培训材料1-白车身尺寸匹配控制
白车身重要尺寸
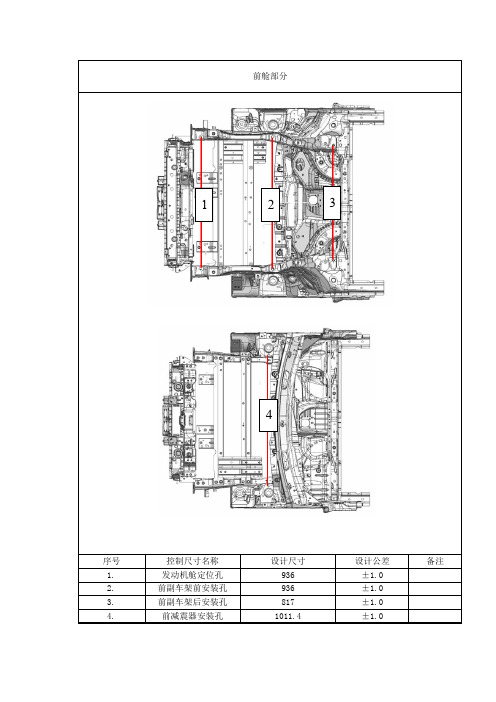
装点II 主驾驶座椅安
装点III 副驾驶座椅安
装点Ⅰ 副驾驶座椅安
装点Ⅱ 副驾驶座椅安
装点Ⅲ
设计尺寸 406
605.7 449.4
406 605.7 449.4
设计公差 ±1.0 ±1.0
±1.0 ±1.0 ±1.0
±1.0
备注
前舱部分
1
2
3
Байду номын сангаас
4
序号 1. 2. 3. 4.
控制尺寸名称 发动机舱定位孔 前副车架前安装孔 前副车架后安装孔 前减震器安装孔
设计尺寸 936 936 817
1011.4
设计公差 ±1.0 ±1.0 ±1.0 ±1.0
备注
地板部分
1
2
序号 1. 2.
控制尺寸名称 扭力梁安装孔 管梁安装点
设计尺寸 986 1260
设计公差 ±1.5 ±1.5
备注
侧围部分
1 2
3
序号 1. 2. 3.
控制尺寸名称 侧围主定位孔 侧围辅助定位孔 铰链安装孔
设计尺寸 1515 1548 1449
设计公差 ±1.0 ±1.0 ±1.5
备注
座椅装配尺寸
1
4
2 3
6
5
序号 1. 2. 3. 4. 5. 6.
控制尺寸名称 主驾驶座椅安
白车身制造过程尺寸控制方法PPT课件
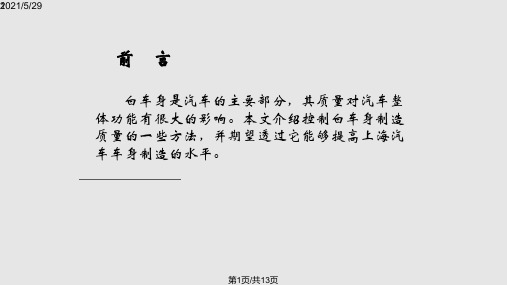
6
2021/5/29
第6页/共13页
6σ,是对一定数量的样本数据波动状况进行评价的阶段评价指 标。样本一般为20~30台。对于小样本离线检测,通常要求通 过数据分离提取出数据的波动项。须使数据具有平稳的统计特 性(近似正态分布)才可以进行6σ的计算。单点6σ计算每个点 波动标准差σ的6倍。从统计意义上讲,代表该点的实际尺寸有 99.73%的可能落在名义值的±3σ以内,因此可以认为表明了该 点数据的变动范围。整车6σ将全部测点的6σ从大到小进行排序, 取95百分位的点的6σ值作为该白车身的6σ值(如图)。
12
2021/5/29
第12页/共13页
感谢您的观看!
