精益的福特生产体系概括
某汽车公司精益生产LP概述

精益生产(LP)概述二战以后,丰田汽车公司的丰田和大野考察了福特汽车公司轿车厂。
当时,这个厂日产7000辆轿车,比丰田公司一年的产量还多。
但丰田却没有想到仅简单地照搬福特的生产模式,他认为“那里的生产体制还有些改进的可能”。
回到日本后,丰田和大野进行了一系列的探索和实验,根据日本国情(社会和文化背景、严格的上下级关系、团队工作精神),建立了一整套新的生产管理体制,采用精益生产方式组织生产和管理,使丰田汽车的质量、产量和效益都跃上一个新台阶,变成世界汽车之王。
与此同时,其它的汽车公司和别的行业也纷纷采用这种组织管理方式,使日本经济得到飞速发展。
与技艺性生产和大批量生产不同,精益生产组合了前两者的优点,避免了技艺性生产的高费用和大批量生产的高刚性。
为此目的,精益生产采用的是由多能工人组成的工作小组和柔性很高的自动化设备。
与大批量生产不同,精益生产的一切都是“精简”的:与大批大量生产相比,只需要一半的劳动强度、一半的制造空间、一半的工具投资、一半的产品开发时间、库存的大量减少、废品大量的减少和品种大量的增加。
两者的最大区别在于它们的最终目标上:大量生产强调“足够”好的质量,因此总是存在着缺陷;而精益生产则追求完美性(不断降低价格、零缺陷、零库存和无限多的品种)。
一、丰田公司的精益生产1. 精益生产的出现由丰田和大野创造的精益生产技术可以通过一个实例来说明。
在大批大量生产方式下,制造汽车覆盖件的冲压模的更换是个很大的问题。
由于精度要求极高,模具的更换即昂贵且费时,需要极高技术的工人来完成。
为了解决这个问题,西方汽车制造商采用一组冲压机来生产同一种零件,于是,他们可以实现几个月甚至几年不更换模具。
对于50年代的丰田公司,这种办法却行不通,他们没有足够的资金来购买好几百台冲压机用于汽车覆盖件的生产,他们必须用少数的几条生产线生产所有汽车的冲压件。
于是,大野发明了一种快速更换模具新技术(SMED法──Single Minute of Dies),这种技术使更换一副模具的时间从1天减少到3分钟,也不需要专门的模具更换工。
精益生产介绍

国际汽车 研究计划
TOYOTA
4
1、精益生产方式简介
3
什么是精益生产?
精益生产方式,它不是概念,而是一种哲学(思想),一种“工具”。它是融入于心的以低价 格准时生产优良品质产品的生产方式——降本增效
精益生产方式的核心思想是——消除浪费
企业活动
浪 价值 费
5
2、八大浪费
定义: 浪费是指不增加附加价值,是成本增加的一系列活动。
★通过应用常识性工具、检查表及工作技巧来进行,不 需要很大的投入,却能获得较大的产出;
★以PDCA作为持续运作的工具,是一个不断提升的过 程;
★以公司制度的方式固定下来,通过对参与者的培训、 引导和奖励,形成一种持续改善的文化氛围,倡导全员 参与。
★充分发挥员工潜力,瓦解员工智慧,培养员工问题 意识、参与意识和改善意识;
勉強
不均勻
浪费的3种形态:
1.勉 强: 超过能力界限的超负荷状态;(会导致设备
故障,品质低下,人员不安全)
能力限度
2.浪 费: 有能力,但未给予充足的工作量的未饱和
状态; (人员工作量不饱满,设备稼动率低)
3.不均衡: 有时超负荷有时又不饱和的状态(差
异状态).
