氧化还原氧化裂解石脑油制乙烯的过程模拟与分析
乙烯的氧化反应方程式

乙烯的氧化反应方程式
乙烯(C2H4)是一种常见的烯烃,也被称为乙烯烃。
乙烯可以通过氧化反应转化为乙烯醛(乙醛),氧化反应的化学方程式如下所示:C2H4 + O2 → C2H4O
在这个方程式中,乙烯(C2H4)与氧气(O2)发生氧化反应,产生乙烯醛(C2H4O)。
乙烯氧化反应是一种重要的化学反应,也是工业生产中的一个重要步骤。
乙烯醛是一种有机化合物,常用于合成其他有机化合物,如乙醇和丙烯醛等。
乙烯氧化反应通常在高温和高压下进行,以促进反应的进行。
乙烯氧化反应是一个氧化还原反应。
在反应中,乙烯失去氢原子,氧气得到氢原子,形成乙烯醛。
氧气在反应中起到氧化剂的作用,促进乙烯的氧化反应。
乙烯氧化反应具有重要的应用价值。
乙烯醛是一种重要的有机合成中间体,可以用于合成各种有机化合物,如聚乙烯醛和聚醋酸乙烯酯等。
乙烯氧化反应也可以用于生产乙醛和其他有机化合物,广泛应用于化工、制药和农药等领域。
总的来说,乙烯的氧化反应是一种重要的化学反应,可以产生有机合成中间体乙烯醛,具有广泛的应用价值。
在工业生产中,乙烯氧
化反应是一个重要的步骤,可以用于合成各种有机化合物,推动化工产业的发展。
热裂解制乙烯裂解炉的工艺数学模型和模拟

结 焦模 型 、流 体 流 动 模 型 、热 量 传 递 模 型 和 质 量 传
递模 型 。按 建 立 方 法 分 类 , 型 可分 为 理论 模 型 、 模 经 验 模 型 及 半 经 验 半 理 论 模 型 。 由于 很 难 确 定 裂 解 原 料 的 组 成 以及 他 们 所 发 生 的 裂 解 反 应 ,建 立 理 论 模
● ● ● ● ● ● ● ● ●
热 裂解 制 乙烯 裂解 炉 的工 艺 数 学模 型 和 模 拟
沙 利 蓝 兴 英 高 金 森 徐 春 明
( 油 大 学 重 质 油加 工 国 家 重 点 实 验 室 , 京 1 2 4 ) 石 北 0 2 9
摘 要 对 乙烯 生 产 过 程 的 数 学 模 型 发 展 状 况 作 一 概 述 。 按 对 反 应 管 轴 向 和 径 向 处 理 的 方 法 ,裂 解 炉 的 工 艺数 学 模 型 可 分 为 一 维 模 型 和 二 维模 型 ,对 一 维 模 型 与 二 维 模 型 的 模 型 假
方 程 式 的数 目 ,研 究 者们 采 取 简 化 措 施 ,提 出半 经 验 半 理 论 模 型 。它 是 将 过 程 的 物 理 的 或 化 学 的机 理 与 生 产 数 据 或 实 验 数 据 相 结 合 ,即从 机理 分 析 抓 住
许 多 重 要 的化 学 工 程 参 数 均不 易 测 出 ,这 给 乙烯 生 产 装 置 的 操 作 带 来 了很 多 不便 。随 着 计 算 机 技 术 的 高 度 发 展 ,利 用 数 学 模 型模 拟 裂 解 炉 内 的复 杂 过 程 已 经 成 为 可 能 , 是一 种 必 然 趋 势 。 也 裂解炉 的工艺 数学模 型包括 反应动 力学模 型 、