2021/5/29
13
第13页/共13页
4
2021/5/29
第4页/共13页
这两种典型的过程控制方法虽然都很有效,但是由于 车身制造工艺的复杂性使得车身上的产品过程监控测点数 多达几百个,这就给判断制造过程的稳定性带来了一定难 度。
5
2021/5/29
第5页/共13页
车身尺寸质量评价指标2mm工程
所谓的“2mm”指的是所有白车身的关键测点的波动(6σ) 值小于2mm。该技术对白车身尺寸质量的评定是以关键 测点的6σ表示,包括单个测点的6σ以及整车的6σ,并以 CII指数(持续质量改进指数)反映尺寸质量的长期变化 趋势。由于车身的测点数据主要是由三坐标测量机采集 的,受硬件条件的限制,采样频次较低,故不适合用 SPC的方法评价尺寸质量的稳定性。目前样板采用 “2mm工程”作为白车身尺寸质量评价的主要指标。
9
2021/5/29
第9页/共13页
车身车间在以先进 的2mm工程所提出 的6σ和CII指数作为 主要指标的同时, 结合尺寸通过率对 白车身尺寸整体水 平进行即时的评估, 并在此基础上建立 了相应的尺寸控制 流程。
白车身尺寸控制论文
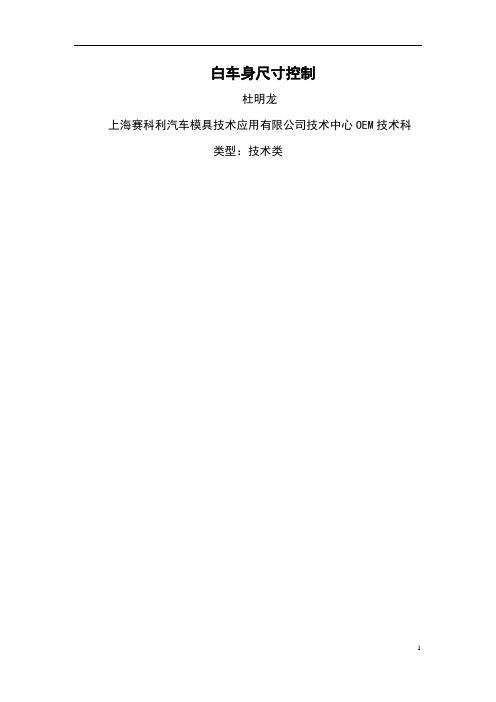
白车身尺寸控制杜明龙上海赛科利汽车模具技术应用有限公司技术中心OEM技术科类型:技术类摘要白车身的制造质量水平主要包含尺寸精度、焊接质量和外观质量等几个方面,其中,白车身尺寸精度是保证整车零部件装配精度的基础。
白车身的制造是由数百个具有复杂空间曲面的薄板冲压零件通过由数十个工位组成的生产线,其特点是大批量、快节奏,零件装配的定位、夹紧点在1000个以上,焊点多达4000~5000个。
白车身的制造过程复杂,影响因素众多,整车的制造尺寸精度取决于各方面因素的综合作用。
关键词:白车身尺寸控制目录第一章绪论 (4)第二章影响因素 (5)2.1.工装夹具 (5)2.2.零件偏差 (5)2.3.操作过程 (5)2.4.测量过程 (6)第三章控制方法 (7)3.1.基于测量的尺寸精度控制 (7)3.2.基于装配的尺寸精度控制 (8)结论 (9)参考文献 (10)第一章绪论现代汽车工业中车身制造的特点是制造系统庞大,往往包括上百个冲压件,几十套工装夹具,和上百个工序;制造工艺复杂,包括材料,冲压,焊接,涂装,总装等工艺流程。
这些特点就导致引起车身尺寸变异的偏差源很多,车身尺寸质量的控制就十分困难。
为了监控车身尺寸质量,就必须对零件、工装、操作、测量全程监控。
第二章影响因素2.1.工装夹具工装夹具是车身各零件定位和装配的载体。
车身主要由薄板冲压件组成,“321”定位原理在车身焊接夹具设计中已不适用,其第一基面上的定位点数目应大于3。
定位效果不仅取决于定位点的数目,还取决于定位点的布置形式。
工装夹具的保证能力是有效控制车身尺寸稳定性的关键。
在车身制造过程中,工装夹具的材料性能、结构设计以及夹具与零件的匹配情况等,都将影响到工装夹具长期使用的尺寸精度保证能力。
在车身生产过程中,基于冲压件尺寸相对于设计尺寸的偏差,会导致工装夹具与零件间产生不同程度的应力集中,长期作用将导致夹具变形和失效,保证能力降低。
