塑料壳体模具设计说明书
外壳塑料零件模具设计说明书

(4)模具设计、加工及各种管理将向数字化、信息化方向发展CAD/CAE/CAM/CAPP及PDM/PLM/ERP等将向智慧化、集成化和网络化方向发展。
(5)更高速、更高精度、更加智慧化的各种模具加工设备将进一步得到发展和推广应用。
分流道设计:
分流道是主流道与浇口之间的通道,一般分设在分型面上,起分流和转向的作用.
(1)、分流道的长度和断面尺寸
分流道的长度取决于模具型腔的总体布置方案和浇口位置,从输送熔体时的减少压力损失和热量损失及减少浇道凝料的要求出发,应力求缩短。L取15.5mm分流道断面尺寸ABS取4。8~9。5取6mm.
本设计通过对壳型塑料件工艺的正确分析,完成一副一模两腔的塑料模具设计。详细地完成模具成型零件包括垫块、复位杆、浇口套、拉料杆、上模座、推板等的设计,重要零件的工艺参数的选择与计算,推出机构与浇注系统以及其它结构的设计过程,并对产品的制作过程作了介绍.
第一章
1。1中国模具发展现状
中国的塑料模具虽然在数量、质量、技术等方面都有了很大进步,但与国民经济发展需求、世界先进水平相比,差距仍很大。一些大型、精密、复杂、长寿命的中高档塑料模具每年仍需大量进口。目前国内一些中、低档塑料模具供过于求,市场竞争激烈。
3
该材料为丙烯腈—丁二烯-苯乙烯共聚物(ABS)
基本特征:ABS是由丙烯腈、丁二烯、苯乙烯共聚而成的。这三种组分各自的特性,使ABS具有良好的综合力学性能。丙烯腈使ABS有良好的耐化学腐蚀及表面硬度,丁二烯使ABS坚韧,苯乙烯使它有良好的加工性和染色性能。
ABS无毒、无味、呈微黄色,成型的塑料有较的光泽。密度为0。9~0.23g /cm。ABS有极好的抗冲击强度,且在低温下也在不迅速下降.ABS有良好的机械强度和一定的耐磨性、耐寒性、耐油性、耐水性、化学稳定性和电气性能.水、无机盐类对ABS几乎无影响,但在酮、醛、酯、中会溶解或形成乳浊液.ABS不溶于大部分醇类,ABS塑料表面受冰醋酸、植物油等化学药品引起开裂.ABS有一定的硬度和尺寸稳定性,易于成型加工,经过调色可配成任何颜色。ABS的缺点就是耐热性不高,连续工作温度为70℃左右,热变形温度93℃左右,且耐气候性差,在紫外线作用先易变硬发脆.
PA66罩壳注塑模具设计说明书
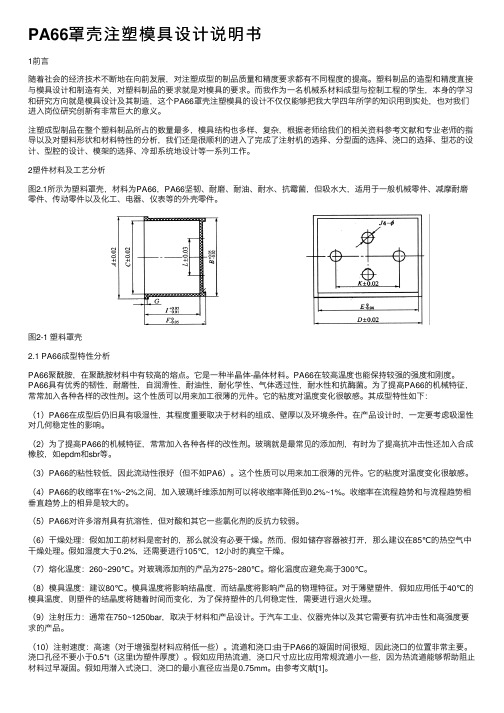
PA66罩壳注塑模具设计说明书1前⾔随着社会的经济技术不断地在向前发展,对注塑成型的制品质量和精度要求都有不同程度的提⾼。
塑料制品的造型和精度直接与模具设计和制造有关,对塑料制品的要求就是对模具的要求。
⽽我作为⼀名机械系材料成型与控制⼯程的学⽣,本⾝的学习和研究⽅向就是模具设计及其制造,这个PA66罩壳注塑模具的设计不仅仅能够把我⼤学四年所学的知识⽤到实处,也对我们进⼊岗位研究创新有⾮常巨⼤的意义。
注塑成型制品在整个塑料制品所占的数量最多,模具结构也多样、复杂,根据⽼师给我们的相关资料参考⽂献和专业⽼师的指导以及对塑料形状和材料特性的分析,我们还是很顺利的进⼊了完成了注射机的选择、分型⾯的选择、浇⼝的选择、型芯的设计、型腔的设计、模架的选择、冷却系统地设计等⼀系列⼯作。
2塑件材料及⼯艺分析图2.1所⽰为塑料罩壳,材料为PA66,PA66坚韧、耐磨、耐油、耐⽔、抗霉菌,但吸⽔⼤,适⽤于⼀般机械零件、减摩耐磨零件、传动零件以及化⼯、电器、仪表等的外壳零件。
图2-1 塑料罩壳2.1 PA66成型特性分析PA66聚酰胺,在聚酰胺材料中有较⾼的熔点。
它是⼀种半晶体-晶体材料。
PA66在较⾼温度也能保持较强的强度和刚度。
PA66具有优秀的韧性,耐磨性,⾃润滑性,耐油性,耐化学性、⽓体透过性,耐⽔性和抗酶菌。
为了提⾼PA66的机械特征,常常加⼊各种各样的改性剂。
这个性质可以⽤来加⼯很薄的元件。
它的粘度对温度变化很敏感。
其成型特性如下:(1)PA66在成型后仍旧具有吸湿性,其程度重要取决于材料的组成、壁厚以及环境条件。
在产品设计时,⼀定要考虑吸湿性对⼏何稳定性的影响。
(2)为了提⾼PA66的机械特征,常常加⼊各种各样的改性剂。
玻璃就是最常见的添加剂,有时为了提⾼抗冲击性还加⼊合成橡胶,如epdm和sbr等。
