极片毛刺检验标准作业指导书
去毛刺作业指导书
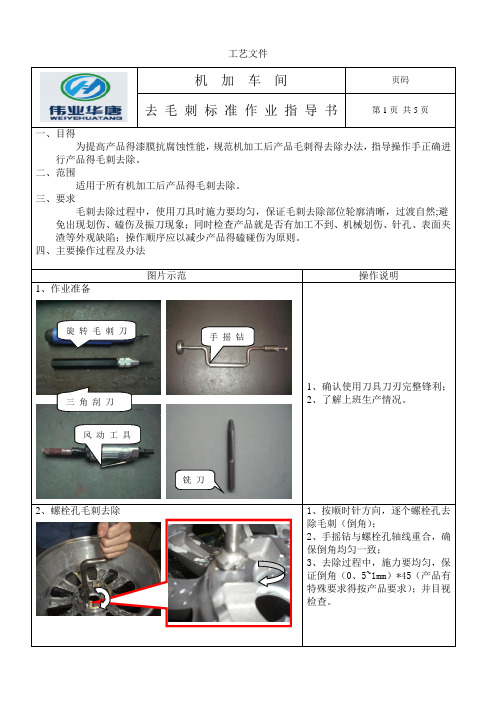
工艺文件
机 加 车 间
页码 去 毛 刺 标 准 作 业 指 导 书
第1页 共5页
一、目得
为提高产品得漆膜抗腐蚀性能,规范机加工后产品毛刺得去除办法,指导操作手正确进行产品得毛刺去除。
二、范围
适用于所有机加工后产品得毛刺去除。
三、要求
毛刺去除过程中,使用刀具时施力要均匀,保证毛刺去除部位轮廓清晰,过渡自然;避免出现划伤、磕伤及振刀现象;同时检查产品就是否有加工不到、机械划伤、针孔、表面夹渣等外观缺陷;操作顺序应以减少产品得磕碰伤为原则。
四、主要操作过程及办法
图片示范
操作说明
1、作业准备
1、确认使用刀具刀刃完整锋利;
2、了解上班生产情况。
2、螺栓孔毛刺去除
1、按顺时针方向,逐个螺栓孔去除毛刺(倒角);
2、手摇钻与螺栓孔轴线重合,确保倒角均匀一致;
3、去除过程中,施力要均匀,保证倒角(0、5~1mm )*45(产品有特殊要求得按产品要求);并目视检查。
旋 转 毛 刺 刀
三 角 刮 刀
手 摇 钻
风 动 工 具
铣 刀
1 2 2)划窝产品背面毛刺去除
3)背面铸窝毛刺去除
4)气门孔沉孔毛刺去除
5、帽口接刀处毛刺去除
6、帽槽毛刺去除
8、正面轮辐毛刺去除
9、窗口毛刺去除1)用风动铣刀铣削窗口
12、正面精车产品正面凹槽毛刺去除
13、正面精车产品螺栓孔沉孔边缘。
去毛刺作业规程
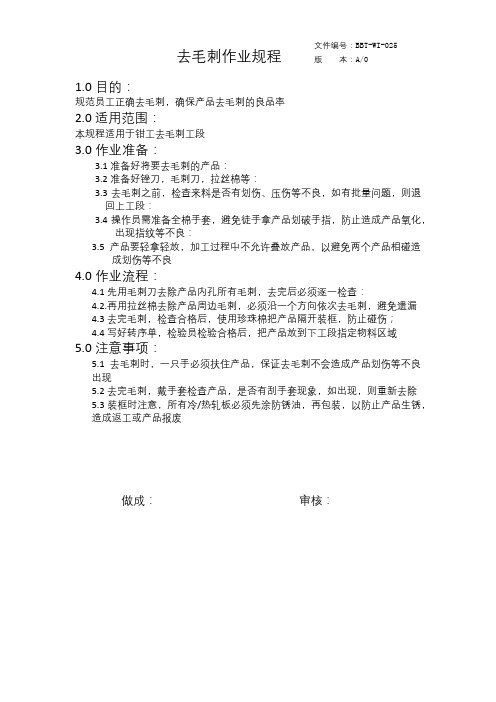
去毛刺作业规程文件编号:BBT-WI-025
版本:A/0
1.0目的:
规范员工正确去毛刺,确保产品去毛刺的良品率
2.0 适用范围:
本规程适用于钳工去毛刺工段
3.0作业准备:
3.1准备好将要去毛刺的产品:
3.2准备好锉刀,毛刺刀,拉丝棉等:
3.3去毛刺之前,检查来料是否有划伤、压伤等不良,如有批量问题,则退
回上工段:
3.4操作员需准备全棉手套,避免徒手拿产品划破手指,防止造成产品氧化,
出现指纹等不良:
3.5产品要轻拿轻放,加工过程中不允许叠放产品,以避免两个产品相碰造
成划伤等不良
4.0作业流程:
4.1先用毛刺刀去除产品内孔所有毛刺,去完后必须逐一检查:
4.2.再用拉丝棉去除产品周边毛刺,必须沿一个方向依次去毛刺,避免遗漏
4.3去完毛刺,检查合格后,使用珍珠棉把产品隔开装框,防止碰伤;
4.4写好转序单,检验员检验合格后,把产品放到下工段指定物料区域
5.0注意事项:
5.1去毛刺时,一只手必须扶住产品,保证去毛刺不会造成产品划伤等不良
出现
5.2去完毛刺,戴手套检查产品,是否有刮手套现象,如出现,则重新去除
5.3装框时注意,所有冷/热轧板必须先涂防锈油,再包装,以防止产品生锈,
造成返工或产品报废
做成:审核:。