浪費
合適
6
2、八大浪费
1
2
72、八大浪费精益生产 Nhomakorabea•小批量多品种 •在同步生产的基础上,强调 缩短生产周期 •提高资源利用率 •需求驱动 起源于20世纪50年代丰田汽车 公司,而在80年代中期被欧美 企业纷纷采用。丰田系统是建 立在准时化观念上的拉动 式生产模式,以应付小订单 多品种的挑战
3
1、精益生产方式简介
2
精益生产方式的诞生
企业精益生产的结构体系

企业精益生产的结构体系1精益生产及其产生精益生产(Lean Production,LP),又称精良生产,其中”精”表示精良、精确、精美;”益”表示利益、效益等等。
精益生产就是及时制造,消灭故障,消除一切浪费,向零缺陷、零库存进军。
它是美国麻省理工学院在一项名为”国际汽车计划”的研究项目中提出来的。
它们在做了大量的调查和对比后,认为日本丰田汽车公司的生产方式是最适用于现代制造企业的一种生产组织管理方式,称之为精益生产,以针对美国大量生产方式过干臃肿的弊病。
精益生产综合了大量生产与单件生产方式的优点,力求在大量生产中实现多品种和高质量产品的低成本生产。
一、精益生产的产生与推广20世纪初,从美国福特汽车公司创立第一条汽车生产流水线以来,大规模的生产流水线一直是现代工业生产的主要特征。
大规模生产方式是以标准化、大批量生产来降低生产成本,提高生产效率的。
这种方式适应了美国当时的国情,汽车生产流水线的产生,一举把汽车从少数富翁的奢侈品变成了大众化的交通工具,美国汽车工业也由此迅速成长为美国的一大支往产业,并带动和促进了包括钢铁、玻璃、橡胶、机电以至交通服务业等在内的一大批产业的发展。
大规模流水生产在生产技术以及生产管理史上具有极为重要的意义。
可是第二次世界大依以后,社会进入了一个市场需求向多2样化发展的新阶段,相应地要求工业生产向多品种、小批量的方向发展,单品种、大批量的流水生产方式的弱点就日渐明显了。
为了顺应这样的时代要求,由日本丰田汽车公司首创的精益生产,作为多品种、小批量混合生产条件下的高质量、低消耗进行生产的方式在实践中摸索、创造出来了。
1950年,日本的丰田英二考察了美国底持律的福特公司的轿车厂。
当时这个厂每天能生产7000辆轿车,比日本丰田公司一年的产量还要多。
但丰田在她的考察报告中却写道:”那里的生产体制还有改进的可能”。
战后的日本经济萧条,缺少资金和外汇。
怎样建立日本的汽车工业?照搬美国的大量生产方式,还是按照日本的国情,另谋出路,丰田选择了后者。
精益生产体系
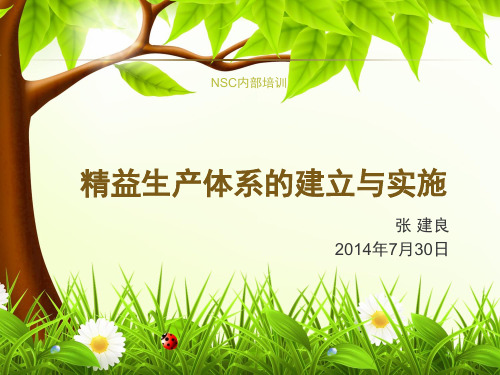
NSC内部培训
▪目标生来产自管于理生的产目任标务
—生产任务通常分解成“QDC” Quality(品质) Delivery(交期) Cost(成本)
直接目标
Safety(安全) Morale(士气) Eviroment(环境)
附加(约 束)目标
精益生产的核心还是生产!
