年产150万吨中厚板车间工艺设计
某中厚板厂车间设计与生产工艺流程的制定

某中厚板厂车间设计与生产工艺流程的制定1. 引言本文档旨在介绍某中厚板厂车间的设计与生产工艺流程的制定。
这些工艺流程的制定将有助于提高生产效率和产品质量,并确保车间的安全性。
本文档将从车间设计和生产工艺两个方面进行详细介绍。
2. 车间设计某中厚板厂车间的设计是确保生产过程顺利进行的关键。
以下是车间设计的要点:2.1 布局设计车间的布局设计需要考虑到生产流程的连贯性和人员的安全。
应将生产设备根据工序进行合理布置,以减少人员和物料的移动距离,并确保设备之间的安全间隔。
合理的布局设计能够提高生产效率和人员工作的舒适度。
2.2 空间规划车间的空间规划应根据生产设备的尺寸和数量进行合理划分。
不同工序的设备应根据工艺流程顺序进行排列,以便流程的顺畅进行。
在规划车间空间时,还需要考虑到人员的通行和安全之间的协调。
2.3 照明和通风良好的照明和通风系统对于车间的安全和生产效率至关重要。
应根据车间的大小和工作场所的需求安装合适的照明设备,并确保照明充足、无阻碍。
通风系统应能够及时排除车间内的有害气体和粉尘,以保证员工的健康和工作环境的适宜性。
3. 生产工艺流程的制定制定良好的生产工艺流程有助于提高生产效率和产品质量。
以下是生产工艺流程的制定细节:3.1 原材料准备生产流程的第一步是原材料的准备工作。
在某中厚板厂,原材料主要是金属板材。
原材料应经过检验和选择,确保其质量符合产品要求。
同时,应确保原材料的供应充足,以避免生产停滞。
3.2 加工工艺加工工艺是生产过程中最关键的环节之一,对产品的质量和性能有直接影响。
在某中厚板厂,加工工艺包括切割、弯曲、冲孔和焊接等步骤。
针对每个工序,应制定详细的工艺参数,以确保产品的尺寸和形状符合设计要求。
同时,应合理选择和配置加工设备,以提高生产效率。
3.3 质量控制质量控制是确保生产产品符合质量要求的重要环节。
在某中厚板厂,质量控制包括原材料检验、加工过程中的自检和互检,以及最终产品的质量检测。
某中厚板厂车间设计与生产工艺流程的制定
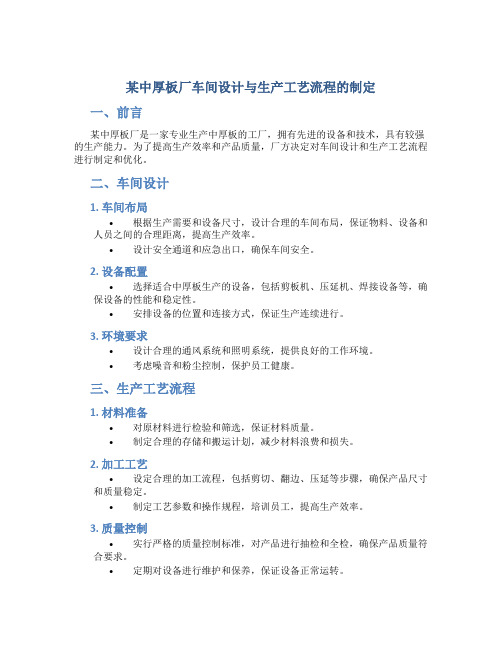
某中厚板厂车间设计与生产工艺流程的制定一、前言某中厚板厂是一家专业生产中厚板的工厂,拥有先进的设备和技术,具有较强的生产能力。
为了提高生产效率和产品质量,厂方决定对车间设计和生产工艺流程进行制定和优化。
二、车间设计1. 车间布局•根据生产需要和设备尺寸,设计合理的车间布局,保证物料、设备和人员之间的合理距离,提高生产效率。
•设计安全通道和应急出口,确保车间安全。
2. 设备配置•选择适合中厚板生产的设备,包括剪板机、压延机、焊接设备等,确保设备的性能和稳定性。
•安排设备的位置和连接方式,保证生产连续进行。
3. 环境要求•设计合理的通风系统和照明系统,提供良好的工作环境。
•考虑噪音和粉尘控制,保护员工健康。
三、生产工艺流程1. 材料准备•对原材料进行检验和筛选,保证材料质量。
•制定合理的存储和搬运计划,减少材料浪费和损失。
2. 加工工艺•设定合理的加工流程,包括剪切、翻边、压延等步骤,确保产品尺寸和质量稳定。
•制定工艺参数和操作规程,培训员工,提高生产效率。
3. 质量控制•实行严格的质量控制标准,对产品进行抽检和全检,确保产品质量符合要求。
•定期对设备进行维护和保养,保证设备正常运转。
四、总结某中厚板厂车间设计和生产工艺流程的制定,是为了提高生产效率和产品质量,确保工厂的可持续发展。
通过合理的车间设计和生产工艺流程制定,可以实现生产流程的规范化和标准化,提高生产效率和产品质量,满足市场需求。
最后,希望厂方能根据本文档提供的建议和指导,不断优化和改进车间设计和生产工艺流程,使中厚板产品更具竞争力。
中厚板生产工艺流程

中厚板生产工艺流程中厚板是一种常用的金属材料,广泛应用于建筑、机械制造、船舶制造等领域。
其生产工艺流程包括原料准备、熔炼、铸造、轧制、切割和成品检验等多个环节。
下面将详细介绍中厚板的生产工艺流程。
1. 原料准备中厚板的主要原料是铁矿石、焦炭和石灰石。
在生产过程中,还需要添加一定比例的废钢和合金元素。
这些原料首先要进行筛选、混合和配比,确保原料的化学成分和物理性能符合生产要求。
2. 熔炼原料混合后,要将其送入高炉进行熔炼。
高炉是将原料加热至高温并进行还原反应的设备,通过高炉熔炼可以得到铁水。
铁水中含有大量的碳和其他杂质,需要进一步精炼才能得到合格的铁水。
3. 铸造经过精炼的铁水被倒入铸造模具中,进行铸造。
铸造是将铁水倒入模具中,通过冷却凝固形成铸坯的过程。
铸坯的形状和尺寸与最终产品相近,但表面粗糙,需要经过轧制进行加工。
4. 轧制铸坯经过加热后,要进行轧制。
轧制是通过轧机对铸坯进行加热、压制和拉伸,使其逐渐变薄并得到所需的尺寸和形状。