去毛刺作业指导书
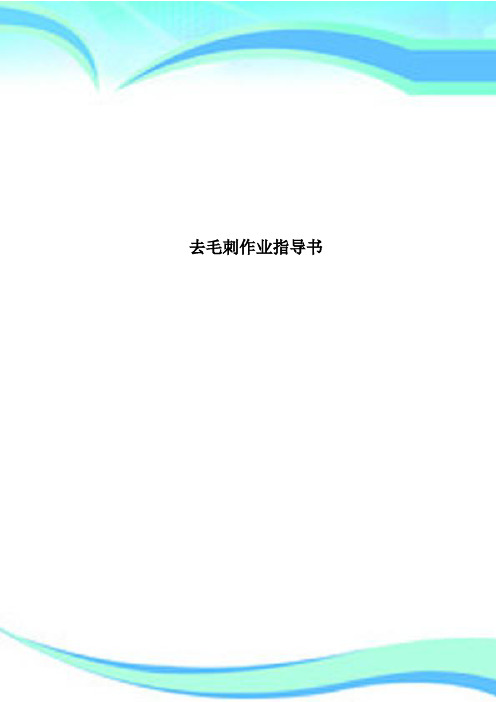
2、了解上班生产情况。
2、螺栓孔毛刺去除
1、按顺时针方向,逐个螺栓孔去除毛刺(倒角);
2、手摇钻与螺栓孔轴线重合,确保倒角均匀一致;
3、去除过程中,施力要均匀,保证倒角(0.5~1mm)*45(产品有特殊要求的按产品要求);并目视检查。
工艺文件
3.气门孔毛刺去除——1)不划窝产品背面毛刺去除
2)用风动砂纸棒对窗口铣削线进行打磨
1、产品窗口铣削合格后,用
风动砂纸棒对窗口铣削线进
行打磨;
2、每个窗口,沿铣削表面打
磨2~3周,打磨方向须与工具
旋转方向相反;
2、操作过程中,要求持稳工
具、施力均匀、动作熟练,不
能损伤窗口周围表面;
3、操作后,目视检查各拐角、
夹角部位的打磨质量。
注:1、砂纸棒使用P150#砂
1、检查气门孔正面毛刺去除
质量;
2、左手托二道轮缘,右手持
三角刮刀,以气门孔逆时针方
向第一根轮辐开始,按逆时针
方向逐个清除轮辐正面毛刺;
3、刀具与加工面夹角控制在
20~30度之间,要求去除过
程排屑均匀连续;
4、过程中避免划伤产品表面,
棱边不能崩漆,过渡要圆滑无
尖角。
注:精车产品去毛刺时,操作
者持刀手不可以带手套且双
背面划窝产生的毛刺,并用
P240#砂纸打磨,保证毛刺去
除干净。
3)背面铸窝毛刺去除
气门孔背面有铸窝的产品,用旋转毛刺刀或三角刮刀清除铸窝周边毛刺,并用P240#砂纸打磨一遍,保证过渡圆滑无尖角。
4)气门孔沉孔毛刺去除
1、将产品平放在工作台上,
左手把住外轮缘,右手用旋转毛刺刀或三角刮刀清除气门孔沉孔周边毛刺,确保去除后轮廓线均匀一致;
去毛刺作业指导书范本
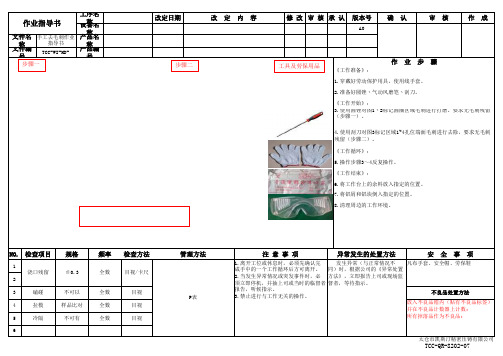
作业指导书工序名称改定日期改 定 内 容修 改设备名称审 核承 认版本号确 认审 核作 成A0文件名称手工去毛刺作业指导书产品名称文件编号TCC-WI-MD-产品编号3.使用圆锉对图1丶2标记圆圈区域毛刺进行打磨。
要求无毛刺残留(步骤一)。
《工作循环》:5.操作步骤3~4反复操作。
《工作结束》:作 业 步 骤《工作准备》:1.穿戴好劳动保护用具,使用线手套。
2.准备好圆锉丶气动风磨笔丶刮刀。
《工作开始》:6.将工作台上的余料放入指定的位置。
7.将铝屑和铝块倒入指定的位置。
8.清理周边的工作环境。
NO.检查项目规格频率检查方法管理方法注 意 事 项异常发生的处置方法安 全 事 项1浇口残留≦0.3全数目视/卡尺P表凡布手套、安全帽、劳保鞋23磕碰不可以全数目视不良品处置方法样品比对全数目视放入不良品箱内(贴有不良品标签)并在不良品计数器上计数;所有掉落品作为不良品;5冷隔不可有全数1.离开工位或休息时,必须先确认完成手中的一个工作循环后方可离开。