我们应对工装夹具进行持续状态监控、潜在失效源排除,及时对故障工装夹具进行维护,消除其失效造成的尺寸偏差。
白车身质量培育焊装

活动
Activities
• 通过检查模具的状态,发现和改善问题 Concerns are identified and improved by checking status of dies - 以工装为基础,确认情况 Confirm the situation based on tooling - 确认公差 Confirm the tolerance
“2mm工程”的本质是建立以数据为基础的制造质量控制体系,通过对制造数据建模分析来识别车身 制造尺寸偏差源,保证车身制造工艺的稳定性,最终提高整车的配合精度。其核心是采用先进的车身测量 技术,建立从冲压工艺、加工装备到装配过程协调、一致、高效的测量系统,通过数据分析和积累,将人 为的经验管理上升到科学管理水平。
4-2. 车身公差设定介绍
分总成公差
外观公差 部件公差
4. 车身品质公差管理
4-3. 车身公差设定流程
车身设定公 差
质量功能展开
公差关系 设定公差 分总成设定
公差
外观公差 车身结构分析
可行性
OK
单件设定公 差
公差
NG
模具
设计制造
例) 4.5±1.5 平 1.0
模、夹、检公差设定及检测标准 B
夹具
检具
TTO 推进活动
TTO(TOOL TRIAL OUT)是通过各设备及夹具所要求的功能的实现,确立对各种问题的对策。
品质目标
Quality Target
• 图纸研讨和目标确认 Draw Review & Target Confirmation • 对厂家的钣金件进行模具和夹具调试Confirmation of Die & Jig Trial for Panels of Maker
简析汽车白车身尺寸开发与控制
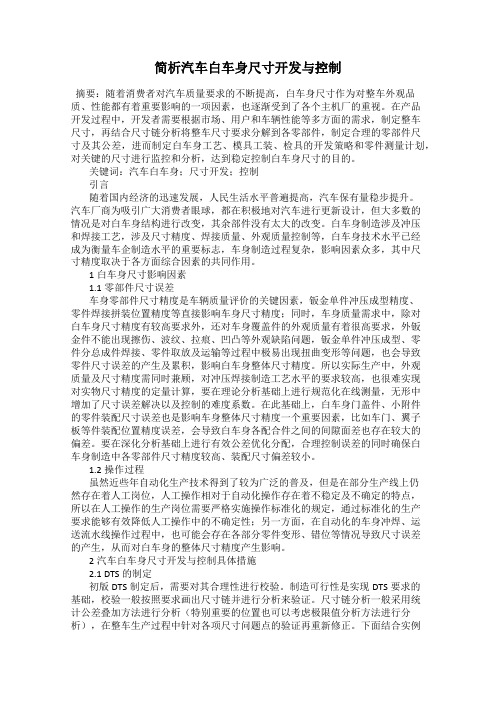
简析汽车白车身尺寸开发与控制摘要:随着消费者对汽车质量要求的不断提高,白车身尺寸作为对整车外观品质、性能都有着重要影响的一项因素,也逐渐受到了各个主机厂的重视。
在产品开发过程中,开发者需要根据市场、用户和车辆性能等多方面的需求,制定整车尺寸,再结合尺寸链分析将整车尺寸要求分解到各零部件,制定合理的零部件尺寸及其公差,进而制定白车身工艺、模具工装、检具的开发策略和零件测量计划,对关键的尺寸进行监控和分析,达到稳定控制白车身尺寸的目的。
关键词:汽车白车身;尺寸开发;控制引言随着国内经济的迅速发展,人民生活水平普遍提高,汽车保有量稳步提升。
汽车厂商为吸引广大消费者眼球,都在积极地对汽车进行更新设计,但大多数的情况是对白车身结构进行改变,其余部件没有太大的改变。
白车身制造涉及冲压和焊接工艺,涉及尺寸精度、焊接质量、外观质量控制等,白车身技术水平已经成为衡量车企制造水平的重要标志,车身制造过程复杂,影响因素众多,其中尺寸精度取决于各方面综合因素的共同作用。
