封装工艺流程简介 (3)
晶圆级封装的工艺流程_概述说明

晶圆级封装的工艺流程概述说明1. 引言1.1 概述晶圆级封装是一种先进的封装技术,它将多个组件和集成电路(IC) 封装在同一个晶圆上,从而提高了芯片的集成度和性能。
相比传统的单芯片封装方式,晶圆级封装具有更高的密度、更短的信号传输路径和更低的功耗。
因此,晶圆级封装已经成为微电子领域中一项重要且不断发展的技术。
1.2 文章结构本文将对晶圆级封装的工艺流程进行全面地概述说明。
首先,在引言部分,我们将对该主题进行简要概述并介绍文章结构。
接下来,在第二部分中,我们将详细阐述晶圆级封装的工艺概述以及相关的工艺步骤、特点与优势。
然后,在第三部分中,我们将探讨实施晶圆级封装工艺时需要考虑的关键要点,包括设计阶段、加工阶段和测试与质量管控方面的要点与技术要求。
在第四部分中,我们将介绍晶圆级封装工艺流程中常见问题及其解决方法,并提出提高封装可靠性的方法和策略,以及工艺流程改进与优化的建议。
最后,在第五部分中,我们将总结回顾晶圆级封装工艺流程,并展望未来晶圆级封装技术的发展方向和趋势。
1.3 目的本文的目的是全面介绍晶圆级封装的工艺流程,提供读者对该领域较为详细和系统的了解。
通过对每个章节内容的详细阐述,读者可以获得关于晶圆级封装工艺流程所涉及到的各个方面的知识和技术要求。
同时,通过对常见问题、解决方法以及未来发展方向等内容的探讨,读者可以更好地理解该技术在微电子领域中的重要性,并为相关研究和应用提供参考。
2. 晶圆级封装的工艺流程:2.1 工艺概述:晶圆级封装是一种先将芯片进行封装,然后再将封装好的芯片与其他组件进行连接的封装技术。
其主要目的是提高芯片的集成度和可靠性,并满足不同应用领域对芯片包装技术的需求。
晶圆级封装工艺拥有多个步骤,其中包括材料准备、焊膏印刷、IC贴装、回流焊接等过程。
2.2 工艺步骤:(1)材料准备:首先需要准备好用于晶圆级封装的相关材料,如底部基板、球柵阵列(BGA)、波士顿背面图案(WLCSP)等。
第二章 封装工艺流程
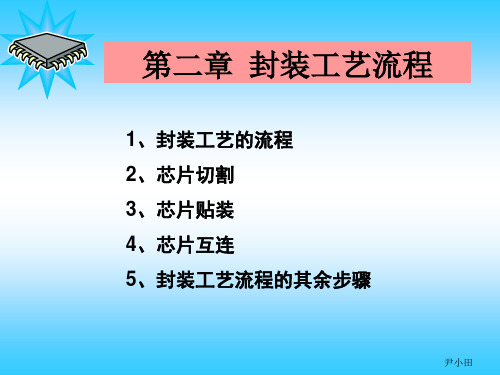
封装工艺的基本流程:
硅片减薄 芯片切割 硅片贴装 芯片互连
打码
上焊锡 切筋成形
成型技术即 (塑料封装) 去飞边毛刺
尹小田
硅片的尺寸越来越大,为了方便制 造、测试和运送过程,厚度增加。
硅片减薄 芯片切割 硅片贴装 芯片互连
成型技术即
打码 上焊锡 切筋成形
(塑料封装) 去飞边毛刺
背面减薄技术有: 磨削、研磨、干式抛光(Dry Polishing)、 化学机械抛光(chemical mechanicai polishing,CMP)、 电化学腐蚀(Electrochemical Etching)、 湿法腐蚀(Wet Etching,WE)、 等离子增强化学腐蚀(Plasma-Enhanced Chemical Etching,PECE) 常压等离子腐蚀(Atmosphere Downstream Plasma
尹小田
(4)玻璃胶粘贴法
方法:用高分子材料聚合物玻璃胶进行芯片粘贴。 工艺:先以盖印、网印、点胶的技术把胶原料涂布在基
板的芯片座中,再把芯片置于玻璃胶上粘贴。
1、多用于陶瓷封装中 2、冷却过程谨慎控制降温的速度以免造成应力破 裂
优3、点增:加可热以、得点到传无导空性隙能、,热可稳以定加性金优属良如的:、箔低、结银合应力、 低湿气含量的芯片粘贴;
尹小田
4、芯片互连
硅片减薄 芯片切割 硅片贴装 芯 切筋成形
(塑料封装) 去飞边毛刺
定义:把电子外壳的I/O引线或基板上的金线焊区与芯片的 焊区相连。
涂布合适的厚度和轮廓的芯片焊盘上进行固化。
1、各向同性材料。
不精确会怎样?
