轧机弯辊液压系统的仿真研究
热轧带钢卷取机的工艺研究及液压系统仿真的开题报告

热轧带钢卷取机的工艺研究及液压系统仿真的开题报告一、课题背景及意义随着钢材生产技术的不断发展,热轧带钢已经成为了钢铁工业中的重要材料,广泛应用于建筑、机械、航空、车辆等领域。
在热轧带钢生产过程中,卷取机是关键设备之一,其性能的稳定与否,直接影响到产量和质量。
因此,热轧带钢的卷取机工艺研究和液压系统仿真成为研究的热点。
二、研究内容和目标1. 热轧带钢卷取机的工艺研究:根据卷取机的工作原理和要求,分析卷取机的工艺特点,包括卷取机的动力系统、控制系统、验收标准等,以及其与整个热轧生产线的关系;2. 液压系统仿真研究:通过对液压系统的建模和仿真,研究液压系统性能的优化,提高系统稳定性和可靠性,同时减少系统能量损失,降低生产成本。
三、研究方法1. 热轧带钢卷取机的工艺研究:采用文献研究和实地考察相结合的方法,分析卷取机的结构和原理,调研卷取机的应用及维护情况,并对其进行性能测试;2. 液压系统仿真研究:建立液压系统的数学模型,并利用MATLAB/Simulink等仿真软件进行仿真研究,通过调整系统参数来优化系统性能。
四、研究成果及预期效果1. 热轧带钢卷取机的工艺研究达到技术标准,为生产提供技术支持,提高生产效率和产品质量,降低生产成本;2. 液压系统仿真研究优化系统性能,提高系统的工作效率和稳定性,实现能源节约,减少生产成本。
五、研究计划1. 前期准备:文献研究、实地考察,了解卷取机的基本工作原理和要求,准备相关实验设备和软件;2. 实验研究:对卷取机进行各项性能测试,收集数据资料;建立液压系统模型,进行仿真测试,分析仿真结果,优化系统性能;3. 结果分析与总结:对实验数据进行流程控制方面的分析,对液压系统仿真结果进行优化;对得出的结论进行总结、评价和比较分析。
六、预期的研究经费来源1. 学校在相关科研计划中安排的经费;2. 企业合作资助。
精轧机弯辊系统液压故障分析与控制

精轧机弯辊系统液压故障分析与控制摘要:工作辊弯辊系统是热轧带钢厂精轧机组的重要组成部分,用于对工作辊提供液压弯辊力,平衡上工作辊重量,消除工作辊和支承辊间隙;它与窜辊系统配合工作,实现带钢凸度和平直度控制。
本文以首钢某热轧2250生产线为对象,详细介绍了工作辊弯辊机械结构和液压控制原理;对生产过程中出现的液压弯辊力突变,从液压故障和轧辊受力进行了详细分析,并提出针对性控制措施。
关键词:弯辊;液压;故障;控制措施0 引言首钢某2250热轧带钢生产线采用半连续式热轧带钢轧机,其中机械介质部分为德国西马克公司整体初步设计,并由首钢国际设计转化,采取进口设备和国内设备制造相结合。
其精轧机为六机架连轧,每架轧机均设计有CVC shifting system(凸度控制系统),即工作辊液压弯辊和窜辊板型控制系统。
液压弯辊用于对工作辊产生弯辊力,平衡上工作辊重量,消除工作辊和支承辊间隙,以实现精轧带钢凸度和平直度控制。
液压弯辊板型控制系统属于电液伺服力控制系统,它具有精度高、响应速度块、功率大、结构紧凑和使用方便等优点,因此得到广泛应用[1]。
2250热轧线自投产以来,精轧多次出现液压弯辊力异常,造成生产线停机。
统计显示,精轧弯辊液压故障,约占该厂精轧液压总停机故障的80-85%,成为了困扰生产稳定的较大隐患,急需攻关解决。
1工作辊弯辊结构原理1.1弯辊机械结构每台精轧机安装有四台工作辊弯辊缸,分别布置在传动侧和操作侧牌坊入口和出口。
操作侧弯辊缸与窜辊缸和工作辊锁紧缸集成在一起;传动侧弯辊缸与轴头抱紧缸集成在一起。
弯辊缸缸杆直接作用在工作辊耳座上镶嵌的铜滑板上,实现上下工作辊弯辊、平衡和压紧功能。
1.2 工作辊弯辊液压控制原理工作辊弯辊液压回路由精轧高压液压系统供油,进油压力为290ba。
四台弯辊缸的有杆腔相互联通,由比例减压阀组控制;两侧弯辊缸无杆腔由各自的伺服阀和比例阀组进行控制,其控制模式分为:轧钢模式和换辊模式。
基于神经网络PID控制的轧机液压弯辊系统研究
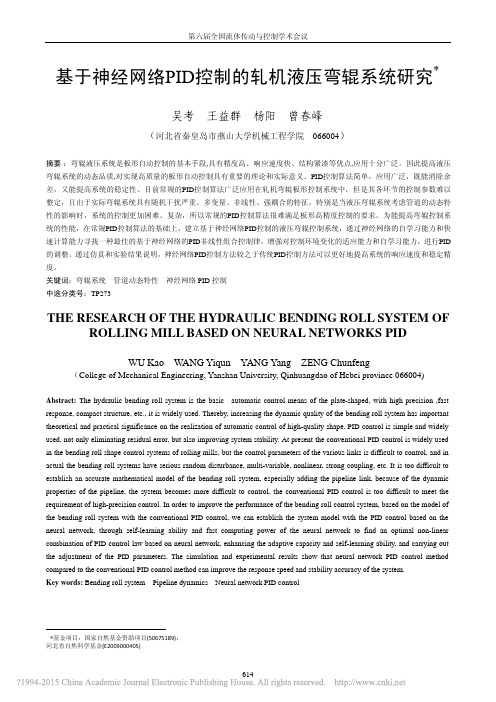
sh [ Γ( s)] Zc (s)
ch [ Γ( s)]
、
设
∂E ( k ) ∂Yout ∂V = −δ ' ,由(5)式可得: " ∂Yout ∂V ∂netl
∂netl" = w"jl ' ∂O j
(12)
u21 =