1白车身尺寸影响因素1.1零部件尺寸误差车身零部件尺寸精度是车辆质量评价的关键因素,钣金单件冲压成型精度、零件焊接拼装位置精度等直接影响车身尺寸精度;同时,车身质量需求中,除对白车身尺寸精度有较高要求外,还对车身覆盖件的外观质量有着很高要求,外钣金件不能出现擦伤、波纹、拉痕、凹凸等外观缺陷问题,钣金单件冲压成型、零件分总成件焊接、零件取放及运输等过程中极易出现扭曲变形等问题,也会导致零件尺寸误差的产生及累积,影响白车身整体尺寸精度。
所以实际生产中,外观质量及尺寸精度需同时兼顾,对冲压焊接制造工艺水平的要求较高,也很难实现对实物尺寸精度的定量计算,要在理论分析基础上进行规范化在线测量,无形中增加了尺寸误差解决以及控制的难度系数。
在此基础上,白车身门盖件、小附件的零件装配尺寸误差也是影响车身整体尺寸精度一个重要因素,比如车门、翼子板等件装配位置精度误差,会导致白车身各配合件之间的间隙面差也存在较大的偏差。
白车身培训教程

第二部分白车身1车身结构: 1.1车身分类: 一般来讲,比较明确而又合理的分类形式是从结构和设计观点出发,按车身承载型式来分。
按承载型式的区别,可将车身分为:非承载式、半承载式和承载式三大类,其定义如下: 1. 非承载式(有车架式) 一般,货车(除微型货车)、大客车、专用汽车及大部分高级轿车上都装有单独的车架,车身上的载荷主要由车架来承担,但车身仍在一定程度上承受由车架弯曲和扭转变形所引起的载荷。
2. 半承载式 半承载式是一种过度型的结构,车身下部仍保留有车架,不过它的强度和刚度要低于非承载式的车架,一般将它称之为底架。
它之所以被命名为半承载式是出于以下考虑:让车身也分担部分载荷,以此来减轻车架的自重力。
这种结构型式主要体现在大客车上。
3. 承载式(无车架式) 承载式车身无车架,车身的强度和刚度通常主要由车身下部来予以保证,一般中低档轿车车身属于承载式车身。
以S11车身为例,如下图所示: 其前端由两根前纵梁、前围板,轮罩形成一刚性较强的框架;车身中部、后部由左、右侧围(包括顶梁、门槛梁、A柱、B柱、C柱等)和地板、顶盖及后备门框等构成的盒形结构 随着立体交叉道路和高速公路的普及,轿车车速不断增高,在轿车轻量化的同时,还必须从保护乘员人身安全的角度出发来仔细研究车身的结构设计。
一般车身结构分为刚性结构和弹性结构,如果在车身前部和后部均为弹性结构而中部为刚性结构的情况下,就能确保乘员安全。
所以,在车身开发的前期阶段,CAE分析尤为重要。
1.2车身结构: 车身总体尺寸和形状以及承载的结构型式确定后,即可着手进行细致的结构分析与设计。
设计车体结构大致按以下步骤进行: 1) 确定整个车体应由哪些主要的和次要的构件组成,使其成为一个连续的完整的受力系统;确定主要杆件采取怎样的截面型式-闭式的或开式的。
2) 确定如何构成这样的截面,截面与其他部件的配合关系,密封或外形的要求,壳体上内外装饰板或压条的固定方法以及组成截面的各部分的制造方法及其装配方法等。
白车身匹配技术
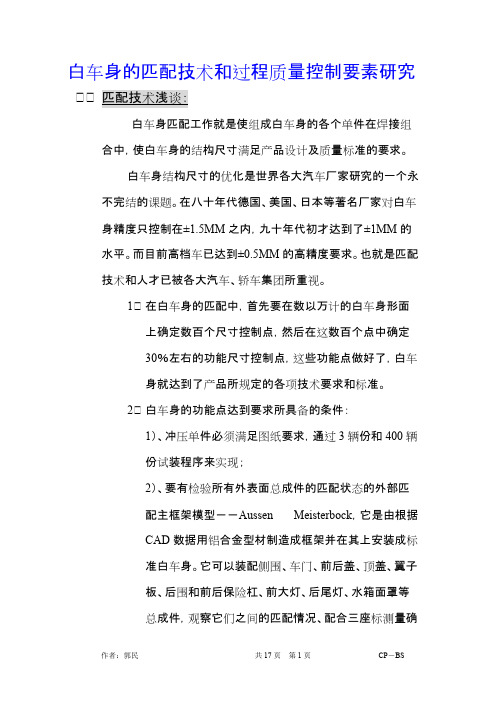
白车身的匹配技术和过程质量控制要素研究、、白车身匹配工作就是使组成白车身的各个单件在焊接组合中,使白车身的结构尺寸满足产品设计及质量标准的要求。
白车身结构尺寸的优化是世界各大汽车厂家研究的一个永不完结的课题。
在八十年代德国、美国、日本等著名厂家对白车身精度只控制在±1.5MM之内,九十年代初才达到了±1MM的水平。