乙烯生产方法选择—烃类热裂解制乙烯
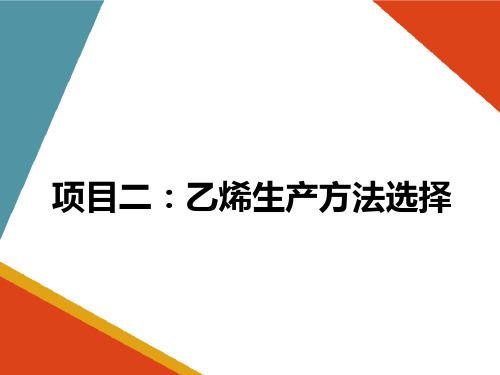
任务二 烃类热裂解制乙烯
1、原料加热及反应系统
由原料罐区来的石脑油等原料换热后,与DS (180℃, 0. 55MPa)按相应的油汽比混合进入裂解 炉对流段加热后进入辐射段。
物料在辐射段炉管内迅速升温进行裂解反应(以控 制辐射炉管出口温度COT的方式控制裂解深度, COT大约为800~900℃)。裂解气出口温度COT通 过调节每组炉管的烃进料量来控制,要求高于裂 解气的露点(裂解气中重组分的露点),若低于露点 温度,则裂解气中的较重组分有一部分会冷凝, 凝结的油雾黏附在急冷换热器管壁上形成流动缓 慢的油膜,既影响传热,又容易发生二次反应。
任务二 烃类热裂解制乙烯
4、水急冷和稀释水蒸气系统
油冷塔顶的裂解气,通过和水冷塔中的循环 急冷水进行直接接触进行冷却和部分冷凝, 温度冷却至28℃,水冷塔的塔顶裂解气被送 到裂解气压缩工段。
任务二 烃类热裂解制乙烯
4、水急冷和稀释水蒸气系统
急冷水和稀释水蒸气系统的生产目的是用水 将裂解气继续降温到40°C左右,将裂解气 中所含的稀释蒸汽冷凝下来,并将油洗时没 有冷凝下来的一部分轻质油也冷凝下来,同 时也可回收部分热量。稀释蒸汽发生器接收 工艺水,发生稀释蒸汽送往裂解炉管,作为 裂解炉进料的稀释蒸汽,降低原料裂解中烃 分压。
任务二 烃类热裂解制乙烯
二.世界乙烯原料情况
平均下来石脑油是最主要的,占了43%,排 第二名是乙烷占36%。但是具体到各国或地 区的情况却不同。欧洲、中国、日本一样主 要采用石脑油作原料。
任务二 烃类热裂解制乙烯
二.世界乙烯原料情况
典型的是西欧乙烯71%来自石脑油,来自轻 烃和LPG的各占11%仅7%来自乙烷。而美 国恰恰相反,主要使用乙烷作原料。它的乙 烯52%来自乙烷,22%来自轻烃5%来自石 脑油。
石脑油裂解参数的考察和研究

水油 比、 裂解温度及温度分 布等参数对 乙烯的收率
有着 较大 的影 响 , 因此 很 多 的科 学 家都 在 运 用 一 些
装置来进行模拟 , 以期望得到最佳 的优化条件 。国
外 已经研 制 开发 了很 多种 蒸 汽 裂 解 模 拟 装 置 , 中 其 最为 成 功 的是 美 国 SYR P O公 司开 发 的蒸 汽 裂 解模 拟装 置 , 该装 置 的进料 系统 控制 比较 精确 , 够很 好 能
地模拟 目前工业装置 的进料 , 炉体 的温度分布也与 工业 装置 很接 近 , 套 装置 几 乎 与工 业 装 置 完 全 相 整 似, 因此模拟的参数很有参考价值。本项 目就是通
过美 国 SY O公 司开发的蒸汽裂解模拟装置来考 PR
察石 脑油 的裂 解工 艺参 数 。
1 2 试 验流 程 .