轧制是中厚板生产中最关键的环节,直接影响产品的质量和性能。
5. 切割经过轧制后的中厚板要进行切割,得到符合要求的尺寸和长度。
切割通常采用火焰切割、等离子切割或机械切割等方式进行,确保产品的尺寸精度和表面质量。
6. 成品检验最后,切割后的中厚板要进行成品检验。
检验包括外观质量、尺寸精度、化学成分和力学性能等多个方面。
只有通过严格的检验,产品才能出厂并投入使用。
以上就是中厚板生产的工艺流程,每个环节都需要精心设计和严格控制,以确保产品质量和性能。
中厚板作为重要的金属材料,在工业领域有着广泛的应用前景,其生产工艺的不断改进和完善,将进一步推动相关行业的发展。
热轧中厚板生产车间设计

热轧中厚板生产车间设计热轧中厚板生产车间设计本设计选用16mm×4500mm规格的中厚板作为典型产品。
通过新工艺、新工艺的应用,设计了优化的生产方案。
完成了轧制参数的计算和相对强度校核,并计算了理论年产量。
然后选择车间的主辅助设备,确定主设备之间的距离,计算出相应的设施面积。
最后,根据设计参数,提出了车间布局设计方案,并绘制了车间布局示意图。
1.3 我国中厚板生产现状1.4 中厚板生产的新技术以及发展趋势1.5设计目的以及主要内容第2章产品大纲的确定和金属平衡表的编制2.1 产品方案的制定2.1.2 编制产品方案的原则2.2 原料的种类和技术要求2.2.1 原料的类别2.2.2 原料质量要求2.3.1 制定金属平衡表第3章生产工艺流程的制定3.1.1 制定生产工艺流程的主要依据3.1.2 工艺流程简述3.2 控制轧制与冷却3.2.1 控制轧制原理3.2.2 控制冷却的主要方式3.3 典型产品的工艺制度及校核3.3.1 原料的尺寸3.3.6 轧制温度的确定第4章主要生产设备的选择4.1 加热炉的选择4.3 4.3高压水除磷装置4.4 剪切设备的选择4.5 矫直机的选择4.6 冷却设备的选择4.6.1 加速冷却设备4.8 无损检测设备的选择5.1.1 研究轧机轧制图表的意义5.1.2 轧制图表的基本形式及其特征5.1.3 轧制图表的计算5.2 轧钢车间年产量5.2.1 典型产品小时产量5.2.2 轧钢机平均小时产量5.2.3 轧钢车间年产量计算第6章车间平面布置6.1 平面布置的原则6.2 金属流程线的确定6.3 主要设备间距的确定6.3.1 加热炉及其前后设备间距6.3.2 轧机及其前后设备间距6.4 仓库面积计算6.4.1 原料仓库面积的计算6.4.2 中间仓库面积计算6.4.3 成品仓库面积的计算6.5 车间平面布置示意图第7章主要经济技术指标及环境保护。
中厚板生产压下规程设计
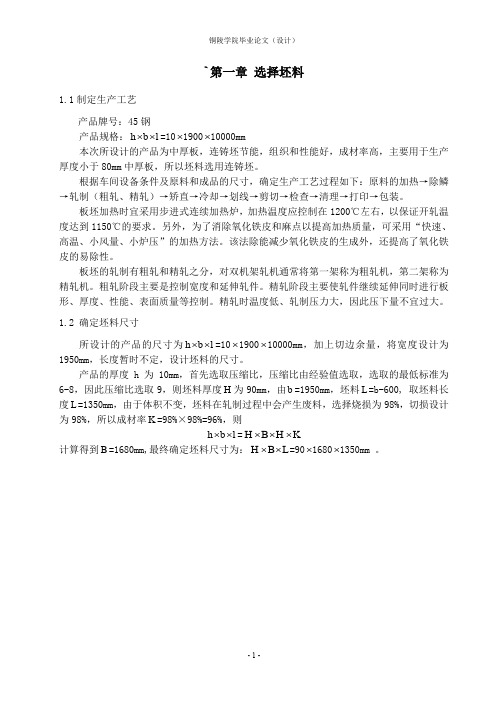
`第一章选择坯料1.1制定生产工艺产品牌号:45钢产品规格:l⨯=10⨯1900⨯10000mmbh⨯本次所设计的产品为中厚板,连铸坯节能,组织和性能好,成材率高,主要用于生产厚度小于80mm中厚板,所以坯料选用连铸坯。
根据车间设备条件及原料和成品的尺寸,确定生产工艺过程如下:原料的加热→除鳞→轧制(粗轧、精轧)→矫直→冷却→划线→剪切→检查→清理→打印→包装。
板坯加热时宜采用步进式连续加热炉,加热温度应控制在1200℃左右,以保证开轧温度达到1150℃的要求。
另外,为了消除氧化铁皮和麻点以提高加热质量,可采用“快速、高温、小风量、小炉压”的加热方法。
该法除能减少氧化铁皮的生成外,还提高了氧化铁皮的易除性。
板坯的轧制有粗轧和精轧之分,对双机架轧机通常将第一架称为粗轧机,第二架称为精轧机。
粗轧阶段主要是控制宽度和延伸轧件。
精轧阶段主要使轧件继续延伸同时进行板形、厚度、性能、表面质量等控制。
精轧时温度低、轧制压力大,因此压下量不宜过大。
1.2 确定坯料尺寸所设计的产品的尺寸为l⨯=10⨯1900⨯10000mm,加上切边余量,将宽度设计为bh⨯1950mm,长度暂时不定,设计坯料的尺寸。
产品的厚度h为10mm,首先选取压缩比,压缩比由经验值选取,选取的最低标准为6-8,因此压缩比选取9,则坯料厚度H为90mm,由b=1950mm,坯料L=b-600, 取坯料长度L=1350mm,由于体积不变,坯料在轧制过程中会产生废料,选择烧损为98%,切损设计为98%,所以成材率K=98%×98%=96%,则h⨯⨯=KblH⨯⨯⨯HB计算得到B=1680mm,最终确定坯料尺寸为:L⨯=90⨯1680⨯1350mm 。
H⨯B第二章变形量分配2.1 确定轧制方法先经过二辊轧机纵轧一道,在不考虑切边的情况下,使板坯长度等于成品宽度,然后转90°横轧到所需规格。
2.2 确定道次压下量坯料尺寸:LBH⨯⨯ =90⨯1680⨯1350mm,则总的压下量为90-10=80mm。
中厚板压下规程设计