sh [ Γ( s)] Z c ( s) 1 u22 = ch[Γ( s)] 、 ch [ Γ( s ) ]
E (k ) ≤ ε
(9)
ε 为目标误差值,按照梯度下降法修正网络的
权系数,即按 E ( k ) 对加权系数的 Z 负梯度方向搜 索调整。 设在 k 时刻,经过神经网络 PID 控制器后的输 出为 V ( k ) 。输入层到隐含层的权值更新公式为:
' ' wij (k + 1) = wij (k ) − η
Abstract: The hydraulic bending roll system is the basic automatic control means of the plate-shaped, with high precision ,fast response, compact structure, etc., it is widely used. Thereby, increasing the dynamic quality of the bending roll system has important theoretical and practical significance on the realization of automatic control of high-quality shape. PID control is simple and widely used, not only eliminating residual error, but also improving system stability. At present the conventional PID control is widely used in the bending roll shape control systems of rolling mills, but the control parameters of the various links is difficult to control, and in actual the bending roll systems have serious random disturbance, multi-variable, nonlinear, strong coupling, etc. It is too difficult to establish an accurate mathematical model of the bending roll system, especially adding the pipeline link, because of the dynamic properties of the pipeline, the system becomes more difficult to control, the conventional PID control is too difficult to meet the requirement of high-precision control. In order to improve the performance of the bending roll control system, based on the model of the bending roll system with the conventional PID control, we can establish the system model with the PID control based on the neural network, through self-learning ability and fast computing power of the neural network to find an optimal non-linear combination of PID control law based on neural network, enhancing the adaptive capacity and self-learning ability, and carrying out the adjustment of the PID parameters. The simulation and experimental results show that neural network PID control method compared to the conventional PID control method can improve the response speed and stability accuracy of the system. Key words: Bending roll system Pipeline dynamics Neural network PID control
