电机绕组的浸漆方法
直流电动机绕组浸漆、烘干处理步骤

直流电动机绕组浸漆、烘干处理步骤直流电动机的浸漆处理,包括电枢绕组、励磁绕组、换向极绕组等的浸漆处理,以及其他绝缘零件的表面浸漆处理、热固性合成树脂的浇注、换向器两端面的绝缘涂封、电枢及定子有关部位的表面喷涂覆盖漆等。
在浸漆、烘干过程中,必须将电枢直立起来,使换向器端在上。
注意切勿让浸漆进入换向器内。
B、F级无溶剂漆沉浸法浸漆工艺见表1,H级硅有机漆沉浸法浸漆工艺见表2。
直流电动机的烘干处理与异步电动机的相同。
表1 B、F级无溶剂漆沉浸法浸漆工艺一例序号工序名称工艺参数B级环氧聚酯酚醛无溶剂漆F级不饱和聚酯无溶剂漆温度(℃)时间(h)热态绝缘电阻(MΩ)温度(℃)时间(h) 热态绝缘电阻(MΩ)1 预烘130 6> 201306>502第一次浸漆烘干浸漆滴漆烘干50~60室温1400.5>110 - -8 50~60室温1500.5>16 - ->103第二次浸漆烘干浸漆滴漆烘干50~60室温1403 min0.5 12 - ->2* 50~60室温1503 min0.510 - ->5注:*第二次浸漆烘干时,绕组热态绝缘电阻需连续3h稳定在同一数值,才能结束烘干。
表2 H级1053有机硅漆沉浸法浸漆工艺一例序号工序名称工艺参数温度(℃) 时间(h)热态绝缘电阻(MΩ)1 预烘1306 >502第一次浸漆烘干浸漆滴漆烘干50~60室温1301800.5>0.546---3第二次浸漆烘干浸漆滴漆烘干50~60室温1301803min0.546---4第三次浸漆烘干浸漆滴漆烘干50~60室温1301901 min> 20min414~16 - -> 10 * 注:*第三次浸漆干燥时,绕组热态绝缘电阻需连续3h稳定在同一数值,才能结束烘干。
直流电动机。
2024年版电动机绕组的浸漆烘干

2024年版电动机绕组的浸漆烘干一、电动机绕组浸漆和烘干的作用1、驱除潮气、提高防潮能力及增强电气绝缘强度绕组的绝缘材料中有很多的毛细孑侪口缝隙溶易吸收潮气而降低绝缘电阻。
烘干时先把潮气^除,浸漆后绝缘漆把毛细孑侪口缝隙全部填满,并在表面上形成一层光滑的漆膜,使潮气很难进入绕组。
绝缘漆的介电强度比空气高得多,因而浸漆后绕组的绝缘强度增大了。
2、增加绕组的散热效果绝缘漆的热传导能力比空气大得多。
浸漆后导线中产生的热量经绝缘漆传导出去,增加了绕组的散热效果,可降低绕组的温升。
3、增强绕组的机械强度电流流过绕组时会在导线上产生电动力。
在重载和启动时电流很大,电动力也很大。
如绕组未做浸漆处理,电动力会使导线振动,时间一长,导线便会松动,进而绝缘会被擦伤,结果可能发生短路或接地故障。
浸漆处理后,绕组被粘结成一个整体,提高了机械强度,减少了损坏的可能性。
二、浸渍漆的种类和浸漆时的黏度1浸渍用绝缘漆要渗透到绕组线圈以及绝缘材料的所有空隙,并填满这些空隙,所以要求绝缘漆具有黏度小、流动性好、渗透力强、含固体成分高,以及吸潮性小等的特点。
2、绝缘漆按是否用溶剂来分,分为有溶剂漆和无溶剂漆两种。