中图分类号 : Q 0 T 23 文献标识码 : A 文章编号 :0 9— 7 5 2 0 )9— 0 4— 3 10 2 ( 0 8 0 02 0
Re e c o c a ki r me e f na ht s ar h n r c ng pa a t r o p ha
e c nyedo tye e T eo t m p rt n l o dt nwa ban dtru h ep rme t dteyedo tye ewa n eo il feh ln . h pi mu o eai a n io so tie ho g x ei n il feh ln s o c i n a h
维普资讯
化 工科 技 市场
CHEMI CAL TECHNOLOGY MARKET
乙烯生产有关知识

乙烯生产有关知识1.不同原料的乙烯产品产率原料是影响乙烯生产成本的重要因素,以石脑油和柴油为原料的乙烯装置,原料在总成本中所占比例高达70%~75%。
乙烯作为下游产品的原料,对下游产品生产成本的影响同样显著,例如在聚乙烯生产成本中其所占比重高达80%左右。
因此,乙烯原料的选择和优化是降低乙烯生产成本、提高石油化工产品市场竞争力的关键。
6.3 我国裂解原料供应面临紧张状况原料缺口问题是国内乙烯工业进一步发展的关键之一。
我国乙烯裂解原料包括石脑油、轻柴油、重油、原油、乙烷和丙烷等,乙烯作为基本的有机化工原料和石油化工业的龙头产品,被誉为“石油化工之母”。
随乙烯原料是影响乙烯生产成本的重要因素,以石脑油油和柴油为原料的乙烯装置,原料在总成本中所占比例高达70%~75%,乙烯作为下游产品的原料,对下游产品生产成木的影响同样著,例如在聚乙烯生产成本中所占比重高达80%左右。
因此,乙烯原料的选择和优化是降低乙烯牛产成本、提高乙烯装置竞争力的重要环节,也是提高石油化工产品市场竞争力的关键。
1 乙烯生产原料的现状分析日前世界上使用的乙烯原料主要仃:乙烷、烷、丙烷、液化油气(LPG)、凝析油、脑油、加氢裂化尾油及柴油等。
由于资源拥有量的不,各地区的原料构成存在差异,呈现出地域性的特点。
预计今后世界乙烯原料的构成基本稳定,石脑油和轻烃仍是主导原料,其中石脑油占50%以上,轻烃(乙烷、丙烷、丁烷)占35%以上,其他原料不到10%。
但由于资源不同,不同国家和地区的原料组成差别较大,如美国和中东乙烯主要原料为乙烷,西欧和亚洲乙烯原料以石脑油为主。
3 开发新原料路线的技术进展3.1 催化裂解制乙烯技术3.2 天然气经甲醇(二甲醚)制乙烯3.3 乙烷脱氢制乙烯工艺3.4 乙烷催化联产乙烯和醋酸3.5 天然气氧化偶联制乙烯4 建议4.1 充分利用好国内外两种资源,增强乙烯原料的适应性我国已成为原油净进口国,如何充分利用好国内外两种资源,非常重要。
乙烯工艺流程分析

乙烯工艺流程分析
《乙烯工艺流程分析》
乙烯是一种重要的化工原料,在很多行业中都有广泛的应用。
乙烯的生产工艺是一个复杂的过程,需要经过多道工序来完成。
下面将针对乙烯生产的工艺流程进行分析。
乙烯的生产通常以石油或天然气作为原料。
首先,原料通过蒸馏或裂解的方式得到乙烯的预生产物——乙烷。
接着,乙烷要经过脱氢反应来制得乙烯。
这个脱氢反应通常在高温、高压下进行,需要通过催化剂来加速反应速度。
脱氢反应后的乙烯会含有杂质,需要进行蒸馏和净化处理,以去除其中的杂质成分。
随后,乙烯要经过合成反应来制得乙烯聚合物,也就是聚乙烯。
这个合成反应通常需要使用催化剂,而且反应条件也相当苛刻。
一旦制得乙烯聚合物,就需要进行后续的加工和处理,最终形成乙烯产品。
整个乙烯生产的工艺流程中,不仅需要各种化工反应工序,还需要配套的设备和管道来保证生产的顺利进行。
而且在整个生产过程中,要保证生产设备的安全和稳定运行,并且要防止化工品的泄漏和污染。
总的来看,乙烯的生产工艺流程是一个复杂的系统工程,需要多个环节的紧密配合,以确保乙烯的高效生产和产品质量。
同时,要加强安全管理和环境保护,以确保生产过程中对环境和人员的安全不会造成影响。
第二章乙烯生产工艺简介
项目 石脑油 乙烷 丙烷 1995 52.4 27.6 9.4 2000 52.2 28.0 10.0 柴油 丁烷 其它 1995 6.3 3.3 1.0 2000 6.3 2.8 0.7
目前世界乙烯原料结构中,石脑油仍占主要地位,2003年 全球乙烯原料结构:石脑油 47.5%、轻烃 36.3%、柴油 4.6%、 其他 11.6%。
17
2. 加氢和脱氢
烯烃可以加氢成饱和的烷烃,例如:
C2H4+H2 C2H6 反应温度低时,有利于加氢平衡。 烯烃也可以进一步脱氢生成二烯烃和炔烃,例如: C2H4 C2H2+H2 CH3CH=CH2 CH3C≡CH+H2 CH3CH2CH=CH2 CH2=CH—CH=CH2+H2 从热力学分析,烯烃的脱氢反应比烷烃的脱氢反应推动 力更小,故需要更高的温度。