1500型粗轧机AWC液压系统的建模与控制研究

分类号密 级U D C学位论文1500型粗轧机AWC液压系统的建模与控制研究作者姓名:石磊指导教师:张志伟副教授东北大学液压与气动技术研究所申请学位级别:硕士学科类别:工学学科专业名称:机械电子工程论文提交日期: 2007年1月18日论文答辩日期:2007年2月28日学位授予日期:答辩委员会主席:评阅人:东北大学2007年2月A Thesis for the Degree of Master in Mechanical &Electronic EngineeringStudy on the Control and Modeling of the 1500 Rough Rolling Mill AWC Hydraulic Systemby Shi LeiSupervisor : Vice professor Zhang ZhiweiNortheastern UniversityFebruary 2007独创性声明本人声明所呈交的学位论文是在导师的指导下完成的。
论文中取得的研究成果除加以标注和致谢的地方外,不包含其他人已经发表或撰写过的研究成果,也不包括本人为获得其他学位而使用过的材料。
与我一同工作的同志对本研究所做的任何贡献均已在论文中作了明确的说明并表示诚挚的谢意。
学位论文作者签名:签字日期:学位论文版权使用授权书本学位论文作者和指导教师完全了解东北大学有关保留、使用学位论文的规定:即学校有权保留并向国家有关部门或机构送交论文的复印件和磁盘,允许论文被查阅和借阅。
本人同意东北大学可以将学位论文的全部或部分内容编入有关数据库进行检索、交流。
(如作者和导师同意网上交流,请在下方签名:否则视为不同意)学位论文作者签名:导师签名:签字日期:签字日期:东北大学硕士学位论文摘要1500型粗轧机AWC液压系统的建模与控制研究摘要自动宽度控制技术是提高板带材的质量,降低板带材的成本的重要手段,而诸如模糊控制等现代控制理论的发展,使现代控制理论在轧机宽度控制系统中的应用具有很强实际意义和工程使用价值。
液压仿真系统实验结论

液压仿真系统实验结论
液压仿真系统是一种模拟液压系统运行的实验设备,通过对液压系统的仿真模拟,可以更好地理解液压系统的工作原理和性能特点。
在进行液压仿真系统实验时,我们得出了以下结论:
1. 液压系统的压力控制能力较强。
在实验中,我们通过调节液压系统的压力控制阀,可以实现对液压系统的压力进行精确控制。
这表明液压系统在工业生产中可以实现对压力的精确控制,从而保证生产过程的稳定性和可靠性。
2. 液压系统的流量控制能力较弱。
在实验中,我们发现液压系统的流量控制能力较弱,难以实现对流量的精确控制。
这表明在液压系统的设计和应用中,需要考虑到流量控制的问题,采取相应的措施来提高液压系统的流量控制能力。
3. 液压系统的能量损失较大。
在实验中,我们发现液压系统的能量损失较大,主要是由于液压系统中的摩擦、泄漏等因素导致的。
这表明在液压系统的设计和应用中,需要采取相应的措施来减少能量损失,提高液压系统的能效性能。
4. 液压系统的稳定性较好。
在实验中,我们发现液压系统的稳定性较好,可以实现对液压系统的稳定控制。
这表明液压系统在工业生产中可以实现对生产过程的稳定控制,从而保证生产过程的稳定性和可靠性。
液压仿真系统实验结论表明液压系统具有压力控制能力较强、流量控制能力较弱、能量损失较大、稳定性较好等特点。
在液压系统的设计和应用中,需要考虑到这些特点,采取相应的措施来提高液压系统的性能和效率。
E2轧机AWC液压控制系统的建模仿真与校正的开题报告

E2轧机AWC液压控制系统的建模仿真与校正的开题报告一、选题背景E2轧机是钢铁冶金工业中重要的生产设备,在钢材生产流程中的作用至关重要,主要用于钢坯的加工和成型。
而AWC液压控制系统是E2轧机中的一项重要的技术创新,它能够通过对轧辊钢坯间隙的调节,实现对轧制过程中的力学参数进行控制,保证轧制出来的钢材质量。