而目前高档车已达到±0.5MM的高精度要求。
也就是匹配技术和人才已被各大汽车、轿车集团所重视。
1、在白车身的匹配中,首先要在数以万计的白车身形面上确定数百个尺寸控制点,然后在这数百个点中确定30%左右的功能尺寸控制点,这些功能点做好了,白车身就达到了产品所规定的各项技术要求和标准。
2、白车身的功能点达到要求所具备的条件:1)、冲压单件必须满足图纸要求,通过3辆份和400辆份试装程序来实现;2)、要有检验所有外表面总成件的匹配状态的外部匹配主框架模型--Aussen Meisterbock,它是由根据CAD数据用铝合金型材制造成框架并在其上安装成标准白车身。
它可以装配侧围、车门、前后盖、顶盖、翼子板、后围和前后保险杠、前大灯、后尾灯、水箱面罩等总成件,观察它们之间的匹配情况、配合三座标测量确定零件的更改数据。
(Aussen Meisterbock示意图)3)、要有检查内饰件与白车身匹配关系的内匹配主框架模型--Innen Meisterbock;它是借助外部框架用合格焊接分总成组装的标准车身,来检查内饰件是否符合匹配要求的工具。
4)、要有正确反映车身下部,即前后轮罩、前后底板、仪表板之间匹配关系的标准车身下部主框架--Fuegen Meisterbock。
它的定位点和夹紧点与生产夹具的定位点完全一致,能实际反映出各总成之间的干涉点和贴合程度,从而确定焊接总成结构尺寸的正确性。
3、匹配过程中对夹具定位、夹紧和工艺的合理性进行验证。
(Inne Meisterbock示意图)1)、基准点系统是否合理、定位点是否与设计基准重合、是满足六点定位原则、定位点尺寸是否正确等;2)、零件的装配顺序是否合理、是否影响尺寸精度;3)、夹具的点定工位点定点是否正确、焊接点定后,到下一工位补焊时,能否保证尺寸稳定;4)、补焊点的顺序对尺寸的稳定性是否有利;5)、夹紧点是否正确,能否保证零件在夹具位置的准确性;6)、夹具顺序是否合理,关键定位点是否首先夹紧;7)、确定能反映零件状态的测量点和功能尺寸;4、单件或总成在匹配过程中的具体步骤1)、首先将满足图纸尺寸的单件按工艺要求顺利放入夹具中,检查零件在夹具上是否贴合,并且无应力。
白车身尺寸精度控制方法研究
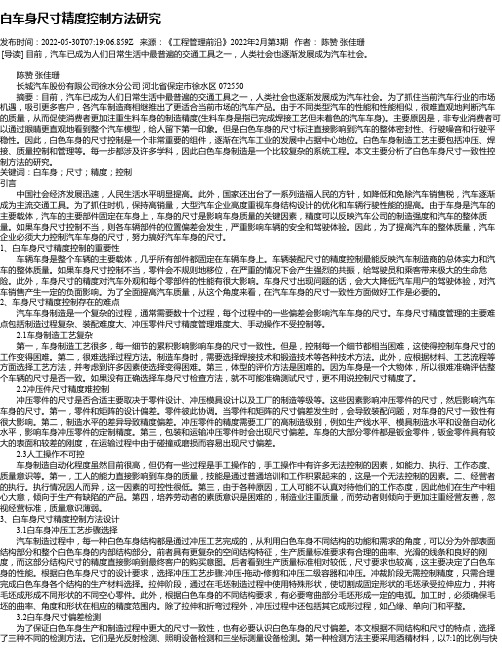
白车身尺寸精度控制方法研究发布时间:2022-05-30T07:19:06.859Z 来源:《工程管理前沿》2022年2月第3期作者:陈赞张佳珊[导读] 目前,汽车已成为人们日常生活中最普遍的交通工具之一,人类社会也逐渐发展成为汽车社会。
陈赞张佳珊长城汽车股份有限公司徐水分公司河北省保定市徐水区 072550摘要:目前,汽车已成为人们日常生活中最普遍的交通工具之一,人类社会也逐渐发展成为汽车社会。
为了抓住当前汽车行业的市场机遇,吸引更多客户,各汽车制造商相继推出了更适合当前市场的汽车产品。
由于不同类型汽车的性能和性能相似,很难直观地判断汽车的质量,从而促使消费者更加注重生料车身的制造精度(生料车身是指已完成焊接工艺但未着色的汽车车身)。
主要原因是,非专业消费者可以通过眼睛更直观地看到整个汽车模型,给人留下第一印象。