一.制定生产工艺及工艺制度1.生产工艺:选择坯料——原料清理——加热——除鳞——纵轧一道(使宽度接近成品宽度)——转90˚横轧到底——矫直——冷却——表面检查——切边——定尺——表面尺寸形状检查——力学性能试验——标记——入库——发货2.工艺制度:在保证压缩比的条件下,坯料尺寸尽量小。
加热时出炉温度应在1120˚—1150˚,温度不要过高,以免发生过热或过烧现象;用高压水去除表面的氧化铁皮,矫直时选用辊式矫直机矫直,开始冷却温度一般要尽量接近终轧温度,轧后快冷到相变温度以下,冷却速度大多选用5—10˚C或稍高一些。
切边用圆盘式剪切机进行纵剪,然后用飞剪定尺。
二.选择坯料1.根据生产经验和实践,目前生产中厚板选择连铸坯已成为主流,所以选择连铸坯2.坯料尺寸的确定坯。
(1)坯料厚度的确定:根据经验,压缩比在6—10之间较好,本设计取10,由成品厚度h=13mm知H=10h=130mm。
(2)坯料宽度的确定假设先轧两道,压下量分别为20mm和10mm,且设两道轧后其长度等于宽度。
假设轧后金属烧损不计,考虑切头尾,切边。
在我国切头尾一般为500mm—2500mm取Δl=500mm,切边Δb=100mm,由体积不变定理得Bˊ×Lˊ×[H-(20+10)]=(l+2×500)×(b+2×100)×13因为Bˊ=Lˊ所以Bˊ=Lˊ=(9000+2×500)(1900+2×100)×13/[130-(20+10)]=1650mm(3)坯料长度的确定由H,B,Bˊ,Lˊ由体积不变定理得H×B×L=Hˊ×Bˊ×Lˊ得L=1270mm三.变形量分配1.根据经验,中厚板压下量在Δh=12mm左右,这里取Δh=12mm2.分配各道次压下量,计算各道次变形程度,轧件尺寸及轧制道次(1)由H=130mm,h=13mm,取轧制道次n=12(二辊7道四辊五道)(2)第一道,先用展宽轧制把坯料的宽度B轧成b(或接近b)且不考虑长度变化由体积不变定理得B×L×H=B×L×(H-Δh1)得Δh1=17mm则变形程度ε1=Δh/H×100%=13.08%轧后轧件尺寸为113×1900×1270mm同理其余道次压下量分配,变形程度,轧件尺寸如下表所示四.设计变形工具1.设计二辊(1)辊身长度L:由L=bmax+a bmax=1900mm 当b=1000-2500mm a=150-200mm 取a=200mm所以L=1900+200=2100mm(2)辊径尺寸中厚板轧机L/D=2.2-2.8 取L/D=2.6 得D=808mm 取810mm(3)辊颈尺寸查表3-5 取d/D=0.75(轧钢机械邹家祥主编) 得d=608mm取d=600mm辊颈长度l 取d/l=1 得l=600mm(3)辊头设计因为对于中厚板轧机来说轧辊调整行程比较大,倾角在8˚-12˚间所以应选择万向辊头。
中厚板轧钢车间设计
中厚板轧钢车间设计创建时间:2008-08-02中厚板轧钢车间设计 (design of plate mill)以板坯或扁锭为原料,经加热轧制生产中厚钢板的车间设计。
中国规定,钢板厚度大于4~20mm 的为中板,厚度大于20~60mm的为厚板,厚度大于60mm的为特厚板,统称为中厚板,中厚钢板主要用于造船、建筑、机器制造、交通运输以及军事工业等部门,还可用作制造螺旋焊管,UOE焊管与焊接钢梁的原料。
在工业发达国家,中厚钢板的产量占钢材总产量的10%~20%。
厚度为4~25.4mm的中厚钢板也可以在带钢热轧机上生产。
车间设计的原则及方法见轧钢厂设计。
简史 18世纪初,西欧开始用二辊轧机轧制出小块中厚钢板。
1854年欧洲建成用蒸汽机传动的二辊可逆式中厚板轧机。
1864年美国建成三辊劳特式中厚板轧机。
1891年美国建成世界上第一台四辊可逆式中厚板轧机,1918年美国又建成主要生产装甲钢板,其辊身长5000mm以上的宽厚板轧机。
以后,世界上又陆续出现了双机架、半连续式、连续式中厚板轧机。
20世纪70年代是中厚板车间建设得最多的时期,不少轧机是4000~5500mm的双机架宽厚板轧机。
1871年中国福州船政局已开始轧制造船板,1907年汉冶萍公司建设了2440mm中板轧机。
1936年在鞍山建成了第一套2300mm三辊劳特式中板轧机。
1958年及1966年鞍山钢铁公司和武汉钢铁公司分别建成了2800mm中厚板轧机,其粗轧机为二辊式、精轧机为四辊式。
1978年设计建成了舞阳钢铁公司4200mm宽厚板车间,1990年上海第三钢铁厂的4200/3300mm厚板车间投产。
坯料选择有扁锭、初轧板坯、连铸板坯和锻坯。
在满足轧制压缩比的条件下,尽可能采用连铸板坯为原料。
某些特殊钢种,根据需要采用锻坯。
设计规模和产品方案设计规模主要取决于轧机和辅机性能、设备组成、市场需求和坯料条件等。
轧机尺寸、组成与设计规模的关系见表1。
年产0万吨中厚板生产车间工艺设计实现可行性方案
年产10万吨中厚板生产车间工艺设计实现可行性方案刚坐下,泡了一杯茶,思绪就飘到了这个年产10万吨中厚板生产车间的工艺设计上。