2、导电硅橡胶。
3、各向异性导电聚合物。 导电胶的缺点:热稳定性不好、高温时容易劣化和引发导 目电用的胶于导是中高电:有可胶改机靠中善物度填胶气要充的体求银导充的颗热分封粒性泄装或,漏。银增而薄强降片散低,热产因能品此力的都。 可是靠是度导,电因的此。不
简述LED生产工艺和LED封装流程
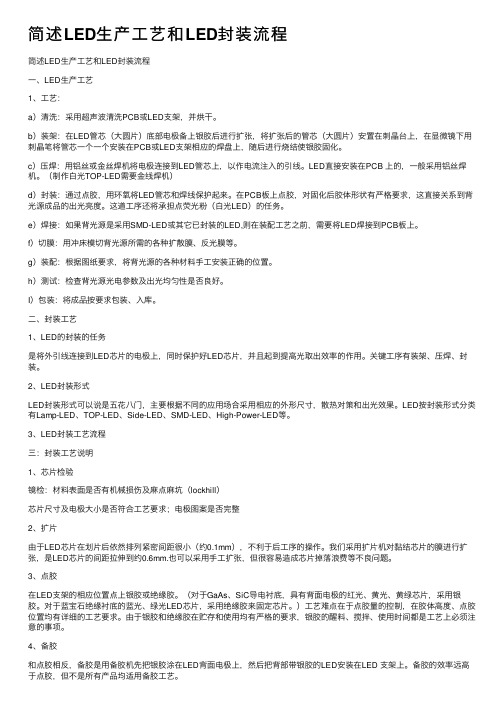
简述LED⽣产⼯艺和LED封装流程简述LED⽣产⼯艺和LED封装流程⼀、LED⽣产⼯艺1、⼯艺:a)清洗:采⽤超声波清洗PCB或LED⽀架,并烘⼲。
b)装架:在LED管芯(⼤圆⽚)底部电极备上银胶后进⾏扩张,将扩张后的管芯(⼤圆⽚)安置在刺晶台上,在显微镜下⽤刺晶笔将管芯⼀个⼀个安装在PCB或LED⽀架相应的焊盘上,随后进⾏烧结使银胶固化。
c)压焊:⽤铝丝或⾦丝焊机将电极连接到LED管芯上,以作电流注⼊的引线。
LED直接安装在PCB 上的,⼀般采⽤铝丝焊机。
(制作⽩光TOP-LED需要⾦线焊机)d)封装:通过点胶,⽤环氧将LED管芯和焊线保护起来。
在PCB板上点胶,对固化后胶体形状有严格要求,这直接关系到背光源成品的出光亮度。
这道⼯序还将承担点荧光粉(⽩光LED)的任务。
e)焊接:如果背光源是采⽤SMD-LED或其它已封装的LED,则在装配⼯艺之前,需要将LED焊接到PCB板上。
f)切膜:⽤冲床模切背光源所需的各种扩散膜、反光膜等。
g)装配:根据图纸要求,将背光源的各种材料⼿⼯安装正确的位置。
h)测试:检查背光源光电参数及出光均匀性是否良好。
I)包装:将成品按要求包装、⼊库。
⼆、封装⼯艺1、LED的封装的任务是将外引线连接到LED芯⽚的电极上,同时保护好LED芯⽚,并且起到提⾼光取出效率的作⽤。
关键⼯序有装架、压焊、封装。
2、LED封装形式LED封装形式可以说是五花⼋门,主要根据不同的应⽤场合采⽤相应的外形尺⼨,散热对策和出光效果。
LED按封装形式分类有Lamp-LED、TOP-LED、Side-LED、SMD-LED、High-Power-LED等。
3、LED封装⼯艺流程三:封装⼯艺说明1、芯⽚检验镜检:材料表⾯是否有机械损伤及⿇点⿇坑(lockhill)芯⽚尺⼨及电极⼤⼩是否符合⼯艺要求;电极图案是否完整2、扩⽚由于LED芯⽚在划⽚后依然排列紧密间距很⼩(约0.1mm),不利于后⼯序的操作。
集成电路封装技术-封装工艺流程介绍

第二章 封装工艺流程
2.4.2 载带自动键合技术
TAB的关键技术
芯片凸点制作技术
TAB载带制作技术
载带引线与芯片凸点的内引线焊接和载带外引线 焊接技术
第二章 封装工艺流程
2.4.2 载带自动键合技术
TAB的关键技术--芯片凸点制作技术
一般工艺方法 将芯片反面淀积一定厚度的Au或Ni,同时在焊盘上淀积
Au-Pd-Ag和Cu的金属层。然后利用合金焊料将芯片焊接在 焊盘上。焊接工艺应在热氮气或能防止氧化的气氛中进行。
硬质焊料
合金焊料
软质焊料
第二章 封装工艺流程
2.3.3 导电胶粘贴法 导电胶是银粉与高分子聚合物〔环氧树脂〕的混合物。银
第二章 封装工艺流程
2.3.1共晶粘贴法 预型片法,此方法适用于较大面积的芯片粘贴。优点是
可以降低芯片粘贴时孔隙平整度不佳而造成的粘贴不完全 的影响。
