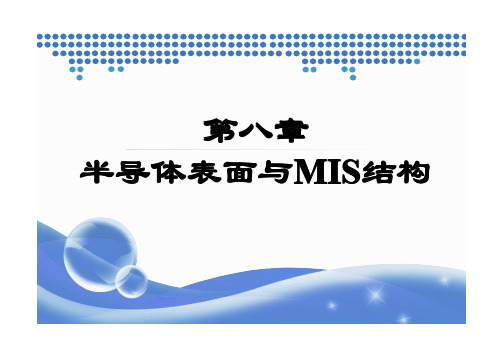
以简化为F ( qVs ,n p0 ) ≈ exp(− qVs )
k0T p p0
2k0T
x
所以:
Es
=
− 2k0T qLD
exp(−
qVs ) 2k0T
Qs
=
2ε rsε 0k0T qLD
exp(−
qVs 2k0T
)
Cs
=
ε T
)
此时,ES、QS、CS随VS按指数规律增大。
Es
=
2k0T qLD
(
qVs
)
1 2
k0T
=
2 LD
(
k0TVs
)
1 2
q
+
于是有:
Qs
=
− 2ε rsε 0k0T qLD
( qVs k0T
1
)2
=
−
2ε rsε 0 LD
(
k0TVs
)
1 2
q
+ +
--
M ++ I - -
P- S
+ +
--
-
Cs
=
ε rsε 0 LD
(
qVs
1 −
)2
2k0T
MI
P-S
(EF )M
EC
(EF)s EV
二、空间电荷区的几种类型
3).多子的耗尽状态
+ +
--
+
M
+ +
I --
+ +
--
P-S
-
VG>0, VS>0,
即表面电子能量比体内电子能量低 ,表面能带向下弯曲,表面处的空 穴浓度比体内低得多。
半导体8 半导体材料制备
基本原理
籽晶杆及其传动组件; 坩埚杆及其传动组件; 进气、排气系统; 功率加热系统;
直pter 8
盛于(石英)坩埚中多晶硅被(电阻)加热熔化,待 其温度在熔点附近并稳定后,将籽晶浸入熔体,并与 其熔接好后以一定速度向上提拉籽晶(同时旋转)引 出晶体(即引晶)。生长一定长度的细颈(细颈以防 籽晶中位错延伸到晶体中),经过“放肩”,“转肩” (晶体逐渐长大到所需直径),等(直)径生长,收 尾,降温,就完成一根单晶锭的拉制。
用一种惰性液体(覆盖 剂B2O3)覆盖着被拉制 材料的熔体,生长室内 冲入惰性气体,使其压 力大于熔体的离分压力, 以抑制熔体中挥发性组 元的蒸发损失,然后按 CZ拉制。
覆盖剂必须满足的条件:
密度小于所拉制材料,使之能浮于熔体表面;
对人体和坩埚在化学上必须是惰性的,不能与熔 体混合,但必须浸润晶体及坩埚; 熔点要低于被拉制材料的熔点,且蒸气压很低; 有较高纯度,熔融状态下透明。 B2O3: 密度1.8g/cm2、软化点450℃、
3. 组分过冷 重掺杂情况下,且K<1,生长过程中杂质不断 “排”向熔体,使熔体中杂质浓度越来越高,从 而造成熔体内部的过冷度大于扩散层附近熔体过 冷度,,而且离固液界面越远,过冷度越大,这 将使固液界面不稳定,甚至导致枝蔓生长。
降低杂质浓度,提高温度梯度,降 低结晶速度,防止发生组分过冷
4、多晶硅 由砂即(二氧化硅)开始,经由电弧炉的 提炼还原成 冶炼级的硅,再经由盐酸氯 化,产生三氯化硅,经蒸馏纯化后,透 过慢速分 解过程,制成棒状或粒状的多 晶硅。
RCA1 RCA2
5H2O : 1H2O2 : 1NH4OH 有机物 5H2O : 1H2O2 : 1HCl 金属离子
七、晶片的几何参数和参考面
半导体物理第八章 半导体表面和MIS结构
qN A xd2
2 rs 0
Cs
rs 0
xd
返回