(3)PA66的粘性较低,因此流动性很好(但不如PA6)。
这个性质可以⽤来加⼯很薄的元件。
它的粘度对温度变化很敏感。
塑料壳体模具课程设计说明书222
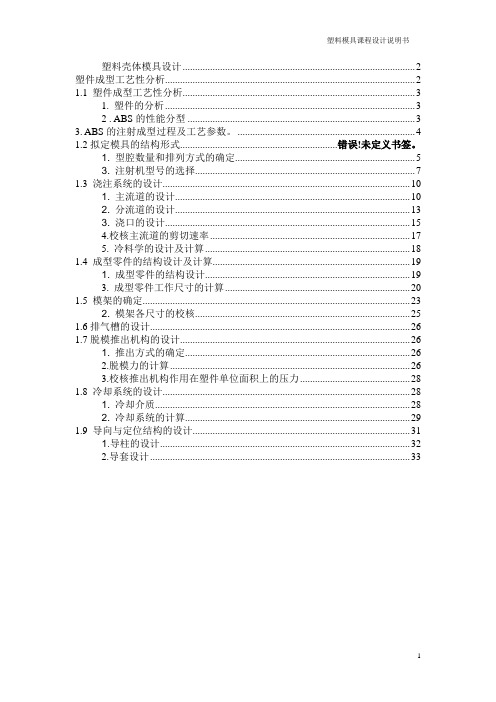
塑料壳体模具设计 (2)塑件成型工艺性分析 (2)1.1 塑件成型工艺性分析 (3)1. 塑件的分析 (3)2 . ABS的性能分型 (3)3. ABS的注射成型过程及工艺参数。
(4)1.2拟定模具的结构形式...............................................................错误!未定义书签。
1. 型腔数量和排列方式的确定 (5)3. 注射机型号的选择 (7)1.3 浇注系统的设计 (10)1. 主流道的设计 (10)2. 分流道的设计 (13)3. 浇口的设计 (15)4.校核主流道的剪切速率 (17)5. 冷料学的设计及计算 (18)1.4 成型零件的结构设计及计算 (19)1. 成型零件的结构设计 (19)3. 成型零件工作尺寸的计算 (20)1.5 模架的确定 (23)2. 模架各尺寸的校核 (25)1.6排气槽的设计 (26)1.7脱模推出机构的设计 (26)1. 推出方式的确定 (26)2.脱模力的计算 (26)3.校核推出机构作用在塑件单位面积上的压力 (28)1.8 冷却系统的设计 (28)1. 冷却介质 (28)2. 冷却系统的计算 (29)1.9 导向与定位结构的设计 (31)1.导柱的设计 (32)2.导套设计 (33)塑料壳体模具设计塑件成型工艺性分析考虑到主该塑料件是一壳体,塑件壁属厚壁塑件,生产批量大,材料选ABS,流道应尽可能短,一般小于60mm,过长则会影响熔体的顺利充型,零件尺寸图形如图1所示:材料 A B C D E F G H I J ABS 105 125 45 5 3 90 40 119 20 40图1 塑料壳体1.1 塑件成型工艺性分析1. 塑件的分析(1)外形尺寸该塑件壁厚为3mm,塑件外形尺寸不大,塑料熔体流程不太长,适合于注射成型。
(2)精度等级每个尺寸的公差都不一样,有的属于一般精度,有的属于高级精度,就按实际公差进行计算。
塑料模具设计说明书【含设计步骤】
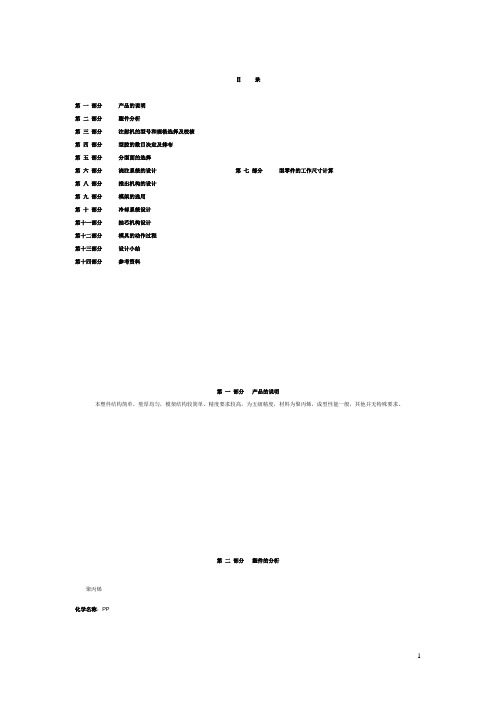
目录第一部分产品的说明第二部分塑件分析第三部分注射机的型号和规格选择及校核第四部分型腔的数目决定及排布第五部分分型面的选择第六部分浇注系统的设计第七部分型零件的工作尺寸计算第八部分推出机构的设计第九部分模架的选用第十部分冷却系统设计第十一部分抽芯机构设计第十二部分模具的动作过程第十三部分设计小结第十四部分参考资料第一部分产品的说明本塑件结构简单,壁厚均匀,模架结构较简单。
精度要求较高,为五级精度,材料为聚丙烯,成型性能一般,其他并无特殊要求。
第二部分塑件的分析聚丙烯化学名称:PP材料分析:塑件的材料采用增强聚丙烯(本色),属于塑性塑料。
从使用性能上看,该塑料具有刚度好、耐水、耐热性强,其介电性能与温度和频率无关等优点,是理想的绝缘材料;从成型性能上看,该塑料吸水性能小,熔料的流动性能较好,成型容易,但收缩率大。
另外,该塑料成型时易产生缩孔、凹痕、变形等缺陷,成型温度低时,方向性明显,凝固速度较快,易产生内应力。
因此,在成型时应注意控制成型温度,浇注系统应较缓慢散热,冷却速度不宜过快。
塑件注射成型工艺参数的确定:根据该塑件的结构特点和得成型性能,查相关手册得到聚丙烯的成型工艺参数:塑件的注射成型工艺参数工艺参数内容工艺参数内容注射时间0~5预热和干燥温度80~90℃成型时间/s时间0.5h 保压时间20~60前段180~200 冷却时间15~50料筒温度/℃中段200~220 总周期35~115后段160~170 螺杆转速/(r/min)30~60喷嘴温度/℃170~190方法室温空冷后处理模具温度/℃20~60 温度/℃20~30注射压力/MPa 70~120 时间/h 1~2第三部分注射机的型号和规格选择及校核注射模是安装在注射机上的,因此在设计注射模具时应该对注射机有关技术规范进行必要的了解,以便设计出符合要求的模具,同时选定合适的注射机型号。