2.当发生异常情况或突发事件时,必须立即停机,并抽上司或当时的临督者报告,听候指示。
3.禁止进行与工作无关的操作。
发生异常(与正常情况不同)时,根据公司的《异常处置方法》,立即报告上司或现场监督者,等待指示。
太仓市凯斯汀精密压铸有限公司4.使用刮刀对图3标记区域1~4孔位端面毛刺进行去除,要求无毛刺残留(步骤二)。
目视64拉模工具及劳保用品步骤二步骤一TCC-QR-8202-07。
去毛刺作业指导书

客户名称
产品名称
产品图号
工艺流程 一、工序内容 序 号
1ห้องสมุดไป่ตู้
作业步骤及要点
去毛刺作业指导书
版本
物料编码
模腔数量 设备编号
三、作业视图
工艺装备
标准工时/ 件
版本号:A-0 ;表单编号:XX-QP07-QR-39
工装编号 产品重量 每小时产能 原材料
g
件
2
3
4
5
6
产品按图示要求摆放,盖确认章后转入下道工序 。
二、控制重点
序 号
检测项目
质量要求
检测方 法
检测频率
记录
1
2
3
4
5
6
说 1、符号标识:关键◆ 重要◇ 记录※ 不记录×
明 2、反应计划:停止生产→标识 → 隔离 →上报组长 → 调整
四、产品视图 责任人
编制(日期)
五、摆放视图 审核(日期)
批准(日期)
影像测量仪测量毛刺及焊接熔深熔宽检验操作规范

影像测量仪测量⽑刺及焊接熔深熔宽检验操作规范1 适⽤范围1.1本操作规范适⽤于动⼒锂离⼦电池极⽚裁切过程中极⽚⽑刺检验和极⽚分切边缘露箔状态检验。
1.2本操作规范适⽤于动⼒锂离⼦电池焊接熔深熔宽状态检验。
2 设备、仪器及仪表2.1 影像测量仪 (图1)转轴1-调节操作台前后位置转轴2-调节显⽰屏的清晰度转轴3-调节操作台左右位置ON OFF- 红⾊电源开关,绿⾊红外线开关转动按钮-左侧轮廓光源开关;右侧表⾯光源开关。
3 操作规程3.1启动系统点击桌⾯QuickMeasuring 快捷⽅式,进⼊操作界⾯,如图3所⽰:转轴1转轴2 转轴3 ON OFF 转动按钮影像摄取窗⼝影像测量窗⼝测量⼯具窗⼝单元摘要窗⼝状态显⽰窗⼝图2 图3打开投影仪⾯电源键,按下第1个(投影仪⾯板左起)绿⾊按钮开启红外线点,转动第3个(投影仪⾯板左起)按钮开启轮廓光源,转动第4个(投影仪⾯板左起)按钮开启表⾯光源;3.2 ⽑刺取样3.2.1按⼯艺⽂件规定的抽样⽐例抽取⽣产线裁切的极⽚,测量模切后极⽚边缘⽑刺取样需要取极⽿间距最⼤间隔数模切位置的极⽚并且带两侧极⽿;测量分切⽑刺、极⽚分切边缘漏箔状态,极⽚取样长度与分切⼑周长⼀致。
3.2.2⽬视检验,如果发现剪切位置明显破损、掉⾓、余⾓现象则直接判为不合格。
3.2.3将切割好的测极⽚试样⽔平放置在测量仪⼯作台上拉直平铺使⽤压块将极⽚压住(如图4横向⽑刺测试、图5纵向⽑刺测试),观察镜头倍数选择4.5,并在软件中设置相应倍数4.5。