第二章 封装工艺流程
2.3.2 焊接粘贴法
变形方式的不同,继而产生的各种应力。当材料在外力作用下不能产生位移时,它的几何形状和尺寸将发
在一点的集度焊称为接应粘力〔贴St法res是s〕利。物用体合由于金外反因而响变进形时行,芯在物片体粘内各贴局的部之方间法产生。相优互作点用是的内力, 应变方向平热行,传而导切应性力好的方。向与应变垂直。按照载荷〔Load〕作用的形式不同,应力又可以分为拉伸压
这三种连接技术对于不同的封装形式和集成电路芯片集成度的限制各有 打线键合适用引脚数为3-257;载带自动键合的适用引脚数为12-600;
第二章 封装工艺流程
2.4.1 打线键合技术
打线键合技术
超声波键合(Ultrasonic Bonding ,U/S bonding)
功率器件封装工艺流程
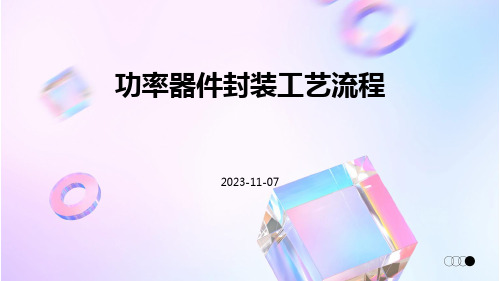
2023-11-07
contents
目录
• 功率器件封装概述 • 前段封装工艺 • 后段封装工艺 • 特殊封装工艺 • 封装工艺材料与设备 • 封装工艺研究与发展趋势
01
功率器件封装概述
封装的作用与重要性
1 2 3
提高功率器件的可靠性
通过封装,可以保护功率器件免受环境因素( 如温度、湿度、尘埃等)的影响,提高其可靠 性。
成品测试
外观检查
对封装完成的功率器件进行外观检查,包括 器件的高度、平整度、引脚是否歪斜等。
电气性能测试
对封装完成的功率器件进行电学性能测试,包括导 通电阻、耐压、电流等参数的测试。
环境适应性测试
对封装完成的功率器件进行环境适应性测试 ,包括高温高湿、振动、盐雾等恶劣环境的 测试。
04
特殊封装工艺
实现标准化和批量生产
通过封装,可以将不同规格和类型的功率器件 进行标准化,从而实现批量生产,提高生产效 率。
提高功率器件的性能
通过先进的封装技术,可以改善功率器件的性 能,例如降低内阻、提高散热性能等。
封装工艺的基本流程
引线键合
将芯片上的电极与引线连接起来, 通常采用超声波键合或热压键合等 方法。
感谢您的观看
THANKS
封装设备
切割设备பைடு நூலகம்
用于将功率器件从原始芯片中分离出来, 并进行初步的切割和形状加工。
清洗设备
用于清洗封装过程中的各种材料和器件, 保证其清洁度和质量。
焊接设备
用于将金属引脚或其他连接件焊接到功率 器件上,保证其可靠性和稳定性。
检测设备
用于检测封装后的功率器件性能和质量, 包括电气性能测试、外观检测等。
mos管封装工艺流程
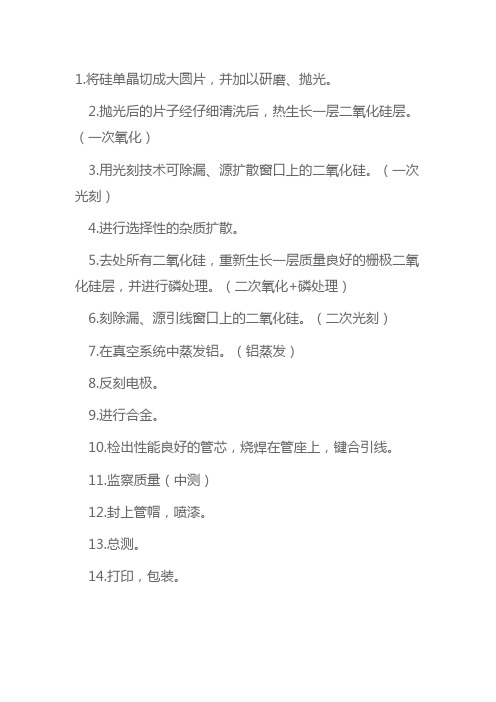
1.将硅单晶切成大圆片,并加以研磨、抛光。
2.抛光后的片子经仔细清洗后,热生长一层二氧化硅层。
(一次氧化)
3.用光刻技术可除漏、源扩散窗口上的二氧化硅。
(一次光刻)
4.进行选择性的杂质扩散。
5.去处所有二氧化硅,重新生长一层质量良好的栅极二氧化硅层,并进行磷处理。
(二次氧化+磷处理)
6.刻除漏、源引线窗口上的二氧化硅。
(二次光刻)
7.在真空系统中蒸发铝。
(铝蒸发)
8.反刻电极。
9.进行合金。
10.检出性能良好的管芯,烧焊在管座上,键合引线。
11.监察质量(中测)
12.封上管帽,喷漆。