这可是个大工程,得好好梳理一下。
咱们就直接进入主题吧。
一、项目背景咱们这个项目,主要是为了满足市场对中厚板的需求,提高企业的生产效率和产品质量。
年产10万吨,听起来就挺有气势的。
不过,要实现这个目标,还得从工艺设计入手。
二、工艺流程设计1.原料准备咱们得准备好原料。
这个原料嘛,主要是铁水。
铁水要从炼钢厂运过来,经过预处理,去除杂质,保证原料的纯净度。
2.热轧就是热轧环节。
这个环节很重要,直接关系到中厚板的质量。
热轧机要选择合适的型号,保证轧制速度和轧制力。
同时,还要注意控制轧制温度,保证板材的力学性能。
3.冷轧热轧后的板材还需要进行冷轧。
冷轧可以进一步提高板材的精度和表面质量。
这个环节要选用高性能的冷轧机,确保轧制效果。
4.热处理冷轧后的板材要进行热处理,以消除内应力,改善力学性能。
热处理的方式有退火、正火、淬火等,根据产品的要求来选择。
5.表面处理热处理后的板材要进行表面处理,提高耐腐蚀性能。
这个环节可以采用镀锌、涂漆等方式。
6.切割根据客户需求,对板材进行切割。
切割方式有激光切割、等离子切割等,保证切割精度和效率。
三、设备选型1.热轧机:选择高速、高精度、节能型的热轧机。
2.冷轧机:选择性能稳定、精度高的冷轧机。
3.热处理设备:选择自动化程度高、节能环保的热处理设备。
4.表面处理设备:选择高效、环保的表面处理设备。
5.切割设备:选择精度高、效率高的切割设备。
四、生产组织与管理1.人员配置(1)项目经理:负责整个项目的策划、组织和实施。
(2)工艺工程师:负责工艺流程的制定和优化。
(3)设备工程师:负责设备选型和维护。
(4)质量工程师:负责产品质量控制。
(5)生产班长:负责生产线管理。
2.生产计划(1)根据订单需求,制定生产计划。
(2)合理分配生产任务,确保生产线高效运行。
中厚板车间毕业设计模版
Abstract
In this paper,a heavy plate plant which produces 230 ten-thousand tons per year was designed in this thesis .The typical product is 16Mn,42×4600mm. The design is simply introduced the development of production technology of the heavy plate in a whole design, the disparity gap of the home and abroad and the heavy plate means in this design ,and adopt the new technology. The main include: 2 step-beam furnace, reversal device high-pressure-water descaling unit, 1 four-roll reservable rough mill, as well as various appurtenances. According to the designed annual capacity, and considering market prospects of the products, the products’ scheme and metal balance were designed reasonably. The rolling system includes: press-down system, velocity system and temperature system. Then, the roll force was calculated; the electromotor load and the roll strength were checked. the electromotor load and the roll strength were checked.And maked out a scientific and reasonable heavy medium plate design scheme . A plant layout drawing was also accomplished in the design, An English paper and its translation by author were attached to the thesis. The features of the designed workshop include: of high strength of products and mechanical property of the products, adoption of advanced processing technology, and environmental protection consideration. The plant achieves high production in lower consumption.