(如图6)图4 图5倍数选择与镜头倍数⼀致图63.2.4横向⽑刺检验3.2.4.1将⽤⼯装固定好的试样平放在投影仪托盘上(如图4),使投影灯垂直照射在试样边缘上,调整转轴1和转轴3,并配合转轴2调整,直⾄屏幕上能够清晰地显⽰试样边缘为⽌。
调节转轴3,沿试样边缘查看最⼤的⽑刺点的位置。
然后停在该位置。
如同时有两个或者两个以上的⽑刺⽆法判断哪个最⼤,则均进⾏测试,选取最⼤值记录,如最⼤值超出⼯艺标准要求⽣产⼈员擦拭⼑具重新取样测量直⾄合格后⽅能进⾏⽣产。
检验作业指导书(共五则)
检验作业指导书(共五则)第一篇:检验作业指导书检验作业指导书1.进料检验 1.1 定义进料检验又称来料检验,是制止不良物料进入生产环节的首要控制点。
进料检验由IQC执行。
1.2 检测要项IQC在对来货检验前,首先应清楚该批货物的品质检测要项,不明之处要向本部门主管问询,直到清楚明了为止。
在必要时,IQC验货员可从来货中随机抽取两件来货样,交IQC主管签发来货检验临时样品,并附相应的品质检测说明,不得在不明来货检验与验证项目、方法和品质允收标准的情况下进行验收。
1.3 检验项目与方法 1.3.1 外观检测一般用目视、手感、限度样品进行验证。
1.3.2 尺寸检测一般用卡尺、千分尺、塞规等量具验证。
1.3.3 结构检测一般用拉力器、扭力器、压力器验证。
1.3.4 特性检测如电气的、物理的、化学的、机械的特性一般采用检测仪器和特定方法来验证。
1.4 检验方式的选择 1.4.1 全检方式适用于来货数量少、价值高、不允许有不合格品物料或公司指定进行全检的物料。
1.4.2 免检方式适用于低值、辅助性材料或经认定的免检厂来料以及生产急用而特批免检的,对于后者IQC应跟进生产时的品质状况。
1.4.3 抽样检验方式适用于平均数量较多、经常性使用的物料。
样本大小:批量的10%(不少于20件),允收数AC=0,拒收数RE=1。
1.5 检验结果的处理方式 1.5.1 允收经IQC验证,不合格品数低于限定的不合格品个数时,则判为该批来货允收。
IQC应在验收单上签名,盖检验合格印章,通知货仓收货。
1.5.2 拒收若不合格品数大于限定的不良品个数,则判定该送检批为拒收。
IQC应及时填制《IQC退货报告》,经相关部门会签后,交仓库、采购办理退货事宜。
同时在该送检批货品外箱标签上盖“退货”字样,并挂“退货”标牌。
1.5.3 特采特采,即进料经IQC检验,品质低于允许水准。
IQC虽提出“退货”的要求,但由于生产的原因,而做出的“特别采用”的要求。
【精品文档】去毛刺作业指导书-范文word版 (3页)