目前,AWC液压控制系统的建模仿真与校正仍然存在一些问题,因此需要开展深入的探讨和研究。
本研究将以E2轧机AWC液压控制系统为研究对象,旨在通过建立AWC 液压控制系统的数学模型,并进行仿真和校正来优化系统的性能,提高钢坯轧制质量。
二、研究内容1、AWC液压控制系统的原理和机构分析;2、AWC液压控制系统的数学模型建立;3、AWC液压控制系统的仿真与分析;4、AWC液压控制系统的校正和优化。
三、研究方法1、系统分析和试验研究相结合,深入了解AWC液压控制系统的原理和机构;2、采用建立数学模型的方法,对AWC液压控制系统进行描述和分析;3、利用仿真软件进行AWC液压控制系统的建模仿真,分析系统的性能;4、采用实验研究和校正方法,对仿真结果进行验证和优化。
四、预期结果1、建立AWC液压控制系统的数学模型,描述系统的动态性能;2、通过仿真分析,评估系统的控制性能;3、利用实验研究和校正方法,对仿真结果进行验证和优化;4、提高AWC液压控制系统的控制性能,提高钢坯轧制质量。
五、研究意义1、提高E2轧机AWC液压控制系统的控制精度,提高钢坯轧制质量;2、为钢铁冶金行业的科学发展提供技术支持;3、为相关领域的研究开展提供参考依据。
六、进度安排1、第一阶段:系统分析(1个月);2、第二阶段:建模分析(2个月);3、第三阶段:仿真分析(3个月);4、第四阶段:实验校正(2个月);5、第五阶段:论文撰写(2个月)。
七、参考文献1. 蔡明志. 电液伺服混合控制技术在AWC系统中的应用研究[J]. 机床与液压, 2015.2. 周冬, 徐云涛, 张宏峰. 基于改进LQG控制的E2轧机AWC液压系统仿真[J]. 中国金属学报, 2014.3. 马琦, 张继勇, 李伟, 等. 基于MATLAB的AWC系统仿真[J]. 机床与液压, 2013.4. 肖俊. 基于小波切换策略的AWC系统仿真研究[J]. 机械工程与自动化, 2015.5. Duan D Y, Sun D C. Research on hydraulic AGC system of hot stripmill[C]//Materials Science Forum. Trans Tech Publ, 2011: 277-280.。
1700铝箔轧机弯辊液压系统工作原理分析

1700铝箔轧机弯辊液压系统工作原理分析黄晓华(中铝公司西北铝加工厂,甘肃定西748111)【摘要】本文单就弯辊系统的工作及控制原理进行分析,以便于更好的使用及维护好该设备,充分发挥设备的技术性能优势。
【关键词】弯辊力弯辊缸交界力1700铝箔轧粗中轧机和精轧机是我厂从奥钢联-克莱西姆公司引进的具有当代世界先进水平的轧机。
该轧机采用了很多先进的控制技术.本文单就弯辊系统的工作及控制原理进行分析,以便于更好的使用及维护好该设备,充分发挥设备的技术性能优势。
1弯辊力的作用安装在轧机机架牌坊上的弯辊缸用于通过轧机轴承箱给轧辊施加径向的外力。
正弯辊所施加的力使上下工作分离;负弯缸所施加的力使上工作辊和上支承分离、下工作辊和下支承辊分离,负弯力使上下工作辊轴承箱靠拢。
加到工作两端的弯辊力起到使工作辊弯曲的作用,从而控制带材的平整度。
在该轧机上正弯缸和负弯缸同时加力,实际的轧辊弯曲取决于正弯力和负弯力的净力即净弯辊力,净弯辊力作用在带材板形上弯辊力的改变是均匀的和近似平行的,因而,轧辊液压缸常被用于控制材料误差的均匀性。
弯辊缸的弯辊力取决缸中油压与无杆腔面积的乘积再乘以缸的数量。
在该系统中,为了实现净弯力,正负弯缸采用两套独立的液压回路,由一套油泵供油,各自采用单独的电液伺服阀、液压缸及传感器。
单独的伺服阀及压力传感器用于各自弯辊缸中压力的闭环、开环的控制及显示。
为了实现净弯力,控制系统必须能单独控制正弯和负弯压力。
通过单独的伺服控制,正负弯缸由单独的伺服阀在任何给定的时间供给压力油,通过各自压力传感器控制缸中的油压。
该设计的优点是进出正负弯缸的油互不影响,从提高了弯辊控制的高稳定性(特别是零位附近)、高响应、无冲击等高性能。
2弯辊控制原理及目的在该轧机上,弯辊伺服阀能用开环和闭环两种方式控制:(1)开环。
用于直接设置轧辊弯辊伺服阀给弯辊缸一个固定输入输出流量的情况,使正常情况下正弯油缸达到设置点的最大压力,以确保轧机急停时,正负力达到设置的最大值,使急停时上下工作辊快速分离。