年产180万吨中厚板生产车间工艺设计毕业设计(可编辑)
年产180万吨中厚板生产车间工艺设计毕业设计设计说明本设计为年产量180万吨的中厚板车间,通过对中厚板市场的调研,介绍了中厚板的发展状况,分析了中厚板的市场需求,并针对目前的技术状况,制定出了合理的产品大纲和金属平衡表。
以典型产品Q235(10mm×1700mm×6000mm、25mm×1000mm×6000mm、4010mm×1450mm×4000mm)钢板为基础,通过确定典型产品的工艺流程,确定了轧机的布置形式和车间各设备的选用,并制定出典型产品合理的压下规程,计算出轧制力能参数,如:轧制力的计算、变形抗力的计算和传动力矩的计算等。
校核轧辊强度并计算电机的容量,以选用合适的轧辊和电机。
确定车间工作制度和年工作时间,计算了轧机的年产量,根据典型产品的工艺和轧件的尺寸等,确定车间平面布置,如合理的设备间距、仓库面积等,并画出车间平面布置图。
分析车间的综合经济指标。
并采取有效的环境保护措施,如车间的绿化、废气和废渣的再回收等。
关键词:中厚板车间,产品大纲、金属平衡表、轧制力、传动力矩Design NotesThe design for the annual production of 180 million tons of plate plant, plate market research, the development of the plate, the plate market demand, and the current state of technology, to develop aa reasonable outline of the products and metal balance sheet. Typicalproduct Q235 10mm × 1700mm × 6000mm, 25mm × 1000mm × 6000mm, 4010mm × 1450mm × 4000mm steel-based, to determine the typical products of the process, to determine the the mill arrangement of workshop equipment selection, and to develop typical products and reasonable reduction procedures to calculate the rolling force parameters, such as: rolling force calculation, the calculation of the deformation resistance and transmission torque calculation. The check rolls intensity and calculate the capacity of the motor to the appropriate choice of rolls and motor. To determine workshop work systems and working hours, calculated the annual production of the mill, according to the typical product of the process and the size of the rolling determine workshop layout, such as device spacing, warehouse area, and draw the workshop floor planAnalysis of the economic indicators of the workshop. And to take effective environmental protection measures, such as the greening of the workshop, waste gas and waste recycling and so on.Keywords: plate workshop, outline, metal balance sheets, rolling force, deformation