但是白色车身的尺寸标注直接影响到汽车的整体密封性、行驶噪音和行驶平稳性。
因此,白色车身的尺寸控制是一个非常重要的组件,逐渐在汽车工业的发展中占据中心地位。
白色车身制造工艺主要包括冲压、焊接、质量控制和管理等。
每一步都涉及许多学科,因此白色车身制造是一个比较复杂的系统工程。
本文主要分析了白色车身尺寸一致性控制方法的研究。
关键词:白车身;尺寸;精度;控制引言中国社会经济发展迅速,人民生活水平明显提高。
此外,国家还出台了一系列造福人民的方针,如降低和免除汽车销售税,汽车逐渐成为主流交通工具。
为了抓住时机,保持高销量,大型汽车企业高度重视车身结构设计的优化和车辆行驶性能的提高。
由于车身是汽车的主要载体,汽车的主要部件固定在车身上,车身的尺寸是影响车身质量的关键因素,精度可以反映汽车公司的制造强度和汽车的整体质量。
如果车身尺寸控制不当,则各车辆部件的位置偏差会发生,严重影响车辆的安全和驾驶体验。
因此,为了提高汽车的整体质量,汽车企业必须大力控制汽车车身的尺寸,努力搞好汽车车身的尺寸。
1、白车身尺寸精度控制的重要性车辆车身是整个车辆的主要载体,几乎所有部件都固定在车辆车身上。
- 1、下载文档前请自行甄别文档内容的完整性,平台不提供额外的编辑、内容补充、找答案等附加服务。
- 2、"仅部分预览"的文档,不可在线预览部分如存在完整性等问题,可反馈申请退款(可完整预览的文档不适用该条件!)。
- 3、如文档侵犯您的权益,请联系客服反馈,我们会尽快为您处理(人工客服工作时间:9:00-18:30)。
底盘RPS点的Z向平顺性 疑问——底盘不平顺有哪些危害?
答:主要两种危害。(此处强调一下:下部总成的刚度与骨架总成的刚度是不同的)
1.前后端Z向尺寸不稳定
2.整车的Y向对中性不稳定
Y
Z
18
底盘RPS点的Z向平顺性 保证地盘平顺的三步骤: 1.排查前后左右4根纵梁单件→分总成,是否存在扭曲; 2.检查后地板总成的4个Z向RPS点是否在一个平面上; 3.用移动三坐标测量关键夹具,并优化夹具。
30
辅助RPS点的Y向平顺性 建议:应优先保证Y向平顺性。 如下图红色圆圈均为Y向辅助RPS,测量支架上有夹具将侧围夹持到理论平面。 在测量支架上,完成夹紧后,应逐一单独打开某一Y向辅助加紧,观察是否有较大回弹 (回弹量大于5mm且夹紧块吃力很大)
如果回弹较大,会影响侧围报告可读性,并导致主焊骨架尺寸不稳定(因为主焊定位夹 具无法克服侧围总成较大的变形,夹具打开后,骨架尺寸则整体回弹)
唯一的辅助Z向RPS点 Z向值越接近零越好, 宁高勿低
3个主定位Z向RPS点 Z向值均为零
20
底盘RPS点的Z向平顺性 保证地盘平顺的三步骤: 1.排查前后左右4根纵梁单件→分总成,是否存在扭曲; 2.检查后地板总成的4个Z向RPS点是否在一个平面上; 3.用移动三坐标测量关键夹具,并优化夹具。
关键夹具,主要指: 3.1下部一主拼工位; 3.2下部一主拼工位紧后面的若干个补焊焊点较多的工位;(须说明,下图) 3.3下部二主拼工位; 3.4下部二主拼工位紧后面的若干个补焊焊点较多的工位。
培训材料1-白车身尺寸控制
2015.6.2