某钢厂热轧乎整机组液压弯辊自动控制系统的研究

2 . A u t o m a t i o n D i v i s i o n ,B a o t o u I r o n& S t e e l( G r o u p )C o . , L t d . ,B a o t o u I n n e r Mo n g o l i a 0 1 4 0 1 0 ,C h i n a )
中图分类号 :T P 2 7 3 文献标 识码 :B 文章 编号 :1 0 0 1— 3 8 8 1( 2 0 1 3 )2 3— 0 6 9— 4
Re s e a r c h o n a Ho t Ro l l i ng Te m pe r Mi l l Hy d r a ul i c Be nd i ng Ro l l Aut o ma t i c Co nt r o l S y s t e m
ZHANG Ch a o y i . FENG Gu i b i n . L I U Mi n g
( 1 . I n f o r m a t i o n E n g i n e e r i n g C o l l e g e , I n n e r Mo n g o l i a U n i v e r s i t y o f S c i e n c e a n d T e c h n o l o g y ,
中的液压 弯辊控制系统 。在平整 的过程 中 ,正负液压 弯辊需要快 速切换 ,这就要求整个液压控制 系统 和主 ห้องสมุดไป่ตู้机调速 系统具有 很强的实时性 ,能够快速跟 随板形
的的变化 。为此某 钢厂热轧平整机组液压弯辊控制 系 统和 主轧 机 的调速 系统 硬件 选用 C P U 4 1 4 - 2 D P和
- 1、下载文档前请自行甄别文档内容的完整性,平台不提供额外的编辑、内容补充、找答案等附加服务。
- 2、"仅部分预览"的文档,不可在线预览部分如存在完整性等问题,可反馈申请退款(可完整预览的文档不适用该条件!)。
- 3、如文档侵犯您的权益,请联系客服反馈,我们会尽快为您处理(人工客服工作时间:9:00-18:30)。
比;∞,为伺服阀的固有频率。
(3)液压缸的力平衡方程。系统最终由液压缸
输出弯辊力,弯辊力再作用于工作辊上使之产生所
需的挠度。弯辊的数学模型可简化为一个弹性模量
很大的弹簧。对液压缸活塞进行受力分析,负载可折
算为惯性、弹性、黏性和摩擦负载系统。弯辊力是由8
个缸共同作用产生的,则液压缸的力平衡方程为c 2]:
力,可大大降低工程造价。缩短研究周期。
2系统的总体分析
’
2.1系统的分析
液压弯辊力控制系统由弯辊液压缸产生弯辊
第一作者简介:曹益忠(1982一),男,在太原重工轧钢锻 压设备公司从事全液压矫直机、轧机的研究工作。Tel:
13994213384,E-mail:wjhhyl23@yahoo.tom.crt
线,见图6。由图6可以看出:该系统的阶跃响应是 衰减振荡。
图5系统的根轨迹图(闭环)
图6系统的阶跃响应曲线 由计算可得超调量口r=29.450 4%,误差带为 5%时的调节时间ts=0.030 0 S,误差带为2%时的调
节时间t产0.042 5 s,这说明系统的响应速度很快。 4结论
在对系统进行频域分析后,可以根据所分析的 结果对系统进行改进,这也是进行仿真的一个重要 目的。提高系统的控制精度和响应速度,必须提高它 的开环增益。但开环增益的提高受到系统稳定性的
求,板形控制也就成为轧钢企业的重点课题。液压弯
辊力板形控制系统以其高效和高精度在钢铁企业得
到日益广泛的应用,但目前国内对液压弯辊力控制
系统的研究还很少,不能满足设计的要求。为了能提
高液压弯辊系统的性能,有必要对整个系统进行仿
真,以进一步了解整个系统。
l计算机仿真的作用
在对液压系统进行设计、分析和改进时,计算机
是—个高度复杂的元件,它具有高阶的非线性动态
特性,其实际动态特性受到供油压力、输入信号幅
值、油温、负载条件等诸多因素的影响。我们把输出
流量对输入电流的传递函数用二阶环节来表示:
错2互K互q i·
(2)
∞:0.7,
式中:g。(s)为伺服阀容积流量;,(s)为伺服阀的驱
动电流;K。为伺服阀的流量增益;玉为伺服阀的阻尼
第32卷
式中:嘶为压力传感器输出电压;南,为压力传感器的
变换系数;只为伺服阀工作压力。
(6)加法器的数学模型
E=uj-ulf.