从模具设计角度考虑,需要了解注射机的主要技术规范。
塑料模具设计说明书实例
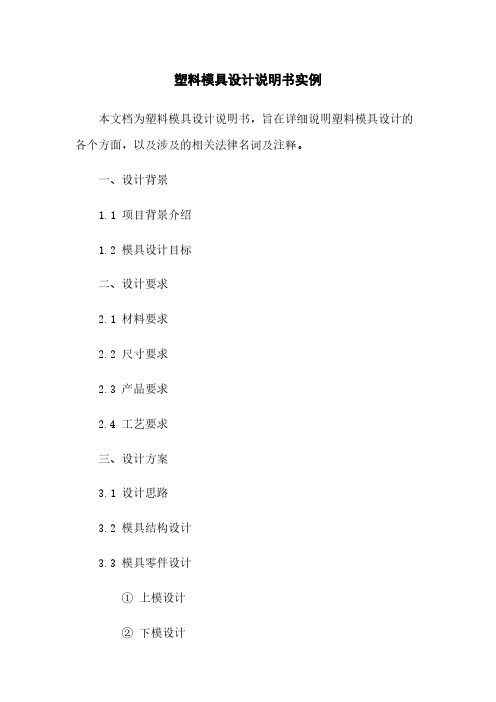
塑料模具设计说明书实例本文档为塑料模具设计说明书,旨在详细说明塑料模具设计的各个方面,以及涉及的相关法律名词及注释。
一、设计背景1.1 项目背景介绍1.2 模具设计目标二、设计要求2.1 材料要求2.2 尺寸要求2.3 产品要求2.4 工艺要求三、设计方案3.1 设计思路3.2 模具结构设计3.3 模具零件设计①上模设计②下模设计③滑动模设计④顶针设计3.4 模具槽设计3.5 模具总体设计四、零件加工与装配4.1 零件加工工艺4.2 模具装配工艺五、设计验证与修改5.1 模具样品检验5.2 修改方案六、其他设计考虑6.1 模具标准件选用6.2 模具自动化程度6.3 模具维修保养附件:详细图纸及说明法律名词及注释:1.模具:指用于制造特定形状、尺寸和表面质量的工业品的工具或设备。
2.材料要求:涉及模具所使用的材料的性能、可加工性和稳定性等方面的要求。
3.尺寸要求:模具设计需要满足的产品尺寸精度和公差要求。
4.产品要求:对模具加工后产品的外观、性能、规格等方面的要求。
5.工艺要求:模具设计中需要考虑的制造工艺、表面处理工艺等要求。
6.模具结构设计:根据产品形状和要求,设计模具的整体结构和组成方式。
7.模具零件设计:对模具的各个零部件进行细化设计,包括上模、下模、滑动模、顶针等。
8.模具槽设计:对模具槽的形状、尺寸和位置等进行设计。
9.模具样品检验:对模具制作完成后的样品进行外观质量、尺寸精度等方面的检验。
10.修正方案:根据样品检验结果,对模具进行必要的修改和调整。
外壳塑料零件模具设计说明书
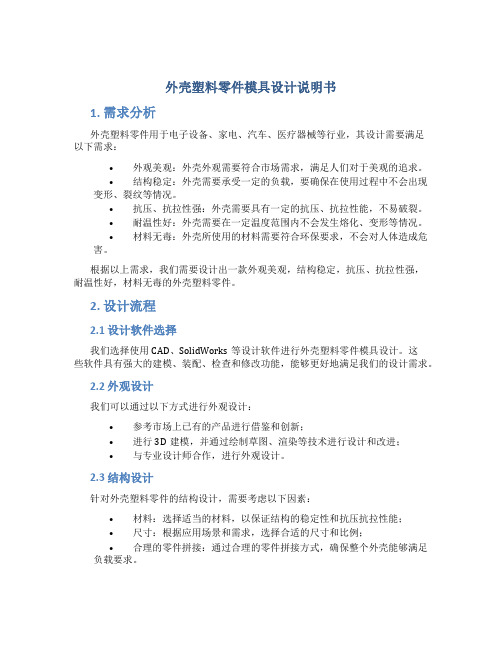
外壳塑料零件模具设计说明书1. 需求分析外壳塑料零件用于电子设备、家电、汽车、医疗器械等行业,其设计需要满足以下需求:•外观美观:外壳外观需要符合市场需求,满足人们对于美观的追求。
•结构稳定:外壳需要承受一定的负载,要确保在使用过程中不会出现变形、裂纹等情况。
•抗压、抗拉性强:外壳需要具有一定的抗压、抗拉性能,不易破裂。
•耐温性好:外壳需要在一定温度范围内不会发生熔化、变形等情况。
•材料无毒:外壳所使用的材料需要符合环保要求,不会对人体造成危害。
根据以上需求,我们需要设计出一款外观美观,结构稳定,抗压、抗拉性强,耐温性好,材料无毒的外壳塑料零件。
2. 设计流程2.1 设计软件选择我们选择使用CAD、SolidWorks等设计软件进行外壳塑料零件模具设计。
这些软件具有强大的建模、装配、检查和修改功能,能够更好地满足我们的设计需求。
2.2 外观设计我们可以通过以下方式进行外观设计:•参考市场上已有的产品进行借鉴和创新;•进行3D建模,并通过绘制草图、渲染等技术进行设计和改进;•与专业设计师合作,进行外观设计。
2.3 结构设计针对外壳塑料零件的结构设计,需要考虑以下因素:•材料:选择适当的材料,以保证结构的稳定性和抗压抗拉性能;•尺寸:根据应用场景和需求,选择合适的尺寸和比例;•合理的零件拼接:通过合理的零件拼接方式,确保整个外壳能够满足负载要求。
2.4 模具设计在外壳塑料零件的设计过程中,我们需要考虑模具的设计,确保能够按照设计要求进行制造。
模具设计需要考虑以下因素:•模具选材:根据设计要求,选择适当的材料;•模具结构:通过合理的模具结构设计,提高模具的寿命和生产效率;•模具加工:使用精密的加工设备进行加工,确保模具制造精度和质量。
3. 设计结果通过以上设计流程,我们可以得到一款满足市场需求,符合设计要求的外壳塑料零件模具。
我们可以进行3D打印进行模型验证,或进行小批量生产进行测试。
4.本文介绍了外壳塑料零件模具的设计流程,从需求分析、软件选择、外观设计、结构设计、模具设计和设计结果等方面进行了简述。
壳体注塑模具设计说明书
1.绪论模具作为工业产品的重要基础工艺装备,在工业生产中是不可或缺的技术与工具,它不仅直接影响工业产品的水平,也是一个国家工业化程度和机械制造工业技术水平的综合体现。