目录 白车身制造及装配流程简介 白车身尺寸控制手段 白车身各分总成的重要尺寸点,重点展开 功能尺寸知识 CP与CPK
1
目录 白车身制造及装配流程简介 白车身尺寸控制手段 白车身各分总成的重要尺寸点,重点展开 功能尺寸知识 CP与CPK
21
白车身各分总成的重要尺寸点,重点展开 下部重要尺寸点: 1.底盘RPS点的Z向平顺性; 2.较高测量点区域的Y向挡距和尺寸对中性; 3.底盘拧紧相关尺寸和“小坐标系”的概念;
22
较高测量点区域的Y向挡距和尺寸对中性
较高的测量点,主要指的是: 前挡板,后座椅靠背,后轮罩等Y向测量点,它们与侧围搭接,直接影响骨架的Y向。 建议:宁窄勿宽。(须说明,最右图)
白车身制造及装配流程简介 2.侧围
1.下部
4.四门
3.骨架
6.整车前端 (调整线) 5.前后盖翼子板
12
白车身各分总成的重要尺寸点,重点展开 下部重要尺寸点: 1.底盘RPS点的Z向平顺性; 2.较高测量点区域的Y向挡距和尺寸对中性; 3.底盘拧紧相关尺寸和“小坐标系”的概念;
13
白车身各分总成的重要尺寸点,重点展开 下部重要尺寸点: 1.底盘RPS点的Z向平顺性; 2.较高测量点区域的Y向挡距和尺寸对中性; 3.底盘拧紧相关尺寸和“小坐标系”的概念;
1.1固定式精测检具: 主要用于四门两盖, 加工精度较高(偏差 0.2mm内),测量点 较多且每个测点要有 点检记录。
1.2移动式精测检具: 主要用于主焊,如风窗,天窗 等。测量点较少。
5
白车身尺寸控制手段: 1.精测检具; 2.实物检具; 3.简易型面样板; 4.三坐标测量(含在线测量)
经过测量后 2.实物检具,就是实际的零件
38
白车身各分总成的重要尺寸点,重点展开 骨架重要尺寸点: 1.前后风挡尺寸控制点; 2.天窗匹配如何保证; 3.与四门匹配相关尺寸控制; 4.后端尺寸控制(举例车身尺寸偏差时,后端匹配如何变化)。 **关于后端零件结构设计的一些建议**
39
前后风挡尺寸控制点
须保证四个功能尺寸,之间要相互配合: 1.风挡上方的车身Y向挡距; 2.风挡下方的车身Y向挡距; 3.上方与下方Y向挡距的对中一致性; 4.顶盖的左右X向差值。 (下图举例,红色为理论位置,蓝色为四种实际偏差的车身状态) 相互配合,指的是:1与2为一组,尽量同大同小;3与4为一组,旋转方向须一致。
27
白车身制造及装配流程简介 2.侧围
1.下部
4.四门
3.骨架
6.整车前端 (调整线) 5.前后盖翼子板
28
白车身各分总成的重要尺寸点,重点展开 侧围重要尺寸点: 1.辅助RPS点的Y向平顺性; 2.侧围的“薄与厚”取决于零件间的服帖程度; 3.影响上述两点的关键零件及分总成;
29
白车身各分总成的重要尺寸点,重点展开 侧围重要尺寸点: 1.辅助RPS点的Y向平顺性; 2.侧围的“薄与厚”取决于零件间的服帖程度; 3.影响上述两点的关键零件及分总成;
1——Y
3——X,Y,Z
2——Y,Z
31
辅助RPS点的Y向平顺性
介绍一下新、老两种工艺——其中新工艺能有效消除侧围不平顺带来的影响。
老 前内板 工 艺
1.
侧围外板
后内板
2. 3.
下部总成
新 工 艺
前内板
1.
下部总成
3.
后内板
2.