(8)
式中:E为输出的偏差电压抛为输人系统的设定电
压信号;uf为压力传感器输出电压。
(7)静摩擦力、动摩擦力方程。
k
(:p_0)
昧1禹Fd(二,≠o)
(9)
【l鄂l
式中:R为活塞所受摩擦力;‰为液压缸活塞的瞬时速 度;E为活塞的静摩擦力;R为活塞的动摩擦力。
一B·8A2一只·8Al一鼹·妒屉·xp--81%--mpxp.一(3)
式中:Pl为液压缸有杆腔油压;P2为液压缸无杆腔油 压;A。为液压缸活塞有杆侧面积;A:为液压缸活塞 无杆侧面积;成为液压缸阻尼比;后为负载弹簧刚 度;%为液压缸活塞位移;Fm为活塞所受摩擦力;m 为负载质量。
通常可认为液压缸有杆腔为恒压,即P1为常 数,对式(3)拉氏变换可得:
(8)信号处理(按PID考虑)
Eo=kpE(t)+ki I E(t)dt+kd掣.
(10)
式中:晶为控制环节输出偏差电压,V;E“)为输出的 偏差电压,V;后。为PID控制中的比例系数;七i为PID 控制中的积分系数;后。为PID控制中的微分系数。 2.4系统的方块图
根据各部分的数学模型,可得方块图(见图3)。 3液压动态的仿真过程及求解 3.1仿真软件的选用
系统性能,缩短系统的调整时间,避免返工;还可以
通过仿真对所设计的系统有更深入的了解,了解多
负载系统中负载之间的相或认识单个元体在
整个系统中的作用等等,从而达到优化系统、优化元
件、优化参数的目的。利用这种技术可以把人们从大
量繁琐的重复性计算中解脱出来,节省大量人力物
总第118期 2009年第2期
文章编号:1672-1152(2009)02-0014-04
山西冶皇 SHANⅪMETAI工.UR(≥Y
轧机弯辊液压系统的仿真研究
Total 118 No.2。2009
曹益忠t王晶2
(1.太原重工股份有限公司, 山西太原030024;2.榆次油研液压有限公司, 山西榆次030600)
在对液压系统作适当改进后,再进行仿真,比较 两者的异同,就可以设计出最佳并有最大的性价比 的系统回路。从系统的频域仿真还可以看m各个参 数对系统影响程度的大小,设计者可以据此对各个 参数作一定的调整,从而使设计者有效地把握各个 元件在系统中的作用,便于设计者选择正确的元件, 保证系统设计的成功。
液压系统中可以由液容(腔)和液阻(节流孔)的组 合构成机械滤波器,它可以消除流过其容腔的高频 液压冲击。选择不同的节流孔与腔的组合可以产生 不同的截止频率。鉴于脉动油压在机械滤波器中流 动时的非恒定性,无法精确地计算出它的截止频率, 可以通过实验初步计算预先制造了参数相近的多个 试件,然后在液压冲击实验台上具体测试,选择最优 参数的滤波器。使用机械滤波器抑制弯辊力冲击,可 以有效地防止弯辊力传感器的损坏,削弱系统外干 扰,提高弯辊力系统的控制精度。
跳)·8A2-(PI·J4 l+脚旦=(w2+嘏·s“)‘菇p(s).(4)
(4)液压缸的流量连续方程。1个伺服阀同时 给8个液压缸供油,每个液压缸分得总流量的118, 则液压缸的流量连续方程为:
q。路鲁‘路警“绋·
(5)
式中:‰为液压缸处于平衡位置时高压腔容积;展为
液压油的等效体积弹性模量;石。为液压缸活塞的瞬
对于一个复杂的液压系统,在进行仿真以前应 当对其作适当的简化,这是系统仿真关键的一个步 骤。在仔细分析了系统图和查阅了大量文献资料之 后,可以将整个系统简化为—个压力控制伺服系统…。
万方数据
2009年第2期
曹益忠,等:轧机弯辊液压系统的仿真研究
其中主要的元件应包括油源、伺服阀、管路、油缸、负 载、控制系统。其简化原理图见图l。
由图4可知,幅值稳定裕量Kr=9.702 2 dB,相 位稳定裕量y=56.6990,系统是稳定的。