13.总测。
14.打印,包装。
3d封装工艺流程
3d封装工艺流程3D封装工艺是一种先进的封装技术,可实现芯片堆叠和三维集成。
以下是3D 封装工艺流程的主要步骤:1. 芯片制备:首先,在硅片上制备出具有不同功能的有源芯片和无源芯片。
这些芯片可以是基于不同材料和工艺制作的,例如CMOS、EEPROM、MOSFET等等。
这些芯片将在后续的工艺流程中用于构建三维集成电路。
2. 基板制备:为了实现芯片的垂直连接,需要使用基板作为支撑和连接材料。
基板通常由高导热性和高电导率的材料制成,例如铜、铝等。
基板上需要制备出凸点和连接线路,以便后续的连接工艺。
3. 芯片贴装:将有源芯片和无源芯片贴装在基板上。
贴装方法可以采用传统的引线键合或倒装焊技术。
在贴装过程中,需要保证芯片的位置和角度精度,以确保后续的连接工艺能够顺利进行。
4. 连接工艺:在贴装完毕后,需要采用引线键合、倒装焊或凸点连接等方法,实现芯片与基板之间的连接。
这些连接方法需要根据不同的应用需求进行选择和优化。
5. 封装保护:在完成连接后,需要采用合适的封装材料和工艺,将整个三维集成电路进行封装保护。
常用的封装材料包括塑料、陶瓷和金属等。
在封装过程中,需要注意保护好内部电路,并确保封装后的可靠性和稳定性。
6. 测试与校准:完成封装后,需要对三维集成电路进行测试和校准。
测试内容可以包括电路性能、电气特性、热特性、机械性能等方面。
根据测试结果进行校准和调整,以保证电路的性能达到预期要求。
以上是3D封装工艺流程的主要步骤。
在实际应用中,根据不同的需求和设计要求,可能还需要进行其他优化和改进。
3D封装工艺的发展为芯片集成和三维集成提供了广阔的应用前景,可以应用于电子器件、通信设备、医疗设备等多个领域。
同时,随着技术的发展和创新,3D封装工艺也将不断得到优化和改进。
陶瓷封装工艺流程
陶瓷封装工艺流程陶瓷封装是一种常用的封装工艺,用于保护集成电路芯片,提高其可靠性和稳定性。
下面是陶瓷封装的工艺流程,详细介绍了各个步骤及其作用。
1.选择陶瓷材料:陶瓷封装主要使用氧化铝陶瓷(Al2O3)作为基材。
根据芯片的需求,选择适当的陶瓷材料,例如高热导率陶瓷、低介电常数陶瓷等。
2.制备陶瓷基片:将选定的陶瓷材料进行制片,通常是通过压制、注塑、模压等工艺进行成型。
制备好的陶瓷基片应具有良好的平整度和尺寸精度。
3.加工陶瓷基片:对制备好的陶瓷基片进行修整和打孔等加工,以便后续的焊接和引线插装。
此步骤需要高精度的机械设备和技术来保证陶瓷基片的质量。
4.制造金属化层:将陶瓷基片进行金属化处理,即在其表面涂覆金属层。
通常使用钼(Mo)或钨(W)等高熔点金属作为电极材料,采用蒸镀、喷涂等技术将金属层均匀地覆盖在陶瓷基片上。
5.焊接芯片:将待封装的芯片通过金线焊接或球焊接等方式连接到陶瓷基片上。
金线焊接使用金线将芯片引脚与陶瓷基片上的金属层相连,球焊接则将芯片引脚与陶瓷基片上的焊球连接。
6.密封封装:将已经焊接好的芯片与陶瓷基片一同放置在封装模具中,然后加以加热和加压处理。
在高温高压下,陶瓷基片与封装模具之间形成均匀的密封,保证芯片在封装过程中不受到外界环境的影响。
7.电性能测试:对已封装的芯片进行电性能测试,包括静态和动态测试等。