本设计是应用计算机软件来完成注塑模具的设计。
本题目涉及注塑模具设计、计算机绘图软件应用等方面知识。
1.1塑料模具发展现状我国塑料模具工业从起步到现在,历经半个多世纪,有了很大发展,模具水平有了较大提高。
由于模具生产产品具有精度高、复杂性高、一致性好、生产效率高、消耗低等优良特性,所以在现代工业中将会起到更大的作用,得到更多的应用。
我国的塑料模具发展至今,已能生产精度达2微米的精密多工位级进模,工位数最多已达160个,寿命1~2亿次。
1.2研究注塑模具的意义模具是现代工业发展的基础,许多产业的发展都离不开模具行业的支持。
用模具生产制件所表现出来的高精度、高复杂程度、高一致性、高生产率和低消耗,是其他加工制造方法所不能比拟的。
在模具工业的总产值中,塑料模具约占33%左右。
不同的塑料成型方法使得塑料模具的原理和结构不同。
按照成型方法的不同,塑料模具分为:注塑模具、压塑模具、挤出模具、吹塑模具等。
注塑模具主要用于热塑型塑料制品的成型,近年来也越来越多的用于热固性塑料制品的成型,注塑成型在塑料制品成型中占有很大比重,世界上塑料成型模具的产量半数以上是注塑模具。
现代工业中,消费品外壳的色彩、手感、精度、壁厚等都提出了新要求,塑料外壳设计成为重要的一环。
精密、设计合理(主要针对薄壁制品)的注塑模具将得到越来越多的应用。
1.3现代注塑模具设计方法目前为了应付当前市场多样化的要求,缩短产品制造周期以取得最佳的竞争优势,模具设计中都引入了CAD/CAM/CAE[8](计算机辅助设计/辅助制造/辅助工程)计算机一体化制造技术[3],以提高产品质量,降低成本,增加竞争力。
一般而言,一件完整理想的工业产品,其制造流程为先有原创型的概念设计出原件,配合计算机辅助工程分析技术,再依据分析结果修改、测试,最后再依此设计图经由计算机辅助制造,进行产品自动化生产,上述整个过程均在计算机上进行[10]。
外壳注塑模具设计说明书
目录1工艺性能分析和结构方案的确定和所需设备的校核 (1)1.1工艺性能分析和模具方案的确定 (1)1.1.1 工艺性能分析 (1)1.1.2 确定模具结构方案 (2)1.2注射机型号的选定及校核 (2)1.2.1 注射量的计算 (3)1.2.2 锁模力的计算 (3)1.2.3 选择注射机 (3)2浇注系统的设计和排溢系统的设计 (4)2.1主流道的设计 (4)2.1.1 主流道的设计 (4)2.1.2 浇口的设计 (5)2.1.3 分流道的设计 (6)2.1.4 冷料穴的设计 (6)2.1.5 排溢系统的设计 (6)3 成型零部件的设计 ........................................ 错误!未定义书签。
3.1凹模(型腔)的设计..................................... 错误!未定义书签。
3.1.1 凹模直径 ..................................................... 错误!未定义书签。
3.1.2 凹模深度(圆柱部分).......................................... 错误!未定义书签。
3.2凸模(型芯)的设计..................................... 错误!未定义书签。
3.2.1 凸模径向尺寸 ................................................. 错误!未定义书签。
3.3成型塑件侧面型芯的设计................................. 错误!未定义书签。