裂解炉及急冷换热气的操作指标见表1及表原料项目煤柴油乙烷反应管出口温度765820反应管入口温度600600反应管出口压力atm078107078107反应管内压力降atm1717停留时间秒04510蒸汽稀释比w075030急冷换热气工艺指标裂解原料出口温度535380停留时间秒005发生的蒸汽压力atm8686从裂解气中分离出燃料油及裂解气油部分裂解气经急冷油喷雾急冷至190后进入初分馏塔塔底分出燃料油裂解重油送至稀释蒸汽发生器利用其热量发生7kgcm表压的稀释蒸汽本身被冷却后一部分作为急冷油循环进入油急冷器使用另一部分作为急冷油被掺入塔底急冷油中以降低油的粘度抽出量由塔中段的液面控制其余部分作为燃料油送出系统外
甲烷氧化偶联制乙烯工艺的能量利用
论文摘要:甲烷氧化偶联反应(OCM)的提出为由资源丰富且相对廉价的天然气替代主要由石脑油制取乙烯提供了新的可能途径,并且该途径是通过一步法制乙烯,是现有乙烯生产工艺中最为简捷的途径。
但是由于甲烷化学性质稳定,使甲烷氧化偶联制乙烯的转化率一直无法突破30%(最低的工业生产要求)。
近期研究发现,可以利用OCM反应放出的热量来实现乙烯生产和发电的结合,以提高它的经济效益,增加实现工业化的可能性。
本文介绍了有关OCM的先进技术,并主要对OCM反应热量的利用进行了分析,提出生产高温高压蒸汽,实施冷热电联产。
Key words:oxidative coupling of methane;ethylene;electricity;co-generationAbstract:The reaction of oxidative coupling of methane(OCM)provides a new possible way to produce ethylene by rich and cheap natural gas instead of naphtha as raw material. It gains ethylene by one step,which is the simplest and directest in producing ethylene nowdays. However,methane is very steady,so the yield of ethylene can not break through 30%,which is the lowest request in industry. But recent studies have claimed that this may be overcome by producing not only ethylene but also electricity by making use of the heat from the exothermic coupling reaction. The way of co-generation of ethylene and electricity by oxidative coupling of methane can increase economic benefit and feasibility in industrialization. This paper introduces advanced technology on the reaction of oxidative coupling of methane and mainly studies the heat from the exothermic coupling reaction,which is used to produce high temperature and high pressure steam to come true combined cold,hot and power.乙烯是重要的化学产品,全世界的乙烯大多由碳氢化合物裂解所得。
不同种类石脑油的裂解产物分布及收率对比分析
不同种类石脑油的裂解产物分布及收率对比分析许江;程中克;王小强;田亮;景媛媛;穆珍珍【摘要】为了对乙烯裂解原料进行优选及优化利用,开展了加氢裂化石脑油、煤化工石脑油、直馏石脑油、柴油加氢石脑油、焦化加氢石脑油的热裂解试验,分别对其裂解产物中乙烯、丙烯、丁二烯、甲烷、抽余C4、裂解液相产物收率进行了对比分析.结果表明,不同种类石脑油的裂解产物分布和收率存在很大差异.如煤化工石脑油、焦化加氢石脑油裂解多产乙烯,加氢裂化石脑油裂解多产丙烯,直馏石脑油裂解丁二烯收率高达6.11%,焦化加氢石脑油的裂解抽余C4收率低至2.73%,柴油加氢石脑油裂解液相产物占比高.因此,结合裂解产物收率、原料成本及供应以及烯烃市场形势,合理选择石脑油进行裂解并有效利用其裂解液相产物可大幅降低乙烯生产成本、提升石脑油裂解制乙烯的综合竞争力.【期刊名称】《石油与天然气化工》【年(卷),期】2019(048)003【总页数】5页(P23-27)【关键词】石脑油;裂解;产物收率;低碳烯烃;液相产物【作者】许江;程中克;王小强;田亮;景媛媛;穆珍珍【作者单位】中国石油兰州化工研究中心;中国石油兰州化工研究中心;中国石油兰州化工研究中心;中国石油兰州化工研究中心;中国石油兰州化工研究中心;中国石油兰州化工研究中心【正文语种】中文乙烯裂解原料的优选及优化利用是决定乙烯企业提质增效的关键因素,对降低乙烯生产成本、提高市场竞争力具有举足轻重的作用。