resistance, drive torque目录设计说明 (1)1 前言 (8)1.1我国中厚板生产技术现状81.1.1中厚板轧钢生产线的工艺装备81.1.2中厚板的生产技术是产品的核心 91.2中厚板轧机生产工艺的发展趋势91.2.1中厚板轧机生产工艺方案91.2.2产品质量及交货状态101.3我国中厚板轧机的发展方向121.4国内中厚板轧机的改造131.4.1围绕提高轧机的目能力水平进行改造131.4.2围绕提高装备水平进行改造141.4.3板坯连铸比151.4.4轧机151.4.5新技术和新工艺 152 中厚板产品方案 (16)2.1编制产品大纲162.2编制金属平衡表162.2.1成材率概念162.2.2金属平衡分析172.2.3Q235钢板的化学成分182.2.4Q235钢板尺寸偏差193 中厚板的生产工艺和轧制区的设备 (21)3.1 中厚板生产工艺流程213.2 典型产品的工艺流程213.3 轧制区设备选择253.3.1 中厚板轧机型式253.3.2 中厚板轧机的布置253.3.3 轧机主机列 263.3.4工作机座的结构 263.3.5 换辊装置293.3.6 轧制区其它设备293.4 辅助设备的选择293.4.1 加热炉选择 293.4.2 剪切机选择 313.4.3热矫直机选择333.4.4 冷床设备选择343.4.5钢板修磨台架选择354 轧机力能参数的确定…………………………………………………………374.1 轧制力计算374.1.1 确定变形制度374.1.2 计算轧制力 384.2 传动力矩计算机及电机校核464.2.1 各道传动力据计算474.2.2 轧机主电机校核524.3轧辊强度校核634.3.1 粗轧机轧辊强度校核634.3.2 精轧机轧辊强度校核664.4 四辊轧机轧辊接触应力的校核 675 轧钢机产量计算 (70)5.1 轧钢机工作图表705.1.1 研究轧钢机工作图表的意义 705.1.2 轧机工作图表705.2轧钢机产量计算725.2.1轧机小时产量计算725.2.2轧钢机平均小时产量735.2.3轧钢机年产量746 车间平面布置 (75)6.1车间平面布置原则 756.2车间工艺平面布置 756.3设备间距的确定766.3.1加热炉间距离766.3.2加热炉到粗轧机距离766.3.3 粗轧机到精轧机距离766.3.4其它设备间距离的确定766.4仓库面积的确定776.4.1原料仓库面积的确定776.4.2成品仓库面积确定786.5车间其它设施面积的确定786.5.1厂方跨度布置786.5.2厂房跨度大小796.5.3柱距尺寸796.5.4吊车轨面标高797 车间技术经济指标……………………………………………………………817.1 各类材料消耗指标817.1.1金属消耗817.1.2燃料消耗827.1.3电能消耗827.1.4轧辊消耗827.1.5水的消耗827.2 综合技术经济指标838 轧钢厂的环境保护与综合利用 (85)8.1 轧钢厂的环境保护858.1.1 绿化858.1.2 各类有害物质的控制与防治 858.1.3 噪音的防治 858.1.4 水质的处理 868.2 轧钢厂的节能与综合利用868.2.1 轧钢厂的节能868.2.2 轧钢厂的综合利用86参考文献 (88)致谢………………………………………………………………………………891 前言近年来,我国中厚板轧机在品种开发、轧机改造、研究新工艺和新技术以及使用连铸坯等方面取得了较大的成绩,但据有关专家预测,7>2014年需中厚板约7000万t;目前我国现有的中厚板轧机的总生产能力为5300万t左右。
- 1、下载文档前请自行甄别文档内容的完整性,平台不提供额外的编辑、内容补充、找答案等附加服务。
- 2、"仅部分预览"的文档,不可在线预览部分如存在完整性等问题,可反馈申请退款(可完整预览的文档不适用该条件!)。
- 3、如文档侵犯您的权益,请联系客服反馈,我们会尽快为您处理(人工客服工作时间:9:00-18:30)。
.................大学本科生毕业设计开题报告题目:年产150万吨中厚板车间工艺设计学院:冶金与能源学院专业:材料成型及控制工程班级:姓名:学号:指导教师:2015年11 月15 日一.选题背景1.1题目来源冶金行业经过了近8年的高速发展,行业的钢材产能已经达到近6亿吨/年。
已有和在建的中厚板生产线近70条,中厚板生产能力达到接近7000万吨/年。
但是国际金融危机的影响和国内经济周期的调整,钢铁产品市场成了典型的买方市场。
冶金企业如何在这一轮经济调整中,实现技术和产品的转型成了决定企业生存的关键。
各中厚板生产厂纷纷根据自身的技术装备特点、技术研发能力、市场客户需求确定自己的产品战略定位。
综合实力强的企业,全力体现出产品的差异化战略,坚持不懈地开发生产其他企业无法生产或难于生产的市场短线、高档产品。