由于溶剂最后挥发到空气中,对环境造成污染,又因F级电机的发展,所以无溶剂漆的使用有增多的趋势。
3、浸漆时,有溶剂绝缘漆的黏度要进行调整,采用1032绝缘漆时,要浸漆两次。
第一次浸渍时绝缘漆的黏度要稀些,第二次浸渍的目的是填满空气隙和加厚漆模,黏度要高些。
在不同温度时,浸漆所需的黏度不同。
无溶剂绝缘漆的黏度随温度上升而迅速下降。
在浸漆时的温度下,黏度下降,所以能浸透并填充到绕组中去。
三、浸漆方法1滴漆(浇漆)把电动机竖直放在滴漆盘上,用漆壶浇绕组的一端,然后经过20-30分钟滴漆,再将电动机翻过来,浇绕组的另一端,直到浇透。
2、沉浸把需浸漆的电动机吊入漆罐中,要使漆面没过电动机200mm以上,以便绝缘漆渗透到绝缘材料的所有空隙内,填满所有空隙。
电动机线圈灌漆的方法
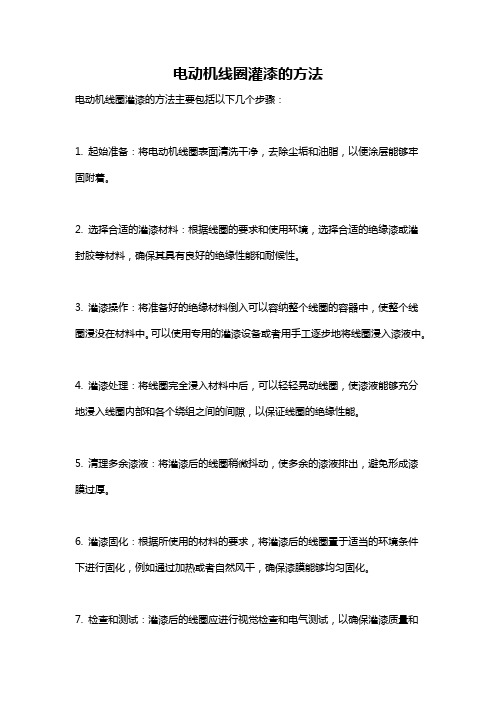
电动机线圈灌漆的方法
电动机线圈灌漆的方法主要包括以下几个步骤:
1. 起始准备:将电动机线圈表面清洗干净,去除尘垢和油脂,以便涂层能够牢固附着。
2. 选择合适的灌漆材料:根据线圈的要求和使用环境,选择合适的绝缘漆或灌封胶等材料,确保其具有良好的绝缘性能和耐候性。
3. 灌漆操作:将准备好的绝缘材料倒入可以容纳整个线圈的容器中,使整个线圈浸没在材料中。
可以使用专用的灌漆设备或者用手工逐步地将线圈浸入漆液中。
4. 灌漆处理:将线圈完全浸入材料中后,可以轻轻晃动线圈,使漆液能够充分地浸入线圈内部和各个绕组之间的间隙,以保证线圈的绝缘性能。
5. 清理多余漆液:将灌漆后的线圈稍微抖动,使多余的漆液排出,避免形成漆膜过厚。
6. 灌漆固化:根据所使用的材料的要求,将灌漆后的线圈置于适当的环境条件下进行固化,例如通过加热或者自然风干,确保漆膜能够均匀固化。
7. 检查和测试:灌漆后的线圈应进行视觉检查和电气测试,以确保灌漆质量和
绝缘性能满足要求。
需要注意的是,在进行电动机线圈灌漆过程中,应注意安全,避免因为电动机绕组的强磁场而对人员和设备造成伤害。
同时,选择适当的灌漆材料和操作方法,以确保灌漆质量和绝缘性能的可靠性。
定子绕组浸漆工艺

定子绕组浸漆工艺操作规范电机绕组浸漆烘干的目的,是在于把绝缘材料中所含的潮气驱除,用绝缘漆填满所有空间气隙,这样,即可提高绕组的绝缘强度和防潮性能,又可提高绕组的耐热性和散热性,还可提高绕组绝缘的机械性能和化学稳定性,电动机浸漆质量的好坏,直接影响到电机的温升和使用寿命。
1、真空浸漆原理真空浸漆原理:将工件放入浸烘罐预烘,在真空环境中排除线圈内部的空气和挥发物,再在真空条件下依靠漆液重力和线圈中的毛细管的作用,真空浸漆,使漆液迅速渗透并充满绝缘结构内层的一种机械作业的绝缘工艺。
2、适用范围本工艺适用于本公司生产的各类Y系列及Y派生系列专用三相异步电动机定子绕组的浸漆烘干。
3、主要原辅材料3.1 831绝缘漆3.2 831-X稀释剂3.3 漆刷、揩布4、设备及工具4.1 FJH-1600型复合真空浸渍烘干机4.2 吊篮4.3 涂-4粘度计4.4 兆欧表 1000V5、工艺准备5.1.检查所有材料、设备、装置、计量仪表和有关器具是否正常并符合使用要求。