4侧抽和内抽机构的设计及校核 (7)4.1浇注系统凝料的脱出 (7)4.2推出方式的确定 (7)4.3侧抽零件的设计 (7)4.3.1 抽芯距S的计算 (7)4.3.2 斜销有效长度L的计算 (7)4.3.3 斜销的直径d (7)4.3.4 斜销长度的计算 (8)5 模架的设计 (9)5.1模架的设计和对其的校核 (9)5.1.1 模架的选择 (9)5.1.2 定模座板的设计 (9)5.1.3 侧抽芯滑块的设计 (10)5.1.4 型芯固定板的设计 (10)5.1.5 垫板的设计 (10)5.1.6 垫块的设计和校核 (10)5.1.7 动模座板的设计 (10)6推出机构和复位机构的设计 (11)6.1推出机构和复位机构的设计 (11)6.1.1 脱模力的计算 (11)6.1.2 拉杆直径的确定 (12)6.1.3 推件机构导向的设计 (13)6.1.4 复位机构的设计 (13)7冷却系统的设计和校核 (13)7.1冷却水道的设计 (13)7.1.1 冷却水道的选择 (13)7.1.2 冷却水的体积流量 (13)7.1.3 冷却管道直径的确定 (14)7.1.4 冷却水在管道中的流速 (14)7.1.5 冷却管道孔壁与冷却水之间的传热模系数 (14)7.1.6 冷却管道的总传热面积 (14)7.1.7 模具上应开设的冷却水孔数 (14)参考文献 (15)1工艺性能分析和结构方案的确定和所需设备的校核1.1工艺性能分析和模具方案的确定1.1.1工艺性能分析图1.1 零件图(1)形状:如图所示.该制件为塑料外壳.外形尺寸直径为Φ108mm.壁厚为3mm.高为16mm.形状为圆形壳体。
塑料模具设计说明书
塑料模具设计说明书塑料模具设计说明书1.引言在本文档中,我们将详细说明塑料模具的设计要求和技术规范,以确保模具的性能和质量满足项目要求。
本说明书适用于塑料模具的设计和制造。
2.设计需求2.1 目标和用途明确模具的使用目标和用途,例如生产特定塑料制品、塑料零件,或者其他要求。
2.2 材料要求根据目标和用途选择适当的塑料材料,考虑材料的强度、耐磨性、耐高温性等因素,并确保满足相关法律法规的要求。
2.3 几何要求定义模具的尺寸、形状、几何特征,包括外观要求、内部结构、孔洞等细节,并确保符合客户的要求和标准。
2.4 模具寿命和维护考虑模具的寿命和维护要求,选择适当的材料和制造工艺,设计合理的模具结构,以延长模具的使用寿命并减少维护成本。
3.设计过程3.1 初步设计基于客户提供的产品要求和样品,进行初步设计,包括模具的整体结构、分模结构、定位结构等。
3.2 详细设计基于初步设计,进行详细设计,包括模具的每个零部件的尺寸、形状、位置等具体要求,并绘制相应的设计图纸和模型。
3.3 模具流程分析进行模具流程分析,确定塑料注射过程中可能出现的问题和优化方案,包括模具分线、喷嘴位置、冷却系统等。
3.4 模具结构优化根据模具流程分析结果,优化模具结构,提高生产效率和产品质量,并确保模具的可维护性和可调试性。
4.制造要求4.1 材料采购选择合适的材料供应商,并根据设计要求采购所需的塑料材料,确保材料的质量和兼容性。
4.2 制造工艺选择适当的制造工艺,包括雕刻、铣床加工、精密加工等,并确保每个制造步骤的准确性和质量。
4.3 安装和调试按照设计要求进行模具的安装和调试,确保模具的正常运行和稳定性,并进行必要的调整和修正。
5.模具测试和验收进行模具测试和验收,包括检查模具的尺寸精度、结构强度、生产效率等指标,并根据测试结果做必要的修改和优化。
附件:本文档所涉及的附件包括设计图纸、模型文件、测试报告等,请参阅相关附件。
法律名词及注释:1.模具:用于生产塑料制品或零件的工具或设备。
塑料模具设计说明书实例
塑料模具设计说明书姓名吴高安班级模具 1301塑料模具设计说明书目录1.塑件的工艺剖析塑件的成型工艺性剖析塑件如图 1 所示。
图1 塑件图产品名称:套管产品资料: ABS产品数目:较大量量生产塑件尺寸:如图 1 所示塑件重量: 25 克塑件颜色:红色塑件要求:塑件外侧表面圆滑,下端外沿不同意有浇口印迹。
塑件同意最大脱模斜度°塑件资料 ABS的使用性能可参照《简洁塑料模具设计手册》 P30表 1-13综合性能较好,冲击韧度、力学强度较高,尺寸稳固,耐化学性、电气性能优秀;易于成形和机械加工,与有机玻璃的熔接性优秀,可作双色成形塑件,且表面可镀铬。
适于制作一般机械部件、减摩耐磨部件、传动部件和电信构造部件。
塑件资料 ABS的加工特征可参照《简洁塑料模具设计手册》 P32表 1-14无定型塑料,其品种好多,各品种的机电性能及成形特征也各有差别,应按品种确立成形方法及成形条件。