32
侧围外板
白车身各分总成的重要尺寸点,重点展开 侧围重要尺寸点: 1.辅助RPS点的Y向平顺性; 2.侧围的“薄与厚”取决于零件间的服帖程度; 3.影响上述两点的关键零件及分总成;
33
侧围的“薄与厚”取决于零件间的服帖程度 侧围的“薄与厚”的几点总结: 1.在下部Y向尺寸既定的前提下,侧围的“薄与厚”直接决定骨架尺寸的“宽与窄”; 2.侧围上的零件,多数为Y向贴合焊接,能靠夹具直接调整侧围“薄厚”的区域很少 (如A柱和C柱风挡区域,可以靠夹具调整)见下图;
大图
3.多数情况下,侧围都是偏厚的——因为侧围零件Y向搭接时,各自曲面不能完全服帖, 导致一层层焊接成为侧围总成后,就越来越厚一些。
2.车身主RPS的钣金平面与理论平面不平行,导致勾销加紧后,车身RPS孔附近的钣 金与理论平面出现线接触,而不是面接触。则测量的孔心实际上高于理论平面,将其 强制归“零”后,就会显得辅助RPS是低的。
16
底盘RPS点的Z向平顺性 疑问——Z向的辅助RPS都是理论位置,为什么会出现负数? 答:两种情况:
纵梁单件或总成扭曲的最明显的表现,是RPS1所在平面与RPS2所在平面,不平行。 可以将单件或总成放置在测量支架上面,在自由状态下观察两个平面是否为面接触。
19
底盘RPS点的Z向平顺性
保证地盘平顺的三步骤: 1.排查前后左右4根纵梁单件→分总成,是否存在扭曲; 2.检查后地板总成的4个Z向RPS点是否在一个平面上; 3.用移动三坐标测量关键夹具,并优化夹具。
42
天窗匹配如何保证 难点零件较多,天窗匹配要求较高,遂采取一些极端方法(兼顾表面质量): 1.天窗加强框制作矫形夹具; 2.整车骨架上,用机器人对天窗Z向进行矫形。
43
白车身各分总成的重要尺寸点,重点展开 骨架重要尺寸点: 1.前后风挡尺寸控制点; 2.天窗匹配如何保证; 3.与四门匹配相关尺寸控制; 4.后端尺寸控制(举例车身尺寸偏差时,后端匹配如何变化)。 **关于后端零件结构设计的一些建议**
44
与四门匹配相关尺寸控制
相对简单,骨架须注意两点: 1.保证车身整体Y向对中性,尤其是车顶;
否则会导致:车门调整要掰门;窗框区域漏雨;车门闭合力大等典型问题。 2.A柱、B柱、C柱三者的Y向偏差是否一致,尽量平行;
2
白车身制造及装配流程简介 2.侧围
1.下部
4.四门
3.骨架
6.整车前端 (调整线) 5.前后盖翼子板
3
目录 白车身制造及装配流程简介 白车身尺寸控制手段 白车身各分总成的重要尺寸点,重点展开 功能尺寸知识 CP与CPK
4
白车身尺寸控制手段:
1.精测检具; 2.实物检具; 3.简易型面样板; 4.三坐标测量(含在线测量)
24
白车身各分总成的重要尺寸点,重点展开 下部重要尺寸点: 1.底盘RPS点的Z向平顺性; 2.较高测量点区域的Y向挡距和尺寸对中性; 3.底盘拧紧相关尺寸和“小坐标系”的概念;
25
底盘拧紧相关尺寸和“小坐标系”的概念 底盘拧紧相关尺寸,主要指的是: 发动机传动器装配孔,前、后副车架装配孔,油箱装配孔,排气管支架。
9
白车身尺寸控制手段: 4.三坐标测量(含在线测量)——3-2-1基准(N-2-1基准)
其余均为Z向辅 助定位支撑
3——X,Y,Z
10
1——Z 2——Y,Z
目录 白车身制造及装配流程简介 白车身尺寸控制手段 白车身各分总成的重要尺寸点,重点展开 功能尺寸知识 CP与CPK
11
下部
侧围
下部左图尺寸,影响车身骨架 的Y向,越高的区域受到的影响 越大。
23
当零件有间隙进行焊接时, 焊枪的瞬间夹持和焊接热 熔,会使两个钣金轻微变 形,此变形会弥补此间隙 带来的偏差。反之,零件 若互相干涉,就无此弥补。
较高测量点区域的Y向挡距和尺寸对中性 较高的测量点,主要指的是: 前挡板,后座椅靠背,后轮罩等Y向测量点,它们与侧围搭接,直接影响骨架的Y向。 建议:宁窄勿宽——下图,下部的功能尺寸为不对等公差带(-3.0,+1.0)
1
2
3
4
40
前后风挡尺寸控制点
3
1
2
4
平面度要求,很 少出现问题 。
41
白车身各分总成的重要尺寸点,重点展开 骨架重要尺寸点: 1.前后风挡尺寸控制点; 2.天窗匹配如何保证; 3.与四门匹配相关尺寸控制; 4.后端尺寸控制(举例车身尺寸偏差时,后端匹配如何变化)。 **关于后端零件结构设计的一些建议**
(零件完全服帖不大可能,因此在侧围普遍厚的情况下,下部尺寸适当做窄是合理的)
34
白车身各分总成的重要尺寸点,重点展开 侧围重要尺寸点: 1.辅助RPS点的Y向平顺性; 2.侧围的“薄与厚”取决于零件间的服帖程度; 3.影响上述两点的关键零件及分总成;