静态测试主要检测芯片的电流、电压和功耗等参数,动态测试则测试芯片在不同频率和负载条件下的工作性能。
8.外观检查与包装:对已测试的芯片进行外观检查,包括焊接连接的质量、封装的完整性等。
然后将芯片进行清洁处理,并进行标识和包装,以便后续的运输和应用。
芯片封装工艺流程
芯片封装工艺流程芯片封装是集成电路制造中至关重要的一步,通过封装工艺,将芯片连接到外部引脚,并保护芯片不受外界环境影响。
本文将介绍芯片封装的工艺流程,包括封装前的准备工作、封装工艺的具体步骤以及封装后的测试与质量控制。
1. 准备工作在进行芯片封装之前,需要进行一系列的准备工作。
首先是设计封装方案,根据芯片的功能和性能要求,确定封装形式、引脚数量和布局等参数。
然后进行封装材料的准备,包括封装基板、引线、封装胶等材料的采购和检验。
此外,还需要准备封装设备和工艺流程,确保封装过程能够顺利进行。
2. 封装工艺流程(1)粘合首先将芯片粘合到封装基板上,通常采用导热胶将芯片固定在基板上,以便后续的引线焊接和封装胶注射。
(2)引线焊接接下来是引线焊接的工艺步骤,通过焊接将芯片的引脚与封装基板上的引线连接起来。
这一步需要精密的焊接设备和工艺控制,确保焊接质量和可靠性。
(3)封装胶注射完成引线焊接后,需要将封装胶注射到芯片和基板之间,用于保护芯片和引线,同时还能起到固定和导热的作用。
封装胶的注射需要精确控制注射量和注射位置,以确保封装胶能够完全覆盖引线和芯片。
(4)固化封装胶注射完成后,需要对封装胶进行固化处理,通常采用加热或紫外光固化的方式,确保封装胶能够牢固固定芯片和引线,并具有良好的导热性能。
(5)切割最后一步是对封装基板进行切割,将多个芯片分割成单个封装好的芯片模块。
切割工艺需要精密的设备和工艺控制,以避免对芯片造成损坏。
3. 测试与质量控制封装完成后,需要对芯片进行测试和质量控制,以确保封装质量和性能符合要求。
常见的测试包括外观检查、引脚可焊性测试、封装胶可靠性测试等。
同时还需要进行温度循环测试、湿热循环测试等环境适应性测试,以验证封装的可靠性和稳定性。
总结芯片封装工艺流程包括准备工作、封装工艺步骤和测试与质量控制三个主要环节。
通过精心设计和严格控制每个环节的工艺参数,可以确保封装质量和性能达到要求,为集成电路的应用提供可靠保障。
SOP封装工艺流程介绍
目录
• SOP封装简介 • SOP封装工艺流程 • SOP封装材料 • SOP封装技术发展趋势 • SOP封装工艺问题与对策
01
SOP封装简介
SOP封装定义
SOP封装,全称为Small Outline Package,是一种常见的电子封装形 式,主要用于将集成电路(IC)封装 在印刷电路板(PCB)上。
微型化是指通过减小封装尺寸来减小整个电子设备的体积和重量。SOP封装技 术通过改进封装结构、减小引脚间距、采用薄型小尺寸封装等形式,实现了更 小的封装尺寸,满足了电子设备微型化的需求。
高集成度
总结词
随着集成电路技术的发展,SOP封装技术也呈现出高集成度 的发展趋势。
详细描述
高集成度是指通过在单一封装内集成更多的电子元件和功能 ,提高整个系统的性能和功能。SOP封装技术通过采用多芯 片组装、集成无源元件等方式,实现了更高的集成度,提高 了系统的性能和功能。
02