本文部分内容来自网络整理,本司不为其真实性负责,如有异议或侵权请及时联系,本司将立即删除!== 本文为word格式,下载后可方便编辑和修改! ==去毛刺作业指导书篇一:除毛刺作业指导书篇二:锌合金去毛刺抛光作业指导书篇三:去毛刺机作业指导书 Microsoft Word 文档去毛刺机控制系统主要分为以下几个部分:一. 去毛刺机检测系统二. 去毛刺机横梁升降控制系统三. 去毛刺机横梁翻转控制系统四. 去毛刺机刀头升降控制系统五 .去毛刺机推杆控制系统1、去毛刺机检测系统构成和功能: a 构成;5组光栅由(LB1、LB2、LB3、LB4、LB5)和9个限位(S161 、S162、 S163 S164、 S165、S173 、 S174 、S175、 S176、 )构成。
b :功能:其中光栅LB1~~LB5检测铸坯的位置和控制毛刺机的动作及辊道的运转;限位S161~~S178检测去毛刺机各机构的位置。
2、去毛刺机横梁升降系统构成和主要功能如下:a:系统构成:该系统包括去毛刺机机旁操作箱、升降气压缸控制气磁阀Y101、光栅检测元件、升降限位检测S161、S173(横梁高位) S162 、S174(横梁低位)b.主要控制功能:当铸坯挡住1# 、2#、3#光栅,检测铸坯的位置并控制升降气磁阀Y101动作。
使横梁上升到高位S161、S173信号到,气动阀 Y101失电。
3、去毛刺机横梁翻转控制系统的系统构成和主要功能如下: a、系统构成:包括气动阀Y103、 Y104,限位S162(工作位)、S161(清洗位)、光栅。
b.主要控制功能:当去毛刺结束气动阀Y104得电动作横梁翻转到清洗位S164清洗毛刺,由清洗位信号S163后气动阀Y103得电动作横梁翻转到工作位。
4. 去毛刺机刀头升降控制系统的构成和功能:a. 系统构成:包括气动阀Y102b. 主要功能:当铸坯档住1#、2#、3# 、4#光栅时气动阀Y102得电,刀头上升;当铸坯离开4#、3#、2#光栅时,横梁到清洗位气动阀Y102失电动作,刀头下降。
去毛刺作业指导书
去毛刺作业指导书
1
工艺文件
机 加 车 间
页码 去 毛 刺 标 准 作 业 指 导 书
第1页 共5页
一、目的
为提高产品的漆膜抗腐蚀性能,规范机加工后产品毛刺的去除办法,指导操作手正确进行产品的毛刺去除。
二、范围
适用于所有机加工后产品的毛刺去除。
三、要求
毛刺去除过程中,使用刀具时施力要均匀,保证毛刺去除部位轮廓清晰,过渡自然;避免出现划伤、磕伤及振刀现象;同时检查产品是否有加工不到、机械划伤、针孔、表面夹渣等外观缺陷;操作顺序应以减少产品的磕碰伤为原则。
四、主要操作过程及办法
图片示范
操作说明
1、作业准备
1、确认使用刀具刀刃完整锋利;
2、了解上班生产情况。
2、螺栓孔毛刺去除
1、按顺时针方向,逐个螺栓孔去除毛刺(倒角);
2、手摇钻与螺栓孔轴线重合,确保倒角均匀一致;
3、去除过程中,施力要均匀,保证倒角(0.5~1mm )*45(产品有特殊要求的按产品要求);并目视检查。
旋 转 毛 刺 刀
三 角 刮 刀
手 摇 钻
风 动 工 具
铣 刀