5.2.检查有绕组定子铁芯的端部绝缘不应有损伤和物渍。
对引出线破损、线圈碰坏、槽楔滑出、绑扎松动等工件应予以处理后方可浸漆。
5.3.必要时将定子引出线上涂好硅脂。
5.4.配漆(即加漆和稀释剂)5.5.打开漆和稀释剂的桶盖,目测两种材料的外观颜色、粘稠程度、有无机械杂质。
5.6.严格按照真空浸漆烘干机操作加入绝缘漆和稀释剂。
5.7.测量绝缘漆的粘度:先用温度计测量漆的温度,然后用涂4号粘度计测量漆的粘度(在漆面下约100mm处取样,测量两次求平均值),并做好记录,查粘度应符合规定的标准(标准:涂4号粘度计:0℃-10℃时25-16秒; 10℃-20℃时16-11秒; 20℃-30℃时11-8秒),粘度计用完后必须清洗干净。
6、工艺过程6.1 将真空浸漆缸清理干净(每月最低清理2次),把待浸漆的工件放入吊篮,注意每批待烘的定子其规格大小应尽量相近,并吊入浸漆缸内盖好浸漆缸盖。
定子绕组浸漆工艺
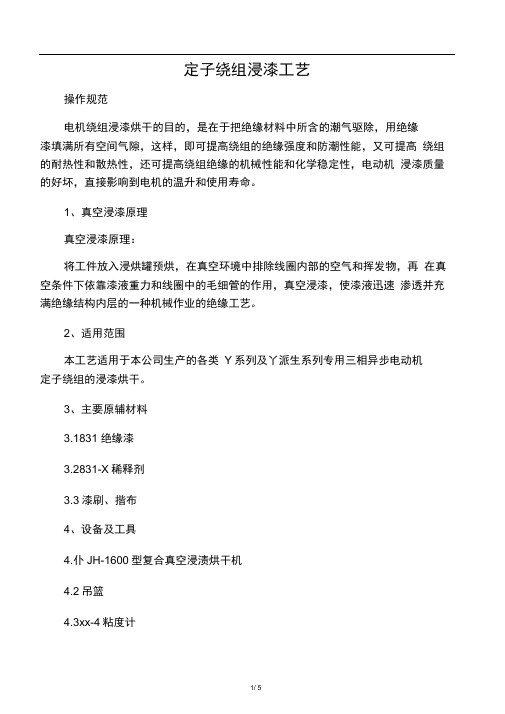
定子绕组浸漆工艺操作规范电机绕组浸漆烘干的目的,是在于把绝缘材料中所含的潮气驱除,用绝缘漆填满所有空间气隙,这样,即可提高绕组的绝缘强度和防潮性能,又可提高绕组的耐热性和散热性,还可提高绕组绝缘的机械性能和化学稳定性,电动机浸漆质量的好坏,直接影响到电机的温升和使用寿命。
1、真空浸漆原理真空浸漆原理:将工件放入浸烘罐预烘,在真空环境中排除线圈内部的空气和挥发物,再在真空条件下依靠漆液重力和线圈中的毛细管的作用,真空浸漆,使漆液迅速渗透并充满绝缘结构内层的一种机械作业的绝缘工艺。
2、适用范围本工艺适用于本公司生产的各类Y系列及丫派生系列专用三相异步电动机定子绕组的浸漆烘干。
3、主要原辅材料3.1831 绝缘漆3.2831-X稀释剂3.3漆刷、揩布4、设备及工具4.仆JH-1600型复合真空浸渍烘干机4.2吊篮4.3xx-4粘度计4.4兆欧表1000V5、工艺准备5.1. 检查所有材料、设备、装置、计量仪表和有关器具是否正常并符合使用要求。
5.2. 检查有绕组定子铁芯的端部绝缘不应有损伤和物渍。
对引出线破损、线圈碰坏、槽楔滑出、绑扎松动等工件应予以处理后方可浸漆。
5.3. 必要时将定子引出线上涂好硅脂。
5.4.配漆(即加漆和稀释剂)5.5. 打开漆和稀释剂的桶盖,目测两种材料的外观颜色、粘稠程度、有无机械杂质。
5.6. 严格按照真空浸漆烘干机操作加入绝缘漆和稀释剂。
5.7. 测量绝缘漆的粘度:先用温度计测量漆的温度,然后用涂 4 号粘度计测量漆的粘度(在漆面下约100mm 处取样,测量两次求平均值),并做好记录,查粘度应符合规定的标准(标准:涂 4 号粘度计:O C-10C 时25-16 秒;10C -20C 时16-11 秒;20C-30 C时11-8秒),粘度计用完后必须清洗干净。
6、工艺过程6.1 将真空浸漆缸清理干净(每月最低清理2 次),把待浸漆的工件放入吊篮,注意每批待烘的定子其规格大小应尽量相近,并吊入浸漆缸内盖好浸漆缸盖。
真空浸漆或真空压力浸漆