石脑油裂解是烯烃市场最重要的供应部分,我国乙烯原料以石脑油、轻烃、轻柴油、加氢尾油及煤炭为主,其中石脑油占比约50%,以石脑油为主的乙烯裂解装置也被认为是石油化工装置的核心。
“十三五”期间是乙烯产能投产的高峰期,在炼化一体化、企业内部互供原料的格局下,乙烯原料已逐步向多样化、轻质化发展,但乙烯原料缺口仍然很大,主要大型乙烯裂解装置原料供应均依托于千万吨级炼厂,乙烯装置的设计以及实际原料组成仍将以石脑油为主,其裂解主要产物中三烯和三苯均为重要基础化工原料,其他产物如抽余C4、裂解汽油、裂解燃料油等产品附加值较高[1-4]。
石油化工装置常用“三剂”基础知识
图2-2-2 催化反应原理图
催化剂的基本特征 在长期的生产实践和科学实验中,人们总结出催化剂有 以下基本的特征: (1)催化剂只能加速在化学上(通过热力学计算判断) 可能进行的反应速度,而不能加速在热力学上无法进行的反 应。 (2)催化剂只能改变化学反应的速率,而不能改变化学 平衡位置。 (3)催化剂对反应具有选择性,或者说对复杂反应具有 定向作用,因而并没有万能的催化剂。 (4)催化剂能改变化学反应速率,但它本身并不进入化 学反应的化学计量。 (5)催化剂的使用寿命是有限的。
催化剂的分类:
生物催化剂 按催化作用分类 均相催化剂 多相催化剂
石油化工催化剂 石油炼制催化剂 按使用领域分类 无机化工催化剂 环境保护催化剂
第3章 催化剂的基本特征及性能评价
催化剂的特性和性能评价 在某些反应中,单一的元素或化合物可作为催化剂,但在多数场合 为了使催化剂具备特定的性能,常由几种成分配合而成。在催化剂中起 催化作用的主要部分为具有催化活性的物质,称为活性组分。催化剂由 单一组分构成时,这一组分即为活性组分,对于固体催化剂来说称为无 载体催化剂。 在石油化工中最常用的是固体催化剂,一般来说是由活性组分(主 催化剂)、助催化剂、催化剂载体三部分组成。 活性组分是使催化剂具备活性所必需的成分,是起催化作用的根本 物质。 助催化剂是一类能改善活性组分的催化性能的物质,这类物质单独 存在时并不呈现所需要的催化活性,但与催化活性组分共存时则可改善 后者的催化性能,可提高催化剂的活性、选择性,改善催化剂的耐热性、 抗毒性、机械强度和寿命等性能。
时间 20世纪初
化学反应过程 油脂加氢制硬化油 由合成气制甲烷
催化剂 Ni Ni Fe Fe
10年代
合成氨-Haber-Bosch过程 煤加氢合成液态烃-Bergius过程
- 1、下载文档前请自行甄别文档内容的完整性,平台不提供额外的编辑、内容补充、找答案等附加服务。
- 2、"仅部分预览"的文档,不可在线预览部分如存在完整性等问题,可反馈申请退款(可完整预览的文档不适用该条件!)。
- 3、如文档侵犯您的权益,请联系客服反馈,我们会尽快为您处理(人工客服工作时间:9:00-18:30)。
1. Introduction
Ethylene is one of the most important organic materials; it is used as a building block to produce fibers, plastics, and other chemicals. Global ethylene production capacity was around 1.48 Â 108 t in 2014, representing a 32% increase over the past decade [1]. At present, ethylene is almost exclusively produced via the steam cracking of gaseous and liquid hydrocarbon feedstocks such as ethane, naphtha, and gas oil. Due to its high endothermicity and complex product-separation steps, steam cracking is one of the most energy-intensive processes in the chemical industry. Although ethane is the most common feedstock for cracking in the United States and Middle East, more than 80% of the ethylene produced in Europe and the Asian-Pacific region is from naphtha [2,3].