吸湿性强,含水量应小于%,一定充足干燥,要求表面光彩的塑件应要求长时间预热干燥。
流动性中等,溢边料 mm左右(流动性比聚苯乙烯,AS差,但比聚碳酸酯、聚氯乙烯好)。
比聚苯乙烯加工困难,宜取高料温、模温(对耐热、高抗冲击和中抗冲击型树脂,料温更宜取高)。
料温对物性影响较大、料温过高易分解(分解温度为250℃左右,比聚苯乙烯易分解),对要求精度较高塑件,模温宜取 50~ 60℃,要求光彩及耐热型料宜取60~80℃。
注射压力应比加工聚苯乙烯稍高,一般用柱塞式注塑机时料温为180~ 230℃,注射压力为 100~ 140 MPa,螺杆式注塑机则取160~ 220℃, 70~ 100 MPa为宜。
模具设计时要注意浇注系统,选择好进料口地点、形式。
推卖力过大或机械加工时塑件表面体现“白色”印迹(但在热水中加热可消逝)。
脱模斜度宜取2℃以上。
塑件的成型工艺参数确立可参照《简洁塑料模具设计手册》 P54表 1-18查手册获得ABS塑料的成型工艺参数:合用注射机种类螺杆式密度~ g/cm 3;缩短率~ % ;预热温度80C°~ 85C°,预热时间 2 ~ 3 h;料筒温度后段 150C°~ 170C°,中段 180C°~ 200C°,前段 160C°~ 180C°;喷嘴温度 170C °~ 180C°;模具温度 50C°~ 80C°;注射压力60~ 100 MPa ;成型时间注射时间 20 ~ 90s,保压时间 0 ~ 5s,冷却时间20 ~ 120s 。
- 1、下载文档前请自行甄别文档内容的完整性,平台不提供额外的编辑、内容补充、找答案等附加服务。
- 2、"仅部分预览"的文档,不可在线预览部分如存在完整性等问题,可反馈申请退款(可完整预览的文档不适用该条件!)。
- 3、如文档侵犯您的权益,请联系客服反馈,我们会尽快为您处理(人工客服工作时间:9:00-18:30)。
Hefei University课程设计C O U R S E P R O J E C T题目:注塑模课程设计系别:机械工程系专业:07材料成型及控制工程(2)班学制:四年姓名:徐斌学号:0706032003导师:周伟2010年9 月10 日目录一.塑件成型工艺性分析 (3)二.分型面位置的确定 (3)三.确定型腔数量和排列方式 (3)四.模具结构形式的确定 (4)五.注射机型号的选定 (4)六.浇注系统的设计 (5)6.1 主流道设计 (5)6.2 主流道衬套的形式 (6)6.3 主流道衬套的固定 (7)6.4 冷料穴的设计 (7)6.5 分流道设计 (8)6.6 浇口的设计 (9)6.7 浇注系统的平衡 (10)6.8 浇注系统凝料体积计算 (10)6.9 .普通浇注系统截面尺寸的计算与校核 (10)6.9.1 确定适当的剪切速率r (10)6.9.2 确定体积流率q (10)6.9.3 注射时间(充模时间)的计算 (11)6.9.4 校核各处剪切速率 (11)七.成型零件的结构设计和计算 (11)八.合模导向机构的设计 (14)8.1 导向机构的总体设计 (14)8.2 导柱的设计 (14)8.3 导套设计 (14)九.脱模推出机构的设计 (16)十.湿度调节系统设计 (17)总结 (19)参考文献 (20)一.塑件成型工艺性分析该塑件是一壳体,塑件壁属厚壁塑件,生产批量大,材料选PS,考虑到主流道应尽可能短,一般小于60mm,过长则会影响熔体的顺利充型,因此采用下列数据:二.分型面位置的确定根据塑件结构形式分型面应选在I上,如下图:三.确定型腔数量和排列方式1.该塑件精度要求不高,批量大,可以采用一模多腔,考虑到模具的制造费用和设备的运转费用,定为一模四腔。
2.型腔排列方式的确定如下图:四.模具结构形式的确定从上面的分析中可知本模具采用一模四腔,双列直排,推件板推出,流道采用平衡式,浇口采用侧浇口,动模部分需要一块型芯,固定板,支撑板。