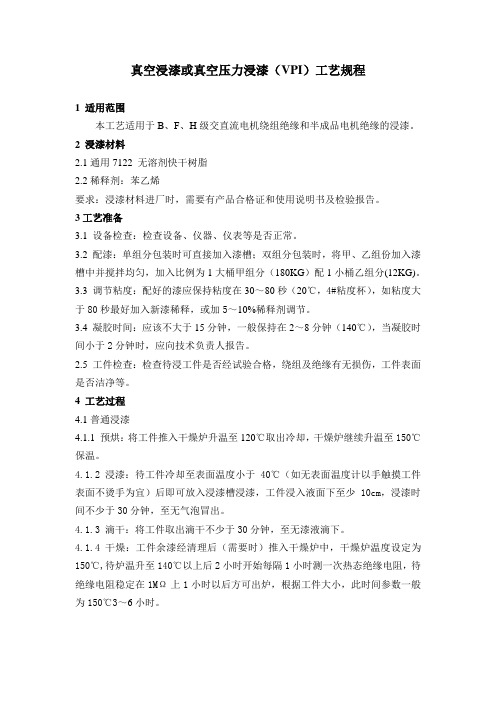
真空浸漆或真空压力浸漆(VPI)工艺规程1 适用范围本工艺适用于B、F、H级交直流电机绕组绝缘和半成品电机绝缘的浸漆。
2 浸漆材料2.1通用7122 无溶剂快干树脂2.2稀释剂:苯乙烯要求:浸漆材料进厂时,需要有产品合格证和使用说明书及检验报告。
3工艺准备3.1 设备检查:检查设备、仪器、仪表等是否正常。
3.2 配漆:单组分包装时可直接加入漆槽;双组分包装时,将甲、乙组份加入漆槽中并搅拌均匀,加入比例为1大桶甲组分(180KG)配1小桶乙组分(12KG)。
3.3 调节粘度:配好的漆应保持粘度在30~80秒(20℃,4#粘度杯),如粘度大于80秒最好加入新漆稀释,或加5~10%稀释剂调节。
3.4 凝胶时间:应该不大于15分钟,一般保持在2~8分钟(140℃),当凝胶时间小于2分钟时,应向技术负责人报告。
2.5 工件检查:检查待浸工件是否经试验合格,绕组及绝缘有无损伤,工件表面是否洁净等。
4 工艺过程4.1普通浸漆4.1.1 预烘:将工件推入干燥炉升温至120℃取出冷却,干燥炉继续升温至150℃保温。
4.1.2 浸漆:待工件冷却至表面温度小于40℃(如无表面温度计以手触摸工件表面不烫手为宜)后即可放入浸漆槽浸漆,工件浸入液面下至少10cm,浸漆时间不少于30分钟,至无气泡冒出。
4.1.3 滴干:将工件取出滴干不少于30分钟,至无漆液滴下。
4.1.4 干燥:工件余漆经清理后(需要时)推入干燥炉中,干燥炉温度设定为150℃,待炉温升至140℃以上后2小时开始每隔1小时测一次热态绝缘电阻,待绝缘电阻稳定在1MΩ上1小时以后方可出炉,根据工件大小,此时间参数一般为150℃3~6小时。
5.2 VPI浸漆工艺5.2.1预烘:将工件推入干燥炉升温至100℃~130℃,保温2~4小时,取出冷却至50℃以下进罐。
注意工件浸入液面下至少10cm。
5.2.2真空去湿5.2.2.1手动扳开(1)号压缩空气阀,在工控机上开(30)号密封圈充气阀,进行工件真空去湿。
电动机绕组浸漆的办法

电动机绕组浸漆的办法绕组浸漆的方法许多,一般依据修补单位的设备条件、电动机的体积和对绝缘质量的央求,选用以下方法对绕组进行浸漆。
1.浇浸修补单台电动机时绕组浸漆可施行浇浸。
浇浸时,将定子垂直置于滴漆盘上,绕组一端向上,用漆壶或漆刷往绕组上端部浇漆。
待绕组缝隙灌满漆液并初步从另一端缝隙渗出来,便将定子翻转,浇另一端绕组。
直至浇透接连。
零星修补小型电动机时,选用此法可削减绝缘漆的糟蹋。
2.滴浸这种方法适用于中小型电动机的浸漆处理。
短少专用设备的单位可选用手艺滴漆技能。
下面介绍一种对小型电动机绕组进行浸漆处理常用的滴漆技能。
①配方。
6十1环氧树脂50%(质量比)、桐油顺丁烯二酸酐50%,现配现用。
②预热。
在绕组内通电加热4min分配,温度操控在十0~115℃之间(用点温度计丈量),或许将绕组置于单调炉内加热约0.5h。
③滴浸。
将电动机定子垂直置于漆盘上,当电动机温度降为60~70℃时初步手艺滴漆,十min后,将定子翻转,滴浸绕组另一端,直至浇透接连。