8.1 表面电场效应 8.1.3 各种表面层状态下的电容情况
对于耗尽状态,空间电荷区也可以用“耗尽层近似”
来处理,即假设空间电荷区内所有负电荷全部由电
离受主提供,对于均匀掺杂的半导体,电荷密度为:
x qNA
代入泊松方程求解,得到:
电势分布 V qNAxd x2表面势
q 2 rs0k0T
k0T k0T
pp0
k0T k0T
令
1/ 2
LD
2 rs0k0T
q2 pp0
F( qV
,
np0 ) {[exp(
qV
)
qV
1]
np0
[exp( qV
)
qV
1
1]} 2
k0T pp0
k0T k0T
pp0
k0T k0T
12 3 4
8.1 表面电场效应 8.1.2 表面空间电荷层的电场、电势和电容
②强反型层出现的条件:当P型衬底表面处的电子浓 度等于体内的多子空穴浓度时。
Ec
ns
ni
exp
E f Eis kT
Ef
Ei0 Ef
p0
ni
exp Ei0 E f kT
Eis
Ev
p0 ns
Ef
Eis
Ei0 E f
qVB qVs
Ei0 Eis
2qVB
此时表面势为:Vs 2VB
分别称为德拜长度 ,F函数。 则
E 2k0T F ( qV , np0 ) qLD k0T pp0
式中当V大于0时,取“+”号;V小于0时, 取“-”号。
半导体材料第8章III--VV族多元化合物半导体
吉林大学电子科学与工程学院
半导体材料
超晶格 : 由两种(或两种以上)组分(或导电类 型)不同、厚度d极小的薄层材料交替生长在一起 而得到的一种多周期结构材料。
厚度d远大于材料的晶格常数a,但相近与或小于 电子的平均自由程
衬底
这是在原来“自然”晶体晶格的周期性结构上又叠 加了一个很大的“人工”周期的新型人造材料。
吉林大学电子科学与工程学院
半导体材料
c) 电价因素
连续固溶体必要条件:原子价(或离子价)相同 多组元复合取代总价数相等,电中性。 ( 不是充 分条件) ¾ 电负性相近,有利于固溶体的生成 ¾ 电负性差别大,倾向于生成化合物 如果价态不同,则最多只能生成有限固溶体(满 足尺寸条件前提下)
吉林大学电子科学与工程学院
使用四元固溶体可增加一个对其主要性能进行调 整和裁剪的自由度,即可通过两种组元的组分改 变来调整其带隙和晶格常数。
吉林大学电子科学与工程学院
半导体材料
从 图 上 可 知 : 与 InP 晶 格 (0.5869nm) 相 匹 配 的 该固溶体的带隙可在 0.74~1.35eV之间调整
吉林大学电子科学与工程学院
吉林大学电子科学与工程学院
半导体材料
三元固溶体:
Vegard定律
晶格常数
aAB=xaA+(1-x)aB aA和aB分别为互溶材料A和B的晶格常数 带隙宽度
Eg,AB= a+bx+cx2 其中,a,b,c为特定固溶体材料的特征常数
吉林大学电子科学与工程学院
半导体材料
固溶体晶格常数随组分变化
晶格常数 a (nm)
吉林大学电子科学与工程学院
半导体材料
E(k)
3.0
芯片制造-半导体工艺教程