五.注射机型号的选定1.通过分析,塑件为=1m 26.5g ,∂=/m v 11,=∂ 1.05 V=25.23cm ,流道凝料的质量12.6m 0m = ==.6nm 1m2.塑件和流道凝料在分型面上的投影面积2A ,2A 可用0.35nA 1来进行估算,所以121A 5.31A nA A =+= n=1.35⨯4⨯A 1=25920mm 2 式中21mm 48006080A =⨯= 查表2-2<塑料模具设计指导> 取Mpa 25P =型N 6480002525920AP Fm =⨯==型 3.选择注射机根据每一生产周期的注射量和锁模力的计算值可选用SZ-250/1250理论注射量3/cm 270 锁模力KN /1250螺杆直径mm / 45 拉杆内间距mm /415⨯415 注射压力MPa /160 移模行程mm /360 注射速率s g //110 最大模厚mm / 塑化能力/18.9 最小模厚mm /150 螺杆转速200~10/ 定位孔直径mm /160 喷嘴半径mm /15 锁模方式/双曲肘 4、注射机有关参数的校核47.145.26/)5.2646.03600/3036009.188.0(/])3600/305.108.0[(/)3600/(2212≥=⨯⨯-⨯⨯⨯=-⨯⨯=-≤m m m m KMt n型腔数校核合格。
式中,K —-注塑机最大注射量的利用系数一般取0.8 m —注射机的额定塑化量(10.5g/s ) T —成型周期取30s 1)注射压力校核,c P k ≥ Mpa 195150.31P 0=⨯=,K ——注射压力的安全系数,一般取K ,=1.25-1.4 Mpa 130P 0取--,中等壁厚件 2)锁模力校核.6KN 777648.21KAP F =⨯=≥型。
而F=1250KN K 0--锁模力安全系数,一般取K 0=1.1-1.2其他安装尺寸的校核要待模架的选定,结构尺寸确定后才可进行。
六.浇注系统的设计6.1 主流道设计1)主流道尺寸设计根据所选注射机,则主流道小端尺寸为 d=注射机喷嘴尺寸+(0.5-1) =42)主流道球面半径为SR=喷嘴球面半径+(1-2)=16mm 3)球面配合高度 h=3mm-5mm ,取h=3mm4)主流道长度,尽量小于60,由标准模架结合该模具的结构,取 L=25+20=45mm 5)主流道大端直径D=d+2Ltana=6.54mm (半锥角a 为︒︒-21,取a=︒2)取D=6.5mm 6)浇口套总长 0L =25+20+h+2=50 6.2 主流道衬套的形式主流道小端入口处与注射机喷嘴反复接触属易损性,对材料要求严格,因而模具主流道部分常设计可拆卸更换的主流道衬套形式即浇口套,以便常用碳素工具如T8A ,T10A 等,热处理硬度为50HRC-55HRC ,如图示由于该模具主流道较长,定位圈和衬套设计成分体式较宜,其定位圈结构尺寸如下图6.3 主流道衬套的固定主流道衬套的固定形式如下图6.4 冷料穴的设计1)主流道冷料穴的设计开模时应将主流道中的凝料拉出,所以冷料穴直径稍大于主流道大端直径,采用Z 形头冷料穴,很容易将主流道凝料拉离定模,如图所示1:定模座板 2:冷料穴 3:动模板 4:推杆主流道凝料体积)5.35.35.65.6(12/40)(12/h Q 2222+⨯+=++=ππd Dd D 主 =809mm 2=0.8mm 2 主流道剪切速率校核 有经验公式v=3.3q/R π2v .5cm 1028.508.2254.80q q q q =+⨯+=++=塑件分主cm 25.02/]2/)5.65.3[(R n =+=主流道剪切速率偏小主要是注射量小,喷嘴尺寸偏大,使主流道尺寸偏大所致。
6.5 分流道设计1)分流道布置形式分流道布置有多种形式,但是需要循两方面原则;一方面排列紧凑,缩小模具版面尺寸;另一方面流程尽量短,锁模力力求平衡。
应采用平衡时分流道。
如图:2)分流道长度第一级分流道 mm 50L 1= 第二级分流道 mm 15L 2=3)分流道的形式。
截面尺寸以及凝料体积为了便于加工及凝料脱模,分流道大多设置在分型面上。
工程设计中常用梯形截面,加工工艺好,且塑料熔体的热量散失。
流动阻力均不大,一般采用下面的经验公式可确定其截面尺寸,即B=0.2654式中,B---梯形大底边的宽度 m---塑件的质量,为26.5g 根据《塑料模具设计手册》表4-9,取B=4 H=2/3B=2.67mm, 取H=3mm从理论上1.2,1.3分流道可以1.1截面小1/10,但为了刀具的统一和加工方便,在分型面上的分流道采用一样的截面。