这一步骤中,需要检查产品是否有明显的缺陷、污渍或不良的
机械性能。
外观检查通常采用自动化设备进行,以提高检查效率和准确性。
03
测试与筛选
测试与筛选是对已完成的SOP封装产品进行电气 性能测试和筛选的过程。
这一步骤中,需要使用测试设备对产品的电气性 能进行检测,如电压、电流、电阻和电容等。
对于不合格的产品需要进行筛选和处理,以确保 最终产品的质量和可靠性。
VS
详细描述
引脚扭曲的原因可能包括引脚材料质量不 佳、加工精度不足、插装过程中受到外力 等。为了解决这个问题,可以加强引脚材 料的质量控制、提高加工精度、优化插装 工艺,并在插装过程中避免外力作用。
芯片破损
总结词
- 1、下载文档前请自行甄别文档内容的完整性,平台不提供额外的编辑、内容补充、找答案等附加服务。
- 2、"仅部分预览"的文档,不可在线预览部分如存在完整性等问题,可反馈申请退款(可完整预览的文档不适用该条件!)。
- 3、如文档侵犯您的权益,请联系客服反馈,我们会尽快为您处理(人工客服工作时间:9:00-18:30)。
设备:
封装工艺流程简介
Tape and reel 编带
设备:
描述:
使用卷带包装设备,将单 颗产品用编带材料(卷带+盖 带)进行打卷包装。
封装工艺流程简介
Packing 包装
描述:
通过捆绑/包装以确 保产品在操作,运输的过 程中不受湿气, ESD的侵 袭,同时也确保产品在运 输过程中不受损伤。
封装工艺流程简介
2016-Jan-1
封装工艺流程简介
FOL
IQA SMT Pre-bake
基板收取Βιβλιοθήκη 来料检验IQA表面贴装* 可选 基板烘烤
Taping BG W/M
De-tape
D/S
2/O Fail
QA Pass
DA
DAC
Plasma
圆片收取 来料检验 贴保护膜 背部研磨 圆片装载 去掉保护膜
芯片切割 第二次光学检查
封装工艺流程简介
Baking 烘烤
描述:
PCB需要在做DA之 前做一下烘烤,以去 除PCB中的水分,提高 产品的可靠性能。
设备:
N2以防止PCB氧化
N2 inlet
Carrier Carrier
Outlet
125oC
封装工艺流程简介
Die Attach 装片
描述:
利用银浆或Film的 粘性将切割好的好的 晶粒吸取并粘贴于基 板上,以便于后制程作 业。
等离子清洗示意图
封装工艺流程简介
MD 包封
描述:
将前道完成后的产品 ,使用塑封料把芯片 塑封起来,免受外力损 坏。同时加强器件的 物理特性便于使用。
设备:
封装工艺流程简介
PMC 包封后烘
描述:
把塑封后的产品放入烘箱对其 进行固化,以提高塑封体的硬 度,稳定固化物分子结构。
N2 inlet
Carrier Carrier
描述:
Final test是集成电路 在完成相应的制造过程后, 测试产品是否达到设计时规 定的各种参数标准。简而言 之, 就是测试集成电路是否 合格。
在测试程序的控制下 ,对被测器件输入指定的激 励信号并测量其响应的设备 。根据应用的范畴可分为: 数字信号、模拟信号、混合 信号及存储器件测试机。 当前主要的测试机供应商包 括:
设备: 设备:
Capillary
金线 焊针
晶粒
铝垫 金手指
Wire
封装工艺流程简介
Plasma (Before MD) 等离子清洗