利用Matlab软件绘制出系统闭环的根轨迹图, 见下页图5。
仿真的另一结果是根轨迹图。所谓根轨迹是指 当系统某个参数(如开环增益K)由0到无穷大变 化时,闭环特性方程的根在[s]平面上移动的轨迹。 控制系统的稳定性,由其闭环极点唯一确定,由此可 以判别系统是否稳定可靠。由图5可知:闭环的极点 都在虚轴左侧,因此系统是稳定的。闭环的极点离虚 轴较远,动态分量衰减较快,系统快速性较好[4|。
控制系统的动态性能指标 通常是在零初始条件下,通过 系统阶跃响应的特征来进行定 义的。稳定控制系统的阶跃响 应可分为单调变化和衰减振荡 两种情况。系统的动态性能指 标实际上就是刻画阶跃响应曲 线特征的一些量。利用Matlab 软件绘制出系统的阶跃响应曲
万方数据
2009年第2期
曹益忠。等:轧机弯辊液压系统的仿真研究
图1 弯辊力控制系统简化原理图
压力传感器将采集到的弯辊液压缸压力值反馈 给伺服阀的控制单元,组成了弯辊液压缸油压的闭 环控制系统。在板带的轧制过程中,应根据板带的实 际形状来实时调节弯辊力的大小,使之在预设定的 弯辊力值附近波动。在板带进入轧钢瞬间和板带离 开轧机瞬间,产生的的压力波动会对工作辊和支承 辊的辊形产生很大的影响,构成了弯辊力控制系统 的外干扰。要保证弯辊力控制板形的精度,必须使系 统具有较高的抗干扰能力。另外板带的断面形状、轧 辊的热凸度及其压扁变形、板带宽度、张力、轧制速 度、轧辊磨损等因素都会引起弯棍力的变化。由图l 可以画出电液伺服弯辊力控制系统的原理图,见图2。
力,在轧制过程中向工作辊辊颈施加液压弯辊力,瞬 时改变轧辊的有效挠度,从而改变承载辊缝形状,使 轧制后带钢的延伸沿横向均匀分布,进而达到控制板 形的目的。根据具体的工艺条件适当地改变弯辊力, 就可实现改善板形的目的。液压弯辊板形控制系统属 于电液伺服力控制系统,它具有精度高、响应速度快、 功率大、结构紧凑和使用方便等优点,因此得到广泛 的应用。电液伺服力控制系统有多种形式,针对精轧 机组弯辊力控制系统,从应用目的上分析,应该属于 电液伺服加载力(弯辊力)j空制系统。精轧机组的液压 弯辊力控制系统由操作侧和传动侧各一套彼此独立 的电液伺服弯辊力控制系统组成。每侧各有—套调节 伺服阀,控制各自液压缸油压,从而达到控制弯辊力 的目的。实际上,弯辊力控制系统是通过压力传感器 测出油缸油压来表征加载力f弯辊力),即油压是被控 量,其又作为反馈量进人闭环控制系统。所以液压弯
动态仿真具有重要的价值。在许多液压技术应用场
合,如果设计人员在设计阶段就考虑到液压系统动
静态特性,则可大大缩短液压系统或元件的设计周
期,避免因重复试验及加工所带来的昂贵费用,且可
及早地认识到该系统在动静态特性方面所存在的薄
弱环节并加以消除。通过对系统的动静态特性进行
预测来实现计算机仿真不仅可以在设计过程中预测
辊力控制系统是电液伺服压力(油压脏制系统。
液压油与负载质量(如轧辊)组成的质量为弹簧二 阶振荡系统,对于二阶振荡系统的品质的—个非常重 要指标是其阻尼比的大小。一般电液伺服控制系统的 阻尼比都比较小,用电液伺服压力控制系统替代电液 伺服弯辊力控制系统后阻尼比是增加还是减小,这对 系统的品质非常关键,因为阻尼比过小,压力峰值会 很大,就会使压力传感器损坏,轧制后板带钢出现波 浪或翘曲等缺陷。为此。先建立了系统的数学模型,进 行仿真分析以选择合适的措施提高系统的阻尼。 2.2系统的简化
时速度;Gp为液压缸泄漏系数;gd为液压缸容积流 量;£为伺服阀工作压力,如忽略管路压力损失,则 P。=P2。对式(5)拉氏变换得:
半以州如)=(钳鲁5)Pc(s)· (6)