4)分流道的表面粗糙度由于分流道中与模具接触的外层塑料迅速冷却,只有中心部位的塑料熔体的流动状态较理想,因此分流道的内表面粗糙度Ra 并不要求很低,一般取0.63um---1.6um ,这样表面并不光滑,有助于增大塑料熔体的外层流动阻力,避免熔体表面滑移,使中心层具有较高的剪切速率。
此处Ra=0.8um 。
5)凝料体积分流道长度 L=(50+8⨯2+1⨯2)⨯2=136mm 分流道截面面积 25.103]2/)43[(A mm =⨯+= 凝料体积 33cm 28.41mm 1428.510136q ==⨯=分 6)分流道剪切速率校核采用经验公式r=3.3q/6801)25.014.3(/2.1101.33R 33=⨯⨯=π 式中 q=v/t=4⨯25.28=101.12 6.6 浇口的设计浇口截面积通常为分流道截面积的0.07--0.09倍,浇口截面积形状多为矩形和圆形两种,浇口长度为0.5--2mm 。
浇口具体尺寸一般根据经验确定,取其下限值,然后在试模时逐渐修正。
(1)浇口类型及位置确定该模具是中小型塑件的多型腔模具,设置侧浇口比较合适,侧浇口开设在垂直分型面上,从型腔(塑件)外侧面进料,侧浇口是典型的矩形截面浇口,能很方便的调整充模时的剪切速率和浇口封闭时间,因而又被称为标准浇口。
这类浇口加工容易,修正方便,并且可以根据塑件的形状特征灵活地选择进料位置,因此它是广泛使用的一种浇口形式,普遍使用于中小型的多型腔模具。
(2)浇口结构尺寸的经验公式 侧浇口深度和宽度经验计算: 经验公式为 h=nt=1mm w=2.3 式中,h ——侧浇口深度(mm ) W ——浇口宽度(mm ) A ——塑件外表面积; T ——塑件厚度(约为3mm ) n ——塑料系数,查表得n=0.66.7 浇注系统的平衡对于该模具,从主流道到各个型腔的分流道的长度相等,形状及截面尺寸对应相同,各个浇口也相同,浇注是平衡的。
6.8 浇注系统凝料体积计算(1)主流道与主流道冷料井凝料体积3,2228.15919)(4/)(12/h V V V mm h D d Dd D =+++=⨯=ππ冷锥主 6.9 .普通浇注系统截面尺寸的计算与校核 6.9.1 确定适当的剪切速率r根据经验浇注系统各段的r 取以下值,所成型塑件质量较好。
1)主流道1312s s 105s 105r --⨯-⨯= 2)分流道 12R s 105r -⨯= 3)点浇口 15G s 10r -⨯= 4)其他浇口1413G s 105s 10r --⨯⨯=— 6.9.2 确定体积流率q1)主流道体积流率s q因塑件小,即使是一模四腔的模具结构,所需注射塑料熔体的体积也还是比较小的,而主流道尺寸并不小,因此主流道体积流率并不大,取13s s 101r -⨯=代入得:s cm r R /9.213.0104/4/q 3333s =⨯⨯==ππ2)浇口体积流率q g侧(矩形)浇口用适当的剪切速率14G s 101r -⨯=代入得:s cm r /386/101.03.26/Wh q 3422G =⨯⨯==6.9.3 注射时间(充模时间)的计算1)模具充模时间s q v s s 15.19.21/28.25/t s ===式中体的体积模具成型时所需塑料熔注射时间;主流道体积流率------v s s v t q ;2)单个型腔的充模时间s q G 66.038/25.25/V t G G ===3)注射时间根据经验公式求得注射时间s t G 82.03/23/t t a =+=6.9.4 校核各处剪切速率1)浇口剪切速率13223G 1059.61.03.2/25.256/V 6r -⨯=⨯⨯==s W h2)分流道剪切速率由经验公式 1333108.625.014.3/12.1013.3/3.3r -⨯=⨯⨯==s R q π七.成型零件的结构设计和计算塑料模具型腔在成型过程中受到塑料熔体的高压作用应具有足够的强度和刚度,如果型腔侧壁和底版厚度过小,可能因强度不够而产生塑性变形甚至破坏,也可能因刚度不足而产生挠曲变形,导致溢 14 料飞边,降低塑件尺寸精度并影响顺利脱模。