高档次产品开发离不开性能控制技术,性能控制的新技术不仅提高钢板的性能,还可以带来生产成本的降低。
1.2项目概述:经过对国内外中厚板市场现状的分析以及前景预测,综合对当地各种物料供应、能源等其它资源的分析,我们选择区域与资源优势居一体的唐山曹妃甸地区作为建厂厂址,设计一座年产量150万吨4300热轧中厚板车间,并且能够生产规格齐全、性能优良,能满足市场需求的产品。
1.3中厚板简介中厚钢板:厚度大于4mm的钢板属于中厚钢板。
其中,厚度4.0-20.0mm的钢板称为中厚板,厚度20.0-60.0mm的称为厚板,厚度超过60.0mm的为特厚板。
中厚板的用途:中厚板主要用于建筑工程、机械制造、容器制造、造船、桥梁等行业,并且随着国民经济建设其需求量非常之大,范围也十分广。
(1)造船钢板:用于制造海洋及内河船舶船体。
要求强度高、塑性、韧性、冷弯性能、焊接性能、耐蚀性能都好。
(2)桥梁用钢板用于大型铁路桥梁。
要求承受动载荷、冲击、震动、耐蚀等。
(3)锅炉钢板:用于制造各种锅炉及重要附件,由于锅炉钢板处于中温(350℃以下)高压状态下工作,除承受较高压力外,还受到冲击,疲劳载荷及水和气腐蚀,要求保证一定强度,还要有良好的焊接及冷弯性能。
(4)压力容器用钢板:主要用于制造石油、化工气体分离和气体储运的压力容器或其它类似设备,一般工作压力在常压到320kg/cm2甚至到630kg/cm2,温度在-20~450℃范围内工作,要求容器钢板除具有一定强度和良好塑性和韧性外,还必须有较好冷弯和焊接性能。
(5)汽车大梁钢,用于制造汽车大梁(纵梁、横梁)用厚度为2.5-12.0mm的低合金热轧钢板。
由汽车大梁形状复杂,除要求较高强度和冷弯性能外,要求冲压性能好。
1.4我国中厚板生产技术现状1.4.1中厚板轧钢生产线的工艺装备中厚板轧钢生产线的工艺装备是在钢坯质量一定的前提下保证最终产品质量的重要环节。
以往的轧钢厂是以轧机为中心,其余的装备往往是因陋就简,尤其是在以普材为主的生产厂更是如此。
中厚板的生产尽管在加热和精整工序上考虑了一些如不产生划伤和剪切质量等因素,但是随着产品质量、品种规格、产品档次和用途等市场因素的变化,各生产厂已开始逐步重视并对整个工艺线进行分析、升级和改造。
由于历史原因,我国目前大部分中厚板轧机生产线的总体装备水平与国外先进水平存在一定的差距。
主要体现在:1)规模小,装备水平低;2)加热炉大部分为推钢式,加热能力和质量保证能力差;3)后部精整能力不足,因陋就简,如矫直机(几乎没有冷矫),纵剪能力达到30 mm以上的不多,且剪切质量差。
在线无损探伤线、热处理和喷丸等工艺大部分工厂没有配备;4)核心技术不精、不专,主要体现在控温、辊型设计、水冷和控制轧制等,尤其是独特的、具有自主知识产权的工艺、产品不多。
与国外先进企业比较,国内中厚板轧钢厂尽管在装备上存在着一定的差距,但近几年一些大钢厂正在逐步引进、消化和改造一批中厚板生产设备和工艺,如首钢和济钢的3 500 mm轧机、鞍钢的4 300 mm轧机和宝钢的5 000 mm轧机等陆续投产;首秦公司的4 300 mm轧机,天津、唐钢和福建三明的3 500mm轧机等一大批即将投产的中厚板轧机,将逐渐参与中厚板的市场竞争,这对我国的中厚板生产企业提升整体装备水平、提升产品档次和质量将会起到极大的促进作用1.4.2中厚板的生产技术是产品的核心随着国内中厚板产能增加、工艺不断升级改造和引进新的工艺装备,产品档次的提升和质量的提高应源于工艺技术的开发和应用。
钢铁产品的现代技术主要有4个方面,即钢质洁净技术、微合金化技术、晶粒细化技术和尺寸、表面精准化技术。
这4方面的技术集成最终体现在钢材性能最佳和生产成本最低。
钢质洁净技术是冶炼专业的工作,但后3个方面的技术将与轧制工艺技术紧密相关。
微合金化的设计与轧制工艺紧密配合,形成细晶强化。
实践证明:细晶强化改变了以往碳当量的强化机理;微合金元素V、N-V、Nb和Ti等合金元素的不同组合,在一定的轧制工艺条件下,以析出强化、固溶强化的方式提高钢材的综合性能。
1.5中厚板轧机生产工艺的发展趋势1.5.1中厚板轧机生产工艺方案一种是传统的常规中厚板生产线,如三辊式劳特轧机、单机架四辊轧机、双机架两辊粗轧+四辊精轧、双机架四辊粗轧+四辊精轧机组。
另外一种是20世纪80年代逐步发展起来的,即可单张钢板轧制,又可采用卷轧方式生产中厚板。
宽炉卷轧机产品定位于中低档,适合单一品种、大批量、高效率,单机架宽炉卷轧机年生产规模110万吨,投资较高。
韶钢一期新建单机架3500mm 轧机,生产规模80万吨,预留二期上热卷箱及卷取机的位置,总投资14亿元(外汇4200万美元);安阳钢厂新建中厚板炉卷车间,生产能力110万吨,总投资约18亿元。
常规中厚板轧机产品定位于中高档,具有投资省、见效快、备品备件国产化率高等优点,如北台、济钢双机架3500 mm中厚板轧机,年生产能力140万吨(生产普碳钢时),投资约12~14亿元。