芯片制造-半导体工艺教程芯片制造-半导体工艺教程芯片制造-半导体工艺教程Microchip Fabrication ----A Practical Guide to Semicondutor Processing 目录:第一章:半导体工业第二章:半导体材料和工艺化学品第三章:晶圆制备第四章:芯片制造概述第五章:污染控制第六章:工艺良品率第七章:氧化第八章:基本光刻工艺流程-从表面准备到曝光第九章:基本光刻工艺流程-从曝光到最终检验第十章:高级光刻工艺第十一章:掺杂第十二章:淀积第十三章:金属淀积第十四章:工艺和器件评估第十五章:晶圆加工中的商务因素第十六章:半导体器件和集成电路的形成第十七章:集成电路的类型第十八章:封装附录:术语表1芯片制造-半导体工艺教程#1 第一章半导体工业--1芯片制造-半导体工艺教程点击查看章节目录by r__ 概述本章通过历史简介,在世界经济中的重要性以及纵览重大技术的发展和其成为世界领导工业的发展趋势来介绍半导体工业。
并将按照产品类型介绍主要生产阶段和解释晶体管结构与集成度水平。
目的完成本章后您将能够:1. 描述分立器件和集成电路的区别。
2. 说明术语D固态,‖ D平面工艺‖,DDN‖‖型和DP‖型半导体材料。
3. 列举出四个主要半导体工艺步骤。
4. 解释集成度和不同集成水平电路的工艺的含义。
5. 列举出半导体制造的主要工艺和器件发展趋势。
一个工业的诞生电信号处理工业始于由Lee Deforest 在1906年发现的真空三极管。
1真空三极管使得收音机, 电视和其它消费电子产品成为可能。
它也是世界上第一台电子计算机的大脑,这台被称为电子数字集成器和计算器(ENIAC)的计算机于1947年在宾西法尼亚的摩尔工程学院进行首次演示。
这台电子计算机和现代的计算机大相径庭。
它占据约1500平方英尺,重30吨,工作时产生大量的热,并需要一个小型发电站来供电,花费了1940年时的400, 000美元。
- 1、下载文档前请自行甄别文档内容的完整性,平台不提供额外的编辑、内容补充、找答案等附加服务。
- 2、"仅部分预览"的文档,不可在线预览部分如存在完整性等问题,可反馈申请退款(可完整预览的文档不适用该条件!)。
- 3、如文档侵犯您的权益,请联系客服反馈,我们会尽快为您处理(人工客服工作时间:9:00-18:30)。
8-1超大规模集成电路对图形转换有哪些要求?
答:
(1)图形转换的保真度高
在刻蚀时,通常在纵向刻蚀时,也会有横向(侧向)刻蚀,但这种横向刻蚀在工艺中是不希望出现的。
因此,在工艺中,就要严格控制这种侧向刻蚀,使之越小越好。
(2)选择比
刻蚀时,光刻胶和衬底在刻蚀过程中不参与反应,也就是说不会被刻蚀。
但事实上,光刻胶与衬底,在整个刻蚀过程中,也会参与反应,也会被刻蚀掉部分。
这种现象是不希望出现的。
因此,在刻蚀过程中,要求光刻胶和衬底的刻蚀速率十分缓慢。
(3)均匀性
现在商业化生产的晶圆直径往往大于12英寸,而且刻蚀的是≤1mm的微细图形。
这种大直径硅片上的薄膜厚度一旦不均匀,就会引起刻蚀速率的不均匀,将直接导致图形转移的不均匀性。
而且随着晶圆直径的增大,这种不均匀性就会越来越明显。
(4)刻蚀的清洁
超大规模集成电路的图形非常精细,在刻蚀过程中,任何人为引入的污染,既影响到图形转移的精度,又增加刻蚀后清洗的复杂性。
8-2湿法刻蚀有哪些特点?