④固化。
滴浸后,绕组通电固化,绕组温度坚持十0~150℃;丈量绝缘电阻值合格(20MΩ)接连,或许将绕组置于单调炉内加热,温度同上,时间约2h(视电动机巨细而定),绝缘电阻跨过1.5MΩ时出炉。
3.滚漆这种方法适用于转子或电枢绕组的浸漆处理。
滚漆时,往漆槽内倒入绝缘漆,将转子置于漆槽内,漆面应浸没转子绕组200mm以上。
假定漆槽太浅,转子绕组浸上漆的面积小,则应屡次翻滚转子,或许一边翻滚转子一边用刷子刷漆。
一般翻滚3~5次,就可使绝缘漆渗透绝缘。
4.沉溺批量修补中小型电动机时,绕组浸漆可施行沉溺。
沉溺时,先往漆罐中装入恰当绝缘漆,然后吊入电动机定子,使漆液吞没定子200mm以上。
待漆液渗透绕组和绝缘纸的悉数缝隙,便将定子吊起滴漆。
浸漆时若加0.3~0.5MPa压力。
则作用十分好。
5.真空压力浸高压电动机,以及对绝缘质量央求较高的中小型电动机,其绕组可施行真空压力浸漆。
电机绕组的浸漆方法

其工艺过程由预烘、浸漆两个主要工序组成。
一:
预烘
1.预烘目的
绕组在浸漆前应先进行预烘,是为了驱除绕组中的潮气和提高工件浸漆时的温度,以提高浸漆质量和漆的浸透能力。
电机绕组的浸漆方法
绕组在电机的结构中是最脆弱的部件,为了提高绕组的耐潮防度腐性和绝缘强度,并提高机械强度、导热性和散热效果和延缓老化等,必须对重绕后的电机绕组进行浸漆处理。并要求浸漆与烘干严格按照绝缘处理工艺进行,以保证绝缘漆的渗透性好、漆膜表面光滑和机械强度高。使定子绕组粘结成为一个结实的整体。
目前
(d)当停止滴漆约20~30min,把电机定子翻过来,再将绝缘漆浇向绕组上端部(原下端部)直至渗透为止;
(e)再停止滴漆约30min后,用布蘸上煤油,将定子内膛及机座上的余漆清除,然后进行烘干;
(f)若需二次浸漆的,经烘干后取出凉至60~80度再进行二次浇浸,操作同上。
4.浸漆方法
浸漆的主要方法有:
浇浸、沉浸、真空压力浸。
对单台修理的电机浸漆,多采用浇浸,而沉浸和真空压力浸通常用于制造电机,对批量的可考虑沉浸,高压电机才采用真空压力浸。常用的浇浸工艺方法为:
(a)取出预烘的电机,待温度凉至60~80度,竖直架于漆盘之上;(b)将无溶剂漆灌入空饮料塑料瓶中,以便把握浇浸漆量;(c)手拿装有绝缘漆的塑料瓶,斜倾瓶口使绝缘漆流出瓶口呈线状,从绕组上端部浇入绝缘漆,使漆在线圈中渗透并由绕组下端部回流到漆盘;
如果工件温度过高,漆中溶剂迅速挥发,使绕组表面过早形成漆膜,而不易浸透到绕组内部,也造成材料浪费;若温度过低,就失去预烘作用,使漆的粘度增大,流动性和渗透性较差,也使浸漆效果不好。
实践证明,工件温度在60~80度浸漆为宜。
- 1、下载文档前请自行甄别文档内容的完整性,平台不提供额外的编辑、内容补充、找答案等附加服务。
- 2、"仅部分预览"的文档,不可在线预览部分如存在完整性等问题,可反馈申请退款(可完整预览的文档不适用该条件!)。
- 3、如文档侵犯您的权益,请联系客服反馈,我们会尽快为您处理(人工客服工作时间:9:00-18:30)。
电机绕组的浸漆方法