1 2 2)划窝产品背面毛刺去除
3)背面铸窝毛刺去除
4. 背腔法兰盘及轮辐减重窝毛刺去除
5. 帽口接刀处毛刺去除
7. 螺栓孔沉孔毛刺去除
8. 正面轮辐毛刺去除。
毛刺整修作业指导书
共1页 第1页
2净重(g)10.2
首检
巡检
1器具领取1
2
修剪
1234
批准日期
标记处数更改文件号
日期
控制要求:零件表面不允许有划痕,污渍,过刀处因光滑,毛刺无沾附,未修断缺陷。
修毛刺后状态
C 100%自检3件
2件/小时
修毛刺过程
操作要点:用修剪刀将图示毛刺进行修整与被修面平齐。
作业工步
检验特殊特性
评价技术操作者
目测窗口毛刺
排气飞边
项目工序名称
整修材料规格/牌号
料口毛刺
小方孔孔口毛刺
零件控制
操作者领取修剪刀,周转盒
用修剪刀依下图顺序及所示部位将毛刺修平。
签字
补充说明:修理好的零件用气枪进行清理后包装。
异常情况处理:识别→隔离→重修毛刺
核心小组
修毛刺前状态
产品特性要求
修毛刺后,零件表面光洁,无划痕、污渍等,过刀处应光滑,毛刺无沾附,未修断缺陷。
管理要求
操作步骤:
标记工步号
外壳
零件名称
修 剪 作 业 指 导 书
XX市XX有限公司
ZD/QJ-60-2013
文件编号零件图号
工序号
POM(5%GF)白色。
- 1、下载文档前请自行甄别文档内容的完整性,平台不提供额外的编辑、内容补充、找答案等附加服务。
- 2、"仅部分预览"的文档,不可在线预览部分如存在完整性等问题,可反馈申请退款(可完整预览的文档不适用该条件!)。
- 3、如文档侵犯您的权益,请联系客服反馈,我们会尽快为您处理(人工客服工作时间:9:00-18:30)。
3.0注意事项
3.1
测量仪的使用参见其操作指导书;
3.2
戴好手指套操作;
3.3
注意工作台面保持清洁;
编制/日期
会签/日期
审核/日期
批准/日期
生效/日期
编号:E-SIP-
版本:00/00
页码:第2页共2页
毛刺检验标准作业指导书
版本
变更内容
变更日期
备注
编号. 版本: 页码
E-SIP-2027
00/00
第1页共2页
毛刺检验标准作业指导书
1.0目的和规范:
规范毛刺作业首检、巡检制度,确保制片极片的毛刺满足工艺标准和品质要求。
适用于毛刺作业首检、巡检。
2.0工装、检验步骤
工装、夹具、设备、仪器
辅料
2.5元测量仪
碎布
NO
检测步骤
检测要点
2.01
用碎布将极片边缘擦拭2-3遍,擦粉方向由极片头部顺着边缘 擦向尾部。(如图一)
1、毛刺测量时机:
a、每次首检进行时;
b刀模累积使用50小时后;
c、刀模磨刀后;
2、将毛刺数据记录在《毛刺巡检 记录表》上;
2.02
将冲切极片放在测量仪工作台面上;
2.03
选取镜头焦距为4.5X档,其放大倍数为135倍,测量极片毛 刺
2.04
以极片某一边为基准线,测量其突出部分至基准线的距离d