答:
(1)湿法刻蚀的反应物必须是气体或能溶于刻蚀剂的物质,否则会造成反应物沉淀,从而影响刻蚀正常进行。
(2)湿法刻蚀是各向异性的,刻蚀中腐蚀液不但浸入到纵向方向,而且也在侧向进行腐蚀。
这样腐蚀后得到的图形结构像一个倒八字形,而不是理想的垂直墙。
(3)湿法刻蚀过程伴有放热和放气过程。
放热造成刻蚀局部温度升高,引起化学反应速率增加,一旦温度剧烈增加,又反过来使刻蚀处于不受控制的恶性循环中,使得刻蚀效果变差。
8-3分别阐述SiO2和Si3N4膜的湿法刻蚀原理及刻蚀液配方。
答:
(1)二氧化硅的湿法刻蚀
腐蚀液:氢氟酸和氟化氨的混合液
原理:溶液中的F-与二氧化硅中的Si4+络合成六氟硅酸根络离子(SiF6)-2,它与H+结合而生成可溶性的六氟硅酸。
反应原理:
SiO2+6HF H2[SiF6]+2H2O
(2)氮化硅的湿法刻蚀
•氢氟酸对氮化硅的腐蚀速度比二氧化硅慢得多,而磷酸则容易腐蚀氮化硅。
•所以常用热磷酸作为氮化硅的腐蚀剂。
•化学反应原理:
Si3N4+H3PO4 Si(H2PO4)4+NH3
8-4用湿法刻蚀二氧化硅时,为什么要添加NH4F?
答:因为用氢氟酸腐蚀二氧化硅时,反应过程较为剧烈,会影响刻蚀的均匀性,因此可以添加NH4F溶液作为缓冲剂,因为NH4F在水中电离为F+会使得刻蚀过程向相反的方向进行,从而减小刻蚀速率,以提高刻蚀的均匀性。
所以氟化氨起缓冲的作用。
8-5阐述干法刻蚀的原理。
答:干法刻蚀是以等离子体来进行薄膜刻蚀的一种技术。
在干法刻蚀过程中,不涉及溶液的参与,所以称为干法刻蚀。
干法刻蚀可分为物理刻蚀和化学刻蚀。
物理刻蚀是利用辉光放电将气体(比如氩气)解离成带正电的离子,再利用偏压将带正电的离子加速,轰击在被刻蚀薄膜的表面,从而将被刻蚀物质的院子轰击出去。
化学刻蚀又叫做等离子刻蚀,它与物理刻蚀完全不同,它是利用等离子体,将反应气体解离,然后借助离子与薄膜之间的化学反应,把裸露在等离子体中的薄膜,反应生成挥发性的物质而被真空系统抽离。
8-6干法刻蚀有哪几种刻蚀方法?各有何特点?
答:干法刻蚀有溅射刻蚀、化学刻蚀和反应离子刻蚀三种;
溅射刻蚀时一种纯物理轰击刻蚀,选择各向异性好,但选择性差;
化学刻蚀选择性好,但是是一种各向同性刻蚀;
而反应离子刻蚀结合了物理轰击和化学反应两者优点,选择性好,各向异性也较好。
8-7干法刻蚀有哪些优点?
答:干法刻蚀最大的优点就是刻蚀时是一种各向异性刻蚀。
8-8阐述SiO2、Si3N4、多晶硅、金属铝膜的干法刻蚀原理、刻蚀气体及刻蚀过程。
答:(1)SiO2的刻蚀
从早期的干法刻蚀技术的应用到现在,大都采用含有氟碳化合物的等离子体来进行SiO2的干法刻蚀。
所使用的气体,从早期的四氟化碳(CF4)到现在的CHF3,或是C2F6和C3F8,都可以作为提供碳原子及氟原子的反应气体。
以CF4为例介绍SiO2的刻蚀,其反应式如下:
CF4 2
SiO2+4F SiF2+2O
Si+4F SiF4
SiO2+2CF2 SiF4+2CO
这些反应就把SiO2的Si原子和F原子生成具有挥发性的SiF4。
(2)Si3N4的刻蚀
基本上,用来刻蚀SiO2的干法刻蚀方法都可以用来刻蚀Si3N4膜,但是由于Si—N键的键结合强度介于Si—O键与Si—Si之间,因此,若采用CF4或是其他含氟的气体等离子体来进行Si3N4的刻蚀,其选择性比较差。