NSC内部培训
生产管理方式的变革
•不必要 在过程中投入的资源
超出必要数量以上的部分, 纯粹属于浪费。
NSC内部培训
增加值工过零件程与非增组值装产过品 程
电镀 油漆
点数
库存
品质检验
搬运
人员
资/能源
环境
材
设备
成
料
品
三、精益生产之方式与要求
JIT模式
NSC内部培训
Just In Time
适品 ·适量 ·适时
连续流 生产
单件流 生产
浪费传等统的于在烧钱
成本认识
材料费 人工费 设备折旧费 场地租赁费 能源费 管理费
NSC内部培训
现在的 成本认识
浪费
最佳的
成本
(真正产生 价值的资源)
NSC内部培训
价值流图的概念
认识价值流图(Value Stream Mapping, VSM):
价值流的定义:
—一个产品或一项服务从开始到结束所经过的所有过程(包括增值的和非增 值的过程)。
82案年,例G:M弗里蒙特工厂濒临破产
NSC内部培训
由于经营管理出现 过多问题,GM弗里 蒙特工厂于1982年 关闭。
NSC内部培训
案例:
84年,GM与丰田合资成立NUMMI
作为丰田和通用汽车的合资企业,NUMMI于1984年末重新投入 生产 ➢ 工厂没有进行搬迁 ➢ 新工厂大部分员工(85%)从旧员工重聘,包括整个工会 组织(UAW) ➢ 没有投资什么新技术 ➢ 只有一个新的(丰田)管理体系
01-精益生产理念

1.45-->1.88 70.8%-->91.9% 1.56M 1.9M
2 : Flexibility (Models produced at the same time)
23 Conveyor Line
1.18
1.64 1.56
1.31 1.21 1.06
1.63 1.55
1.32 1.23
Jun'02 A
Jul'02
0.83 Aug'02
Month
B
C
D
E
1.81 1.59 1 1..2 25 3
Sep'02
实例
3. Productivity Results
Vision
Result
1: Productivity
57.1%
二 精益生产理念
目录
一:精益生产理念
1. 精益生产的目的 2. 理想精益生产系统
二:精益生产工具
1. 直线式生产流程 2. 团队工作 3. 客户导向 4. 拉式生产/JIT供应 5. In Line System 6. 多技能员工 7. 标准化作业 8. 持续现场改善 9. 损失分析,暴露问题 10. 一个流生产 11. 看板管理 12. Cell 生产方式
插件 2 ● ○ △
○ ●
○
插件 3 ○ ◎ ●
○ ◎ △ ●
焊接 ○ ◎ ◎
● △
组装 1 ◎
○
● ○
组装 2 ◎
○
●
检测 ● ○ ◎ ●
○
包装 ● △
精益生产LP概述

精益生产LP概述二战以后,丰田汽车公司的丰田和大野调查了福特汽车公司轿车厂。
事先,这个厂日产7000辆轿车,比丰田公司一年的产量还多。
但丰田却没有想到仅复杂地照搬福特的消费形式,他以为〝那里的消费体制还有些改良的能够〞。
回到日本后,丰田和大野停止了一系列的探求和实验,依据日本国情〔社会和文明背景、严厉的上下级关系、团队任务肉体〕,树立了一整套新的消费管理体制,采用精益消费方式组织消费和管理,使丰田汽车的质量、产量和效益都跃上一个新台阶,变成世界汽车之王。
与此同时,其它的汽车公司和别的行业也纷繁采用这种组织管理方式,使日本经济失掉飞速开展。
与技艺性消费和大批量消费不同,精益消费组合了前两者的优点,防止了技艺性消费的高费用和大批量消费的高刚性。
为此目的,精益消费采用的是由多能工人组成的任务小组和柔性很高的自动化设备。
与大批量消费不同,精益消费的一切都是〝精简〞的:与大批少量消费相比,只需求一半的休息强度、一半的制造空间、一半的工具投资、一半的产品开发时间、库存的少量增加、废品少量的增加和种类少量的添加。