描述:
使用电解氩离子和氧 离子,将表面污染及 碳化物清洗掉,以增 加PCB与塑封料的结合 ,提高产品的可靠性 能。
设备:
氩离子 H2O CO2
U
氧离子 Ar2 + O2
DAC 装片后烘烤
描述:
装片后的基板需要 放在烘箱中进行烘烤, 以确保银浆或者Film能 粘住芯片。
设备:
封装工艺流程简介
Plasma 等离子清洗
描述:
使用电解氩离子和高 活性原子,将表面污 染形成挥发性气体, 再有真空系统带走, 达到表面清洁之作用 ,使得焊线时结合力 更好。
WB 球焊
描述:
利用金线(铜线)将晶 粒与基板上的外接电 路连接, W/B质量的好 坏直接影响到产品的 可靠性,性能和使用寿 命。
封装工艺流程简介
SMT 表面贴装
描述:
将电容,电阻,电感 等元器件通过锡膏贴焊 于基板上,然后通过 Reflow 焊接,最后通过 Cleaning机台清洗产品 表面的助焊剂。
Solder Paste Printing Surface Mount Technology
SMT Cleaning
SMT reflow
封装工艺流程简介
设备:
Taping 贴保护膜
描述:
在圆片表面贴上一 层保护膜以防止在磨 片过程中圆片表面线 路受损。
材料:
胶膜
Photo 1 晶圆
作业平台
BG+W/M+ De-taping 背部研磨+贴片+去胶膜
描述:
通过研磨轮对圆片的 背面进行研磨,使其符 合封装工艺要求。
原始厚度晶圆
晶圆背面
贴片 研磨砂轮
激光
封装工艺流程简介
SGN 切割
描述:
将一条产品用刀片切 成一个一个的产品并盛装 在Tray盘中,便于后续包 装出货.
设备:
Blade 刀片
封装工艺流程简介
FVI 外观检验
描述:
对产品进行人工检验 (产品外观缺陷,如印字 、植球、基板和塑封体表 面的品质等)
设备:
封装工艺流程简介
FT 电性能测试
WB1 球焊1
WB2
球焊2*可选
3/O
Fail QA Pass
第三次光学检查 QA第三次光学检查
QA第二次光学检查
装片 装片后烘 等离子清洗
封装工艺流程简介
EOL
Plasma
MD
PMC
LMK
SGN
Lead scan
FVI Fail
QA Pass
Packing
产品收取 等离子清洗 包封 包封后烘烤 激光打印 产品切割 外观扫描 外观检查 QA外观检查 包装
去胶膜
目标厚度晶圆
封装工艺流程简介
WS 圆片切割
设备:
描述:
通过高速旋转的刀 片将绷膜好的wafer 切 割成单个 的芯片,与此 同时冷却水和离子水一 边冷却由于高速摩擦而 产生的热量; 一边清洗 划片时产生的硅屑。
Laser grooving 激光开槽
描述:
在极短的时间内,激光 雷射能量通过聚光 棱镜集中照射到微 小的面积上,使固 体升华或者蒸发, 从而达到切割的目 的.主要用于Low-K 圆片的切割
Outlet
175oC
封装工艺流程简介
MK 激光打印
描述:
将被打印的内容在计算 机上编好,通过机器使具 有一定能量的激光束按照 设定的轨迹在塑封体上烧 刻出所需要的打印内容。 通常打印的内容括:
客户公司商标、产品 批次号、封装日期和国家 等。
设备:
XX科技 CZ013 2014.01.06
XXX科技 CZ013 20