以CHF3的等离子体为例,其对SiO2与Si的刻蚀选择性在10以上,但是对Si3N4与Si的选择性则只有3~5,对Si3N4与SiO2的选择性仅在有2~4之间。
近期采用以NF3
为主的等离子体来进行Si 3N 4的刻蚀,通过对气体组分的控制,Si 3N 4的选择性将可以提高到比较能接受的程度。
反应过程如下:
NF 3 N 2+F
Si 3N 4+F SiF 4+N 2
(3)多晶硅的刻蚀
工艺中常采用Cl 2来作为Si 3N 4的刻蚀,其会提供比氟原子好的多的各项异性腐蚀,除了Cl 2,还可以是HCl 、SiCl 4等。
使用含氯气体刻蚀多晶硅还有一个好处是,因为氯所形成的等离子体对Si 和SiO 2刻蚀的选择性都比较好。
Cl 2与多晶硅的反应式如下:
Cl 2 2Cl
Si+2Cl SiCl 2
SiCl 2+2Cl SiCl 4
(4)金属铝膜的刻蚀
氟化物不适合铝的刻蚀,因为所形成的化合物AlF 3的挥发性很低,目前大都采用氯化物,如SiCl 4、CCl 4等气体与氯气混合气体来进行刻蚀。
铝和氯反应生成具有挥发性的三氯化铝(AlCl 3),随着腔内气体被抽干。
一般铝的刻蚀温度比室温稍高,三氯化铝的挥发性更好,可以减少残留物。
铝的等离子体刻蚀原理如下: 2Al(s)+3Cl 2(g) 2AlCl 3
上述反应中所生产的AlCl 3具有挥发性,随气体逸出。
需要注意的是,铝很容易和空气中的氧或水汽反应,形成大约3~5nm 厚的氧化铝层。
此氧化铝层化学性质不活泼,隔绝了氧和铝的接触,保证铝不再被氧化。
另一方面,在铝的刻蚀初期,这一层氧化膜同样也隔绝了氯与铝的接触,阻碍了刻蚀的进行。
所以铝的初期刻蚀也要分两个步骤进行:先把表面的Al 2O 3膜去掉,然后再刻蚀铝。
8-9如何用湿法方式进行去胶?
答:工艺中通常可以采用溶剂和氧化两种湿法方式进行去胶。
1.溶剂去胶
把带有光刻胶的硅片浸在适当的溶剂内,使聚合物膨胀,然后把胶去除,称为溶剂去胶。
去胶剂一般是含有氯的烃化物,如三氯乙烯等。
这些化合物含有较多的无机杂质,因此会在衬底表面留下微量杂质,在制备MOS 器件时,会引起不良后果。
另外,其洗涤周期长,操作较麻烦,故很少采用。
这种方法的优点是在常温下进行,不会使铝层发生变化。
2.氧化去胶
氧化去胶是指利用氧化剂把光刻胶去掉。
这种方法使用十分普遍,也成为湿法去胶。
常用的氧化剂为硫酸。
它使光刻胶中的碳被氧化而析出来。
但是,碳的析出会影响硅片的表面质量,因此,通过在硫酸中加入双氧水(H 2O 2),使碳氧化成CO 2析出。
典型的氧化去胶的去胶液的配方是:H 2SO 4:H 2O 2=3:1。
也有人用硫酸和重铬酸钾配合使用。
8-10阐述等离子体去胶原理及过程。
答:等离子体去胶是近几年发展起来的一种新的去胶工艺。
它不需要化学试剂,也不需要加温,因此,器件的结特性和铝层都不会受到影响,这对提高产品质量和器件可靠性有好处。
在干法去胶系统中,外加的高频电磁场使通入石英管中的氧在高频电场作用下电离,形成等离子区。
其中,活化的原子态氧,约占10%~20%,它们活性活泼、氧化能力强,将与光刻胶发生反应,使之变成CO2、CO、H2O和其它挥发性氧化物而被机械泵排出,达到去胶的目的。