两者的最大区别在于它们的最终目的上:少量消费强调〝足够〞好的质量,因此总是存在着缺陷;而精益消费那么追求完美性〔不时降低价钱、零缺陷、零库存和有限多的种类〕。
一、丰田公司的精益消费1. 精益消费的出现由丰田和大野发明的精益消费技术可以经过一个实例来说明。
在大批少量消费方式下,制造汽车掩盖件的冲压模的改换是个很大的效果。
由于精度要求极高,模具的改换即昂贵且费时,需求极高技术的工人来完成。
为了处置这个效果,西方汽车制造商采用一组冲压机来消费同一种零件,于是,他们可以完成几个月甚至几年不改换模具。
关于50年代的丰田公司,这种方法却行不通,他们没有足够的资金来购置好几百台冲压机用于汽车掩盖件的消费,他们必需用少数的几条消费线消费一切汽车的冲压件。
于是,大野发明了一种快速改换模具新技术〔SMED法──Single Minute of Dies〕,这种技术使改换一副模具的时间从1天增加到3分钟,也不需求专门的模具改换工。
精益生产的历史概述
精益生产的历史概述引言精益生产是一种管理方法,旨在通过最小化浪费和提高价值创造,为企业实现持续改进和优化生产过程。
这种管理方法起源于日本汽车制造业,随后逐渐在全球范围内得到应用和推广。
本文将对精益生产的历史进行概述,介绍其起源、发展和核心原理。
起源精益生产起源于日本的汽车制造行业,尤其是丰田汽车公司。
20世纪50年代末期,丰田汽车公司面临着诸多挑战:生产效率低下、质量不稳定、库存过多等问题。
为了应对这些挑战,丰田汽车公司向美国的福特汽车公司学习了大规模生产的方法,并结合日本本土的文化和价值观,逐渐形成了精益生产的理念。
丰田汽车公司将精益生产定义为“为顾客创造最大价值,通过最小化浪费来实现连续改进。
”他们将精益生产视为一项长期的持续改进活动,旨在通过消除各种类型的浪费来提高效率和质量。
发展经过多年的实践和持续改进,精益生产逐渐得到了验证和认可,并在全球范围内推广开来。
1980年代,美国的一些汽车制造企业开始引入精益生产的概念,并取得了显著的效果。
其中最具代表性的案例就是通用汽车公司引入的“世界级制造”概念,它基于精益生产的原理和方法,成功地提高了生产效率和质量水平。
随着时间的推移,精益生产的理念逐渐应用于其他行业,如电子制造、医疗保健、服务业等。
目前,许多企业都在不同程度上采用了精益生产的原则和方法,以提高业务绩效和客户满意度。
核心原理精益生产的核心原理基于几个关键概念和方法:价值流思维精益生产强调的第一个原则是要以价值流为导向来思考问题。
价值流是指产品或服务在整个生产过程中的所有活动和步骤,从原材料采购到最终交付给顾客。
精益生产通过分析价值流,识别并消除其中的浪费,以优化整个生产过程。
浪费的消除精益生产把浪费定义为不增加价值的任何活动或资源的使用。
它将各种类型的浪费归结为以下七种:超生产、等待、运输、过程中的库存、过度加工、不必要的运动和缺陷。
通过分析和消除这些浪费,企业可以提高生产效率和质量。
精益生产理念及体系简介
精益生产 Lean Production,简称LP
n 1990年著作《改变世界的机器》,第一次 把丰田生产方式定名为 Lean Production, 即精益生产方式
n 1996年经过四年的“国际汽车计划” (IMVP)第二阶段著作《精益思想》。
精益生产理念及体系简介
精益生产 Lean Production,简称LP
n 精益生产主要研究时间和效率 , 注重提升 系统的稳定性 ,50多年来精益生产的成功 案例已证实: ●精益生产让生产时间减少 90% ●精益生产让库存减少 90% ●精益生产使生产效率提高 60% ●精益生产使市场缺陷减少 50% ●精益生产让废品率降低 50% ●精益生产让安全指数提升 50%
n ……否则,要检查一下你在哪里做错了!