1.5.2中厚板车间现状及发展趋势(1)主轧机的型式从机架的结构来看有二辊可逆式、三辊劳特式、四辊可逆式、万能式和复合式之分,而现代建设的轧机大部分是四辊可逆式和万能式,而二辊可逆式和三辊劳特式在现代轧机建设中已不多见。
新建设中厚板轧机宽度尺寸在三米以上;四辊轧机的结构趋于稳定和成熟,为了增加轧机强度和刚度,增大机架牌坊立柱断面尺寸和重量、支撑辊直径,以承受更大的轧制力。
一般单位轧制力都在20MN/mm以上,单位功率在2KW/mm以上,刚度在20MN/mm 以上。
轧机尺寸在3500mm以上,轧制速度达5~7.8m/s,牌坊主柱截面在9000cm2以上,每片单重达300t吨以上,并采用快速换辊装置。
换一次工作轧辊只8-15min,换支撑辊只1h之内。
主传动采用交流电动机,带有HAGC、弯工作轧辊PC或CVC板形控制装置及近接γ射线测厚仪。
(2)加热炉步进式加热炉被公认为当代最先进的炉型。
老生产线中只有鞍钢厚板、武钢轧板、济钢中厚板、邯钢中板采用,而新建在建的生产线中有13条选用此炉型,比起我国原先普遍使用的推钢式加热炉在提高板坯质量、减少氧化、烧损等方面大大前进了一步。
从与轧制产能匹配角度和轧制品种考虑,宝钢的5.0m 轧机设置了2 座,首钢4.3m 轧机设置了3 座。
(3)快冷装置在生产高等级、高技术含量、高附加值产品时,一般都采用控制轧制技术工艺。
此技术的应用必须有良好的冷却系统相配合,新建和在建的生产线大多都装备了先进的快冷系统。
装置一般都采用DQ+U 形管层流的冷却型式,一些老生产线近几年也对冷却系统进行了改造,目前酒钢中板采用ADCO 气雾冷却,鞍钢厚板、新余中板、舞阳厚板、武钢轧板等采用U 形管层流冷却,首钢中板、南钢中板采用直流式层流冷却,都属于比较先进实用的装备。
(4)热矫直机2005 年以前大都采用辊式矫直机,此型式由于受辊径和辊距的配合限制,所以矫直板厚有一定范围,一般最厚与最薄之比为4,新生产线中大都采用有张力机能的新型矫直机。
其矫直最厚与最薄之比可以达到25,而且矫直力也可以增加一倍。
也有些老生产线对原有的矫直机进行了改造,如济钢中厚板采用了从法国进口的11 辊四重式矫直机,效果较好,矫直精度达1.5mm/m。
(5)冷床由于以前大多数生产线采用拉钢冷床,非但容易划伤钢板,也容易造成钢板冷却不均匀。
新建生产线的冷床大都采用步进格板式或盘辊式,有足够的面积放置钢板,不需要在冷床前进行热剪分段,对提高成材率有利。
也有一些老生产线对冷床进行了改进,如柳钢采用步进式冷床,浦钢和济钢采用了盘辊式,效果都不错[2]。
1.5.3国内外中厚板新产品新工艺新技术的开发近几年我国的中厚板品种开发主要围绕一些专用钢板的钢质纯净化、低碳高强化、耐高温、耐高压、耐断裂、耐腐蚀等方面展开,并取得了长足的进步:( 1) 新产品开发有15 家企业能生产X65 级别的管线钢,8 家能生产X70 级,宝钢、鞍钢、舞钢、武钢、济钢等具备了生产X80 级的能力,其中宝钢、鞍钢、武钢已能大批量生产,并于2005 年完成了X100 级的试验室工作。
宝钢、舞钢、武钢、鞍钢、马钢等能生产高级别的海洋石油平台用钢。
以及CORTEN 耐候桥梁板、BHW35 高压锅炉板、P20 塑料用模具板、N19 低温板、AH32-EH36 级和F 级船板、HT80 高强板,百万千瓦火电及核电用特厚钢板、25万千伏安以上变压器用高磁感低铁损取向硅钢等高附加值产品已经相继开发。
(2)新技术的应用1)热送热装技术为了节能和提高炉子加热能力,新建厂都很注意炼钢连铸和轧钢加热之间板坯运输、保温及调度等关系,做到生产管理一贯制,做到热装热送率达40%-70%以上,热装温度达450-680以上,吨钢燃耗降至0.8GJ以下,并在板坯仓库内设置保温坑或罩,尽可能提高板坯装炉温度。
目前,日本已实现了直接轧制,使燃料达到零耗。
2)控轧控冷技术将控轧与快冷有效地相结合在一起是中厚板生产技术的一大进步,这种工艺可显著地改善钢板性能,降低生产成本与节约贵重合金元素。
而中厚板轧机最适合于控轧控冷工艺,许多钢板都可用此工艺生产,某些方面其性能超过热处理钢板,有的厂已实现控轧率达60%以上。
条件好的厂以TMCP为主,而一般厂均以CR生产。
目前等轧方式都采用在轧机前后延伸辊道上多块钢板轧制来实现。
日本TMCP有快冷装置的称之为水冷型,而不用快冷的称之为非水型。
各公司都有自己专利,如新日铁为NIC,日本钢管为NCT,川崎为SCR和KTR,住友金属为SHT和SSC,神户为KONTROLL。
3)板形控制技术这是一项钢板三维立体形状的控制技术,目标是生产出尺寸偏差非常小、切头尾和切边极少、矩形、近似矩形及齐边(不切边或铣边)、性能均一的平直钢板。
此技术可扩大产品,生产出各种异形板。