绕组在电机的结构中是最脆弱的部件,为了提高绕组的耐潮防度腐性和绝缘强度,并提高机械强度、导热性和散热效果和延缓老化等,必须对重绕后的电机绕组进行浸漆处理。
并要求浸漆与烘干严格按照绝缘处理工艺进行,以保证绝缘漆的渗透性好、漆膜表面光滑和机械强度高。
使定子绕组粘结成为一个结实的整体。
目前E、B级绝缘的电机定子绕组浸漆的处理,一般采用1032三聚氰胺醇酸树脂漆,溶剂为甲苯或二甲苯,浸漆次数为二次,将其统称为普遍二次浸漆热沉浸式艺。
其工艺过程由预烘、浸漆两个主要工序组成。
一:预烘
1.预烘目的
绕组在浸漆前应先进行预烘,是为了驱除绕组中的潮气和提高工件浸漆时的温度,以提高浸漆质量和漆的浸透能力。
2.预烘方法
预烘加热要逐渐增温,温升速度以不大于20-30度/h为宜。
预烘温度视绝缘等级来定,对E级绝缘应控制在120~125度,B级绝缘应达到125~130度,在该温度下保温4~6小时,然后将预烘后的绕组冷却到60~80度开始浸漆。
二:浸漆
浸漆时应注意工件的温度、浸的粘度以及浸漆时间等问题。
1.浸漆温度
如果工件温度过高,漆中溶剂迅速挥发,使绕组表面过早形成漆膜,而不易浸透到绕组内部,也造成材料浪费;若温度过低,就失去预烘作用,使漆的粘度增大,流动性和渗透性较差,也使浸漆效果不好。
实践证明,工件温度在60~80度浸漆为宜。
2.漆的粘度
漆的粘度选择应适当,第一次浸漆时希望漆浸透到绕组内部,因此要求漆的流动性好一些,故漆的粘度应较低,一般可取22~26s(20度、4号粘度计);第二次浸漆时,主要希望在绕组表面形成一层较好的漆膜,因此漆的粘度应该大一些,一般取30~38s为宜。
由于漆温对粘度影响很大,所以一般规定以20度为基准,故测量粘度时应根据漆的温度作适当调整。
3.浸漆时间
浸漆时间的选择原则:第一次浸漆,希望漆能尽量浸透到绕组内部,因此浸漆时间应长一些,约15~20min第二次浸漆,主要是形成较好的表面漆膜,因此浸漆时间应短一些,以免时间过长反而将漆膜损坏,故约10~15min为宜。
但一定要浸透,一直浸到不冒气泡为止,若不理想可适当延长浸漆时间。
每次浸漆完成后,都要把定子绕组垂直放置,滴干余漆,时间应为30min,并用溶剂将其它部位余漆擦净。
4.浸漆方法
浸漆的主要方法有:浇浸、沉浸、真空压力浸。
对单台修理的电机浸漆,多采用浇浸,而沉浸和真空压力浸通常用于制造电机,对批量的可考虑沉浸,高压电机才采用真空压力浸。
常用的浇浸工艺方法为:
(a)取出预烘的电机,待温度凉至60~80度,竖直架于漆盘之上;(b)将无溶剂漆灌入空饮料塑料瓶中,以便把握浇浸漆量;
(c)手拿装有绝缘漆的塑料瓶,斜倾瓶口使绝缘漆流出瓶口呈线状,从绕组上端部浇入绝缘漆,使漆在线圈中渗透并由绕组下端部
回流到漆盘;
(d)当停止滴漆约20~30min,把电机定子翻过来,再将绝缘漆浇向绕组上端部(原下端部)直至渗透为止;
(e)再停止滴漆约30min后,用布蘸上煤油,将定子内膛及机座上的余漆清除,然后进行烘干;
(f)若需二次浸漆的,经烘干后取出凉至60~80度再进行二次浇浸,操作同上。