目视管理三要点
n 无论是谁都能判明是好是坏(异常)。 n 能迅速判断,精度高。 n 判断结果不会因人而异。
精益生产理念及体系简介
目视管理的类别
n 红牌 n 看板 n 信号灯或者异常信号灯 n 操作流程图 n 警示线 n 告示板
·············
精益生产理念及体系简介
目视管理的事例
精益生产理念及体系简介
精益生产理念及体系简介
看板操作的六个使用规则
n 没有看板不能生产也不能搬运。
n 看板只能来自后工序。
n 前工序只能生产取走的部分。
n 前工序按收到看板的顺序进行生产。
n 看板必须和实物一起。
n 不把不良品交给后工序。
精益生产理念及体系简介
标准化作业
n 所谓作业标准化,就是对在作业系统调查分析的基 础上,将现行作业方法的每一操作程序和每一动作 进行分解,以科学技术、规章制度和实践经验为依 据,以安全、质量效益为目标,对作业过程进行改 善,从而形成一种优化作业程序,逐步达到安全、 准确、高效、省力的作业效果。
精益生产体系介绍
26
防错意味著“第一次把事情做好”。
防错技术,又称愚巧法、防呆法。是指在过程失误发生之 前即加以防止。是一种在作业过程中采用自动作用、报 警、标识、分类等手段,使作业人员不特别注意也不会 失误的方法。
*在源头预防或探测差错 *失效模式分析是差错预防的基础
论上加以概括和总结。
--标志:1996年《精益思想》发表
“精益” -- 精益求精,追求完美!
益
精:精良、精细 益:利益、效
精益生产又被称之为不做无用功的精干型生产系统,从直观上看精益生 产在生产过程中尽量减少了人力、设备、空间的浪费,生产的组织利用了 准时化(JIT)、单件流、全员品质管理和全员设备维护等方法。
高 低 高 物资缺乏、供不应 求
低 更低 更高 买方市场
9
传统生产与精益生产的比较动画演示
只保持必须的物料库存
非常低的在制品 主/副流程同步生产
后拉供货(看板)
缩短生产周期 消除七大浪费
没有成品库存
后拉生产
五、精益生产的管理之屋
精益企业
作业标准
绩效指标 改善的心智模式
经营政策
防错技术
自
暗灯技术
働 化 标准作业
持续改善
生产总成本
直通率
生产周期
生产效率
准交率
后拉生产 及 连续流 时 快速换线 生 精益布局 产
消除浪费 互信&尊重
5S和目视管理 全员生产保全 均衡化生产 稳定的运作系统
IE工业工程 团队合作 改善提案 技能培训 授权的文化
11
六、精益生产在制鞋业的实践
• 早在2002年,NIKE,adidas等世界性运动品牌已开始要求其所有代工 加工厂进行精益生产方式的实践。
精益生产理念及体系简介PPT课件
Amphenol AHSI
精益生产的基本原则
➢流动 (Flow) 产品在工厂里从原料到成品必须经过的路程 及所需的时间
Amphenol AHSI
精益生产的基本原则
➢拉动 (Pull) 以客户的真实需求拉动产品的生产 ➢库存即是浪费 ➢尚未售出的完成品也是浪费 ➢去除过剩的产能 ➢提高客户需求拉动速度
……否则,要检查一下你在哪里做错了!
Amphenol AHSI
精益工具及术语
➢SMED ➢5S ➢TPM ➢Jidoka/自动化 ➢Kaikaku/创新 ➢Kanban/JIT ➢Kaizen/CI
➢定义价值 ➢价值流 ➢均衡、稳定性 ➢拉动 ➢单元布局 ➢标准化作业
Amphenol AHSI
同时,精益生产把责任下放到组织结构的各个层
次,采用小组工作法,充分调动全体职工的积极
性和聪明才智,把缺陷和浪费及时地消灭在每一
ቤተ መጻሕፍቲ ባይዱ个岗位。
Amphenol AHSI
Amphenol AHSI
精益生产的好处
精益生产主要研究时间和效率 , 注重提升 系统的稳定性 ,50多年来精益生产的成功 案例已证实: ●精益生产让生产时间减少 90% ●精益生产让库存减少 90% ●精益生产使生产效率提高 60% ●精益生产使市场缺陷减少 50% ●精益生产让废品率降低 50% ●精益生产让安全指数提升 50%
经过30多年的努力,终于形成了完整的丰 田生产方式,使日本的汽车工业超过了美 国,产量达到了1300万辆,占世界汽车总 量的30%以上。
Amphenol AHSI
精益生产核心
其核心是消除一切无效劳动和浪费,它把目标确 定在尽善尽美上
通过不断地降低成本、提高质量、增强生产灵活 性、实现无废品和零库存等手段确保企业在市场 竞争中的优势