The oxidative cracking of naphtha using a heterogeneous catalyst is a promising option [8–10]. However, the high reactivity of
V.P. Haribal et al. / Engineering 4 (2018) 714–721
Ó 2018 THE AUTHORS. Published by Elsevier LTD on behalf of Chinese Academy of Engineering and Higher Education Press Limited Company. This is an open access article under the CC BY-NC-ND license
715
the olefins poses a challenge in identifying a suitable catalyst with high selectivity [11]. Moreover, there is an additional difficulty of separating the oxygenate byproducts [6]. The flammability of the gaseous mixture, which contains oxygen (O2) and fuels, also presents safety concerns. Hot spots can result from over-oxidation of the hydrocarbons to carbon monoxide (CO) and CO2, lowering the product selectivity [3,12,13]. The current study investigates a two-step, redox oxy-cracking (ROC) process for naphtha conversion in an O2-free environment. The first step involves selective oxidation of the hydrogen (H2) produced from hexane cracking with active lattice oxygen in a mixed-oxide redox catalyst. The redox catalyst particles, which enter the reactor at high temperatures, provide the sensible heat to compensate for the endothermicity of the cracking reactions. Meanwhile, the catalyst is reduced during this step. The reduced redox catalyst is later oxidized, regenerated, and reheated in air to complete the redox loop. The absence of gas-phase oxygen in the naphtha conversion step has the potential to ① inhibit the non-selective reaction pathways, ② reduce the potential safety hazards [13–15], and ③ decrease parasitic energy losses by eliminating the air-separation unit and providing tighter temperature control [16]. The overall process also significantly decreases the energy consumption and, hence, the nitrogen oxide (NOx) and CO2 emissions. Despite its advantages over steam cracking and conventional oxy-cracking, this novel ROC approach has yet to be investigated in detail.
abstract
Ethylene production by the thermal cracking of naphtha is an energy-intensive process (up to 40 GJ heat per tonne ethylene), leading to significant formation of coke and nitrogen oxide (NOx), along with 1.8– 2 kg of carbon dioxide (CO2) emission per kilogram of ethylene produced. We propose an alternative process for the redox oxy-cracking (ROC) of naphtha. In this two-step process, hydrogen (H2) from naphtha cracking is selectively combusted by a redox catalyst with its lattice oxygen first. The redox catalyst is subsequently re-oxidized by air and releases heat, which is used to satisfy the heat requirement for the cracking reactions. This intensified process reduces parasitic energy consumption and CO2 and NOx emissions. Moreover, the formation of ethylene and propylene can be enhanced due to the selective combustion of H2. In this study, the ROC process is simulated with ASPEN PlusÒ based on experimental data from recently developed redox catalysts. Compared with traditional naphtha cracking, the ROC process can provide up to 52% reduction in energy consumption and CO2 emissions. The upstream section of the process consumes approximately 67% less energy while producing 28% more ethylene and propylene for every kilogram of naphtha feedstock.
Naphtha is a mixture of hydrocarbons with a boiling point range of 30–200 °C. In naphtha-based steam-cracking processes, naphtha is first fed into the convective section of the furnace for preheating
Vasudev Pralhad Haribal a, Yun Chen a,b, Luke Neal a, Fanxing Li a,⇑
a Department of Chemical and Biomolecular Engineering, North Carolina State University, Raleigh, NC 27695-7905, USA b School of Chemistry and Chemical Engineering, South China University of Technology, Guangzhou 510640, China